
487
.pdfменяется в ограниченных масштабах. Алюминий, полученный после электролитического рафинирования, обычно соответствует маркам высокой чистоты.
Рафинирование алюминия возможно и другими способами. Для получения алюминия особой чистоты широкое примене-
ние получил метод зонной перекристаллизации, в основе которой лежит неодинаковое распределение примесей алюминия (или другого рафинируемого металла) между жидкой и твердой фазой при частичном расплавлении.
51

4. ПРОИЗВОДСТВО МЕДИ
Медь используется человеком с бронзового века. Наиболее важное свойство меди, обеспечившее ей широкое применение, − хорошая электропроводимость и теплопроводность, высокая пластичность и способность образовывать технологичные сплавы, которые отлично обрабатываются и обладают хорошими механическими свойствами.
Температура плавления меди составляет 1083 °С, кипения − 2360 °С. Предел прочности чистой меди не очень высок − 220 МПа. Ее кристаллическая решетка − кубическая гранецентрированная с параметром а = 0,361 нм. Плотность меди равна 8,93 г/см3, твердость почти в 2 раза меньше, чем у железа.
4.1. Медные руды
Главным источником меди (примерно 80 % мировой добычи) служат сульфидные руды, содержащие чаще всего СuS2, называемый медным колчеданом, или другие сернистые минералы меди, например СuS. В этих рудах обычно находятся много пирита FеS2 и сульфиды цинка, свинца, никеля и нередко − серебро и золото.
Другим источником меди являются окисленные медные руды, содержащие медь в виде куприта Сu2О или азурита 2СuСO3 Сu(ОН)2. Широко известен теперь уже очень редкий, окисленный минерал меди − малахит СuСО3 Сu(ОН)2. Встречаются также смешанные сульфидноокисленные медные руды. Содержание меди в комплексных рудах незначительно (часто 1…2 %). Перед плавкой их почти всегда подвергают обогащению, которое позволяет флотацией выделить из руды отдельно медный концентрат, содержащий 11…35 % Сu, и цинковый или пиритный концентрат.
52

Для получения меди из руд можно использовать пирометаллургические способы: плавка на штейн, восстановительная плавка (рис. 14); но некоторые руды успешно перерабатывают и гидрометаллургическими способами, например выщелачиванием серной кислотой.
|
|
|
|
|
|
|
|
|
|
|
|
|
Руда |
|
|
|
|
|
|
|
|
|
|
|
|
|
|||
|
|
|
|
|
|
|
|
|
|
|
|
|
|
|
|
|
|
|
|
|
|
|
|
|
Zn |
||||
|
|
|
|
|
|
|
|
|
|
|
|
|
|
|
|
|
|
|
|
|
|
|
|
|
|||||
|
|
|
|
|
|
|
|
|
|
|
|
|
|
|
|
|
|
|
|
|
|||||||||
|
|
Хвосты |
|
|
|
|
|
Обогащение |
|
|
|
|
|
концентрат |
|||||||||||||||
|
|
|
|
|
|
|
|
|
|
|
|||||||||||||||||||
|
|
|
|
|
|
|
|
|
|
|
|
|
|
|
|
|
|
|
|
|
|
|
|
|
|
|
|
|
|
|
|
|
|
|
|
|
|
|
|
|
|
|
|
|
|
|
|
|
|
|
|
|
|
|
|
|
|
|
|
|
|
|
|
|
|
|
|
|
|
|
|
|
|
|
|
|
|
|
|
|
|
|
|
|
|
|
|
|
|
|
|
Газы |
|
|
|
|
Плавка на штейн |
|
|
|
|
|
|
Шлак |
|
|
|||||||||||||
|
|
|
|
|
|
|
|
|
|
|
|
|
|
|
|||||||||||||||
|
|
|
|
|
|
|
|
|
|
|
|
|
|
|
|
|
|
|
|
|
|
|
|
|
|
|
|
|
|
|
|
|
|
|
|
|
|
|
|
|
|
|
|
|
|
|
|
|
|
|
|
|
|
|
|
|
|
|
|
|
|
|
|
|
|
|
|
|
|
|
|
|
|
|
|
|
|
|
|
|
|
|
|
|
|
|
|
|
|
|
|
|
|
|
|
|
|
|
|
|
|
|
Штей |
|
|
|
|
|
|
|
|
|
|
|
|
|
|
||
|
|
|
|
|
|
|
|
|
|
|
|
|
|
|
|
|
|
|
|
|
|
|
|
|
|
|
|||
|
|
|
|
|
|
|
|
|
|
|
|
|
|
|
|
|
|
|
|
|
|
|
|
|
|
|
|
|
|
|
|
|
|
|
|
|
|
|
|
|
|
|
|
|
|
|
|
|
|
|
|
|
|
|
|
|
|
|
|
|
|
|
|
|
|
|
|
|
|
|
|
|
|
|
|
|
|
|
|
|
|
|
|
|
|
|
|
|
|
|
|
Газы |
|
|
|
|
|
|
Конвертиров |
|
|
|
|
|
Шлак |
|
|
||||||||||||
|
|
|
|
|
|
|
|
|
|
|
|
|
|
|
|
||||||||||||||
|
|
|
|
|
|
|
|
|
|
|
|
|
|
|
|
|
|
|
|
|
|
|
|
|
|
|
|
|
|
|
|
|
|
|
|
|
|
|
|
|
|
|
|
|
|
|
|
|
|
|
|
|
|
|
|
|
|
|
|
|
|
|
|
|
|
|
|
|
|
|
|
|
|
|
|
|
|
|
|
|
|
|
|
|
|
|
|
|
|
На производство |
|
|
|
|
Черновая медь |
|
|
|
|
|
|
|
|
|
|
||||||||||||||
|
|
|
|
|
|
|
|
|
|
|
|
|
|
|
|
|
|
|
|
|
|||||||||
|
|
|
|
|
|
|
|
|
|
|
|
|
|
|
|
|
|
|
|
|
|||||||||
серной кислоты |
|
|
|
|
|
|
|
|
|
|
|
|
|
|
|
|
|
|
|
|
|
||||||||
|
|
|
|
Огневое |
|
|
|
|
|
|
|
|
|
|
|||||||||||||||
|
|
|
|
|
|
|
|
|
|
|
|
|
|
|
|
|
|
|
|
|
|
|
|||||||
|
|
|
|
|
|
|
|
|
|
|
|
|
рафинирование |
|
|
|
|
|
|
|
|
|
|
||||||
|
|
|
|
|
|
|
|
|
|
|
|
|
|
|
|
|
|
|
|
|
|
|
|||||||
|
|
|
|
|
|
|
|
|
|
|
|
|
|
|
|
|
|
|
|
|
|
|
|
|
|
|
|
|
|
|
|
|
|
|
|
|
|
|
|
|
|
|
|
|
|
|
|
|
|
|
|
|
|
|
|
|
|
|
|
|
|
|
|
|
|
|
|
|
|
|
|
|
|
|
|
|
|
|
|
|
|
|
|
|
|
|
|
|
|
|
|
Шлам |
|
|
|
|
Электролитическое |
|
|
|
|
|
Скрап |
|
|||||||||||||||
|
|
|
|
|
|
|
рафинирование |
|
|
|
|
|
|
||||||||||||||||
|
|
|
|
|
|
|
|
|
|
|
|
|
|
|
|||||||||||||||
|
|
|
|
|
|
|
|
|
|
|
|
|
|
|
|
|
|
|
|
|
|
|
|||||||
|
На извлечение |
|
|
|
|
|
|
|
|
|
|
|
|
|
|
|
|
|
|
|
|
|
|||||||
|
|
|
|
|
|
|
|
|
|
|
|
|
|
|
|
|
|
|
|
|
|
||||||||
|
|
|
|
Катодная |
|
|
|
|
|
|
|
|
|
|
|||||||||||||||
|
|
Au и Aq |
|
|
|
|
|
|
|
|
|
|
|
|
|
|
|||||||||||||
|
|
|
|
|
|
|
|
|
|
|
|
|
|
|
|
|
|
|
|
|
|
|
Рис. 14. Упрощенная схема получения меди из сульфидных руд пирометаллургическим способом
4.2. Получение медных штейнов
Штейн в застывшем виде − это сплав сульфидов главным образом меди и железа (обычно 80…90 %) и сульфидов цинка, свинца, никеля. Жидкие штейны хорошо растворяют в себе золото и серебро, и, если эти ценные металлы есть в руде, они почти полностью концентрируются в штейне. Цель плавки на штейн − отделение сернистых соединений меди и железа от содержащихся в руде примесей, присутствующих в ней в виде окисленных соединений.
53

Штейн получают либо в шахтных печах, если сырьем служит кусковая медная руда, содержащая много серы, либо в отражательных печах, если исходным продуктом служат порошкообразные флотационные концентраты.
Отражательные печи для получения медного штейна (рис. 15) обычно бывают длиной 35…40, шириной 7…10 и высотой 3,5…4,5 м. Стены и свод делают из динасового или магнезитового кирпича. Огнеупор выбирают в зависимости от преобладания в шихте основных или кислотных оксидов, так как соответствие состава шихты и огнеупорных материалов удлиняет срок службы последних.
Отражательные печи отапливают мазутом, угольной пылью или газом, вдувая топливо форсунками (4…10 шт.) через окна, имеющиеся в торце печи. Максимальная температура в головной части печи 1550 °С, в хвостовой части обычно 1250…1300 °С. Шихту в эти печи загружают через отверстия в своде, расположенные вдоль печи у боковых стенок. При загрузке шихта ложится откосами вдоль стен, предохраняя кладку от прямого воздействия шлаков и газов. По мере нагрева шихты начинаются реакции частичного восстановления высших оксидов железа и меди, окисления серы и шлакообразования, например:
FеS + 3Fе3О4 + SiO2 = 5 (2FеО SiO2) + SO2;
2Сu2S + 3O2 = 2СuO2 + 2SO2.
Сульфиды меди и железа, сплавляясь, дают первичный штейн, который, стекая по откосам, изменяет свой состав, обедняясь железом и обогащаясь медью:
В печи идут и многие другие химические реакции. 2FеS + 2Сu2O + SiO2 = 2FеО SiO2 + 2Сu2S.
в шлак |
в штейн |
54
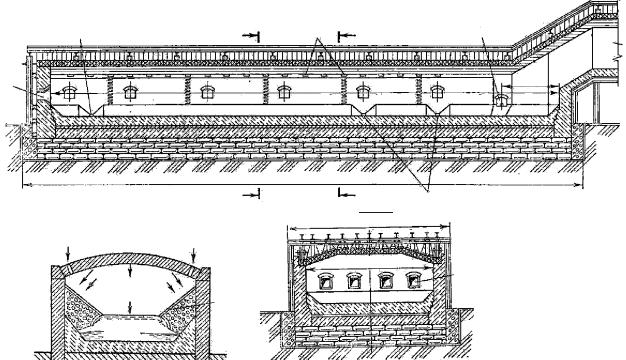
4
5
Cхематический разрез по I−I работающей печи
Загрузка Загрузка
Горение |
|
|
|||
|
|
|
|
|
|
топлива |
Плавление |
||||
|
|
|
|
|
|
|
Шлак |
|
|
|
|
Штейн |
|
|
|
||
|
|
|
|
|
|
I |
|
II |
|
|
1 |
2 |
|||
|
|
|
|
|
|
3 |
|
|
|
|
|
31 700 |
|
4500 |
|
|
|
|
|
|
|
39 500 |
|
I |
II II −I |
4 |
10 000 |
|
8000 |
5 |
|
Рис. 15. Отражательная печь для плавки медных концентратов: 1 – загрузочные отверстия; 2 – окно для слива шлака; 3 – дымоход; 4 – шпуровые отверстия для выпуска штейна; 5 – отверстия для топливных форсунок
55
Штейн, имеющий плотность около 5 г/см3, собирается на поду печи, а шлак образует второй верхний жидкий слой плотностью примерно 3,5 г/см3; шлак выпускают по мере накопления через шлаковое окно, расположенное в хвостовой части печи. Отверстия для выпуска штейна (обычно два) находятся в одной из боковых стенок печи. Выпуск штейна производят по мере его образования и потребности в нем последующего конвертерного передела.
Штейны содержат 23…28 % S, 16…60 % Сu и 50…15 % Fе.
Главными составляющими шлаков являются кремнезем (45…30 %) и закись железа (25…45 %).
Процессы образования штейна и шлака в шахтной печи из-за применения кусковых материалов протекают сложнее, чем в отражательной печи, но результат их может быть выражен уравнениями химических реакций, приведенными выше. При некоторой герметизации шахтной печи, создании восстановительной атмосферы в ней и увеличении расхода кокса можно наряду со штейном получить и пары серы с последующей конденсацией их из отходящих газов.
4.3. Переработка медного штейна в черновую медь
Для получения меди из штейнов применяют конвертерный способ, аналогичный известному в сталеплавильном производстве (рис. 16). Наружный диаметр конвертера обычно равен 2,3…4 м, длина − 4,3…10 м. Наиболее крупные конвертеры выдают за один цикл процесса до 100 т меди. Воздух в конвертер подается через ряд фурм, расположенных по образующей цилиндра. Цилиндр опирается двумя прочными бандажами на четыре пары роликов, что позволяет поворачивать его на необходимый угол для заливки штейна в горловину и выпуска продуктов плавки. Внутри конвертер футерован магнезитовым и хромомагнезитовым кирпичом.
56

330 5082896
330
А-А |
|
|
1791 |
Направление |
|
|
А поворота |
||
1882 |
|
|
3 |
конвертера |
|
|
|
|
|
5080 |
508 |
|
2 |
330 |
|
|
|||
|
|
|
1348 |
1448 |
|
|
|
3658 |
4 |
|
|
|
1 |
|
|
|
1 |
||
|
|
|
||
|
|
|
|
|
6096 |
|
|
|
5 |
|
|
|
|
Рис. 16. Конвертер для получения черновой меди: 1 − фурма; 2 − кольцевой воздухопровод; 3 − горловина для заливки штейна и отвода газов; 4 −опорный обод; 5 −опорные ролики
Переработка штейна протекает в два периода. В конвертер загружают кусковой кварц, заливают расплавленный штейн и продувают его воздухом. Воздух, энергично перемешивая штейн, окисляет сульфиды меди и железа:
2FеS + 3О2 = 2FеО + 2SO2 + 940 000 Дж,
2Сu2S + 3O2 = 2Сu2O + 2SO2+ 775 000 Дж.
При этом закись меди благодаря обменному взаимодействию вновь превращается в сульфид:
Сu2O + FeS = Сu2S + FеО.
По этой причине в первом периоде идет окисление практически только железа, а закись железа шлакуется кварцем:
57
2FеО + SiO2 = 2FеО SiO2.
Образующийся шлак периодически сливают и в конвертер добавляют свежие порции медного штейна и кускового кварца. Температура заливаемого штейна обычно 1200 °С, но за время продувки за счет большого выделения теплоты при окислении сульфидов температура повышается до 1350 °С. Продолжительность первого периода зависит от количества меди в штейне и составляет 6…20 ч.
Первый период закончится, когда в продуваемом штейне окислится сернистое железо. После этого тщательно удаляют шлак и продолжают продувку без добавки штейна и кварца. Воздух окисляет теперь только Сu2S, образовавшаяся закись меди способствует появлению в конвертере металлической меди по реакции
Сu2S + 2Сu2 O = 6Сu + 5O2.
Второй период заканчивается, когда в конвертере весь штейн превращается в медь, на что обычно уходит 2…3 ч. В конвертере и во втором периоде образуется небольшое количество богатого медью шлака, который остается в нем после выливания черновой меди и перерабатывается в следующем цикле. Конвертерные шлаки первого периода направляют для переработки в отражательные печи. Конвертерные газы содержат 12…17 % SO2. После очистки от пыли их используют для получения серной кислоты.
Черновую медь по окончании процесса, наклоняя конвертер, выпускают в ковш и разливают в изложницы. Полученную в конвертере медь называют черновой, так как в ней содержится 1…2 % железа, цинка, никеля, мышьяка, сурьмы, кислорода, серы и других примесей; в ней также растворены благородные металлы, ранее находившиеся в штейне.
58
4.4. Рафинирование меди
Черновая медь всегда подвергается рафинированию для удаления из нее примесей, ухудшающих ее свойства, а также для извлечения из нее золота и серебра. Рафинирование проводят последовательно двумя принципиально различными методами: пирометаллургическим и электролитическим.
Огневое (пирометаллургическое) рафинирование меди проводят в отражательных печах. В отличие от отражательных печей для получения штейна эти печи обладают меньшими размерами (ширина 5 м, длина 12…15 м, глубина ванны 0,9 м). Такие печи вмещают до 400 т меди.
Весь цикл огневого рафинирования состоит из операций: загрузки и расплавления, окисления примесей, удаления газов, раскисления меди и разливки; он занимает обычно 12…16 ч. Если рафинирование проводят на заводе, выплавляющем черновую медь, и ее заливают в печь в жидком виде, продолжительность рафинирования значительно сокращается. Примеси в черновой меди окисляют воздухом, который вдувают через стальную трубку диаметром 20…40 мм, футерованную огнеупорами и погружаемую в расплавленную медь. В ванне наиболее быстро окисляется медь по реакции
4 [Сu] + O2 = 2(Cu2O).
Закись меди благодаря перемешиванию вдуваемым воздухом быстро распространяется по всему объему ванны; окисление примесей идет по общей схеме:
[Мепр] + (Сu2O) = (МепрО) + 2 [Сu]ж,
где [Мепр] − все примеси.
Оксиды примесей всплывают на поверхность и образуют шлак. Отдельные летучие оксиды могут переходить частично и в парообразное состояние. Таким путем удается удалить основную часть
59
примесей: А1, Рb, Мn, Zn, Sn, Fе, Ni, S и частично Sb, Аs, Bi; не окисляются и остаются в меди золото, серебро, а также селен и теллур.
Удаление растворенных газов из меди принято называть «дразнением на плотность». В металл ванны погружают сырые деревянные жерди, древесина которых выделяет газообразные углеводороды, бурно перемешивающие медь и удаляющие из металла сернистый и другие газы. Для сохранения природных ресурсов и экономии древесины некоторые заводы заменяют сырую древесину природным газом, паромазутной смесью или другими газообразными восстановителями, являющимися отходами соседних производств. После удаления газов для получения пластичной меди начинают раскисление, так как содержание растворенного в меди кислорода после окисления иногда достигает нескольких процентов. Раскислителями служат газы, которые вводят под зеркало металла так же, как и вдувают воздух, − через металлическую трубку.
Процесс может идти, например, по уравнениям:
[О]Cu + СО = СО2,
(Сu2O) + Н2= Н2Опар + 2 [Сu].
Для обеспечения более полного раскисления поверхность меди засыпают древесным углем, но предварительно тщательно удаляют шлаки во избежание обратного восстановления из них примесей. Медь после огневого рафинирования подают на разливочные машины для отливки анодов − квадратных плит размером 1×1 м и толщиной 40…50 мм (массой 250…320 кг), имеющих ушки для подвешивания в электролизере. Литые аноды направляют на электролитическое рафинирование.
Электролитическое рафинирование меди проводят в ваннах, наполненных раствором сернокислой меди, подкисленным серной
60