
3587
.pdf2)технологических характеристик (возможность с минимальным количеством операций изготовить заданное изделие);
3)стоимости и дефицитности материала (так как стоимость металла - основная составляющая стоимости штампованного изделия).
Маркировка листовых металлов, технические требования
кним, правила приемки и сортамент определяются соответствующими государственными или ведомственными стандартами.
1.3. Факторы, влияющие на штампуемость листовых материалов
Штампуемость – способность металла пластически деформироваться в той или иной операции.
Понятие о штампуемости, главным образом, связано с понятием допустимой степени деформации.
На штампуемость влияет:
1. Химический состав материала (характеристика основного металла и примесей).
Для штамповки, в основном, распространено применение сталей с содержанием углерода до 0,03 – 0,1 % и в некоторых случаях до 0,24 %. Углерод увеличивает прочностные характеристики при одновременном уменьшении пластичности.
Примеси марганца в стали (до 0,4 %), связывая примеси серы, способствуют улучшению характеристик прочности и пластичности (но не свыше 0,6 %).
Увеличение примеси кремния (0,03 – 0,37 %) значительно влияет на понижение пластических свойств, повышает прочность, твѐрдость и упругость.
Сера (0,03 – 0,05 %) вредна, так как приводит к появлению неметаллических включений, вызывает хрупкость.
Фосфор (0,03 – 0,04%) дает интенсивное упрочнение в процессе штамповки, повышает склонность к старению.
11
Хром и никель (0,1 - 0,25 %) – способствуют повышению прочностных характеристик при почти неизменной пластичности (хотя в ряде сталей – нержавеющих - относительное удлинение может быть больше, чем у малоуглеродистых сталей).
В стандартах на металлы всегда указывается допустимое предельное содержание примесей.
2.Величина зерна. Для штампуемого материала желательно иметь величину зерна с поперечными размерами 0,045 мм.
При чрезмерно большом увеличении размеров зерна пластичность снижается. Кроме того, на деформированных участках после штамповки образуется шероховатая поверхность, что в некоторых случаях, например, в облицовочных деталях, недопустимо.
С уменьшением величины зерна возрастает сопротивление деформированию, увеличивается упругое пружинение, которое влияет на точность изготовления заданных изделий (величина зерна определяется по шкале, в которой величина зерен распределена по баллам от 0 до 9 баллов, чем выше балл, тем меньше зерно).
Неравномерность зерен по величине значительно снижает допустимую степень деформации.
3.Наличие неметаллических включений. Неметаллические включения, вкрапливаясь между зерен или образуя пленку, могут при содержании их в большом количестве привести
кместному расслоению металла. Наличие неметаллических включений регламентируется нормами на их содержание (по баллам, по эталонам).
4.Структурное состояние стали также влияет на характеристики штампуемости. Углерод в форме структурно свободного цементита (расположен по границам зерен) приводит
крезкому снижению пластичности. Хорошо штампуется сталь, в которой перлит зернистый, при пластинчатом перлите – штампуемость незначительно ниже, чем при зернистом.
5.Полосчатость микроструктуры (характеризуется вытянутостью кристаллитов) указывает на наличие упрочнения
12

(наклепа) в стали. Наклеп вызывает повышение прочностных характеристик и снижение характеристик пластичности. Допустимая полосчатость регламентируется соотношением размеров вдоль и поперек зерна, равным 1,4, и определяется шкалой. Если штамповка производится в несколько операций, часто назначается промежуточный отжиг.
В холоднодеформируемом металле в процессе деформирования возникают нарушения в строении кристаллической решетки, а после снятия деформирующих усилий появляются остаточные напряжения.
Холоднодеформированный металл имеет пониженную сопротивляемость коррозии.
Возврат дает снятие остаточных напряжений первого и частично второго рода почти без изменения прочностных характеристик. Состоит в нагреве до небольших температур (для стали 250 ÷ 300 С). Форма зерен в процессе возврата не меняется, вытянутость остается. После возврата сопротивление коррозии вновь приходит почти к исходному.
При дальнейшем нагреве до более высоких температур
(до Тнагр 0,4 Тплав для чистых металлов) наступает второе явление – рекристаллизация, которое приводит к полной замене
вытянутых зерен равноосными и к полному восстановлению механических характеристик.
Возврат и рекристаллизация – основные виды термообработки, сопутствующие холодной штамповке.
Температура рекристаллизации сплава выше, чем температура рекристаллизации чистого металла, и устанавливается опытным путем.
Рекристаллизационный отжиг ведется при температурах ниже фазовых превращений.
6. Наличие площадки текучести. При деформировании с небольшими степенями деформации заготовка будет получать деформации, близкие к пределу текучести, и если металл имеет значительную площадку текучести, то на поверхности появляются линии скольжения (участки с меньшей толщиной) или же линии течения при двухосном растяжении. Изменение ха-
13
рактера диаграммы растяжения, при котором устраняется площадка текучести для штампуемого металла, можно достигнуть предварительной прокаткой с небольшим обжатием листа (дрессировкой) или пропусканием через ряд валков, где производится гибка листа с последующей его правкой. Таким образом, металл преднамеренно получает незначительное упрочнение. Вид диаграммы растяжения для такого металла меняется
– устраняется площадка текучести. Деформацию нужно давать несколько большую, чем соответствующая концу площадки текучести. При длительном хранении после дрессировки и гибки сталь восстанавливает способность образовывать площадку текучести при линейном растяжении.
7.Деформационное старение. После холодного деформирования в течение определенного промежутка времени наблюдаются некоторые изменения в механических свойствах деформируемого металла, а именно прочностные характеристики и характеристики твердости возрастают, а характеристики пластичности снижаются.
Это явление называется деформационным старением и объясняется некоторыми изменениями в кристаллическом строении металла, (выпадение дисперсных частичек по плоскостям скольжения) и зависит от наличия кислорода в металле.
В настоящее время получены стали, где раскисление алюминием проведено полностью. В таких сталях явление старения почти не проявляется.
Старение может привести к изменению механических свойств штампованных деталей в процессе хранения или в течение промежутка времени между операциями.
8.Качество поверхности исходного металла. Шероховатость, риски, раковины на заготовке не только переходят на изделие, но и могут увеличиваться. Кроме того, качество поверхности влияет на поведение металла во время штамповки и на величину допустимой степени деформации.
9.Текстура приводит к анизотропии свойств, что сказывается на течении металла, вызывая появление фестонов (ушей) при вытяжке цилиндрических деталей.
14
1.4. Методы контроля и оценки штампуемости листовых материалов
Вопросам контроля и штампуемости листовых материалов посвящено много исследований как в России, так и за ее пределами. Однако, несмотря на обилие выполненных исследований, до настоящего времени нет надежных методов оценки штампуемости тонколистовых металлов. «Трудно найти проблему, - писал Л.А. Шофман, - которой было бы посвящено столь большое количество работ во всѐм мире. Их количество измеряется сотнями. Работы эти представляют собой изыскания рациональных методов испытания листового металла. Поиски в этом направлении непрерывно продолжаются, и проблема, кажущаяся на первый взгляд столь простой, оказывается столь сложной, что в течение многих лет не получает окончательного своего решения».
Основной причиной отсутствия возможности объективной и всесторонней оценки штампуемости тонколистового металла является все еще недостаточно глубокая теоретическая разработка вопросов, связанных с раскрытием механизма пластического формоизменения с учетом всех факторов, влияющих на процесс: химического состава, структуры и характеристик механических свойств металла, условий деформирования и т.д.
Нашей задачей является ознакомление с методами контроля и оценки штампуемости, существующими в настоящее время, с тем, чтобы правильно применять эти методы для практических целей и совершенствовать их в дальнейшем.
Испытание металла на соответствие пластическим условиям проводятся на заводе-поставщике и заводе-изготовителе.
Существующие способы оценки качества металла, его пригодности для выполнения операций листовой штамповки можно подразделить на 3 группы:
1)физико–химические исследования;
2)механические испытания;
3)технологические пробы.
15
На первые две группы испытаний имеются соответствующие Государственные стандарты, регламентирующие химсостав, физические и механические свойства материалов.
Технологические пробы ставят своей целью определить предельную степень деформации металла в условиях, близких
кпроизводственным.
Втех случаях, когда показатели технологических испытаний определяются стандартом, с помощью технологических проб устанавливается соответствие этих показателей требованиям Государственных стандартов.
Почти все виды технологических испытаний проводятся до момента разрушения испытываемого образца (до появления трещины или разрыва), после чего фиксируется предельная степень деформации, являющаяся критерием штампуемости металлов.
Рассмотрим основные виды технологических испытаний. Испытание на перегиб и изгиб Листовой металл в виде листа или ленты испытывают на
перегиб. Для этого полоску металла определенной ширины закрепляют в специальном приспособлении и производят мно-
гократный двойной перегиб на 180 до момента разрушения. Число двойных перегибов до наступления излома является характеристикой этого вида испытаний.
Кроме того, листовой металл испытывают на изгиб до определенного угла, вплотную до соприкосновения сторон образца или до параллельности сторон образца. Вид изгиба зависит от качества металла и его толщины. Если после испытания на изгиб на образце не обнаружено трещин, надрывов, излома и т.п., считается, что образец испытание выдержал.
Испытание на вытяжку цилиндрического колпачка Данный вид испытаний предложен Г. Свифтом (Англия
1913 г.), в СССР развит трудами сотрудников ЦНИИТМаша Л.А. Шофманом и А.В. Алтыкисом. Испытание заключается в вытяжке цилиндрических колпачков в вытяжном штампе с прижимом из круглых листовых заготовок различного диаметра до момента обрыва дна колпачка (рис. 1.1).
16

Рис. 1.1. Схема испытания на вытяжку цилиндрического колпачка
В результате испытаний определяется критерий штампуемости m, представляющий собой отношение диаметра колпачка к наибольшему диаметру заготовки, из которой получился колпачок без разрушения:
m |
d |
. |
(1.1) |
|
Dзаг |
||||
|
|
|
Установлено, что чем меньше величина m, тем штампуемость металла выше.
Испытания выполняются на специальной машине для испытаний технологических свойств листового металла модели МТЛ – 10Г или на специальном прессе-приборе конструкции ЦНИИТМаша, представляющем собой гидравлический пресс двойного действия усилием 170 кН, оборудованный силоизмерителями для определения усилия вытяжки и усилия прижима. При испытаниях на машине мод. МТЛ – 10Г вытягивается колпачок диаметром 32 мм, при испытаниях на приборе конструкции ЦНИИТМаша – колпачок диаметром 50 мм.
При испытании на вытяжку цилиндрического колпачка напряженное состояние очага пластической деформации
17

(фланца) сжато–растянутое. Поэтому данный вид испытания рекомендуется применять в тех случаях, когда испытываемый металл предназначен для штамповки цилиндрических изделий (например, металлической посуды), при вытяжке которых, как и при испытаниях путем вытяжки колпачка, возникает сходное напряженное состояние. К числу недостатков рассматриваемого способа (испытания) следует отнести длительность процесса испытания и некоторую погрешность результатов вследствие влияния масштабного фактора и условий трения.
Развивая метод испытаний по Свифту, Г.Д. Рогоза предложил в качестве критерия штампуемости показатель, представляющий собой отношение степени вытяжки K d п
к показателю интенсивности упрочнения , определяемому углом наклона схематизированной диаграммы, построенной в осях ― - к‖ ( - нормальное напряжение, возникающее в вертикальной стенке колпачка при вытяжке). По мнению Г.Д. Рогозы, этот критерий лучше характеризует штампуемость листового металла, чем только один предельный коэффициент
вытяжки mпр.
Испытание на глубину формовки лунки Испытание на глубину формовки лунки было предложе-
но шведским инженером А. Эриксеном в 1914 году. Этот вид технологических испытаний пользуется наибольшим распространением при оценке штампуемости тонколистового металла. Испытание заключается в формовке сферическим пуансоном лунки в образце, прочно зажатом между матрицей и прижимным кольцом (рис 1.2.).
При испытании по Эриксену деформация происходит за счет уменьшения заготовки. Испытание по Эриксену выполняется на специальной машине для испытания технологических свойств листового металла, модели МТЛ-10Г, регистрирующей усилие формовки и усилие прижима. Испытательная машина модели МТЛ-10Г имеет гидравлический привод, усилие формовки и прижима определяется при помощи манометров, величина хода рабочих органов отсчитывается по индикатору
18
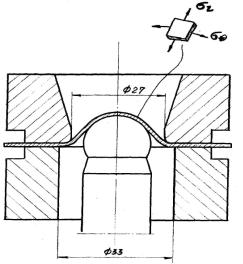
с точностью до 0,1 мм. Наибольшее усилие формовки, развиваемое этой машиной, - 100 кН, наибольшее усилие прижима – 20 кН, толщина испытываемого металла – до 2–х мм.
Рис. 1.2. Схема испытания на глубину формовки лунки
Условия проведения испытаний на формовку лунки регламентированы Государственным стандартом, в соответствии с которым пуансон должен иметь диаметр 20 мм, матрица - 27 мм, заготовка для испытаний в виде полосы должна иметь ширину равную 90 мм и усилие прижима 10 кН. Критерием испытания установлена глубина лунки в момент уменьшения (спада) усилия формовки.
При вытяжке цилиндрических изделий в очаге пластической деформации (фланец) возникают не только радиальные растягивающие напряжения, но и окружные сжимающие, что не соответствует условиям проведения испытаний по Эриксену. Поэтому в заводской практике иногда можно наблюдать, что листы металла с малыми показателями по Эриксену обнаруживают хорошие пластические свойства при вытяжке.
Характер разрушения и качество поверхности лунки также позволяют судить о штампуемости металла: разрыв лунки по дуге окружности указывает на изотропность металла,
19

прямолинейный разрыв свидетельствует о полосчатости структуры или о наличии дефектов прокатки. Чистая гладкая поверхность лунки характеризует мелкозернистую структуру, шероховатая поверхность свидетельствует о крупнозернистой структуре металла.
При испытании по Эриксену в очаге деформации возникает двухосное растяжение. Поэтому данный вид испытаний может дать положительный результат в тех случаях, когда испытываемый металл предназначен для получения сложных пространственных выпуклых деталей или деталей сферической и параболической формы (типа автомобильных фар), при вытяжке которых в очаге деформации, как и при испытании по Эриксену, возникает двухосное растяжение. Для тонколистовой стали марок 08 и 10 глубина лунки должна быть не менее 7 – 12 мм, в зависимости от толщины листа и его категории.
Испытание на вытяжку конического колпачка Испытание металла на штампуемость по методу, пред-
ложенному Фукуи (Япония, 1939 г.), заключается в вытяжке (без прижима) конического колпачка из плоской заготовки при помощи полусферического пуансона и конической матрицы
(рис. 1.3).
Рис. 1.3. Схема испытания на вытяжку конического колпачка
20