
3218
.pdfPig 2.5» Formation of fin*
94-
Fig* 2*6* Formation of a scab i
a) the preheating of the surface layer of the mould and arising of stresses!
b) the shearing the face layer of the mould| w
c) the crack formation' and scab arising*
Foundry Department |
n Casting defects and |
Dr*V* Bastrakovo |
measures of their prevention” |
The nature of scab formation is the following. When
molten metal is poured into a green sand mould the uncov ered surface of the mould is heated by radiation.
At the same time the air and gasses inside the mould cav ity are heated too and they give their heat to the facing layer of the »avity. The latter gets heated to a high temperature and losses its moisture because of the inte
nsive evaporation, A part of the steam is removed from
the mould through risers and venting holes,the basic one passes through pores of the mould mixture. The moisture removed from the face condenses in some distance from the surface when the steam reaches a cool sand. So a zone of the higher moisture appears while further, behind it , we tness of the mixture remains constant. As the temperat ure of the sand behind the mould face rises, moisture ev
aporates from the damp layer and condenses s t ill further
back. In other words the high moisture zone removes from
the face |
inside |
the |
mould becoming broader and less inte |
nse as it |
recedes. |
|
|
It |
is of |
mor6 |
importance that wet and dry layers |
of the moulding sand have a different heat conductivity
and strength* The mould layers of the higher .moisture
%
have, relatively to other layers, the lowest strength and the highest heat conductivity. So varying the moisture distribution across the mould causes the corraspending
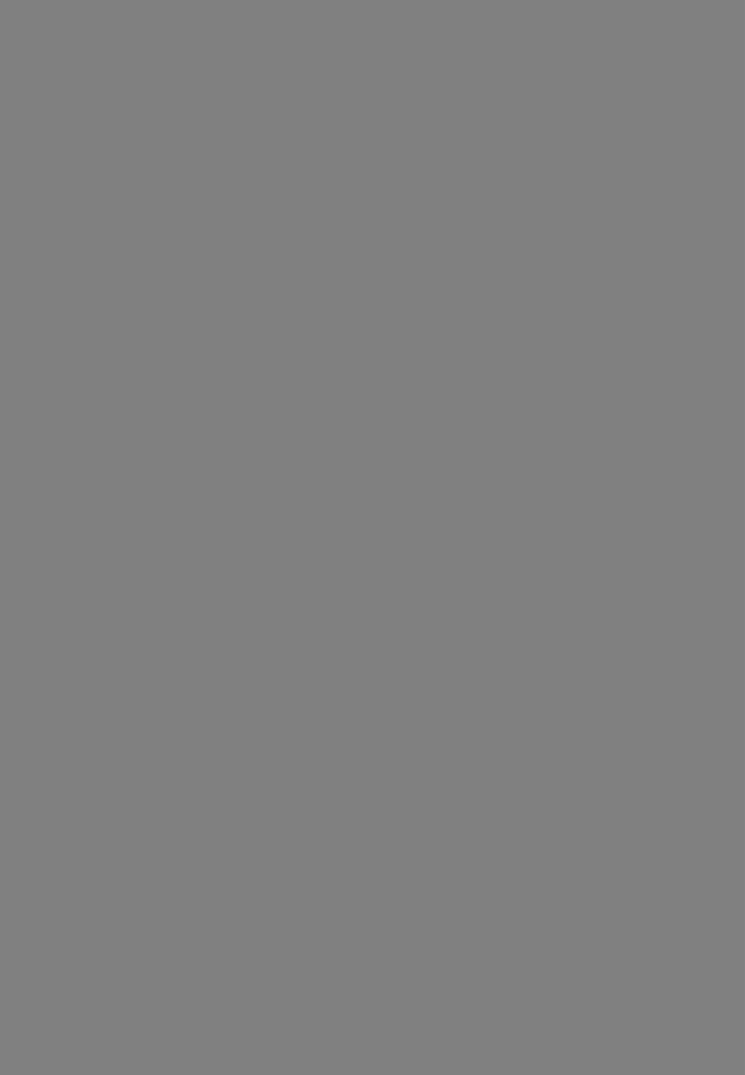
smashed sand as we11 as |
the sand fa ll |
down from the pre |
heated surface upon the |
rising liquid |
metal can cause sand |
spots and inclusions or |
other kind of |
defects. |
Quality of moulding materials may be the reason of scabbing too. Usually the most part of a moulding mixt
ure is an used or, so called, "burnt" sand. So it is rep eatedly subjected to heatings from the molten metali The high temperature is the destructive agent continuously
deteriorating durability of the moulding sand. The hea vier the work, the more rapid silica grains crack and
disintegrate. |
When really large castings |
are made regu |
|||
larly - when the sand |
at the |
moulding face |
may remain at |
||
a red heat fo r |
two or |
three |
days-the re-used sand w ill |
||
soon reach |
so "burnt" a condition that serious scabbing |
||||
or washing |
may occur |
as a result of this deterioration. |
The high hardness of ramming a sand and the devel opment of a high gas pressure in a region of too low per meability can also produce excessive stresses in the cope and cause scabbing.
Scabs due to sand expansion were discussed. Their
characteristics |
is the presence |
of a thin |
layer |
of sand |
|
the thickness of |
\ |
about |
1 mmor less i |
A scab of |
|
which is |
|||||
this kind occurs |
only during the period when the mould |
||||
is being fille d . |
Once the |
mould is fu ll, |
pressure from |

It is too rarely but sometimes scabs are obtained
on casting face when they have been made in dry sand mo ulds. Binding materials of dry sand mould usually contain some, too small, amount of the chemically combined water, the behaviour of whioh during the pouring of molten metal
may be adequate to that of green sand moulds. Indeed, such the amount of water cannot essentially decrease the
strength of the surface layer of the mould, but the defect
may occur if the mould has the large area of send which is being heated and cracks may form on its face unless the mould can deform.
Usually, elimination of scabbing is not a particul arly d ifficu lt task in foundries. Practically the use of
dry sand moulds allows foundrymen to solve this task convpletely but drying the moulds sharply increases their cost
and, thus, the price |
of castings. Therefore^; |
is better^ |
to find ways of the |
scabbing prevention without |
a radical |
change of the technological process of the casting manuf
acture. |
It is possible to do it'b y t |
||
- |
the change of regimes of pouring { |
||
- |
the provision |
of needed physical and ив chanical |
|
|
properties of |
moulding mixtures, especially of |
|
|
a facing |
sand; |
|
- |
the use |
of special refractory paints t |
|
- |
the inclusion of some change into a pattern design? |
||
- |
some other means. |



