
1463
.pdf
|
|
|
|
|
|
Т а б л и ц а 8 |
|
|
Предел проч |
Предел теку |
Относитель |
Ударная |
Твердость по |
Марка |
ности при |
|||||
растяжении |
чести» к г / м м 2 |
ное удлине |
вязкость, |
Бринелю |
||
|
|
к г / м м 2 |
|
ние, % |
к г м / с м 1 |
|
ВЧ 45—0 |
45 |
36 |
|
|
187—255Н В |
|
ВЧ |
50—1,5 |
50 |
38 |
1,5 |
1,5 |
187—255Н В |
ВЧ |
60—2 |
60 |
42 |
2 |
1,5 |
197—269Н В |
ВЧ |
45—5 |
45 |
33 |
5 |
2,0 |
170—207ЯБ |
ВЧ |
40—10 |
40 |
30 |
10 |
3,0 |
156— 97Н В |
|
Получение требуемой структуры металлической |
основы раз |
личных видов чугуна в первую очередь зависит от толщины сте нок и содержания кремния.
Прочность отливок из серого чугуна можно ориентировочно найти:
0,4 Н В °ь Сгр + 1,0 '
Количество марганца в чугунах должно быть всегда доста точным, чтобы связать и нейтрализовать серу. Это количество выражается формулой Mn = 2S + 0,2. Чем больше марганца сверх этого количества (но не более 1,0—1,5%), тем легче получить перлит и тем труднее получить феррит. При большом количе стве марганца чугун отбеливается.
Фосфор вызывает хрупкость, поэтому более 0,2% Р не допус кается ни в ковком, ни в высокопрочном чугуне, поскольку эти
чугуны должны обладать пластичностью. |
|
Весьма низкое содержание серы |
у высокопрочных чугунов |
объясняется обессеривающим действием магния. |
|
Л е г и р о в а н н ы е ч у г у н ы |
получают для улучшения |
свойств чугуна, добавкой специальных примесей. Чаще всего в шихту дают для этого природнолегированные доменные чугуны. Легирование 0,8—1,0% Ni, 0 ,6 —0,8% Сг увеличивает стой кость чугуна в щелочах. Для специальных целей применяют вы соколегированные чугуны. Большое распространение получили феррито-карбидные высокохромистые чугуны Х-28 и Х-34, со держащие до 36% Сг. Эти чугуны жаростойки до 1100°С, стой ки в азотной кислоте, против паров серы и сернистых соедине ний, в крепкой серной кислоте, фосфорной кислоте, в большин стве органических кислот и т. п.
Значительный интерес представляют никельмедистые чугуны (12—15% Ni, 5—8 % Си). Последний чугун известен под назва нием н и р е з и с т .
Преимуществом указанных чугунов по сравнению с хроми стыми является меньшая твердость и лучшая обрабатываемость, но они менее доступны из-за дефицитности никеля.
S*
2. ТЕРМИЧЕСКАЯ ОБРАБОТКА СТАЛИ
Для улучшения свойств стали применяют различные виды термической (закалки, отпуска, отжига) и химико-термической обработки, изменяющие структуру стали. Все виды термической обработки имеют обязательные операции: нагрев до определенной температуры, выдержку при назначенной температуре и охлаж дение.
В большинстве случаев нагрев для закалки и отжига стали производится выше температур фазового превращения (^Пр) на 30—50° С. Для доэвтектоидных сталей это выше линии GS диа граммы Fe—Fe3C с целью превращения феррита и перлита в ау стенит а для заэвтектоидных сталей выше линии PSK с целью
Рис. 51. Кривые термической обработки стали (схема)
превращения перлита в аустенит. Более высокие температуры нагрева без особой необходимости нежелательны во избежание чрезмерного роста аустенитного зерна.
Характер превращения аустенита зависит от скорости его последующего охлаждения. При замедленном охлаждении в пе чи происходит отжиг стали; если охлаждение осуществляется на воздухе, отжиг называется нормализацией.
При ускоренном охлаждении в воде или масле происходит закалка. Отжиг и закалка называются полными, если при на греве вся структура стала аустенитной, и неполными, если нагрев производился только до аустенито-перлитной или аустенитоцементитной области.
После закалки обязательно проводится отпуск, задачей ко торого является несколько уменьшить неравномерность структу ры и тем самым снять внутренние напряжения в детали. Отпуск производится при температуре ниже фазового превращения (рис. 51).
Чтобы понять процессы превращения аустенита при различ ных видах термической обработки, необходимо ознакомиться
с S-образной диаграммой, которая характеризует изотермиче ское превращение переохлажденного аустенита, т. е. аустенита, который удается кратковременно зафиксировать при температу рах ниже критических.
На рис. 52 представлена типовая S-образная диаграмма для эвтектоидной стали. На оси абсцисс отложена продолжитель
ность превращения |
(время), а на оси ординат температуры, при |
||||
которых происходит превращение. Первая S-образная линия ха |
|||||
рактеризует |
начало |
превращения переохлажденного аустенита, |
|||
а вторая — конец превращения. |
|
||||
При температурах выше пе |
|
||||
региба (выше — 500° С) |
проис |
|
|||
ходит превращение аустенита в |
|
||||
пластинчатый |
перлит; в интер |
|
|||
вале перегиба |
происходит пре |
|
|||
вращение аустенита в пластин |
|
||||
чатый сорбит; |
при |
температу |
|
||
рах ниже перегиба происходит, |
|
||||
превращение аустенита в трос |
|
||||
тит (при температурах немного |
|
||||
выше перегиба |
т р о с т и т по |
|
|||
лучается п л а с т и н ч а т ы м , а |
|
||||
при более |
низких |
температу |
Рис. 52. С-образная диаграмма для |
||
рах — и г о л ь ч а т ым , |
такую |
эвтектоидной стали |
|||
структуру |
иногда |
называют |
|
бе йнит ом) . Все эти структуры представляют собой смесь фер рита с цементитом и чем ниже температуры, тем они дисперснее.
Пластинчатыми структуры называются потому, что перлит, сорбит и тростит представляют собой смеси пластинок цементита и феррита. Однако при очень низких температурах превращения феррит приобретает игольчатую направленность, а поэтому и тростит называется игольчатым. Соответственно меняется твер дость (и прочность), НВ:
Перлит |
крупный . . . . |
190—230 |
|
Перлит |
сорбитообразный |
230—260 |
|
Тростит |
................. |
300—400 |
|
Тростит |
игольчатый |
450—550 |
Все превращения, при которых получаются перечисленные структуры, называются диффузионными; происходит перестрой ка y-Fe-^a-Fe и выделение (диффузия) углерода из твердого раствора.
При более низких температурах выделение углерода из твер дого раствора не может произойти, приостановить же превраще ние y-Fe-^a-Fe невозможно, а поэтому получается пересы щенный, неравновесный твердый раствор углерода в a-Fe, получивший название ма р т е н с и т . Мартенситная структура
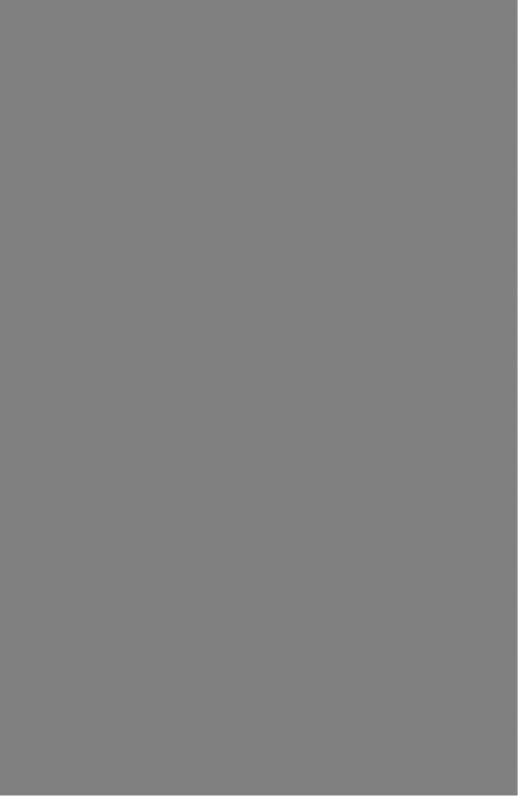
Поэтому закаленные структуры всегда переохлаждены и неравно весны. Если растворяющаяся среда не имеет полиморфных пре вращений, получается истинный твердый раствор, обычно способ ный к пластической деформации. Поскольку при закалке стали имеет место полиморфное превращение, аустенит зафиксировать не удается, а образуется мартенсит, который не способен к пла стической деформации и очень тверд.
Т в е р д о с т ь м а р т е н с и т а т е м б о л ь ше , чем больше в нем растворено углерода и для инструментальной заэвтектоидной стали равна 62НРС и выше. Твердость мартенсита объяс няется напряженностью решетки a-Fe, поскольку оно не спо собно растворять в себе углерода.
Согласно данным Г. В. Курдюмова, когда при закалке весь углерод оказывается растворенным в a-Fe, последняя имеет решетку не объемноцентрированного куба, а тетрагональную
обеспечивается тогда, когда скорость охлаждения
является критической (aKp). Критической скоростью называется минимальная скорость охлаждения, при которой не получаются структуры диффузионного превращения, а получается мартенсит.
Сталь способна принимать закалку, если она содержит не ме
нее 0,2% |
С. Кроме з а к а л и в а е м о с т и , большое значение |
имеет и |
п р о к а л и в а е м о с т ь , т. е. способность стали прока |
ливаться на определенную глубину. Чем более устойчив пере охлажденный аустенит, т. е. чем больше расстояние от оси орди нат до перегиба (кривой начала превращения), тем на большую глубину прокаливается сталь. Углеродистая сталь прокаливается на небольшую глубину. Для закалки на большие глубины приме няются легированные стали.
Нагрев под закалку может производиться в газовой и жидкой среде.
Печи газового нагрева могут иметь нефтяной (мазутный), га зовый или электрический обогрев.
Печи могут быть сделаны герметическими и наполняться газа ми, предохраняющими металл от окисления. Такие контролируе мые, неокисляющиеся атмосферы состоят из аргона, гелия, азо та, смесей Na2 + Н2 + СО и др., образуемых в специальных гене раторах из нефтепродуктов или светильного газа.
Помимо газового нагрева, широкое применение нашел жидкостный нагрев под закалку в расплавленных металлах (сви нец, сплавы свинца, силумин) и солях (хлориды, карбонаты, нитраты).
Нагрев в жидких средах имеет ряд преимуществ перед газо вым нагревом: значительно более быстрый прогрев изделий, однородность температуры среды, меньшее окисление, чем на воз духе, возможность местного нагрева и др.
К недостаткам жидкостного нагрева относится малая-стой кость тиглей, необходимость специальной очистки изделий после термообработки, большая опасность работы для персонала..
Нагрев в жидких средах производится в специальных печахвакнах, тигли которых подогреваются мазутом, газом, электри чеством.
Для высокотемпературного нагрева (до 1300° С) обычно при меняют электродные печи-ванны, в которых электросопротивле нием служит сама расплавленная соль — хлористый барий.
Закалку производят в различные закалочные среды — воду, масло, расплавленные соли, воздух.
Если принять охлаждающую способность спокойной воды при 20° С за единицу, то относительная охлаждающая способность 10%-ного водного раствора NaCl составит 1,23, масла — 0,20, спокойного воздуха — 0,03.
Для уменьшения коробления и поводки производят изотерми ческую закалку в расплавленные соли, находящиеся при темпе ратуре устойчивости аустенита, и последующего охлаждения.
После закалки производят о т п у с к для. уменьшения нерав новесное™ структуры.
Взависимости от требований, предъявляемых к окончатель ной структуре, выбирается температура отпуска. Она должна быть ниже температуры фазового превращения.
Вчастности, при нагреве до температуры не выше МПмартен сит будет отпущенным, из него выделится часть углерода и сни мается часть остаточных напряжений, которые могут вызвать
разрушение изделия. Такой отпуск называют н и з к о т е м п е р а т у р н ы м (180—220° С) и применяют при закалке инструмента, поскольку здесь требуется сохранить мартенсит. При нагреве до 300—400° С мартенсит превращается в тростит. Такой отпуск называют с р е д н е т е м п е р а т у р н ы м и применяют при за калке штампов, пружин и т. п. При нагреве до 500—550° С тростит превращается в сорбит. Такой отпуск называют в ы с о к о т е м п е р а т у р н ы м и применяют чаще всего для конструкционной стали. Свойства тростита и сорбита, полученные при отпуске мар тенсита, превосходят по вязкости аналогичные структуры, полу чаемые при охлаждении непосредственно из аустенита. Объяс няется это тем, что цементитная фаза в этих структурах при рас паде мартенсита получается не пластинчатой, а сфероидальной.
Отпуск можно производить в газовой среде (воздух или за щитные атмосферы), в жидкой среде (кипячение в воде для сня тия напряжений), низкотемпературный отпуск в масле (до 2 0 0 — 250°С), высокотемпературный отпуск (до 500—550° С) в расплав ленной селитре и щелочи.
Термическая обработка доэвтектоидной стали заключается в закалке на мартенсит и высокотемпературном отпуске на сор
бит и называется у л у ч ше н и е м . Повышение прочностных свойств здесь объясняется преобразованием феррито-перлитной структуры в сорбитную.
Преобразование феррито-перлитной структуры в сорбитную может быть получено и путем нормализации, но в этом случае эффект повышения прочности свойств менее значителен, чем при закалке с отпуском.
Отжиг
Отжиг имеет различные назначения и бывает двух родов: отжиг первого рода — нагрев ниже температур фазового превра щения и второго рода — нагрев выше температур фазового пре вращения.
О т ж и г п е р в о г о р о д а (низкотемпературный) применяют для снятия остаточных напряжений, для снятия наклепа, сфероидизации цементита в заэвтектоидных сталях для их смягчения, т. е. для облегчения обрабатываемости.
Обычно, чем выше температура, тем короче может быть вы держка, но все же для сфероидизации требуется длительная выдержка.
Отжиг для снятия наклепа (см. главу «Обработка давле нием») производят после холодной пластической деформации; при этом происходит не только снятие напряжений, но и рекри сталлизация структуры, а поэтому он называется рекристаллизационным.
О т ж и г в т о р о г о р о д а имеет различные цели, а именно: а) измельчение зерна; б) получение равновесной, более мягкой структуры; в) уничтожение литой структуры; г) устранение ден дритной ликвации.
Отжиг доэвтектоидных сталей производят нагревом на 20— 50° С выше температуры фазового превращения, т. е. выше ли нии GS (см. диаграмму железо — углерод).
При указанных температурах происходит превращение a-Fe ->Tf-Fe и образование большого числа мелких зерен аусте нита независимо от исходных размеров ферритного и перлитного зерна. Последующее охлаждение изделий с малым аустенитным зерном приводит к образованию мелкого ферритного и перлит ного зерна. Значительный перегрев выше линии GS дает не из мельчение, а укрупнение зерна.
Литые структуры очень часто бывают крупнозернистыми, а из быточная фаза, например феррит в доэвтектоидной стали и вто ричный цементит в заэвтектоидной стали, располагается в зернах
под углом 60 и 90°, образуя своего рода скелет |
(рис. 54). Такая |
структура называется в и д м а н ш т е т т о в о й |
и обладает пони |
женной вязкостью по сравнению с нормальной структурой. При
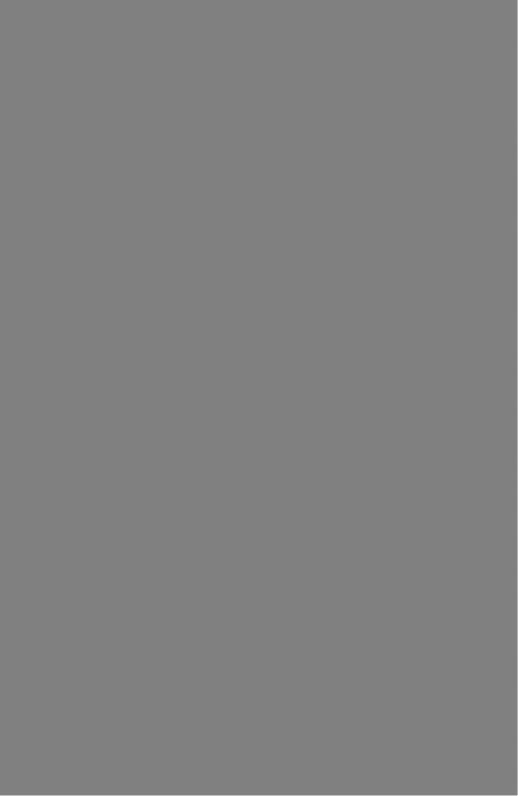
улучшения, производят и поверхностную (местную) закалку на мартенсит.
При индивидуальном и серийном производстве быстрый мест ный нагрев может быть осуществлен применением кислородно ацетиленовых горелок. При массовом производстве применяется высокочастотный нагрев, обеспечивающий более качественную поверхность.
Глубина прогретого слоя пропорциональна соотношению
где р - удельное электросопротивление, ц — магнитная проницае мость, / — частота тока.
Нагрев изделий токами высокой частоты (т. в.ч.) производится в индукторах, питаемых от специальных установок— генерато ров т. в. ч.
Для прогрева массивных изделий на большую глубину при меняют машинные генераторы (спаренный блок-электродвига тель с высокочастотным генератором). Получаемая частота рав
на— Ю кгц.
При закалке изделий небольших размеров и в случае, когда не требуется большая глубина закал'ки применяют ламповые ге нераторы т. в. ч. с частотой в десятки и сотни килогерц.
Закалку изделий токами высокой частоты в условиях массо вого производства осуществляют на специальных станкахавтоматах высокой производительности.
3. ХИМИКО-ТЕРМИЧЕСКАЯ ОБРАБОТКА
Химико-термическая обработка заключается в обработке го товых деталей в активных средах, что приводит к изменению химического состава, структуры и свойств поверхностных слоев. Химико-термическую обработку производят главным образом для поверхностного упрочнения металлов.
Наибольшее распространение получили: цементация, азотиро вание и цианирование.
Цементация
Цементация производится при 900—950° С для науглерожи вания поверхности малоуглеродистой (менее 0,25%) нёзакалившейсЯ стали до 0,8% С. Благодаря цементации, изделие стано вится двухслойным — поверхность науглероженная, сердцевина ненаугДероженная. После цементации изделие подвергается за калке и низкотемпературному отпуску. При этом сердцевина не принимает закалку, остается вязкой и может работать в усло виях Динамических нагрузок, а поверхность приобретает маптен-
ситную поверхность на глубине около 1 , 0 мм и хорошо сопротив ляется износу при трении.
Цементация осуществляется в твердом или газообразном кар бюризаторе; в обоих случаях переносчиком атомов углерода является газовая фаза.
При цементации в твердом карбюризаторе изделия упаковы вают е смеси, состоящей из 70—80% древесного угля и 20—30 % 1 углекислых солей (ВаСОз, Na2 C03 или К2 СО3 ), играющих роль катализатора и способствующих выделению углерода в атомар ном состоянии, необходимого для цементации.
Цементированная поверхность годится для эксплуатации при невысоких температурах, так как при температуре выше 150— 200° С мартенсит распадается.
Газовая цементация имеет значительные преимущества перед цементацией в карбюризаторах: технология более гигиенична, процесс протекает в два-три раза быстрее, меньше вырастает аустенитное зерно (особенно если применяют стали, мало чув ствительные к росту зерна), а поэтому отпадает надобность в промежуточных операциях (термическая обработка для измель чения зерна).
Газовая цементация требует специальное, более сложное обо
рудование, и применяется при массовом производстве. |
цементи |
||||
Газовая |
цементация легче всего осуществляется в |
||||
рующих |
газах типа предельных углеводородов (СпГЬп+г), как |
||||
метан, пропан, бутан и др. |
При нагревании газов до высоких |
||||
температур |
(900—970° С) |
выделяется |
атомарный |
углерод |
|
(СН4 |
С + 2Н2), который |
цементирует |
сталь. Например, при |
||
нагреве мётана |
|
|
|
||
|
|
СН4 |
С + 2Н2. |
|
|
Весьма производительным является процесс газовой цемента ции с нагревом токами высокой частоты. Так, при цементации автомобильных шестерен из стали 18ХГТ при нагреве т. в. ч. до 1050—1080° С в атмосфере городского газа время для получения цементированного слоя в 0,8—1,2 мм составляет всего 40 мин.
Азотирование
Способ азотирования основан на образовании в поверхност ном слое твердого раствора азота в железе и нитридов. Твердость азотированной поверхности значительно выше твердости цемен тированной закаленной поверхности и достигает 1 1 0 0 —1 2 0 0 ЯВ. Азотирование проводится при относительно низких температурах (—500—600° С) в среде аммиака, который, разлагаясь, выделяет атомарный азот, способный реагировать с металлом
NH3 ЗН + N.