
книги / Технология лаков и красок
..pdfвым вентилем. Емкость типовых реакторов составляет от 1 до 16 м3 и принимается в зависимости от масштабов, производства и специфичности производства некоторых видов синтетических ла ков и смол. В настоящее время для крупнотоннажных производств проектируются реакторы емкостью до 50 м3.
На рис. 10.1— 10.3 представлены реакторы различных типов, применяющиеся для синтеза смол. Реактор с рубашкой и змееви ком, приведенный на рис. 10.1, может применяться при обогреве конденсирующимися парами воды или высококипящими теплоно сителями. Обогрев реактора осуществляется при помощи рубашки 4у а охлаждение — при помощи змеевика 5. Загрузка реактора твердыми и жидкими компонентами производится через люк и штуцера, расположенные на крышке 2; выгрузка содержимого
реактора производится |
через угловой вентиль |
7 с |
помощью |
механизма слива 8. Ластовая мешалка 6, сидящая |
на валу 3, |
||
приводится во вращение |
электродвигателем 1 |
через |
редуктор, |
укрепленный на крышке реактора. Аппарат имеет четыре лапы, расположенные под углом 90 °С, на которых он монтируется в перекрытии или на площадке.
Реактор с полутрубными элементами обогрева (см. рис. 10.2) применяется в тех же случаях, что и реактор, описанный выше. Обогрев реактора ведется при помощи полутрубных элементов обогрева 4. Загрузка и выгрузка реактора производятся так же, как и в предыдущем случае.
Для процессов синтеза алкидных и других смол при 220—300 °С применяется преимущественно реактор с электроиндукционным обогревом. Обогрев реактора ведется секционными электроиндукционными нагревателями. Несколько секций нагревателей распо ложены на цилиндрической части реактора и одна секция — в донной части. Внутри аппарата расположен змеевик, который ис пользуется для охлаждения содержимого реактора или (в случае комбинированного пароэлектрического обогре ва)— для обогрева реактора конденсирующи мися парами воды. Загрузка и выгрузка реак тора производится таким же образом, как и в реакторах, описанных выше. Реактор снаб жен ластовой мешалкой. В настоящее время отечественной промышленностью создан и эксплуатируется реактор с электроиндукцион ным обогревом емкостью 32 м3, который имеет высокие технологические и технико-экономи ческие показатели. В одиннадцатой пятилетке намечается широкое внедрение этих реакторов в промышленность.
Р н с . 10.3. Р е а к т о р с к о м б и н и р о в а н н ы м о б о г р е в о м :
1 — э л е к т р о д в и г а т е л ь ; 2 — к р ы ш к а ; 3 — к о р п у с р е а к т о р а ; 4 — в а л ; 5,— п р о п е л л е р н а я м е ш а л к а ; 6 — р у б а ш к а д л я о б о г р е в а п а р а м и Д Ф С ; 7 — э л е к т р о н а г р е в а т е л ь .
811
Для синтеза алкидных смол, алкидиых олиф и некоторых дру*
гих смол ^применяется реактор с комбинированным |
обогревом |
(см. рис. 10.3) парами высококипящих теплоносителей |
(дифениль- |
ная смесь). Пары жидкой дифенилыюй смеси, находящейся в удлиненной рубашке реактора 6, образующиеся при нагреве смеси погруженными в нее электронагревателями, обогревают стенки и днище аппарата 3 и, конденсируясь, стекают на дно рубашки. Загрузка и выгрузка реактора производится через люк и штуцер, расположенные в крышке 2. Выгрузочная труба опущена до дна аппарата. Реакторы снабжены пропеллерной мешалкой 5 и изго тавливаются из нержавеющей двухслойной или эмалированной стали.
Технологические процессы при производстве пленкообразую щих проходят в температурном интервале 60—350 °С (нижний пре дел — при нагреве пленкообразующих перед их очисткой; верх ний— для процессов полимеризации и при синтезе некоторых пленкообразующих).
При изготовлении некоторых смол, в частности эпоксидных, необходима отгонка растворителя из реакционной смеси. Из-за высокой вязкости смолы и термической ее нестабильности прове дение ректификации в аппаратах периодического действия боль шой емкости вызывает ряд затруднений.
Для этой цели нашли применение роторно-пленочные испарите ли колонного типа. В них процесс ректификации проходит в тонкой пленке, образуемой при вращении ротора. Аппарат (рис. 10.4) представляет собой колонну, состоящую из отдельных царг 5. Межфазный контакт между жидкостью и паром осуществляется на поверхности пленки жидкости. Роль ротора в аппаратах этого типа сводится к распределению жидкой фазы по твердой поверх ности с образованием стекающей тонким слоем пленки, а также к турбулизации паровой фазы за счет вращательного движения ро тора. Ротор представляет собой вал 5, на котором насажена крыльчатка типа «беличьего» колеса с подвижными лопастями 4. Каждая царга снабжена паровой рубашкой.
Способы обогрева. Основными способами обогрева реакцион ной аппаратуры являются:
1)паровой обогрев (конденсирующимся водяным паром);
2)огневой обогрев — продуктами сгорания топлива;
3)обогрев электрическим током;
4)обогрев высококипящими теплоносителями.
Па р о в о й о б о г р е в . Процессы, протекающие при темпера туре до 140 °С, обычно осуществляются в аппаратах с обогревом конденсирующимся водяным паром (при синтезе карбамидных, ряда фенольных и других смол). При температурах выше 140°С
приходится применять пар повышенного давления (выше 0,7 МПа), что не всегда является возможным.
При паровом обогреве применяются паровые рубашки, паровые змеевики и трубчатые подогреватели (теплообменники).
912
Рис. 10.4. Пленочно-роторный испаритель:
/ — пробка; 2—диск; 3—вал; 4—лопасть; 5—царга.
Рис. 10.5. Индивидуальная кольцевая топка:
/ — кольцевой дымоход; 2—реактор; 3—топка; центральный канал.
Все аппараты, предназначенные для обогрева конденсирую щимся водяным паром, могут быть, применены в качестве аппара
тов для охлаждения. |
И н д и в и д у а л ь н ы е |
топки. |
|
О г н е в о й |
о б о г р е в . |
Простейшими устройствами огневого обогрева являются индиви дуальные кольцевые топки (рис. 10.5) для твердого или жидкого топлива. Управление такими топками производится из помещения, отделенного от помещений реакторов огнестойкой перегородкой. Продукты сгорания поступают из топки 3 непосредственно под днище реактора 2, обогревают его и .через кольцевой дымоход 1 и боров выходят в дымовую трубу. Коэффициент полезного действия таких топок очень низок. В топках улучшенной конструкции топоч ные газы поступают сначала в кольцевой канал и обогревают стенки реактора и днище. Коэффициент полезного действия таких топок выше, так как обеспечивается более полное использование тепла топочных газов. При этом уменьшается напряжение поверх ности нагрева и, следовательно, вероятность прогорания днища реакторов.
313
6 |
5 |
4 |
Рис. 10.6. Схема централизованного обогрева:
/ —реактор; 2—шибера; 3—сборный боров; 4—топка; 5—дымосос; 6—дымовая труба.
Ц е н т р а л и з о в а н н ы й о б о г р е в . При централизован ном обогреве (рис. 10.6) группа реакторов 1 обслуживается одной топкой 4. Продукты сгорания топлива от топки к реакторам посту пают по центральному борову. .Отработанные газы собираются в сборном борове 3 и дымососом 5 удаляются через трубу 6 в ат мосферу. Регулирование температуры в реакторах осуществляется с помощью шиберов 2. Преимущества централизованного обо грева: улучшение управления топками, снижение температуры то почных газов и увеличение коэффициента полезного действия то пок. Недостатком централизованной системы обогрева является наличие длинных газоходов, через стенки которых неизбежны по тери тепла, что сказывается на показателях реакторов, располо женных на разных расстояниях от топки.
Кнедостаткам нагревательных устройств с применением
продуктов сгорания твердого и жидкого топлива можно от нести трудность регулирования технологического процесса, от носительную громоздкость топочных устройств, невысокий коэф
фициент полезного действия, |
сложность |
обслуживания и |
огне |
опасность. |
|
|
|
Г а з о в ы й о б о г р е в . В |
отличие от |
рассмотренных |
выше |
видов нагревательных устройств для твердого и жидкого топлива газовый обогрев реакторов имеет преимущество в возможности регулирования технологических процессов включением и выключе нием горелок или групп горелок. При газовом обогреве достигается более высокий коэффициент полезного действия, обслуживание реакторов несложно. К недостаткам газового обогрева можно от нести громоздкость топочных устройств и огнеопасность. Газовый обогрев применяется часто для топок котлов-парогенераторов при использовании высококипящих теплоносителей для обогрева реак торов.
зн
О б о г р е в э л е к т р и ч е с к и м током. При нагревании реакционной массы электрическим током применяют внутренние и наружные электронагреватели. Внутренние электронагреватели опускаются в реакционное пространство или служат для предва рительного нагревания реакционной массы в выносных теплооб менниках при непрерывном процессе. Наружные электронагрева тели располагаются на наружной поверхности реактора, при этом обычно монтируют несколько секций обогрева. Вокруг обмотки возникает переменное магнитное поле, индуцирующее в стенках реактора электродвижущую силу или вторичный ток, который, превращаясь в тепло, нагревает стенки реактора по всей толщине. К преимуществам применения электрического тока для нагревания реакторов следует отнести легкость регулирования технологиче ского процесса, небольшие размеры нагревательных устройств и обслуживания. Кроме того, обогрев электрическим током можно сочетать с другими видами обогрева.
О б о г р е в вы с о к о к и п я щ и м и т е п л о н о с и т е л я м и . Наибольшее применение для обогрева реакторов в производствах лаковых смол получила дифенильная смесь (ВОТ, даутерм, динил), которая представляет собой эвтектическую смесь дифенила (СбН5) 2 и дифенилоксида (СгНбЬО в соотношении 26,5 и 73,5%. Температура плавления дифенильной смеси 12,8 °С, температура кипения 258 °С. Эта смесь является стойкой к длительному нагре ванию (при 325°С — 4—5 лет, при 370°С — 2—3 года). Дифе нильная смесь горюча, однако не взрывоопасна, не агрессивна и малотоксична.
Схема работы установок для обогрева дифенильной смесью напоминает установки для обогрева парами воды. Котлом-пароге нератором могут служить обычные вертикальные двухбарабанные котлы. Система предназначается для централизованного обогрева нескольких реакторов. Различаются системы обогрева с принуди тельным и самотечным возвратом конденсата в котел-парогене ратор. Самотечные системы требуют высокого расположения реакторов — потребителей тепла. В качестве топлива для котловпарогенераторов лучше использовать газ или мазут. Получил рас пространение индивидуальный обогрев парами дифенильной смеси реакторов с удлиненными рубашками. Дифенильная смесь при газовом или электрическом обогреве испаряется непосредственно под реактором. Последнее время значительное распространение для обогрева реакторов получили высококипящие теплоносите ли — дикумилметан и тетраарилсиликат, которые благодаря высо кой температуре кипения (соответственно 336 и 426 °С) могут применяться в виде жидкости. Применение высококипящих тепло носителей дает возможность регулировать технологические процес сы, протекающие в реакторах; к другим преимуществам обогрева высококипящими теплоносителями можно отнести простоту обслу живания и экономичность процесса.
815
А п п а р а ту р а для см еш ен и я и р аств ор ен и я л аковы х см ол
Конструкция аппаратов для смешения и растворения лаковых смол определяется, главным образом, химическими свойствами смол и их способностью к растворению. Большое влияние на кон струкцию аппаратов оказывают размеры производственных поме щений и габариты здания. Аппараты для смешения и растворения
лаковых смол можно разделить на несколько типов: |
главным |
||
1) |
вертикальные смесители, которые |
применяются |
|
образом для растворения алкидных смол; |
растворения |
алкидных |
|
2) |
горизонтальные смесители для |
||
смол; |
|
|
|
3)вертикальные смесители для растворения смол и эфиров целлюлозы;
4)горизонтальные смесители для растворения эфиров целлю*
лозы;
5)турбомешатели.
Вертикальные смесители для алкидных смол. После синтеза в реакторах некоторых видов смол (типа алкидных) для их раство рения применяются вертикальные смесители цилиндрической фор мы со сферическим днищем и крышкой, снабженные водяной ру башкой и мешалкой. Мешалка может быть пропеллерной, турбин ной или якорной. В крышке смесителя располагаются штуцера для загрузки жидкого сырья, штуцер для присоединения к холодиль нику, штуцера для приборов температурного контроля и люк для профилактических осмотров и ремонта смесителя. Выгрузка сме сителя производится через штуцер в днище аппарата или, если по условиям монтажа это неудобно, через выгрузочную трубу, прохо дящую через крышку в нижнюю часть аппарата. Емкость смеси телей должна соответствовать емкости реакторов и составляет от 2 до 20 м3. В качестве материала смесителей могут быть исполь зованы: углеродистая, двухслойная или нержавеющая сталь.
Горизонтальные смесители для алкидных смол (рис. 10.7) так же применяются для растворения смол после их синтеза. Их уста навливают в тех случаях, когда по требованиям монтажа высота здания цеха должна быть умень шена. Смеситель представляет собой горизонтально расположен ный цилиндрический корпус с приваренными с торцов сфериче скими крышками. Для перемеши вания устанавливаются две мощ ные турбинные мешалки 6 или
Рис. 10.7. Горизонтальный смеситель:
/ — люк; 2—пробоотборник; 3- привод мешалки; 4—корпус смесителя; 5—гильза термопары; б—турбинная мешалка; 7—опора; 5—рубашка*
die
Рис. 10.8. Вертикальны!} смеситель для растворения смол и эфиров целлюлозы:
/— привод; 5—лапа; 3—лопастная мешалка; «/—от бойная планка; 5—корпус смесителя; б—рубашка.
. „ у f II II—^
циркуляционные насосы. В верхней ча сти смесителя расположены необходи мые штуцера (для загрузки жидких компонентов, для присоединения к хо лодильнику и термопаре 5), люки 1 для мешалок и люк для профилакти ческих осмотров и ремонта. Выгрузка производится через штуцера в нижней части аппарата или через выгрузочную трубу, проходящую сверху. Смеситель снабжается водяной рубашкой для охлаждения 8. Устанавливается сме ситель на опорах 7. Емкость смесите лей должна соответствовать емкости реакторов и составляет от 2 до 80 м3. Материал смесителей — нержавеющая или двухслойная сталь.
Вертикальные смесители для ра створения смол и эфиров целлюлозы. Для растворения смол и эфиров цел
люлозы применяют смесители цилиндрической формы со сфериче ским днищем, снабженные лопастными, якорными.или планетар ными мешалками (рис. 10.8). При применении лопастных мешалок на стенках аппарата предусматривают отбойные планки 4. Смеси тели снабжаются рубашкой 6 для подогрева содержимого смеси теля горячей водой или паром давлением до 0,2 МПа. В крышке аппарата предусматриваются штуцера: для загрузки жидкого сырья, инертного газа, для присоединения к холодильнику, для термопары и люк для загрузки сырья и чистки. В днище смесителя предусматривается выгрузочный штуцер с угловым вентилем. Ем кость смесителей — от 1 до 16 м3. Материал аппаратов — углеро дистая или нержавеющая сталь.
Горизонтальные смесители для растворения эфиров целлюлозы (малаксеры). Горизонтальные смесители для растворения эфиров целлюлозы (рис. 10.9) представляют собой цилиндрический корпус 4 с приваренными к нему с торцов сферическими крышками. Через ось аппарата проходит горизонтальный вал с насаженными на него лопастями 5. Аппарат крепится в наклонном положении к массив ной станине (раме) 1 из швеллеров, на которой также устанавли вается привод 2. Загрузка аппарата эфирами целлюлозы произво дится через люки 3, расположенные на верхней образующей кор пуса. В верхней части корпуса расположены штуцера для загрузки жидкого сырья, контрольно-измерительных приборов и других
$17
Рис. 10.9. Горизонтальный смеситель для растворения эфиров целлюлозы:
/ —опорная рама; 2—привод; 3—загрузочный люк; 4—корпус смесителя; 5—лопастная ме шалка; 6—штуцер для выгрузки; 7—рубашка.
целей. Выгрузка осуществляется через штуцер 6, расположенный в одном из днищ. Цилиндрическая часть корпуса аппарата снаб жена паровой рубашкой 7. Емкость аппаратов — от 1 до 6 м3. Ча стота вращения мешалки — 30—60 об/мин. Аппарат служит для приготовления высоковязких растворов эфиров целлюлозы (типа кабельных лаков). Материал аппарата — углеродистая сталь.
Турбомешатели применяются для интенсивного размешивания лаковых основ и синтетических смол при их растворении в смеси телях и для перемешивания пигментированных лакокрасочных ма териалов. Турбомешатели используются в стационарных и пере движных аппаратах. Турбомешатель представляет собой мешалку, сидящую на одном валу с мотором, без редуктора. На конце вала насажена турбина, вращающаяся в направляющем аппарате. Вдоль вала расположены съемные диффузоры, которые создают направленное движение перемешиваемой массы. При необходимо сти смешения пигментов со связующим предусмотрена воронка для загрузки пигментов. Отечественные смесители серии ТМ вы пускаются с диаметром турбинок от 70 до 180 мм следующих типов: ТМ-7, ТМ-11, ТМ-14, ТМ-15 и ТМ-18. Основные данные смесителя типа ТМ-14: диаметр турбинки— 110 мм; окружная скорость турбинки — 8 м/с, частота вращения турбинки — 1420 об/мин; мощность электродвигателя— 1,7 кВт. За рубежом применяются подобные типы турбомешателей («Ротамикс», «Уль трамикс») .
318
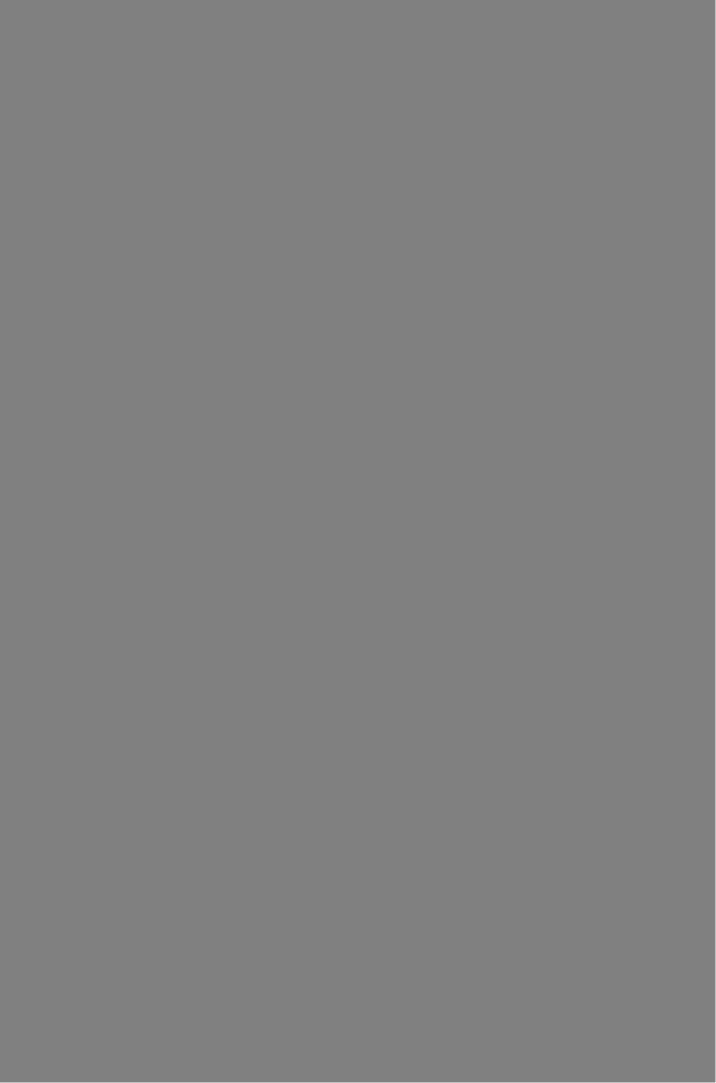
Рис. 10.11. Змеевнковый плавнтель канифоли:
корпус; 2—люк для загрузки канифоли; 3—штуцер для выпуска расплавленной кани фоли; 4—змеевики; 5—перфорированная предохранительная перегородка; 5—вентиляционный
отвод.
Рис. 10.12. Рубашковый плавитель фенола:
ячейка; 2—крышка; 3—барабан с фенолом; 4—вентиляционный воздуховод; 5—приямок; 5—.рубашка; 7—термоизоляция.
обогрева подается пар. Канифоль, соприкасаясь с горячими поверхностями кольев, постепенно плавится, и бочка опускается. Канифоль, выплавленная из бочки, собирается в конической части аппарата, откуда по обогреваемым трубопроводам поступает в мерники и реакторы. Освобожденная от канифоли бочка вынима ется из выплавителя. Кольевой выплавитель прост по устройству и несложен в эксплуатации. Материал выплавителя — углеродистая сталь.
З м е е в и к о в ы й п л а в и т е л ь к а н и ф о л и (рис. 10.11) служит для плавления кусковой канифоли, предварительно разби той на крупные куски. Он представляет собой цилиндрический аппарат с плоской крышкой и слегка наклонным плоским днищем. В крышке аппарата по его оси расположен конический люк 2 для загрузки канифоли (в кусках) и штуцера для пара и конденсата. В нижней части аппарата конически расположено несколько сек ций змеевиков 4. Канифоль падает на перфорированную перего родку 5, с которой сползает на змеевики, где расплавляется и стекает на дно аппарата. Расплавленная канифоль выводится че рез штуцер 3, который вварен в боковую стенку аппарата у самой нижней точки днища. На боковой образующей имеется вентиля ционный отвод 6. Корпус аппарата выполняется из углеродистой стали.
Плавитель фенола. Для плавления фенола применяются несколько конструкций аппаратов, работающих по разному прин-
820