
3109
.pdf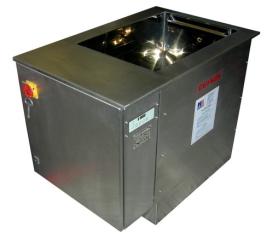
Рис. 33. Ультразвуковая ванна KS300 Mk3
Основными загрязнениями обычно являются следы масел, жира, отпечатки пальцев, пушинки, разнообразные пылевые частицы.
Последовательность операций предварительной очистки может изменяться в широких пределах, а для окончательной, наоборот, должна оставаться неизменной.
Химическая окончательная очистка предусматривает ультразвуковую мойку в горячей воде с растворенным в ней моющим средством, а затем длительное промывание в горячей воде наивысшей достижимой чистоты.
5.2. Металлизация звукопроводов
Независимо от выбранного метода последующего формирования встречно-штыревых структур преобразователей, на поверхность звукопроводов должно быть нанесено проводящее покрытие, к которому предъявляются требования минимального электрического сопротивления, высокой адгезии, однородности по структуре, составу, толщине, отсутствия проколов, наплывов, царапин, коррозионной стойкости, хорошей растворимости в травителе,
81
технологичности, стабильности основных физико-химических свойств пленки от партии к партии. Дополнительными требованиями являются: малое различие акустических сопротивлений материала металлизации Zм и звукопровода Zз, низкая удельная плотность во избежание сильных отражений и слабые дисперсионные свойства.
Для получения хорошей адгезии и воспроизводимости электрофизических свойств нанесенных металлических пленок поверхность звукопровода как отмечалось выше должна быть хорошо очищена, причем способ очистки в большей степени зависит от метода последующей металлизации.
Наиболее широко при изготовлении фильтров и резонаторов ПАВ используются алюминий, серебро, золото, иногда медь с защитой никелем. Учитывая, что алюминий не дорогой и позволяет получить сравнительно низкое сопротивление пленочных проводников, в фильтрах ПАВ как со звукопроводами из кварца, так и ниобата лития, наиболее часто используется алюминиевое покрытие. Медное или золотое покрытие с подслоем хрома хорошо сочетается с германатом висмута.
С целью получения хорошей электропроводности при незначительных дисперсионных искажениях и для надежности присоединения золотых проводников, например, методом сварки со сдвоенным электродом толщину пленки контактных шин следует выбирать в пределах 250…300 нм. Толщина электродов ВШП может быть уменьшена до 100…200 нм. Для улучшения адгезии алюминия целесообразно использовать подслой ванадия толщиной 30 нм, что позволяет обойтись одним травителем и проводить только одноэтапную фотолитографию.
Для осаждения пленок из алюминия, меди, золота, серебра наиболее часто используется термовакуумное напыление.
Применение электронно-лучевого испарения из тигля этих материалов, например алюминия, позволяет существенно
82
улучшить адгезию к поверхности звукопровода и отказаться от адгезионного подслоя.
Катодное и магнетронное распыление также используется для получения пленок тугоплавких металлов. Химическое осаждение применяется, главным образом, для металлизации крупногабаритных звукопроводов длиной свыше 100…180 мм.
При термовакуумном напылении, например, алюминия на ниобат лития или кварц, очищенные звукопроводы сначала прогреваются при температуре 250 ±10°С в течение 10 ±1 мин для удаления мономолекулярных загрязнений, а также для снятия механических напряжений и выравнивания потенциального рельефа поверхности.
Для большинства пьезокерамик недопустим перегрев выше 100…430 °С. После этого звукопроводы охлаждаются до температуры 130 ±10 °С с целью получения малого удельного сопротивления напыляемых слоев ванадия и алюминия, и производится распыление указанных материалов.
Рассмотрим формирование ПАВ структур резонаторов с использованием кварцевых пластин. Перед процессом металлизации, на поверхность под электроды, для повышения электропроводности и адгезии металлического слоя и подложки наносят слой ванадия, толщиной в 4·10-8м, что позволяет применить одноэтапную фотолитографию при одном травителе. Нанесение металлических слоев, как алюминия, так и ванадия производится осаждением методом термовакуумного напыления. При осаждении методом термовакуумного напыления необходимо стремится к получению максимально тонкого металлического слоя при сохранении его проводящих свойств. Для этого, перед напылением, звукопровод сперва необходимо прогреть в течение 10 минут при температуре 300°С для снятия механических напряжений, удаления мономолекулярных загрязнений и выравнивания рельефа поверхности. За операцией прогрева следует охлаждение подложки до температуры 120°С с целью получения малого удельного сопротивления напыляемых слоев ванадия и алюминия. Распыление металлов можно производить на
83
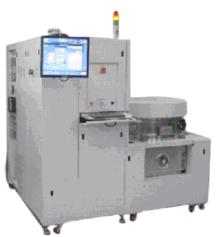
установке термовакуумного распыления SC-1000, внешний вид которой приведен на рис. 34. Данное оборудование состоит из двух модулей: рабочей камеры и модуля управления. Модуль управления включает в себя вакуумметр для проверки внутреннего давления в рабочей камере и монитор криогенных температур. Контроллер служит для управления толщиной напыления пленок
Рис. 34. Внешний вид установки термовакуумного распыления SC-1000
Перед нанесением металлического слоя необходимо тщательно очистить подложку, чтобы обеспечить наилучший контакт электродов с ее поверхностью. Использование тех или иных способов очистки и средств зависит от материала подложки и технологии нанесения металлического покрытия. Чаще всего используют химические и ультразвуковые способы.
Нанесение электродных покрытий, производится благодаря входящему в состав оборудования, специальному программному обеспечению. Это программное обеспечение позволяет напылять электроды нужной нам толщины (250 нм) и по требуемым координатам.
84
5.3. Методы изготовления встречно-штыревых структур фильтров на поверхностных акустических волнах
Технология изготовления структур фильтров ПАВ сводится к формированию заданной конфигурации металлических электродов и контактных шин. Для наиболее освоенного диапазона частот от 15 до 1000 МГц ширина электродов колеблется от 1 до 50 мкм для одиночных штырей и от 0.8 до 25 мкм для расщепленных штырей; длина электродов составляет 1…10 мм, а общее количество электродов изменяется от 20 – 100 до 400 − 600. Число преобразователей, размещенных на одном звукопроводе, может достигать шести. Общее поле, занимаемое встречно-штыревыми структурами, составляет от 1× 1 мм2 до 30 × 100 мм2. При этом к качеству структур ВШП предъявляются весьма жесткие требования. Для большинства фильтров (особенно широкополосных) практически не допускаются обрывы электродов, наиболее опасные в области центрального лепестка встречно-штыревой структуры. Не допускаются замыкания электродов в зоне их взаимного перекрытия, вне этой зоны возможно наличие не более трех – пяти дефектов типа «островок», замыкающих три
– пять электродов преобразователя. Допуски на размеры контактных шин и площадок, а также на расстояние между отдельными преобразователями составляют 5…10 мкм, т.е. сравнимы с допусками на размеры элементов интегральных микросхем. Несоосность расположения встречно-штыревых структур относительно базовой кромки звукопровода или относительно друг друга допускается в пределах ±(5…20)'. Допуски на размеры электродов ВШП почти на порядок жестче допусков на размеры элементов тонкопленочных интегральных микросхем.
Так для получения затухания боковых лепестков АЧХ фильтра до aб =(50…60) дБ заданную ширину электродов
необходимо выдерживать с точностью не хуже ±(0,5…0,8) мкм, а длину электродов и их шаг, соответственно, не хуже
±(0,5…1,2) и ±(0,2…0,5) мкм. Принципиально для 85
формирования встречно-штыревых структур фильтров ПАВ , отвечающих перечисленным требованиям, можно использовать те же методы, что и для получения заданной конфигурации элементов интегральных микросхем по планарной технологии: фотолитографию (с зазором, контактную, проекционную); голографию; лучевую обработку (пучком ионов, лучом лазера, рентгеновским пучком, растровую и проекционную обработку электронным пучком). Рассмотрим достоинства и недостатки перечисленных методов.
При изготовлении уникальных устройств обработки сигналов на ПАВ иногда используется механическая нарезка металлического покрытия, нанесенного непосредственно на звукопровод. Использование этого метода позволяет создавать структуры с рабочими полями до 100 × 300 мм2 . Однако реализуемая при этом методе точность ±(2…4) мкм явно недостаточна для качественных фильтров ПАВ. Для изготовления устройств на ПАВ более целесообразно использовать метод фотолитографии, иллюстрируемый на рис. 35. Подложку тщательно полируют для получения оптически плоской поверхности, а затем очищают от посторонних частиц и обезжиривают. После этого с помощью вакуумного испарения или магнетронного напыления напыляют пленку алюминия (рис. 35 а) толщиной 0,1…0,3 мкм. Для улучшения адгезии часто для алюминиевых пленок по соображениям простоты химического травления используют предварительно подслой ванадия, а тонкий подслой хрома применяют для золотых и медных пленок. На следующем этапе образец покрывают фоторезистом − раствором фоточувствительного полимера и вращают с большой скоростью, стремясь получить тонкий однородный слой. Затем фоторезист укрепляют термической сушкой и экспонируют в ультрафиолетовом излучении через фотошаблон (рис. 35 б). На фотошаблоне имеются непрозрачные области из фотоэмульсии или пленки хрома, соответствующие топологии металлизации изделия. В экспонированных областях фоторезиста происходят химические изменения, позволяющие впоследствии удалить их
86
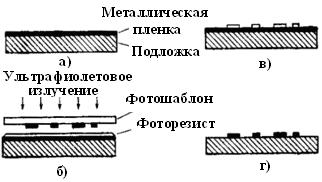
проявляющим раствором (рис. 35 в). Области металла, не защищенные фоторезистом, удаляют химическим травлением. Наконец, оставшийся фоторезист растворяют, оставляя на подложке металлический рисунок, соответствующий рисунку на фотошаблоне (рис. 35 г). С помощью этого процесса можно воспроизводить полоски шириной до 1,0 мкм, что соответствует рабочей частоте ВШП около 1,0 ГГц. Наиболее ответственная стадия процесса − оптическая экспозиция, при которой фотошаблон должен плотно прилегать к образцу. Обычно для этой цели используют промышленные установки совмещения. Из-за анизотропии подложки часто требуется высокая точность углового совмещения фотошаблона и образца, обычно 1° и менее.
Рис. 35. Этапы изготовления фильтров на ПАВ методом фотолитографии
Известно, что основной причиной ограничения разрешающей способности фотолитографии являются дифракция светового луча, ошибки при оптической передаче изображения на звукопровод из-за сферической абберации, астигматизма и так далее, а также ошибки при химических операциях проявления, травления, особенно при больших рабочих полях. Для обеспечения необходимой разрешающей способности на большой площади в настоящее время разрабатываются голографические методы, позволяющие упростить процесс фотолитографии и избежать применения
87
высокоразрешающих объективов. Достигнутое разрешение до 200 нм на большом поле и крайне низкий уровень искажений вполне удовлетворяют требованиям технологии изготовления большинства высокочастотных устройств на ПАВ.
Рассмотрим более подробно нанесение и экспонирование методом контактного проецирования через фотошаблон. При этом могут быть использованы различные фоторезисты. Фоторезисты представляют собой фоточувствительные вещества, которые в жидком состоянии наносят на чистую полированную поверхность пластины (либо на поверхность, уже покрытую металлическим слоем). Жидкие фоторезисты незаменимы в производстве элементов с высокой степенью монтажа (разрешение элементов до 10 микрон). В последнем случае применение жидких фоторезистов удешевляет процесс, что существенно для среднесерийного производства. После засыхания эти вещества образуют тонкий равномерный слой, плотно прилегающий к подложке.
Основными требованиями, предъявляемыми к фоторезисту, являются его способность равномерно покрывать пластину, сохранять свои размеры после соответствующей обработки и устойчивость к средствам травления. После выполнения своих функций фоторезист должен без остатка удаляться с подложки с помощью подходящего растворителя. В качестве используемого, может быть выбран фоторезист Российской фирмы ФП-27-18 БС. Он соответствует всем изложенным требованиям.
На практике используют негативные и позитивные фоторезисты. Негативный рабочий фоторезист не растворим после экспонирования, в то время как в местах, защищенных до экспонирования, фоторезист растворяется при погружении в проявитель (из позитивного фотошаблона после проявления возникает негативная маска). Позитивные фоторезисты характеризуются обратным действием. На экспонированной поверхности позитивные фоторезисты растворяются в проявителе. Из позитивных фоторезистов наиболее распространены композиции, содержащие в качестве
88
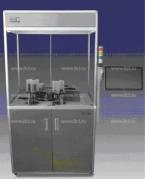
светочувствительного компонента сульфоэфиры на фгохинондиазиде (5-40% по массе), а в качестве пленкообразователя - новолачные смолы (до 50%). При экспонировании сульфоэфир переходит в сульфопроизводноеинденкарбоновой кислоты и при проявлении под действием водно-щелочного растворителя удаляется с экспонированных участков поверхности вместе со смолой. Позитивные фоторезисты чувствительны к экспозиции 10-250 мДж/см2, имеют разрешающую способность 0,1-2,0 мкм, контрастность 1,5-5, теплостойкость 120-140 0С ; негативные фоторезисты, как правило, более чувствительны, но имеют худшую разрешающую способность. Перед использованием необходимо добиться однородности фоторезиста фильтрацией и с помощью автоматической установки нанесения фоторезиста УНФ-150А российского производства, внешний вид которой представлен на рис. 36.
Рис. 36. Установка нанесения фоторезиста УНФ-150А
В состав установки входит: модуль центрифугирования; модуль термообработки; транспортный робот-манипулятор; модуль загрузки и выгрузки пластин; система управления установкой; модуль термостабилизации фоторезиста; защитный бокс. Установка обеспечивает: подачу раствора полимера на пластину в статическом и динамическом режимах (сканирование); подачу раствора полимера в любую заданную точку пластины; подачу раствора полимера дозатором;
89
стабилизацию и регулирование температуры раствора полимера; автоматическую промывку ванны растворителем. Нанесение фоторезиста осуществляется преимущественно разбрызгиванием. Путем разбрызгивания с применением центрифуги. Нанесенный слой сначала подсушивают в естественных условиях в течение 5 — 10 мин, так чтобы не образовались неровности на поверхности, а затем досушивают при повышенной температуре. После тепловой обработки следует экспонирование в течение 1-10 с. Самым перспективным оборудованием представляется автоматическая установка экспонирования SFB-520 разработанной зарубежной фирмой SUN-FUBAO ELECTRONICS CO для двух и одностороннего экспонирования жидкой и сухой паяльной маски, а также для экспонирования всех типов сухих и мокрых фоторезистов, которая в соответствии с программой ЭВМ осуществляет экспонирование в заданном масштабе. Она обеспечивает согласование нужной формы световых пучков и движений стола с фотографической пластиной на нем, что дает возможность получить нужный рисунок. При этом уменьшается число последовательных операций, требуемых при изготовлении фотоматриц классическим способом. Кроме того, исчезает необходимость в использовании координатографа и редукционных фотокамер. Система экспонирования имеет две вакуумные загрузочные рамы типа «майлар-стекло». Для обеспечения плотного контакта между фотошаблоном и заготовкой применяется откачка воздуха внутри загрузочной рамы встроенным вакуумным насосом. Внешний вид установки представлен на рис. 37. В установке используются две ртутные дуговые лампы по 5 кВт. Охлаждение ламп осуществляется встроенной системой водяного охлаждения, имеющей собственную емкость, циркуляционный насос и теплообменник для подачи внешней охлаждающей воды (водопроводная вода, либо дополнительный внешний чиллер).
Охлаждение рабочей зоны рам экспонирования осуществляется встроенной холодильной системой
90