
487
.pdfкислотой. Размеры ванн зависят от размеров и числа электродов. В ваннах устанавливают до 45 катодов и 44 анода. Корпуса ванн изготовляют из бетона или дерева, стенки ванны внутри покрывают винипластом, свинцом или другим кислотоупорным материалом. Аноды соединяют с положительным полюсом источника постоянного тока. Параллельно каждому аноду по бокам его устанавливают соединенные с отрицательным полюсом катодные основы − тонкие (0,2…0,3 мм) листы электролитной меди, имеющие петли, с помощью которых их подвешивают в ванне. Катодные основы обычно шире и длиннее анодов.
При электролизе медь анода переходит в раствор по реакции
Сu = Сu2+ − 2е.
Ионы меди из раствора восстанавливаются и плотными кристаллами оседают на катодных основах по реакции
Сu2+ + 2е = Сu.
Примеси, имеющие более отрицательный потенциал (Zn, Fе, Ni, Bi, Sb, Аs и др.), переходят в раствор, но не могут выделиться на катоде при наличии в электролите большого количества ионов меди. Золото и серебро не переходят в раствор и оседают на дно ванны вместе с не успевшими раствориться на аноде отдельными кусочками меди, образуя шлам. В шлам переходят также соединения серы, селена и теллура.
Напряжение между анодом и катодом в ванне составляет примерно 0,3 В, электролит содержит 30…40 г/л Сu и 200 г/л Н2SО4. Электролит, имеющий температуру 50…55 °С, непрерывно циркулирует, переливаясь из одной ванны в другую, его периодически частично заменяют и очищают от накопившихся в нем примесей. Растворение анода длится 25…30 дней в зависимости от его массы и режима электролиза. Анодные остатки, составляющие
61
около 15 % первоначальной их массы, извлекают и заменяют новыми анодами.
Катоды выгружают через 5…12 дней во избежание короткого замыкания катодного осадка с анодом, так как расстояние между электродами только 30 мм, а катодный осадок часто образует наросты. Шлам, выпадающий на дно ванны, периодически выгружают при чистке ванн и направляют на переработку для извлечения из него полезных составляющих. Нередко в шламе содержится до 35 % Аg, 14…16 % Сu, 5…6 % Sb, 3 % Те и до 1 % Аu, а также другие ценные составляющие.
Катоды, извлеченные из ванн, тщательно промывают водой, а затем их направляют для переплавки или производства сплавов в электрических или отражательных печах. Из расплавленной рафинированной меди непрерывной разливкой получают заготовки для дальнейшей обработки давлением.
Товарная чистая медь в виде слитков может иметь 11 марок. Марки меди М00б, М0б и М1 получаются обычно только после ее электролитического рафинирования, другие марки могут быть получены и путем переплавки отходов. Для получения бескислородной меди (марка М0б) и меди с пониженным содержанием кислорода (М1р, М2р и др.) переплавку катода ведут в канальных индукционных электропечах со стальным сердечником, а разливку − в защитной среде непрерывно. Для меди марок с класса «р» и «ф» применяют раскисление фосфористой медью.
Суммарно допустимое количество примесей Bi, Sb, Аs, Рb, Sn, Fе, Ni, S, О для технической меди в марке М00 − 0,01 %, в самой низкой марке М3 − 0,5 %.
62

5. ПРОИЗВОДСТВО ТИТАНА
Титан − металл серебристого цвета с голубоватым отливом, имеет невысокую плотность 4,507 г/см3, плавится при температуре 1660 °С, кипит при 3260 °С. Титан имеет две аллотропические модификации: до 882 °С существует α-титан, имеющий гексагональную решетку с параметрами а0 = 0,295 нм и с0 = 0,468 нм, и при более высоких температурах − β-титан с кубической объемно центрированной решеткой с параметром а = 0,304 нм.
Механические свойства титана изменяются в зависимости от содержания в нем примесей. Чистый титан ковок, имеет невысокую твердость (НВ 70); технический титан хрупок и тверд (НВ
180…280).
Вредные примеси титана − азот и кислород − резко снижают его пластичность, а углерод при содержании более 0,15 % снижает ковкость, затрудняет обработку титана резанием и резко ухудшает свариваемость. Водород в большой степени повышает чувствительность титана к надрезу, поэтому такой эффект называют водородной хрупкостью.
На поверхности титана образуется стойкая оксидная пленка, вследствие чего титан обладает высокой сопротивляемостью коррозии в некоторых кислотах, морской и пресной воде. На воздухе титан устойчив, он мало изменяет свои механические свойства при нагреве до 400 °С. При более высоком нагреве он начинает поглощать кислород, ухудшаются его механические свойства, а выше 540 °С − становится хрупким. При нагреве выше 800 °С титан энергично поглощает кислород, азот и водород, что используется в металлургии при производстве легированной стали.
63
Титан образует ряд оксидов. Из них наиболее изучены ТiO2, Тi2O3. Двуокись титана ТiO2 − амфотерный порошок белого цвета, практически нерастворимый в воде и разбавленных кислотах. Двуокись титана является основным продуктом переработки титанового сырья.
За последние десятилетия после промышленного освоения ковкого титана его используют как прочный, относительно легкий коррозионно-стойкий и жаропрочный конструкционный материал в самолетостроении, ракетостроении, а также в судостроении, из-за его устойчивости к воздействию морской воды.
5.1. Титановые руды
По распространенности в земной коре титан занимает десятое место среди других элементов (0,61%). Известно примерно 60 минералов титана, из них наибольшее промышленное значение имеют ильменит, рутил, сфен.
Ильменит FeO TiO2 − блестящий минерал буро-черного цвета, измельчающийся при выветривании и поэтому часто встречающийся в россыпях. Важным источником ильменита служат титаномагнетитовые железные руды − смеси ильменита с магнетитом Fе3O4 и частично с гематитом Fе2O3. В этих рудах содержание двуокиси титана достигает иногда 20 %. Титаномагнетитовые руды можно подвергать гравитационному и магнитному обогащению, в результате чего удается получать концентрат, содержащий более 40 % ТiO2, около 50 % оксидов железа и примерно 8 % других оксидов.
Рутил ТiO2 прозрачен, обладает алмазно-металлическим блеском, бывает окрашен в различные цвета (красно-коричневый, желтый, синий, черный). Крупные месторождения рутила встречаются редко.
64
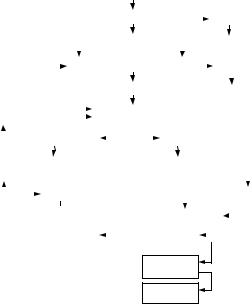
Сфен (титанит) СаО ТiO2 SiO2 − титаносиликат кальция, встречается вместе с другими полезными минералами − апатитом и нефелином и при условии комплексной переработки может быть перспективным сырьем, хотя он и беднее, чем ранее рассмотренные минералы.
Известно несколько различных способов получения титана из его руд, причем во всех случаях металлургической переработке всегда предшествует обогащение руды и получение концентрата.
5.2. Получение титана
Для ильменитовых концентратов, служащих основным материалом для получения титана и его соединений, наиболее часто применяют избирательное восстановление. Разберем одну из схем получения титана (рис. 17).
|
|
|
|
|
|
|
|
|
|
|
|
|
|
|
Ильменитовая руда |
|
|
|
|
|
|
|
|
|
|
|
|
|
|
|
|
|||||||||||||
|
|
|
|
|
|
|
|
|
|
|
|
|
|
|
|
|
|
|
|
|
|
|
|
|
|
|
|
|
|
|
|
|
|
|
|
|
|
|
|
|||||
|
|
|
|
|
|
|
|
|
|
|
|
|
|
|
|
|
|
Обогащение |
|
|
|
|
|
|
|
Хвосты |
||||||||||||||||||
|
|
|
|
|
|
|
|
|
|
|
|
|
|
|
|
|
|
|
|
|
|
|
|
|
|
|
|
|
|
|||||||||||||||
|
|
|
|
|
|
|
|
|
|
|
|
|
|
|
|
|
|
|
|
|
|
|
|
|
|
|
|
|
|
|
|
|
В отвал |
|||||||||||
|
|
|
|
|
|
|
|
|
|
|
|
|
|
|
|
|
|
Концентрат |
|
|
|
|
|
|
||||||||||||||||||||
|
|
|
|
|
|
|
|
|
|
|
|
|
|
|
|
|
|
|
|
|
|
|
|
|
|
|
||||||||||||||||||
|
|
|
|
|
|
|
|
|
|
|
|
|
|
|
|
|
|
|
|
|
|
|
|
|
|
|
|
|
|
|
|
|
|
|
|
|
|
|
|
|
|
|
|
|
|
|
|
Кокс |
|
|
|
|
Восстановительная плавка |
|
|
|
|
|
|
|
Чугун |
|
|
||||||||||||||||||||||||||
|
|
|
|
|
|
|
|
|
|
|
|
|
|
|
|
|||||||||||||||||||||||||||||
|
|
|
|
|
|
|
|
|
|
|
|
|
|
|
|
|
|
|
|
|
|
|
|
|
|
|
|
|
|
|
|
|
|
|
|
|
|
|
|
|
|
|
|
|
|
|
|
|
|
|
|
|
|
|
|
|
|
|
|
|
|
|
|
|
|
|
|
|
|
|
|
|
|
|
|
|
|
|
|
|
|
|
|
|
|
|
|
|
|
|
|
|
|
|
|
|
|
|
|
|
|
|
|
|
|
|
|
|
|
Шлак |
|
|
|
|
|
|
На производство |
|||||||||||||||||
|
|
|
|
|
|
|
|
|
|
|
|
|
|
|
|
|
|
|
|
|
|
|
|
|
|
|
|
|
|
|
|
|
|
|
|
|
|
|
стали |
|||||
|
Хлор |
|
|
|
|
|
|
|
|
|
|
|
Хлорирование |
|
|
|
|
|
|
|
|
|
|
|
|
|
|
|
|
|
|
|
||||||||||||
|
|
|
|
|
|
|
|
|
|
|
|
|
|
|
|
|
|
|
|
|
|
|
|
|
|
|
|
|
|
|
|
|
|
|
|
|
|
|||||||
|
|
|
|
|
|
|
|
|
|
|
|
|
|
|
|
|
|
|
|
|
|
|
|
|
|
|
|
|
|
|
|
|
|
|
|
|
|
|
|
|
|
|
|
|
|
|
|
|
|
Жидкие хлориды |
|
|
|
|
|
|
|
|
Газы |
|
|
|
|
|
|
|
|
|
|
|
|
|
|
|
|||||||||||||||
|
|
|
|
|
|
|
|
|
|
|
|
|
|
|
|
|
|
|
|
|
|
|
|
|
|
|
||||||||||||||||||
|
|
|
|
|
|
|
|
|
|
|
|
|
|
|
|
|
|
|
|
|
|
|
|
|
|
|
|
|
|
|
|
|
||||||||||||
|
Электролитическое |
|
|
|
|
|
|
|
|
|
|
Очистка и |
||||||||||||||||||||||||||||||||
|
получение магния |
|
|
|
|
|
|
|
|
ректификация |
|
|
||||||||||||||||||||||||||||||||
|
|
|
|
|
|
|
|
|
|
|
|
|||||||||||||||||||||||||||||||||
|
|
|
|
|
|
|
|
|
|
|
|
|
|
|
|
|
|
|
|
|
|
|
|
|
|
|
|
|
|
|
|
|
|
|
|
|
|
|
|
|
|
|
|
|
|
|
|
|
|
|
|
|
|
Магний |
|
|
|
|
|
|
|
Четырёххлористый титан |
|
||||||||||||||||||||||||||
|
|
|
|
|
|
|
|
|
|
|
|
|
|
|
|
|
||||||||||||||||||||||||||||
|
|
|
|
|
|
|
|
|
|
|
|
|
|
|
|
|
|
|
|
|
|
|
|
|
|
|
|
|
|
|
|
|
|
|
|
|
|
|
|
|
|
|
|
|
|
|
|
|
|
|
|
|
|
|
|
|
|
|
|
|
|
|
|
|
|
|
|
Восстановление |
|
|
|
|
|
|
|||||||||||||||
|
|
|
|
|
|
|
|
|
|
|
|
|
|
|
|
|
|
|
|
|
|
|
|
|
|
|
|
|
||||||||||||||||
|
|
|
|
|
|
|
|
|
Хлористый |
|
|
|
|
|
Титановая |
|
|
|
|
|
|
|
|
|
|
|
|
|
||||||||||||||||
|
|
|
|
|
|
|
|
|
|
магний |
|
|
|
|
|
|
|
|
|
|
|
|
|
|
|
|
|
|
||||||||||||||||
|
|
|
|
|
|
|
|
|
|
|
|
|
|
|
|
губка |
|
|
|
|
|
|
|
|
|
|
|
|
|
|||||||||||||||
|
|
|
|
|
|
|
|
|
|
|
|
|
|
|
|
|
|
|
|
|
|
|
|
|
|
|
|
|
|
|
|
|
|
|
|
|
||||||||
|
|
|
|
|
|
|
|
|
|
|
|
|
|
|
|
|
|
|
|
|
|
|
|
|
|
|
|
|
|
|
|
|
|
|
|
|
Переплавка |
губки |
Ковкий |
титан |
Рис. 17 . Схема получения титана из ильменитовой руды
65
Избирательную восстановительную плавку ведут в руднотермических электропечах различных конструкций, футерованных магнезитовым кирпичом. Концентрат шихтуют с углем (антрацитом) и перед загрузкой в печь брикетируют. В результате плавки восстанавливаются оксиды железа, образуя низкоуглеродистый чугун, содержащий менее 2,5 % углерода и небольшое количество кремния и марганца (0,4…0,9 %). Оксиды титана и кремнезем образуют шлак, содержащий 65…85 % ТiO2 и других низших оксидов титана, 10…15 % SiO2 + СаО MgO, остальное – А12О3, Fе2О3 и другие оксиды.
Этот шлак способен при охлаждении саморассыпаться. Порошкообразный шлак направляют на вторую основную операцию − хлорирование в обогреваемом переменным током хлораторе, в котором находятся расплавленные хлориды магния, калия и натрия. Хлор подается в печь через несколько фурм. В присутствии угля хлорирование двуокиси титана происходит при температуре выше 600 °С по следующей реакции:
ТO2 + 2С12 + С = ТiCl4 + СО2 + 205 000 Дж.
Наряду с хлористым титаном образуются и хлориды некоторых примесей: SiС14, FеС13, МgС12 и др.
Четыреххлористый титан плавится при температуре −23 °С и кипит при +136 °С, поэтому он выделяется из печи в виде паров, увлекая за собой летучие хлориды кремния и железа. Менее летучие хлориды магния, кальция и других металлов образуют жидкость.
Парогазовую смесь, выходящую из хлоратора, содержащую четыреххлористый титан и хлориды некоторых других соединений, направляют в сложную систему конденсационных установок, в которых она ступенчато охлаждается и, благодаря различной температуре конденсации хлоридов примесей титана (тетрахлорид TiCl4), очищается.
66
После конденсации ТiС14 газовая смесь нейтрализуется и выбрасывается, а жидкий конденсат хлористого титана отстаивается, очищается от твердой фазы и направляется на сложную и длительную очистку ректификацией. Четыреххлористый титан в виде прозрачной, бесцветной жидкости, дымящейся при соприкосновении с воздухом, прошедшей все стадии очистки, содержит несколько тысячных долей процента ванадия, кремния, железа и алюминия.
Важнейшую технологическую операцию − получение металлического титана − довольно часто осуществляют восстановлением четыреххлористого титана магнием. Кратко ознакомимся с этим методом.
Периодически титан получают в цилиндрических стальных герметичных ретортах диаметром 850…1500 мм и высотой 1800…3000 мм, производящих за одну операцию до 1500 кг титана. Реторты устанавливают вертикально, обычно в электропечь сопротивления. Сверху реторта закрыта крышкой, имеющей патрубки для загрузки магния, подачи ТiС14, откачки воздуха и подвода аргона (рис. 18).
После установки реторты в печь и откачки из нее воздуха реторту заполняют осушенным аргоном, нагревают до температуры 740…800 °С, заливают жидкий магний и начинают подачу жидкого тетрахлорида титана. Процесс получения титана можно упрощенно представить следующим уравнением реакции:
ТiС14(газ) + 2Мgж = 2МgС12(ж) + Тiтв + Q.
После интенсивного развития реакции выключают нагрев и поддерживают температуру в пределах 750…850 °С, регулируя скорость подачи тетрахлорида титана. Титан выделяется в реторте в виде хорошо развитых дендритов, которые получили название титановой губки. Жидкий хлористый магний периодически выпускают через патрубок в днище реторты, так как его объем в 10 раз превышает объем получаемой титановой губки. За один раз сливают 100…200 кг хлористого магния, который направляют в электролиз-
67
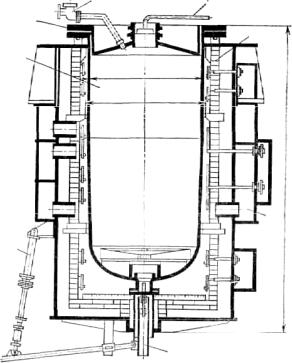
ный цех для получения металлического магния. После введения расчетного количества ТiС14 и затухания реакции включают обогрев и выдерживают реторту еще 1 ч при температуре 900 °С для завершения восстановления. Весь процесс восстановления в заводских условиях занимает 30…35 ч. Затем реторту извлекают из печи краном и охлаждают водой на отдельном стенде несколько часов до температуры 20…40 °С.
3 |
|
|
|
4 |
|||
|
2
5
1
251250
1350
3465
6
7
7
Рис. 18. Электропечь и реактор для восстановления тетрахлорида титана: 1 − реактор; 2 − крышка с теплоизоляцией; 3 − патрубок для заливки магния; 4 − труба для ввода четыреххлористого титана; 5 − электропечь сопротивления; 6 − коллекторы для подачи охлаждаемого воздуха; 7 − запорное устройство для слива хлористого магния
68
Для разделения продуктов реакции, состоящих из титановой губки (50…70 %), остатка хлористого магния (15…20 %), заполняющего поры губки, и избытка магния (30…35 %), пользуются различием давлений их паров при температуре 900 °С в вакууме. Крышку реторты снимают и укрепляют вместо нее охлаждаемый водой конденсатор, а реторту снова устанавливают в печь.
Дистилляцию магния и хлорида магния проводят при температуре 950…1000 °С и остаточном давлении 0,1 Па в течение нескольких десятков часов. Примеси Mg и MgCl2 из титановой губки расплавляются, частично испаряются и затем выделяются в конденсаторах. Получаемый оборотный магний и MgCl2 возвращаются в производство. Реторту вновь медленно охлаждают, открывают и пневматическими зубилами выбивают из нее титановую губку, так как она часто плотно приваривается к стенкам реторты.
Титановую губку дробят и тщательно сортируют. Наиболее чистую губку направляют на переплавку; низкосортную, содержащую включения хлоридов, брикетируют и используют как раскислитель стали в черной металлургии.
Для использования титана и его сплавов в качестве материала ответственных изделий очень важны его хорошая пластичность и свариваемость, а также термостойкость, поэтому в титановой губке не должно быть более 0,012 % С12, 0,1 % O2 и 0,04 % N2.
Для получения компактных слитков титана губку плавят в вакуумной дуговой печи во избежание загрязнения титана газами воздуха. Материал тигля также может загрязнить титан, поэтому плавку ведут в медном кристаллизаторе, стенки которого охлаждаются водой. Затвердевая около холодных стенок, титан не сплавляется с медью.
Слиток титана, помещенный на поддон кристаллизатора, служит одним полюсом дуги постоянного тока; расходуемый электрод из прессованной губки титана служит обычно другим полюсом, ко-
69
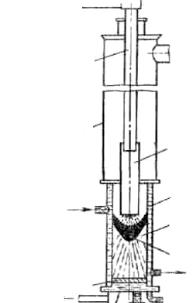
торый опускается в кристаллизатор сверху и плавится. Стабилизацию дуги в печи и перемешивание жидкого металла осуществляют с помощью соленоида, окружающего плавильное пространство кристаллизатора. Схема вакуумной дуговой печи (ВДП) для плавки с расходуемыми электродами показана на рис. 19. Она имеет устройство для вертикального перемещения электрода, а иногда – и для опускания дна поддона медного кристаллизатора. Перед началом плавки расходуемый электрод тщательно сушат и из плавильного пространства печи откачивают воздух до остаточного давления, равного 7 Па.
К генератору
7
6
1
Вода 2
3
4
5 Вода
Рис. 19. Схема вакуумно-дуговой печи с расходуемым электродом: 1 − расходуемый электрод; 2 − охлаждаемый водой кристаллизатор; 3 − слиток титана; 4 − расплавленный металл; 5 − медный охлаждаемый водой поддон; 6 − вакуумная камера; 7 − токопровод
70