
3587
.pdf
тает и, являясь сжимающим, уменьшает утонение. В точке, где
толщина в процессе деформирования не изменяется. Так как при раздаче RИ ; r3 не превышают 1,5, можно за-
ключить, что основную долю очага деформации составляет зона, в которой толщина заготовки уменьшается, и это приводит к уменьшению значения max .
Упрочнение увеличивает напряжение max . Таким обра-
зом при раздаче, так же как и при отбортовке, влияние утоне- |
|
ния в какой-то мере компенсирует упрочнение. Поэтому |
max |
|
|
можно определить по приведенной выше формуле (3.95). |
|
Формула (3.95) позволяет оценить возможность выполнения раздачи без потери ее устойчивости.
В первом приближении можно считать, что потеря устойчивости наступит при max = S в стенках исходной заго-
товки. То обстоятельство, что при раздаче изгибающий момент препятствует увеличению диаметра заготовки вблизи границы очага деформации, несколько повышает устойчивость и потеря устойчивости происходит при большем значении max , чем при обжиме.
На величину допустимого увеличения диаметра заготовки без разрушения при раздаче оказывают влияние те же факторы, что и при отбортовке:
1)состояние металла у кромки;
2)отношение толщины заготовки к ее диаметру. Коэффициент раздачи определяется как:
k |
|
RИ |
или m |
d |
|
|
1 |
|
|
|
. (3.96) |
P |
|
|
|
|
|
|
|
|
|||
|
r3 |
P |
Dmax |
|
|
|
2S |
|
|
|
|
|
|
|
|
exp( Ш |
|
Sin |
) |
|
|||
|
|
|
|
|
|
|
d |
|
|||
|
|
|
|
|
|
|
|
|
|
|
На его величину влияет угол конусности. С уменьшением угла допустимый коэффициент раздачи уменьшается. Объясняется это тем, что сдерживающее влияние соседних эле-
221
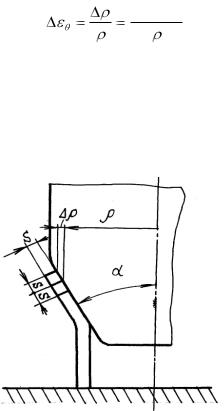
ментов, препятствующее образованию шейки в краевом элементе, уменьшается с уменьшением градиента деформации в меридиональном направлении.
Если в краевом элементе устойчивая деформация исчерпана, то сопротивление, оказываемое соседним элементом развитию локальной деформации в краевом элементе будет тем больше, чем меньше деформация, полученная этим элементом по сравнению с деформацией, соответствующей пределу прочности.
Рассмотрим отличие в деформациях 2-х соседних элементов при раздаче коническим пуансоном (рис. 3.53)
SinS .
С уменьшением убывает разница в деформациях смежных элементов и, следовательно, уменьшается сдерживающее влияние элементов с меньшей деформацией на возникновение локальной деформации в элементе с большей деформацией.
222

Рис. 3.53. Деформации соседних элементов
Но влияние на величину kP невелико, и kР. ДОП .. меньше при хорошей смазке, чем при плохой. При малых значениях облегчается тангенциальное смещение элементов заготовки в процессе образования шейки, при увеличении
силы трения затрудняют образование и развитие шейки в краевых элементах. Однако при увеличении
возрастает усилие, что ведет к
потере устойчивости, повышенному износу инструмента и дефектам заготовки. Упрощенно усилие раздачи можно определить:
P dS Bc , |
(3.97) |
где с = 0,4 ÷ 1,0 (при m = 0,7 ÷ 0,9) - коэффициент учѐта упрочнения и свободного изгиба.
3.6 Формовка
Формовкой называется операция, при которой происходит изменение формы заготовки или полуфабриката за счет местного растяжения материала.
Типовые примеры формовки (рельефной):
1.Штамповка ребер жесткости, выдавок (рис. 3.54).
2.Штамповка рельефных выпукло – вогнутых деталей и художественных украшений.
3.Штамповка – формовка деталей сложной и несимметричной конфигурации открытой формы.
223

Рис. 3.54. Примеры рельефной формовки:
а) – штамповка рѐбер жѐсткости; б) – штамповка выдавок
Предельная степень деформации определяется равномерным удлинением материала и отношением разности пло-
щадей и первоначальной площади n |
(Fn F3 ) |
. |
|
||
|
F3 |
Усилие при штамповке рѐбер жѐсткости может быть определено по формуле
P LSk B ,
где L – длина ребер в мм;
k - коэффициент, зависящий от ширины и глубины ребра. Усилие при рельефной штамповке
P FkS2 ,
где F - площадь рельефа;
k - коэффициент (сталь: 200 - 300 н/мм4, латунь 150 - 200 н/мм4).
Процесс формовки осуществляется на фрикционных, кривошипных, гидравлических прессах, на прессах двойного действия при объединении формовки с вытяжкой. Рельефная формовка тонкого материала осуществляется на резине, полиуретане.
224
4. ИМПУЛЬСНОЕ ВЫСОКОСКОРОСТНОЕ ДЕФОРМИРОВАНИЕ МЕТАЛЛОВ
С давних времен идет непрерывное увеличение энергии, запасаемой рабочей машиной и отдаваемой детали в процессе обработки (молоты простого действия, молоты двойного действия и т.п.). Увеличение энергии определялось, главным образом, ростом размера и веса деталей. Однако скорости деформирования усилились незначительно. Паровой молот м.п.ч. 227000 кг выделяет энергии 1180000 дж при скорости
9,1 м/с.
Процессы высокоскоростного деформирования обеспечивают высокие скорости преобразования энергии, что ведет к резкому возрастанию кинетической энергии - в этом проявляется основное отличие высокоскоростного деформирования от обычных способов деформирования металла.
Первый патент был выдан в Англии в 1898 году на технологию соединения труб при производстве велосипедов путем раздачи с помощью взрыва небольших зарядов ВВ.
В 1909 году в США заряд уже использовался при формовании цилиндрических деталей из стального листа.
Первое промышленное применение взрыва для формообразования может быть отнесено к 1950 году при штамповке втулок вытяжных вентиляторов фирмой ―Мур‖.
Наступление космической эры (примерно с 1955 года) дало новый толчок широкому промышленному внедрению процесса взрывной штамповки для производства крупногабаритных конструкций из труднодеформируемых металлов без уникальных прессов и штампов.
Электрогидроимпульсная штамповка – возможность получения ударных волн высокой интенсивности при разрядке аккумулированной электрической энергии через электроды, погруженные в жидкую среду. Принцип штамповки упомина-
225
ется впервые в 1936 году. В начале 50-х годов в СССР и США началось исследование этого процесса. Первые попытки использования этой энергии были сделаны в США в 1958 году, когда Эли и Дау применили данный метод для пробивки отверстия в стальных листах толщиной 1,6 мм.
Электромагнитная штамповка – первое сообщение, касающееся создания мощного импульсного магнитного поля было сделано Каницем в 1924 году. Источником энергии служила специальная батарея аккумуляторов. Интерес к процессу возрастает ввиду того, что при этом отсутствует контакт между инструментом и заготовкой. Первая промышленная установка была создана в 1962 году. Энергоемкость установки 6250 дж. Производительность 10 импульсов в минуту.
Пневмомеханические машины – основаны на использовании сжатого воздуха в качестве источника энергии для сообщения высоких скоростей движущим частям машины.
Машина «Динопак» демонстрировалась в 1958 году. Энергоносителем системы являлся сжатый азот, перепускаемый через систему клапанов и разгоняющий при этом массивный боѐк до 64,5 м /с.
Внедрение процессов Широкое внедрение процессов относится к началу 1960
года и мотивировалось развитием космической техники. Выбор того или иного процесса обусловлен экономическими факторами, которые должны быть тщательно проанализированы. Например, детонирующие ВВ (тротил) лучше, чем пороховые, можно получить любую форму и габариты деталей, штамповка может быть осуществлена как в открытых, так и в закрытых штампах. Пороховые ВВ, применяемые на практике, требуют более сложных и дорогих закрытых емкостей.
Электрогидравлическая штамповка более легко встраивается в автоматические линии, чем взрывная. Но требования производительности могут привести к сложным жестким требованиям к источнику энергии. Велики капиталовложения.
Электромагнитная штамповка легко встраивается в автоматические линии. Магнитное поле с индукцией 0,5 МГС соз-
226
даѐт такую же плотность энергии, как взрыв детонирующего ВВ. Создание таких полей в ощутимых объемах даже во время порядка 0,1 с весьма сложно и дорого. Электромагнитная штамповка производится при значительно меньших плотностях, достаточных для деформирования тонкостенного материала. Не решена проблема конструкции индуктора, т.к. он испытывает те же нагрузки, что и обрабатываемая деталь.
Импульсными методами штамповки можно выполнять разделительные, формообразующие и сборочные операции, что используют в условиях мелкосерийного производства.
Поведение материала Необходимо отметить влияние высокой скорости про-
цессов на:
1)пластичность и прочность материала;
2)силы трения при перемещении заготовки относительно штампа;
3)стабильность геометрии штампуемой детали;
4)характер протекания процесса.
Влияние скорости на деформируемость для одних металлов проявляется в уменьшении пластичности, для других – в увеличении. Прочность в условиях динамического нагружения увеличивается, что требует для высокоскоростного деформирования больших энергий.
Трение уменьшается с увеличением скорости перемещения заготовки относительно штампа, при этом температура возрастает и нарушается смазка. При очень высоких скоростях температура может достигать таких значений, при которых тонкие поверхностные слои заготовки расплавляются и действуют как смазка.
Стабильность геометрии деталей: при определенных предельных скоростях деформирования наблюдается более равномерное утонение без образования шейки.
Механизм деформирования плоской заготовки имеет следующие особенности:
1. Приложенная нагрузка имеет кратковременный характер и высокие давления.
227
2.Импульсный характер приложения нагрузки вызывает инерционные силы, которые влияют на процесс деформирования.
3.Имеется два периода деформирования – активный и пассивный.
Активный период деформирования соответствует времени действия импульсной нагрузки и характеризуется тем, что элементы заготовки, имея положительное ускорение, разгоняются до некоторой максимальной скорости и получают определенный запас кинетической энергии.
Впассивном периоде накопленная кинетическая энергия расходуется на дальнейшее пластическое деформирование заготовки и ее элементы испытывают отрицательное ускорение (замедление) с уменьшением скорости смещения до нуля в конце деформирования.
1.Скорости при штамповке близки к скоростям распространения пластических волн. Деформирование импульсным магнитным полем осуществляется со значительным влиянием волновых процессов.
2.Влияние волновых процессов проявляется в следую-
щем:
1) скорости пластических волн ограничивают скорости изменения границ очага пластической деформации, а, следовательно, в ряде случаев и скорости деформирования заготовки;
2) взаимодействие прямых и отраженных волн может создавать дополнительные очаги пластической деформации или не приводить к ликвидации существующих очагов деформации;
3) это же взаимодействие может приводить в отдельных случаях к изменению схемы напряженного состояния в деформируемой заготовке (при отражении продольных волн от свободных поверхностей).
3.В общем случае в деформируемом теле могут возникать продольные волны, распространяемые в направлении действующей силы, и поперечные волны, распространяемые перпендикулярно направлению действующей силы.
228
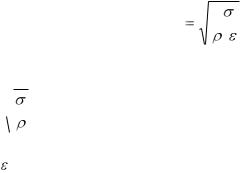
Применительно к листовым заготовкам продольные волны дают смещение элементов заготовки вдоль касательной к ее срединной поверхности, а поперечные – в направлении, перпендикулярном к срединной поверхности.
Скорость продольных волн в стержне:
c1 |
d |
, |
|
|
|||
d |
|||
|
|
скорость поперечных волн:
c2 ,
где - напряжение при испытании на растяжение; - относительное удлинение;
ρ– плотность.
Впервом приближении можно принять, что скорость распространения пластических волн в тонкой пластине определяется так же по указанным формулам с той лишь разницей, что будет являться напряжением, действующим перпендикулярно фронту волны, а влияние схемы напряженного состояние учитывается коэффициентом, который для плоской деформации, например, равен 2/3.
Из формул можно установить, что скорость продольных волн пропорциональна корню квадратному из текущего значения модуля упрочнения, определяемого по графику зависимости условного напряжения от деформации.
Из этих же формул можно установить, что в начальных стадиях пластического деформирования при напряжениях, превышающих предел текучести, скорость пластических волн
вобычно штампуемых материалах исчисляется сотнями метров в секунду.
При вытяжке и формовке основным этапом деформации, дающим наибольшее формоизменение заготовки, является период пассивного деформирования под действием сил инерции.
229

4.1.Деформирование металла импульсным полем
В1924 году академик П.И. Капица применил силовое воздействие импульсного магнитного поля на металл.
В1958 году на 2-й Женевской конференции по мирному использованию атомной энергии была продемонстрирована первая электромагнитная установка.
Сущность процесса Метод деформирования металла импульсным магнитным
полем основан на преобразовании электрической энергии, накопленной в конденсаторной батарее (накопителе), при разряде через индуктор в энергию импульсного магнитного поля, совершающего работу деформирования заготовки. Индуктор при этом может как охватывать полуфабрикат, так и располагаться в его полости.
Рис. 4.1. Схема магнито-импульсной штамповки
Конденсаторная батарея С заряжается от высоковольтного выпрямителя 1 до напряжения U , при этом в батарее запа-
cU 2
сается энергия E (Дж).
2
230