
3218
.pdf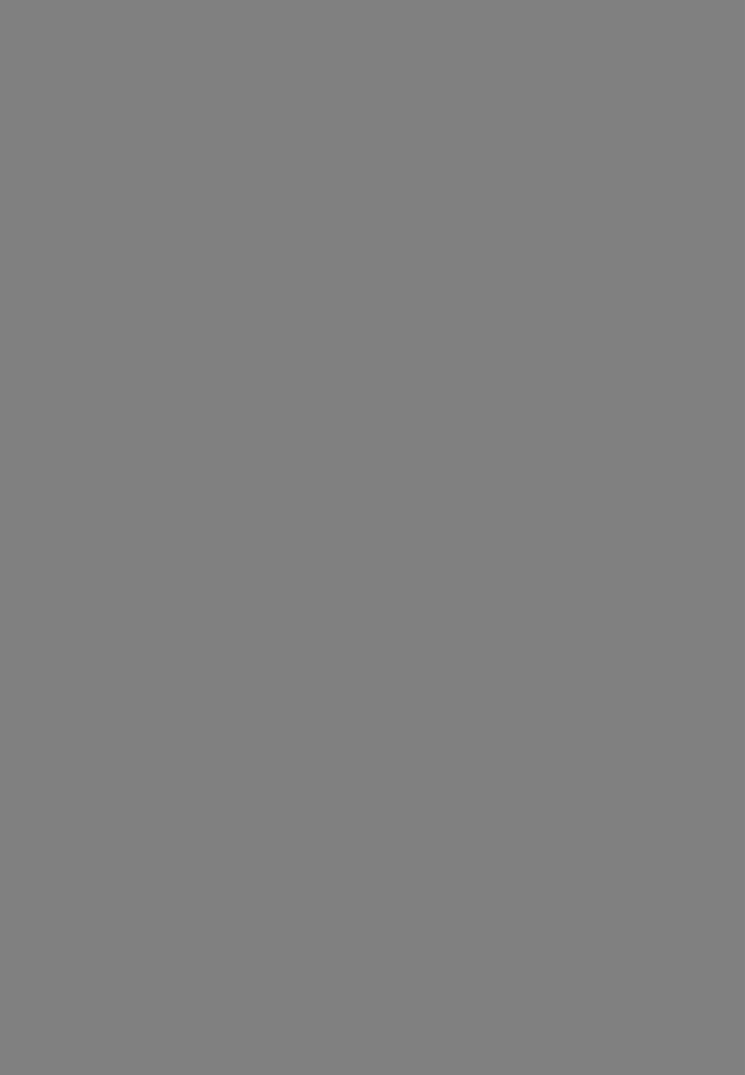
The shuts are oaused by |
|
|
|
|
|
- |
insufficient fluidity |
of |
the |
molten metal, |
|
- |
extensive heat condictivity |
of the |
mould materials, |
||
-unsatisfactory content |
of |
a moulding |
sand, |
-high gc.3 pressure in the mould cavity during pouring the metal,
-the use of unsatisfaetpry methods of running and gating*
It is |
known that |
fluidity |
of a molten metal dependg |
|||||
on its |
temperature |
and |
chemical |
composition* At the |
same |
|||
temperature |
of ovorhaating |
pure |
meto.ls |
and eutectic |
alloys |
|||
\ |
the |
higher |
fluidity |
than alloys |
solidifying |
over |
||
possess |
a temperature range* This explains the wide practical preference for eutectic or near-eutectic alloys from foundrymen, esfccially for castings with thin sections*
Different additions to the alloy may be used to inc
rease |
its flu idity, but the simplest way is the |
increase |
|
of its |
pouring temperature* However^ this measure can |
||
cease |
the appearance of other undesirable defects, such |
||
as hot |
cracks, |
shrinkage cavities and porosity, |
bunning- |
-on, etc* |
|
|
|
|
Usually moulding materials used are not. wotted by |
||
a molten metal. |
Therefore, materials used for |
the prepa |
ring of moulding sands, paints, and coatings cannot influence on fluidity of the molten metal*

They increase porosity of the mould, decrease the mixture density, reduce its heat conductivity due to that the
coefficient of heat accumulating |
ability decreases» Such |
additions may be the following |
saw-dust - for mixtures used |
for cast iron and steel casting, |
burnt asbestos and gypsum- |
* for aluminium alloys* |
|
Sometimes moulding mixtures with |
low heat accumulating |
ability are used for facing risers, hot jrope and feeding headers»
In order to defend permanent metal moulds from sudden
thermal shocks and to decrease their heat accumulating abi
lity |
and so to |
improve the fillin g moulds with metal,their |
||
face |
is oovorod |
with a heat ia»-olaiing |
paint, |
composition |
of which depends on the poured metal» |
For the |
decreasing |
||
|
|
heat isolating powders |
are used» They are chalfc, |
of heat accumulating ability of green sandryflour, acetylene "" soot, oharcoal dustfor iron ce.stings, hexachlorinothane-
- for aluminium alloy castings, |
acetylene soot-for magnesium |
|
and copper alloy castings» |
|
|
As an example , the influence of |
heat isolating |
powders |
on fillin g ability of a mould with molten cast |
iron is |
|
shown in Fig’ 2ClO |
|
|
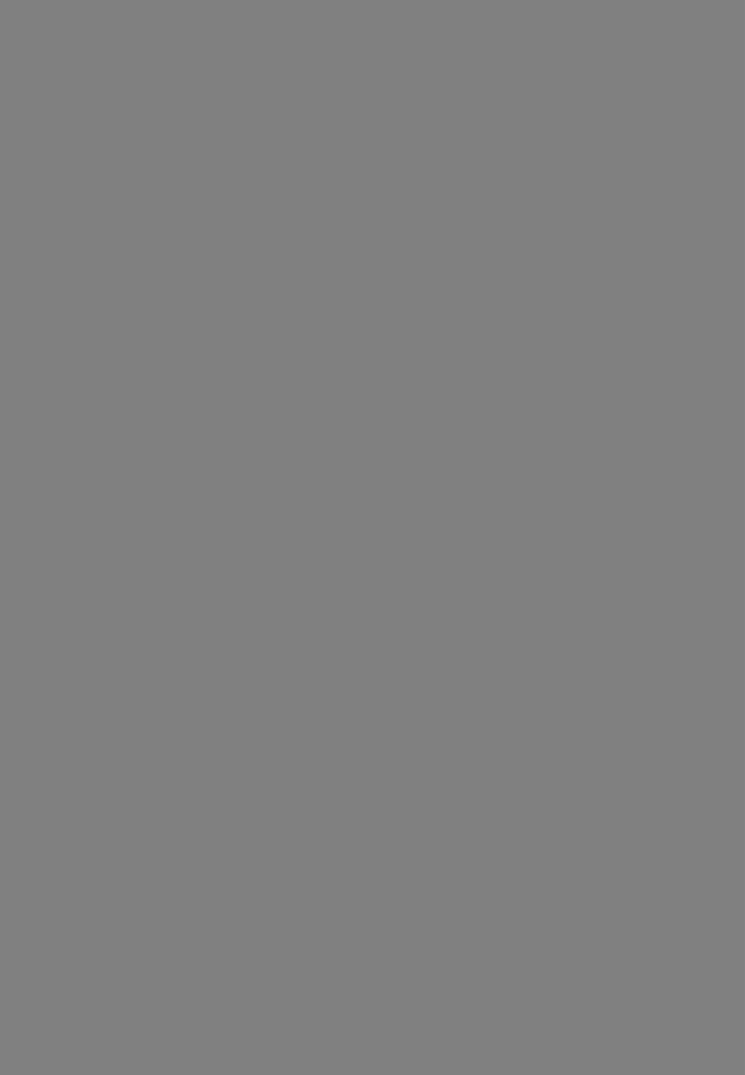

ohoise |
of a running |
system providing |
smoother |
flow by |
||||
a solid stream allow |
to eliminate this |
defect |
in |
surfa |
||||
ces of |
thin wall |
castings |
(3)* But |
sometimes |
a combin |
|||
ation |
of mentioned above |
expedients |
is |
to be |
used. |
|||
|
|
Laps-, seams„and cold |
shots |
|
|
|||
|
Surface laps, seams |
and cold shots are a variety |
||||||
of a cold shuts. |
Laps have the appearance of |
a patch on |
||||||
the casting surface alongated in the shape of a tongue. |
||||||||
Seams can be of |
a different shape in |
a surface. |
But cold |
|||||
shots have the appearence of small shotlilce spheres |
||||||||
metal which are |
almost completely iistih et from the wast |
ing. They are formed when a spurt of liquid metal striking
on either bottom surface of a mould cavity or some other obstacle in its path is turned into separate sprays? Heasures of these defect prevention are alike thoserof mentioned above.
|
Surface roughness |
Roughness and smoothness of casting surfaces is mainly |
|
determined by the |
size of the sand grains and temperature |
of molten metal. |
There is., a general agreement that, as the |
permeability of the sand decreases, as result of small |
|
voids between the |
sand grains, surface finish improves. |

|
Notes |
1* |
^he |
content |
of |
the protective fluorio add |
ition |
not less |
than 6l.5 % |
F, |
22*5 % NH^» 4*5-5*5 B, |
||
|
2* |
The content of boric addition : not less than |
||||
|
|
99% boric |
a cil, |
|
|
|
|
3* |
Paints |
No. |
1 and 2 are |
used to paint moulds and |
|
|
|
copes for Al-alloy castings, |
||||
|
4» |
Paint |
N6^3 |
i3 used to paint cores to be dried at£ |
||
|
|
temperature not more than 180°C, |
||||
|
5* |
|
|
|
|
to |
|
PaintBBo.4 and 5 are usedv"paint cores to be dried |
|||||
|
|
at temperature 220-250°C. |
When the pressure feePf&d^ the metal exeeds a certain
critical value which depends on the diameter of the pores
in the |
sand, metal may be |
forced in between the |
sand grains* |
When the castings are large |
so that the pressure |
is high |
|
and the temperature of the mould is maintained for a long |
|||
period, |
metal may penetrate |
to a considerable depth farming |
|
a layer |
of burning-on* |
|
|
Burning-On
Burning-on is в-.тоге or less thiolc layer of a durable combination of a moulding sand and casting metal as a result of heat, mechanical, and physical-chemical processes taking place during the period of pouring, solidification., ,and oooling of the casting. This nonmetalic crust cons isting of grains of a moulding material! and bonding or cementising substance is hardly retained on the casting surface.
