
Модернизация и научные исследования в транспортном комплексе
..pdf
и электронным блоком управления впрыском 4 при достижении действительной скорости транспортного средства, равной критической, датчики 5, фиксирующие усредненную полезную нагрузку, определяющие вертикальную координату центра масс и величину поперечного крена кузова, датчик 6, установленный на валу рулевого механизма, фиксирующий угол поворота руля, датчик 7, установленный на балке моста транспортного средства, фиксирующий поперечный наклон дорожного профиля, устройство 8 светозвуковой сигнализации, заблаговременно предупреждающее водителя о приближении действительной скорости к критической, устройство ввода параметров технической характеристики транспортного средства 9, датчик угловой скорости ведущих колес 10, радар 11, установленный над ведущим колесом и определяющий абсолютную линейную скорость этого колеса, сумматор 12, определяющий среднее значение абсолютных линейных скоростей ведущих колес.
Рис. Структурная схема системы контроля и ограничения скорости движения колесных машин
Посредством устройства ввода 9 в систему вводятся значения параметров технической характеристики транспортного средства (L – длина базы, м; В – ширина колеи, м; h – высота центра масс при снаряженной массе транспортного средства, м; Uру – передаточное число рулевого управления; rк – радиус колеса, м). В случае загрузки транспортного
91

средства в устройство определения критической скорости 1 со стороны датчиков 5 поступает измененное значение высоты центра масс. В устройстве 1 происходит определение коэффициента поперечной устойчивости автомобиля:
η = |
В |
. |
(1) |
|
|||
|
2h |
|
|
В случае бокового крена кузова происходит изменение значения |
|||
координат центра масс, определяемое датчиками 5 |
и передаваемое |
в устройство 1. Тогда в устройстве 1 происходит определение угла γ (град) бокового крена кузова:
dz |
(2) |
|
γ = arctg dy , |
||
|
где dz и dy – соответственно изменение вертикальной и поперечной координат центра масс.
Со стороны датчика 7, установленного на балке моста транспортного средства, в устройство 1 поступает сигнал о значении угла поперечного наклона дорожного профиля β (град), со стороны датчика 10 угловой скорости ведущих колес – сигнал о значении угловой скорости его вращения ωкi (рад/с), со стороны датчика 6 – сигнал о значении угла поворота рулевого колеса θ (град), со стороны радара 11, установленного над ведущими колесами, – значение абсолютной (реальной) линейной скорости этих колес vкi (м/с). При этом в устройстве 1 происходит определение среднего угла поворота управляемых колес (град):
Ωупр |
= |
θр.к |
; |
(3) |
|
||||
|
Uр.у |
|
радиуса поворота транспортного средства (м):
L |
|
|
R = tgΩупр |
; |
(4) |
теоретической линейной скорости:
vтi = rк·ωкi (м/с),
92
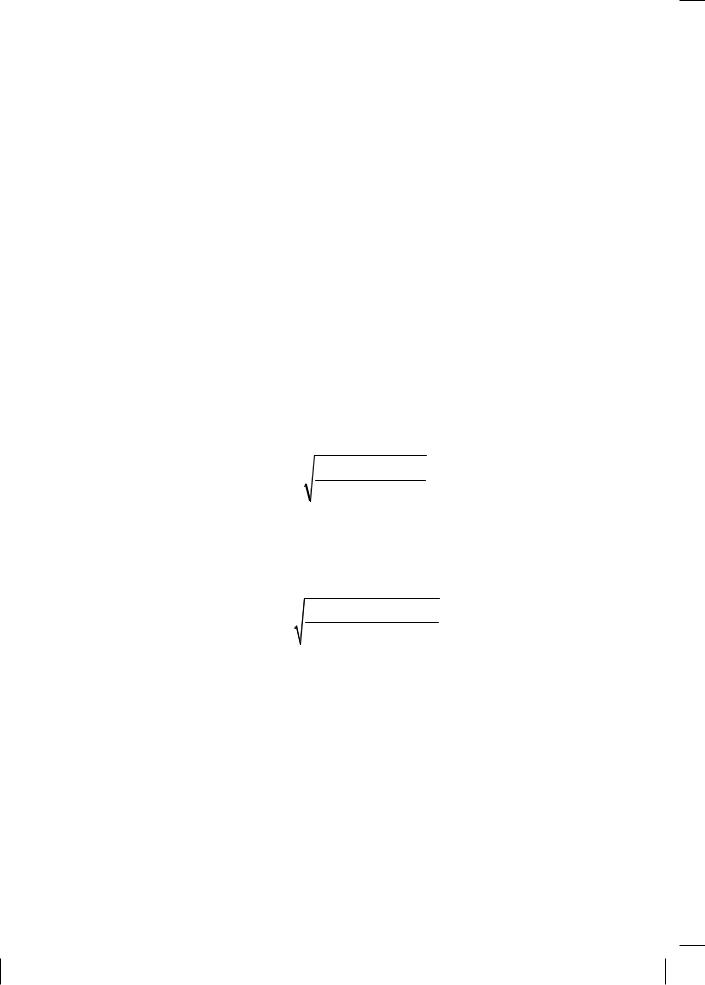
и определяется коэффициент скольжения колеса
sкi = (vкi – vтi)/vкi.
Далее в устройстве 1 определяется среднее значение коэффициента
n
скольжения sср = sкi (где n – число ведущих колес) и по функцио-
i=1
нальной зависимости определяется значение коэффициента сцепления колес с опорной поверхностью φ = f (sср). Затем происходит сравнение коэффициента сцепления с коэффициентом поперечной устойчивости транспортного средства. В случае если φ < η, то при повороте существует вероятность нарушения курсовой устойчивости, проявляющегося в виде заноса. Если φ > η, то при повороте существует вероятность нарушения поперечной устойчивости, проявляющегося в виде опрокидывания транспортного средства.
Если при повороте транспортного средства может наступить занос, то в устройстве 1 происходит определение критической скорости по заносу:
v = φ+ tg(β− γ) gR . (5)
кр. зан |
1 |
− tg(β− γ) |
|
Если при повороте транспортного средства может наступить опрокидывание, то в устройстве 1 происходит определение критической скорости по опрокидыванию:
v = tg(β− γ) + 0,5B gR . (6)
кр. опр |
h − 0,5Btg(β− γ) |
|
Одновременно с радара 11 значение абсолютной (реальной) линейной скорости ведущих колес vкi (м/с) поступает в сумматор 12, где происходит определение среднего значения абсолютных линейных
n
скоростей ведущих колес vср = vкi . Далее в устройстве 1 происходит
i=1
сравнение реальной скорости транспортного средства по средней линейной скорости колес vср с критической vкр.
В том случае если реальная скорость транспортного средства достигает значения vср = 0,85vкр, устройство 8 выдает звуковой и световой
93

сигналы водителю о приближении значения скорости движения транспортного средства к значению критической скорости. Если скорость транспортного средства продолжает расти и становится равной 0,9vкр, то устройство 1 подает сигнал на рассогласователь 2.
Рассогласователь 2 разрывает связь между датчиком 3 положения педали подачи топлива и электронным блоком 4 управления впрыском и выдает эквивалентный сигнал сигналу датчика 3 положения педали подачи топлива. Кроме того, на рассогласователь 2 поступают: сигнал с сумматора 12 о мгновенной скорости движения транспортного средства; сигнал с датчика 3 о скорости нажатия на педаль подачи топлива. Если значение мгновенной скорости транспортного средства vср соответствует значению 0,9vкр, то рассогласователь 2 выдает сигнал, соответствующий малому перемещению педали подачи топлива.
Электронный блок 4 управления впрыском топлива, получая такой сигнал, полностью прекращает выдачу командных импульсов на топливную форсунку, которая при этом прекращает подачу топлива в цилиндры двигателя, обеспечивая тем самым процесс торможения транспортного средства.
Список литературы
1. Автоматизированная система обеспечения курсовой и поперечной устойчивости транспортных средств при движении на повороте / Р.Р. Жарков, В.В. Ляхова, Е.В. Свиридов, С.Л. Овечкин // Междунар. науч. ин-т «Educatio»: ежемес. науч. журн. – Новосибирск, 2014. –
№ 7. – Ч. 3. – С. 91–93.
2. Жарков Р.Р., Свиридов Е.В. Система обеспечения курсовой и поперечной устойчивости автомобильной техники при криволинейном движении // Теоретические и прикладные аспекты современной науки: сб. науч. трудов по материалам V Междунар. науч.-практ. конф. 30 нояб. 2014 г.: в 6 ч. – Белгород, 2014. – Ч. 3. – С. 44–49.
3. Жарков Р.Р., Овечкин С.Л., Свиридов Е.В. Система обеспечения устойчивости движения транспортных средств на повороте // Модернизация и научные исследования в транспортном комплексе. – 2015. –
№1. – С. 62–65.
4.Жарков Р.Р., Свиридов Е.В., Овечкин С.Л. Система контроля и ограничения скорости движения колесных машин на повороте // Актуальные вопросы совершенствования военной и специальной техники:
94
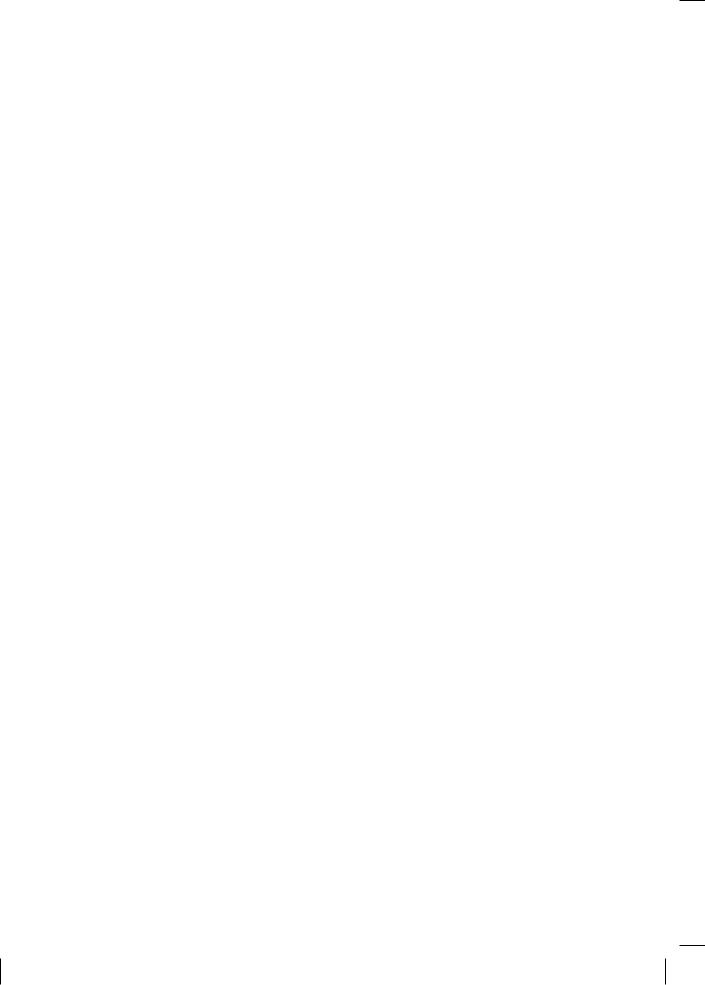
сб. науч. материалов, посвященный 105-й годовщине со дня образования автомобильных войск России. – Пермь, 2015. – С. 22–27.
5. Пат. 157919 Российская Федерация, МПК В60К 31/00 Автоматическое устройство контроля и ограничения скорости транспортного средства на повороте по параметрам курсовой и поперечной устойчивости / Е.В. Свиридов, С.А. Объедков.
Об авторах
Объедков Сергей Анатольевич (Пермь, Россия) – курсант пятого курса факультета технического обеспечения, Пермский военный институт ВВ МВД России (614112, г. Пермь, ул. Гремячий Лог, 1; e-mail: sergei2005893@yandex.ru).
Свиридов Евгений Викторович(Пермь, Россия) – кандидат техни-
ческих наук, доцент кафедры «Автомобили и технологические машины», Пермский национальный исследовательский политехнический универси-
тет (614990, г. Пермь, Комсомольский пр., 29; e-mail: schem_sev@bk.ru).
95

УДК 621.19
ОСОБЕННОСТИ УПРАВЛЕНИЯ ТОЧНОСТЬЮ ПРЕЦИЗИОННОЙ ОБРАБОТКИ ДЕТАЛЕЙ ТРАНСПОРТНЫХ МАШИН
А.К. Остапчук1, Е.М. Кузнецова1, А.Г. Михалищев1, А.И. Шашков2
1Курганский институт железнодорожного транспорта, Россия
2Уральский государственный университет путей сообщения, Екатеринбург, Россия
Рассмотрены особенности управления точностью технологической обрабатывающей системы. Разработана структура комбинированного управления точностью прецизионной обработки.
Ключевые слова: прецизионная обработка, математическая модель, управление по возмущению, управление по отклонению.
Управление точностью прецизионной обработки имеет свои особенности, связанные со спецификой условий, в которых она осуществляется:
–небольшие снимаемые припуски (5–20 мкм) и как следствие снижение интенсивности износа режущего инструмента;
–малые (единицы микрометров) допуски на размер, повышающие степень ответственности контрольно-измерительных операций, что практически приводит к увеличению их продолжительности и делает соразмерными со временем обработки;
–рост влияния тепловых возмущений ввиду того, что величина вызываемых ими деформаций элементов конструкции станка соизмерима с допуском на размер.
Специфика же управления в данном случае состоит в том, что важным является определение не величины подналадочного импульса,
амомента, когда его необходимо вводить. Это связано с тем, что для уменьшения вероятности случайных выбросов процесс обработки целесообразно центрировать к середине поля допуска. Таким образом, особую актуальность приобретает прогнозирование поведения процесса обработки в ближайшем будущем, что позволит упорядочить проце-
96

дуру контрольно-измерительных операций в направлении оптимизации их периодичности. Анализ существующих методов прогнозирования временных рядов, образованных отклонениями размеров от заданных, показал, что наиболее предпочтительным является использование методов, основанных на построении моделей, отслеживающих нестационарность исследуемого процесса на фоне помехи [1]. К числу этих моделей относятся, например, полиномиальные – на основе метода наименьших квадратов и расширенного метода наименьших квадратов
идискретные – на основе уравнения смешанного процесса авторегрессии проинтегрированного скользящего среднего (АРПСС) [2].
Вслучае если помеха носит характер белого шума или тепловой переходный процесс закончился, режим обработки стабилизируется
ивыполнение контрольно-измерительных операций становится практически нецелесообразным, поскольку зафиксированные в их ходе отдельные случайные выбросы не могут служить основанием для введения коррекции и последующего контроля реакции системы на нее. В этом случае с учетом специфики условий обработки более рациональной будет реализация автоматического контроля состояния технологической обрабатывающей системы с помощью соответствующей аппаратуры, т.е. организация канала управления по возмущению.
Постоянство градиента или колебания в заданных пределах отражают устойчивость процесса обработки и исключают необходимость проведения измерений изготовленных деталей, существенно увеличивая, тем самым, производительность оборудования. Рост размаха колебаний или появление значимого дрейфа температуры в опорной точке явится сигналом нарушения условия стационарности и определит момент проведения измерения.
Таким образом, в условиях прецизионной обработки целесообразной является реализация комбинированного управления точностью технологической системы (рисунок), канал управления по отклонению которого будет задействован преимущественно в переходном тепловом режиме, а канал управления по возмущению – в основном в условиях его стационарности.
Измерение размеров осуществляется встроенным в модуль датчиком положения поверхности с погрешностью не более 0,6 мкм. Для определения периодичности измерений в условиях управления по отклонению с помощью имитационного моделирования прогнозировалась точность обработки с применением следующих моделей [2]:
97

Рис. Структурная схема комбинированного управления точностью прецизионной обработки
1) авторегрессионная модель (AR):
A(z) y(t) = e(t),
где A(z) = 1 + a1z–1 + a2z–2 + … + anz–n; 2) модель ARX:
A(z) y(t) = B(z) u(t) + e(t),
где B(z) = b1 + b2z–1 + b3z–2 + … + bnz–n+1;
3) ARXMAX модель (модель авторегрессионной функции с использованием скользящего среднего):
A(z) y(t) = B(z) u(t – nk) + C(z) e(t),
где C(z) = 1 + c1z–1 + c2z–2 + … + cnz–n; nk – величина задержки; 4) модель вход-выход:
y(t) = B(z) u(t − nk) + e(t), F(z)
где F(z) = 1 + f1z–1 + f2z–2 + … + fnfz–nf;
98

5) модель Бокса-Дженкинса:
y(t) = B(z) u(t − nk) + C(z) e(t), F(z) D(z)
6)модель для переменных состояния:
x(t + 1) = Ax(t) + Bu(t),
y(t) = Cx(t) + Du(t) + ν(t),
где A, B, C, D – матрицы соответствующих размеров.
Анализ моделей показал, что периодичность измерений составляет 3–5 деталей при работе технологической системы в условиях динамического равновесия. Момент измерения при управлении по возмущению определялся исходя из условия увеличения размаха колебаний, генерируемых технологической обрабатывающей системой. Исходными данными для построения моделей и последующего анализа их точности были значения вибросигнала при чистовой токарной обработке, измеренные при помощи датчика акселерометра. Горизонт прогноза управления точностью по возмущению определялся на основе старшего показателя Ляпунова. В случае невозможности прогнозирования изза работы технологической обрабатывающей системы в области неустойчивости периодичность измерений уменьшается до одной детали. Последующим шагом при управлении точностью прецизионной обработки будет коррекция режимов обработки, позволяющая привести систему в устойчивое состояние.
Практическая реализация разработанных средств комбинированного управления точностью обработки позволит сократить брак до уровня случайных выбросов и повысить производительность оборудования на 10–30 %.
Список литературы
1.Остапчук А.К., Хрипунов С.В. Применение теории детерминированного хаоса к прогнозированию точности обработки // Изв. Челяб.
науч. центра УрО РАН. – 2005. – № 2. – С. 37–41.
2.Льюинг Л. Идентификация систем. Теория для пользователя. –
М.: Наука, 1991.
99

3.Остапчук А.К., Овсянников В.Е. Синергетический подход к определению отклика технологической системы на внешнее воздействие // Вестн. Урал. гос. ун-та путей сообщения. – 2011. – № 3. – С. 36–41.
4.Использование сигналов виброакустики для оптимизации режимов обработки / А.К. Остапчук, А.М. Симонов, Е.Ю. Рогов, Ю.В. Грохотов // Наука и образование транспорту. – 2011. – № 1. – С. 104–107.
Об авторах
Остапчук Александр Константинович (Курган, Россия) – канди-
дат технических наук, доцент, Курганский институт железнодорожного транспорта (e-mail: ostapchuk_ss@mail.ru).
Кузнецова Елена Михайловна (Курган, Россия) – аспирантка, Курганский институт железнодорожноготранспорта (e-mail: lenkuz@bk.ru).
Михалищев Александр Геннадьевич (Курган, Россия) – аспирант,
Курганский институт железнодорожного транспорта (e-mail: markos45 @mail.ru).
Шашков Алексей Игоревич (Екатеринбург, Россия) – аспирант, Уральский государственный университет путей сообщения (e-mail: svoboda666free@gmail.com).
100