
3490
.pdf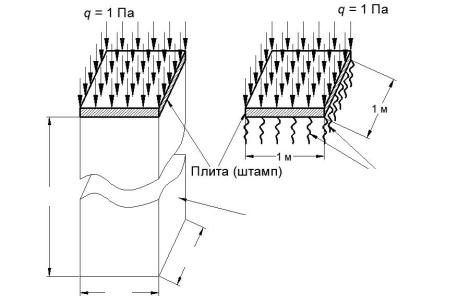
Issue № 2(34), 2017 |
ISSN 2542-0526 |
sized 1 1 m, height 10 m (the distance from the bottom of the shell to the bottom of the massive from the section above, i.e. the depth of the compressed soil) loaded at the top with the pressure 1 Pа transmitted onto the massive with the stiff stamp (Ешт = 2 1015 Pа, = 0.3). The massive (Fig. 3а) is supported not to be shifted towards the normal along the sides and bottom. The plate (stamp) is supported from the horizontal displacements with a minimum number of bonds providing its geometric stability. Flat four-node and volumetric eight-node finite elements were used to design the finite element model.
|
|
Pa |
Pa |
a)b)
|
|
|
|
1 m |
|
|
|
|
|
|
|
|
|
|
|
|
|
|
1 m |
||||
Plate (stamp) |
|
|
Elastic foundation |
||
|
|
10 m
Soil massive
1 m
1 m
Fig. 3. Calculation scheme to determine the coefficient of the subbase of the elastic base corresponding with the volumetric massive:
а) rod of the soil; b) elastic soil
As a result the maximum complete displacement of the plate (stamp) w1 was obtained. Further on, the massive of the soil was replaced with the elastic base (corresponding GAP elements) with the coefficient of the subbase K0 = 1 108 n/m3 (Fig. 3b). The calculation of the plate (stamp) using the elastic soil at the same pressure (1 Pа) obtained the maximum complete displacement w2. The coefficient of the subbase of the base that roughly corresponds with the deformation modulus from the section above (Eгр = 1.634 · 109 n/m2) can be given by the following formula
K K0 w2 . w1
The coefficient of the subbase of the elastic base calculated in this manner was K = 2.20 108 n/m3. Using this coefficient of the subbase of the base the compressive stiffness
11

Russian journal of building construction and architecture
of the GAP elements was identified as well as the shell interacting with the base impacting its eigen weight for the same type of support as in the section below. As a result the components of the stress-strain of the shell were obtained. The maximum equivalent Mises strains in internal вequiv and external нequiv fibres of the shell as well as its maximum complete displacement wmax are listed in Table (column “Variant 2”).
3. Cylindrical shell interacting with the approximated elastic layer
Further on another simplified model of the system “shell-soil” is investigated. The soil surrounding the shell is modelled by the approximated elastic layer (Fig. 1c). In order to account for the soil possibly sticking off the shell, the approximated elastic layer and the shell are joined with the contact GAP elements operating during compression as in the first case (Sсж = 107 n/m, Sр = 10-7 n/m). The material of the elastic layer is accepted to be orthotropic in the cylindrical system of coordinates with the same elasticity modulus in all the directions, the Poisson coefficients that all equal zero and the displacement modulus two units as low as for an isothropic material. This is due to seeking to approximate the behavior of the elastic layer as much as possible to the that of the elastic base, i.e. to reduce the effect of the displacement deformations in the elastic layer. Let us connect the approximated modulus of the elastic layer Eпр with the coefficient of the subbase of the elastic base K so that the elementary potential energies of the deformation layer and the base are dWсл dWос . We assume that the elastic layer (Fig. 4) operates during compression or tension only in a radial or circular direction and its outer surface is supported from displacements (wн = 0).
Fig. 4. Elementary segment of the elastic layer
12
Issue № 2(34), 2017 |
ISSN 2542-0526 |
The elementary potential energy of the deformation of the layer is given by the following formula
Rн |
|
|
dWсл 12 R |
r r rd drdz |
(1) |
в |
|
|
Strains and deformations in a radial and circular direction considering the accepted assumptions on a material are the following respectively:
|
r Eпр r ; |
Eпр ; |
|||||||||
r |
wн wв |
|
0 wв wв ; |
||||||||
|
|
||||||||||
|
|
|
tпр |
|
|
|
tпр |
|
|
|
tпр |
|
|
|
2 (r w) 2 r |
w . |
|||||||
|
|
||||||||||
|
|
|
|
|
2 r |
|
|
|
r |
||
Considering the expressions (2––4) formula (1) takes the shape |
|||||||||||
|
Eпр |
Rн |
w |
2 |
w 2 |
||||||
dWсл |
|
|
|
|
|
в |
|
|
|
|
rdrd dz . |
2 |
|
t |
|
||||||||
|
|
пр |
|
|
r |
|
|||||
|
|
Rв |
|
|
|
|
|
|
|
(2)
(3)
(4)
(5)
Radial displacements of random points of the layer assuming that they change their thickness according to the linear law are calculated using the formula
|
w |
w |
|
|
r R |
|
w wв |
н |
в |
|
|
в |
|
|
tпр |
( r Rв ) wв 1 |
tпр |
. |
||
|
|
|
|
|
In order to simplify the calculation of the integral in expression (5), we assume that
w const wн wв 0 wв 1 wв .
2 2 2
Considering (6) expression (5) takes the shape
|
Eпр |
Rн |
|
w |
2 |
|
|
w 2 |
|||
dWсл |
|
|
|
|
в |
|
|
в |
rdrd dz |
||
2 |
t |
||||||||||
|
|
|
|
|
|
|
2r |
|
|||
|
|
Rв |
|
|
пр |
|
|
|
|
Calculating the integral in (7) and omitting the elementary transformations we get
|
Епр |
w2 |
|
R R |
1 |
ln |
|
Rв tпр |
|||
dW |
|
|
н в |
|
|
|
|
d dz |
|||
2 |
|
4 |
R |
||||||||
сл |
в |
|
2t |
пр |
|
|
|||||
|
|
|
|
|
|
|
|
в |
|
(6)
(7)
(8)
The elementary potential energy of deformation of the base is determined using the formula
dw |
|
1 Kw2R d dz . |
(9) |
ос |
|
2 в в |
|
13

Russian journal of building construction and architecture
Equalling the expressions of the energy (8) and (9) we get
|
Епр |
w2 |
|
R |
R |
1 |
ln |
Rв tпр |
|
|
|
|
1 |
Kw2R d dz. |
(10) |
||||||||
|
|
|
н |
|
в |
|
|
|
|
|
|
|
|
|
d dz |
|
|
|
|||||
|
|
2t |
|
4 |
|
R |
|
|
2 |
||||||||||||||
|
2 в |
|
пр |
|
|
|
|
|
в в |
|
|||||||||||||
|
|
|
|
|
|
|
|
|
|
|
в |
|
|
|
|
|
|
|
|
|
|||
Hence |
|
|
|
|
|
|
|
|
|
|
|
|
|
|
|
|
|
|
|
|
|
|
|
|
|
|
|
|
|
Eпр |
|
|
|
|
|
|
|
KRв |
|
|
|
|
|
|
(11) |
||
|
|
|
|
|
|
|
2Rв |
tпр |
|
1 |
|
Rв tпр |
|
||||||||||
|
|
|
|
|
|
|
|
|
|
|
|
|
|
|
|
ln |
|
|
|
|
|
||
|
|
|
|
|
|
|
|
|
|
2tпр |
|
4 |
Rв |
|
|
|
|||||||
|
|
|
|
|
|
|
|
|
|
|
|
|
|
|
|
|
|
E.g., at |
R 1 m, t |
пр |
0.08 m, K 2.2 108 |
n/m3 the calculated approximated modulus of |
|
|
в |
|
|
|
|
the elasticity of the layer was |
E 1.690 107 |
n/m2. Note that the formula identical to (11) but |
|||
|
|
|
|
пр |
|
not considering deformations of the layer in the circular direction is given in [21]. It has no member containing a natural logarithm.
The elastic layer modelling the soil is approximated by eight-mode volumetric elements (Fig. 1c). The use of only one layer of the volumetric elements in this case is possible as the elastic characteristics of this layer are not real but approximated ones. Five calculations for different thicknesses of the elastic layer for the effect of the eigen weight of the shell for such supports are performed as in the previous sections. The outer surface of the elastic layer was accepted to be supported from all displacements. As a result, the components of the stressstrain of the shell are calculated. Maximum complete displacements wmax and maximum equivalent Mises strains in the internal вequiv and external нequiv fibers of the shell for different thicknesses of the elastic layer are listed in Table (columns “variant 3”). Note that for the other layer with the thickness of 0.08 m to 0.4 m (0.08Rв tпр 0.4Rв ) the calculated maximum displacements and strains in the shell were found to be quite close and consistent with the similar results obtained using the other models of the soil base. This is in agreement with the formula (11) and assumptions accepted as they were hypothesized.
Conclusions
As a result, the authors were able to develop the method considering one-sided contacts of the shell and the soil base to allow three models of the soil surrounding the shell to be compared: the Winkler-Fuss base, model of the elastic layer and volumetric massive. The accurate formula for the approximated elasticity modulus of the elastic layer is hypothesized. Let us sum up in the following way.
1. The results of the calculation of the system “shell-surrounding soil” obtained using three above models of soil are in good agreement qualitatively and quantitavely, which suggests
14
Issue № 2(34), 2017 |
ISSN 2542-0526 |
that the calculations and models were correct. Displacements, strains and deformations of the shell as well as areas where the soil sticks off are identical in all the cases.
2.The model of the approximated elastic layer should be applied unless there are finite elements in software that model the elastic base or the shape of the finite elements of the shell is regular. For the latter calculating actual stiffness of the GAP elements.
3.While choosing the thickness of the approximated elastic layer and using the formula (11) it should not be made too thick (tпр 0.4 0.5 Rв ).
4.In calculations we should avoid using mostly volumetric models of the massive of the soil with contact elements for considering the fact it might stick off the shell but due to complexity associated with such calculations it is acceptable to make use of the elastic base modelled using GAP elements as well as the model of the approximated elastic layer with extra contact elements.
References
1.Kositsyn S. B., Chan Suan Lin'. Chislennyy analiz napryazhenno –– deformirovannogo sostoyaniya ortogonal'no peresekayushchikhsya tsilindricheskikh obolochek bez ucheta i s uchetom ikh odnostoronnego vzaimodeystviya s okruzhayushchim massivom grunta [Numerical analysis of stress –– strain state orthogonal intersecting cylindrical shells with and without taking into account their unilateral interaction with the surrounding soil]. International Journal for Computational Civil and Structural Engineering, 2014, vol. 10, iss. 1, pp. 72––78.
2.Kleyn G. K. Raschet podzemnykh truboprovodov [Calculation of underground pipelines]. Moscow, Izdatel'stvo literatury po stroitel'stvu, 1969. 240 p.
3.Leont'ev N. N. [A practical method of calculation of thin-walled cylindrical pipe on an elastic Foundation]. Trudy Moskovskogo inzhenerno-stroitel'nogo instituta [Proc. of the Moscow Institute of civil engineering]. Moscow, 1957, pp. 47––69.
4.Prevo R. Raschet na prochnost' truboprovodov zalozhennykh v grunt [Strength calculation of pipelines laid in the ground]. Moscow, Stroyizdat Publ., 1964. 123 p.
5.Shaposhnikov N. N. [Calculation of circular tunnel linings in elastic Foundation characterized by the two ratios of bed]. Nauchnye trudy Moskovskogo instituta inzhenerov zheleznodorozhnogo transporta [Proc. of the Moscow Institute of railway transport engineers], 1961, iss. 131, pp. 296––305.
6.Shagivaleev K. F. Raschet zamknutoy tsilindricheskoy obolochki, zapolnennoy sypuchim materialom, na radial'nuyu nagruzku [The calculation of a closed cylindrical shell filled with loose material, radial load].
Izvestiya vuzov. Stroitel'stvo, 2003, no. 2, pp. 20––23.
7.Gabbasov R. F. K raschetu gibkikh trub na sovmestnoe deystvie vneshney nagruzki i vnutrennego davleniya s uchetom otpora grunta [To the calculation of flexible pipes for the joint action of external loads and internal pressure, given the resistance of the soil]. Gidrotekhnicheskoe stroitel'stvo, 1970, no. 10, pp. 17––19.
15

Russian journal of building construction and architecture
8.Aynbinder A. B. Raschet magistral'nykh i promyslovykh truboprovodov na prochnost' i ustoychivost' [Calculation of main and field pipelines on the strength and stability]. Moscow, Nedra Publ., 1991. 288 p.
9.Aleshin V. V., Seleznev V. E., Klishin G. S., etc, Aleshin V. V., Seleznev V. E., eds. Chislennyy analiz prochnosti podzemnykh truboprovodov [Numerical analysis of strength of underground pipelines]. Moscow, Editorial URSS Publ., 2003, 320 p.
10.Lalin V. V., Yavarov A. B. Sovremennye tekhnologii rascheta magistral'nykh truboprovodov [Modern technology of calculation of the main pipelines]. Inzhenerno-stroitel'nyy zhurnal, 2010, no. 3, pp. 43––47.
11.Seleznev V. E., Aleshin V. V., Pryalov S. N. Osnovy chislennogo modelirovaniya magistral'nykh truboprovodov [Basics of numerical modeling of pipelines]. Moscow, KomKniga Publ., 2005. 496 p.
12.Zienkiewicz O. C., Taylor R. L. The finite element method. 5-th edition. Butterworth-Heinemann, 2000, vol. 2: Solid mechanics. 479 p.
13.Altaee A., Fellenius B. H. Finite element modeling of lateral pipeline-soil interaction. 14th International Conference on Offshore Mechanics and Arctic Engineering. OMAE 96. Florence, 1996.
14.Nobahar A. Effect of soil spatial variability on soil-structure interaction: thesis Doctor of Philosophy. St. John. Canada, 2003. 305 p.
15.Phillips R., Barrette J., Jafari A., Park T., Piercey G. Pipeline integrity for ground movement hazards. Canada, 2008. 154 p.
16.Popescu R., Nobahar A. 3D Finite element analysis of pipe-soil interaction effects of groundwater. St. John, Canada, C-CORE, 2003. 34 p.
17.Savin G. N. Raspredelenie napryazheniy okolo otverstiy [The distribution of stresses around holes]. Kiev, Naukova Dumka Publ., 1968. 891 p.
18.Chan Suan Lin'. Otsenka razmerov massiva grunta, zadavaemogo pri prostranstvennykh raschetakh podzemnykh sooruzheniy, iskhodya iz usloviy zatukhaniya ego napryazhenno-deformirovannogo sostoyaniya [The assessment of the magnitude of the soil specified for the spatial calculations of underground structures, based on the conditions of damping of its stress-strain state]. Stroitel'naya mekhanika inzhenernykh konstruktsiy i sooruzheniy, 2013, no. 4, pp. 41––43.
19.Kositsyn S. B., Dolotkazin D. B. Raschet sterzhnevykh sistem, vzaimodeystvuyushchikh s uprugim osnovaniem, metodom konechnykh elementov s ispol'zovaniem programmnogo kompleksa MSC/NASTRAN FOR WINDOWS [Calculation of rod systems interacting with an elastic Foundation, finite element method using the software complex MSC/NASTRAN FOR WINDOWS]. Moscow, MIIT, 2004. 116 p.
20.Aleksandrov A. V., Potapov V. D. Osnovy teorii uprugosti i plastichnosti [Fundamentals of the theory of elasticity and plasticity]. Moscow, Vysshaya shkola Publ., 1990. 400 p.
21.Kositsyn S. B. Neklassicheskie krivolineynye konechnoelementnye modeli v lineynykh i ne-lineynykh zadachakh stroitel'noy mekhaniki. Diss. dokt. tekhn. nauk [Non-classical curvilinear finite element models in linear and nonlinear structural mechanics problems. Dr. eng. sci. diss.]. Moscow, MIIT,1993. 424 p.
22.Seredin P. V., Glotov A. V., Domashevskaya E. P. e. a. Structural and spectral features of MOCVD AlxGayIn1-x-yAszP1-z/GaAs (100) alloys. Semiconductors, 2012, vol. 46, iss. 6, pp. 719––729.
16

Issue № 2(34), 2017 |
ISSN 2542-0526 |
HEAT AND GAS SUPPLY,VENTILATION,AIR CONDITIONING,
GAS SUPPLY AND ILLUMINATION
UDC 621.039:697.34
V. N. Mel'kumov1, S. V. Chuikin2, A. I. Kolosov3
DISTRICT HEATING FROM NUCLEAR POWER STATIONS
Voronezh State University of Architecture and Civil Engineering Russia, Voronezh, tel.: (473)271-53-21, e-mail: teplosnab_kaf@vgasu.vrn.ru
1D. Sc. in Engineering, Prof., Head of the Dept. of Heat and Gas Supply and Oil and Gas Business Russia, Voronezh, tel.: (473)271-53-21, e-mail: ser.chu@mail.ru
2PhD in Engineering, Assoc. Prof. of the Dept. of Heat and Gas Supply and Oil and Gas Business Russia, Voronezh, tel.: (473)271-53-21, e-mail: teplosnab_kaf@vgasu.vrn.ru
3PhD in Engineering, Assoc. Prof. of the Dept. of Heat and Gas Supply and Oil and Gas Business
Statement of the problem. The limited proven reserves of energy resources lead to the need for a wider use of nuclear energy for heat supply of cities. Therefore studying the possible schemes of district heating from nuclear sources is becoming increasingly important and most promising as it is capable of making up for a growing shortage of generating capacity.
Results and conclusions. The article considers thermal schemes of nuclear power plants heat and atomic power plants, as well as lists the parameters of their main units. This data can be used as an input when searching for the most optimal modes of work stations so that through more profound analysis ways to improve the basic circuits of nuclear power stations could be identified. The method of increasing the economic efficiency of nuclear stations of a heat supply based on a joint work with peak boiler-houses lo-cated in the center of heat loads is set forth.
Keywords:heatpowerengineering,heatsupply,nuclearenergy,nuclearstationsof heatsupply, atomic powerplant.
Introduction
Currently fuel has become one of the defining factors of production. A good illustration of the key role of fuel and energy base of the global economy is a so-called energy crises that has made this issue one pressing and global. The emerging energy situation is associated with a rapid decrease in the body of non-renewable reserves of oil, and later on gas, which causes
© Mel'kumov V. N., Chuikin S. V., Kolosov A. I., 2017
17

Russian journal of building construction and architecture
increasing costs as they are being sought after. The response to the energy crises was the development of a strategy for the utilization of fuel and energy based on energy saving and optimization of the structure of fuel and energy resources. It is obvious that in these conditions the share of nuclear energy in fuel-energy balance will steadily increase. The decline of the level of confidence in the nuclear energy after the accident at the Chernobyl nuclear power plant and an increasing reliability of modern designs of nuclear reactors contributed to the change in the tendency of the reduction in the share of nuclear energy in the global balance promote its growth.
The most common are power reactors to generate the electricity in nuclear power plants (NPPs). In the process of the development of atomic energy, a number of different thermal schemes of nuclear power plants (NPP) were suggested. However, the experience of the development of heat schemes of nuclear power plants was the foundation of a further improvement of nuclear installations and thermal equipment. At the same time, the thermal energy characteristic of the Northern territories is in growing demand. For example, in addition to the existing nuclear power plants (ATEC) located in the Chukotka Autonomous District (Bilibino NPP), the construction of a plant for the supply of Arkhangelsk and Severodvinsk is being planned. A floating plant for its Northern territories is being developed as well.
These nuclear facilities for the generation of heat associated with the end-point user via a heat exchanger. The principal scheme of such a setup is shown in Fig. 1. The setup includes a reactor, a piping system, relational pump. In a one-contour loop the heat exchanger flows the same coolant installed in the reactor. In this case, the coolant has a large induced radioactivity and in some cases may contain a radioactive fission product. During the decompression of the heat exchanger radioactive materials will penetrate the end-point contour.
To the |
|
To the |
end-point user |
|
end-point user |
Fig. 1. Single-loop (a) and bypass (b) nuclear power plant for heat supply: 1 — nuclear reactor; 2 — pipe; 3 — intermediate heat exchanger;
4, 5 –– circulation pumps of the first and second contours; 6 — end-point exchanger
18
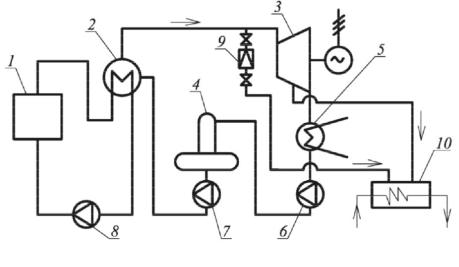
Issue № 2(34), 2017 |
ISSN 2542-0526 |
One-contour setups cannot be used when contamination it is not permitted to pollute a coolant circuit of the consumer. Therefore, the practical use is made of a multi-circuit setup where transfer of heat to the external consumer makes use of two or more coolants not contacting with each other directly. In Fig. 1b the reactor with an intermediate heat exchanger forms the first closed loop and the intermediate heat exchanger, piping and terminal heat exchanger do the second circuit. Each circuit has its own circulating pump.
In multi-loop setups there is hardly any contact of the active coolant of the first circuit to the operating environment of the consumer. However, the implementation of a multicontour setup is more complicated, since additional hardware is required. In addition to the special stations for heat supply, some nuclear power plants might be utilized. E.g., in Leningrad and Beloyarsk NPP in addition to generating electrical energy there is also a low-grade heat and hot water for adjoining communities. However, the maximum performance of thermal energy is observed for ATEC and nuclear stations of heat supply (NSHS).
1. Schematic diagram of the nuclear steam plant. Nuclear thermal electric pipeline generates electricity and simultaneously through the network heaters releases heat to consumers. The steam for heating water in a network is directed from a heater that is controlled from the selection of the turbine (Fig. 2).
Into the heating network
Fig. 2. Scheme of ATEC:
1 is a reactor; 2 is a steam generator; 3 is a turbine; 4 is a deaerator; 5 is a condenser; 6 is a condensation pump; 7 is a feed pump; 8 is a circulating pump; 9 is a reduction-cooling setup; 10 is a heater of nuclear water
19

Russian journal of building construction and architecture
To satisfy the peak heat demand a reduction-cooling setup 9 is used. Steam and heat balances of the plant are determined by the following expressions
G = Gn + Gk , |
(1) |
Nэ = N n + Nk , |
(2) |
where G is the total steam flow to the turbine; Gn is the steam consumption selected to meet thermal demands; Gk is the consumption of steam sent to the condenser; Nn is the electrical power produced by the steam selection; Nk is the electrical power produced by the steam entering the condenser.
The most efficient ratio of the produced heat and electric energy is determined by calculating the thermal efficiency using the following expressions. The efficiency of an ATEC:
|
АТЭЦ |
|
QИСП |
|
Nэ QТ.П. |
, |
(3) |
|
|
|
Q |
|
Q |
р |
|
||
|
|
|
ЗАТР |
|
|
|
where QТ.C. is the amount of heat sent to the consumer; Qр is the amount of the thermal energy of the power of the reactor.
The efficiency of the production of thermal energy:
|
QТ.П. |
· |
пг |
· |
mp1 |
· |
mp2 |
· |
m.c. |
, |
(4) |
Т.П. |
p |
|
|
|
|
|
|
||||
|
QТ.Р. |
|
|
|
|
|
|
|
|
|
|
where QТ.R. is the amount of thermal energy for the production QТ.C.; ηт. с. is the amount of heat losses in heating networks;
The efficiency of the production of thermal energy at an ATEC:
ЭАТЭЦ |
NЭ |
. |
(5) |
|
Qp QТ.П. / Т.П. |
||||
|
|
|
In some cases the index of the specific production of thermal energy for meeting a demand for heating is used:
ЭТП |
NЭТП |
, |
(6) |
|
Q |
||||
|
|
|
||
|
Т.П. |
|
|
where NETC is the amount of thermal energy that is released by the steam by the selection for a heating demand as well as that for heating provisional water.
In the above scheme the plant thermal energy of nuclear fission is perceived by thermal carriers of the first circuit. Let us consider in more detail the composition of the coolant equipment, e.g. the installation of a reactor VVER-1000 has much in common with the first contours of ATEC for different purposes.
20