
675
.pdf
компания RWE Energy. Конструкция такой трубки (рис. 11) мало отличается от классической (см. рис. 1) [16]. При прохождении вдоль трубки часть газа охлаждается. Для некоторых компонентов, таких как пар, наступает температура конденсации. Также действует центробежная сила, которая прижимает конденсат и другие тяжелые компоненты к стенке трубки.
Далее компоненты стекают через специальные отверстия в специальный резервуар для конденсата. Поток горячего газа через специальную щель проходит по специальной трубе и соединяется с холодным потоком.
Конструкция изображена схематично на рис. 12. Газ из трубопровода проходит в подогреватель, после чего происходит впрыскива-
ние в газ гликоля. Впрыскивание и предварительный нагрев нужны для предотвращения образования гидратов и гидрокарбонатов. После этого газ подается через контрольный клапан в вихревую трубу, где происходит его осушка. Далее горячий поток газа, в котором содержится гликоль, приходит в холодный сепаратор, где за счет охлаждения происходит регенерация гликоля, а также горячий поток соединяется с конденсатом. Но теперь смешивания газа и конденсата не происходит, так как конденсат находится в жидком состоянии.
Рис. 12. Схема установки для сепарации газов [16]
51
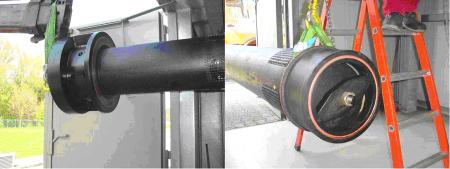
Затем гликоль по трубопроводу идет к началу установки, где происходит его впрыскивание. Далее горячий поток с конденсатом соединяется с холодным потоком и идет в сепаратор, где происходит слив конденсата. Поток газа идет в подогреватель, после чего поступает дальше в сеть.
Следует отметить, что на практике используются две вихревые трубы. Они функционируют по отдельности или параллельно в зависимости от давления газа и величины потока. В каждую трубу на входе газ поступает из двух труб. Чтобы разбить входной поток газа и контролировать его поступление в вихревую трубу, используются два контрольных клапана. Входные отверстия труб сконструированы так, чтобы максимально увеличить скорость потока.
Данная установка была разработана немецкой фирмой в 2000 г. и внедрена в производство в 2006 г. Установка привлекает своей простотой, высокой надежностью и долговечностью. На рис. 13 изображена вихревая труба после пяти лет успешного функционирования. На ней не обнаружено никаких видимых следов механического износа. По сравнению с традиционными установками для осушки газа применение гликоля было снижено на 90 %, а также существенно сокращено негативное влияние на окружающую среду.
Рис. 13. Вихревая труба после пяти лет испытаний
В России применение вихревых труб для сепарации газов пока развито недостаточно. Компания RWE Energy применяет самую простую конструкцию вихревой трубы и только для сепарации природного газа. Возможно усовершенствование вихревой трубы и установки в целом, а также разработка подобной установки для сепарации попутного нефтяного газа. Также возможно создание численной математической модели установки, которая бы позволила моделировать основные процессы, происходящие в вихревой трубе, оценивать ее эффективность и нормальное функционирование и усовершенствовать конструкцию.
52
Список литературы
1.Мартыновский В.С., Мельцер Л.З. О холодильном эффекте вихревой трубы // Холодильная техника. – 1952. – № 4.
2.Мартыновский В.С. Алексеев В.П. Вихревой эффект охлаждения
иего применение // Холодильная техника. – 1953. – № 3.
3.Мартыновский В.С., Алексеев В.П. Термодинамический анализ эффекта вихревого температурного разделения газов и паров // Теплоэнергети-
ка. – 1955. – № 11.
4.Мартыновский В.С., Алексеев В.П. Эффект вихревого температурного распределения перегретых паров и опытная проверка гипотезы Хильша – Фультона // Известия АН СССР. – 1956. – № 1.
5.Меркулов А.П. Вихревой эффект и его применение в технике – М.: Машиностроение, 1969. – 185 с.
6.Вихревые аппараты / А.Д. Суслов, С.В. Иванов, А.В. Мурашкин, Ю.В. Чижиков. – М.: Машиностроение, 1985. – 256 с.
7. Гуцол А.Ф. Эффект Ранка // Успехи физических наук. – 1997. –
Т. 167, № 6. – С. 665–687.
8.Leont’ev A.I. Gasdynamic methods of temperature stratification // Fluid dynamics. – 2002. – Vol. 37, № 4. – P. 512–536.
9.Коновалов В.И., Орлов А.Ю., Гатапова Н.Ц. Сушка и другие технологические процессы с вихревой трубкой Ранка – Хильша: возможности и экспериментальная техника // Вестник ТГТУ. – 2010. – Т. 16, № 4. – С. 803–825.
10.Baker P.S., Rathcamp W.R. Investigations on the Ranque – Hilsh (vortex) tube / Oak Ridge National Laboratory. – Oak Ridge, 1954. – 38 р.
11.Ahlborn B.K., Gordon J.M. The vortex tube as a classic thermodynamic refrigeration cycle // Journal of applied physics. – 2000. – Vol. 88, № 6. – P. 3645– 3653.
12.Gao C. Experimental study on the Ranque – Hilsh vortex tube // PhD Study. – 2005. – 151 р.
13.Fulton C.D. Comments on the vortex tube // J. ASRE Refrigerating Engng, – 1950. – Vol. 58.
14.Cockerill T. Ranque – Hilsh vortex tube // Master thesis, University of Cambridge, 1995.
15.Linderstorm-Lang C.U. Studies on transport of mass and energy in the vortex tube // The significance of the secondary flow and its interaction with the tangential velocity distribution. Riso report, Denmark, 1971. – 30 р.
16.Gronner J. Sucessful experience with vortex tube technology at the epe cavity storage of RWE Energy // 23rd World Gas Conference. – Amsterdam, 2006. – 11 р.
Получено 1.11.2012
53
Коркодинов Ярослав Александрович – аспирант, Пермский нацио-
нальный исследовательский политехнический университет (614990, г. Пермь,
Комсомольский пр., 29, e-mail: svarogjk1989@rambler.ru).
Хурматуллин Олег Гаднанович – соискатель ПНИПУ, «Урал-
инструмент-Пумори» (614107, г. Пермь, ул. Инженерная, 14, e-mail: oleg@uipumori.ru).
Korkodinov Iaroslav Aleksandrovich – Graduate Student, Perm National Research Polytechnic University (614990, Perm, Komsomolsky av., 29, e-mail: svarogjk1989@rambler.ru).
Khurmatullin Oleg Gadnanovich – Applicant, Ural-Tool-Pumori Ltd (614107, Perm, Inzhenernaya st., 14, e-mail: oleg@uipumori.ru).
54
УДК 621.762.4.044
И.В. Яковлев, В.М. Оголихин, С.Д. Шемелин
I.V. Yakovlev, V.M. Ogolikhin, S.D. Shemelin
Институт гидродинамики им. М.А. Лаврентьева СО РАН, г. Новосибирск
Lavrentyev Institute of Hydrodynamics Siberian Branch of RAS, Novosibirsk
ВЗРЫВНОЕ ИЗГОТОВЛЕНИЕ МЕТАЛЛОКЕРАМИЧЕСКИХ ЗАЩИТНЫХ КОНТЕЙНЕРОВ
EXPLOSIVE FABRICATION OF METALLOCERAMICS
PROTECTIVE CONTAINERS
Показана возможность использования энергии взрыва при создания контейнеров для перевозки и хранения радиоактивных веществ.
Ключевые слова: взрывное компактирование, металлокерамический контейнер, радиоактивное вещество, взрывчатое вещество, структура компакта.
The possibility of using the explosive energy to create metalloceramics containers for the transport and storage of radioactive substances is presented.
Keywords: explosive compaction, metalloceramics container, radioactive material, high explosive, structure of compact. .
При транспортировке и хранении радиоактивных веществ требуется эффективная защита от излучения. Известно, что карбид вольфрама, как защитный материал, достаточно успешно справляется с подобными задачами. Однако карбид вольфрама существует в виде порошка, компактирование которого в форме законченного изделия ни динамическими, ни статическими методами невозможен.
При этом имеются доказательства того, что использование энергии взрыва для консолидации и компактирования порошковых композиций является перспективным направлением создания композиционных материалов [1]. При этом следует иметь в виду, что взрывное нагружение твердых и хрупких порошковых материалов может привести только к их уплотнению, но не консолидации. В таких порошковых композициях положительный эффект достигается добавлением в основной порошок связки из пластичного порошкового материала.
55
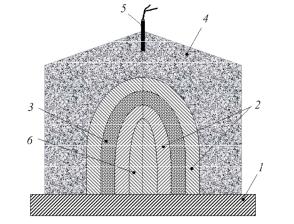
Процессы, протекающие в порошке при его взрывном компактировании, существенно отличаются от процессов при статическом прессовании. При взрывном компактировании не происходит одновременного уплотнения по всему объему изделия. Ударная волна, проходя через порошок, оставляет за собой скомпактированный материал. Высокая скорость нагружения за очень короткое время действия ударного импульса приводит к повышению температуры в компакте до значений порядка точки плавления материала порошка и может привести к частичному спеканию по поверхностям контакта [2]. Считается, что процесс консолидации порошков под действием ударных волн происходит стадию дробления частиц, а затем – уплотнения и оплавления контактных границ в результате взаимного трения.
Взрывным компактированием получаются заготовки, которые после механической обработки превращаются в изделия. Свойства заготовок, в первую очередь плотность порошковой составляющей, в значительной степени зависят от схем взрывного компактирования. Различные схемы взрывного компактирования наиболее полно представлены в работе [3]. В настоящей работе рассматривается взрывное компактирование порошковых материалов в специальных цилиндрических ампулах. При этом нагружение осуществляется скользящей ударной волной, образующейся в результате взрыва цилиндрических зарядов взрывчатого вещества (рис. 1).
Рис. 1. Схема взрывного компактирования порошковых материалов в ампулах сложной конфигурации: 1 – основание; 2 – сферическо-цилиндрическая ампула (с внутренней и внешней оболочками); 3 – полость технологической ампулы со смесью порошков; 4 – заряд взрывчатого вещества; 5 – детонатор; 6 – технологическая вставка
В процессе разработки схем взрывного компактирования порошковых материалов в цилиндрических ампулах необходимо обеспечить однородность нагружения по длине ампулы, исключить образование трещин и разрушений
56

врадиальном и осевом направлениях, а также исключить неоднородность компакта.
Для изготовления защитных контейнеров кроме цилиндрических элементов необходимы также плоские многослойные элементы, содержащие
вкачестве внутреннего слоя порошок. В результате проведенных исследований был разработан способ, позволивший получить многослойное изделие с внутренним слоем из карбида вольфрама.
По схеме, приведенной на рис. 1, были выполнены заготовки цилиндри- ческо-сферической формы тел вращения, которые после механической обработки превращались в элементы защитных устройств (рис. 2). Представленный контейнер состоит из трех слоев: сталь – спрессованная смесь порошков карбида вольфрама и меди (10 %) – сталь. При исследовании структуры спрессованного порошка было установлено, что такого количества меди достаточно, чтобы получился компакт с плотностью, близкой к плотности монолита. Такая конструкция наиболее эффективна при изготовлении малоразмерных контейнеров. Контейнер такой конструкции при изготовлении имеет определенную трудоемкость, резко возрастающую при увеличении его габаритов, поэтому была разработана схема более простого в изготовлении, но более емкого контейнера, включающего в себя в качестве основных элементов внутреннюю и внешнюю трубы из стали и порошк карбида вольфрама и меди между ними (рис. 3).
Рис. 2. Композиционный малоразмерный контейнер для защиты от ионизирующих излучений
57

Рис. 3. Цилиндрическая часть контейнера
Вместе с этим была отработана технология изготовления трехслойных дисков (сталь – порошковая смесь – сталь для элементов на верхний и нижний торец трехслойной цилиндрической детали, рис. 4).
Рис. 4. Трехслойный диск: сталь – карбид вольфрама – сталь
При отработке технологии изготовления цилиндрических контейнеров были получены трехслойные трубы с внутренним и внешним диаметрами 60 и 110 мм соответственно и длиной 330 мм, а также трехслойные диски диаметром 135 мм и толщиной 15 мм. Из полученных элементов были изготовлены защитные контейнеры (рис. 5).
58
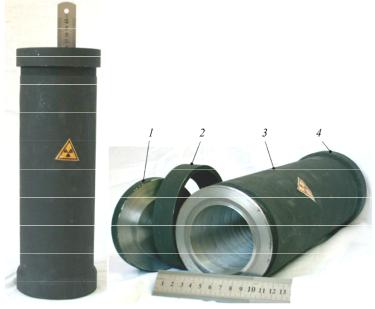
а |
б |
Рис. 5. Контейнер радиационно-защитный: а – контейнер; б – узлы и детали контейнера; 1 – крышка съемная; 2 – гайка; 3 – цилиндрическая часть контейнера; 4 – крышка несъемная
Представленные результаты свидетельствуют о том, что технология взрывного компактирования порошковых материалов в металлических ампулах сложной конструкции является перспективной для получения металлокерамических композитов, обладающих специальными свойствами.
Список литературы
1.Композиционные материалы и конструкции на основе титана и его соединений: монография / В.Н. Анциферов, Л.Д. Сиротенко, А.М. Ханов, И.В. Яковлев.– Новосибирск: Изд-во Ин-та гидродинамики им. М.А. Лаврен-
тьева СО РАН. – 2001. – 370 с.
2.Кузьмин Г.Е., Пай В.В., Яковлев И.В. Экспериментально-аналитиче- ские методы в задачах динамического нагружения материалов: монография. – Новосибирск: Изд-во СО РАН, 2002. – 312 с.
3.Рогозин В.Д. Взрывная обработка порошковых материалов: монография / ВолгГТУ. – Волгоград, 2002. – 136 с.
Получено 1.11.2012
59
Яковлев Игорь Валентинович – доктор технических наук, профессор, Институт гидродинамики им. М.А. Лаврентьева СО РАН (630090, г. Новоси-
бирск, пр. ак. Лаврентьева, 15, e-mail: yakovlev@hydro.nsc.ru).
Оголихин Виктор Михайлович – доктор технических наук, Институт гидродинамики им. М.А. Лаврентьева СО РАН (630090, г. Новосибирск,
ул. Терешковой, 29, e-mail: s-shem@yandex.ru).
Шемелин Сергей Дмитриевич – научный сотрудник, Институт гидродинамики им. М.А. Лаврентьева СО РАН (630090, г. Новосибирск, ул. Те-
решковой, 29, e-mail: s-shem@yandex.ru).
Yakovlev Igor Valentinovich – Doctor of Technical Sciences, Professor, Lavrentyev Institute of Hydrodynamics SB RAS (630090, Novosibirsk, Lavrentyeva av., 15, e-mail: yakovlev@hydro.nsc.ru).
Ogolikhin Viktor Michajlovich – Doctor of Technical Sciences, Lavrentyev Institute of Hydrodynamics SB RAS (630090, Novosibirsk, Tereshkovoy st., 29, e-mail: s-shem@yandex.ru).
Shemelin Sergey Dmitrievich – Scientific Researcher, Lavrentyev Institute of Hydrodynamics SB RAS (630090, Novosibirsk, Tereshkovoy st., 29, e-mail: s-shem@yandex.ru).
60