
487
.pdfвнём углеродом кокса. После побеления шлака в него вводят еще более сильные восстановители − молотый ферросилиций или алюминий.
Отличительной особенностью плавки стали в электропечах является активное раскисление шлака, что приводит к диффузионному раскислению металла, непрерывно отдающему растворенный
внем кислород в восстановительный шлак. Такой метод раскисления предотвращает загрязнение металла неметаллическими включениями, выделяющимися при раскислении (А12О3 и др.).
Высокая температура, низкое содержание в шлаке закиси железа и высокое содержание извести в дуговой электропечи позволяют полнее вывести из металла серу в виде СаS. Продолжительность выплавки стали в дуговой печи составляет 3…6 ч и зависит от ее мощности и конструкции, выплавляемой марки стали, а также характера исходного сырья.
Описанная технология может быть изменена с учетом перерабатываемого сырья и тех марок стали, которые приходится выплавлять.
Расход электроэнергии на 1 т выплавляемой стали зависит от мощности и конструкции печи, продолжительности плавки и, следовательно, характера сырья и заданной марки стали. На 1 т выплавляемой углеродистой стали расходуется 500…700 кВт·ч, на 1 т
легированной стали − до 1000 кВт·ч.
Получение стали в дуговых электропечах имеет неоспоримые преимущества, важнейшие из которых − очень высокое качество получаемой стали, возможность выплавлять стали любых марок, включая высоколегированные, тугоплавкие и жаропрочные. Электропечи обеспечивают минимальный угар железа по сравнению с другими сталеплавильными агрегатами и, что особенно важно, минимальное окисление дорогостоящих легирующих присадок благодаря нейтральной атмосфере в печи. Следует отметить удобство
31
регулирования температурного режима и легкость обслуживания этих печей.
Недостатком выплавки стали в дуговых электропечах является потребность в большом количестве электроэнергии и высокая стоимость передела.
В черной металлургии плавку стали в индукционных печах применяют значительно реже, чем в дуговых. Обычно используют печи без железного сердечника, состоящие из индуктора в виде катушки (из медной трубки, охлаждаемой водой), которая служит первичной обмоткой, окружающей огнеупорный тигель, куда загружают плавящийся металл. Магнитные силовые линии, создаваемые катушкой, проходя через металл, находящийся в тигле, вызывают в нем вихревые токи, которые нагревают и плавят его. Так как в индукционных печах теплота возникает в металле, шлак в них нагревается только через металл. Вместимость современных индукционных печей достигает в отдельных случаях 15 т.
Крупные печи могут работать на переменном токе с промышленной частотой 50 Гц; для более мелких необходимы генераторы, работающие на частоте 500…2500 Гц. Выплавка стали из чугуна в индукционных печах распространения не получила, так как окисление и рафинирование с помощью шлака в них почти невозможны. Эти печи с успехом используют для переплавки чистых легированных сталей, так как высокая температура, возможность работы в вакууме и отсутствие науглероживания металла электродами дают возможность получить в них стали с малым содержанием углерода и различные сложные сплавы, к которым предъявляются повышенные требования.
32
2.4. Разливка стали и получение слитков
На металлургических заводах жидкую сталь после выпуска из печи разливают в слитки различной формы и массы, которые затем служат заготовками в прокатных и кузнечных цехах.
Жидкую сталь из печей выпускают в большие разливочные ковши, в дне которых имеется отверстие, закрывающееся сверху стопором через систему рычагов, выведенных за стенку ковша. Ковши имеют прочный кожух с цапфами для захвата его краном. Внутри ковш и стопор футеруют шамотным огнеупором. Металл, выпущенный в ковш, выдерживают 5…10 мин для выравнивания его состава и всплывания неметаллических примесей и газов, попавших в сталь при выпуске из печи. Затем ковш направляют либо на разливку в изложницы, либо на установку для непрерывной разливки.
Заполнение изложниц сталью возможно сверху непосредственно из донного отверстия ковша или сифонным способом (рис. 6), через вертикальный литник, из которого жидкая сталь через горизонтальные литниковые ходы поступает снизу в несколько изложниц. Слитки для сортового проката имеют квадратное или круглое сечение. Слитки для проката на лист − плоские. Наиболее часто слитки отливают массой 1…20 т, а иногда − 100 т и более. Для изготовления крупных слитков сталь обычно заливают сверху, мелких − сифонным способом.
Затвердевание стали в металлической изложнице начинается от холодных стенок и дна, а затем распространяется внутрь слитка. При затвердевании объем жидкой стали уменьшается на несколько процентов. Все это приводит к образованию в слитке усадочной раковины в ее головной части, а иногда и мелких раковин ниже головной части слитка.
33
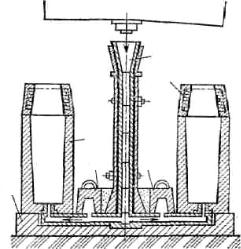
5
4
6
1
3 3
2
Рис. 6. Схема сифонной разливки стали в изложницы: 1 − изложницы; 2 − поддон; 3 − шлакоуловители; 4 − воронки и центровая трубка; 5 − разливочный ковш; 6 − утепленная насадка изложницы
Для уменьшения размера усадочной раковины принимают различные меры: слиток расширяют вверху и сужают к нижней части; верхнюю съемную часть изложницы футеруют огнеупором (так называемыми утепленными насадками); у крупных слитков после начала затвердевания верхнюю часть нагревают сварочной дугой или термитной смесью.
Если слиток спокойной стали разрезать вдоль и отшлифовать, то можно увидеть несколько различных структурных зон (рис. 7). У поверхности боковых стенок и дна слитка есть небольшой слой мелких однородных плотных кристаллов; затем следует второй, более толстый слой столбчатых дендритных кристаллов, образующих различные дефекты и пустоты в местах стыка отдельных дендритов, особенно при стыке дендритов боковых стенок и дна; в середине находится третья зона равноосных кристаллов разного размера неплотной структуры с большим количеством неметаллических
34
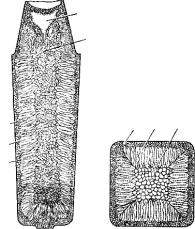
включений, вызванных тем, что эта область слитка застывает последней и часть неметаллических примесей оттесняется сюда затвердевающими у стенок дендритами.
4
5
3 3 2 1
2
1
Рис. 7. Строение слитка спокойной стали (продольное и поперечное сечения): 1 − зона крупных равноосных кристаллов; 2 − зона столбчатых кристаллов; 3 − корковая зона мелких кристаллов; 4 − усадочная раковина;
5 − усадочная рыхлость
В середине верхней трети или четверти слитка спокойной стали располагается компактная усадочная раковина, вблизи которой часто можно увидеть мелкие раковины и рыхлоту. Эту часть слитка перед прокаткой отрезают.
Структура слитка в различных его частях, так же как химический состав стали, отличается от средних данных, полученных после взятия пробы из жидкой стали перед разливкой, в связи с ликвацией, происходящей при остывании слитка в изложнице. Кроме того, химический состав стали и других сплавов в различных местах одного и того же дендрита получается неоднородным. Оси дендрита, образовавшиеся позднее, богаче легкоплавким элементом и
35
плавятся быстрее (а застывают позже), чем ранее сформировавшиеся оси. Поэтому слиток в зоне дендритов имеет внутрикристаллическую или дендритную ликвацию.
Еще более резко в слитке спокойной стали выражена так называемая зональная ликвация. Пробы металла, взятые у стенок слитка, в его средней (третьей) зоне, по содержанию углерода, а особенно − серы и фосфора, могут различаться в 2…3 раза.
Впоследние десятилетия создано много установок для непрерывной разливки стали (рис. 8, а). Сталь из разливочного ковша через промежуточный ковш непрерывной и равномерной струей заливается в кристаллизатор, представляющий собой слегка качающийся вверх и вниз двустенный короб из красной меди, стенки которого интенсивно охлаждаются проточной водой. Благодаря этому сталь быстро формирует прочные и плотные стенки слитка. Из кристаллизатора слиток непрерывно вытягивается валками со скоростью, соответствующей скорости его кристаллизации. Ниже кристаллизатора до выхода из валков слиток подвергается вторичному охлаждению водяными душами, при этом заканчивается его затвердевание. После выхода из валков от непрерывно опускающегося слитка кислородно-газовой горелкой отрезают куски необходимой длины.
Впоследние годы появились не только вертикальные установки для разливки стали, но и установки с изгибом слитка. Наиболее популярна установка радиальной непрерывной разливки (рис. 8, б), которая может быть размещена в габаритах существующих сталелитейных цехов.
Слитки непрерывной разливки по сравнению со слитками, полученными в изложницах, имеют более чистую поверхность, не имеют усадочных раковин. Из-за большой скорости охлаждения они характеризуются мелкой структурой и менее развитой химической неоднородностью, минимальной по продольной оси слитка.
36
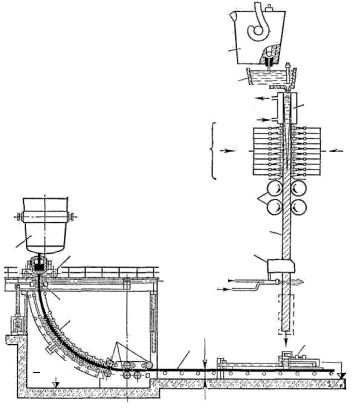
Однако и эти слитки имеют свои дефекты: наиболее часты продольные и поперечные наружные трещины, появляющиеся при нарушении скорости вытягивания слитка, которая может изменяться от 0,4 до 10 м/мин.
|
|
|
|
|
|
|
1 |
|
|
|
|
|
|
|
|
|
|
|
|
|
|
|
|
|
|
|
|
||||||
|
|
|
|
|
|
|
|
2 |
Вода |
|||||||
|
|
|
|
|
|
|
|
|
||||||||
|
|
|
|
|
|
|
|
|
|
|
|
|
|
|
||
|
|
|
|
|
4 |
|
||||||||||
|
|
|
|
|
Вода |
|
||||||||||
|
|
|
|
5 |
|
|||||||||||
|
|
|
|
|
|
|
|
|
|
|
|
|
|
|
|
|
|
|
|
|
|
6 |
|
|
|
|
|||||||
|
|
|
|
|
|
|
|
|
|
|
|
|
|
|
|
|
|
|
|
|
|
7 |
|||||||||||
|
|
|
|
|
|
|
|
|
|
|
|
|
|
|
|
|
1 |
2 |
|
|
8 |
Ацетилен
Кислород
3
5
6
7850
4750
б
3
Вода
а
8
50
Рис. 8. Установка для непрерывной разливки стали: а − вертикальная разливка; б − радиальная разливка; 1 − ковш; 2 − разливочное устройство;
3 − водоохлаждаемый кристаллизатор; 4 − вода для охлаждения; 5 − зона вторичного охлаждения; 6 − тянущие валки;
7 − слиток; 8 − газорез
37
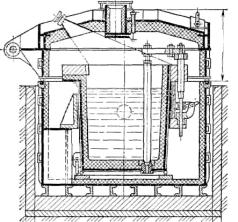
Непрерывная разливка на разливочной машине обеспечивает повышение качества слитков и резко уменьшает потери металла в отходы, а также значительно облегчает условия работы и резко повышает производительность труда как при разливке стали, так и при дальнейшей обработке слитков. Одноручьевая установка непрерывной разливки позволяет получать 20…150 т/ч слитков (в зависимости от их сечения и формы).
Существенное повышение качества стали достигается ее вакуумированием перед разливкой и вакуумной разливкой в слитки. Вакуумирование стали перед разливкой проводят в ковше, помещая его в камеру (рис. 9). Обработка стали в ковше длится 10…12 мин при остаточном давлении 300 Па.
1650
Рис. 9. Простейшая камера для вакуумной обработки жидкой стали
Выделение газов при вакуумировании вызывает бурное кипение и перемешивание металла. Этот способ применим для небольших масс металла (до 50 т). Лучшие результаты можно получить, применяя одновременное электромагнитное перемешивание. Более
38
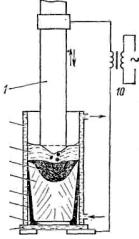
эффективно получение слитков в вакууме. Этот способ применяют главным образом для высококачественных и некоторых высоколегированных марок стали. Из стали при разливке в вакууме удаляется около 60 % растворенного водорода и другие газы, уменьшается количество неметаллических включений, повышаются механические свойства и пластичность. Стоимость слитков, отлитых этим способом, значительно повышается.
Для значительного улучшения качества металла стальных слитков применяют так называемый электрошлаковый переплав
(рис. 10).
1 |
|
|
10 |
||
|
|
|
2
3
4
5
6
7
8
9
Рис. 10. Установка для электрошлакового переплава:
1 − расходуемый электрод;
2 − водоохлаждаемый кристаллизатор; 3 − шлаковая ванна; 4 − металлическая ванна; 5 − слиток; 6 − шлаковый гарнисаж; 7 − воздушный зазор; 8 − затравка; 9 − поддон;
10 − трансформатор
В конусном водоохлаждаемом кристаллизаторе расплавляют слой шлака, содержащего значительное количество плавикового шпата (СаF2). Ко дну изложницы подводят один из полюсов источника переменного тока большой силы; стальной стержень или слиток, отлитый любым путем, опускают в шлак и подводят к нему другой полюс; при достаточно большой силе тока стальной стержень разогревается и начинает плавиться его часть, опущенная в шлак. Капли металла, проходя через шлак, очищаются от не- металли-ческих включений и растворенных газов. Попадая на холодные стенки изложницы, капли начинают кристаллизоваться, образуя новый слиток. По мере его образования первичный слиток − электрод
39
− медленно опускают, так как диаметр вторичного слитка всегда больше первичного. Новый слиток благодаря кристаллизации под флюсом и перемещению зоны кристаллизации имеет хорошую структуру и меньше неметаллических включений.
Применяют также обработку жидкой стали синтетическими шлаками с целью ее раскисления, дополнительной очистки от серы и неметаллических включений. В отдельной печи с угольной футеровкой расплавляют шлак, состоящий из 55 % СаО и до 45 % А12О3
снебольшим количеством кремнезема и возможным минимумом FеО (не более 1 %). Этот шлак заливают в разливочный ковш при температуре 1700 °С в количестве 3…5 % массы выпускаемой стали. Затем в этот шлак выпускается из печи сталь. Струя стали, падая
свысоты, равной 3 м, интенсивно смешивается со шлаком, что за короткий срок обеспечивает большую эффективность её рафинирования. Количество серы в металле снижается на 50…70 %. Металл раскисляется, неметаллические включения из металла в значительной степени переходят в шлак. Синтетическими шлаками обрабатывают сталь, полученную в конвертерах, мартеновских печах и крупных электропечах.
40