
Основы проектирования электронных средств Материалы к Экз ОПЭС-2014 РК-01-02 / Не для распространения Введение в технологию поверхностного монтажа
.pdf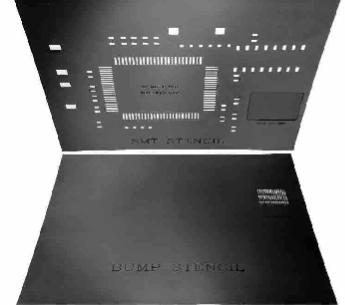
нанесения пасты на контактные площадки под flip chip с размером отверстий 0,127 мм и шагом отверстий 0,3 мм изображен на Рис. 1.18. Трафарет изготовлен методом химического травления, стенки отверстий подвергнуты электрохимической обработке и имеют трапецеидальную форму с 6-микронным сужением каждой стороны.
На втором этапе паста через трафарет наносится на контактные площадки под остальные ПМИ. Для этого используется трафарет толщиной 180 мкм с полостями со стороны ПП глубиной 90 мкм. Полости в трафарете обеспечивают зазор, предотвращающий размазывание отпечатков пасты на контактных площадках под flip chip. После вышеописанного нанесения пасты через трафарет в два этапа происходит установка компонентов на плату PCMCIA и пайка оплавлением. Трафарет для нанесения пасты на контактные площадки под остальные ПМИ изображен на Рис. 1.19. Когда размеры кристалла компонента flip chip превышают 5х5 мм, в полостях трафарета вытравливаются поддерживающие столбики для того, чтобы избежать прогибов трафарета в областях контактных площадок под flip chip и размазывания отпечатков пасты. Эти поддерживающие столбики располагаются между отпечатками пасты.
Рис. 1.19. Трафареты для нанесения пасты в два прохода (снизу трафарет для нанесения пасты на контактные площадки под flip chip, сверху – под остальные ПМИ)
Некоторые преимущества использования трафаретов для нанесения пасты в два прохода в случае наличия в изделии flip chip и других ПМИ таковы:
∙так как используются различные трафареты, есть возможность раздельной оптимизации процессов нанесения пасты на контактные площадки под flip chip и другие ПМИ;
∙поскольку операции нанесения пасты раздельны, возможно нанесение различных типов пасты на контактные площадки под flip chip и под остальные ПМИ. Также возможно использование flip chip с полимерными выводами и нанесение токопроводящего полимера на контактные площадки под flip chip с последующим нанесением пасты на контактные площадки под остальные ПМИ.
1.3.5. Трафареты для кристаллов
Повышенный интерес к компонентам flip chip инициировал заинтересованность в рассмотрении альтернативных методов формирования выводов на поверхности кристаллов. Традиционно, выводы на поверхности кристаллов изготавливали по технологии C4 (Controlled Collapse Chip Connection), разработанной IBM более четверти столетия тому назад. В конце XX в. были получены металлические и полимерные выводы на поверхности кристаллов методом трафаретной печати. Трафарет для формирования
21

выводов кристаллов показан на Рис. 1.20. На Рис. 1.21 показаны выводы из токопроводящего полимера, нанесенного через трафарет.
Требуемый шаг отверстий трафарета лежит в пределах 0,10-0,38 мм, размеры отверстий составляют 0,05-0,18 мм. Требования по толщине трафарета таковы: 25-75 мкм. Трафареты для формирования выводов кристалла изготавливаются методами химического травления, гальванопластики, лазерной резки. Однако изготовление методом лазерной резки более 100000 отверстий занимает много времени и, следовательно, дорого. После изготовления трафареты должны подвергаться контролю на предмет наличия всех отверстий и соответствия размеров отверстий заданным значениям. Более того, при обнаружении дефектов необходимо их устранение. Дефект, заключающийся в отсутствии отверстия, как правило, можно исправить, но избыточное отверстие – критичный дефект, обычно не подлежащий исправлению. Очень важно контролировать искажения рисунка трафарета, особенно при диаметре пластины 200 мм. При изготовлении трафаретов методами химического травления и гальванопластики необходимо использовать качественные пленочные или стеклянные фотошаблоны.
Рис. 1.20. Трафарет для формирования выводов |
Рис. 1.21. Кристалл с выводами из |
кристалла (размер отверстий 0,127 мм, шаг отверстий |
токопроводящего полимера, нанесенного |
0,3 мм, толщина трафарета 50 мкм, кол-во отверстий |
через трафарет (внизу – увеличенный вид) |
110000) |
|
1.3.6. Трафареты для ПМИ / BGA
Область применения микросхем в корпусе BGA заметно увеличивается, и популярность этих компонентов будет продолжать повышаться. Нанесение пасты на контактные площадки под BGA и под остальные ПМИ, возможно, потребует применения различных трафаретов. Выводы компонентов PBGA (пластиковые BGA) изготовлены из эвтектического сплава, высота которых уменьшается в процессе пайки до уровня 75% от начальной. Компоненты CBGA (керамические BGA) имеют выводы, изготовленные из более тугоплавкого сплава Sn90/Pb10, и их высота не уменьшается во время пайки. Следовательно, компоненты CBGA более чувствительны к проблемам, связанным с компланарности выводов (отсутствие контакта), чем PBGA. Если в ПУ среди ПМИ присутствуют компоненты PBGA, то толщина трафарета может определяться, исходя из требований, предъявляемых другими ПМИ; типичные значения: 150 мм при шаге выводов 0,5 мм, 125 мкм – при 0,4 мм. Минимальная толщина трафарета при использовании компонентов CBGA 200 мкм, что необходимо для обеспечения достаточной высоты отпечатков пасты в целях исключения отсутствия контакта. Если в изделии имеются компоненты CBGA с шагом выводов 0,5 мм, рекомендуется использовать ступенчатые трафареты толщиной в области CBGA 200 мкм, а в области QFP и других ПМИ с малыми
22

размерами – 150 мкм. Отверстия трафарета для CBGA и μBGA (с шагом выводов 0,5 мм) рекомендуется изготовлять методам лазерной резки для точного контроля количества наносимой пасты. Имеются данные, что трафареты со слегка скругленными отверстиями обеспечивают более высокий результат, чем трафареты с круглыми отверстиями.
Итак, при разработке конструкции трафарета не стоит ограничиваться только трафаретами фиксированной толщины. Ступенчатые трафареты – это эффективное средство достижения нанесения надлежащего количества пасты при пайке оплавлением ПУ, содержащих небольшое количество штырьковых компонентов, а также компонентов CBGA. При пайке оплавлением штырьковых компонентов, требующих нанесение большего количества пасты, могут применяться трафареты для нанесения пасты в два прохода. Можно с уверенностью утверждать, что только тщательный подбор материалов, разработка конструкции и качество изготовления трафарета могут обеспечивать высокие результаты трафаретной печати и качество паяных соединений.
1.4.Технологические параметры. Выбор технологических параметров
Основные технологические параметры процесса трафаретной печати таковы:
∙усилие прижима ракеля к трафарету;
∙скорость движения ракеля;
∙зазор между трафаретом и ПП;
∙угол наклона ракеля;
∙твердость ракеля;
∙температура.
Fр
Ракель
Паяльная
паста
Трафарет
Fпод
α r
Fравн
Рис. 1.22. Силы, действующие на ракель в процессе нанесения пасты
Связь между многочисленными силами и параметрами может быть описана при помощи основных законов гидромеханики. Паяльная паста продавливается через отверстия под действием гидродинамического давления, действующего на ракель и трафарет. Гидродинамическое давление пасты на ракель приводит к возникновению подъемной силы (Fпод), которая вместе с усилием ракеля (Fр) результируется в равнодействующей силе Fравн (см. Рис. 1.22). Это описывается следующим соотношением:
Fравн = Fр − Fпод cosα
Подъемная сила, входящая в данное уравнение, создается гидродинамическим давлением пасты, действующим на ракель. Это давление приближенно выражается так:
≈ ηVf (α) pп r
из чего следует
Fпод = ηVf (Q) f (α) ,
где η – вязкость пасты;
V – скорость движения ракеля;
r – ширина области контакта валика пасты с трафаретом;
23
α – угол наклона ракеля;
f(α) – геометрическая функция α (значение которой уменьшается с 5 при α=60° до 4
при α=70°);
f(Q) – функция, зависящая от количества пасты перед ракелем (значение которой увеличивается при повышение количества пасты).
Критерий оценки качества трафаретной печати – очистка верхней поверхности трафарета от пасты при проходе ракеля.
Усилие. Усилие оказывает очень существенное влияние на процесс нанесения пасты. Эмпирическое правило: 1 кг / 100 мм длины ракеля при скорости 10 мм/с. Но это приблизительное значение, с которого следует начинать подбор. При этом при увеличении скорости в два раза усилие также следует удвоить.
В идеале, скорость движения ракеля и усилие должны задаваться так, чтобы верхняя поверхность трафарета оставалась чистой. Если усилие недостаточно, то паста будет размазываться по трафарету, высота отпечатков будет слишком большой и трудно контролируемой. Если усилие слишком велико, то ракель будет вычерпывать пасту из отверстий трафарета, что приведет к малой высоте отпечатков. Если длина ракеля существенно превышает длину ПП, то при использовании металлических ракелей слишком большое усилие может привести к изменению угла наклона ракеля по причине его деформации.
Использование твердого ракеля может привести к снижению влияния данного эффекта. Однако в случае применения ступенчатого трафарета ракель должен быть достаточно гибким для прогибания в области минимальной толщины, в которых имеются отверстия.
Если усилие слишком велико, то будет наблюдаться не только вычерпывание, но паста будет затекать под трафарет и стремится образовывать перемычки. Это приведет к необходимости частой очистки нижней поверхности трафарета.
Как только определено подходящее усилие, системы создания давления с обратной связью, использующиеся в автоматах трафаретной печати, будут поддерживать заданное значение во время нанесения пасты, обеспечивая повторяемость и устраняя необходимость регулировки.
Скорость движения ракеля. Скорость движения ракеля обычно задается в соответствии с вязкостью пасты. Чем больше вязкость, тем меньше скорость движения ракеля, следовательно, чем меньше вязкость, тем выше скорость. Как правило, скорость движения ракеля выбирается в пределах 12-50 мм/с.
Проблема, ассоциируемая со скоростью движения ракеля, заключается в недостаточном времени для заполнения пастой отверстий трафарета. Если выбрана скорость, равная 12 мм/с, то заполнение пастой отверстия шириной 0,3 мм потребует 25 мс. Следовательно, скорость движения ракеля может быть снижена, чтобы увеличить вероятность успешного нанесения пасты через столь малые отверстия. Если это не приводит к успеху, то, возможно, требуется изменение конструкции трафарета. Необходимо заметить, что уменьшение скорости движения ракеля приведет к увеличению давления на пасту. И наоборот, увеличение скорости движения снизит прилагаемое давление. Изменение скорости движения ракеля повлечет за собой корректировку усилия.
Необходимо отметить, что в настоящее время существует целый класс паст, предназначенных для нанесения на повышенной скорости. Эти пасты характеризуются высоким тиксотропным индексом, благодаря чему при приложении усилия вязкость ее резко уменьшается, и паста продавливается в отверстия трафарета. После снятия усилия вязкость пасты быстро восстанавливается до первоначального значения. При использовании паст такого типа возможно качественное нанесение пасты под компоненты с шагом 0,5мм со скоростью около 100мм/с.
24
Твердость ракеля. Твердость ракелей определяется по методу Шора. Существует несколько уровней твердости ракелей, но не все из них распространены. Наиболее широко применяются ракели трех типов:
∙мягкий, с твердостью 65 единиц;
∙средний, с твердостью 75 единиц;
∙жесткий, с твердостью 90 единиц.
Тип ракеля подбирается, исходя из используемого трафарета: ракель средней жесткости для ступенчатого трафарета, жесткий – для трафарета фиксированной толщины.
Важно правильно установить ракель в держателе. Если ракель расположен неровно, то и отпечатки будут неровными. Это проявляется тем заметнее, чем выше твердость ракеля. Мягкий ракель будет стремиться самовыравниваться, хотя вероятность вычерпывания пасты из отверстий трафарета будет высокой. Отклонение ракеля от горизонтального положения может компенсироваться увеличением усилия, но вновь будет происходить вычерпывание пасты.
Внастоящее время наиболее широко используются металлические ракели, так как они обеспечивают лучшее управление технологическим процессом. Как правило, срок службы металлических ракелей больше, и их применение позволяет снизить вероятность вычерпывания пасты. Развитие в области конструирования ракелей привело к появлению различных покрытий, скругленных краев, увеличивающих срок службы трафарета, а также к использованию ракелей с различными углами наклона. Уменьшение угла наклона ракеля увеличивает качество и повторяемость нанесения пасты на контактные площадки под компоненты с малым шагом выводов. Металлические ракели “полируют” поверхность трафарета, что является одним из их отличий от полиуретановых ракелей.
1.5.Технология Pin in Paste
Впрактике часто случаются ситуации, когда на плату с большим количеством поверхностно-монтируемых компонентов требуется установить всего несколько штырьковых компонентов. Пайка этих компонентов вручную или волной ведет к увеличению себестоимости изделия. В этом случае можно рассмотреть возможность пайки штырьковых компонентов в печи оплавления за один проход с ПМИ (технология Pin in paste). Особенно если имеющиеся на предприятии автоматы установки компонентов имеют возможность работы со штырьковыми компонентами. Это технология довольно сложна, однако успешно применяется на ряде предприятий.
При применении технологии Pin in Paste следует принять во внимание следующие правила и соображения.
Конструкция трафарета. Конструкция трафарета должна в первую очередь обеспечить качественное нанесение пасты под ПМИ. Размеры отверстий для пасты под штырьковые компоненты выполняются размером, несколько большим, чем размеры контактных площадок. Таким образом, паста не только заполняет отверстие, но и наносится на контактную площадку и вокруг контактной площадки на паяльную маску. Дело в том, что при оплавлении объем пасты уменьшается примерно наполовину. И тем не менее этого объема должно хватить для полного заполнения монтажного отверстия и формирования галтелей сверху и снизу ПП. Диаметры отверстий для пасты под штырьковые компоненты рассчитываются по формуле, приведенной в разделе 1.3.3.
Степень заполнения монтажных отверстий регулируется подбором параметров нанесения. В отдельных случаях можно рассмотреть возможность создания местных утолщений на трафарете либо использование двух трафаретов разной толщины – сначала для нанесения пасты под ПМИ, затем под штырьковые компоненты. Обычно толщина трафарета для штырьковых компонентов составляет 0,4 – 0,8 мм. Нижняя сторона такого трафарета, прилегающая к ПП, имеет рельефную поверхность, содержащую протравленные углубления на глубину не менее 0,25 мм в тех местах ПП, где уже нанесена паста для компонентов поверхностного монтажа.
25

Штырьковые компоненты должны быть пригодны к пайке в печи оплавления:
∙компоненты должны выдерживать температуру в печи оплавления;
∙корпуса компонентов не должны касаться пасты, т.е. должны несколько возвышаться над ПП. Касание корпусом пасты может привести к возникновению шариков припоя и перемычек или воспрепятствовать расплавлению пасты. Для некоторых компонентов наличие специальных буртиков предусмотрено производителем;
∙вывод компонента не должен выступать с нижней стороны ПП более, чем на 1,5 мм. В противном случае паста может не затечь в отверстие, сформировав каплю на конце вывода, или стечь в печь.
Паста должна быть пригодна для Pin in Paste. В принципе для Pin in Paste
пригодны все пасты, однако не все из них дают одинаково хорошие результаты. Паста должна обеспечить хорошее заполнение отверстий при перемещении ракеля и должна хорошо удерживаться в отверстии и на выводе.
Технологические параметры нанесения:
∙для улучшения заполнения монтажных отверстий диаметр валика пасты перед ракелем должен быть не менее 25 мм;
∙по этой же причине необходимо снижать скорость нанесения;
∙увеличить усилие ракелей. При этом увеличивается деформация ракеля, что приводит к уменьшению угла наклона и, соответственно, давления нанесения;
∙применять ракели с углом наклона 45º;
∙нанесение за два прохода. Однако при этом может ухудшиться качество печати для ПМИ.
Очень хорошие результаты нанесения пасты в отверстия дает система ProFlow.
Благодаря своей конструкции она создает только вертикальное усилие, обеспечивающее великолепное проникновение пасты в отверстия.
1.6.Технология ProFlow
Сувеличением плотности монтажа, расширением применения компонентов с малым шагом выводов и повышением требований к производительности сборочномонтажных линий, в области трафаретной печати стало производиться больше исследований. Как следствие в последние несколько лет традиционное оборудование для трафаретной печати и технологии нанесения пасты претерпели существенные изменения.
При нанесении пасты ракелями на тяговое усилие/усилие нанесения оказывают влияние следующие параметры:
∙угол наклона ракелей;
∙скорость перемещения ракелей;
∙реология пасты;
∙объем пасты в валике.
Рис. 1.23. Процесс нанесения пасты с использованием ракелей
26

В отличие от традиционного процесса трафаретной печати с использованием ракелей нанесение пасты с применением Proflow обладает следующими преимуществами:
∙давление, прилагаемое к паяльной пасте, не зависит от объема пасты в валике;
∙паста находится внутри головки и изолирована от влияния атмосферного воздуха, что препятствует испарению растворителей из пасты, ее окислению и загрязнению;
∙обеспечивается постоянный объем пасты на трафарете;
∙уменьшаются потери пасты.
Система Proflow работает следующим образом. Головка Proflow постоянно находится на трафарете. Перед началом цикла нанесения после считывания реперов головка прижимается к трафарету с запрограммированным усилием. Поршень Proflow подключается к давлению, величина которого устанавливается программно и регулируется с помощью автоматического регулятора давления. Затем головка Proflow перемещается с заданной скоростью.
Рис. 1.24. Процесс нанесения пасты с использованием Proflow
Технологические параметры при работе с Proflow таковы: усилие прижима головки Proflow к трафарету, давление на поршень Proflow, скорость перемещения головки Proflow. При нанесении пасты с помощью Proflow очень важна правильная поддержка ПП и трафарета снизу. Размеры ПП всегда меньше размера головки Proflow, поэтому неправильно организованная поддержка с краев Proflow приведет к нестабильным результатам нанесения и загрязнению трафарета пастой.
Рис. 1.25. Поддержка Proflow
27

Рис. 1.26. Неправильная поддержка
При нанесении пасты с использование Proflow давление, оказываемое на пасту, значительно превышает давление при использовании ракелей. Поэтому при проектировании трафаретов размеры отверстий для компонентов с малым шагом необходимо уменьшать на 10% по сравнению с размерами контактных площадок. В противном случае возможно проникновение пасты в зазор между ПП и трафаретом и образование перемычек. Вообще говоря, это правило следует применять и при использовании ракелей.
Рис. 1.27. Правило конструирования отверстий трафаретов для микросхем с малым шагом
Из-за конструктивных особенностей Proflow отверстия трафарета не должны находиться ближе 5 мм к краю ПП. Во избежание повреждения скребков или трафарета отверстия размером более 5 мм следует выполнять в виде нескольких меньших отверстий, разделенных перемычками размером не менее 0,2 мм.
Рис. 1.28. Разделение отверстий больших размеров
1.7.Технология нанесения клея через трафарет
Врезультате повышения плотности монтажа и увеличения многообразия элементной базы перед предприятиями электронной промышленности встала необходимость внедрения новых технологий сборочно-монтажных работ. В течение многих лет для нанесения клея под ПМИ перед пайкой волной использовалось
28
дозирование. Широкое применение высокопроизводительных автоматов установки чипкомпонентов и еще большее усложнение ПУ привело к тому, что автомат дозирования становится “узким” местом производственной линии, ограничивающим производительность. Вследствие этого возродился интерес к нанесению клея через трафарет, что не осталось незамеченным основными производителями клеев, каждый из которых сейчас предлагает специальные клеи для нанесения через трафарет.
Нанесение клея через трафарет – сверхвысокопроизводительный и дешевый технологический процесс. В то время как дозирование – последовательный процесс, все клеевые точки могут быть нанесены через трафарет за один рабочий ход ракеля.
Хотя это и не имело широкого распространения, но в течение нескольких лет отдельное число производителей электроники применяло нанесение клея через трафарет перед установкой пассивных компонентов, и оказалось, что процесс обладает высокой стабильностью. Однако единственным ощутимым недостатком нанесения клея через обычный металлический трафарет является невозможность получения клеевых точек различной высоты для разных компонентов без использования дорогих ступенчатых трафаретов.
Металлические трафареты могут быть использованы для нанесения клея также, как и для нанесения пасты, но, как правило, для нанесения клея используются трафареты большей толщины. Типичная толщина металлического трафарета для нанесения пасты составляет 250 мкм. Если использовать в качестве материала трафарета пластик, то становится возможным наносить клей через трафареты толщиной более 1 мм с отверстиями, полученными сверлением.
1.7.1. Факторы, подлежащие рассмотрению
Рассмотрим основные факторы, влияющие на технологический процесс (см. Табл.
1.5)
|
Дозирование |
|
|
Нанесение с помощью трафарета |
||||
|
|
|
1. Клей |
|
|
|
|
|
∙ |
Вязкость |
|
|
∙ |
Вязкость |
|
|
|
∙ |
Смачивающая способность |
|
∙ |
Смачивающая способность |
|
|||
∙ |
Температурная стабильность |
|
∙ |
Температурная стабильность |
|
|||
|
|
|
2. Автомат |
|
|
|
||
∙ |
Давление |
|
|
∙ |
Усилие ракеля |
|
|
|
∙ |
Время |
|
|
∙ |
Скорость движения ракеля |
|
|
|
∙ |
Температурная стабильность |
|
∙ |
Зазор между трафаретом и ПП |
||||
∙ |
Система поддержки ПП |
|
∙ |
Система поддержки ПП |
|
|
||
∙ |
Производительность |
|
∙ |
Производительность |
|
|
||
|
|
|
3. Оснастка |
|
|
|
||
∙ |
Конструкция |
дозирующей |
иглы |
∙ |
Конструкция отверстий |
|
(отношение |
|
|
(расстояние от иглы до ПП, диаметр и т. |
|
площади |
отверстий |
к |
толщине |
||
∙ |
д.) |
|
|
∙ |
трафарета и т. д.) |
|
|
|
Закупорка дозирующей иглы |
|
Закупорка отверстий трафарета |
||||||
∙ |
Износ дозирующей иглы |
|
∙ |
Тип ракеля |
|
|
|
|
∙ |
Прочистка дозирующей иглы |
|
∙ |
Износ ракеля |
|
|
||
|
|
|
|
∙ |
Очистка трафарета |
|
|
|
|
|
|
4. Конструкция ПП |
|
|
|
||
∙ |
Конструкция контактных площадок (ПП |
∙ |
Конструкция контактных площадок (ПП |
|||||
|
с поверхностью, выровненной горячим |
|
с поверхностью, выровненной горячим |
|||||
∙ |
воздухом и др.) |
|
|
∙ |
воздухом и др.) |
|
|
|
Защитная маска |
|
|
Защитная маска |
|
|
|||
∙ |
Расположение проводников |
|
∙ |
Расположение проводников |
|
29
∙ Расположение отверстий |
∙ Расположение отверстий |
Табл. 1.5. Факторы, влияющие на технологический процесс
Клей. Характеристики клея играют главную роль, как при дозировании, так и при нанесении через трафарет. Вязкость материала может определять давление воздуха и время нахождения дозирующей головки в нижнем положении при дозировании и скорость движения ракеля при нанесении через трафарет. Клеи, предназначенные для дозирования, могут наноситься через трафарет, но при этом надо принять во внимание дополнительные факторы. Эти факторы включают в себя высыхание, поглощение влаги, загрязнение растворителями, используемыми для очистки трафарета, и т. д. По этим причинам химический состав клеев специально разрабатывался для соответствия требованиям, предъявляемым условиями их использования.
Автомат. Обычно давление ракеля задается так, чтобы поверхность трафарета оставалась чистой так же, как и при нанесении пасты. Зазор между трафаретом и ПП задается для контактного нанесения клея так же, как и при нанесении пасты. Наиболее важным параметром является скорость движения ракеля. Как правило, скорость движения ракеля ограничена вязкостью клея. Нанесение клея через трафарет благодаря меньшему типичному значению вязкости клея может происходить при более высокой скорости движения ракеля. Поэтому время цикла обычно составляет около 30 сек. Сравнивая это значение с характеристиками высокопроизводительных автоматов дозирования, вы увидите явное преимущество нанесения клея через трафарет при увеличении количества клеевых точек или компонентов.
Оснастка. Конструкция трафарета главным образом зависит от типа компонентов. Технологические ограничения, такие, как отношение площади отверстия к толщине трафарета, играют роль при малых размерах компонентов. Это приводит к проблемам при наличии как компонентов с малыми размерами, так и крупных компонентов с большими зазорами. В таком случае возможно использование трафаретов с нестандартной конструкцией отверстий. Следующим вопросом, который необходимо затронуть при рассмотрении оснастки, является вопрос ракелей. Металлический ракель с углом 45° показал высокую повторяемость отпечатков клея.
Конструкция ПП. Также играет важную роль при нанесении клея. Непостоянство толщины защитной маски и контактных площадок, что имеет место в ПП с поверхностью, выровненной горячим воздухом, может привести к возникновению проблем, как при дозировании, так и при нанесении через трафарет.
1.7.2. Что дает нанесение через трафарет?
Производительность. Ниже приведено сравнение времени цикла автоматов дозирования с производительностью 30000 и 40000 доз/ч с временем цикла автомата трафаретной печати (см. Табл. 1.6). Необходимо заметить, что время цикла автомата дозирования указано на основе максимальной производительности.
Производительность 30000 доз/ч |
Производительность 40000 доз/ч |
||||
Время цикла |
Кол- |
Время цикла |
Время цикла |
Кол- |
Время цикла |
автомата |
во |
автомата |
автомата |
во |
автомата |
трафаретной |
доз |
дозирования, |
трафаретной |
доз |
дозирования, |
печати, мин. |
|
мин. |
печати, мин. |
|
мин. |
0,5 |
100 |
0,20 |
0,5 |
100 |
0,15 |
0,5 |
250 |
0,50 |
0,5 |
250 |
0,38 |
0,5 |
500 |
1,00 |
0,5 |
500 |
0,75 |
0,5 |
1000 |
2,00 |
0,5 |
1000 |
1,50 |
0,5 |
2000 |
4,00 |
0,5 |
2000 |
3,00 |
0,5 |
5000 |
10,00 |
0,5 |
5000 |
7,50 |
30