
1463
.pdfванне химического состава, всплывание неметаллических частиц
и дегазация ее.
Основным преимуществом такой системы ковшей является то, что во время разливки шлаки почти не попадают в слитки,
задерживаются в ковше.
Для повышения качества стали в отдельных случаях раз- ливочные ковши после наполнения их металлом помещают в
вакуумные |
камеры |
(рис. 8 ). Под |
|
|
|
|
|
|
|
||||||||
вакуумом сталь более активно дега |
|
|
|
|
|
|
|
||||||||||
зируется |
и |
рафинируется. Иногда |
|
|
|
|
|
|
|
||||||||
разливку стали производят под ва |
|
|
|
|
|
|
|
||||||||||
куумом. |
|
стали |
в |
изложницы |
|
|
|
|
|
|
|
||||||
|
Разливку |
|
|
|
|
|
|
|
|||||||||
в зависимости от веса получаемого |
|
|
|
|
|
|
|
||||||||||
слитка производят сверху или снизу |
|
|
|
|
|
|
|
||||||||||
сифоннььм способом. |
Слитки |
|
полу |
|
|
|
|
|
|
|
|||||||
чают |
различного веса |
от |
1 0 0 |
|
кг до |
|
|
|
|
|
|
|
|||||
100 т и |
больше. |
Разливку |
|
стали |
|
|
|
|
|
|
|
||||||
производят |
также |
|
непрерывным |
|
|
|
|
|
|
|
|||||||
способом. |
|
|
|
|
|
применяют |
|
|
|
|
|
|
|
||||
в |
Для разливки стали |
|
|
|
|
|
|
|
|||||||||
основном |
чугунные |
изложницы |
|
|
|
|
|
|
|
||||||||
(рис. |
9). |
Разливку |
стали |
сверху |
Р и с . И . |
С и ф о н н а я |
р а з л и в |
||||||||||
(рис. |
1 0 ) производят для получения |
1 — поддон |
к а |
стали : |
|
2 — из |
|||||||||||
крупных слитков. При этом способе |
с |
ручьями; |
|||||||||||||||
ложницы; |
3 — центровой |
стояк; |
|||||||||||||||
разливки |
сталь из |
ковша заливают |
4 — центровые |
трубки; |
5 — цент |
||||||||||||
в каждую изложницу отдельно. Для |
ровой кирпич |
«звездочка»; 6 — |
|||||||||||||||
|
сифонные кирпичи; лейка |
|
|||||||||||||||
этого ковш с жидкой сталью пода- |
|
|
|
|
|
й так |
|||||||||||
ется |
краном |
к месту разливки и ставится над изложнице |
» |
||||||||||||||
чтобы отверстие разливочного стакана располагалось над |
^ |
||||||||||||||||
ром изложницы. Для образования меньшей усадочной раков |
^ |
||||||||||||||||
на изложницу устанавливают утеплительные надставки. |
|
||||||||||||||||
меньшего разбрызгивания металла и направления струи |
|
|
|||||||||||||||
зуются промежуточными воронками. |
11) |
|
|
|
пплуче- |
||||||||||||
|
Сифонную разливку стали |
|
(рис. |
применяют для |
|
J |
|||||||||||
|
|
|
|
|
|
|
Р |
днего веса.. Ддлия этогоJiui и |
стальV.*—— |
из- |
ковша |
||||||
НИЯ слитков мелкого и сре |
|
по |
" А |
" 1" ..... |
|
|
"-г,- |
|
|||||||||
выпускают в центральный стояк, от которого она отводится по |
|||||||||||||||||
литниковым каналам |
в расположенные на поддоне изложницы. |
||||||||||||||||
Обычно на п о д д о н |
у с т я « а1,„ |
|
|
з1е |
|
- ....... |
* |
иногда |
|||||||||
|
|
на п°ДД°не изло |
иногда |
||||||||||||||
и больше. |
|
|
|
|
|
вливают 2, 4, |
6 изложниц, |
а |
|||||||||
|
Разливка |
стали |
ceeDxv пп |
сРавнению с разливкой |
сифоном |
||||||||||||
обеспечивает |
получение к |
Л 0 |
|
||||||||||||||
ти |
слитка |
и |
меньшее |
|
,~.олее гоРячего металла в головной час- |
||||||||||||
в' нижней части его |
Сил |
Личество неметаллических включений |
|||||||||||||||
лее |
чистую поверхностью НЗЯ Разливка позволяет получить бо- |
||||||||||||||||
нижней части. |
|
|
слитка и более горячий металл в |
его |

Б последнее время на ряде заводов применяют непрерывную разливку стали. При непрерывной разливке стали получается большой выход годного металла и не требуется парка излож ниц. Непрерывную разливку стали производят на машинах вер тикального и горизонтального типа. Принципиальная схема вер тикальной машины приведена на рис. 12. Жидкая сталь из ковша 1 непрерывной струей поступает в промежуточное устрой ство 2. Из промежуточного устройства сталь направляется в кристаллизаторы 3, охлаждаемые водой. В каждый кристалли затор перед заливкой стали вставляется затравка, представляю щая собой подобие пробки из стали, которая внутри кристалли затора задерживает первые порции залитого металла. Залитая
сталь |
в кристаллизатор при |
соприкосновении |
со |
стенками его |
||
и затравкой |
быстро затвердевает, сцепляется |
с |
заготовкой |
и |
||
вместе |
с ней |
вытягивается |
из кристаллизаторов |
роликами |
5. |
Окончательное формирование слитка и затвердевание его про исходит при переходе его через зону вторичного охлаждения 4 водой ниже верхних роликов. Затвердевший слиток направля ется к тележкам резаками 6. Опускаясь вместе с тележками, слиток разрезается на заготовки мерной длины и по конвейеру через приемный стол направляется на склад.
Машина для непрерывной разливки стали горизонтального типа представляет собой два замкнутых конвейера, располо женных друг над другом. На конвейерах смонтированы чугунные полуформы. При движении конвейеров полуформы соединя ются, образуя как бы несколько форм по длине. В такую «фор му» сталь непрерывно заливается из ковша через промежуточное разливочное устройство. В формах сталь кристаллизуется и про исходит формирование слитка. Слиток из машины, проходя по ‘роликам, направляется к месту резки для получения мерных заготовок.
Строение стального слитка и его дефекты
Залитая в изложницу сталь охлаждается с различной ско ростью у стенок изложницы и внутри нее. У стенок изложницы скорость охлаждения стала больше, чем внутри, так как имеет ся большой перепад температур: 1540° С и выше (сталь) и 80— 100° С (изложницы). При соприкосновении стали с относитель но холодной изложницей образуется большое количество цент ров кристаллизации. Вокруг этих центров растут мелкие, рав номерные кристаллы, которые образуют наружный слой слитка.
Развитию роста кристаллов препятствует большое количест во образовавшихся центров кристаллизации и интенсивное ох лаждение стали с поверхности слитка. Вследствие образования первого слоя кристаллов объем металла уменьшается, а из ложница, нагреваясь, расширяется. По мере нагревания стенок
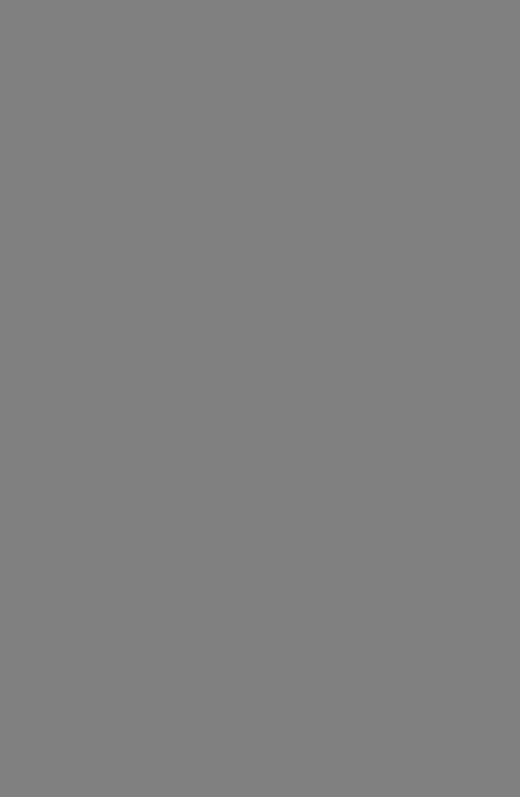
чего эти зоны по слитку как бы рассредоточиваются. Газовые пузыри в слитке кипящей стали во время обработки его давле нием завариваются. Следовательно, выход годного металла из слитка увеличивается.
В слитке, кроме указанных пороков, могут быть и другие, как например, трещины продольные и поперечные, газовые ра ковины, плены, засор. Образование трещин может быть вызва но развитием неравномерных напряжений при кристаллизации металла в изложнице и не свободной усадки его. Плены обра зуются обычно при заливке стали сверху вследствие разбрыз гивания ее. Засор попадает за счет разрушения огнеупорных материалов из ковша и разливочных устройств, используемых при подготовке изложниц к заливке сифонным способом. Газо вые раковины — результат выделения газо-в как из самого метал ла, так и из красок, нанесенных на внутреннюю полость излож ницы перед заливкой стали.
4. МЕТАЛЛУРГИЯ МЕДИ, АЛЮМИНИЯ, МАГНИЯ И ТИТАНА
Медь, алюминий и магний относятся к группе цветных ме таллов. Эти металлы широко применяются в машиностроении, что объясняется их особыми свойствами (пластичностью, малым удельным весом, большой удельной прочностью и др.), важны ми для многих деталей машин. Но вследствие их высокой стои мости, где возможно их заменяют черными металлами и други ми материалами.
Получение меди
Медь редко встречается в природе в виде самородной метал лической меди. Она входит в состав руд в виде сульфидных или окисных соединений. Медные руды обычно содержат 1—5% меди и подразделяются на сульфидные и окисные.
В сульфидных рудах медь может находиться в соединениях CuFeS2 (халькопирит), 5Cu3FeS • Fe2 S3 (борнит), CuS (ковенлин) и Cu2S (халькозин).
В окисленных рудах медь находится в соединениях Си20 (ку прит), СиС03 • Си(ОН) 2 (малахит), 2CuC03Cu(0H ) 2 (азурит)
иCuSi03 -2H20 (хризоккола) и др.
Врудах с самородной медью последняя находится в свобод ном виде.
Сульфидные руды являются основными исходными материа лами для получения меди. В СССР из этих руд получают до 80% меди. Руды обычно, кроме меди, содержат цинк, свинец, никель
идругие металлы. Богатые руды с содержанием меди 3% и выше подвергают непосредственной переплавке, а с меньшим содержа нием меди подвергают обогащению.
Окисленные медные руды с высоким содержанием меди (3— 5% и больше) переплавляют, а с содержанием до 3% меди
перерабатывают гидрометаллургическим способом. Из окислен ных руд добывают до 15% меди. Самородной меди из руд полу чают до 5%. Руды, содержащие самородную медь, также подвер гают обогащению, плавке или гидрометаллургической обработке.
Обогащение руд производят методом флотации. Флотация основана на способности некоторых тонкоизмельченных мине ралов, содержащих металл, смачиваться маслом (реагентами) и всплывать на поверхность водяной ванны под влиянием пу зырьков пропускаемого через ванну воздуха. Минералы пустой
Р и с. |
14. |
С х ем а |
ф л отац и он н ой |
м аш ины : |
|
|||
/ — корпус; |
2 — дно из |
плотного |
полотна; |
3 — труба |
для |
|||
подачи воздуха; 4 — камера для |
засыпки |
руды; |
5 — ван |
|||||
на; 6 — пульпа; |
7 — г.устая порода; |
8 — отверстие |
для |
|||||
удаления породы; |
9 — труба |
для |
заливки |
воды |
|
породы такими свойствами не обладают, они осаждаются на дно ванны и таким образом отделяются от металлической составля ющей руды.
Для флотации руду подвергают дроблению и размолу для получения зерна размером до 0,5 мм. Флотацию производят на флотационных машинах (рис. 14), представляющих собой ван ны, наполненные водой с добавкой реагента, через дно которых пропускают воздух. В качестве реагентов используются масла, получаемые при перегонке нефти или пихтового масла. Части цы руды,'содержащие металл, покрываются тонким слоем мас ла и под воздействием воздуха поднимаются вверх и собираются в виде пены, представляющей собой медный концентрат. Пустая порода смачивается водой и осаждается на дно ванны; ее пе риодически удаляют. В концентрат переходит 85—90% меди от общего содержания ее в руде. Медные концентраты, получен ные флотацией, содержат от 15 до 30% меди.и больше.
Концентрат и многосернистые, богатые по содержанию мед ные руды подвергают обжигу. Целью обжига является удале ние влаги, окисление части сульфидов, т. е. снижение содержа ния серы до необходимых пределов.
Процесс обжига ведут в многоподовых печах шахтного типа или в кипящем слое.
Многоподовые печи (рис. 15) работают по принципу проти вотока. Сверху загружают концентрат или руду, снизу подают
чл'чг-... I |
продукты |
горения, |
а через пусто |
|
|
телый вал |
воздух — концентрат |
||
|
или руда |
нагреваются в |
печи до |
|
|
800—850° С. При |
этой |
темпе- |
Р и с. |
15. |
М н о го п о д о в а я |
печь: |
Р и с . 16. С х ем а о б ж и г а р у д в к и п я |
|||
\ — бункер |
для |
засыпки |
руды |
||||
щ ем сл о е |
|||||||
в печь; 2 — кожух |
печи; |
3 — футе |
|||||
|
|||||||
ровка |
печи; |
4 — полка; |
5 — пере |
|
|||
греватель; |
6 — пустотелый |
вал; |
|
||||
|
7 — руда; 8 — газоотвод |
|
|
ауТ ся о Г ш Ж ^ " н \едГ п '0° ^ Г ” ИЗбЫТ0К “ Р"’ °бРа-
4FeSa + 11 0 2 |
= 2Fe2 0 8 + 8 |
S02; |
2 FeS -f- 3 0 |
3 = 2 FeO + 2 |
S02; |
2CU2S + 3 0 2 = 2СщО + 2S02. |
ты. ОбжигТпип1!,аЗЫ Улавливают для производства серной кислоной на ри с^б ^ КИПЯ,ЩеМ СЛ°е производят по схеме, приведенпортером / в п и т а ю т Т Т 3 измельченную руду подают транс-
поступает в к а м е п ^ |
И бункеР 2>откуда через дозатор 3 руда |
Для подачи воздтаУя \ |
ИмеющУю в поду 5 отверстия (фурмы) |
Душную коробку б Пп |
ТуПающего по воздухопроводу в воз- |
перемешивается ~ « 1 \?И подаче воздуха порошкообразная руда
ДУха обпячппаи,,, |
кипит>> вследствие воздействия потоков воз- |
|
HL сепы соярп1 |
И в„ыделения сернистого газа за счет окисле- |
|
Щие газы’ из |
кям«аЩеИСЯ В сУльфидах железа и меди. Отходя |
|
щие газы из |
камеры поступают в пылеуловитель 7, где очища- |
ются от пыли и направляются для получения серной кислоты. Температура в камере поддерживается в пределах 600—700° С; при таком режиме в процессе обжига получают окисленное же лезо, часть окисленной меди, сульфиды меди и других металлов. Концентраты руды после обогащения и обжига поступают на плавку для получения штейна.
Получение меди переплавом
Получение штейна
Плавку концентратов и руд для получения медного штейна ведут в шахтных или пламенных печах.
Шахтная печь (рис. 17) имеет прямоугольную форму высотой от 1 0 до 11 м, шириной 1,3—1,4 мм. Высота шахты от фурм за грузочной площадки 4,5—6 , 0 м. Шахта печи охлаждается водой.
Загрузку шихты, состоящей из руды или концентрата и кок
са, производят сверху, а воздух для горения топлива через фур мы подают в горн печи.
Пламенная печь для плавки медных руд или концентратов (рис. 18) в настоящее время является основным плавильным агрегатом для получения штейна. Пламенные печи имеют длину 28 29, ширину 6,5—9,0 м; площадь пода печей находится в пределах от 170 до 240 м2. Основное преимущество пламенных печей по сравнению с шахтными печами состоит в том, что в них можно использовать низкосортное пылевидное топливо, а так же жидкое и газообразное т о п л и в о с высоким содержанием серы.
Во время плавки в печах развиваются температуры порядка 1500—1600° С, а для того чтобы сернистое железо полностью не окислялось, поддерживают слабо окислительную атмосферу. В печи при этих условиях протекают следующие основные реак ции (температура 900° С):
Cu2S 4" 2 Cu20 |
6 Си 4~S02, |
Cu2S 4 - 2 СиО |
4 Си 4 - S02. |
Образовавшаяся чистая медь, находясь в расплаве, вступает в соединение с сернистым железом:
FeS 4- Си -> CuS 4 - Fe, Cu20 4 - FeS Cu2S 4 - FeO.
Закись железа соединяется с кремнеземом по реакции 2FeO-j-Si0 2 = 2 Fe0 • ЭЮг и переходит в шлак. В результате протекания этих реакций образуется в жидком виде штейн, со держащий 20—50% Си, 20—40% Fe и 22—25% S. Температура
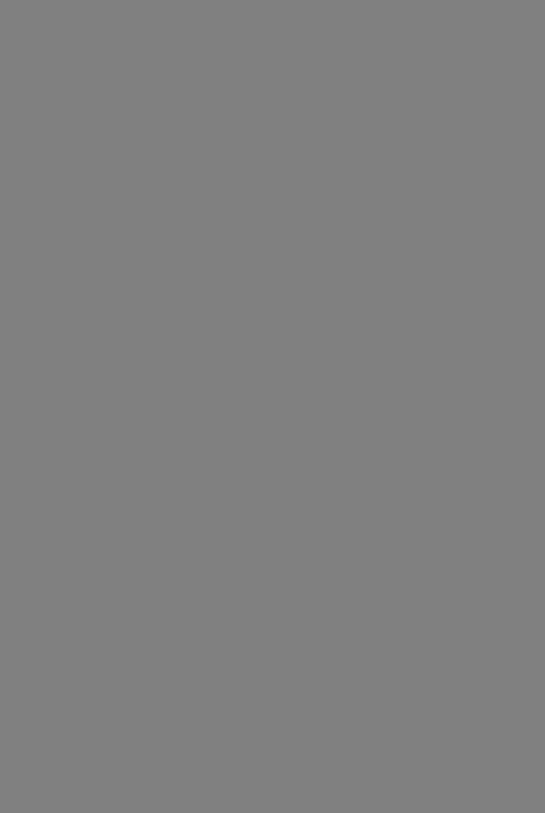
плавления штейна около 1000° С и плотность около 5. Пустая порода руд переходит в шлак, который, имея меньшую плот ность по сравнению со штейном, всплывает на поверхность и лег ко отделяется от штейна. Полученный медный штейн в жидком виде используется для получения черновой меди.
Получение черновой меди
Полученный штейн перерабатывают на черновую медь в конвертерах. На наших заводах применяют конвертеры гори зонтального типа (рис. 19). Перед заливкой штейна через гор ловину в конвертер последний поворачивают на такой угол, чтобы не залить фурмы. Затем на залитый штейн загружают кварцевый флюс, необходимый для ошлакования FeO. После загрузки кварцевого флюса подают дутье под давлением 0 ,8 — 1,2 ат и поворачивают конвертер в нормальное положение. Плав ку в конвертере ведут в два периода. В первый период серни стое железо, содержащееся в штейне, окисляется, образуя закись железа и сернистый ангидрид по реакции
FeS + 3 / 2 0 2 FeO + S02 + Q.
Сернистый ангидрид улетучивается, а закись железа реа гирует с кремнеземом флюса по реакции
2 FeO -{- Si02 —>■2 FeO • Si02 -f- Qi*
Эти реакции протекают с выделением тепла, поэтому темпера тура расплава не понижается, а повышается.
В результате |
окисления сернистого железа и перехода его |
||
в шлак, |
в |
сплаве |
остается почти чистая полусернистая медь |
(C112S); |
на |
этом |
заканчивается первый период плавки. После |
первого периода конвертер поворачивают и шлак сливают. Пос ле того как шлак слит, опять включают дутье, поворачивают конвертер в нормальное положение и производят второй период продувки./
В этот период в конвертере протекает окисление сульфидов меди по реакции
Cu2S -j- 3/ 2 0 2 —>Cu20 -J- S02 -f- Qo.
Окисленная медь в свою очередь взаимодействует с полусернистой медью
2 Cu20 + Cu2S 6 Си + S02 — Q3
и образуется чистая медь. Последняя реакция протекает с по глощением тепла, но так как в конвертере имеется некоторый запас тепла от первого периода, при подаче воздуха в заданных пределах эта реакция протекает нормально.