
- •ВВЕДЕНИЕ
- •1. ВЫПОЛНЕНИЕ ЭСКИЗОВ ДЕТАЛЕЙ МАШИН
- •1.1. Общие сведения
- •1.2. Последовательность выполнения эскиза
- •2.3. Расчет и эскизирование конических зубчатых колес
- •4. СТАНДАРТИЗИРОВАННЫЕ ЭЛЕМЕНТЫ
- •4.1. Нормальные линейные и угловые размеры
- •4.2. Резьбы
- •4.3. Радиусы закруглений и фаски
- •4.4. Центровые отверстия
- •4.5. Рифления прямые и сетчатые
- •4.6. Шпоночные соединения
- •4.8. Канавки для выхода шлифовального круга
- •4.9. Штифтовые соединения
- •4.10. Лыски, квадраты, шестигранники
- •4.11. Сальниковые уплотнительные кольца
- •4.12. Материалы, применяемые для изготовления деталей
- •5. ОБОЗНАЧЕНИЕ ШЕРОХОВАТОСТИ ПОВЕРХНОСТЕЙ
- •5.1. Параметры шероховатости поверхностей
- •5.2. Правила обозначения шероховатости поверхностей
- •5.3. Правила нанесения обозначений шероховатости на чертеже
- •ВОПРОСЫ ДЛЯ САМОПРОВЕРКИ
- •ЗАКЛЮЧЕНИЕ
- •БИБЛИОГРАФИЧЕСКИЙ СПИСОК
- •ОГЛАВЛЕНИЕ
1. ВЫПОЛНЕНИЕ ЭСКИЗОВ ДЕТАЛЕЙ МАШИН
1.1. Общие сведения
Эскизом называется конструкторский документ, выполненный от руки (без применения чертежных инструментов) на любой бумаге в глазомерном масштабе, но с соблюдением пропорций в размерах отдельных элементов и всего изделия.
Эскизы – это временный конструкторский документ, используемый на стадиях организации производства, разработки, эксперимента, изобретательства, усовершенствования существующих изделий. По ним изготовляют изделия при ремонте, в опытном производстве. Если эскиз предполагают использовать многократно, то по нему выполняют чертеж.
Эскиз требует такого же тщательного выполнения, как и чертеж. Несмотря на то, что эскиз выполняется от руки и в глазомерном масштабе, размеры, проставляемые на нем, должны соответствовать действительным размерам детали.
При выполнении эскиза соблюдаются все правила, установленные стандартами ЕСКД.
1.2. Последовательность выполнения эскиза
Выполнение эскиза условно можно разделить на два этапа: подготовительный и основной – включающий в себя вычерчивание изображений; нанесение размеров и знаков шероховатости поверхностей деталей; выполнение необходимых надписей и окончательное оформление эскиза.
1.2.1. Подготовительный этап
На подготовительном этапе нужно внимательно осмотреть деталь, уяснить ее конструкцию, назначение, технологию изготовления. При изучении конструкции надо тщательно проанализировать форму детали: определить имеющиеся в ней отверстия, канавки, проточки, приливы, выступы, фаски и другие элементы, мысленно расчленить деталь
4

на простейшие геометрические формы (цилиндр, конус, призма и др.), определить, как эти формы связаны между собой, собраны воедино.
Затем нужно установить материал, из которого деталь изготовлена, и основн ые технологиче кие операции (резание, штамповка, литье и т. д.), которые использовались ри изготовлени и детали. Если возможно, то устанав ивают, частью какого изделия является данная деталь, каково ее назначение в этом из елии.
Определяют, какие виды, разрез ы или другие из бражен ия, дополняющие г авное изображение, необходимые для полного выявления конструк ции детали, целесообраз о выпо нить (рис. 1). Изображени на эскизе, как и на чертеже, могут быть увеличены или уменьшены по сравнению с натуральными. Согласно ГОСТу 2.305 –2008 количество изображе ий дол жно быть миним альным, но достаточным для перед ачи форм детали.
Рис. 1 Изображение эскизируемой детали
Затем приступаю т к выбору главного изображения детал , учитывая некоторые требования констр ктивного и технологического порядка. Главное изображение должно давать наибольшую ин ормацию о форме етали.
Форма деталей определяется не только к нструкцией, но технологией их изготовления, и несет в себе элем нты, характерн е для этой технологии. Например, у литых деталей имеются литейные уклоны и скругления, у деталей токарной обработки преобладаю щими являются поверхности вращен ия. Это отдельные детали машин, наприм р маховики, шк вы, цилиндры, крышки, рычаги, это детали типа опор, кронштейнов; корпусные коробчатые детали закрытого или открытого типа.
5
Корпусные детали коробчатого типа располагают относительно фронтальной плоскости проекций так, чтобы их основные базовые поверхности занимали горизонтальное положение, а детали типа фланцев или шкивов – так, чтобы их ось проецировалась параллельно основной надписи чертежа, поскольку такое их расположение соответствует положению детали при ее токарной обработке.
Детали, изготавливаемые токарной обработкой, преобладающими имеют поверхности вращения. Для них, а также для деталей типа валов и втулок с резьбой достаточно одного изображения. Если на таких деталях имеются отверстия, срезы, пазы, то главное изображение дополняют одним или несколькими видами, разрезами, сечениями, которые выявляют форму этих элементов, а также выносными элементами.
Для тонких плоских деталей любой формы достаточно одного изображения.
Главный вид детали выбирают с учетом технологии ее изготовления. Планки, линейки, валики, оси и т. п. рекомендуется располагать на формате горизонтально, а корпуса, кронштейны и т. п. – основанием вниз.
Если деталь сложной конструкции и в процессе изготовления не имеет заведомо преобладающего положения, то за главное изображение таких деталей принимают их расположение в готовом изделии – приборе, машине.
Для деталей типа шкивов, колес главным изображением является фронтальный разрез. Его выполняют полностью, что облегчает нанесение размеров.
Детали типа винтов, болтов, валиков изготовляют на токарных станках или автоматах. Их ось при обработке горизонтальна. При изображении таких деталей на эскизе учитывают также положение, в котором выполняют наибольший объем работ по изготовлению детали, т. е. выполняют наибольшее число переходов (переход – обработка одной элементарной поверхности).
Учитывая сложность детали и ее размеры, выбирают размеры листа бумаги в соответствии с ГОСТом 2.301–68, решают вопрос о выборе приблизительного масштаба изображения, чтобы рационально использовать рабочую площадь эскиза. Изображение должно быть таким, чтобы не затруднялись чтение эскиза и простановка размеров.
6
1.2.2. Порядок выполнения эскиза детали с натуры
Выбрав размер формата, наносят внутреннюю рамку и намечают место под основную надпись (рис. 3).
Выбрав приблизительно масштаб изображений, необходимо наметить размещение видов на чертеже с помощью габаритных прямоугольников так, чтобы изображение было равномерно распределено по формату (рис. 3).
Затем нужно построить изображение видов, предварительно нанеся осевые и центровые линии, если это необходимо (рис. 4). И наконец, вычерчиваются выбранные разрезы и сечения (рис. 5).
Проверив выполненные изображения, необходимо убрать лишние линии, выполнить штриховку в разрезах и сечениях по ГОСТу 2.306–68, обвести видимый контур изображений сплошной толстой линией (рис. 6).
Далее намечают размерные базы и проводят выносные и размерные линии для габаритных размеров, межосевых и межцентровых размеров и их расстояний до баз и для размеров отдельных элементов деталей (рис. 6). Нанесение размеров на чертеже регламентируется ГОСТом 2.307–2011.
Затем деталь обмеряют и сопоставляют полученные размеры с размерами, рекомендуемыми таблицами размерных рядов. На эскиз наносят размеры скорректированные, но близкие к измеренным. При этом нужно помнить о сопрягаемых размерах, которые могут быть проверены и уточнены по сопрягаемым с данной поверхностью деталям в готовом изделии. Для определения действительных размеров деталей пользуются различными измерительными инструментами: металлической линейкой, угломером, штангенциркулем, нутромером и др.
Необходимо учитывать, что стандарты позволяют на единой основе разрабатывать размерные ряды для самых разнообразных изделий и их составных частей (не только в машиностроении и приборостроении, но и во многих других отраслях народного хозяйства), удовлетворяющие требованиям взаимозаменяемости, заимствования, стыковки и многим другим. Поэтому размерные числа, определяемые путем обмера деталей при выполнении учебных эскизов или чертежей, необходимо согласовывать с числами, рекомендуемыми ГОСТом 6636–69 и ГОСТом 8908–81.
7

Полученные размеры наносят над соответствующими размерными линиями (рис. 8). Размерные числа рекомендуется записывать сразу после каждого измерения, не накапливая их в памяти.
Далее определяют шероховатость поверхностей детали и наносят ее на эскиз условными обозначениями, как и разрезы, сечения, выносные элементы.
В заключение необходимо проверить выполненные изображения, устранив ошибки и погрешности, заполнить технические требования, а также таблицы, если они необходимы (рис. 9).
Затем нужно заполнить основную надпись. Формы, размерыи порядок заполнения основной надписи и дополнительных граф к ней в чертежах, схемахитекстовыхдокументахустанавливаетГОСТ2.104–2006.
Содержание, расположение и размеры граф основной надписи, дополнительных граф к ней, а также размеры рамок на чертежах должны соответствовать форме 1 (рис. 2) указанного выше ГОСТа.
Рис. 2. Основная надпись, форма 1
Так как эскиз выполняется в глазомерном масштабе, графу 6 («Масштаб») основной надписи не заполняют.
8

9
Рис. 3 Разметка формата габаритными прямоугольниками
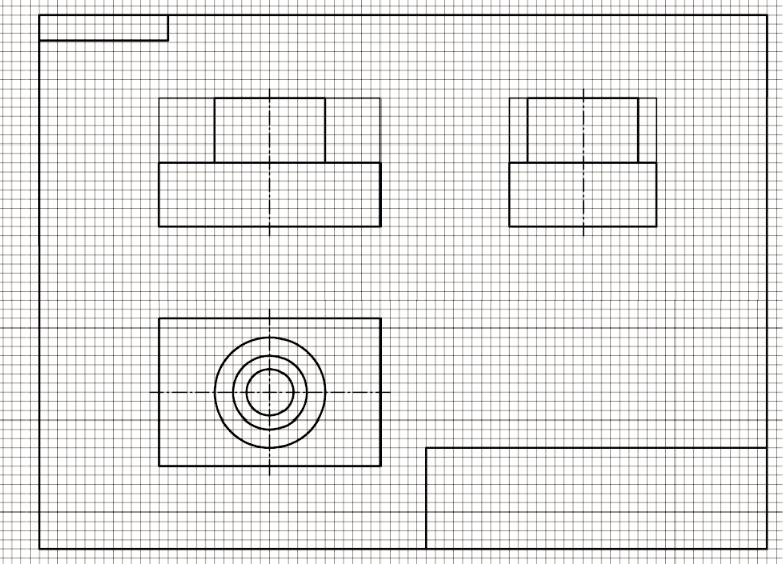
10
Рис. 4. Построение изображения видов внутри габаритных прямоугольников

11
Рис. 5. Построение изображения внутренних поверхностей детали

12
Рис. 6. Удаление лишних линий, штриховка и обводка изображения

13
Рис. 7. Нанесение размерных линий

14
Рис. 8. Нанесение размерных чисел
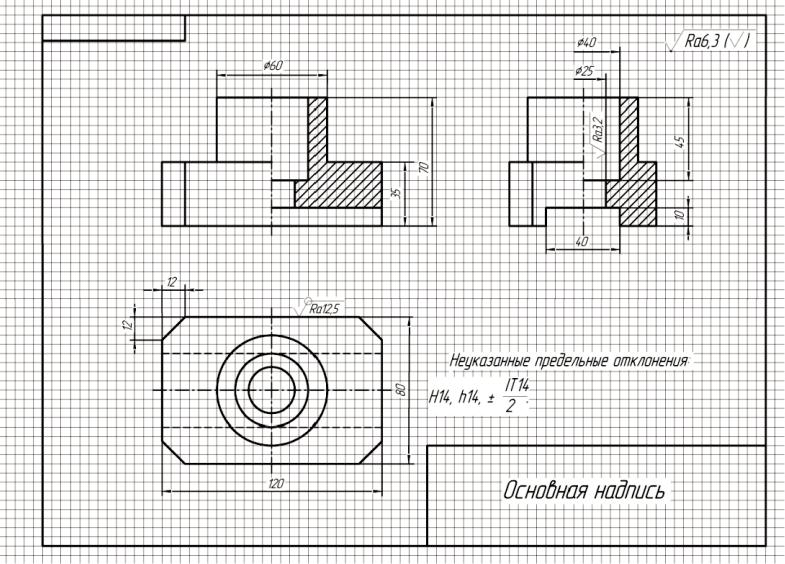
15
Рис. 9. Нанесение шероховатости, заполнение технических требований и основной надписи

1.2.3. Особенности выполнения эскиза литой детали
В машиностроении литые детали нашли очень широкое применение, это, например, отдельные детали машин (маховики, шкивы, цилиндры, крышки, рычаги), детали типа опор, кронштейнов; корпусные коробчатые детали закрытого или открытого типа, имеющие точно обработанные отверстия и плоские наружные поверхности.
Общее количество изображений на эскизе или чертеже литой детали во многом зависит от правильного выбора главного вида, от рационального сочетания видов с разрезами, выполнения местных разрезов, сечений, выносных элементов, условностей и упрощений.
При выполнении эскизов и чертежей литых деталей необходимо придерживаться следующих требований:
–литейные уклоны на чертеже не изображают, а делают соответствующую запись в технических требованиях;
–для того чтобы деталь не имела внутренних напряжений и литейных дефектов, нужно осуществлять плавный переход от одной толщины стенки к другой.
Например, если отношение толщин стенок S/S1 ≤ 2, то переход осуществляется с помощью скруглений радиусом R = (0,3...0,4)h, как показано на рис. 10;
Рис. 10. Изображение плавного перехода от одной толщины стенки к другой, когда S/S1 ≤ 2
если отношение толщин стенок S/S1 > 2, то переход осуществляется с помощью уклона длиной l = (4...5)h, как показано на рис. 11;
Рис. 11. Изображение плавного перехода
от одной толщины стенки к другой, когда S/S1 > 2
16

–опорные бурты (фланцы) должны быть толще основной части детали и должен быть предусмотрен плавный переход от стенки к фланцу, как показано на рис. 12, а;
–обрабатываемые поверхности нужно располагать над необрабатываемыми (рис. 12, б), т. к. это обеспечит свободный выход режущему инструменту и уменьшит площадь механической обработки;
а б
Рис. 12. Изображение литой детали с буртом (фланцем) (а)
иобрабатываемой поверхностью (б)
–если плита-основание устанавливается на другую деталь, то привалочную плоскость делают несплошной, чтобы уменьшить площадь обработки, как показано на рис.13;
Рис. 13. Изображение литой плиты-основания
– поверхности, в которых сверлят отверстия, выполняют с приливами, торцевые плоскости которых должны быть перпендикулярны оси отверстия.
При выполнении эскиза или чертежа литой детали необходимо выбрать основные литейные и конструкторские базы. Литейными ба-
17

зами могут служить оси или плоскости симметрии или необрабатываемые поверхности. От литейных баз наносят размеры, определяющие форму и положение необрабатываемых поверхностей. Отдельно наносят размеры, определяющие форму и положение обрабатываемых поверхностей относительно конструкторских баз.
Рис. 14. Изображение приливов на литых деталях для выполнения отверстий
При нанесении размеров на эскизы и чертежи литых деталей нужно учитывать следующие особенности:
–взаимное положение необрабатываемых поверхностей детали указывают размерами, которые связывают эти поверхности между собой;
–механически обработанные и необрабатываемые поверхности связывают между собой не более чем одним размером по длине, высоте или глубине детали.
Размеры на эскизах и чертежах литых деталей не допускается наносить в виде замкнутой цепи. На рабочем чертеже (эскизе) литой детали должны быть помещены технические требования. На учебных чертежах в технических требованиях можно ограничиться только указанием размеров неуказанных литейных радиусов и размеров для справок.
Пример выполнения эскиза литой детали приведен на рис. 15.
18
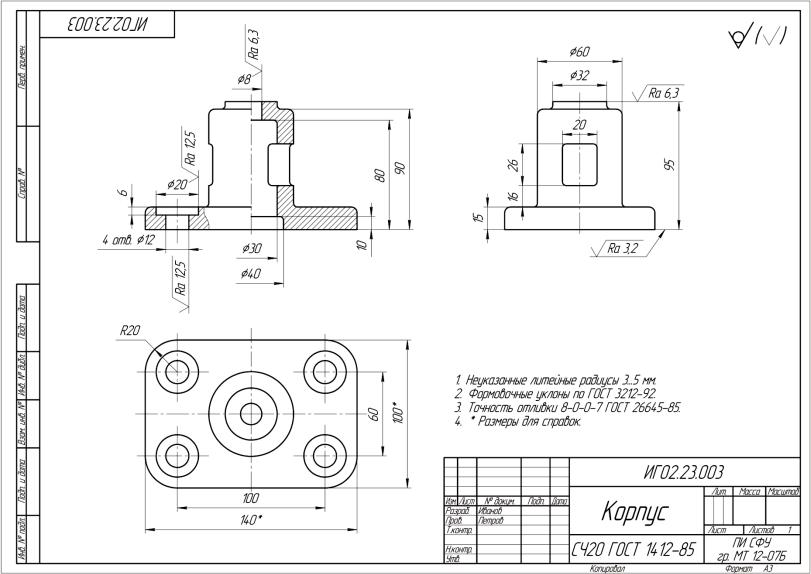
19
Рис. 15. Эскиз литой детали
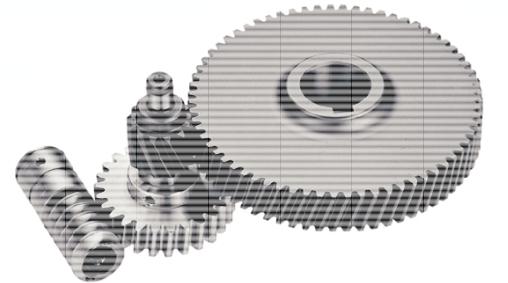
2.ВЫПОЛНЕНИЕ ЭСКИЗА
ЗУБЧАТОГО КОЛЕСА
2.1. О щие сведения
Зубчатые передачи широко используют в машинах, ста ках и механизмах для передачи вра щательн го движения от одного вала к другому.
Рис. 16. Детали зубчатой и червячной передач
Зубчатая передача состоит, как правило, из двух колёс, на поверхности которых чередуются впадины и выступы – зубья. Принцип работы передачи основан на зацеплении зубчатых колёс, когда зубья одного из них входят во впадины другого (рис. 16). Вращательное движ ние от одного колеса к другому передаётся за счёт давления зуба од ного колеса на зуб другого.
Эскизы как и рабочие чертежи зубчатых передач и их деталей) долж ны выполняться по правилам, установленными Государственными стандартами ЕСКД.
Терминология, определения и обозначения элементов зубчатых передач даны в ГОСТе 1653 –83 и Г ОСТе 16531–83, их условные изображения на черт жах – в ГОСТе 2.402– 8, а ра очие чертежи зубчатых колес – в ГОСТе 2.40 3–75 и ГОСТе 2.405–75.
Зубчатое колесо любой цилиндрической передачи, которое сообща т вращение второму ко есу (па ному), называется веду щим, а
20

второе колесо – ведомым. Колесо передачи с меньшим числом зубьев
называется шестерней, а с большим – |
колесом. Если ч сла зуб ев ве- |
дуще о и вед мого колёс оди наковы, |
то шестерней называется веду- |
щее колесо. Если передача состоит из |
дной пары колёс, она именует- |
ся од оступенчатой, если из нескольких пар – м ногоступенчатой. |
|
По ориентации о тносительно оси |
вращения колеса зубья могут |
быть прямозубые, косозубые, шевронн ые. Шевронные колёса можно рассматривать как соединение двух косозубых колёс с разны м направлением зубьев.
По взаимному расположению о ей колёс разли ают пе редачи цилиндрические – с параллельным расположе ием осей, конические, если си пересекаются, винтовые – оси скрещиваются.
Зубчатая передача может быть закрытой, когда она работает в специальном корпусе с масляной ванной, и ткрытой , работ ющей без корпуса и смазывания.
2.2. Расчет эскизирование цил ндрических зубчатых колес
Для выполнения расчетов, черте ей и эскизов зу чатых колёс и других деталей зубчатых передач надо знать основн е элементы и параметры зубчатых зацеплений и условности, принятые для изображени зубчатого венца.
а б
Р ис. 17. Шестерни с элементами фикса ции на валу
Основным элементом зубчатого колеса является зуб. Начальная поверхность делит зуб по его ысоте на две не авные части – г ловку
21

и ножку. Часть зуба, расположенная над делительной поверхностью, называется головкой зуба, а расположенная ниже делительной поверхности – ножкой зуба. Зубья с ободом составляют венец зубчатого колеса, который через диск или спицы соединён со ступицей, имеющей отверстие для вала, зачастую с элементами фиксации колеса на валу, например, при помощи шпоночного (рис. 17, а) или шлицевого (рис. 17, б) соединений.
2.2.1. Расчет цилиндрического зубчатого колеса с прямыми зубьями
Конструктивные элементы цилиндрического прямозубого зубчатого колеса показаны на рис. 18.
Рис. 18. Конструктивные элементы зубчатого колеса
Условные обозначения параметров венца зубчатого колеса приведены на рис. 19:
d – диаметр делительной окружности;
22
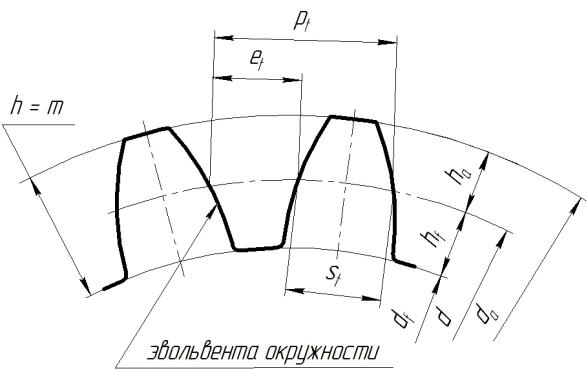
dа – диаметр окружности вершин; df – диаметр окружности впадин; h – высота зуба;
ha – высота головки зуба, ограниченная окружностью вершин; hf – высота ножки зуба с основанием на окружности впадин; st – толщина зуба;
et – ширина впадины;
pt – окружной делительный шаг зацепления, определяющий расстояние между одноимёнными профилями двух смежных зубьев, измеренное по делительной окружности;
b – длина зуба, которая определяется расстоянием между торцовыми поверхностями ширины зубчатого колеса.
Рис. 19. Параметры зубчатого колеса
Боковые стороны поверхности зуба, называемые его профилем, должны быть очерчены по кривым линиям, у которых нормаль, проведённая через точку касания профилей зубьев зацепляющихся колёс, при любом их положении всегда должна проходить через одну точку, называемую полюсом зацепления. Эта точка лежит на линии, соединяющей центры двух колёс.
При этом условии один из двух сопрягающихся профилей колёс можно очертить произвольной кривой. Практически же, чтобы обес-
23

печить возможность изготовления зуборежущих инструментов, профили нарезаемых зубьев выполняются по эвольвенте (см. рис. 19), циклоидальным кривым или дугам окружности. Наиболее распространён эвольвентный профиль, при котором линия зацепления зубьев (геометрическое место касания их сопряжённых профилей) является производящей прямой и поэтому при зубонарезании на станке можно пользоваться простым инструментом.
В нормальном эвольвентном зацеплении линия зацепления расположена под углом зацепления (углом между этой линией и прямой,
перпендикулярной линии, соединяющей центры колёс), равным 20 . Практически профиль зуба при известном диаметре основной окружности вычерчивают упрощённо, заменяя эвольвенту циркуль-
ной кривой, т. е. приближённым очертанием профиля зуба. Основными параметрами зубчатой цилиндрической передачи
являются:
m – модуль зацепления;
z – число зубьев шестерни или колеса; d – диаметр делительной окружности; dа – диаметр окружности вершин;
df – диаметр окружности впадин.
Обычно окружной делительный шаг зацепления выражают числом, кратным π. Модуль – величина, в π раз меньшая pt. Численно модуль равен отношению диаметра делительной окружности к числу зубьев:
m = .
Модуль зацепления выражается всегда в миллиметрах, его значения должны соответствовать значениям, установленным требованиями ГОСТа 9563–60. Модули зубчатых и червячных передач приведены в табл. 1, величины из первого ряда предпочтительны.
При нормальном эвольвентном зацеплении с углом α = 20° размеры для вычерчивания цилиндрического прямозубого колеса определяют по формулам:
высота головки зуба ha = m; высота ножки зуба hf = 1,25m; полная высота зуба h = 2,25m;
диаметр делительной окружности d = mz; диаметр окружности вершин da = m(z + 2); диаметр окружности впадин df = d – 2,5m;
24

шаг зацепления pt = πm;
ширина впадины et = 0,5pt = 0,5πm; толщина зуба st = 0,5pt = 0,5πm.
Таблица 1
Модули зубчатых и червячных передач по ГОСТу 9563-60, мм
Ряды |
|
|
|
Значения модулей |
|||
|
|
|
|
|
|
0,15 |
|
1-й ряд |
0,05 |
0,06 |
0,08 |
0,1 |
0,12 |
||
2-й ряд |
0,055 |
0,07 |
0,09 |
0,11 |
0,14 |
0,18 |
|
1-й ряд |
0,4 |
0,5 |
0,6 |
0,8 |
1 |
|
|
1,25 |
|||||||
2-й ряд |
0,45 |
0,55 |
0,7 |
0,9 |
1,125 |
|
1,375 |
1-йряд |
3 |
4 |
5 |
6 |
8 |
10 |
2-й ряд |
3,5 |
4,5 |
5,5 |
7 |
9 |
11 |
1-й ряд |
25 |
32 |
40 |
50 |
60 |
80 |
2-йряд |
28 |
36 |
45 |
55 |
70 |
90 |
0,2 |
0,25 |
0,3 |
|
0,25 |
0,28 |
0,35 |
|
|
|
2 |
2,5 |
1,5 |
|||
|
1,75 |
2,25 |
2,75 |
12 |
16 |
20 |
14 |
18 |
22 |
100 |
– |
– |
Размеры остальных конструктивных элементов цилиндрического прямозубого зубчатого колеса (рис. 20) определяют на основании соотношений, установленных практикой расчета и конструирования зубчатых колес в зависимости от модуля m и диаметра вала dв по формулам:
ширина зубчатого венца b = (6 8)m; толщина обода зубчатого венца δ1 = (2,5 3)m; наружный диаметр ступицы Dст = (1,6 1,8)dв; толщина диска δ2 = (3 3,6)m;
длина ступицы Lст = 1,5dв.
Чертежи и эскизы зубчатых колёс выполняют в соответствии с требованиями, установленными ГОСТом 2.403–75:
–окружности и образующие поверхностей вершин зубьев показывают сплошными основными линиями;
–делительные и начальные окружности, а также образующие поверхностей делительных и начальных цилиндров показывают штрихпунктирными тонкими линиями на всех изображениях колеса
(рис. 21);
–окружности и образующие поверхностей впадин зубьев в разрезах и сечениях показывают сплошными основными линиями (рис. 21, а), на видах допускается показывать сплошными тонкими линиями (рис. 21, б);
25

– зубья вычерчивают только на осевых разрезах и сечениях, в остальных случаях изображения зубьев ограничивают поверхностями вершин. При необходимости показывают профиль зуба на выносном элементе или на местном разрезе;
Рис. 20. Построение изображения прямозубого цилиндрического колеса
–если секущая плоскость проходит через ось зубчатого колеса, то на разрезах и сечениях зубья показывают нерассечёнными;
–если секущая плоскость проходит перпендикулярно к оси зубчатого колеса, то зубчатые колёса, как правило, показывают нерассе-
26

чёнными; при необходимости показать их рассечёнными применяют местный разрез и проводят штриховку до линии поверхности впадин;
а |
б |
|
Рис. 21. Изображение зубьев |
–если необходимо показать направление зубьев зубчатого колеса, то на изображение поверхности зубьев наносят (как правило, вблизи оси) три сплошные тонкие параллельные линии с наклоном в соответствующую сторону;
–если секущая плоскость проходит через оси обоих зубчатых колёс, находящихся в зацеплении, то на разрезе в зоне зацепления зуб одного из колёс (предпочтительно ведущего) показывают располженным перед зубом сопрягаемого колеса.
Зубчатое колесо на чертеже можно выполнять в двух проекциях (фронтальный разрез на месте главного вида и вид слева). В большинстве случаев для выявления формы зубчатого колеса достаточно одного изображения – фронтального разреза. Для показа отверстия
вступицах зубчатых колёс и шпоночных пазов вместо полного изображения детали допускается давать лишь контур отверстия и па-
за (рис. 25).
В соответствии с ГОСТом 2.403–75 на рабочих чертежах цилиндрических зубчатых колёс с эвольвентным профилем зуба указывают:
–диаметр окружности вершин и предельное значение радиального биения поверхности вершин;
27

– |
шири у зубчатого венца и при необходимости предельное |
||
значение биения поверхности базового торца; |
|
||
– |
разме ы фасок |
и рад усы кр визны |
линий притупле ия на |
кромках зубьев; |
|
|
|
– |
шероховатость |
боковой поверхности |
зубьев, повер ности |
верш н и пов рхности впадин.
Рис. 22. Таблица п араметров зубчатого колеса
На чертеже зубчатого колеса в правом верхнем углу ф рмата поме щают таблицу параметр в (рис. 22). Та лица состоит из трёх частей, отделённых друг от друга сплошными основными ли иями: первая часть – основн ые данные (для изготовления); вторая часть – данны е для контроля; третья часть – правочные данные. Неиспользованные гра ы табл цы параметров исключают или прочёркивают. В учебных чертежах приводят сокращённую таблицу, как показано на прим ре выполнения эскиза (рис. 25).
2.2.2. Вы полнение эскиза прямозубого цилинд ическо о колеса с натуры
При выполнении эскиза (рис. 25) или чертежа цилиндрического зубчатого колеса с натуры необходим ознакомиться с конструкцией детали и определить ее технологические и конструкти ные элементы и особенности формы тела зубчатого колеса, фаски, шпоночные пазы, шлицы.
28

Дляопределенияосновныхпараметровзуб атогоколеса тре уется:
–измерить диаметр окружности вершин da(пр);
–подсчитать число зубьев колеса z.
Если число зубьев четное и раз еры зубчатого колеса небольшие, то диам тр вершин зубьев измеряют штангенциркулем, как показано на рис. 23.
Если число зубьев нечетное или очень б льшой диаметр зубчатого колеса, то диаметр вершин зубьев определяется так, как показано на рис. 24, т. е. штангенциркулем измеряют диаметр отверстия dв, затем определя т диаметр вершин зубьев по формуле
da( пр) = dв + 2L.
Рис. 3. Определение диаметра вершин
збчатого колеса с натуры da(пр)
при четно м количестве зубьев
Рис. 24. Определение диамет а вер-
ин зубчатого колеса с натуры da(пр) при четном количестве зубьевили
большом диаметре зубчатого колеса
Прибли енное значение модуля m(пр) зубчатого колеса определяют, подставив полученные значения в формулу
где z |
m пр) = |
пр |
, |
– число зубьев, получ нное п дсчётом на готовом изделии; |
|||
da(пр) – |
измеренный диаметр окружности вершин, мм. |
29

Рис. 25. Эскиз цилиндрического зубчатого колеса с прямыми зубьями
30