
книги / Порошковое материаловедение. Ч. 2
.pdfСопоставляя полученные данные, можно отметить, что одной из наиболее важных особенностей покрытий, оплавленных лучом лазера, является трещиноватость. Она выступает важной характеристикой технологической прочности покрытий, т.е. способности покрытий сопротивляться разрушениям в процессе лазерной обработки. В свою очередь технологическая прочность во многом определяет работоспособность покрытий в процессе эксплуатации.
Различают два основных вида технологической прочности:
−способность покрытия воспринимать термодеформационное воздействие при высоких температурах в процессе лазерной обработки без образования горячих трещин;
−формирование структуры и свойств покрытия на стадии охлаждения без образования холодных трещин в процессе фазовых и структурных превращений в твердом состоянии.
Горячие трещины – это хрупкие интеркристаллитные разрушения, возникающие в покрытии на фазе его затвердевания. Причина возникновения горячих трещин – высокие значения упругопластических деформаций, превосходящие мгновенную деформационную способность твердеющего материала покрытия. По современным представлениям, определяющей в процессе образования горячих трещин является упругопластическая деформация удлинения.
Механизм образования горячих трещин в покрытиях имеет следующие особенности. Являясь эвтектическим сплавом, материал самофлюсующегося покрытия характеризуется некоторым температурным интервалом кристаллизации, внутри которого сплав находится в твердожидком двухфазном состоянии. При кристаллизации в структурированной жидкости с переменным содержанием твердой фазы происходит специфическое изменение механических свойств сплава. В начальной стадии превалирует жидкая фаза, отдельные
361
ELIB.PSTU.RU
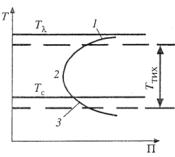
|
кристаллиты разъединены жид- |
||
|
кой прослойкой. Металличе- |
||
|
ская система в этом состоянии |
||
|
имеет высокую |
пластичность, |
|
|
степень которой |
определяется |
|
|
как свойствами жидкости (теп- |
||
|
лопроводностью, |
|
вязкостью, |
|
жидкотекучестью |
и |
др.), так |
|
и тепловыми особенностями ее |
||
Рис. 138. Зависимость пла- |
существования (температурны- |
||
стичности П сплава от тем- |
ми градиентами, гидродинами- |
||
пературы. Tλ – температура |
ческими явлениями, автоколе- |
||
ликвидуса, T – температура |
баниями и др.). Указанная осо- |
||
c |
бенность графически отражена |
||
солидуса |
|||
|
участком 1 на рис. 138. |
||
Увеличение соотношения объемов твердой |
и жидкой |
фазы, определяемое снижением температуры, ведет к формированию межчастичных мостиков, характеризующих начальную стадию образования скелетного каркаса. Гидродинамический напор циркулирующей жидкости в сочетании с высокими температурными градиентами обусловливает значительную локальную деформацию каркаса, что приводит к хрупкому интеркристаллитному разрушению по металлическим мостикам. На этой стадии пластичность покрытия падает до критически малых значений (участок 2, рис. 138). Дальнейшее снижение температуры стимулирует образование сплошного каркаса, определяющего повышение пластичности покрытия (участок 3, рис. 138). Характер разрушения на этой стадии изменяется от хрупкого интеркристаллитного до вязкого внутрикристаллитного. Следовательно, при лазерной обработке покрытий существует характерный температурный диапазон, в котором пластичность (вязкость) системы весьма мала, что обусловливает низкие значения прочности и пластичности покрытия на стадии оплавления.
362
ELIB.PSTU.RU
На рис. 138 указанный интервал обозначен как TТИХ (ТИХ – температурный интервал хрупкости) и характеризует наиболее вероятное разрушение покрытия в процессе его лазерного оплавления.
Дальнейший анализ механизма образования горячих трещин, проведенный А.Г. Григорьянцем для случая лазерной сварки, показывает, что вероятность их образования определяют три основных фактора: темп упругопластических деформаций при охлаждении расплава, значение ТИХ и минимальная пластичность Пmin сплава в диапазоне TТИХ. До-
полнительные исследования показывали, что с измельчением структуры металла в ходе лазерной обработки повышается сопротивляемость к образованию горячих трещин.
В оплавленных излучением лазера покрытиях на стадии охлаждения в области температур ниже точки превращений в твердой фазе, а также в течение длительного времени после обработки могут возникать трещины иного происхождения, определяемые в литературе как холодные.
Холодные трещины характеризуются замедленным разрушением, наблюдаемым при длительной постоянной или малоизменяющейся нагрузке. При этом сопротивление разрушению оказывается значительно ниже кратковременной прочности, что объясняется сдвигом зерен металла покрытия относительно друг друга под воздействием длительных напряжений. Границы зерен имеют пониженную сопротивляемость сдвигу по сравнению с телом зерна вследствие значительной неупорядоченности строения металла, высокой концентрации вакансий, дислокаций и других дефектов. В результате этого в вершинах зерен, где сходятся скользящие границы, может зарождаться трещина. Дальнейшее ее развитие может происходить как по границе, так и по телу зерна.
При лазерной обработке покрытий вследствие неравномерности нагрева и охлаждения, а также из-за структурных
363
ELIB.PSTU.RU
и фазовых превращений происходят упругопластические деформации и возникают остаточные напряжения. Если при этом деформационная способность металла покрытия и переходной зоны по границам зерен оказывается недостаточной, то остаточные напряжения релаксируют с образованием холодных трещин.
Анализ литературы показывает, что чаще всего холодные трещины возникают в результате фазовых и структурных превращений с образованием мартенсита, т.е. в результате полной или частичной закалки, а также под влиянием наводороживания. Закалочный механизм образования трещин реализуется вследствие γ→α-превращения аустенита в мартенсит, который характеризуется высокой твердостью, малой пластичностью и повышенным удельным объемом по сравнению с аустенитом.
Следует указать, что γ→α-превращение в стальных покрытиях обычно происходит при температуре 473–673 К, а в ряде случаев при лазерной обработке реализуется распад остаточного аустенита и при пониженных температурах (293–473 К). В связи с тем, что покрытия в исходном состоянии имеют повышенную структурную, фазовую и химическую неоднородность, происходит образование мартенсита закалки либо мартенсита отпуска на отдельных участках. Это обстоятельство обусловливает формирование остаточных напряжений, связанных с фазовым наклепом, неоднородно распределенных в объеме обработанного покрытия. Таким образом, возникают предпосылки для возникновения холодных трещин.
При обработке стальных и титансодержащих покрытий образование холодных трещин обусловлено влиянием водорода. Водород относится к числу газов, растворимость которых в сталях, титановых и других сплавах существенно возрастает при повышении температуры. Поэтому в процессе газотермического (в особенности плазменного и электроду-
364
ELIB.PSTU.RU
гового) напыления покрытий, а также в ходе их лазерной обработки в присутствии жидкой фазы в металле растворяется большое количество водорода, содержащегося в виде влаги в плазмообразующих и защитных газах, адсорбированных газах, микропорах и др. Значительное влияние оказывает термодиффузия водорода из менее нагретых участков в зону лазерной обработки. Водород в расплаве находится в атомарном виде и обладает высокой диффузионной способностью. При охлаждении покрытия уменьшается равновесная растворимость, поэтому его высокая концентрация в металле покрытия значительно превосходит равновесную растворимость. Вследствие этого водород диффундирует из расплавленных участков в соседние окружающие зоны, где скапливается в усадочных раковинах, микропорах, трещинах и других несовершенствах структуры. Атомарный водород
вэтих скоплениях переходит в молекулярный. Дальнейшее поступление атомарного водорода и его рекомбинация обусловливает повышение давления газа. Это приводит к созданию высоких неоднородно распределенных по объему покрытия напряжений, способствующих генерации холодных трещин. Кроме того, адсорбированный на поверхности металла водород вызывает его охрупчивание. В реальных случаях лазерной обработки покрытий образование холодных трещин вызвано действием обоих факторов – как фазового наклепа, так и наводороживания.
Анализ возможного воздействия лазерного излучения на технологическую прочность покрытий указывает на альтернативное влияние лазерной обработки, т.е. технологическая задача имеет экстремальное решение и подлежит оптимизации. Например, повышение скорости нагрева и охлаждения
взоне лазерного воздействия значительно уменьшает время пребывания металла при высоких температурах, что обусловливает значительное измельчение структуры и изменение характера кристаллизации, в результате чего возрастает
365
ELIB.PSTU.RU
гомогенность покрытия. Измельчение структуры способствует уменьшению степени химической неоднородности и понижению концентрации вредных примесей по границам кристаллов. При этом уменьшается вероятность наводороживания. Указанные факторы способствуют повышению сопротивляемости металла покрытия, образованию холодных трещин. Вместе с тем увеличение скорости нагрева и охлаждения определяет возрастание фазовых напряжений, что повышает вероятность образования холодных трещин.
Необходимо отметить, что в реальных случаях лазерной обработки покрытий определяющее влияние на технологическую прочность может оказать остаточная пористость напыленных покрытий. Так, если пористость термообработанного слоя не будет превышать 3–55 %, а поры имеют округлую форму и равномерно распределены в объеме покрытия, то сопротивляемость покрытия растрескиванию может возрастать ввиду увеличения работы раскрытия трещины в этих условиях. В то же время явления усадочного характера в оплавленном слое покрытия приводит к возрастанию остаточных напряжений. Отмеченные обстоятельства определяют исходную пористость покрытия ключевым фактором процесса его лазерной обработки.
Другое замечание касается особенностей преобразования переходной зоны системы покрытие – порошковая основа в ходе лазерной обработки. Дело в том, что в процессе напыления тонкий приповерхностный слой основы подвергается сильному термосиловому воздействию, что вызывает фазовые превращения материала подложки. Последующая лазерная обработка накладывает дополнительные изменения переходной зоны, связанные с термическими и диффузионными процессами, а также с инфильтрацией и механическим перемешиванием расплава в переходной зоне.
366
ELIB.PSTU.RU
9.2.Пути управления структурой
исвойствами порошковых материалов
Повышенная склонность порошковых сталей к коррозии, окислению, эрозионному и контактному износу вызывает необходимость их защиты и упрочнения. Наряду с методами ТО и ХТО в технологии порошковой металлургии используются методы пропитки, покраски их поверхности или эмалирование, электролитические покрытия [1, 2]. Существующие методы характеризуются недостаточной эффективностью упрочнения, высокой энергоемкостью, громоздкостью и сложностью оборудования, низкой степенью автоматизации и экологической безопасности, необоснованными затратами на дорогие и дефицитные легирующие материалы.
Как правило, наилучшие результаты по структуре и свойствам достигаются при совместной оптимизации режимов прессования, спекания и термообработки поликомпонентных сталей сложного химического состава. В то же время назначение и область применения порошковых материалов могут быть существенно расширены за счет разработки нетрадиционных методов модифицирования поверхности, основанных на использовании концентрированных потоков энергии, таких как плазма и излучение лазера.
Плазменное напыление оксинитрида кремния на пенистое основание из того же материала при низком давлении применяется для создания высокоэффективных обтекателей антенны радиолокаторов авиакосмической техники [3]. В патентах [4, 5] для снижения в 2–4 раза теплопроводности деталей из карбида и нитрида кремния предлагается покрывать их поверхность теплозащитным слоем из стабилизированного оксида циркония, нанесенного плазменным напылением.
Перспективным направлением упрочняющей обработки порошковых материалов является лазерное модифицирование поверхности.
367
ELIB.PSTU.RU
Среди исследований специфики ЛТМ порошковых материалов необходимо выделить работы школы Н.Н. Рыкалина [78–80], в которых детально проанализирована роль пористости в механизмах взаимодействия излучения с веществом. Установлено, что при импульсной обработке наличие пористости обусловливает следующие особенности:
−снижение затрат на нагрев, плавление и испарение вещества (в том числе объемного на готовых центрах) из-за уменьшения коэффициентов отражения излучения и температуропроводности основы с ростом пористости;
−увеличение параметров ЗЛВ за счет выделения свободной энергии пространства пор;
−возрастание доли удаленного вещества в ЗЛВ по механизму «выкалывания».
Наибольшее внимание исследователей уделяется изучению ЛТМ порошковых материалов на основе железа в целях повышения их поверхностных свойств (износо- и коррозионностойкости, жаростойкости и др.). Установлено, что лазерное борирование быстрорежущих сталей марок РОМ 23-МП повышает их твердость в 1,8 раз, а износостойкость – в 2,5– 4,5 раза по сравнению с объемной закалкой [6]. Лазерное легирование хромом спеченных железных изделий изучалось
вработе [7], ЛТМ порошковых конструкционных и инструментальных сталей – в работах [8, 9]. Установлено, что микротвердость зоны закалки из жидкости может быть как выше, так и ниже исходной; структура ЗТВ обладает значительной наследственностью, твердость ЗТВ выше твердости ЗО; горячая твердость резцов при 700 °С на 200–300 НV выше стандартной. Аналогичные зависимости улучшения долговечности при плоском изгибе установлены для спеченных сталей типа дисталоя и бондалоя [10].
Детальному исследованию лазерного упрочнения порошковой стали ЖГр0,5ДЗК0,3 посвящена работа [11], где установлено благоприятное влияние ЛТМ на гомогенизацию
368
ELIB.PSTU.RU
стали и ее упрочнение. В ходе ЛХТМ хромом и карбидом бора в структуре формируются упрочняющие фазы боридов железа и карбидов хрома, что обеспечивает твердость стали порядка 1400–1500 HV. При этом наблюдается значительное трещинообразование. Комплексное легирование стали карбидом титана и хромом обеспечивает повышение износостойкости в 200 раз относительно исходной и в 7 раз относительно нитроцементированной.
Необходимо отметить, что наилучшие результаты по структуре и свойствам порошковых сталей достигнуты при ЛТМ и ЛХТМ непрерывным излучением СО2-лазера [87]. В работах [88–90], в которых, по-видимому, впервые проведены исследования влияния лазерной обработки (импульсным и непрерывным излучением) на структуру и свойства порошковых углеродистых и легированных сталей, установлено, что в ходе ЛТМ непрерывным излучением поры концентрируются в приповерхностной зоне, а импульсным – преимущественно на границе раздела ЗО и ЗТВ. Показано, что ЛТМ позволяет получать литые поверхностные слои высокой твердости, обеспечивающие повышение износостойкости сталей от 2–5 до 17–70 раз в сравнении со спеченным состоянием.
9.3. Лазерное химико-термическое модифицирование порошковых сталей
В целях установления закономерностей формирования структуры, прочностных и триботехнических характеристик исследовано ЛХТМ порошковой стали СП60-2 из твердого и жидкого легирующего материла [12, 13].
Предварительная подготовка образцов (в виде прямоугольных призм размерами 6×6×40) проводилась по двум схемам:
– нанесением поглощающего покрытия двух видов (раствор коллоидного графита в этиловом спирте на силикатной
369
ELIB.PSTU.RU
связке и каменноугольный лак толщиной 30 и 130 мкм для каждого вида) с последующей просушкой на воздухе;
– предварительной пропиткой углеродсодержащими жидкостями двух видов (тетрахлорид углерода с выдержкой 24 ч, индустриальное масло И-45 с выдержкой 3, 4, 192 ч) при нормальных условиях.
Количество углерода в мартенсите после ЛХТМ исследовали на дифрактометре ДРОН-3 (СОα-излучение) по положению одной из линий мартенситного дублета [12] (вторая линия дублета [14] накладывается на линию α-Fе, получаемую при съемке попавших под рентгеновский пучок необработанных участков поверхности образца) и вычисляли с применением квадратичной формы для тетрагональной сингонии и известной методики Курдюмова определения межплоскостных расстояний в мартенсите. Количественное содержание остаточного аустенита исследовали методом РФА, микротвердость – на приборе ПМТ-3 при нагрузке 0,5 Н, триботехнические характеристики в условиях смазки – на машине трения СМЦ-2 при нагрузке 400 МПа и скорости скольжения образца по контртелу из закаленной стали Х12М, равной 1 м/с. Для сравнения исследовали образцы из стали СП60-2, обработанные аналогично, но без применения указанных способов лазерной цементации.
В ходе лазерной обработки без использования легирующих углеродсодержащих материалов исходная однородная ферритоперлитная структура поверхности образцов трансформировалась в две последовательно расположенные зоны различной структуры и фазового состава: зону оплавления (ЗО) и зону термического влияния (ЗТВ). Зона закалки из расплава представляет собой мартенсит, содержащий до 0,6 % углерода, и остаточный аустенит. Пористость ЗО снизилась до 4–5 %. Структура ЗТВ представляет собой смесь мартенсита, троостита и феррита.
370
ELIB.PSTU.RU