
Модернизация и научные исследования в транспортном комплексе
..pdf
УДК 621.43
МАТЕМАТИЧЕСКОЕ МОДЕЛИРОВАНИЕ, ИССЛЕДОВАНИЕ И РАСЧЕТ ДИНАМИЧЕСКИХ ПРОЦЕССОВ В СИСТЕМЕ «АВТОМОБИЛЬНЫЙ ДВИГАТЕЛЬ – НАГРУЗКА»
А.Е. Радько, Р.Н. Хмелев
Тульский государственный университет, Россия
Приведены результаты математического моделирования, исследования и расчета динамических процессов в системе «Автомобильный двигатель – нагрузка» на примере автомобиля ГАЗ-3110 с двигателем ЗМЗ-4062. Установлены закономерности влияния параметров нагрузки на эффективность функционирования автомобильного двигателя и автомобиля в целом.
Ключевые слова: автомобильный двигатель внутреннего сгорания, автомобиль, нагрузка, математическое моделирование.
Современный автомобильный двигатель внутреннего сгорания (ДВС) является сложной технической системой, работающей большую часть времени в переходных режимах, характеризующихся постоянным изменением частоты вращения коленчатого вала и нагрузки. Одним из резервов улучшения мощностных, экономических
иэкологических показателей автомобильных ДВС, а также алгоритмов управления двигателями является выявление сложных закономерностей функционирования системы «Автомобильный ДВС – Нагрузка». Установление данных закономерностей позволит существенно сократить затраты при создании и доводке автомобильных ДВС и автомобиля «в целом» за счет их комплексной оптимизации учетом сложных динамических процессов в элементах системы «Автомобильный ДВС – Нагрузка».
Для автомобильного ДВС определение текущего значения нагрузки (момента сопротивления) является сложной задачей, решение которой зависит от совокупности динамических процессов, происходящих как в двигателе, так и в автомобиле «в целом», а также от дорожных
иметеорологических условий. В существующих работах момент сопротивления, как правило, определяется на основе опытных данных по эмпирическим зависимостям.
101
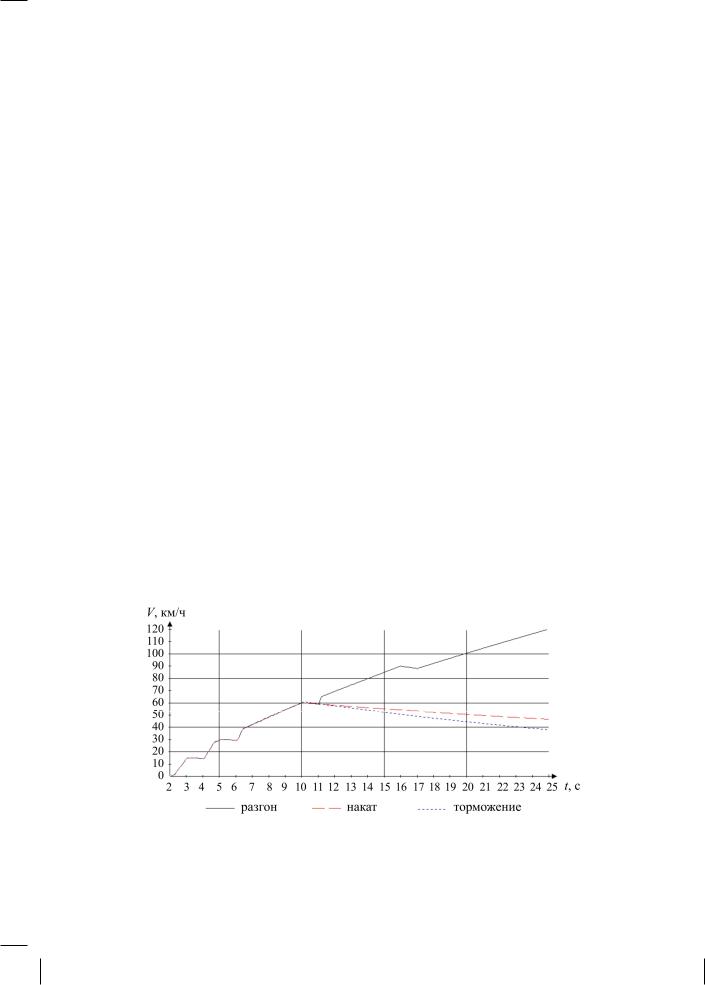
Данная работа посвящена совершенствованию методов теоретического исследования системы «Автомобильный ДВС – Нагрузка» для улучшения мощностных и экономических показателей автомобильного ДВС и автомобиля «в целом», а также сокращения затрат при их проектировании и доводке.
Для математического описания динамических процессов в системе «Автомобильный двигатель – Нагрузка» использовалась фазовая математическая модель, базирующаяся на теории графов связей [1–4]. В качестве объекта исследования был выбран автомобиль ГАЗ-3110 с двигателем ЗМЗ-4062.
Отличительной особенностью предлагаемого подхода является тот факт, что при проведении вычислительных экспериментов нагрузка (момент сопротивления на коленчатом валу двигателя) определяется в результате решения системы дифференциальных уравнений [4] в зависимости от режима движения автомобиля.
На рис. 1 и 2 в качестве примера приведены результаты расчетов изменения скорости движения и нагрузки при последовательном переключении передач и разгоне автомобиля, движении накатом после 10 с, а также торможении двигателем после 10 с.
На примере автомобиля ГАЗ-3110 с двигателем ЗМЗ-4062 был выполнен анализ влияния изменения передаточных чисел коробки переключения передач (КПП) на функционирование системы «Автомобильный ДВС – Нагрузка». Вычислительный эксперимент проводился
стремя исследуемыми КПП:
–пятиступенчатой коробкой передач 3110-1700010;
–четырехступенчатой коробкой передач 3110-1700010-10;
–пятиступенчатой коробкой передач 3302-1700010.
Рис. 1. Результаты расчета скорости движения автомобиля при разгоне, движении накатом и торможении двигателем
102

Рис. 2. Результаты расчета нагрузки при разгоне, движении накатом и торможении двигателем
На рис. 3 приведены результаты расчета расхода топлива при последовательном переключении передач и разгоне автомобиля с различными КПП.
Рис. 3. Результаты расчета расхода топлива при разгоне автомобиля с различными КПП
Приведенные результаты расчетов подтверждают широкие возможности разработанного математического и программного обеспечения. При этом результаты исследования и расчета динамических процессов в системе «Автомобильный двигатель – Нагрузка» могут использоваться для улучшения показателей автомобильного двигателя и автомобиля в целом, а также сокращения материальных и временных затрат при их проектировании и доводке.
Список литературы
1. Радько А.Е., Подъемщиков А.Н., Хмелев Р.Н. Разработка и исследование динамических моделей двигателей легковых автомобилей //
103

Изв. ТулГУ. Сер. Технические науки. Вып. 11. Ч. 1. – Тула: Изд-во ТулГУ, 2014. – С. 362–368.
2.Малиованов М.В., Хмелев Р.Н., Радько А.Е. Особенности применения аппарата графов связей для математического описания процесса функционирования автомобиля // Перспективы развития науки
иобразования: материалы МЗНПК. – Тамбов, 2014. – С. 77–79.
3.Свидетельство о государственной регистрации программы для ЭВМ № 2014617074 / М.В. Малиованов, А.Е. Радько, Р.Н. Хмелев Про-
граммный комплекс «Имитационная динамическая модель автомобиля»; дата регистрации 10.06.2014.
4. Малиованов М.В., Хмелев Р.Н. Разработка и исследование динамической модели автомобиля // Модернизация и научные исследования в транспортном комплексе: материалы МНПК. – Пермь: Изд-во Перм. нац. гос. политехн. ун-та, 2013. – С. 207–216.
Об авторах
Радько Александр Евгеньевич (Тула, Россия) – аспирант кафедры
«Автомобили и автомобильное хозяйство», Тульский государственный университет (300012, г. Тула, пр. Ленина, 92; e-mail: aiah@yandex.ru).
Хмелев Роман Николаевич (Тула, Россия) – доктор технических наук, доцент, профессор кафедры «Автомобили и автомобильное хозяйство», Тульский государственный университет (300012, г. Тула,
пр. Ленина, 92; e-mail: aiah@yandex.ru).
104

УДК 621.873.3: 519.718.2
МЕТОДЫ УПРАВЛЕНИЯ И КОНТРОЛЯ УСТОЙЧИВОСТИ МОБИЛЬНЫХ ГРУЗОПОДЪЕМНЫХ МАШИН
А.В. Редькин, И.Н. Муравец
Тульский государственный университет, Россия
Рассмотрены вопросы повышения уровня эксплуатационной производительности и безопасности погрузочно-разгрузочных работ, выполняемых стреловыми самоходными кранами, при ненормируемых внешних воздействиях путем мониторинга грузовой устойчивости и стабилизации опорного контура.
Ключевые слова: грузоподъемная машина, безопасность, устойчивость, управление, мониторинг.
Обеспечение устойчивости мобильных грузоподъемных средств (стреловых самоходных кранов, подъемников, других машин, работающих на выносных опорах) является одним из необходимых условий при разработке систем управления грузоподъемными операциями. Особенностью этого класса машин является работа на неподготовленных площадках в заранее неизвестных условиях. Для мониторинга устойчивого положения предложен метод определения грузовой устойчивости по положению равнодействующей всех сил, действующих на грузоподъемную установку (или проекции центра масс), относительно опорного контура [1, 2]. В основе метода лежит ряд положений.
1.Для обеспечения гарантированной устойчивости свободностоящей крановой установки необходимым условием является нахождение внутри опорного контура равнодействующей вертикальных опорных давлений (рис. 1).
2.В качестве критерия устойчивого состояния выступает коэффициент устойчивости, определяемый степенью приближения точки приложения этой равнодействующей к границам опорного контура.
Коэффициент устойчивости определяется отношением размера опорного контура lx ,l y (рисунок) к расстоянию от точки приложения
равнодействующей сил (или центра масс) С до наиболее удаленной
границы опорного контура k = |
2l |
≥ 1, 2. |
|
l + b′ |
|||
|
|
105

Рис. Схема расположения контрольных областей устойчивости: 1 – гарантированная устойчивость; 2 – опасное снижение устойчивости;
3 – контрольная зона
Выбрав в качестве контролируемого параметра положение проекции центра масс, можно показать, что максимум коэффициента устойчивости (k = 2) будет при C x = 0 ( C y = 0 ), а минимум (k = 1,2) при
C x = (lx − 0,6lx ) / 0,6 , ( C y = (l y − 0,6l y ) / 0,6 ) (область 1 на рисунке). Если проекция центра масс C находится внутри этой области, устойчивое состояние ССК гарантировано. Для предотвращения аварийных ситуаций дополнительно вводится контрольная зона 3. Согласно правилам устройства и безопасной эксплуатации грузоподъемных кранов расчет устойчивости предусмотрен без динамических нагрузок. При статических нагрузках коэффициент устойчивости k ≥1,4. При попадании проекции центра масс в контрольную зону (положение C′′ ) необходимо изменить текущие параметры рабочих операций (снижение скорости перемещения, ограничение вылета стрелы, уменьшение момента на валу двигателя), предотвращая тем самым смещение центра масс в область опасного снижения устойчивости.
Управление исполнительными приводами по положению, скорости и моменту можно осуществить дроссельным регулированием [3]. Простота управления скоростью и моментом посредством золотникового преобразователя характеризуется тем, что регулирование гидравлических сопротивлений управляемых дросселей достигается при малых перемещениях золотника, которые могут измеряться долями милли-
106

метра. Постоянный контроль параметров, которые определяют запас крана по устойчивости, осуществляется теми или иными датчиками нагрузки, а также положения и скорости кранового оборудования.
Для определения текущего значения приведенной нагрузки (опрокидывающего момента) с учетом влияния динамического нагружения во время поворотного движения предложен способ [4]. На подвешенный на канате груз действуют сила тяжести и дополнительные динамические нагрузки, результирующая сила передается по канату через оголовок стрелы, изменение натяжения каната определяется датчиком. На основании полученной информации определяется изменение радиуса и высоты действия сил по отношению к ребру опрокидывания крана. Полученное значение натяжения позволяет определить текущее значение опрокидывающего момента, которое сравнивается с допустимым, вычисленным для данного положения кранового оборудования согласно защитной характеристике и показаниям датчиков положения и скорости. С учетом возможности изменения положения крана определяют оптимальные значения таких величин, как длина стрелы, высота подвеса, скорость и ускорение при совершении дальнейших грузоподъемных операций. В случае превышения допустимого опрокидывающего момента движение плавно прекращается, при этом дальнейшее движение возможно только в рекомендованном системой управления режиме.
Так как в основе способа действий лежит математическая модель крана, находящаяся в памяти бортового микропроцессора, она может быть изменена в зависимости от типа крана и его индивидуальных особенностей и усложнена при предъявлении более жестких требований и по мере развития исследований, т.е. устойчива к моральному старению.
Список литературы
1.Пат. РФ 2267458. Система контроля грузовой устойчивости мобильных грузоподъемных машин / П.А. Сорокин, А.В. Редькин, М.В. Козлов; 2006. Бюл. № 1.
2.Сорокин П.А., Анцев В.Ю., Редькин А.В., Обыденов В.А. Алгоритмы нечеткой логики в управлении устойчивостью стационарного башенного крана // Изв. Тул. гос. ун-та. Технические науки. – 2011. – № 4. – С. 238–245.
107

3.Сорокин П.А., Редькин А.В., Жильцов А.В. Обеспечение устойчивости стрелового самоходного крана с электрогидравлическим приводом // Подъемно-транспортное дело. – 2008. – № 6. – С. 5–7.
4.Пат. РФ 2440924. Способ управления грузоподъемным краном / П.А. Сорокин, А.В. Редькин, А.В. Чернов; 2012. Бюл. № 3.
Об авторах
Редькин Алексей Владимирович (Тула, Россия) – кандидат тех-
нических наук, доцент, доцент Тульского государственного универси-
тета (300012, г. Тула, пр. Ленина, 92; e-mail: ra171171@yandex.ru).
Муравец Илья Николаевич (Тула, Россия) – магистрант, Тульский государственный университет (300012, г. Тула, пр. Ленина, 92; e-mail: flok_ne@live.com).
108
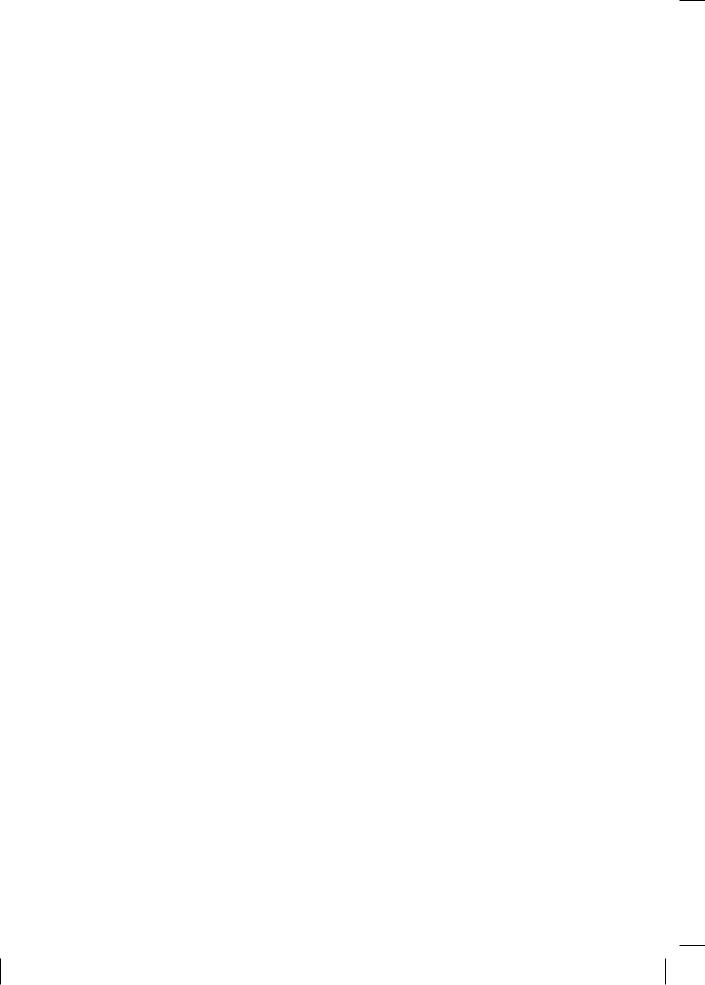
УДК 539.4: 621. 791.053
КИНЕТИКА ОБРАЗОВАНИЯ УСТАЛОСТНЫХ ТРЕЩИН В СВАРНЫХ СОЕДИНЕНИЯХ МЕТАЛЛОКОНСТРУКЦИЙ ГРУЗОПОДЪЕМНЫХ МАШИН
В.И. Сероштан, Т.В. Гаах
Московский государственный технический университет им. Н.Э. Баумана (Калужский филиал), Россия
Описаны условия и причины возникновения в металлоконструкциях ГПМ усталостных трещин, факторы, способствующие их зарождению, росту и оценке.
Ключевые слова: металлоконструкции, сварка, дефекты, трещина, усталость, сварные соединения, остаточные напряжения, скорость роста трещин.
Впроцессе эксплуатации парка грузоподъемных машин (ГПМ),
врезультате проводимых экспертными организациями технических обследований устаревших машин, отработавших нормативный срок службы, накоплен обширный эмпирический материал об их техническом состоянии. Однако до сих пор отсутствует приемлемая для практического использования в процессе дальнейшей эксплуатации таких ГПМ методика оценки их технического состояния. Особенно это актуально для сварных соединений несущих металлоконструкций с внутренними дефектами, которые зачастую становятся причиной поражений, разрушений и аварий (в том числе с трагическим исходом) металлоконструкций ГПМ [1].
Дефекты сварных соединений условно можно представить двумя группами. В первую группу входят допущенные дефекты при подготовке конструкции к сварке. Наиболее характерными дефектами этой группы являются: несовпадение стыковых плоскостей кромок свариваемых деталей, непостоянство зазоров между кромками, неправильный угол скоса кромок в швах, чрезмерное или недостаточное притупление стыкуемых кромок по длине, расслоение металла и загрязнения на кромках. Допущенные дефекты при подготовке и сборке к сварке приводят к появлению сварочных дефектов в виде пор, шлаковых включений, подрезов, непроваров, несплавления, кратеров, прожигов [2].
109

Сварочные дефекты бывают наружными (поверхностными)
ивнутренними. Наружные дефекты сварки обычно обнаруживают внешним осмотром и геометрическими измерениями с помощью специализированного инструмента и шаблонов. Внутренние макроскопические дефекты выявляют неразрушающими методами контроля (НК). Дефекты, обнаруживаемые визуально, могут быть исправлены. Значительное количество поверхностных дефектов обычно указывает на наличие в этом месте и внутренних дефектов.
При сварке плавлением регламентируют ширину и выпуклость шва, число проходов, глубину проплавления. Неполномерность швов может образоваться вследствие неустойчивого режима сварки, неравномерности зазора и угла скоса кромок, неточного направления электрода относительно разделки, недостаточной или увеличенной скорости подачи электрода.
Наиболее часто встречающиеся дефекты сварных соединений – это поры и шлаковые включения с размерами от нескольких микрометров до нескольких миллиметров. Форма их обычно сферическая. Часть из них выходит на поверхность. Из канальных пор обычно развиваются сквозные дефекты, так называемые свищи. Поры образуются при плохой зачистке кромок от ржавчины, окалины и загрязнения. Также причиной их образования может быть большая скорость сварки и недостаточная сила тока. Шлаковые включения могут располагаться на границе сплавления основного металла с наплавленным, вызывая местную концентрацию и снижая прочность соединения. Микроскопические шлаковые включения представляют собой загрязнения в виде окиси железа, сульфидов, нитридов, легкоплавких эвтектик.
Подрезы образуются на поверхности сварных швов, в виде появляющихся в процессе сварки вдоль края шва углубления. Образуются они при обрыве дуги, уменьшая рабочее сечение шва, снижая его прочность и коррозионнуюстойкость. Частьподрезовслужиточагомпоявлениятрещин.
Внутренние дефекты сварных соединений, как правило, закладываются в процессе изготовления или ремонта металлоконструкции. Размеры этих дефектов очень малы по сравнению с размерами самых соединений. В процессе эксплуатации ГПМ под влиянием прилагаемых циклических нагрузок внутренние дефекты являются источником зарождения внутренних усталостных трещин. Процесс зарождения
ираспространения зародившейся трещины, вплоть до ее выхода на поверхность элемента металлоконструкции, имеет скрытый характер
ивизуально не наблюдается.
110