
Журнал магистров. Masters journal N 2
.pdf
|
|
Окончание табл. 2 |
Программа |
Возможности |
Примечания |
Power |
Токарная, фрезерная, сверлильная |
|
solutions |
обработка |
|
|
Фрезернаяспроизвольнымчислом |
|
|
управляемыхосей, токарнаяобра- |
|
|
ботка, токарно-фрезернаяобработка, |
|
|
эрозионнаяплоскаяиобъемнаяоб- |
|
ADEM |
работка, гравированиеплоское |
|
|
иобъемное, резка(синструментом |
|
|
автоматическойраскладкидеталей |
|
|
произвольнойформыналисте), |
|
|
лазернаяобработка, обработка |
|
|
напрессахсЧПУ |
|
Таким образом, CAD/CAM-технологии позволяют добиться двух важных результатов – сократить время изготовления продукции и значительно снизить влияние человеческого фактора (а значит, ошибок).
Самостоятельное, не связанное между собой функционирование систем CAD и CAM дает эффект, размер которого может быть существенно увеличен интеграцией этих систем посредством CAPP. Такая интегрированная система CAD/CAM на информационном уровне поддерживается единой базой данных, в которой хранится трехмерная математическая модель изделия, т.е. информация о его структуре и геометрии (как результат проектирования в системе CAD), о технологии изготовления (как результат системы CAPP) и УП для оборудования с ЧПУ (как исходная информация для обработки в системе CAM на оборудовании с ЧПУ).
На данный момент в мире уже существует большое количество различных CAD/CAM-программ. Чаще CAM-модуль бывает в составе универсальной PLMсистемы, так как сквозное проектирование, где все параметры изделия зависят друг от друга и реагируют на изменения любой стадии, является наиболее предпочтительным. Также постоянно ведется разработка новых программ и совершенствование существующих. Каждый производитель стремится упростить освоение и использование продукта, а также развивать отличное от конкурентов направление. Это позволяет занять свою нишу и стимулирует специализированные производства использовать именно этот продукт. Однако на мировом рынке уже естьнесколько лидирующих компаний, программныепакеты которыхмогут составитьконкуренциюпрактическивовсехобластях.
Список литературы
1. Норенков И.П. Основы автоматизированного проектирования: учебник для вузов. – 4-е изд., перераб. и доп. – М.: Изд-во МГТУ им. Н.Э. Баума-
на, 2009. – 430 с.
41
2.Невлюдов И.Ш., Великодный С.С., Омаров М.А Использование CAD/CAM/CAE/CAPP при формировании управляющих программ для станков
сЧПУ // Вост.-Европ. журнал передовых технологий. – 2010. – № 2/2 (44). –
С. 37–44.
3.Смелов В.Г., Шитарев И.Л. Пути 3D-параметризации лопаток ГТД для использования с CAD/CAM/CAE пакетах // Вестн. Самар. гос. аэрокосм.
ун-та. – 2008. – № 3. – С. 44–47.
4.Глинских А. Мировой рынок CAD/CAM/CAE-систем // Компьютер-
Информ: сайт. – URL: http://old.ci.ru/inform01_02/p_22-23.htm (дата обращения: 21.05.14).
5.Волков С.А. Системы автоматизированного проектирования технологических процессов: учеб. пособие. – Рыбинск: Изд-во РГАТА им. П.А. Со-
ловьева, 2005. – 120 с.
6.Прогрессивные технологии моделирования, оптимизации и интеллектуальной автоматизации этапов жизненного цикла авиационных двигателей: монография / А.В. Богуслаев [и др.]; Запорож. нац. техн. ун-т. – Запорожье:
Мотор-Сич, 2009. – 468 с.
7.Суханов Ю. Проект «Короли» и «капуста» на ниве САМ: Действительные и мнимые лидеры мирового рынка САМ-систем в 2010 году, часть II // CAD/CAM/CAE Observer. – 2011. – № 8 (68). – С. 10–18.
Получено 7.10.2014
Сазонова Анна Олеговна – студент, ПНИПУ, МТФ, e-mail: anolsa@mail.ru.
Дроздов Андрей Александрович – аспирант, ПНИПУ, МТФ, e-mail: ittamp@mail.ru.
42
УДК 621.762
К.Э. Андраковская, М.Н. Каченюк
K.E. Andrakovskaya, M.N. Kachenuk
Пермский национальный исследовательский политехнический университет
Perm National Research Polytechnic University
КОНСОЛИДАЦИЯ КОМПОЗИЦИЙ НА ОСНОВЕ TIC МЕТОДОМ ПЛАЗМЕННО-ИСКРОВОГО СПЕКАНИЯ
CONSOLIDATION COMPOSITIONS BASED ON TIC
BY SPARK PLASMA SINTERING
Показана зависимость плотности спеченного материала от температуры режима плазмен- но-искрового спекания и исходного состава шихты. Представлены результаты проведенных режимов, сделан вывод о целесообразности применения метода плазменно-искрового спекания для консолидации порошков на основе карбида титана TiC.
Showed the dependence of density the sintered temperature regime of spark plasma sintering and the initial composition of the charge. Presented the results of the regimes, concluded the feasibility of applying the method of spark plasma sintering powders for consolidation based on titanium carbide TiC.
Ключевые слова: плазменно-искровое спекание, карбид титана, плотность, усадка, консолидация.
Keywords: spark plasma sintering, titanium carbide, density, shrinkage, consolidation.
Плазменно-искровое спекание (ПИС) является наиболее современной техникой спекания под давлением и применяется многими исследователями с 2000 г. [1, 2]. Принцип ПИС заключается в совместном воздействии на порошковый материал импульсного постоянного тока и механического давления (рис. 1). Материал в зоне воздействия разогревается до очень высоких температур, вплоть до плазменного состояния.
Консолидацию порошков проводили на установке Dr. Synter SPS-1050b (SPS Syntex, Япония) в графитовой пресс-форме с молибденовой обечайкой при температуре 1100–1400 °С, давлении 30 МПа, изотермической выдержке 5 мин. Средняя скорость нагрева составляла 80 °С/мин. Величина тока для образцов диаметром 20 мм составляла 1100–1300 А в зависимости от конечной температуры спекания.
Спеченные образцы взвешивали на аналитических весах ВЛА-200. Плотность образцов определяли гидростатическим взвешиванием по стандартной методике [3].
43
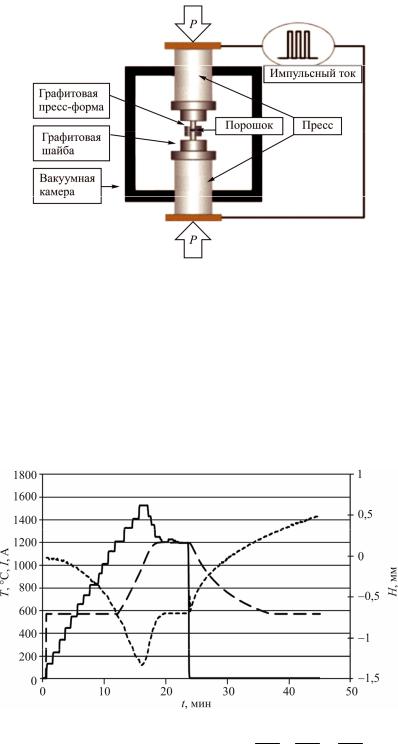
Рис. 1. Схема установки для плазменно-искрового спекания
Из графика на рис. 2 видно, что при увеличении тока происходит увеличение температуры оснастки. С увеличением температуры изменяется усадка образца. В начале режима происходит расширение пресс-формы. Далее при определенной температуре расширение сменяется усадкой, что связано с уплотнением материала. Во время выдержки изменение высоты образца отсутствует, поскольку соответствующий участок усадки горизонтален. После окончания режима, в то время как образец охлаждается, усадка начинает расти за счет термического сжатия.
Рис. 2. Зависимость тока и усадки от времени при плазменно-искровом спекании TiC при температуре 1200 оС: I; T; h
44
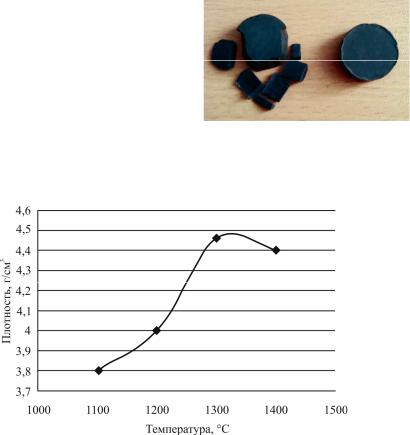
При извлечении образцов на основе карбида титана без добавок из оснастки все они растрескиваются (рис. 3, а), что говорит о слабой связи между частицами (табл. 1).
|
|
|
|
|
|
|
|
Таблица 1 |
|
|
Результаты исследования спеченных образцов чистого TiC |
|
|||||||
|
|
|
|
|
|
|
|
|
|
№ |
Состав |
t, оС |
∆h, мм |
ρ, г/см3 |
В, % |
|
По, % |
П, % |
Пз, % |
п/п |
|
|
|
|
|
|
|
|
|
1 |
TiC0,7 |
1100 |
1,66 |
3,8 |
4,63 |
|
17,6 |
23 |
5,4 |
2 |
TiC0,7 |
1200 |
1,67 |
4,0 |
3,5 |
|
14 |
18,9 |
4,9 |
3 |
TiC0,7 |
1300 |
2,4 |
4,46 |
1,14 |
|
5,12 |
9,6 |
4,5 |
4 |
TiC0,7 |
1400 |
2,84 |
4,4 |
1,29 |
|
5,67 |
10,8 |
5,1 |
|
Примечание: ρ – плотность, г/см3; В – водопоглощение, %; По – открытая порис- |
||||||||
тость, %; П – пористость, %; Пз – закрытая пористость, %. |
|
|
|
Таким образом, при исследованных температурах спекания методом ПИС невозможно получить материал на основе чистого карбида титана. На рис. 4 можно проследить, как изменялась плотность TiC, спеченного в интервале тем-
ператур 1100–1400 оС.
Из графика зависимости плотности от температуры спекания следует, что до 1300 °С происходит увеличение плотности, но при дальнейшем увеличении температуры плотность не растет.
аб
Рис. 3. Спеченные образцы:
а – TiC без добавок; б – TiC+10%SiC
Рис. 4. Зависимость плотности от температуры при плазменно-искровом спекании TiC
45
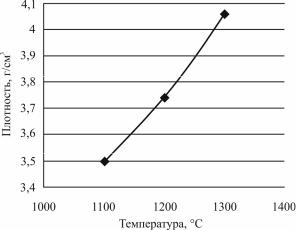
Результаты исследования спеченного образца карбида титана с добавле-
нием 6 % никеля (TiC0,7+6%Ni):
t, оС |
h, мм |
ρ, г/см3 |
В, % |
По, % |
П, % |
Пз, % |
1400 |
2,7 |
5,04 |
0,3 |
5,12 |
9,6 |
4,5 |
Добавка никеля в порошковую смесь способствует небольшому уплотнению материала, образец так же растрескивается при извлечении из молибденовой обечайки, хотя и в меньшей степени.
Добавка SiC в порошковую смесь влияет на температурный интервал усадки материала, значительно упрочняет связи между частицами карбида титана в спеченном образце – образцы сохраняют форму после извлечения из пресс-формы (рис. 3, б), но несколько уменьшает плотность. Влияние добавки на пористость материала не наблюдается, пористость остается на уровне
16–19 % для температуры 1100 °С и 14–16 % для 1200 °С (табл. 2).
Таблица 2
Результаты исследования спеченных образцов карбида титана с добавлением 10 и 20 % карбида кремния
|
|
|
|
|
|
|
|
|
№ |
Состав |
t, оС |
h, мм |
ρ, г/см3 |
В, % |
По, % |
П, % |
Пз, % |
п/п |
|
|
|
|
|
|
|
|
1 |
TiC0,7+10%SiC |
1100 |
1,1 |
3,64 |
4,54 |
16,54 |
22,4 |
5,86 |
2 |
TiC0,7+10%SiC |
1100 |
1,25 |
3,59 |
5,2 |
18,7 |
23,2 |
4,5 |
3 |
TiC0,7+10%SiC |
1200 |
- |
3,74 |
4,0 |
15,0 |
19,3 |
4,3 |
4 |
TiC0,7+10%SiC |
1300 |
1,94 |
4,06 |
2,9 |
11,8 |
12,3 |
0,5 |
5 |
TiC0,7+20%SiC |
1100 |
1,11 |
3,4 |
5,83 |
19,2 |
23,6 |
4,4 |
6 |
TiC0,7+20%SiC |
1200 |
1,66 |
3,55 |
4,65 |
16,51 |
21,46 |
4,95 |
Рис. 5. Зависимость плотности от температуры при плазменно-искровом спекании TiC+10%SiC
46
На рис. 5 можно увидеть, как изменяется плотность компактного материала в интервале температур 1100–1300 оС.
При повышении температуры ПИС плотность материала растет до некоторого предела. Добавление никеля позволяет несколько повысить прочность материала на основе карбида титана. При увеличении содержания карбида кремния снижается абсолютная плотность, а пористость остается неизменной. Для получения материала на основе карбида титана методом ПИС необходимо использовать спекающие добавки.
Список литературы
1.Effect of starting powders on the sintering of nanostructured ZrO2 ceramics by colloidal processing / G. Suárez, Y. Sakka, T.S. Suzuki [et al.] // Science and Technology of Advanced Mater. – 2009. – Vol. 10, № 2. – Р. 68–76.
2.Preparation of nanocrystalline BaTiO3 ceramics / X.Y. Deng, D.J. Li, J.B. Li [et al.] // Science in China. Ser. E: Technological Sciences. – 2009. – Vol. 52, № 6. – Р. 1730–1734.
3.ГОСТ 18847–84. Методы определения водопоглощения, кажущейся плотности и открытой пористости зернистых материалов. – М.: Изд-во стан-
дартов, 2004. – 6 с.
Получено 7.10.2014
Андраковская Ксения Эдуардовна – магистрант, ПНИПУ, МТФ,
гр. МТН-13м, e-mail: andrakovi4@yandex.ru.
Каченюк Максим Николаевич – кандидат технических наук, доцент,
ПНИПУ, МТФ, e-mail: maxx@pm.pstu.ac.ru.
47
УДК 621.762
С.А. Оглезнева, К.А. Мазуренко
S.A. Oglezneva, K.A. Mazurenko
Пермский национальный исследовательский политехнический университет
Perm National Research Polytechnic University
ИЗУЧЕНИЕ ФИЗИКО-МЕХАНИЧЕСКИХ СВОЙСТВ
ИИЗНОСОСТОЙКОСТИ МЕДЬ-УГЛЕРОДНЫХ ЭЛЕКТРОТЕХНИЧЕСКИХ МАТЕРИАЛОВ
STUDY OF PHYSICAL AND MECHANICAL PROPERTIES AND WEAR RESISTANCE OF COPPER-CARBON ELECTROTECHNICAL MATERIALS
Рассмотрена сущность процесса электроэрозионной обработки и основные требования, предъявляемые к электродам-инструментам. Представлены классические материалы для электроэрозионной обработки, их свойства. Описано физико-химическое взаимодействие в системе медь – графит, характеристики и свойства порошков ПМС-1, ПМВД-0, графита и углеродного наноматериала «Таунит». Изложены методики эксперимента и исследований. Изучено влияния состава конструкционных материалов на пористость, прочность, электросопротивление, относительную износостойкость ЭИ.
The essence of the process of electrical discharge machining and basic requirements for the tool electrode are investigated. Presented classic materials for electrical discharge machining, their properties. Described physical and chemical interaction in the copper – graphite, characteristics and properties of powders ПМС-1, ПМВД-0, graphite and carbon nanomaterial Taunit. Sets out methods of experiment and research. Studied the impact of composite material on porosity, strength, electrical receptivity, relative wear resistance of tool electrode.
Ключевые слова: электроэрозионная обработка, система медь – углеродные фазы, графит, нанопорошки, материалы электродов-инструментов, пористость, прочность, электросопротивление, износостойкость.
Keywords: electrical discharge machining, system copper – carbon phase, graphite, nanopowders, materials tool electrode, porosity, strength, electrical receptivity, relative wear resistance.
Современные тенденции развития машино- и приборостроения связаны с расширением использования прогрессивных технологических процессов и применением жаропрочных, тугоплавких, сверхтвердых и других труднообрабатываемых материалов, что вызывает большой интерес к технологиче-
48
ским процессам и оборудованию для электроэрозионной обработки. Электроэрозионная обработка (ЭЭО) основана на эффекте расплавления и испарения микропорций материала, в основном под тепловым воздействием импульсов электрической энергии. Эта энергия выделяется в канале разряда между поверхностью обрабатываемой детали и электродом-инструментом, погруженным в жидкую (обычную неэлектропроводящую) среду. Следующие друг за другом импульсные разряды производят выплавление и испарение микропорции материала; частицы расплавленного материала выбрасываются из зоны обработки развивающимся в канале разряда давлением, и электродинструмент получает возможность внедряться в обрабатываемую деталь [1].
Электроды-инструменты (ЭИ) являются одними из основных элементов, участвующих в электроэрозионном процессе. Их параметры оказывают существенное влияние на стабильность электроэрозионного процесса, его эффективность и область использования. Производительность и качество ЭЭО также находится в зависимости от материала ЭИ. Электрод-инструмент должен изготовляться из эрозионно-стойкого материала, обеспечивать стабильную работу во всем диапазоне рабочих режимов ЭЭО и максимальную производительность при малом износе. Количество тепловой энергии, выделяющейся на каждом из электродов при импульсном электрическом разряде, неодинаково; также различно и количество снимаемого материала с поверхности каждого из электродов.
Масса расплавленного и удаленного с электрода материала зависит от ряда факторов: это теплофизические свойства материалов, из которых изготовлены электроды (температура кипения, плавления, теплопроводность и теплостойкость); параметры рабочего импульса; полярность подключенных электродов. Электрическая эрозия будет менее интенсивной у материалов, обладающих высокими температурами плавления, и наоборот [2]. Одним из путей снижения износа электрода-инструмента является использование материалов, имеющих высокую эрозионную стойкость. Если расположить известные материалы, используемые для изготовления электродов-инструментов, в порядке возрастания их эрозионнойстойкости, топереченьбудетвыглядетьтак: алюминийиегосплавы, серыйчугун, латунь, медь, вольфрам, графитированныематериалы[3].
Электроды-инструменты из меди дают возможность запускать ЭЭО на самых производительных режимах, обеспечивают наиболее стабильное течение процесса. Медь позволяет высокоточно изготовить электрод практически любой сложнойформыипрофилянаметаллообрабатывающемоборудовании[4].
Электроды-инструменты из графита, углеграфитового, графитизированного материала широко используются при ЭЭО благодаря высокой электроэрозионной стойкости, хорошей обрабатываемости и низкой стоимости. По стабильности процесса электроды несколько уступают медным, особенно на чистовых режимах обработки. Ограничение применения графитизирован-
49
ного материала диктуется главным образом его сравнительно низкой механической прочностью, что не позволяет получать механообработкой сложнопрофильные тонкостенные конструкции ЭИ [4].
При обработке твердых сплавов и тугоплавких материалов на основе вольфрама, молибдена и ряда других материалов широко применяют ЭИ из композиционных материалов, так как при использовании графитовых ЭИ необеспечивается высокая производительность из-за низкой стабильности электроэрозионного процесса, а ЭИ из меди имеют большой износ, достигающий десятка процентов, и высокую стоимость [2]. Композиционные материалы системы медь – вольфрам имеют очень высокую стойкость, чаще применяются для исполнениясложныхработ, однакоимеютповышеннуюстоимость.
Существующие электродные материалы, применяемые в промышленности, уже не удовлетворяют в полной мере предъявляемым к ним требованиям. В ряде случаев дальнейшее развитие электроэрозионного метода обработки сдерживается недостаточной износостойкостью или дороговизной и сложностью изготовления электродов-инструментов. Например, эрозионный износ ЭИ, изготовленных из меди, латуни, чугуна, может быть в 10–100 раз выше, чем объем снятого металла с детали, что значительно снижает эффективность или делает даже нецелесообразным применение метода электроэрозионной обработки. Разработка новых технологических процессов создания эрозионно-стойких материалов, обладающих низкой стоимостью, представляет собой весьма важную задачу и имеет большое экономическое значение. Известны материалы, применяемые для изготовления электродов-инструментов станков электроэрозионной обработки на основе меди с различными добавками, повышающими стойкость к электрической эрозии, так как медь обладает хорошими электротехническими и прочностнымисвойствами
Цель работы – разработка материалов электродов-инструментов системы медь – углеродные фазы для электроэрозионной обработки.
Методики эксперимента и исследований. Для изготовления электро-
дов из композиционных материалов использованы порошки меди ПМС-1 (ГОСТ 49-60–75), ультрадисперсный медный порошок ПМВД-0, полученный методом газофазной конденсации по ТУ 1790-040-12288779–2005 (табл. 1), препарат сухого коллоидального графита марки С-1 (ТУ 113-08-48-63–90), материал углеродный наноструктурный «Таунит МД» (далее – таунит) (ТУ 2166-001-02069289–2007). Углеродный наноматериал таунит представляет собой одномерные наномасштабные нитевидные образования поликристаллического графита, преимущественно цилиндрической формы, с внутренним каналом – многослойные нанотрубки. Он имеет вид полидисперсного сыпучего порошка черного цвета, размер гранул 1–300 мкм, гидрофобен, не слеживается, малотоксичен.
50