
3218
.pdf
the shielded gas. ^etal-inert gas welding permits very high production rates but is usually economical only when fu ll utilization oan be made of the speo;! cf the process* It is finding use for repair and joining of large steel cast ings.
In gas welding the heat of ohemical combustion of two gases is used to melt the surface to be repaired (fig .3 ilO)*
Welding of some of the lowor-melting-point metals can be
accomplished by burning ixygen and hydrogen (oxyhydrogen)
flame). But for most commercial metals welding is conduct ed with a mixture of oxygen and acetylene. The oxyacetylene
flame is particularly veil adapted to welding. Flame temper |
|
atures as high as 3100°to 3300°C are obtained, and the chem |
|
ica l characteristics of the |
flame and its action on the |
weld metal aan be regulated |
closely. |
Depending on the ratio of oxygen to acetylene the oxy
acetylene flame may be neutral (the ratio is about |
1.04-1.14); |
||
oxidizing ( the ratio is about 1.15-1.51) |
, or carburizing |
||
(the ratio is about 0.$5-0.95). |
|
|
|
^he neutral flame is edeal for welding |
steel; |
the |
|
molten pool of weld metal remains clear |
and quielr’; |
with |
|
no boiling, foaming, or sparking. |
|
|
|
The flame protects the metal from oxidation |
• The result |
||
is clean, sound, and ductilo weld .metal |
i f |
all other var |
|
iables as welding rod and manipulation are |
under control. |

Exothermic welding*
Large shrinkage cavities, cracks, and other forms of
gross porosity are sometimes repaired with exothermic meth
ods* |
This |
technique*' is similar to |
that |
used for |
exother |
mic risers* |
The area to be repaired |
is |
cleaned as |
for |
|
standard welding, and a dgm of sand or other refractory |
|||||
built |
around it* For repairing steel |
castings, a mixture |
of iron-oxide aluminum, and alloy powders (blended to give
proper |
composition in the |
fille r |
metal) |
is either charged |
|||
into a |
separate |
melting chamber, |
or used |
to |
f i l l |
a large |
|
mould |
above the |
defective |
area# |
The mixture |
is |
ignited |
" in situ" or reacted in the separate vessel and the molten metal formed extthermally (without additons of ext ernal heat) is poured into the mould* Either method is used
satisfactorily. |
Lletal is formed by the |
exothermic reaction* |
||||
|
|
Fe2°3 |
+ 2 A1 * A1203 + 2 Fe |
|
|
|
and about 2500°C, |
and this metal ^ttlea readily from the |
|||||
AlgO^ slag* |
The porous area is melted by |
the |
high heat |
|||
and |
a sound weld |
is formed# The weld deposit |
can be made |
|||
to |
the chemsitjy |
desired, and is not limited to ferrous |
||||
compositions, by using other exothermic |
reactants, non— |
|||||
-ferrous alloys can also be repaired* |
|
|
|
|||
|
|
|
Plow welding,(’burning |
in") |
,_______ |
|
|
|
|
|
|
localized shrink |
|
|
Папу times casting defects such as |
|||||
age cavities are repaired by remelting and recastingln |
||||||
situ", using metal from the Idadle.The |
casting is embedded |
|||||
in |
sand, or |
a dam of sand molded around |
the defective area* |



squore cm, ia created in the tank* |
After this it is dried |
|
in air during 2-3 hours and heat -treated in a furnace. |
||
Regi'-rai of the heat-treatment is the following: an in itia l |
||
temperature in the furnace should be about 25-35°C, the |
||
rising of a temperature up to 80-100°C |
during 2 hours |
|
and then up to 130-160°C during 1 |
hour |
additionally, heat- |
-treatment at a |
temperature 160-1S0°G during 1.5 hours |
and cooling the |
casting together with the furnace up to |
the temperature |
about 30-36°C. |
The technological process for resin impregnation is similar to bakelite treatment, but in this case, the heating
of the casting before impregnation is not essential. Depending on the used resin castings are dried in air after impregna
tion or heat-treated as required to "set” the impregnant permanently.
After heat treatment, castings are shot-blasted and tested under the pressure topping the work pressure by
10-20%.
Hot natural drying o il As used |
for impregnation too. |
The impregnation is carried out under the pressure 2-3 |
|
kg/omo , iftet1 which the casting is |
dried in air during one |
day. |
|
When 10%-somtlon of liquid glass is used as an impreg |
|
nant the casting is also primerily |
heated up to a temperature |
about 85- 95°0 and after impregnation up to a temperature 100-110°C.
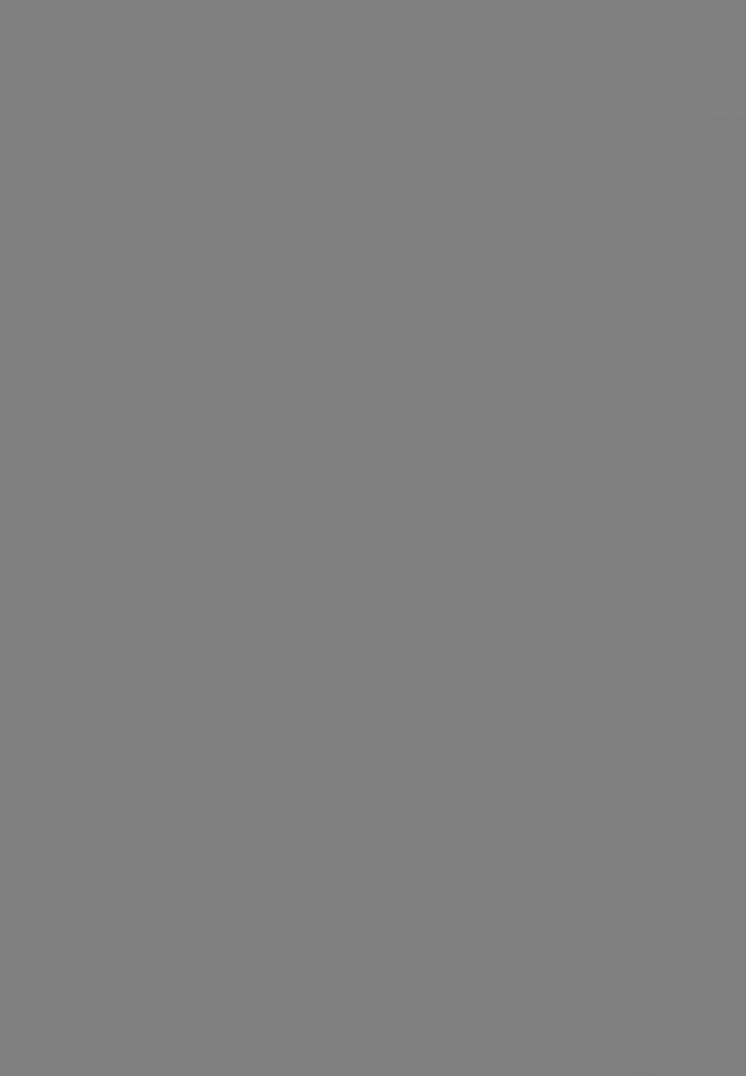
This Is a pasty mixture of |
iron |
filin gs |
in |
a hardening |
||||||
agent, which ’’sets" in air to very nearly the hardness |
||||||||||
and color of the oasting. It is |
d ifficu lt |
to |
notice repairs |
|||||||
of |
this |
sort |
on |
tiie |
surface |
of |
iron castings, |
particularly |
||
i f |
the |
part |
is |
later ground |
or |
machined |
and cleaned by |
|||
tumbling or shot-blasting. |
|
|
|
|
|
|||||
Today* |
repair |
of |
casting |
defects with |
epoxide compounds |
|||||
is |
widespreaded |
in |
practice |
of |
foundries* |
In this case |
the surface of defects to be repaired should be thoroughly cleaned by shotblasting and degreased with benzine, benzol,
acetone, etc, |
|
|
|
|
|
|
|
|
The composition |
of |
the |
compound whioh is used Is the |
|||||
following: |
|
|
|
|
|
|
|
|
|
epoxide |
resin |
|
|
-100 weight parts |
|||
|
dibutyl |
phthalate |
- 10-25 w.p* |
|||||
|
polyethylene polyamine - 8-9 w,p, |
|||||||
|
intei |
fille r |
- |
about |
60% of the resin weight |
|||
Portland cement |
, |
|
zini |
oxide, |
aluminium oxide, maroh- |
|||
a lite, |
ta ll may be |
used |
as |
a fille r |
material. All inert |
|||
fille r s |
should be |
dried |
at |
a temperature about 110 - 120°C, |
EpodtLde resin is mixed with dibutyl phthalate at a temperature 55- 60°0 , Polyethylene polyamine acts as a
hardener, and it is added into the mixture directly befiwe the use o£^
'"the compound. Due to the interaction 6f polyethylene polya mine with epoxide resin the temperature of the compound-