
3357
.pdf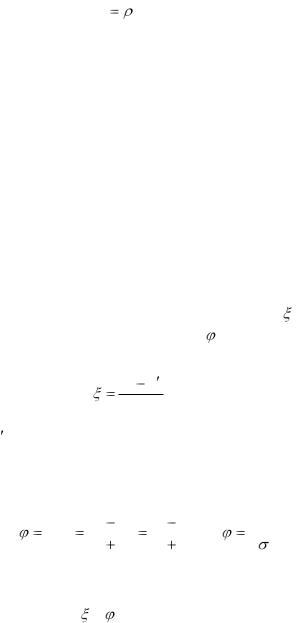
C FV 2 , |
(8.4) |
где – плотность материала ремня;
V – скорость ремня, м/с;
F – площадь поперечного сечения ремня.
Таким образом, натяжение в ветвях при работе передачи будет равно: S1 + C; S2 + C и при холостом ходе S0 + C.
8.2.3. Расчет передач по кривым скольжения
Цель расчета: обеспечить необходимые тяговые свойства ремня (отсутствие буксования и неспокойного хода ремня) и высокий КПД передачи. При этом методе расчета напряжения в ремне получаются меньше допускаемых, одновременно обеспечиваются и тяговые свойства ремня и достаточная его прочность. Кривые скольжения получают экспериментально (рис. 8.6): при постоянном натяжении S0 постепенно повыша-
ют полезную нагрузку P и измеряют скольжение . При этом вводится понятие о коэффициенте тяги .
Относительное скольжение S равно:
n2 n2 100% , n2
где n2 и n2 – частоты вращения ведомого шкива соответствен-
но на холостом ходу и под нагрузкой. Отношение передаваемого ремнем окружного усилия к
сумме натяжений его ветвей называется коэффициентом тяги.
P |
|
S1 |
S2 |
|
m |
1 |
, |
K |
, |
2S0 |
|
S1 |
S2 |
|
m |
1 |
2 0 |
где – коэффициент тяги;
K – полезное напряжение в ремне.
В координатах – строится кривая тяговой характеристики ременной передачи (рис. 8.6). Прямолинейный участок, где с ростом прямо пропорционально растет S называется
119

рабочим участком. Второй участок криволинейный, отражающий неустойчивую работу ремня (пробуксовки и полное буксование) называется нерабочим.
Рис. 8.6
Точка перехода от прямолинейного участка к криволинейному называется критической точкой тяговой характеристики. Кривые скольжения и КПД показывают, что оптимальная нагрузка ременных передач лежит в зоне критических значений
коэффициента тяги |
0 и наиболее высокого КПД При < |
0 тя- |
|
говая способность ремня не используется полностью, при |
> 0 |
||
ремень работает неустойчиво и быстро изнашивается. |
|
||
Отношение |
max/ |
передач, рассчитанных по кривым |
скольжения, характеризует их способность к перегрузкам. Численные значения коэффициента тяги зависят от вида ремня, его толщины, диаметра шкивов, скорости и т.д. Однако характер кривой скольжения остается постоянным при любой комбинации перечисленных параметров. Это положение позволило установить общие нормы работоспособности ремня с учетом влияния различных параметров. Так, условия работы ременной передачи считаются нормальными, если
120
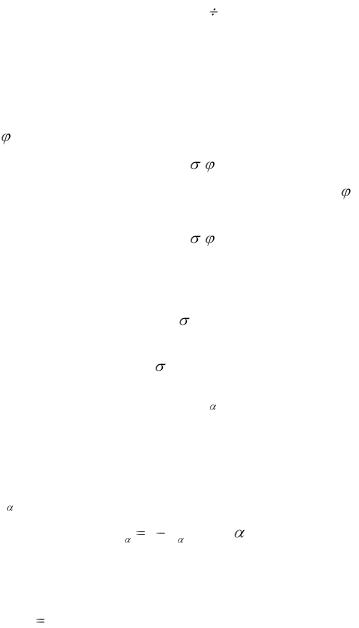
Dmin/h = 33 37,
где Dmin – наименьший диаметр шкива; h – толщина ремня;
8.2.4. Допустимое полезное напряжение.
Полезное напряжение, соответствующее коэффициенту тяги будет равно:
K = 2 0 .
Для критического значения коэффициента тяги 0 полезное напряжение, обозначенное K0 будет:
K0 = 2 0 0.
В таблицах приводятся значения K0 для различных ремней при разном соотношении. В действительности условия отличаются от табличных, поэтому расчет передачи следует вести не по K0, а по напряжению П, с учетом поправочных коэффициентов:
П = KC,
C = C0 Ch C CV,
где C0 – коэффициент, учитывающий условия натяжения ремня и расположение передачи в пространстве.
Ch – коэффициент, учитывающий влияние отношения
Dmin/h
C – коэффициент, учитывающий влияние угла обхвата.
C 1 C' (1800 ) .
CV – скоростной коэффициент, учитывающий ослабление сцепления ремня со шкивом под действием центробежной силы. Для передач с автоматическим регулированием натяжение ремня CV 1.
121
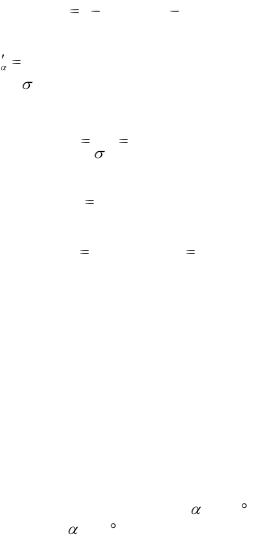
|
C 1 C' ( 0,01v2 1). |
||||||||
|
v |
|
|
|
v |
|
|
|
|
Для плоских среднескоростных ремней из традиционных |
|||||||||
материалов C |
0,04 и т.д. |
|
|
|
|
|
|||
Величина |
П необходима, |
например, при расчете пара- |
|||||||
метров ремня. |
|
|
|
|
|
|
|
|
|
|
F |
|
|
P |
|
bh , см2, |
|
|
|
|
|
|
|
|
|
|
|||
|
|
|
П |
|
|
|
|||
|
|
|
|
|
|
|
|
|
|
где |
P |
|
|
N |
|
, Н; |
|
|
|
|
|
V |
|
|
|
||||
|
|
|
|
|
|
|
|
|
|
b – ширина ремня b |
|
|
P |
или b |
F |
; |
|||
|
/ K / h |
|
|||||||
|
|
|
|
h |
|||||
h – ширина ремня, |
которой задаются, соблюдая соотно- |
||||||||
шение Dmin/h. |
|
|
|
|
|
|
|
|
8.2.5. Клиноременная передача
Клиноременная передача имеет большее сцепление ремня со шкивов, чем плоскоременная. Это позволяет осуществить передачи с малым межосевым расстоянием, большим передаточным числом и с меньшим давлением на опоры. Работа передачи более спокойна т.к. отсутствует сшивка ремней, что важно при эксплуатации точных механизмов. К недостаткам относятся меньший срок службы ремней. При их вытяжке регулируется передвижение электродвигателя на салазках. Рекомендуемые угол обхвата малого шкива = 120 , но передача хорошо работает и при = 90 .
Максимально допустимая скорость Vmax = 35 м/с. Практикой установлено Dmin/h = 11 для ремней малых сечений и Dmin/h = 27
– для ремней больших сечений. Здесь h – высота профиля клинового ремня. Чем меньше отношение Dmin/h, тем ниже КПД. Расчетным диаметром шкива считают диаметр его окружности по нейтральному слою. Кривые скольжения для клиновых
122
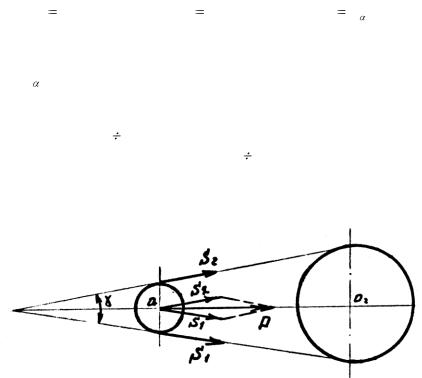
ремней аналогичны кривым плоских ремней, но φ0 для клиновых ремней больше.
8.2.6. Расчет клиноременных передач.
Расчет по тяговой способности рекомендуется производить по допускаемой полезной нагрузке P0 на один ремень. В зависимости от сечения ремня, P0 выбирается из таблиц (ГОСТ 1284.3-96). Значения P0 в таблицах приведены при условии:
V + 10 м/с; |
u = 1. |
Общая полезная окружная сила и мощность равны:
P |
ZP0C |
; |
N |
P0VZC |
; |
C C CV , |
|
K |
102K |
||||||
|
|
|
|
|
|||
где P – окружная сила, Н; |
|
|
|
|
|||
N– мощность, Вт; |
|
|
|
|
|||
C – коэффициент, учитывающий влияние угла обхвата; |
|||||||
CV – скоростной коэффициент; |
|
|
|||||
K – |
коэффициент |
динамичности и |
режима работы |
(K = 1 1,6);
Z – число ремней. Обычно Z = 8 12.
Коэффициенты выбираются по таблицам (см. табл.24, 25,
26 [1]).
-нагрузка на валы (рис. 8.7).
Рис. 8.7
123
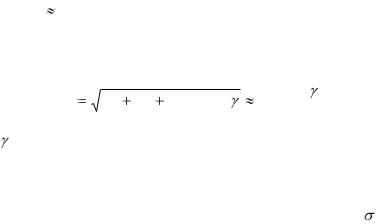
Силы, возникающие в ременной передаче необходимо знать для расчета шкивов, валов, опор. Принимают, что материал ремней следует закону Гука.
Тогда после приложения полезной нагрузки сумма натяжений ветвей остаѐтся постоянной. Если ветви ремня параллельны (u 1), то сила
Q = 2S0.
Если ветви ремня не параллельны, то:
Q |
S 2 |
S 2 |
2S S |
2 |
cos |
2S |
0 |
cos |
|
, |
|
||||||||||
|
1 |
2 |
1 |
|
|
2 |
|
|||
|
|
|
|
|
|
|
|
|
где – угол между ветвями ремня.
Так как обычно усилие натяжения не контролируется в передачах с не смещаемыми осями валов, его устанавливают с запасом и оно сохраняется до вытягивания ремня. Поэтому при расчете максимальных сил на валы рекомендуется S0 и 0 увеличить в 1,5 раза.
9. 3АКЛЕПОЧНЫЕ СОЕДИНЕНИЯ
Соединительными деталями в заклепочном соединении являются заклепки. Во избежание электрохимической коррозии, материал заклепок выбирают однородным с материалом соединяемых деталей. Диаметр заклепок d обычно выбирают в зависимости от толщины соединяемых деталей δ в пределах d = (1,5…2)δmin. Отверстия под заклепки выполняют несколько большего диаметра. Шаг заклепочного ряда t выбирают по соотношению t = (3...6)d . Расстояние от заклепок первого ряда до свободной кромки детали в направлении действующей силы e = (1,5...2) d; в перпендикулярном направлении e= (1,2...1,5)d.
Расчеты на прочность основаны на следующих допуще-
ниях:
нагрузка на соединения распределяется между всеми заклепками равномерно;
124
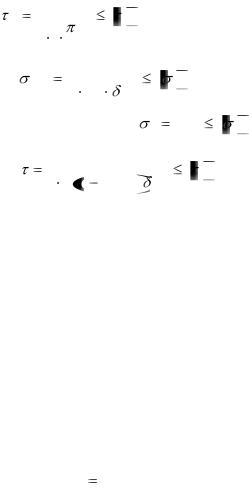
силы трения между соединяемыми элементами не учитываются;
напряжения смятия в каждой точке контакта заклепки и детали по величине одинаковы.
Условия прочности записываются в следующем виде:
заклепок на срез |
|
|
|
|
|
P |
|
|
; |
|
|
|
|||
ср |
|
|
|
|
|
|
|
|
|
|
|
|
|
||
|
|
|
|
2 |
|
|
ср |
|
|
||||||
|
|
|
|
|
|
|
d0 |
|
|
|
|
||||
|
|
|
|
|
|
|
|
|
|
|
|
|
|
||
|
|
|
z i |
|
|
|
|
|
|
|
|
|
|
||
|
|
4 |
|
|
|
|
|
|
|
|
|||||
|
|
|
|
|
|
|
|
|
|
|
|
|
|
||
заклепок на снятие |
|
|
|
|
|
|
|
P |
|
|
см ; |
|
|||
см |
|
|
|
|
|
|
|
|
|
|
|||||
|
|
z d0 |
min |
|
|
|
|||||||||
|
|
|
|
|
|
|
|
|
|
|
|||||
соединяемых деталей на растяжение |
|
|
PHT |
; |
|||||||||||
р |
|
||||||||||||||
|
|
|
|
|
|
|
|
|
|
|
|
FHT |
p |
||
|
|
|
|
|
|
|
|
|
|
|
|
|
|
||
|
|
|
|
|
|
|
|
|
|
|
|
|
|
|
|
на срез края детали |
|
|
|
|
|
|
|
|
P |
|
|
|
, |
||
|
|
|
|
|
|
|
|
|
|
|
|
|
|||
|
|
|
z 2 e |
0,5d0 |
min |
|
|||||||||
|
|
|
|
|
|
|
где Р – нагрузка на соединение;
z – число заклепок (на соединяемой детали), воспринимающих нагрузку Р;
i – число плоскостей среза одной заклепки; d0 – диаметр отверстия под заклепку;
Fнт – площадь поперечного сечения детали, наиболее ослабленного отверстиями под заклепки
Fнт = δmin (b – zнт d0);
b – ширина листа;
δmin – толщина самой тонкой из соединяемых деталей; zнт – число заклепок в поперечном сечении детали;
Pнт – нагрузка, действующая в поперечном сечении детали, наиболее ослабленном отверстиями под заклепки
P |
P |
z |
|
. |
|
НТ |
|||
НТ |
z |
|
||
|
|
|
Коэффициент ослабления листа отверстиями под заклепки определяется:
125
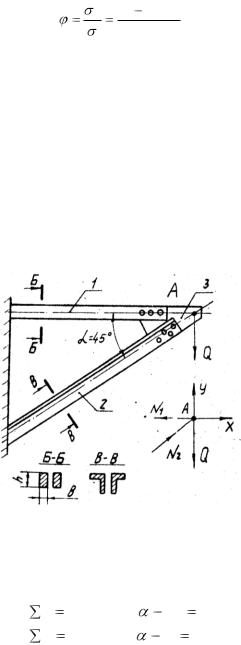
/ ( b z d0 )
b
где – напряжение в ослабленном сечении; b – ширина листа. Ниже рассмотрены примеры расчета при статическом
действии нагрузок на заклепочные соединения.
Пример 1.
Рассчитать заклепочное соединение узла А (рис.9.1). Тяга 1, состоящая из двух стержней прямоугольного поперечного сечения, укосина 2 – из двух неравнополочных уголков и пластина (3) толщиной 8 мм изготовлены из стали Ст.3. [σ]р = 160 МПа; [σ]см = 320
МПа; [τ]ср = 140 МПа; табл.1.2 [1]. Нагрузка Q = 40 кН.
Рис. 9.1 Соединение узла А
Решение
Из условий равновесия узла А:
x |
0; |
N2 cos |
N1 |
0; |
y |
0; |
N2 sin |
Q |
0 |
|
|
126 |
|
|
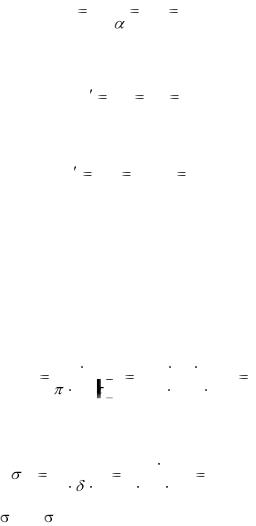
определены нормальные силы N1 и N2, действующие на тягу и укосину.
N1 = Q ctgα = 40
1 = 40 кН.
N |
|
Q |
40 |
57,06 кН . |
||
2 |
|
|
|
|||
sin |
0,7 |
|||||
|
|
|
На каждый из двух стержней тяги (1) действует растягивающая нормальная сила
N1 |
N1 |
|
40 |
20 кН . |
|
2 |
|
2 |
|
||
|
|
|
На каждый уголок косынки (2) действует сжимающая сила
N |
|
N2 |
|
57,06 |
28,5 кН . |
2 |
2 |
2 |
|||
|
|
|
Выбираем материал заклепок – Ст.3.
Толщину стержня тяги в (Рис. 9.1) принимаем равной половине толщины пластины 3 , т.е. в = 4 мм.
По табл. 9 [1] выбираем диаметр заклепок d = 8 мм; шаг заклепочного ряда t = 3,5 d = 3,5
8 = 28 мм.
Для соединения тяги и пластины определяем необходимое число заклепок по условию их прочности на срез. Так как каждая заклепка имеет две плоскости среза, то
z1 |
2 N1 |
|
|
2 |
40 10 |
2,85 |
||
d 2 |
ср |
3,14 |
0,82 |
140 |
||||
|
|
|||||||
|
|
|
|
|
|
|
Принимаем z1 = 3.
Проверяем заклепки на смятие,
|
N1 |
|
|
40 10 |
208,3 МПа, |
|
см |
z1 |
d 3 0,8 0,8 |
||||
|
||||||
|
|
Т.к. см < [ ]см – условие прочности выполнено.
127
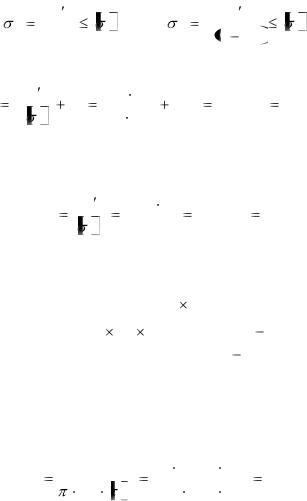
Диаметр отверстия под заклепки d0 выбираем в табл. 1.1.[5], т.е. d0 = 8,5 мм. Расстояние ℓ1 от оси крайней заклепки до кромки тяги в направлении действующей силы принимаем
ℓ1 = 1,5d = 1,58 = 12 мм.
Определяем высоту стержня тяги h (Рис. 9.1) из условия прочности на растяжение в сечении, ослабленном отверстиями под заклепки
|
N1 |
или P |
N1 |
|
|
|
P |
|
P |
|
|
P |
|
|
Fнетто |
|
b h d |
0 |
|
Откуда
h |
|
N1 |
|
d |
|
20 10 |
|
0,85 3,95 см 39,5 мм |
b |
|
|
0 |
0,4 160 |
||||
|
|
P |
|
|
||||
|
|
|
|
|
|
|
Принимаем h = 40 мм.
Из условия прочности на сжатие определяем требуемую площадь поперечного сечения уголка
F |
N |
2 20,5 10 |
1,78 см |
2 |
178 мм |
2 |
||
|
сж |
|
160 |
|
|
|||
|
|
|
|
|
|
|||
|
|
|
|
|
|
|
|
При этом предполагаем, что продольная гибкость укосины достаточна, и потеря устойчивости не наблюдается.
По сортаменту ГОСТ 19772-74 выбираем уголок неравнополочный с размерами полок 40 32 мм и толщиной 4 мм:
Уголок |
40 32 4 ГОСТ 19772 74 |
|
Ст3 ГОСТ 11474 76 |
||
|
С площадью поперечного сечения F = 2,00 см2 = 200 мм2. Для соединения укосины 2 с пластиной 3 выбираем диа-
метр заклѐпок d = 8 мм. Определяем необходимое число заклепок из условия прочности их на срез:
z |
|
N2 |
|
|
2 57,06 10 |
4,07 |
|
2 |
d 2 |
|
3,14 0,82 |
140 |
|||
|
|
ср |
|
||||
|
|
|
|
|
|
|
|
|
|
|
|
128 |
|
|