
- •1.1.2.1. Мембраны на основе аморфного SiO2
- •1.2. Структура пористых материалов
- •1.2.2.2. Классификация пор по месту нахождения
- •1.3.1. Влияние состава шихты на необходимые технологические условия и свойства подложек
- •1.3.3. Добавки
- •1.5. Выводы
- •2.2. Обоснование выбора состава и технологических параметров производства подложек
- •2.3.2. Определение точки пузырька по ГОСТ 50516-93 и распределения пор по размерам
- •2.3.4. Исследование подложек методом сканирующей электронной микроскопии (СЭМ, SEM)
- •2.4.3.3. Определение точки пузырька и распределения пор по размерам
- •2.4.3.5. Исследование подложек методом сканирующей электронной микроскопии
- •2.5. Выводы
- •3.2. Опасные и вредные факторы на основных стадиях работы
- •3.3. Токсикологическая характеристика сырья и реагентов
- •3.3.1. Корунд
- •3.3.3. Поливиниловый спирт (ПВС)
- •3.4. Режим личной безопасности
- •3.5. Производственная санитария
- •3.5.3. Метеоусловия
- •3.7. Техника безопасности
- •3.8. Пожарная профилактика
- •3.8.1. Категорирование помещений лаборатории по пожаровзрывоопасности
- •4.2. Задачи экономического исследования
- •4.4. Расчет затрат на дипломную научно - исследовательскую работу
- •4.6. Выводы:
- •5. Охрана окружающей среды от промышленных загрязнений
- •5.1. Введение
- •5.2. Экологическое обоснование темы работы и предполагаемых технологических решений
- •5.3. Экологическое обоснование разработанной технологической схемы
- •5.4. Токсикологическая характеристика сырья и реагентов
- •5.5. Охрана водоёмов от загрязнения сточными водами
- •5.7. Экономическая оценка природоохранных мероприятий
- •Список литературы
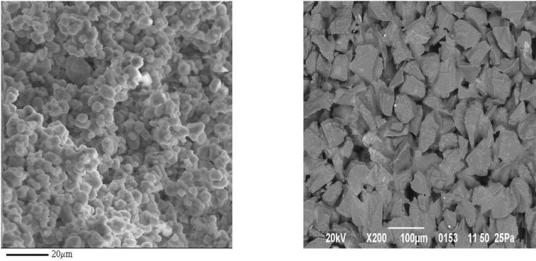
Рисунок 1.10 - Микроструктура пористой проницаемой керамики из узкофракционированных порошков,
а – прямой контакт частиц порошка друг с другом, б – контакт частиц порошка через связку [28].
В большинстве случаев условия эксплуатации изделий таковы что с точки зрения экономики целесообразно использовать изделия с микроструктурой приведённой на рисунке 1.10б. Для создания керамики с такой микроструктурой применяют порошок наполнителя и связку (тонкомолотый и \ или легкоплавкий компонент). В качестве связки обычно используют пластичные огнеупорные или тугоплавкие глины, бентонитовые глины а также некоторые другие материалы [29].
Выводы:
• использование шихты, состоящей из наполнителя и связки, приводит к удешевлению мембран.
1.3.1. Влияние состава шихты на необходимые технологические условия и свойства подложек
В работах [30, 31] использовали шихту состоящую из 40 масс. % корунда (2 - 4 мкм) и 60 масс. % зёрен спёка на основе муллита (50 - 100 мкм) и 2 % cмеси MgO и SiC сверх 100 % (2 мкм), обжигали до пористости 29 % и прочности 300 МПа при температуре 1500 °C, кроме того для получения спёка на основе муллита понадобился дополнительный обжиг при 1600 °C. Использование такой шихты
23
приводит к очень высоким значениям прочности, однако, материалы, полученные с их использованием, имеют относительно высокую себестоимость.
Вработе [32] использовали шихту состоящую из 73 % корунда F-600 (10 мкм)
и27 % золя SiO2 (2 - 4 мм) обжигали до пористости 47 % и прочности 25,8 МПа, при температуре 1400 °C и выдержкой в течении четырёх часов. Использование такой шихты приводит к высоким значениям пористости, однако, материалы, полученные с их использованием, имеют существенную себестоимость.
Вработе [33] использовали шихту состоящую из 60 % Al2O3 (2 - 3 мкм) и 40 % SiC (80 - 100 мкм) с тонкомолотой (5 мкм) упрочняющей добавкой — 2 % сверх 100 % и выгорающей добавкой 25 % сверх 100 %. Обжигали до пористости 39,9 % и прочности 60 МПа при 1580 °C и выдержке в течении 2 часов. Использование такой шихты приводит к высоким значениям пористости, и повышенным значениям прочности, однако, материалы, полученные с их использованием, имеют относительно высокую себестоимость.
Выводы:
•для получения образцов при низких температурах обжига, в качестве связки следует применять компонент, благодаря которому образуется жидкая фаза, что приводит к переходу от твёрдофазного спекания к жидкофазному;
•для того, чтобы уменьшить количество загрязнителей шихты, приводящих к ухудшению коррозионной стойкости, в качестве компонента образующую жидкую фазу, следует использовать огнеупорную глину.
1.3.2. Влияние зернистости заполнителя на характеристики подложек С целью изучения влияния размера зёрен заполнителя на основные физико-
технические свойства керамики, в работе [34] использовали для её получения электрокорунд со средним размером частиц соответственно 5, 20, 63 и 120 мкм, обжиг при температуре 1500 °C с выдержкой при максимальной температуре 2 ч результаты свели в таблицу 1.1.
24
Таблица 1.1 - Свойства пористой керамики на основе Al2O3 [34].
Размер зёрен |
Давление |
Линейная |
Открытая |
Средний |
Предел |
Газопрони- |
электрокорунда |
прессования, |
усадка, |
пористость, |
размер пор, |
прочности при |
цаемость, |
мкм |
Н/мм2 |
% |
% |
мкм |
изгибе, Н/мм2 |
мкм2 |
|
|
|
|
|
|
|
120 |
100 |
1,2 |
34,0 |
4,5 |
105 |
0,13 |
|
|
|
|
|
|
|
63 |
100 |
4,5 |
33,3 |
3,8 |
110 |
0,10 |
|
|
|
|
|
|
|
20 |
100 |
5,4 |
30,5 |
3,1 |
125 |
0,09 |
|
|
|
|
|
|
|
5 |
100 |
11,3 |
19,0 |
2,2 |
195 |
0,03 |
|
|
|
|
|
|
|
Керамика с размером зёрен электрокорунда от 20 до 120 мкм имеет достаточно высокую механическую прочность, но размер пор, изменяющийся от 3.1 до 4,5 мкм, слишком велик, чтобы использовать этот материал в качестве фильтра для разделения газовых смесей. Керамический материал на основе электрокорунда с размером зерен 5 мкм вследствие небольшого среднего размера пор (около 2 мкм) и относительно невысокой пористости (19 %) характеризуется пониженной газопроницаемостью, составляющей 0,03 мкм2, и превосходит керамику из более крупнозернистых масс по механической прочности, поэтому перспективно его использование для фильтров.
Выводы:
•использование электрокорунда с размером зёрен менее 5 мкм приводит к сильному ухудшению газопроницаемости по причине уменьшающегося размера пор, приводящего к увеличению гидравлического сопротивления;
•применение электрокорунда с размером зёрен более 20 мкм ухудшает прочность, по причине уменьшающегося количества контактов между зёрнами.
1.3.3.Добавки
Для повышения прочности, термической и химической стойкости при сохранении проницаемости, пористости и распределения по размерам пор в шихту, из которой будет получена корундовая мембрана можно добавить смесь порошков карбида кремния и одного из оксидов из ряда CaO, MgO, MnO, NiO, ZnO при
25
соотношении SiC:MeO, равном 2:1, при следующем соотношении компонентов, масс. %: Al2O3 95 - 99; смесь порошков SiC и одного из оксидов из ряда CaO, MgO, MnO, NiO, ZnO (при соотношении SiC:MeO 2:1) - 1 — 5. Предлагаемый состав
шихты обеспечивает |
получение пористой |
прочной и термостойкой |
керамики. |
||
Пористость изделий |
составляет 25 - 45 %, прочность |
на изгиб |
85 - 150 МПа, |
||
термостойкость более |
30 теплосмен при |
термоударах |
1200 °C |
— |
вода. [35]. |
В некоторых случаях для повышения качества мембран вводят добавки обладающие особым влиянием на структуру [36], например:
• использование |
в качестве |
фракционированного наполнителя веществ |
||
с природной формой |
частиц, имеющих |
высокую |
плотность, окатанную форму |
|
с минимальной шероховатостью. |
Это |
приводит |
к снижению гидравлического |
сопротивления фильтруемой среды и повышению проницаемости;
• введение добавок, увеличивающих объём при фазовых переходах, увеличивает открытую и проницаемую пористость.
В работе [37] для получения фильтров исследовали влияние выгорающих добавок на пористость в корундовой мембране. Керамическую основу готовили из порошков оксида алюминия марки Alcoa CT3000SG с D50 = 0,7 мкм с добавлением крахмала, в качестве порообразователя, что после термообработки при 1300 °C вызвало образование пористости 40 % из которых открытых пор 87 %. В отсутствие порообразователя пористость была только 25 % с 49 % открытых пор.
1.4. Формование заготовки Наиболее распространённые методы формования керамических подложек для
мембран — полусухое прессование и экструзия.
При экструзии в образце появляется анизотропность и некоторая текстура, выраженная в том, что в объеме образуются каналы параллельно направлению истечения материала или каверн от скопления влаги в энергетически благоприятных
зонах, расположенных в объеме крупных |
фракций, которые практически |
не работают при истечении фильтрата |
в направлении, перпендикулярном |
26