
Добавил:
ivanov666
Опубликованный материал нарушает ваши авторские права? Сообщите нам.
Вуз:
Предмет:
Файл:книги / Порошковое материаловедение. Ч. 2
.pdf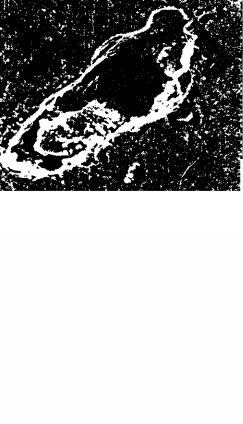
Рис. 151. Поверхность электрода после снятия анодной поляризационной кривой.
Язвенная коррозия
Рис. 152. Поверхность электрода после снятия анодной поляризационной кривой.
Питтинговая коррозия
Анализ факторов, влияющих на коррозионные свойства в изучаемых системах, позволяет сделать вывод о том, что структурные изменения, протекающие в поверхностных слоях при ЛТМ образцов с исходной пористостью, достаточны для увеличения коррозионной стойкости в случае равномерного растворения, но не влияют на устойчивость к локальным видам коррозии.
396
ELIB.PSTU.RU
Соседние файлы в папке книги