
- •1.Пальцевые зуборезные фрезы. Геометрические и конструктивные элементы.
- •2.Режимы обработки и качество поверхности при строгании и долбление.
- •3.Автоматизация проектирования для расчета круглой протяжки.(Привести блок-схему, или алгоритм)
- •4.Типы сменных наладок
- •5.Термическое и химико-термическое отделение цеха.
- •6. Нормирование оборотных средств.
1.Пальцевые зуборезные фрезы. Геометрические и конструктивные элементы.
Модульные фрезы – дисковые и пальцевые – характеризуются низкой производительностью и пониженной точностью. Это частный случай фасонных фрез с затылованными зубьями, поэтому большинство конструктивных элементов выбираются аналогично обычным затылованным фрезам.
Профиль зуба дисковой фрезы (или проекция пальцевой модульной фрезы на основную плоскость) при нарезании прямозубых колес в точности соответствует профилю впадины зубчатого колеса и состоит из рабочего участка ВЕ – отрезок эвольвенты и нерабочего участка ВО1, ограниченного переходной кривой (см. рис. 107).
Профиль эвольвентного участка ВЕ может быть определен графически, что наглядно, но неточно, или аналитически.
Определить эвольвенту – значит определить координаты любой точки М (x,y), лежащей на рабочем (эвольвентном) участке. Координаты любой точки x и y рабочего профиля (участка) фрезы (см. рис. 107):
;
.
Используя формулы определения параметров зубчатых колес, получим выражение для определения угла δx.Задаваясь рядом значений rx, получим координаты x и y.
радиан
– для некорригированных колес.
радиан
– для корригированных колес,
где:
z– число зубьев нарезаемого колеса;
ξ – коэффициент смещения исходного контура нарезаемого колеса;
–угол давления
на делительной окружности, угол зацепления
равен 20°;
invαx–
эвольвентная функция, равна (–
)
(или инволюта);
ΔSи
– утонение зуба по делительной окружности
для создания гарантированного зазора.
Рис. 107. Профиль зуба фрезы
Е
rx
ra
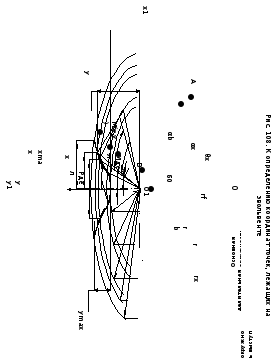
Чтобы определить
invαx,
необходимо определитьугол давления
αx.
Используя уравнение эвольвенты в
полярных координатах rx=
,
получим
.
Задаваясь рядом значенийrx,
и зная, что радиус основной окружности
,
получим ряд соответствующих значений
.
Для удобства построения профиля шаблона переносят начало координат в точку О1 (см.рис.108) и тогда
xшабл = x;
yшабл = y – rf,
где rf – радиус окружности впадин колеса.
Для определения
профиля рабочего участка зуба фрезы
находят ряд точек, что трудоемко, поэтому
разработаны таблицы, по которым быстро
определяются координаты точек профиля
зуба фрезы для нормального зацепления
с углом
= 20°, наиболее часто встречающимся в
промышленности [2].
Для точного
нарезания зубчатого колеса с данным
числом зубьев методом копирования
требуется отдельная фреза с особым
профилем, а для обеспечения нарезания
всех колес с числом зубьев от 12 до
теоретически нужно иметь бесконечное
число различных дисковых фрез.
Для уменьшения
ассортимента фрез применяют наборы из
8, 15, 26 фрез каждого модуля. Набор из 8
фрез применяют для нарезания колес
модулем
8
мм. Для колес больших модулем применяют
наборы из 15 или 26 номеров (табл. 13).
Каждая фреза из набора предназначена для нарезания ряда колес с определенным интервалом чисел зубьев. Расчет профиля зуба фрезы ведется по колесу с наименьшим числом зубьев обрабатываемого ряда колес: это исключает заклинивание зубьев колес. Если бы рассчитывали по максимальному числу зубьев из-за неточности профиля могло бы быть заклинивание зубьев.
Например, фрезой номер 6 из набора из 8 фрез можно нарезать колеса с числами зубьев z = 35 … 54 (определенного модуля), или z = 35 … 41 при наборе из 15 фрез.
Отсюда вытекает низкая точность нарезаемых колес (10…12 степени точности).
Таблица 13
Наборы фрез (модульных) по ГОСТ 10996–64
Набор |
Номер фрезы N | ||||||||||||||
1 |
|
2 |
|
3 |
|
4 |
|
5 |
|
6 |
|
7 |
|
8 | |
Из 8 фрез |
Число зубьев колеса | ||||||||||||||
12 … 13 |
|
14 … 16 |
|
17 … 20 |
|
21 … 25 |
|
26 … 34 |
|
35 … 54 |
|
55 … 134 |
|
135 … рейка | |
Из 15 фрез |
12 |
13 |
14 |
15 … 16 |
17 … 18 |
19 … 20 |
21 … 22 |
23 … 25 |
26 … 29 |
30 … 34 |
35 … 41 |
42 … 54 |
55 … 79 |
80 … 134 |
135 … рейка |
Дисковые модульные фрезы (рис.109)
Применяют для нарезания прямо– и косозубых цилиндрических колес с
модулем m = 0,3 до 45 мм; для прямозубых конических колес, зубчатых;
реек; шлицевых валов.
Различают:
Цельные и сборные
Черновые (γ = 5…10°) и чистовые (γ = 0°)
Быстрорежущие и твердосплавные.
Со шлифованным и нешлифованным профилем зуба.
Низкие производительность и стойкость дисковых фрез обусловлены:
малыми наружными диаметрами (от 50 мм до 180 мм );
малым числом зубьев (от 14 до 6);
нулевыми передними углами (для чистовой фрезы);
малыми задними углами на боковых сторонах зуба (1°20´…2°30´).
Повышение стойкости в 2… 3 раза можно получить, применяя сборные незатылованные (остроконечные) твердосплавные фрезы. Их применяют для модулей 6…30 мм. Можно получить 9 степень точности зуба нарезаемого колеса. По ГОСТ 1643–81 установлены 12 степеней точности по нормам точности:
кинематическая точность;
плавность работы;
контакта зубьев колес;
бокового зазора между нерабочими поверхностями.
Конструктивные
и геометрические элементы дисковой
модульной фрезы
Рис. 109. Общий вид дисковой модульной фрезы
Координаты рабочего (эвольвентного) участка зуба x и y.
Форма переходного (нерабочего) участка зуба (см.рис. 110).
Наружный диаметр D: 50;55;63;70;80;90;100;110;125;140;160;180; диаметр отверстия dотв: 19; 22; 27; 32; 40; 50;число зубьев:14; 12; 10.
Элементы шпоночной канавки – согласно диаметра отверстия dотв.
Элементы зуба и стружечной канавки в торцовом сечении (рис. 111).
– величина затылования,
–задний угол при
вершине.
= 10…12°, но чтобы
был обеспечен задний угол на боковых
сто-ронах профиля αб
не менее 2°30´:
,
где
– угол между касательной к профилю в
точке и осью, перпен-дикулярной оси
фрезы (см. рис. 112).
H = h + К + r – высота зуба (глубина стружечной канавки) – для фрез с нешлифованным профилем зуба;
где h = 2,25m – высота фрезеруемого слоя;
r – радиус закругления дна стружечной канавки;r = 1…5 мм.
θ – угол стружечной канавки – назначают исходя из прочности зуба:
θ = 18; 22; 25; 30°.
6. Ширина фрезы В:
В = 2Х max + (2…3)
После расчета элементов зуба рекомен-дуется произвести прочерчивание фрезы в масштабе. Проверяют, чтобы:
а) Толщина тела l в опасном сечении над шпонкой должна быть равна (см. рис. 109):
l ≥ 0,35 dотв;
б) Ширина зуба у основания С:
С ≥ 0,75 H(см. рис.111)
Перетачивание зуба – по передней поверхности.
Рис.
110. К определению нерабочего участка
зуба фрезы
r
k
Н
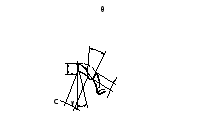
Рис. 111.Форма зуба и стружечной канавки
y
y
а-а
Зуборезные
инструменты, работающие по методу обката
Цилиндрические колеса (прямо- или косозубые) методом обката нарезают назубофрезерных, зубодол-бежных, зубострогальных и специальных станках.
а
а
В соответствии с этим исполь-зуют режущие инструменты: червячные фрезы, долбяки, зуборезные гребенки, резцы-летучки.
При
методе обката заготовка и инструмент
находятся в сопря-женном зацеплении
как колеса зубчатой пары; при этом
нача-льные окружности инструмента и
нарезаемого колеса должны перекатываться
друг по другу без скольжения, т.е.
начальные окружности
одновременно являются и делительными,
т.е. такими, на которых
и
колеса равны
и
инструмента.
Профиль зуба нарезаемого колеса получают как огибающую последовательных положений режущих кромок инструмента. При этом инструмент работает тремя режущими кромками на каждом зубе: одной – на вершине зуба и двумя на боковых сторонах: ВС – вершинная кромка зуба; АВ и СD – боковые кромки зуба (см. рис. 113).
Рис. 113. Режущие кромки зуба
Существенным недостатком инструментов, работающих методом обката, является неравномерность нагрузки на режущие кромки, т.е. схема резания такова, что вершинная кромка (ВС) срезает наиболее толстый слой, тоньше срезает боковая входная кромка и самый тонкий слой срезает выходная кромка. Это приводит к тому, что износ зубьев по передней и задней поверхностям происходит неравномерно.
Этот недостаток можно исправить конструктивно. Например, у червячных фрез выполняют различными по высоте зубья: четные зубья имеют заниженную высоту и режут только боковыми кромками, нечетные имеют нормальную высоту и режут всеми режущими кромками, причем вершинные кромки срезают слои в два раза толще по сравнению со стандартной фрезой.
Стойкость таких фрез увеличена. Однако усложняется техпроцесс изготовления фрез, что ведет к повышению их стоимости.
Еще одним недостатком инструментов, работающим методом обката, является огранка (отклонение профиля зуба от эвольвенты) вследствие чего шероховатость поверхности (обработанной) в ряде случаев высокая (см. рис. 114) I – первое положение зуба инструмента; II – второе положение зуба инструмента.
Рис.114. Огранка
Величина огранки f = 0,003 … 0,004 мм и ею пренебрегают.
Увеличение числа
заходов увеличивает огранку, т.к.
уменьшает число резов. Волнистость,
т.е. высота гребешков по дну впадины
или по боковой стороне
(на рис. 115 условно не показана) равна:
[1]
ось колеса
I положение фрезы
II положение фрезы
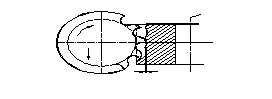
Рис.115. Схема образования волнистости
ff
S
,
,[1]
где:
–продольная
подача фрезы на один оборот;
–угол наклона
зубьев;
–угол зацепления.
Количество резов
увеличивается при повышении числа
зубьев фрезы
;
повышении числа зубьев колеса
;
с уменьшением угла профиля (зацепления)
;
с уменьшением числа заходов
.