
926
.pdfАгломерацию применяют в том случае, когда в плавку по ступают мелкие малосернистые или бессернистые материалы, т. е. образующиеся газы не могут быть использованы для про изводства серной кислоты.
Рис. 15. Схема производства брикетов и шихтовка при медно сер ной ,плав!ке
При агломерации преследуются две цели: |
1) 0КУС |
|
||
мелкого материала и 2) |
окисление сульфидов |
(в СЛУ4^ |
|
|
мерации сернистых материалов). Агломерацию произв Д |
||||
прямолинейных машинах с прососом воздуха через сл0^ |
; |
|||
Агломерационная машина (рис. 16) |
состоит из не.пР £ едви_ |
|||
цепи стальных тележек |
с решетчатым |
дном (паллет;, |
i |
гающихся на роликах вокруг клепаной рамы с помощью двух приводных звездочек. Внутри машины расположены камеры всасывания, в которых постоянно поддерживается разрежение. Специальными пластинами тележки плотно прижимаются к «бортам камеры всасывания.
Шихта с помощью питателя ровным слоем распределяется по ширине паллеты. Загруженная тележка проходит под зажига-
Шихта
Рис. 16. Схема прямолинейной агломерационной машины:
1 — рама; 2 — тележка; |
3 |
— |
зажигательная печь; 4 — камеры |
всасывания; |
5 |
— |
приводной механизм |
тельной печью и сульфиды или топливо воспламеняются. В мо- % мент воспламенения паллета находится над камерой всасывания а через шихту просасывается воздух.
Наряду с горением топлива реакции окисления, протекаю щие в слое шихты, сопровождаются выделением тепла, что и обеспечивает оплавление ее частичек. При дальнейшем про движении тележки шихта охлаждается и превращается в спечен ный агломерат. В разгрузочном конце машины агломерат от рывается от тележки, скатывается на грохот и с него в прием ный бункер.
В отечественной практике в настоящее время для агломера ции медьсодержащих материалов применяют машины размером 25 X 2 м с площадью всасывания эО м2. К шихте агломерации предъявляют следующие требования:
1) шихта должна содержать 10—12% |
влаги, |
которая явля |
|
ется своеобразным терморегулятором |
процесса, |
снижает рас- |
|
° лыливание при загрузке и унос пыли |
в |
газоходную систему; |
2)шихта должна быть не крупнее 5—6 мм и содержать •фракции различных классов, что обеспечивает равномерный про рос через нее воздуха;
3)все компоненты шихты должны быть тщательно переме
шаны.
По сравнению с брикетированием агломерация имеет сле дующие преимущества:
1) значительно меньший расход топлива (при агломерации сернистых материалов), которое расходуется только на зажи гание шихты;
2)для агломерата характерно низкое содержание серы, что обеспечивает при плавке получение более богатых штейнов;
3)агломерат имеет значительно .большую прочность, что обеспечивает при плавке меньшее пылеобразование и унос пыли;
4)пористая структура агломерата обеспечивает хорошую га зопроницаемость шихты, что улучшает технико-экономические показатели плавки.
При агломерации сульфидных медьсодержащих материалов достигнуты следующие показатели при удельной производитель ности агломерационной машины 118—25 т шихты на 1 м2 эффек тивной поверхности всасывающей камеры в сутки:
Выход годного агломерата, |
% от веса шихты |
80—85 |
|
Расход электроэнергии на 1 |
пг шихты, квпг-ч |
15—20 |
|
Выжиг серы, % . . |
|
|
50—70 |
Извлечение меди, % |
|
|
99,0—99,7 |
Производительность агломерационной машины можно под |
|||
считать по формуле |
|
|
|
Q = №KBHyV, |
|
||
где Q — производительность машины |
за сутки, |
т/м2; |
|
К — выход годного агломерата, т; |
|
||
В — ширина машины, м; |
|
|
|
Н — высота слоя шихты, м; |
|
|
|
у — насыпной вес шихты, т/м3; |
|
|
|
V — скорость движения машины, м/мин. |
|
||
При агломерации бессернистых |
материалов (сора и др.) в |
||
шихту добавляют 10—12% |
коксика. |
|
|
ОСНОВНЫЕ ПОЛОЖЕНИЯ ТЕОРИИ ШАХТНОЙ ПЛАВКИ
Полупиритная плавка
Отличительные особенности полупиритной плавки следую щие:
1) процесс идет за счет тепла, выделяющегося при окисле нии сульфидов, и тепла горения топлива, причем количество топлива (кокс) составляет от 2,5—3% до 12—12,5%;
2) кокс не сгорает в нижней части подготовительной зоны печи, а достигает области фурм и сгорает за счет кислорода дутья.
44
В зависимости от физико-химических превращений, проис ходящих при. шахтной плавке, шахтную печь по высоте (сверху вниз) можно условно разбить на следующие зоны:
1. Подготовительная зона — от верхнего уровня загружен ной шихты до области печи с температурой 700° С. Здесь проис ходит подсушивание шихты с удалением влаги, нагрев шихты поднимающимися снизу газами, начинаются и в основном за канчиваются процессы разложения сульфидов, а также начина ется разложение известняка.
2. Зона ликвации сульфидов — занимает область с темпера
турой от 700 до |
1000° С. Здесь происходит плавление сульфидов |
с образованием |
легкоплавких сплавов и заканчивается разло |
жение известняка.
3. «Фокус» печи — зона в области фурм. Здесь температура достигает 1000—1400° С, все пространство печи заполнено рас каленными кусками кварца, окиси кальция и кокса, происходит
•окисление сульфидов железа и образование |
шлака |
и |
штейна. |
||
4. |
Нижняя |
зона печи — внутренний горн, |
в котором |
собира |
|
ются |
жидкие |
продукты плавки., |
|
350° С на |
|
В подготовительной зоне при температуре около |
|||||
чинается окисление сульфидов железа: |
|
|
|
2FeS2 + 5V20 2 = Fe20 3 + 4S02,
3FeS2 + 802 = Fe30 4 + 6S02.
Образующаяся окись железа в присутствии сульфидов легко переходит в магнетит:
10Fe2O3 + FeS = 7Fe30 4 + S02,
16Fe20 3 + FeS2 = 1 lFe30 4 + 2S02*
Магнетит практически без изменений доходит до зоны мак симальных температур и над фурмами разлагается кремнезетмом, жидкими сульфидами и углеродом с образованием сили катов:
3Fe30 4 + FeS + 5Si02 = 5Fe2Si04 + S02 — 4760 кал (20 кдж),
Fe30 4 + СО (С) = 3FeO + С02 (СО).
Из-за недостаточного контакта между исходными вещест вами разложение магнетита идет не полностью и часть его растворяется в штейне и шлаке.
Сульфиды меди в процессе плавки частично окисляются: 6CuFeS2 + 17V20 2 = 3Cu20 + 2Fe30 4 + 12S02,
Cu2S + IV2O2 = Cu20 + S02,
до образовавшаяся закись меди снова сульфидируется серни стым железом
Cu20 -f- FeS —Cu2S FeO.
Сульфид цинка частично разлагается и уносится е газами в виде летучих соединений (10—15% от общего содержания цинка в шихте), частично окисляется в подготовительной зоне* но в основном окисляется над фурмами и в виде окиси пере ходит в шлак:
ZnS + 1 V2Os = ZnO + S02.
В шлак переходит .от 44 до 86%' цинка от содержания его» в шихте, что вызывает повышение температуры плавления шла ка. Окисные соединения цинка реагируют с кварцем с образо ванием тугоплавких силикатов, которые отлагаются в верхней части печи в виде настылей и нарушают нормальный ход плавки. Таким образом, присутствие в шихте соединений цинка для шахтной плавки нежелательно, особенно при содержании более
10%.
Тепло, необходимое для процесса полупиритной плавки, об разуется в результате горения кокса:
С + 0 2 = С02 + ~ 97 000 кал (32,546 Мдж)
и в результате окисления сернистого железа:
FeS + 1V20 2 = FeO + $02 + |
~ 113 500 кал |
(476,7 кдж) |
|
или ~ 75 600 кал (316,62 кдж) |
на II г-моль |
кислорода; |
кис |
лород дутья в первую очередь расходуется на горение кокса. Раскаленный кокс частично восстанавливает сернистый ан
гидрид
С + S02 = С02 + V2S2 + ~ 28 000 кал (117,6 кдж),
что также является дополнительным источником тепла. Однако при избытке кокса возможна реакция
С + С02 = 2СО — 41 000 кал (169,2 кдж),
что отрицательно сказывается на тепловом балансе печи и вы зывает перерасход кокса.
В верхней подготовительной зоне печи высшие сульфиды же леза и меди разлагаются с выделением элементарной серы. Поскольку атмосфера в печи окислительная, здесь имеют место процессы, аналогичные протекающим на верхних подах обжи говой печи. Таким образом, десульфуризация при полупиритной плавке складывается из:
1) диссоциации и окисления сульфидов и взаимодействия сульфидов с окислами в твердой фазе в подготовительной^ зоне печи;
2) окисления расплавленных сульфидов в зоне фурм.
В практических условиях десульфуризация при полупирит ной плавке достигает 50—75%,
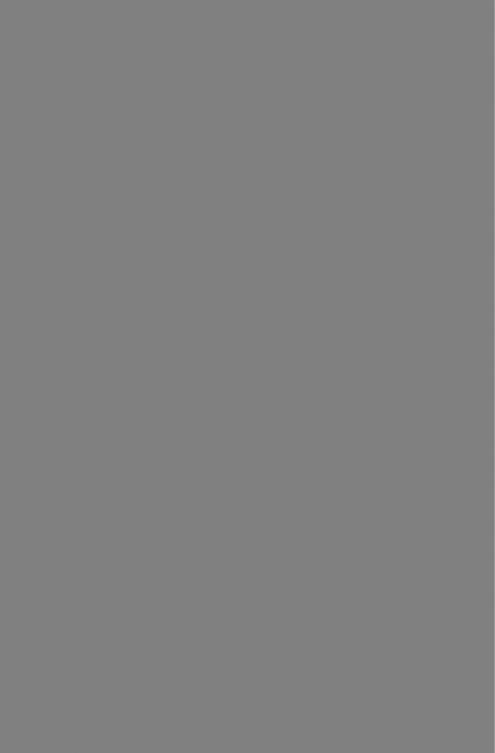
печи увеличивают на 2 м и между двумя верхними зонами и «фокусом» печи создают дополнительную восстановительную зону, для чего повышают до 8—10% подачу в шихту кокса. Чтобы до максимума снизить подсос воздуха и разубоживание газов, колошник печи и загрузочное устройство делают герме тичными. Чтобы не допустить конденсации серы в газоходах
{точка кипения |
серы 444,5° С), |
температуру отходящих газов |
||
поддерживают |
около 450° С. Для_ этого |
шахту печи |
кессони- |
|
руют только до |
области фурм, |
а выше |
выполняют из |
кирпича |
и заключают в металлический кожух.
Распределение серы по продуктам плавки выглядит следую щим образом, %:
Штейн |
9 ,8 |
Шлак . . . |
4 ,5 |
Газоходная пыль |
0,5 |
Газы |
8 5 ,2 |
В том числе в виде: |
|
элементарной |
77 |
s o 2 |
8 ,2 |
Из нижней (окислительной) зоны в восстановительную по ступают газы состава: 85% N2, 14—15% SO2 и небольшое коли чество углекислого газа.
В восстановительной зоне углерод раскаленного кокса вос станавливает S02:
С -j- S02 —С02 ~Ь V2S2 28 000 кал (117,04 кдж).
Чтобы эта реакция протекала достаточно полно, кокс должен иметь большую поверхность. С этой целью применяют пористый доменный кокс крупностью 25 мм.
Помимо указанной основной реакции, в восстановительной зоне протекает ряд побочных:
2С + 0 2 = 2СО + 36 000 кал (151,2 кдж), С + S2 = CS2 — 29000 кал (121,8 кдж), 1/2S2 СО = COS -j- 8000 кал (33,4 кдж),
S02 + 2СО = 2С02 + V2S2 + 67 000 кал (281,4 кдж), 2Н20 1V2S2 = 2H2S -f- S02,
H20 + FeS = FeO + H„S.
■0
Выходящие из печи газы в среднем содержат 1,5—>1,7% S02, 0,8-1,0% COS, 0,3—0,9% CS2, 0,2—0,5% H2S, 13,5—14,6%. С02, 57—67% г/м3 элементарной серы. Состав газов по ходу плавки непостоянен, но для нормальной работы химического цеха не обходимо, чтобы содержание S02 не опускалось ниже 1,8%. Га зы проходят систему очистки от пыли и вредных примесей (в ча стности, мышьяка) и поступают в контактные камеры химичес кого цеха, где сера конденсируется и в жидком виде стекает в
48
приемники. Углеродистые соединения серы и сероводород реа гируют с сернистым ангидридом с выделением элементарной се ры. В результате извлечение серы составляет 78—80% от обще го «количества ее в шихте.
Для усовершенствованной пиритной или медно-серной плав ки присутствие цинка в шихте еще более вредно, так «как обра зующиеся окись цинка и парообразный цинк 'понижают пори стость шихты и способствуют образованию настылей. Поэтому для медно-серной плавки необходимы чистые пиритные руды с минимальным содержанием цинка (доЗ%) и мышьяка (до 0,5%).
Процессы шлако- я штейнообразования при медно-серной плавке аналогичны процессам, протекающим при любой шахт ной плавке сульфидных материалов. Штейн обычно получается с невысоким (8—Л2%) содержанием меди, поэтому его подвер гают повторной (сократительной, или концентрационной) полупиритной плавке в обычных шахтных печах.
МАТЕРИАЛЬНЫЙ И ТЕПЛОВОЙ БАЛАНСЫ ШАХТНОЙ ПЛАВКИ
Материальный и тепловой балансы рудной и сократительной плавки (на 1000 к г руды и штейна) приведены в табл. 12—15 и на рис. 17.
Тепло химических |
|
|
реакций, |
Отходящие |
|
шихть/ и воздуха |
||
газы |
||
|
||
|
39-Ы А |
Реакции диссоциации 13-
Потери в отпосферу
i^ A w v x A w m /5-/6%
Шлак 26-28%
Штейн
J-4%
Рис. 17. Тепловой баланс шахтной печи
4 Б. В. Мальцев |
49 |
|
|
Поступило в печь |
|
|
Получено к г |
в |
|
|
|
|
содержа |
вес |
|
|
|
|
Ш И Х Т Ы |
ние |
к г |
штейне |
шлаке |
|
|
|
|
|
% |
|
|
|
|
Халькопирит CuFeS2 |
7,4 |
74,0 |
— |
— |
— |
||
В том числе: |
1 |
25,6 |
|
— |
|||
Си |
|
|
34,6 |
25,6 |
— |
||
Fe |
|
|
30,5 |
22,6 |
22,6 |
— |
— |
S . . |
|
34,9 |
25,8 |
25,8 |
— |
— |
|
Сфалерит ZnS |
|
4,4 |
44,0 |
— |
— |
— |
|
в том числе: |
67,0 |
29,5 |
3,4 |
13,1 |
13,0 |
||
Zn |
|
|
|||||
S . |
. |
33,0 |
14,5 |
1,7 |
6,5 |
6,3 |
|
Пирротин Fe7S8 |
33,5 |
335,0 |
— |
— |
— |
||
В том числе: |
60,4 |
202,0 |
57,1 |
144,9 |
|
||
Fe |
|
|
— |
||||
S ............................ |
39,6 |
133,0 |
12,3 |
— |
120,7 |
||
Биотит |
KH2(Mg, Fe)3-(A1, Fe)- |
12,2 |
122,0 |
— |
—■ |
— |
|
•Si30 12 |
|
||||||
В том |
числе: |
27,8 |
33,9 |
— |
33,9 |
— |
|
А120 3 |
|
||||||
Si02 |
|
39,4 |
48,1 |
— |
48,1 |
— |
|
F e O ............................. |
32,8 |
40,0 |
— |
40,0 |
— |
||
Актинолит Са (Mg, Fe)3 Si40 12 |
17,1 |
171,0 |
— |
— |
|
||
В том числе: |
13,4 |
22,9 |
— |
22,9 |
— |
||
СаО |
|
||||||
MgO |
|
22,4 |
38,2 |
— |
38,2 |
— |
|
FeO |
|
9,0 |
15,4 |
— |
15,4 |
— |
|
Si02 . . |
55,2 |
94,5 |
— |
94,5 |
— |
||
Кальцит CaC03 |
10,4 |
104,0 |
— |
— |
— |
||
В том числе: |
56,0 |
58,2 |
|
58,2 |
|
||
СаО |
|
— |
— |
||||
С02 |
|
44,0 |
45,8 |
— |
— |
45,8 |
|
Кварц Si02 |
|
14,1 |
141,0 |
— |
14,0 |
— |
|
Прочие |
|
|
0,9 |
9,0 |
— |
9,0 |
|
Кокс (5% от веса шихты) |
— |
50 |
— |
— |
|
||
В том числе: |
2,3 |
1,1 |
|
1,1 |
|
||
Fe |
|
|
— |
— |
|||
S |
|
|
1,6 |
0 , 8 |
— |
— |
0 , 8 |
|
|
4,2 |
— |
4,2 |
|
||
SiOo |
|
8,4 |
— |
||||
А12б 3 |
|
3,6 |
1,8 |
— |
1,8 |
— |
|
С |
|
|
83,9 |
42,0 |
— |
— |
42,0 |
прочие |
|
0,2 |
0,1 |
— |
— |
0 , 1 |
|
Дутье, воздух |
|
— |
2079 |
— |
|
|
|
В том числе: |
23,0 |
478,0 |
|
41,4 |
436,6 |
||
о 2 |
|
|
— |
||||
N2 |
|
77,0 |
1601,0 |
— |
— |
1601,0 |
|
Влага |
|
|
— |
31,7 |
— |
— |
— |
В том числе: |
|
10,0 |
|
|
|
||
в шихте |
|
— |
— |
— |
1 0 , 0 |
||
в дутье |
|
|
21,7 |
|
|
О 1 *7 |
|
|
— |
— ■ |
|
21,7 |
|||
|
|
И т о г о |
— |
3160,7 |
148,5 |
714,2 |
2298,0 |
|
|
|
|
|
|
|
Т а б л ица |
13 |
|
|
ТЕПЛОВОЙ БАЛАНС РУДНОЙ ПЛАВКИ НА 1000 кг РУДЫ |
|
|
||||||
|
|
1 ккал = |
4186,8 |
дж |
|
|
|
|
|
|
Приход |
ккал |
% |
|
Расход |
ккал |
|
% |
|
Горение С в С02 |
340200 |
39,2 |
Разложение СаС03 |
46991 |
5,4 |
||||
Горение S в S02 |
276560 |
31,9 |
Разложение FeS |
62104 |
7,1 |
||||
Окисление Fe в FeO |
169968 |
19,5 |
Разложение ZnS |
8600 |
1,0 |
||||
Окисление Zn в ZnO |
16965 |
2,0 |
Тепло со штейном |
33413 |
3,9 |
||||
Образование 2FeO SiOs |
31816 |
3,6 |
Тепло со шлаком |
232115 |
26.7 |
||||
Образование C aO Si02 |
18554 |
2,1 |
Тепло с газами |
354633 |
40.8 |
||||
Тепло шихты |
5250 |
0,6 |
Потери в атмосферу |
131201 |
15,1 |
||||
Тепло дутья .................... |
9744 |
1,1 |
|
|
|
|
|
|
|
|
И т о г о |
869057 |
100,0 |
|
И т о г о |
869057 |
100,0 |
||
|
|
|
|
|
|
|
Т а б л и ц а |
14 |
|
МАТЕРИАЛЬНЫЙ БАЛАНС СОКРАТИТЕЛЬНОЙ ПЛАВКИ НА 1000 кг ШТЕЙНА |
|||||||||
|
Поступило в печь |
|
|
Получено, кг, |
В |
|
|||
|
шихты |
|
содер- |
вес |
|
|
|
|
|
|
|
жание |
штейне |
шлаке |
газах |
||||
|
|
кг |
|||||||
|
|
|
|
% |
|
|
|
|
|
Штейн |
. . |
|
|
|
1000 |
|
|
|
|
в том |
числе: |
|
|
|
|
|
_ |
|
_ |
Си |
|
|
|
16,0 |
160,0 |
160,0 |
|
||
Fe |
|
|
|
4 9 ,8 |
4 9 8 ,0 |
6 9 ,5 |
4 2 8 ,5 |
|
_ |
Zn |
|
|
|
2 ,1 |
2 1 ,0 |
2 , 5 |
9 ,2 |
|
9 ,3 |
S |
. |
|
|
2 4 ,9 |
2 4 9 ,0 |
7 3 ,6 |
4 ,6 |
|
170,8 |
прочие |
|
|
7 ,2 |
7 2 ,0 |
_ |
7 2 ,0 |
|
_ |
|
Кварц S i 0 2 |
|
100,0 |
2 9 3 ,0 |
— |
2 9 3 ,0 |
|
_ |
||
Кокс |
. . . |
|
|
— |
5 ,0 |
— |
— |
|
4 1 ,9 |
в том |
числе: |
|
|
|
|
|
_ |
|
|
С |
|
|
|
8 3 ,9 |
4 1 ,9 |
— |
|
4 1 ,9 |
|
Fe |
|
|
|
2 ,3 |
1,2 |
— |
1,2 |
|
— |
S |
|
|
|
1,6 |
0 , 8 |
— |
|
|
0 ,8 |
S i 0 2 |
|
|
8 , 4 |
4 ,2 |
— |
4 ,2 |
|
1,9 |
|
прочие |
|
|
3 ,8 |
1 ,9 |
------- |
|
|
||
|
|
|
|
|
|
|
|
|
|
Д утье, воздух |
|
|
— |
2874 |
— |
— |
|
|
|
в том |
числе: |
|
|
|
|
|
|
|
|
N 2 |
|
|
|
7 7 ,0 |
2 2 1 3 ,0 |
_ |
— |
2 2 1 3 ,0 |
|
0 2 |
|
|
|
2 3 ,0 |
6 6 1 ,0 |
122,8 |
|
5 3 8 ,2 |
|
Влага |
. . . |
|
|
— |
40 |
— |
_ |
|
|
в том |
числе: |
|
|
|
|
|
|
|
|
в штейне |
|
|
— |
1 0 ,0 |
— |
— |
|
10,0 |
|
в дутье |
|
|
— |
3 0 ,0 |
— |
— |
|
3 0 ,0 |
И т о г о |
— |
4257,0 |
305,6 |
93 5 ,5 |
3015,9 |