
3218
.pdf2*3* Imporfeotion of a metal composition and
struoture*- Chemio.al Conroogition
Chemical composition and structure entirely determine
mechanical and physical properties and, thus, strength and
exploitative |
lia b ility of a casting |
metal* |
In order to |
|||||
produce a casting with the required |
properties, the |
alloy |
||||||
meitftd must |
be of a specified composition* |
Therefore, |
|
|||||
compositions of the most of alloys are limited by corresp |
||||||||
onding standards* |
But, due to |
some reasons |
having been |
|||||
during the melting process, it |
is very d ifficu lt to |
get |
||||||
the alloy |
of |
a definite chemical composition* |
That |
is |
why, |
|||
according |
to |
the standard, the |
content o f basic elements |
|||||
in an alloy |
is ranged in the proper |
lim its, |
which are |
...-d |
||||
determined by the requred properties in castings* |
In |
the |
||||||
simplest case standaat specifications give only "the comp |
||||||||
osition and tolerances in the main alloying elements* |
|
|||||||
However, |
as |
a rule, |
in alloys |
there |
are unwanted or |
und- |
isirable elements the total content of which is negligible but they can affect deleteriously the required properties* Por some applications, the standard may specify the tolera nces in' those elements termed tramp or residual elements, the presence o f which must not exceed the limits specified* Some tramp elements or impurities are particularly injurious and have to bo kept to very muoh finer limits*

- dirty raw charge and scrap covered with sand, rust or corrosion products are used for melting,
- raw materials of unknown ohomical compositon are melted,
-Different kinds of raw materials are mixed at the stor age,
-incorrect weighing of charging materials,
- the charge is composed erroneously,
V
•• the charts is о<'трояне, erroneously,
-there are some error in the calculation of a metal
waste at the melting in the furnace*
- melting operations are imperfect.
To prevent this kind of the defect it is necessary*
-to control and analyse all raw materials in spite of
|
the |
pressence |
of sert^fates |
from a plant-supplier, |
|
«• |
to |
weigh a ll |
materials used in the charge according to |
||
|
the |
prescribed dosage, |
|
||
• |
to |
assort the |
scrap and to keep raw materials in the |
||
|
charge |
store |
in order, |
|
|
• |
do not |
allow |
errors in tho |
calculation of a change, |
•to observe the order of maintenance of melting furnaces_ as well as the prescribed techanological regime of melt ing a metal,
•to analyse the metal chemical composition during melting and prior to pouring*

Alloy
Composttio/i
Fig* 2*30* ghase diagram for jthe nickel-copper a ll system* Microstructures shown are obtained by very slow solidification*
Fig«2*31* Phase diagram of the aluminium-rich end of the aluminium-copper'fifijase diagram* Microstructures shown are obtained by very slow solidification*
Foundry Department |
” Casting defects |
and |
Dr* V. Bastrakov |
measures of their |
prevention” |
4 50-50 alloy w ill |
be chosen, solidification |
w ill |
bo consi |
||||
dered to he very slow* |
I f |
such an alloy is melted |
and poured |
||||
solidification w ill |
begin |
at 13l3eC. |
Nucleation of a solid |
||||
solution of nickel |
and copper w ill |
take place, and dendrites |
|||||
will begin to grow, the |
composition |
of |
the in itia l |
solid |
|||
36, |
|
balance nickel, as |
shown in fig* |
||||
will beVper cent copper, |
|||||||
2230. |
|
|
|
|
|
|
|
As the alloy cools, the solid grains continue to grow. |
|||||||
Since the in itia l solid |
contains less |
copper |
than |
the liquid |
|||
(36% as compared to 50%) |
the liquid becomes |
gradually richer |
|||||
in copper. Ai 1283°C, the liquid has increased in copper |
|||||||
content to 57 per cent, |
with the result the |
solid |
whicJhh |
is freezing increases in composition to 42 per cent copper. Diffusion of copper in the solid eliminates concentration gradients, and the f$$zen portion of tho melt is a solid solution containing 42 per cent copper (a288°C).
fin ally, at the solidus (1249°C) tho last copper liquid, containing 67 per cent copper, freezes to a solid containing
50 per cent copper. The excess copper atoms from the liquid diffuse into the metal to make the whole solid alloy a homogeneous solid solution of 50 per cent nickel, 50 per cent copper.
Metals that are not mutually soluble in all proportions combine as meohanical mixtures to fourm alloys. Alloys of this type are made up of two ehemic ally (and sometimes structurally) different tygtes of crystals^

ф .
he copper-rich crystals which freeze are beta-crystals
of 52*5 per cent copper* Simultaneously with their formation, more aluminium-rich. crystals are able to form, with the result that at the eutectic temperature a mechanical mix ture of fine copper-rich crystals and fine aluminium-rich crystals freeze to form an aggregate known as eutectic
The structure is sketched in fig*2*ЗЗцС.
Unfortunatelly (usually) for the metallurgist and
the heat treater,solidification in castings is seldom slow
enough to |
attain |
the ideal |
diffusion in the solid descr |
ibed above |
in two |
cases* Such ideal solid ification iis called |
|
equilibrium |
solidification.^ |
Most frequently, solidification |
of casting occurs under non-equilibrium conditions, in which lack of complete diffusion in the solid state results in
coring* In both two examples,the outer surface <bf the dend
rites would have had a considerably .higher copper content than the center, the dendrite would have been “gored*1* Por example, for the aluminium-copper alloy containing 10
per cent copper( the last case), the. composition o f Jbhe center of the dendrites can be as low as 1 or 2 per cent copper*
Coring |
in aluminium alloys contaning between 5*65 per eent |
|||
and 33 |
per cent copper results in an increase |
in the amount |
||
of eutectic obtained in the structure |
but does |
not |
lower |
|
the final solidification temperature* |
In the |
case |
of |
|
aluminium alloys containing less than 5*65 per |
cent |
copper, |
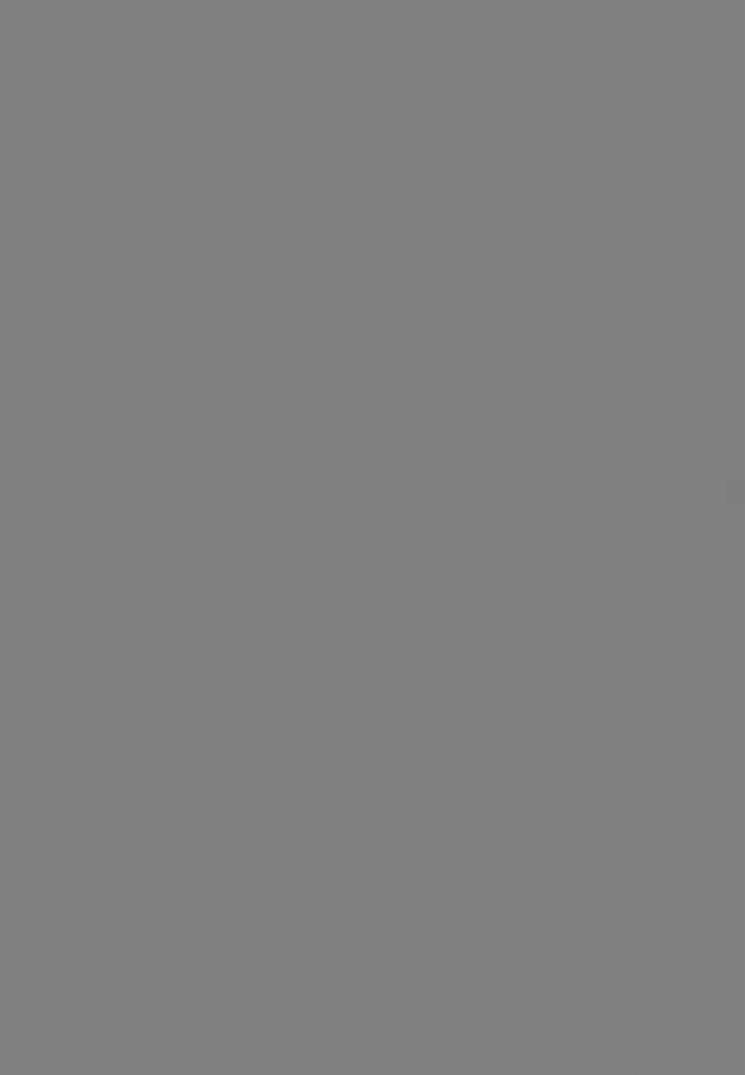
-improve casting ductility, especially in ingots which
are to be subsequently worked , or
-dissolve a maximum amount of certain desirable constit uents in the lattice structure iqo make the alloy amena-
ble'^Subsequent hardq^ng treatments#
An example of solution treatment for the latter purpose might be chosen from nearly any ane of the higher-
-strength aluminium, magnesium, or,copper-base alloys, typical of these is the aluminium -45 per cent copper
alloy |
(Fig,2#3£)# |
According to the phase diagram, i f |
||
the cast alloy |
is |
subsequently heated to a temperature of |
||
about |
5l6°C, it |
is |
a single-field and the beta |
phase w ill |
tend |
to dissolve# |
At this temperature, rate of |
diffusion |
are much faster than at room temperature, the rate of solution and the elimination of concentration gradients will occur in a reasonable length of time (8 to l6hours)# When the alloy is completely solutiorfeed, it is quenched (oooled rapidly ) to room temperature to retain the homo geneous, single-phase structure#
In certain alloys macrosegregation can take place# Macrosegregation is a chemical irregularity of an alloy in different parts of a solid casting# It is usually known as body or major segregation#
The process of cooling and freezing a cast alloy in the mould begins from the outer surface of the cast ing an&then is continuing in the direction to the wall centeri