
3218
.pdf- surface casting defects deteriorating their exte rnal appearance or making impossible to use them in prac tice because of their bad marketable state*
Causes of the arising of such defects are different
in every concrete |
case. |
They may be |
j |
a pattern, a technological process, |
a casting design, pou |
||
ring conditions, |
and so |
on. |
|
But knowing reasons of their arising it is easy to prevent and to eliminate the origin of defects in future.
|
|
Discrepancy |
of casting sizes to droughts |
|
|
|
This defect |
of castings is, as a rule*, the conseque- |
|
nce^ |
t |
|
|
|
- |
the |
inaccurate |
making of patterns or permanent mould |
|
|
( dies ) complete set | |
|||
- |
committed errors in mould assembling ; |
|||
- |
distortion or displacement of cores in the mould j |
|||
- |
mistakes at |
the |
calculation of a shrinkage value ; |
|
- |
an incorrect |
casting design. |
The repairing or correction of the pattern and equ ipment find the increasing of the mould assembling accur acy allow one to reach required dimensional accuracy of a casting in a g i % alloy.
Cores may be the reason of casting sizes .imperfec tions too. Errors in the assembling of moulds and in # fixing of cores as well as a core distortion during bak ing and metal pouring are followed by a casting sizes change•
Dimentional inaccuracy due to,a core distortion is particularly dangerous because it cannot be, as a rule, detected by an inspection of the casting since the exte rnal dimensions are not affected. It can lead to a red uction in wall thicknesses and white iron can be formed in thin cross-sections of cast iron castings and the cas tings may be hard to machine or, what is worse, fa il in service. The core distortion takes place invariably due to Underbaking. In this case remedies are obvious*--.
|
The dimensional inaoonracy may be also a result of |
|
distorted moulds |
at their tempering or calcination. |
|
It |
is especially |
characteristic of moulds for investment |
or |
shell castings. |
Sometimes oversize castings result from rapping a pattern too hard when it is removed from the mould or from excessive allowance in the pattern for metal shrink.
At the process cf solidification from the liquid state and cooling to the room temperature in the solid state a casting metal contracts rod the casting changer.
its sizes. Different metals have different heat eapansion coefficient and it is obvious that alloys have vari
ous values of the |
linear and volumetric contraction. |
|
|
Besides values of |
a solid |
contraction are dependent on co |
|
mposite cn and pbi.se constitutions. Some information |
abo |
||
ut free alloy contraction |
is summerisod in Cable 2*1. |
|
|
|
|
Cable |
2.1 |
Approximate values of free contraction of some metals and alloys
•fetal |
or alloy |
linear con |
volumetric |
||
traction , |
contract |
||||
|
|
|
|||
|
|
|
in % |
ion in. % |
|
Gray cast |
iron О *5- 5»7% C) |
1.04 |
5*12 |
||
Nodular cast iron |
|
1.45 |
4.30 |
||
Mall9ab?.e oast iron after annea |
|
|
|||
ling- t 2. 5~2.$% C ) |
1.70 |
5.08 |
|||
Steel (0 -2- 0 .3% C) |
2.00 |
6.00 |
|||
Aluminium |
|
|
1.79 |
5.56 |
|
Aluminium allots |
: |
|
|
||
Al-Ci ( 5.0% S-i ) |
|
1.55 |
4 i06 |
||
Al-Si C '12.0% Si |
) |
1.10 |
5.51 |
||
Al-Si-Mg |
(7.0% S i,0.5% Mg ) |
1.50 |
5.90 |
||
Al-Cit ( 8.0% Cu ) |
|
1.50 |
5.90 |

|
Linear cont— |
volumetri |
Metal or |
alloy |
|
Zink |
1*61 |
4.8;5 |
Lead |
1.09 |
3.26 |
Tin |
0.73 |
2.34 |
As a result of solid contraction |
o f a |
casting |
metal |
||||
the patternmaker *s |
allowance |
fo r contraction |
must be |
fore |
|||
seen on the pattern |
and its |
dimensions |
in a ll directions |
||||
must be enlarged in the proper value. But unfortunately |
|||||||
the free |
contraction and shrinkage..are p ra ctica lly never |
||||||
possible |
as surfaces of castings are usually |
not |
complete |
||||
ly free |
to move relatively to the mould |
et^rface |
because o f |
||||
friction |
or because |
of interlocking of |
irregu la rities |
o f |
the two surfaces. In addition to this the casting |
may also |
be contracting on some parts of the mould, such as |
the in t |
ernal cores ( F ig.2 .1 ), which hinder the metal from |
con tr |
action. |
|
As a consequence of the mould resistance and varying rate cf cooling solid contraction of d ifferen t casting pa rts is usually non-uniform. But to take it into account at

Fig.2*l. Origin of stresses restricting
free contraction because of casting design and core and mould resistance
Гaunary Department |
"Ousting defects and |
Drо V. Bastrakov |
measures of their prevention" |
Practical linear contraction of cast alloys•
Alloy |
Linear |
contraction, in |
% |
small |
Middle |
Large |
|
|
easting |
casting |
oasting |
|
J |
|
|
Gray cast iron |
0.8-1*0 |
0.7-0 .9 |
0*6—0*8 |
Nodular cast iron |
1.0*40 |
0.9-1.2 |
0*8—1*1 |
Carbon steel |
1.8-2*2 |
1*6-2.0 |
1.4-1.8 |
Cupper alloys. |
1.4-1.6 |
1.0-1.4 |
0.8-1.2 |
Aluminium alloys |
0.9-1.35 |
0.7-1.2 |
0.6-1.0 |
Note : Low limits are used at the presence of hindered srinkage of alloys poured into dry Sand moulds*
Warping and Cambering,
Warping is a distortion of a casting shape under the action of internal or residual stresses arising as a result
of non»uniform cooling and contraction due to thermal gra dients in various cro ssfo o t ions or parts of a casting*
A greater resistances to contraction in one part of the cas ting than in another is the reason of warping too*
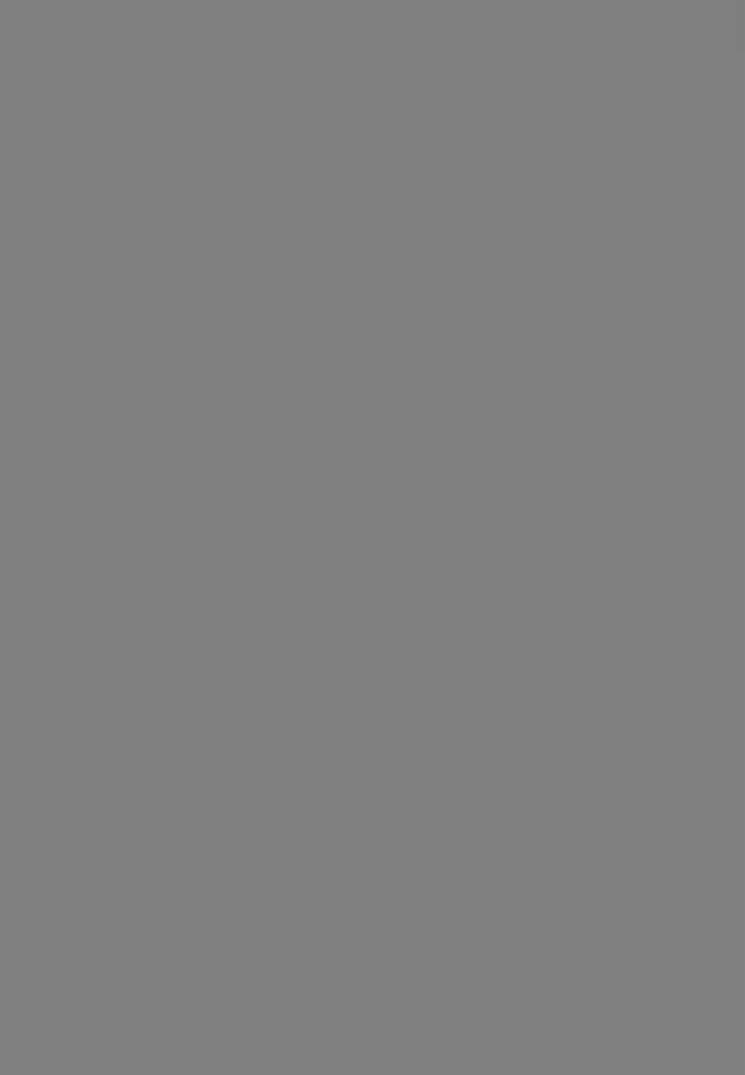
- is -
Compression side
Tension side
(Я)
(b)
Fig*2.i. Warping of eastings as |
a result of |
|
internal and residual streams 9 after |
cooling t |
|
a) |
odd-sided frame castingj |
(b) elongated plate |
with ribs |
of rigidity; (c) casting of |
girder section |
d)bracbut. Dotted linos show the right shape of castings. Arrows show directions of internal and rosidual stresses act ion after cooling*
Foundry Department; |
"Casting defects .»nd |
Dr* * Dus ura-rov« |
:iOisuroo of thoir provention" |
|