
3490
.pdfIssue № 2(34), 2017 |
ISSN 2542-0526 |
5 to 4 cm. Wherein strength safety factors which exceed required values were obtained. It allowed one to assume that the selected constructions meet the requirement for both of the strength criteria. SMA based on slag aggregate with a higher bearing capacity is also evaluated. It is proved by means of the strength safety factor when bending of 1.69 compared to granite rubble based SMA top layer value of 1.59. Wherein as the calculations showed, there are no stresses in pavements that lead to fatigue cracks formation during the pavement life time.
SMA was produced at the asphalt mixing plant in Lipetsk (Russia). In the composition of a mineral mix there are granite screening dust –– 11.4 %, slag rubble of 5…10 mm fraction –– 74 %, mineral powder –– 14.1 %, Viatop cellulose additive 0.5 %, BND 60/90 bitumen over 100 % –– 6.5 %. Test batch volume was 2100 tons.
SMA-15 laying and compacting were performed at 150 оС by a 4 cm layer on a prepared and compacted bottom made of black chippings with the thickness of 10 cm, asphalt treated permeable bases and coarse-graded dense asphalt with the thickness of 8 and 6 cm retrospectively. The total pavement area was 24.000 m2 in 2010.
Implementation economical effect compared to SMA-15 based on granite rubble was achieved by a reduction in slag rubble cost which does not exceed 300 rub/ton compared to granite rubble of 500 rub/ton cost. The asphalt test batch of 2100 tons volume implementation economical effect was 540 000 rub or 22.5 rub/m2. SMA condition observations showed its high bearing capacity and lack of defects. Slag aggregate based SMA-15 implementation within pavements showed its efficiency and durability.
Section Slag aggregate based SMA durability laboratory study
Durability as a property of an organic mineral composite reflects a complex of changes in the strength, deformation and other physical and mechanical asphalt properties under the impact of internal and external factors. It depends on the speed of bitumen membranes aging on SMA aggregate grains surface.
The most important slag based SMA property that determine its durability is the stability of the structure in a changing humidity and temperature. SMA as a porous material is more likely to fail during prolonged moistening and at low temperatures. Its water-resistance depends on the water saturation, swell and water-resistance coefficient (wrc). Slag aggregate based SMA-10 tests results showed that slag rubble by water saturation (3.13 vol.%) meets GOST requirements (1––4 allowed), wrc = 1.03, swelling = 0.015 % (last two parameters are not regulated).
31

Russian journal of building construction and architecture
When we determine fatigue durability, there have to be considered real impacts that come into play throughout the operation of a pavement. Thus corresponding to F. V. Rudensky data asphalt testing mode that imitates real work conditions under traffic loads influence a fatigue test by a cycle dynamic bend.
It is known that the larger applied stress is, the more likely a failure is. Therefore at present stress asphalt fatigue is determined by time during which pavement can bear this stress without break. Dynamic fatigue at cyclic loads is determined by a number of cycles that material can withstand before it fails.
The 868 min-1 frequency is the closest to actual operational road conditions. A single load applied on the estimated time of a cycle at this mode is 0.02s approximately. It is consistent with pavement loading mode when a car passes at the speed of 60 km/h. At 0.35 the amplitude cycle number before it fails is 25958. It provides durability. To predict that, SMA samples were tested in an aggressive environment in operational conditions close to actual ones. The total testing time was 360 cycles. Based on these results, the chemical resistance coefficient was determined (Kchr) ≤ 50 %. Every cycle time was 8 hours.
Based on current operation conditions pavement economically optimal life cycle accepting that during this period Kchr should equal c. For the selected operation period, e.g., 10 years, the chemical resistance of a surface is provided when Kchr decreases by no more than 50 % (c = 0.5).
For predicting the durability Kchr is calculated according to a strength loss. The results of the calculations are listed in Table 2. The compressive strength before the test was 3.877 MPa. Kchr values calculation was made by means of the following formula:
lgКchr = а + b ∙ lg , |
(6) |
where lg Кchr is its logarithm for a current life time , a and b are the constants for a current environment and concrete types.
|
|
|
|
|
|
|
|
Table 2 |
|
|
The results of calculating the chemical resistance coefficients |
|
|
||||||
|
|
|
|
|
|
|
|
|
|
Indicators |
|
|
Indicator value after testing, cycles |
|
|
||||
|
|
|
|
|
|
|
|
||
2 |
15 |
30 |
60 |
90 |
180 |
270 |
360 |
||
|
|||||||||
|
|
|
|
|
|
|
|
|
|
Rc, MPa |
3.977 |
3.623 |
3.723 |
4.197 |
4.306 |
4.151 |
3.554 |
3.201 |
|
|
|
|
|
|
|
|
|
|
|
Mass logss, g |
–– |
–– |
0.03 |
0.03 |
0.4 |
0.27 |
0.32 |
0.68 |
|
|
|
|
|
|
|
|
|
|
|
Kchr |
1.03 |
0.93 |
0.96 |
1.08 |
1.11 |
1.07 |
0.92 |
0.83 |
|
|
|
|
|
|
|
|
|
|
32
Issue № 2(34), 2017 |
ISSN 2542-0526 |
Optimal composition of SMA with the predicted the durability is no less than 10 years. The strength following the test remains sufficiently high and Kchr ≥ 0.5.
The required correlation between Kchr and the accepted operation period is
lgКchr = 0.243 – 0.1164 lg .
If it is advised that economically asphalt pavement period is to be used for = 10 years (3600 days), then for the optimal composition we have:
lgКchr. = 0.243 – 0.1164 lg = 0.243 – 0.1164 lg 3600 = –0.1709536.
Hence Кchr = 0.6746. Here we obtain: 0,6746 > (1 – 0,5) = 0.5.
Therefore based on the optimal composition of SMA made of slag aggregate experiments results operation by durability prediction will be no less than 10 years. The tested slag aggregate based SMA survived a series of durability tests in an aggressive environment in the conditions more challenging than the actual ones.
Conclusions
1.Domestic and foreign practice enables the production of a cube-shaped rubble with the use of modern secondary and tertiary crushing machines. It is experimentally determined that the first-group rubble production (with the content of lamellar and needle particles lower than
10%) is considered not effective in terms of energy consumption and by screening dust in quantities of 50 % of the initial mass.
2.SMA based slag rubble has advanced mechanical properties that are equal to those of SMA based on the properties of a granite rubble; SMA temperature related aging leads to its structure hardening and an increase in the mechanical properties due to adhesion.
3.With the use of experiment planning for the OCCP method there are regression equations obtained for the physical, mechanical and deformation properties of a cube-shaped slag based SMA allowing one to determine the correlation between these properties and bitumen, aggregate and modifier content.
4.Based on a prolonged mass, the strength loss and Kchr decrease test results of imitating a pavement operation throughout the year predicted SMA life cycle of no less than 10 years.
5.The calculation of an allowable elastic deflection and stresses that occur under short-term loads influencing the monolith layers with traffic intensity taken into account when pavement top layer has the thickness of 4 cm shows that it is possible to make use of cube-shaped slag based SMA without decrease in the bearing capacity of a pavement.
33

Russian journal of building construction and architecture
6. The developed SMA compositions were implemented in actual streets of Lipetsk. Therefore by coarse aggregate in SMA composition compared to granite rubble cost a decrease of only 2100 tons and an economical effect taken into account the resulting expenses is no less than 22.5 rub/m2.
References
1.Brand A. S. and Roesler J. R. Concrete with Steel Furnace Slag and Fractionated Reclaimed Asphalt Pavement, University of Illinois at Urbana-Champaign. Research Report No. ICT-14-015. Civil Engineering Studies. Illinois Center for Transportation Series, 2014, no. 14-015, pp. 1––177. Available at: https://apps.ict.illinois.edu/projects/getfile.asp?id=3174
2.Bondarev B. A., Prozorova L. A. and Shtephan Yu. V. Research of Cast Slag Rubble Made Stone Matrix Asphalt Properties, Scientific Herald of the Voronezh State University of Architecture and Civil Engineering. Construction and Architecture, 2014, no. 3 (35), pp. 96––106.
3.Airey G. D., Collop A. C. and Thom N. H. Mechanical Performance of Asphalt Mixtures Incorporating Slag And Glass Secondary Aggregates. 8th Conference on Asphalt Pavements For Southern Africa. pp. 56––69. Available at: http://asac.csir.co.za/capsa/Documents/056.pdf
4.Wintenborn J. L. and Green J. J. Steelmaking Slag: A Safe and Valuable Product National Slag Association, 1998, pp. 1––20. Available at: http://www.acobrasil.org.br/siderurgiaemfoco/CCABrasil/ NSA%20Risk%20Assessment%20Summary.pdf
5.Liz Hunt P. E. and Boyle G. E. Steel Slag In Hot Mix Asphalt Concrete. Final Report. State Research Project #511. Research Group Oregon Department of Transportation Salem, Oregon 97301-5192, 2000, Apr., pp. 1––19. Available at: http://www.oregon.gov/odot/td/tp_res/docs/reports/steelslaghotmix.pdf
6.Ramirez T. L. Steel Slag Aggregates in Bituminous Mixtures, Final Report, 1992, Mar.
7.Murphy T. R., RE. Slag use Asphalt Recycle With High Performance, Www. Theasphaltpro. Comiasphalt Pro, 2013, Dec., pp. 40––42. Available at: http://oregonslag.com/wp-content/uploads/2014/09/Slag-use-Asphalt- Recycle-With-High-Perform-Article-Murphy-12-4-131.pdf
8.Hadia N. M. A., Ryabtsev S. V., Seredin P. V. e. a. Effect of the temperatures on structural and optical properties of tin oxide (SnOx) powder. Physica B-condensed Matter, 2010, vol. 405, iss. 1, pp. 313––317.
34

Issue № 2(34), 2017 |
ISSN 2542-0526 |
UDC 624.131.54 : 625.855.3
S. V. Nosov1
GENERALIZED DYNAMIC MODEL OF THE INTERACTION OF COMPACTORS
WITH ROAD CONSTRUCTION MATERIALS
Lipetsk State Technical University
Russia, Lipetsk, tel.: (4742)55-59-84, e-mаil: nosovsergej@mail.ru
1D. Sc. in Engineering, Prof. of the Dept. of Building Material Studies and Road Technology
Statement of the problem. Studies of interactions of different technologies and a deformed support base including compacted road construction materials are performed in many ways depending on the issues at hand by a range of institutions and researchers. Therefore developing a generalized dynamic model of the interaction of different compactors with road construction materials based on improving their rheology is essential.
Results. Generalized and specific dynamic models of the interaction of different compactors with road construction materials that are connected in ways determined based on a study of extra elements of the model or neglecting a few due to their irrelevance or no role at all in the process. The physical and mechanical parameter of a compactor that reflects the deformation modulus per a unit of the thickness of a compacted material and considers changes in its deformation based on the use of the theory of hereditary creep of elastic-viscous- and plastic materials is set forth as the major characteristics.
Conclusions. The suggested mathematical model of the interaction of compactors with road construction materials allows their amplitude of oscillations during compaction given the rheological properties of materials and energy power of the investigated processes considering a series of new factors to be determined.
Keywords: road construction materials, compactors, dynamic model.
Introduction
Scientific research commonly makes use of the models with the following classification properties: a method of description, degree of similarity, reproducible properties of the original, physical nature, design method, composition and types of problems at hand. Therefore in order to develop or design a model, it is necessary that there is sufficient research performed into the properties and behavior of a modelled object and knowledge of corresponding phenomena or processes.
© Nosov S. V., 2017
35

Russian journal of building construction and architecture
Some known dynamic models do not allow one to obtain a generalized model due to a complex assembly, mode of operation of compactors or complexity of the models considering the structure of a specific device. There might be or not be angular oscillations of the masses, some inertia loads, dynamic features of transmission, the number of compactors facing compactng materials, etc. But the major disadvantages of these models is not presented as an element with the physical and mechanical properties of a corresponding material being compacted. Even when it is not attempted [1, 21], the best-case scenario would be to have this material being presented with elastic, viscous and plastic elements whose parameters cannot actually be determined independently of one another.
Hence all the known dynamic models of the interaction of the machines with compacting materials do not allow one to evaluate actual dynamic characteristics of the “machineenvironment”, i.e. to perform a quantitative evaluation.
1. Generalized dynamic model of the interaction of road construction materials with compacting elements of road construction machinery. Based on the use of the methods of formalizing dynamic systems, a generalized dynamic model of the interaction of different compactors with road asphalt concrete mixes and soils and using it a few specific models were obtained by equaling to zero the corresponding coefficients of differential equations or excluding some parts of the system equations.
Any technology of compacting road construction materials involves choice and use of a corresponding compacting machinery. E.g., in order to achieve the required standards of the density of soils in the construction of a subbase, a type of a compaction machinery and functional parameters of its operating body (amplitude and frequency of oscillations, static or dynamic contact pressure) should comply with a type of a subbase, its condition and required standards of compaction [9]. The same requirements apply for compacting machinery designed for compacting asphalt concrete mixes as well.
However, the amplitude of oscillations of any compactor depends on the physical and mechanical properties of a material being compacted and changes in the process. Therefore the suggested amplitudes of oscillations in the technical characteristics of compacting machinery should be adjusted to match the rheological properties of a material.
Any technology is designed to suit corresponding operating conditions and a contact of machinery with the environment. Thus it is impossible to start designing a compaction technology without being informed on the parameters or physical and mechanical characteristics of a material being compacted itself. The latter should be tested on site.
36
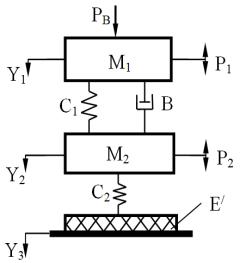
Issue № 2(34), 2017 |
ISSN 2542-0526 |
The major physical and mechanical characteristics of a compacted road construction material can be linear, volumetric or shear deformation. In order to describe the characteristics of a deformed environment with noticeable elastic-viscous-plastic properties that are non-linear and independent on time and nature of the interaction of the engines with the foundation, the Boltzman hereditary integral should be employed.
Fig. 1 shows a generalized dynamic model of different compaction machinery using rheological parameters of a compacted environment identified using the hereditary integral of elastic- viscous-plastic materials. This model allows the amplitude of oscillations and the capacities of compacting road asphalt concrete mixes and foundations for the tools selected to be used for compaction to be determined.
М1 and М2 are oscillating masses (the frame and carrier of the car);
С1 and С2 are the coefficients of elastic resistance; В is the coefficient of viscous friction;
РВ is the inertialess vertical load component from the operating bodies of the machinery; Рi are the external dynamic loads;
Е/ is the physical and mechanical parameter that characterizes the properties of a deformed base; Yi are vertical coordinates of the masses and surface of a compacted layer during the movement
of the compaction machinery
Fig. 1. Generalized dynamic model of compaction machinery for assessing the parameters of vertical oscillations
The model does not allow for the transmission that might come down to the schemes for calculating vertical oscillations of a full-track and wheeled tractors, heavy-duty vehicles, cars, etc. The results of the analysis of dynamic models of compacting machines are presented in Table where the plus sign indicates this element is present in the model and the minus sign shows there is not any.
The generalized two-mass dynamic model (Fig. 1) is described with a system of two linear differential second-order equations:
М1у1 В у1 у2 С1 у1 у2 РВ Р1, |
|
|
||||||
|
|
|
К |
К |
|
|
|
(1) |
|
|
В у1 у2 |
2 |
С1 у1 у2 Р2 |
, |
|||
М2 |
у2 |
1 |
|
|
||||
К1 К2 |
|
|||||||
|
|
|
|
|
|
37

Russian journal of building construction and architecture
where
|
|
|
|
|
К1 С2 Y2 Y3 ; |
|
|
|
||
|
|
|
t |
|
|
|
t |
|
|
|
|
|
|
|
|
S t d |
|
|
|
|
|
К2 |
Е/ Y2 |
|
|
Y2 |
Y3 |
|
Y3 |
S t d |
; |
|
|
|
|
0 |
|
|
|
0 |
|
|
|
S(t – τ) is a relaxation nuclear characterizing hereditary properties of a material; t – τ is a period of time between the moment of observation of the deformation and moment of load application; Е/ is a physical and mechanical parameter of a compacted material that reflects the deformation modulus per unit of the thickness of a compacted layer, N m-1:
|
Е |
Е F |
|
|
|
|
|
|
|
|
|
|
|
||
|
|
к |
. |
|
|
|
|
|
|
|
|
|
(2) |
||
|
(t) h |
|
|
|
|
|
|
|
|
|
|||||
|
|
|
сл |
|
|
|
|
|
|
|
|
|
|
|
|
|
|
|
|
|
|
|
|
|
|
|
|
|
|
Table |
|
Results of analyzing dynamic models of compacting machinery |
|
|
|
|
|
|
|||||||||
|
|
|
|
|
|
|
|
|
|
|
|
|
|
|
|
Type of compacting machinery |
М1 |
М2 |
С1 |
С2 |
В |
Е/ |
РВ |
|
Р1 |
Р2 |
Y1 |
Y2 |
Y3 |
||
Loaders, motor graders |
+ |
– |
– |
+ |
– |
+ |
+ |
|
– |
– |
+ |
– |
+ |
|
|
|
|
|
|
|
|
|
|
|
|
|
|
|
|
|
|
Bulldozers on wheeled tractors |
+ |
+ |
+ |
|
+ |
+ |
+ |
+ |
|
– |
– |
+ |
+ |
+ |
|
|
|
|
|
|
|
|
|
|
|
|
|
|
|
|
|
Scrapers, cars, wheeled tractors |
+ |
+ |
+ |
|
+ |
+ |
+ |
– |
|
– |
– |
+ |
+ |
+ |
|
|
|
|
|
|
|
|
|
|
|
|
|
|
|
|
|
Bulldozers on full–track tractors |
+ |
+ |
+ |
|
– |
– |
+ |
+ |
|
– |
– |
+ |
+ |
+ |
|
|
|
|
|
|
|
|
|
|
|
|
|
|
|
|
|
Full-track tractors, transporters |
+ |
+ |
+ |
|
– |
+ |
+ |
+ |
|
– |
– |
+ |
+ |
+ |
|
|
|
|
|
|
|
|
|
|
|
|
|
|
|
|
|
Self-propelled vibratory rollers |
+ |
+ |
+ |
|
– |
– |
+ |
– |
|
– |
+ |
+ |
+ |
– |
|
|
|
|
|
|
|
|
|
|
|
|
|
|
|
|
|
Self-propelled vacuum–type vibratory rollers |
+ |
+ |
+ |
|
– |
– |
+ |
+ |
|
– |
+ |
+ |
+ |
– |
|
|
|
|
|
|
|
|
|
|
|
|
|
|
|
|
|
Towed vibratory rollers |
– |
+ |
– |
– |
– |
+ |
– |
|
– |
+ |
– |
+ |
– |
|
|
|
|
|
|
|
|
|
|
|
|
|
|
|
|
|
|
One-mass vibratory plates |
– |
+ |
– |
– |
– |
+ |
– |
|
– |
+ |
– |
+ |
– |
|
|
|
|
|
|
|
|
|
|
|
|
|
|
|
|
|
|
Two-mass vibratory plates |
+ |
+ |
+ |
|
– |
– |
+ |
– |
|
– |
+ |
+ |
+ |
– |
|
|
|
|
|
|
|
|
|
|
|
|
|
|
|
|
|
In the last expression Fк is the area of a stamp that is used to determine the deformation modulus of a layer with the thickness hсл; (t) is the relative deformation.
The presented mathematical model (1) of the interaction between compactors with road asphalt concrete mixes and foundations allows their amplitude of oscillations Y2 to be computed during compaction considering the rheological properties of a material.
The following assumptions were made in designing the dynamic model of compaction:
1.Elements of the machinery have the absolute stiffness;
2.The machinery has a longitudinal and transverse symmetry planes;
3.All the oscillatory displacements occur in the planes parallel to the longitudinal symmetry plane;
38
Issue № 2(34), 2017 |
ISSN 2542-0526 |
4.The vibratory operating body works softly with harmonic oscillations;
5.A compacted layer has elastic and viscous properties;
6.Elastic and viscous properties of a vibration damper are linear;
7.Only a vertical component of vibration is examined;
8.Inertia properties of a compacted material can be neglected.
Depending on the type of a compacted layer, operation modes and parameters of a compactor, the fourth and fifth assumptions can be disputed: for high-frequency operating bodies with small amplitudes of oscillations (this applies to self-propelled vibratory rollers for compacting asphalt concrete surfacings where the amplitude of oscillations is 0.25…0.75 mm and it is only at the final stage that microstrokes occur and these assumptions are more accurate than for low-frequency operating bodies working in the vibroimpact mode (self-propelled and towed vibratory rollers for compacting foundations with the amplitude of oscillations from 0.9…2 mm where movement will significantly deviate from being sinusoidal. Nevertheless according to some researchers, these assumptions might be possible.
2. Compaction of a hot asphalt concrete mix using the example of a vacuum-type vibratory roller. Let us investigate compaction of a hot asphalt concrete mix using the example of a vacuum-type vibratory roller [16] that transmits some extra vertical inertialess force due to a vacuum in the chamber.
The fourth assumption was made due to a specific feature of the interaction of the vacuum and the layer of a hot asphalt concrete mix:
––the vacuum effect takes place at high temperatures, which makes vacumm-type vibratory rollers be used when the temperatures reach an extreme high where the stiffness of the layer is considerably smaller thus leading to the vibration stroke operation;
––the vacuum effect reduces the deformation modulus of the layer almost twice, which shows the stroke-free operation to be preferrable;
––the effect of the vacuum chamber as an inertialess extra load reduces the time a vibromill has to be in the air due to extra pressure simultaneously causing a small decrease in the amplitude of oscillations contributing a transfer to the vibration stroke mode to the vibratory one. This is confirmed with an experimental testing of the increased longitudinal stability of the vacuum-type vibratory roller on a longitudinal slope.
39
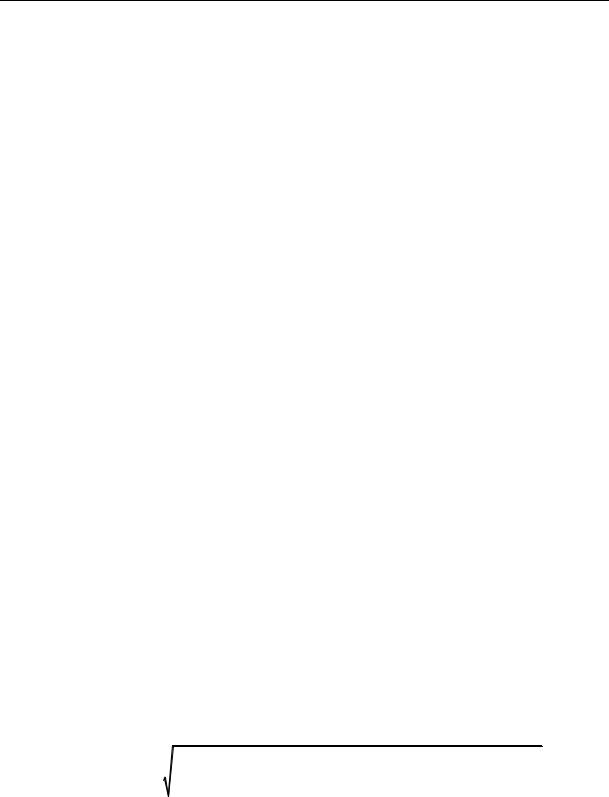
Russian journal of building construction and architecture
As these assumptions are accepted to be true, the calculation scheme of the operation of the vacuum-type vibratory roller is made more simple to become a two-mass system and can thus be described using a system of two linear second-order differential equations [12]:
М |
у |
С(у у |
) Р , |
|
|
|||
|
1 |
1 |
1 |
2 |
|
1 |
|
(3) |
|
|
|
|
|
t |
|
|
|
М2 у2 |
Е у2 |
у2 |
( )S(t )d C(у1 |
у2) Р2 sin( t ), |
|
|||
|
|
|
|
0 |
|
|
|
where М1 and М2 are the mass of a part of the frame of the roller at one end of the vibratory mill and its mass respectively, kg; у1 and у2 are linear displacements of the mass М1 and М2 respectively, m; Р1 is the impact of the vacuum chamber that is the sum of its operating area per the size of the vacuum, N; Р2 is the amplitude that causes forcers from the vibratory mill, N; is the frequency of oscillations, s-1; is the angle of displacement of the vibratory mill and direction of a constraining environment, degrees; С is the stiffness of the shock-absorber, N m-1; S(t- ) is the relaxation nuclear [8, 19]:
S A e t t 1;
А, , are the parameters of the nuclear; е is the base of natural logarithms; Е' is the physical and mechanical parameter of a compacted material, N m-1.
Considering the requirements to a dynamic model, the parameter Е/ is a complex function depending on construction and technology parameters of the roller accounting for the non-linear properties of a compacted material that change over time.
The solutions for the displacements of the mass М1 and М2 obtained for when the law of change in the displacements for a constraining force P2 sin( t- ) are as follows
Y1 Y01 sinwt а, Y2 Y02 sinwt в. (4) The amplitude of the displacements of the vibratory mill or its amplitude of frequencies is given by the expression
А у02 |
|
|
|
|
|
Р2 |
|
|
|
|
|
|
, |
(5) |
|
|
|
|
|
|
2 |
|
|
|
|
||||
|
|
|
|
2 |
СМ1 2 |
|
Р1 |
|
|
Р1 |
2 |
|
||
|
|
|
M2 |
|
|
|
|
|
||||||
|
|
E |
2 ЕD( ) |
А |
ЕС( ) |
А |
|
|||||||
|
|
|
|
|
с М1 |
|
|
|
|
|
|
where D( ) and С( ) are the cosine and sinus Fourier transformation.
As seen from (5), the expression for the amplitude of oscillations of the vibratory mill of the vacuum-type roller is not clear, its solution can be one of the known methods of higher mathematics, e.g. by means of the method of subsequent approximations.
40