
487
.pdfВ уравнениях реакций химические элементы, находящиеся в металле, заключены в квадратные скобки, а находящиеся в шлаке − в круглые.
После 15…16-минутной продувки поднимают фурму, наклоняют конвертер, берут пробу металла на анализ и скачивают большую часть шлака. Это занимает 7…8 мин. Экспресс-анализом определяют основные параметры стали, затем конвертер вновь ставят в вертикальное положение, опускают фурму и вторично продувают кислородом несколько минут, в зависимости от данных анализа и заданной марки стали.
Затем фурму вновь поднимают, конвертер наклоняют, берут контрольную пробу металла, термопарой погружения измеряют его температуру, после чего сталь выпускают через боковую летку в разливочный ковш; после слива металла скачивают оставшийся шлак и заделывают выпускное отверстие. Весь технологический цикл плавки занимает 50…60 мин, а продолжительность продувки кислородом составляет 18…30 мин.
Поворот конвертера, подъем и опускание водоохлаждаемой кислородной фурмы, загрузка сыпучих добавок и некоторые другие технологические операции осуществляются с пульта управления конвертером. Продолжительность и режим дутья, время отбора пробы и другие параметры плавки определяют счетновычислительными устройствами разных типов.
Металл из конвертера выпускают не через горловину, а через верхнюю летку, что предохраняет металл от поглощения азота, так как вся поверхность стали в конвертере в это время закрыта слоем шлака. Получение стали завершается ее раскислением ферромарганцем и ферросилицием. Часть раскислителей вводят в конвертер непосредственно перед разливкой или в разливочный ковш во время выливки металла.
21
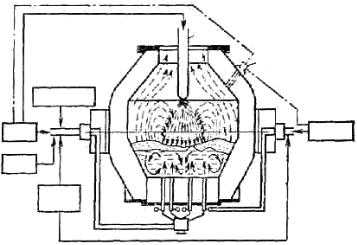
Общий расход технического кислорода на получение 1 т стали в конвертере составляет 50…60 м3, что незначительно превышает теоретически необходимое количество.
Недостатком кислородно-конвертерного способа получения стали является большое пылеобразование, обусловленное обильным окислением и испарением железа. Угар металла составляет 6…9 %, что значительно больше, чем при других способах получения стали. Это требует обязательного сооружения при конвертерах сложных и дорогих пылеочистительных установок.
Совершенствование конвертерных процессов привело к распространению нескольких их разновидностей, например комбинированного дутья, при котором кроме подачи кислорода через фурму сверху предусмотрено вдувание кислорода или воздуха через донные фурмы.
7
6
1
2 |
5 |
3
4
Рис. 3. Кислородный конвертер с комбинированной верхней и донной продувкой: 1 − шлакообразующие (известковый порошок); 2 − кислород; 3 − воздух; 4 − аргон; 5 − углеводородный газ; 6 − боковая фурма; 7 − верхняя фурма
22
Комбинированная продувка (рис. 3) с подачей снизу даже небольшого количества аргона или азота в течение нескольких минут обеспечивает следующие преимущества: снижается окисленность шлака и металла − повышается выход годного металла; уменьшается окисление марганца − повышается удаление фосфора и серы из металла, что позволяет сократить расход шлакообразующей извести.
2.2. Мартеновский способ
Современные мартеновские печи (рис. 4) отапливают обычно смесью доменного газа с коксовальным или природным газом и оборудуют четырьмя регенераторами (по два с каждой стороны печи), заполненными кирпичной решетчатой кладкой для раздельного подогрева газообразного топлива и воздуха, подаваемых в печь. Продукты горения из рабочего пространства печи направляются в одну пару регенераторов (например, правую), нагревая их внутреннюю кладку, и затем выпускаются в дымовую трубу. В это время газ и воздух подают в печь через вторую пару регенераторов (например, левую), которые были нагреты раньше. Через некоторое время с помощью автоматически переключающихся клапанов меняется направление выхода печных газов и подачи топлива. На некоторых заводах работают печи, отапливаемые мазутом или природным газом, в которых подогревается только воздух, подающийся в печь.
Ванна печи, удерживающая расплавленные материалы, имеет сферическую форму. Условную длину и ширину печи обычно определяют на уровне порогов садочных окон, через которые и производят загрузку в печь твердых материалов. Современная 500-тонная печь имеет ванну длиной 19 м, шириной 5,8 м и глубиной более 1 м. Произведение этой длины на ширину принято считать условной площадью пода мартеновской печи.
23
Горячий газ подают в печь по центральному каналу, воздух − по двум боковым. Сходясь в рабочем пространстве печи, эти каналы образуют так называемую головку печи, формирующую газовое пламя. Загрузку твердой шихты в печь производят через окна с помощью завалочных машин. Выпуск стали и шлака из мартеновской печи после завершения плавки проводят через летку, расположенную в задней продольной стене печи, не имеющей загрузочных окон. На время плавки летку (выпускное отверстие) заделывают магнезитовым порошком и огнеупорной глиной.
Различают скрап-процесс, при котором шихта состоит из стального лома (60…70 %) и твердого чушкового чугуна (30…40 %). Эта разновидность процесса применяется на заводах, не имеющих доменного производства и жидкого чугуна. Скрап-рудный процесс характерен тем, что его шихта состоит из 20…50 % скрапа, 80…50 % жидкого чугуна и железной руды в количестве 15…30 % массы металлической части шихты.
Завалочная машина современных крупных печей − это самоходная тележка, перемещающаяся по рельсам вдоль продольных лицевых стенок нескольких мартеновских печей, обычно расположенных в одну линию. На самоходной тележке установлен механизм управления с кабиной машиниста и загрузочный механизм с длинным штоком (хоботом). Хобот завалочной машины поднимает с платформы мульду с шихтой, вносит в печь через окна и, поворачивая, высыпает ее содержимое, затем выносит пустую мульду из печи.
Жидкий чугун загружают в печь через окно с помощью вставляемого стального желоба, футерованного изнутри огнеупором. Чугун заливают в печь, когда твердая шихта прогрета и начинает оплавляться. Во время плавления образуется значительное количество закиси железа, так как избыток воздуха, подаваемого для сжигания топлива (125 % теоретически необходимого), делает пламя в мартеновской печи окислительным.
24
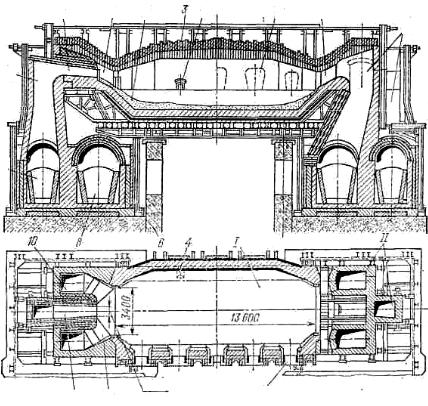
1 |
2 |
7 |
3 |
4 |
5 |
2 |
II
10
9
|
|
|
|
|
|
|
|
|
|
|
|
|
|
II |
|
|
|
|
|
|
|
|
4 |
|
|
|
|
|
|
10 |
|
8 |
|
|
|
|
|
|
|
I |
|
|
||
|
|
|
|
6 |
|
|
|
|
|
|||||
|
|
|
|
|
|
|
|
|
|
|||||
|
|
|
|
|
|
|||||||||
|
|
|
|
|
|
|
|
|
|
|
|
|
|
|
|
|
|
|
|
|
|
|
|
|
|
|
|
|
|
|
|
|
|
|
|
|
|
|
|
|
|
|
|
|
|
|
|
|
|
|
|
|
|
|
|
|
|
|
|
|
|
|
|
|
|
|
|
|
|
|
|
|
|
|
|
|
|
|
3400 |
|
|
|
|
|
|
|
|
|
|
|
|
|
|
|
|
|
|
|
13600 |
|
|
|||
|
|
|
|
|
|
|
|
|
|
|
|
|
|
|
1 |
2 |
800 |
5 |
|
Рис. 4. Мартеновская печь:
I − рабочее пространстве печи; II − головки с вертикалями; 1 − газовый канал головки; 2 − воздушный канал; 3 − свод печи; 4 − летка; 5 − загрузочные окна; 6 − бетонные опоры; 7 − откос пода; 8 − шлаковики воздушного регенератора; 9 − шлаковики газового регенератора; 10 − вертикальные каналы
Образующаяся закись железа окисляет примеси: [Si] + 2 (FеО) = 2Fеж + (SiO2);
[Мn] + (FеО) = Fеж + (МnО);
2 [Р] + 8 (FеО) = 5Fеж + (3FеО Р2O5);
[С] + [FеО] = Fеж + СОгаз.
25
Окисление углерода в еще не прогретой ванне вызывает вспенивание шлака. Этим пользуются для удаления из печи самотеком через пороги загрузочных окон части первичного шлака, содержащего значительное количество фосфора в виде 3FеО Р2O5 и кремнезема. К концу плавления шихты известняк, прогревшись, переходит
визвесть и растворяется в шлаке. После расплавления шихты начинается доводка стали. В печи образуется ванна металла, покрытая сверху слоем шлака, содержащего значительное количество оксидов железа, которые, благодаря перемешиванию ванны, попадают
вметалл и окисляют примеси, в том числе и углерод:
(FеО) + (С) = Fеж + СОгаз.
Образующийся СО в виде газовых пузырьков хорошо перемешивает ванну и способствует выделению из металла газовых и других включений. Процесс выделения угарного газа называют «кипением» ванны. В это время для интенсификации кипения
впечь добавляют железную руду. Увеличение оксидов железа
вшлаке ускоряет процесс. Таким образом, шлак в ванне мартенов-
ской печи, интенсивно перемешиваемый тепловыми потоками и выделяющимся из металла газом, передает металлу теплоту
икислород.
Вэтот же период из шихтовых материалов удаляют фосфор путем периодического скачивания шлака. Важную роль для связывания окислов фосфора играет известь:
3FеО Р2О5 + 4СаО = 4СаО Р2О5 + 3FеО.
Для успешного удаления фосфора необходимо иметь в шлаке максимальное количество извести. Однако большой избыток извести затрудняет мартеновскую плавку, так как подобные шлаки тугоплавки. Наличие свободной извести способствует также и переводу в шлак соединений серы, присутствующих в металле.
26
Процесс доводки металла до нужного химического состава производится в так называемый период чистого кипения металла, начинающегося после прекращения добавок в него железной руды. Чистое кипение ванны протекает не менее 1 ч. Готовность заданной плавки стали определяют взятием пробы и экспресс-анализом.
После этого проводится раскисление и выпуск стали в ковши, из которых ее разливают в слитки. Общая продолжительность получения стали в мартеновской печи занимает несколько часов. Раскисление стали в ванне мартеновской печи проводят сначала доменным ферромарганцем, а затем ферросилицием. Кремний ферросилиция связывает растворенный кислород и образует сложные силикаты железа и марганца, которые всплывают в ванне и переходят в шлак. После этого сталь начинают выпускать из печи и завершают раскисление в ковше, забрасывая в него куски богатого ферросилиция (45 или 75 % Si) и алюминия или силикоалюминия.
Алюминий является активным раскислителем стали, но образующийся А12О3 тугоплавок и в виде тонкой взвеси почти весь остается в стали. Принято считать, что эти частички А12О3 служат центрами кристаллизации при формировании слитка, и с увеличением количества алюминия, вводимого для раскисления, можно получить более мелкую структуру слитка или отливки. Обычно для раскисления расходуют 100…400 г алюминия на 1 т выплавляемой стали в зависимости от ее марки.
Главное преимущество мартеновского способа − его универсальность как в возможности выплавки широкого сортамента углеродистых и легированных сталей, так и в использовании исходных материалов.
Мартеновские печи разной мощности принято сравнивать по суточной производительности, отнесенной к площади пода печи, т. е. суточному съему стали с 1 м2 условной площади пода. В настоящее время эта цифра достигает 11…12 т, а с применением кислоро-
27
да она еще выше. Общая продолжительность плавки 220…260 т стали в печах составляет 7…10 ч при расходе условного топлива 130…150 кг на 1 т стали.
Основными недостатками мартеновского процесса следует считать его большую продолжительность и значительный расход топлива.
2.3. Получение стали в электрических печах
Эти печи обеспечивают в рабочем пространстве высокую температуру и восстановительную или нейтральную атмосферу, что очень важно при плавке высоколегированных сталей.
Для производства стали наиболее часто применяют дуговые трехфазные электропечи с вертикальными графитированными электродами и непроводящим подом. Ток, нагревающий ванну в этих печах, проходит по цепи электрод−дуга−шлак−металл−шлак−дуга−электрод. Вместимостьтакихпечейдостигает400 т.
Печь состоит из металлического кожуха цилиндрической формы и сферического дна (рис. 5). Подобно мартеновским, дуговые печи могут быть кислыми и основными. В основных печах подину выкладывают из магнезитового кирпича (до 80 % MgO), сверху которого наносят набивной слой из магнезита или доломита (150…200 мм). В кислых печах применяют динасовый кирпич (до 90 % SiO2) и набивку из кварцита на жидком стекле.
В цилиндрической части печи имеется рабочее окно и выпускное отверстие с желобом. Электропечи имеют механизмы для наклона печи на 40…45° в сторону выпускного отверстия для слива металла и на 10…15° в сторону рабочего окна для скачивания шлака. Свод печи обычно сферический, и через него в печь опускают три цилиндрических электрода. Рядом с печью помещены механизмы для подъема электродов и понижающий трансформатор, питающий печь электроэнергией. Мощность трансформатора
28
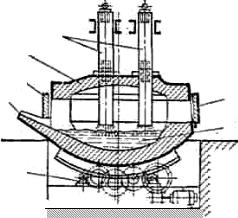
зависит от размеров и вместимости печи. Например, к510-тонные печи имеют трансформатор мощностью 3,5 МВ-А, а 250-тонные печи − трансформатор мощностью 65 МВ-А. Трансформатор печи имеет на низкой стороне несколько ступеней напряжения (3…12), переключая которые можно регулировать энергетическую нагрузку электродов.
4
3
2
1 |
|
|
2 |
6
5
Рис. 5. Схема дуговой трехфазной электропечи:
1 − выпускной желоб; 2 − дверка; 3 − свод; 4 − графитовые электроды; 5 − механизм наклона печи; 6 − расплавленный металл
Небольшие печи загружают через окно (с помощью мульд и завалочной машины), а печи вместимостью более 5 т − через свод, как правило. В этом случае свод с электродами изготовляют съемным, в период загрузки его поднимают, а печь отводят в сторону и мостовым краном сразу или в два приема загружают полную садку печи. После этого сводом вновь быстро накрывают печь.
После загрузки печи электроды опускают на металлическую шихту, предварительно засыпав ее сверху известью в количестве 2…3 % массы загруженного в печь металла. Известь способствует
29
ровному горению дуги, предохраняет материалы от поглощения газов и быстрее образует шлак. Плавление ведут на самых высоких ступенях напряжения, чтобы быстрее создать в печи жидкую фазу. Еще до полного расплавления шихты в печь засыпают известь и железную руду, обычно около 1 % массы металла, для получения в первом периоде плавки окислительного шлака. Через 10…15 мин после загрузки руды из печи скачивают 60…70 % шлака; с ним удаляется большая часть фосфора, так же как и при плавке в мартеновской печи, преимущественно в виде фосфатов железа.
После скачивания шлака в печь опять засыпают известь (1…1,5 % массы металла), полностью расплавляют и нагревают металл, порциями засыпают известь и железную руду для ускорения окисления углерода, фосфора и кремния, которое идёт по реакциям, приведенным в разделе, посвященном мартеновской плавке. По мере повышения температуры усиливаются окисление углерода и кипение ванны, что, как известно, способствует удалению из металла растворенных в нем газов и неметаллических включений.
В период кипения для полного удаления фосфора из металла сливают шлак, причем в это время при высокой температуре и большем количестве извести фосфор связывается в фосфат извести 4СаО Р2О5. Вместо слитого шлака наплавляется новый.
После того как содержание углерода в металле достигает нижнего предела для заданной марки, а содержание фосфора снижается до 0,015 %, шлак опять удаляют и дают ванне «прокипеть» 25 мин без присадки руды (т.е. проводят чистое, или безрудное, кипение). После этого начинают второй, восстановительный период плавки, загружают в печь смеси извести, плавикового шпата СаF2 и мелкого кокса для образования уже восстановительного шлака. Имеющийся в металле ванны кислород при этом образует оксиды железа и марганца, которые переходят в шлак и восстанавливаются имеющимся
30