
2101
.pdf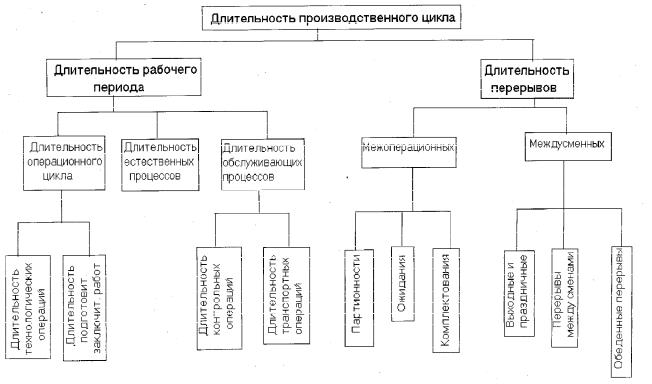
Рис 3.2. Д лительность производственного цикла
Междусменные перер ывы определяются принятым календарным режимом работы. Условно сюда могут быть отнесены обеденные перерывы. Следовательно, длительность производственного цикла Тц определяется по формуле
Тц=Топ+Тест+Ттр+Тк+Тпер. (3.1)
Но это пригодно только для Тц. одного цеха. Но на наших заводах в (Тц) участвуют несколько цехов, и складывать все их (Тц.) в принципе неверно, так как многие из них выполняются одновременно. Поэтому для определения суммарного То.ц. необходимо разработать цикловой график, характеризующий То.ц. каждого цеха и их совместимость во времени.
3.6.Виды движения предметов труда между рабочими местами (постами)
При определении длительности многооперационного циккла необходимо учитывать степень одновременности (параллельности) обработки изделий на разных операциях технологического процесса. Эта степень зависит от метода сочетания во времени выполнения операций на постах (входящих в процесс). Существуют три метода сочетания операций или три вида двиижения предме-
20

тов труда с предыдущей операции на последующую:
1)последовательный;
2)параллельный;
3)последовательно-параллельный.
Сущность последовательности в движении заключается в том, что каждая последующая операция начинается только после окончания обработки всей партии на предыдущей операции. Пример графика последовательного вида движения представлен на рис. 3.3.
|
|
|
|
|
|
|
|
|
|
|
|
Рабочее |
1 |
2 |
3 |
4 |
|
|
|
|
|
|
|
|
время |
|
|
|
|
|
|
|
|
|
||||
1 |
nt1 |
|
|
1 2 |
3 4 |
|
|
|
|
|
|
|
|
|
|
|
|
|
|
|
|
||||
|
|
|
|
|
|
|
|
|
|
|||
2 |
|
|
|
nt2 |
1 |
2 |
3 |
4 |
|
|
|
|
|
|
|
|
|
|
|
||||||
|
|
|
|
|
|
|
|
|||||
3 |
|
|
|
|
|
|
nt3 |
|
1 2 3 4 |
|
||
|
|
|
|
|
|
|
|
|||||
|
|
|
|
|
|
|
|
|
||||
4 |
|
|
|
Тпослоп. . |
|
|
|
|
|
|
|
|
|
|
|
|
|
|
|
|
|
|
|||
|
|
|
|
|
|
|
|
nt4 |
|
|
||
|
|
|
|
|
|
|
|
|
|
|||
|
|
|
|
|
|
|
|
|
|
|
|
|
|
|
|
|
|
|
|
|
|
|
|
|
|
|
|
|
|
|
|
|
|
|
|
|
|
|
N поста (операции)
Рис 3.3. Пример графика последовательного вида движения рабочих по операциям над партией из четырех предметов труда
n – количество изделий в партии; ti – норма времени;
Применяется, например, в кассетном производстве в формовочном
цехе.
Параллельный вид движения характеризуется полным отсутствием (или незначительной величиной) перерывов. Изделия передаются на следующую операцию сразу после окончания предыдущей. Пример графика параллельного вида движения представлен на рис. 3.4.
Применяется в конвейерном производстве или в поточно-агрегатном. Характеризуется самой короткой продолжительностью Топ., но есть и недостатки – имеются перерывы, влекущие простои оборудования и рабочих. Исключение составляет один частный случай, при котором нормы времени равны или кратны, тогда, устанавливая нужное количество рабочих на соответствующих операциях, длительность их приравнивается.
Последовательно-параллельный вид движения предусматривает такое частичное совмещение времени выполнения смежных операций, когда вся изготавливаемая партия проходит через каждую операцию без перерывов.
21

|
1 |
2 |
3 |
4 |
|
|
|
|
|
|
1 |
|
|
|
|
|
|
|
nt1 |
|
|
|
|
1 |
2 |
3 |
4 |
nt2 |
|
|||
|
|
|||||||||
|
|
|
|
|
||||||
2 |
|
|
|
1 |
2 |
3 |
4 |
nt3 |
||
|
|
|||||||||
|
|
|
|
|
||||||
3 |
|
|
|
|
|
|
|
|
|
|
|
|
|
|
|
1 |
2 |
3 |
4 |
nt4 |
|
4 |
N поста |
Т |
послоп. . |
|
|
|
|
|||
|
|
|
|
|
|
|||||
|
|
|
|
|
|
|
|
|||
|
(операции) |
|
|
|
|
|
|
Рабочее
время
Рис.3.4. Пример график параллельного вида движения рабочих по операциям над партией из четырех предметов труда
Необходимо различать два основных варианта последовательнопараллельного сочетания каждой пары смежных операций:
-операционный цикл предшествующей операции меньше последующей;
-операционный цикл предшествующей операции больше последующей. Пример графика параллельно-последовательного вида движения рабочих представлен на рис. 3.5.
|
|
|
|
|
|
|
Рабочее |
1 |
2 |
3 |
4 |
|
|
|
время |
|
|
|
|
||||
1 |
|
|
|
|
|
|
t1>t2 |
|
nt1 |
|
|
|
|
|
|
|
|
1 2 3 4 |
|
|
|
|
|
2 |
|
|
|
|
|
t2<t3 |
|
|
|
nt2 |
|
|
|
||
|
|
|
|
|
|
|
|
|
|
|
1 |
2 |
3 |
4 |
t3>t4 |
3
nt3
1 2 3 4
4
nt4
N поста (операции)
Рис.3.5. Пример графика параллельно-параллельного вида движения рабочих
22
3.7.Пути сокращения длительности производственного цикла
Длительность производственного цикла включает длительность рабочего периода, транспортных контрольных операций и перерывов.
Тпр.ц.=Топ.ц.+Ттр.+Тконт.+Тест.+Тперер. (5.1)
Сокращение длительности производственного цикла способствует улучшению основных технико-экономических показателей предприятия.
Предприятия в настоящее время являются коммерческими организациями. Цель их деятельности – получение максимальной прибыли. Чтобы ее получать, нужны эффективные производственные структуры в целом по предприятию, современные автоматизированные технологические линии, рациональные составы бетона и т. д., целесообразное сочетание во времени основных и вспомогательных операций. Основной производственный процесс должен быть построен по принципам специализации, пропорциональности, прямоточности, непрерывности, ритмичности, компактности. Необходимо стремиться к сокращению длительности производственного цикла. Напомню, что длительность производственного цикла включает длительность рабочего периода и перерывов. Рабочий период состоит из длительности технологических операций, подготовки заключительных работ, транспортных и контрольных операций.
Тпр.ц.=Топ.ц.+Ттр.+Тконтр.+Тест.+Тперер. (3.4)
В результате сокращения длительности производственного цикла увеличивается выпуск продукции, повышается оборачиваемость камер тепловой обработки, использование производственных площадей и т. д. В конечном итоге увеличивается фондоотдача, производительность труда, снижается себестоимость, повышается рентабельность производства. Сокращение длительности производственного цикла должно идти по путям сокращения длительности: Топ.ц., Ттр., Тконтр., Тест., Тпер.
Сокращение длительности операционных циклов достигается путем совершенствования технологических процессов, повышения технологичности конструкции изделия. Под совершенствованием технологических процессов понимается их комплексная механизация и автоматизация, внедрение скоростных режимов, применение прогрессивных технологических процессов, а также концентрация операций. (Конвейерные линии, роторный конвейер, интенсификации режимов перемешивания и т. д.). Повышение технологичности конструкции заключается в максимальном приближении конструкции к требованиям технологического прогресса (изделия должны иметь такую конструкцию, чтобы удобно было формовать и т. д.).
Продолжительность транспортных операций может быть значительно
23
уменьшена в результате перепланировки, компоновки на основе принципа прямоточности механизации подъема и перемещения продукции.
Сокращение длительности контрольных операций достигается путем совмещения времени выполнения технологических и контрольных операций, механизации, внедрения статистических методов контроля.
Длительность естественных процессов сокращается в результате замены их соответствующими технологическими операциями. Например, естественное твердение изделий может быть заменено тепловлажностной обработкой.
На многих предприятиях значительная часть производственного цикла (иногда до 90 %) приходится на разнообразные перерывы (организационные, комплектования, партионности, междусменные и т.д.). Ликвидация или уменьшение их длительности до возможного минимума позволяет существенно сократить длительность производственного цикла.
Время межоперационных перерывов значительно сокращается при переходе от последовательного к параллельно-последовательному виду движения, а также в результате территориального сближения технологических постов.
Полным отсутствием партионности и ожидания характеризуется только непрерывно-поточное производство (параллельный вид движения предметов труда).
Внедрение поточных методов является одним из наиболее эффективных и широко используемых заводами средств для сокращения длительности производственного цикла.
Величина междусменных перерывов может быть снижена даже в рамках принятого режима смежности. Например, в большинстве случаев в ночной перерыв, как правило, происходит тепловлажностная обработка изделий.
Для вскрытия резервов сокращения длительности производственных циклов прибегают к фотографии производственного цикла, к хронометражным наблюдениям за технологическими операциями.
ТЕМА 4. ОСНОВЫ ПРОЕКТИРОВАНИЯ ОСНОВНОГО ВЫСОКОКАЧЕСТВЕННОГО ПРОИЗВОДСТВА
4.1.Понятие о поточном производстве
Поточным производством называется такая форма организации производства, которая основана на ритмичной повторяемости согласованных во времени основных и вспомогательных операций, выполняемых на специализированных рабочих местах, расположенных в последовательности операций технологического процесса.
Для поточного производства характерны уже рассмотренные нами принципы: специализации, прямоточности, непрерывности, параллельности и ритмичности. Оно делится на однопредметное и многопредметное. Однопредметное и многопредметное поточное производство может быть непрерыв-
24
но-поточным и прерывно-поточным (нет равенства производительности на всех операциях). Загрузка оборудования и рабочих мест непостоянная. Технологическая линия работает с заделом между постами. Принцип ритмичности оценивается тактом или ритмом линии. Это интервал времени выпуска с линии одного или партии изделий. Различаются линии с регламентированным и свободным режимом. Первые характерны для непрерывного производства. Ритм здесь поддерживается при помощи конвейеров или звуковой сигнализации. Вторые не имеют технических средств, строго регламентирующих ритм работы. Соблюдение ритма возлагается непосредственно на работников линии.
Транспортные средства:
-непрерывного действия (приводные конвейеры);
-бесприводные (рольганги, скаты и т. д.);
-подъемно-транспортное оборудование циклического действия (мостовые и др. краны, электротележки и др.).
4.2.Синхронизации технологического процесса
При рациональной организации технологического процесса (обеспечение непрерывности) необходимо стремиться к равенству продолжительностей технологических операций на местах. Они должны быть равны или кратны ритму работы линий. При организации производственных процессов необходимо выполнить их синхронизацию. Синхронизация – это процесс согласования длительности операций с тактом поточной линии. Она обеспечивает непрерывность технологического процесса. Для того, чтобы технологический процесс осуществлялся непрерывно, необходимо, чтобы продолжительность каждой операции была равна или кратна такту работы технологической линии.
Такт предприятия - интервал времени между выпуском двух смежных изделий (партий) одной номенклатуры на предприятии в соответствии с его производственной программой.
Такт поточной линии - интервал между выпуском двух смежных изделий (партий) одной номенклатуры на одной поточной линии.
Условия синхронизации следующие:
|
= |
|
= = |
|
= л. |
(4.1) |
|
|
|
|
где ti - норма времени на техническую операцию, чел-мин; сi - число рабочих на операции, человек;
rл - такт технологической линии, мин.
Синхронизация осуществляется путем изменения структуры операций и организационных условий их выполнения. Различают два её этапа:
1.Предварительный - выполняемый в период проектирования линий.
2.Окончательный - выполняемый во время отладки линий в цеховых
25
условиях.
Предварительная синхронизация достигается подбором: метода выполнения операций, оборудования, режимов обработки выполнения и структуры операций.
Например: 1) можно изменить количество операций, выполняемых на одном посту; 2) можно создать на одном посту несколько мест, на которых работы выполняют параллельно или последовательно; 3) можно осуществить техническое или технологическое совершенствование условий выполнения операций (сокращение числа переналадок, создание специальных транспортных устройств).
Однако расчленение смежных операций не всегда удается. Тогда применяют техническое совершенствование, предусматривающее сокращение продолжительности операций за счет усиления механизации, применения соответствующих приспособлений, повышения квалификации рабочих.
Создание параллельных или последовательных мест позволяет определенные виды работ выполнять одновременно на нескольких рабочих местах одного поста (например, формование одновременно на двух постах двумя бетоноукладчиками, установленными параллельно).
На первом этапе, как правило, не удается обеспечить такую синхронизацию процесса. Допускается отклонение в загрузке рабочих мест до 10% ( до - 110%). Эта недозагрузка или перегрузка может быть снята при отладке линии при окончательной синхронизации. Например, можно использовать средства малой механизации, внедрение совершенной оснастки, индивидуального подбора рабочих на перегруженные операции, материального стимулирования. При синхронизации необходимо учитывать также не только продолжительность выполнения основных операций, но и транспортирование, погрузочноразгрузочные работы.
Если синхронизация не удается, то приходиться осуществить прямоточное (прерывно-поточное) производство, т. е. проектирование линий с технологическими заделами и увеличенной длительностью производственного цикла. Однако может быть и частичная синхронизация, когда процесс осуществляется со значительными колебаниями времени на операциях. В этом случае создают не- прерывно-поточные линии со свободным ритмом. Для непрерывной работы на постах создают некоторый задел полуфабрикатов. На таких линиях могут быть использованы любые транспортные средства.
4.3.Основы расчета однопредметных непрерывно-поточных линий
Исходными данными для расчета непрерывно-поточной линии являются: программа запуска продукции за рассчитываемый период (месяц, сутки, смену). Nзап, фонды времени, нормы времени.
Nзап=Nвып* 100/( 100-а). |
(4.2) |
26 |
|

Nзап. - программа запуска изделий, шт.
Nвып. - программа выпуска изделий, шт.
а - технологические потери, % (например, в связи с изготовлением пробных изделий при наладке оборудования, расход на изготовление изделий для контрольных целей, потери в соответствии с нормами технологического проектирования).
Действительный фонд времени работы линии Fg определяется как разность календарного фонда времени и регламентированных перерывов для отдыха и профилактических мероприятий Тn.
Fg=Fk-Tn. |
(4.3) |
Выполнение заданного объема производства обеспечивается тактом (при партионной передаче - ритмом). Надо различать такт предприятия и такт работы линии. Это разные величины и понятия.
= |
|
. |
(4.4) |
зап |
|
Zn – такт предприятия
В связи с этим цикловой график необходимо разрабатывать для каждой линии в отдельности. Пример циклового графика рабочих операций представлен в таблице (табл. 4.1), а пример пооперационной схемы представлен на рис. 4.1.
смазка и сборка форм
подача арматуры
установка арматуры
подача бетонной смеси
формование
предварительная выдержка
тепловлажностная обработка
выгрузка форм с изделиями
распалубка
промежуточное складирование
Рис 4.4. Пример пооперационной схемы технологического процесса поточной линии производства дорожных плит
27

Таблица 4.1. Пример циклового графика рабочих операций изготовления дорожных
плит на поточно-агрегатной линии.
Время выполнения операции.
1Транспортирование смеси к посту формирования
2 |
Транспортировка арматуры |
|
|
|
|
|
|
|
|
|
|
|
|
||
|
к посту сборки |
|
|
|
|
|
|
3 |
Чистка, смазка и сборка |
|
|
|
|
|
|
|
формы |
|
|
|
|
|
|
4 |
Армирование |
|
|
|
|
|
Ткр |
5 |
Формирование |
|
|
|
|
|
|
|
|
|
|
|
|
||
6 |
Распалубка |
|
|
|
|
|
|
|
|
|
|
|
|
||
|
|
|
|
|
|
7Транспортирование изделий на склад
Пооперационная схема позволяет построить цикловой график, главной целью которого является определение минимальной длительности «критической» операции. Эта длительность необходима для определения такта выпуска одного изделия или ритма выпуска партии изделий на проектируемой поточной линии. При определении такта линии (rл) изучаются данные такта по нормам технологического проектирования ( ОНТП. 01...) и анализируется длительность критической операции (Ткр). Как правило, (rл) принимается равным (Ткр).
Количество непрерывно-поточных линий определяется по формуле
л = пл . |
(4.5) |
Если в расчете количество поточных линий - дробное число, то его приводят к ближайшему целому значению. Затем проверяют эффективность использования производственной мощности линий путем определения коэффициента их загрузки (ɳ)
|
л. |
(4.6) |
|
ɳ = |
|
. |
|
л.пр |
|
где: л. - количество линий расчетное;л.пр - количество линий принятое.
Значение коэффициента ɳ < 0,75 свидетельствует о недостаточной эффективности использования мощности принятого числа проектируемых линий и требует пересмотра циклового графика с сокращением длитель-
28
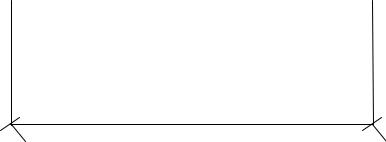
ности «критической» операции. Для этого необходимы целенаправленные новые технологические, технические и организационные решения. Количество рабочих на i-том посту определяется:
= |
|
(4.7) |
л. |
|
где: - расчетное количество рабочих; |
|
|
л - ритм линии. |
|
|
Расчетное количество рабочих приводят к ближайшему большему целому |
||
значению и определяют принятое количество рабочих( Сi прин). |
|
|
Коэффициент загрузки рабочих вычисляется по формуле |
|
|
расч |
∙ 100%. |
(4.8) |
ɳ = С прип |
|
На стадии расчета поточной линии допускаются предельные значения коэффициента загрузки ɳ от 90 до 110%. Поскольку для непрерывного производства используется конвейер, его скорость должна быть учтена при синхронизации линии путем включения длительности этой транспортной операции в норму времени операции на посту.
|
)* |
(м/мин). |
(4.9) |
|
'к = л |
|
|
где: Vк – |
скорость конвейера, м/мин. |
|
|
lo – |
шаг конвейера, м (т. е. расстояние между осями смежных изделий |
равномерно расположенных на конвейере). Расположение постов на конвейере представлено на рис. 4.2.
пост 1 |
|
пост 2 |
|
|
|
lo
|
Рис 4.2. Расположение постов на конвейере |
|
|||
|
60 |
|
(4.10) |
||
|
0проп. камеры = 4 |
|
|
∙ 6ест. ∙ )*8 : :сеч.. |
|
|
л |
|
|||
где: rл – ритм линии; |
|
|
|||
Тест – |
длительность естественных процессов; |
|
|||
nсеч – |
количество изделий по сечению камеры. |
|
Скорость конвейера должна обеспечивать не только его заданную произ-
29