
- •ВВЕДЕНИЕ
- •СОСТАВ, СТРУКТУРА И ОСНОВНЫЕ СВОЙСТВА ДОРОЖНО-СТРОИТЕЛЬНЫХ МАТЕРИАЛОВ
- •ПРИРОДНЫЕ КАМЕННЫЕ МАТЕРИАЛЫ
- •ИСКУССТВЕННЫЕ МАТЕРИАЛЫ НА ОСНОВЕ МИНЕРАЛЬНЫХ ВЯЖУЩИХ И МЕЛКОЗЕРНИСТЫХ ЗАПОЛНИТЕЛЕЙ
- •БЕТОНЫ (ЦЕМЕНТОБЕТОНЫ)
- •СБОРНЫЕ БЕТОННЫЕ И ЖЕЛЕЗОБЕТОННЫЕ ИЗДЕЛИЯ
- •МАТЕРИАЛЫ И ИЗДЕЛИЯ ИЗ ПЛАСТМАСС
- •ОРГАНИЧЕСКИЕ ВЯЖУЩИЕ МАТЕРИАЛЫ
- •АСФАЛЬТОБЕТОН
Глава 10 АСФАЛЬТОБЕТОН
10.1. ОПРЕДЕЛЕНИЕ, КЛАССИФИКАЦИЯ И ОБЛАСТЬ ПРИМЕНЕНИЯ АСФАЛЬТОБЕТОНА
Асфальтобетоном называют материал, который получают после уплотне ния асфальтобетонной смеси, приготовленной в смесителях в нагретом состоя нии из взятых в определенных соотношениях щебня* песка, минерального по рошка и битума. Если вместо битума применяют деготь, то на их основе по лучают дегтебетон. Материал, приготовленный путем смешения битума с ми неральным порошком, принято называть асфальтовяжущим веществом. При введении в асфальтовяжущее вещество песка получают асфальтовый раствор (песчаный асфальтобетон).
Асфальтобетон в зависимости от вязкости битума и температуры смесей при укладке подразделяют на горячий, теплый и холодный (рис. 10.1).
Горячий асфальтобетон приготавливают на вязких битумах. Смесь укла дывают при температуре не ниже 100—120°С, формирование структуры бето на в основном заканчивается в период уплотнения.
Теплый асфальтобетон приготавливают на битумах пониженной вязкости и жидких. Смесь укладывают при 40—80°С; скорость формирования структу ры бетона в зависимости от битума и погодных условий может колебаться от нескольких часов до нескольких недель..
Холодный асфальтобетон приготавливают на жидких битумах. Смесь укладывают при температуре, соответствующей температуре окружающего воздуха (но не ниже 10°С); формирование структуры бетона протекает мед ленно (20—40 сут) в зависимости от скорости загустевания битума, погод ных условий и интенсивности движения автомобилей.
По крупности зерен минерального материала асфальтобетон подразделя ют на: крупнозернистый — наибольший размер зерен до 40 мм; среднезер нистый— до 25—20 мм, мелкозернистый — до 15—10 мм; песчаный — до 5 мм.
По структуре (плотности) асфальтобетон может быть: плотный, который характеризуется микропористой структурой минеральной части и остаточной пористостью от 3 до 5% объема; пористый, минеральная часть которого характеризуется крупнопористой структурой с остаточной пористостью от 5 до 10% объема.
В зависимости от содержания в асфальтобетоне (асфальтовом растворе) щебня или песка формируется макроили мезоструктура (по аналогии с гор ными породами) с базальной, поровой или контактной цементацией.
В асфальтобетоне с базальной структурой зерна крупного компонента не имеют взаимных контактов, они погружены в растворную часть. Механи ческие свойства бетона обусловливаются преимущественно свойствами асфальтового раствора. Дальнейшее насыщение асфальтобетона структуро образующими компонентами приводит к контактированию зерен через тон кие прослойки вяжущего, формируется поровая структура, при которой обра зуется плотный каркас из зерен, способный воспринять значительные внеш ние усилия. В этом случае объем асфальтового раствора соответствует объе му пустот в щебеночном остове. Дальнейшее увеличение содержания щебня приводит к формированию контактной структуры, в которой объем пустот в щебеночном остове превышает объем асфальтового раствора.
Тип асфальтобетона принимают в зависимости от характера движения автомобилей, конструкции дорожной одежды, наличия строительных мате риалов, климатических условий района строительства и условий производ ства работ.
Горяний асфальтобетон широко применяется в дорожном и аэродромном строительстве. Покрытия из горячего асфальтобетона наиболее устойчивы к воздействию автомобилей и атмосферных факторов. Все это обусловливает ся вязкостью битума. Горячий асфальтобетон применяют для строительства верхних и нижних слоев покрытия практически во всех климатических райо нах страны.
Теплый асфальтобетон обладает меньшей прочностью и водостойкостью, чем горячий, но большей трещиностойкостью. Это определяет его применение в холодном климате.
Теплые асфальтобетонные смеси удобоукладываемы при пониженных температурах, что позволяет успешно применять их для устройства дорож ных покрытий при пониженных температурах воздуха (до —10°С) в умерен ном климате.
Холодный асфальтобетон ме-нее устойчив к действию автомобилей и атмо сферным факторам, чем горячий и теплый асфальтобетоны. Отличительная особенность холодных асфальтобетонных смесей — способность длительное время оставаться рыхлыми, что Цозволяет заготавливать смесь впрок (до 8 мес). Этот материал применяют для покрытий на дорогах с малой интен сивностью движения и особенно широко для ремонта асфальтобетонных по крытий.
Крупнозернистый асфальтобетон применяют только для устройства ниж него слоя покрытия, шероховатая и пористая поверхность которого обеспечи вает хорошее сцепление с верхним слоем.
Среднезернистый и мелкозернистый асфальтобетоны поровой структуры применяют для устройства верхнего, слоя покрытия на участках с большими продольными уклонами при тяжелом и интенсивном движении. Покрытия из этих типов асфальтобетона обладают повышенной шероховатостью, что обеспечивает хорошее сцепление с автомобильными шинами. Мелкозернис тый асфальтобетон базальной структуры применяют для устройства верхнего слоя двухслойных покрытий при интенсивном движении с дополнительным втапливанием щебня для создания шероховатой поверхности. Асфальтобе тон этого типа обладает достаточно высокой сопротивляемостью механи ческим воздействиям и атмосферным факторам.
Песчаный асфальтобетон поровой структуры, приготовленный на дробле ном песке с большим содержанием зерен 5—1,25 мм, применяют для устрой ства верхнего слоя покрытия на дорогах со средней интенсивностью движения и на участках, где требуется создание водонепроницаемого слоя. Песчаный асфальтобетон базальной структуры на природном песке с малым содержани ем зерен 5—1,25 мм обладает меньшей сопротивляемостью усилиям, возни-
Типы |
Горячий |
Теплый |
|
Холодный |
||
(ГЯб) |
(ТДБ) |
|
(ХНб) |
|
||
асфальтобетонов |
|
|
||||
Марка |
БНД БНД БНД БНД БНД СГ |
|
СГ |
мг |
||
битумов |
90/60 |
60/90 90/130 130/200200/300130/200 |
70/130 |
70/130 |
||
Дорожные |
|
|
Вязкие |
Жидкие |
|
|
битумы |
|
|
|
|
|
|
Рис. 10.1. Типы асфальтобетонов по вязкости битумов
кающим при движении транспортных средств, чем перечисленные выше типы асфальтобетонов, поэтому его применяют для устройства покрытий на авто мобильных дорогах с легким движением, а также для полов в цехах промыш ленных предприятий, тротуаров, отмосток.
10.2. МАТЕРИАЛЫ ДЛЯ АСФАЛЬТОБЕТОНА
Выбор материалов и технические требования к ним обусловлены их ролью в асфальтобетоне, типом асфальтобетона и его назначением в дорожной
одежде.
Щебень. Для приготовления щебня используют прочные морозостойкие магматические, метаморфические и осадочные горные породы, а также проч ные и морозостойкие медленноохлажденные металлургические шлаки. Проч ность при сжатии горных пород должна быть не менее 100—120 МПа, а осадочных карбонатных пород и металлургических шлаков — не менее 80— 100 МПа. Несколько пониженные требования к прочности известняков, доло митов и шлаков компенсируются повышенной прочностью асфальтобетона в связи с хорошим прилипанием битума к этим материалам. Для нижнего слоя асфальтобетонного покрытия можно применять щебень из горных пород и металлургических шлаков прочностью не менее 60 МПа. Показатель проч ности при износе в полочном барабане для щебня из горных пород установ лен не более 25—35%, а из шлаков не более 35%. Щебень для асфальтобетон ных смесей должен быть чистым, 'не допускается содержание глинистых и пылеватых частиц свыше 2%. Форма зерен щебня должна приближаться к тетраэдрной и кубовидной, а поверхность к шероховатой, что повышает внутреннее трение и прилипание вяжущего. Содержание лешадных и иглова тых зерен ограничивается io—25%. Щебень для асфальтобетонных смесей должен выдерживать без разрушения не менее 50 циклов попеременного замораживания и оттаивания, а для нижнего слоя покрытия — не менее
25циклов.
Для приготовления асфальтобетонных смесей применяют дробленый
гравий с количеством дробленых зерен не менее 80% [< нему предъявляют те же требования, что и к шебню из скальных горных пород.
Песок. Для приготовления асфальтобетонных смесей применяют природ ные и дробленые пески (высевки). Наиболее широко используют природный кварцевый песок, состоящий из окатанных зерен кварца.
Песок должен быть чистым и содержать пылевдХо-глинистых частиц не более 3% по массе.
Дробленый песок получают дроблением скальных горных пород или кристаллических металлургических шлаков. В завцвИМ0С,рИ QX прочности исходной горной породы дробленый песок делят на две марКИ g00 и 400.
Для первого из них применяют горные породы с прочностью при сжатии не ниже 80, для второго — не ниже 40 МПа.
Гранулометрическим состав песка должен обеспечивать получение смеси с другими минеральными материалами, с наибольшей плотностью. Из этих соображении для приготовления асфальтобетона приIVJ^^^юх крупно- и сред незернистые пески (табл. 10.1).
Минеральный нороиюк. Для асфальтобетонных ^Ме^вй минеральный по рошок получают размолом известняков, доломитов (прочностью не ме нее 20 МПа), доменных шлаков, а также битуминозные цзвесхняков Тонкость помола порошков должна быть такой, чтобы при мокр0м рассеве сквозь сит0
с отверстиями 1,25 мм |
проходило 100/6, 0,315 Мм_не |
менее QQO/ |
и 0,071 мм - не менее 70% порошка. При этом пустотИ()сть erQ |
н£ |
|
НИИ в специальной форме |
нагрузкой 40 МПа должна быть не g0J]ee 350^ |
Физико-химическое взаимодейст вие битума с минеральным порошком приближенно определяют коэффици ентом гидрофильности частиц порош ка размером менее 1,25 мм. Коэффи циентом гидрофильности называют отношение набухания минерального порошка в воде (полярная среда) к набуханию в обезвоженном керосине (неполярная среда). Более гидро
фильные порошки имеют большее сродство с водой и характеризуются коэф фициентом гидрофильности более 1, а менее гидрофильные — менее 1. Для асфальтобетона не рекомендуют порошки с коэффициентом гидрофильности более 1.
Характеристика минеральных порошков, отражающая их взаимодейст вие с водой, — степень набухания в воде смеси порошка с битумом. По техни ческим требованиям на минеральный порошок для асфальтобетона набуха ние смеси порошка с битумом не должно превышать 2,5%.
Карбонатные горные породы, используемые для производства минераль ных порошков, не должны содержать глинистых примесей более 5%.
В ряде случаев в качестве минеральных порошков применяют местные материалы — порошкообразные отходы промышленности (пыль уноса цементных заводов, золы, дефекационные отходы сахарных заводов, отходы асбоцементного производства). Качество этих порошков различное, поэтому в каждом случае проверяют свойства порошков и приготовленных смесей. Важно установить также расход битума, технологические свойства смеси на принятом порошке и влияние порошка на долговечность асфальтобетона.
Вследствие того, что минеральные порошки имеют тонкозернистый состав, они обладают повышенной гигроскопичностью и комкуются при длительном хранении на складах. Обладая большой поверхностной энергией, они интен сивно реагируют с битумом, быстро изменяют его вязкость, что несколько затрудняет процессы перемешивания и в особенности уплотнения смесей. Значительно улучшаются свойства минеральных порошков после предвари тельной гидрофобизации, т. е. обработки небольшими дозами битума малой вязкости или другими гидрофобизирующими веществами (торфяным или древесным дегтем, ферролигносульфонатом и др.). Гидрофобизированные порошки при хранении не комкуются, при транспортировании не распыливаются, значительно улучшают перемешивание и уплотнение смесей; расход битума при приготовлении асфальтобетонных смесей уменьшается.
Прогрессивным способом улучшения качества минерального порошка является разработанная Л. Б. Гезенцвеем активация поверхности зерен би тумом с поверхностно-активными добавками в процессе помола, при которой совмещается физико-химическая обработка с механическими воздействиями.
Битумы. Марку вязкого битума, а также класс и марку жидкого битума выбирают в зависимости от вида асфальтобетона, климатических условий района строительства и категории дороги, а для холодного асфальтобетона с учетом условий и сроков хранения смеси на складе. В исключительных
случаях при отсутствии вязких битумов марок БНД 130/200, БНД 200/300 или жидких битумов они могут быть приготовлены на асфальтобетонном заводе смешением вязкого битума с разжижителем. Выбор разжижителя зависит от вида и типа асфальтобетона, качества минеральных составляю щих, условий строительства и эксплуатации дорожных покрытий. Ориентиро вочное Количество разжижителя для получения битумов требуемой марки
приведено в табл. 10.2.
|
|
Количество разжижителя для получения битума |
|
|
|
заданной вязкости, % массы |
|
Требуемая марка битума |
Марка исходного битума |
Топливо для реактивных дви Дизельное топливо Л, ДЗ, |
|
|
|
||
|
|
гателей (Т-1, РТ), дизельное |
ДА, ДС, зеленое масло |
|
|
топливо А и 3, керосин |
|
БНД 200/300 |
БНД 60/90 |
4—7 |
5—8 |
БНД 130/200 |
БНД 90/130 |
3—5 |
4—7 |
БНД 60/90 |
4—6 |
4—6 |
|
СГ 130/200 |
БНД 90/130 |
3—4 |
3 - 5 |
БНД 40/60 |
14— 18 |
— |
|
|
БНД 60/90 |
12— 16 |
— |
СГ 70/130 |
БНД 40/60 |
16—20 |
— |
МГ 130/200 |
БНД 60/90 |
14— 17 |
— |
БНД 40/60 |
— |
17—23 |
|
МГ 70/130 |
БНД 60/90 |
— |
14—18 |
БНД 40/60 |
— |
19—25 |
|
|
БНД 60/90 |
|
16—20 |
Поверхностно-активные вещества. В технологии производства асфальто бетона находят применение поверхностно-активные вещества (ПАВ). Добав ки таких веществ улучшают сцепление битума с минеральным материалом, увеличивают степень обволакивания битумом минеральных частиц, сокра щают время перемешивания, улучшают удобоукладываемость и уплотняемость смесей.
Применяемые в асфальтобетоне ПАВ разделяются на ионогенные и не ионогенные. Ионогенные ПАВ, в свою очередь, подразделяются на два типа: катионактивные и анионактивные. Характерными представителями катионактивных ПАВ являются соли высших первичных, вторичных и третичных алифатических аминов и четырехзамещенные аммониевые основания: БП-3 (высшие алифатические амины, продукт на основе полиэтиленполиамина и синтетических жирных кислот); алифатические амины С17—С21 (продукт процесса гидрирующего алинирования жирных кислот); октадециламин (продукт гидрирования стеарина) и др.
Характерными представителями анионактивных ПАВ являются высшие карбоновые кислоты, соли (мыла) тяжелых и щелочно-земельных метал лов высших карбоновых кислот. Наибольшее применение нашли следующие продукты: кубовые остатки синтетических жирных кислот (побочный про дукт, вырабатываемый заводами жирозаменителей); второй жировой гудрон (побочный продукт мыловаренного производства); госсиполовая смола (хлопковый гудрон); окисленный петролатум; каменноугольная смола.
Эффективным неионогенным ПАВ является камид — продукт на основе моноэтаноламина и кубовых кйслот, образующихся при дистилляции синтети ческих жирных кислот. Рекомендуемый предел концентрации ПАВ при вве дении в битум: для катионактивных 0,5—1,5% от массы битума; для анион активных 3—5%; для неионогенных азотосодержащих* 1—2%.
10.3.РАСПРЕДЕЛЕНИЕ БИТУМА В АСФАЛЬТОБЕТОНЕ
ИЕГО ВЗАИМОДЕЙСТВИЕ С МИНЕРАЛЬНЫМИ МАТЕРИАЛАМИ
Процесс приготовления асфальтобетонной смеси рассчитан на равномер ное распределение вяжущего и полное покрытие каждого минерального зер на пленкой битума.
Равномерное распределение битума в асфальтобетоне решающим обра зом влияет на прочность, устойчивость и долговечность покрытия. В случае неполного покрытия минеральных зерен битумной пленкой из-за недостатка битума асфальтобетон разрушается во влажной среде вследствие проника ния воды через открытые места на зернах под битумную пленку и вытеснения ее с поверхности. Избыток битума ухудшает равномерность распределения вяжущего в асфальтобетоне за счет миграции части битума при уплотнении смеси из зон повышенного напряжения в зоны малого напряжения и др.
Допустим, что зерна в асфальтобетонной смеси приближаются по своей форме к правильной. Их удельную поверхность можно выразить в следующем виде:
где К — коэффициент формы зерен |
(для шара — 6, |
для |
куба — 8,5, |
|
для тетраэдра — 14,7); Л — линейный |
размер зерна, м; |
ум—плотность |
||
минерального материала. |
|
|
материалов, |
|
В табл. 10.3 |
приведены удельные поверхности Некоторых |
|||
применяемых для |
приготовления асфальтобетонных смесей. |
|
Общая поверхность минеральной части асфальтобетона складывается из поверхностей минерального порошка, песка и щебня:
|
S |
см |
=S |
+ S S |
|
Если принять1 |
|
|
пор 1 |
П И |
|
асфальтобетон, содержащий 40% щебня, 40 дробленого |
|||||
песка, 10 природного кварцевого |
песка |
и 10% известнякового порошка, |
то общая поверхность будет равна 49 м2/кг. На долю минерального порошка приходится 80%, дробленого песка 15, природного песка 3,7 и на долю щебня 0,3% от общей поверхности минеральной части. Следовательно, на порошок, который составляет лишь 10% от общей массы, приходится 80% поверхности, в то время как щебень составляет 40, а его поверхность лишь 0,3%.
Распределение битума в асфальтобетоне взаимосвязано с удельной поверхностью минеральных зерен следующей зависимостью:
б аБ
где б — толщина битумной пленки на минеральных зернах, мкм; а — пере
водной |
коэффициент; |
Б — количество |
битума, % от массы минеральной |
||||||||
части; |
S — удельная |
поверхность зерен минерального |
материала, |
м2/кг; |
|||||||
уб — плотность битума. |
|
|
|
|
|
|
|
||||
|
|
|
|
|
|
|
|
|
|
Т а б л и ц а 10.3 |
|
|
|
Удельная площадь поверхности, м2/кг |
|
Удельная площадь поверхности, м2/кг |
|||||||
Размеры |
Извест |
Дио |
Гра |
Кварце |
Размеры |
Извест |
■Дио |
Гра |
Кварце |
||
частиц, мм |
частиц, мм |
||||||||||
|
|
няк |
рит |
|
нит |
вый песок |
|
няк |
рит |
нит |
вый песок |
<0,071 |
470,0 |
286,5 |
290,0 |
190,0 |
1,25-3 |
3,6 |
3,6 |
3,7 |
2,5 |
||
0,071—0,14 |
116,1 |
107,0 |
67,0 |
40,0 |
3 - 5 |
1,45 |
1,4 |
1,7 |
1 |
||
0,14—0,315 |
22,1 |
21,9 |
28,0 |
12,0 |
5 -10 |
0,73 |
0,71 |
0,74 |
— |
||
0,315—0,63 |
10,3 |
10,5 |
14.0 |
8,0 |
10-15 |
0,44 |
0,42 |
0,44 |
— |
||
0,63—1,25 |
5,5 |
5,5 |
|
6,5 |
5,8 |
|
|
|
|
|
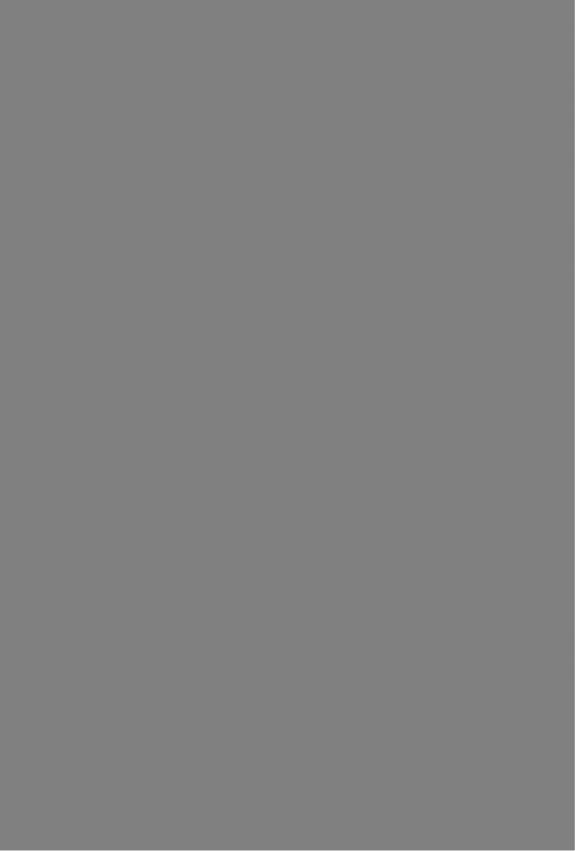
ГруНПОной состли оитума, %
Битум на номеру пости минерального .черна |
|
|
|
|
|
Асфал ьтеш>1 |
Смолы |
|
Масла |
Объемный битум |
6,95 |
38,85 |
\ |
54.20 |
Битум из ориентированного слоя |
10,59 |
42,47 |
46,94 |
Физическое взаимодействие битума с минеральными материалами
обусловлено способностью вяжущего адсорбироваться на поверхности мине ральных зерен. В результате формируются адсорбционные слои (слои повы шенной концентрации высокомолекулярных составляющих битума). Наряду с адсорбционным взаимодействием на границе битум — минеральный мате риал проявляют свое действие межмолекулярные силы минерального мате риала. Это дальнодействующие поверхностные силы, действие которых рас пространяется на несколько сотен и даже тысяч ангстрем. Битум, попадая в зону их действия, претерпевает структурные изменения. Высокомолекуляр ные соединения битума, проявляя «эстафетное действие» (впервые открытое
Б.В. Дерягиным для других систем), образуют цепочки, перпендикулярные
кповерхности минеральных зерен. Наибольшая прочность звеньев цепочки у поверхности зерен (ориентированный слой битума). По мере удаления от зерна прочность связи падает, вяжущее приобретает свойства объемного (свободного) битума.
Вориентированном слое битума выделяют три зоны с характерными структурой и физико-механическими свойствами: твердообразную, структури рованную, диффузионную. Твердообразная зона, граничащая с поверх ностью минерального материала, представляет адсорбционный слой, предель но насыщенный асфальтенами. Минеральные зерна, покрытые пленкой, меж ду собой не слипаются, так как пленка нс обладает клеящей способностью. Толщина твердообразной зоны на минеральных зернах не превышает долей микрометра. Структурированная зона состоит из упорядоченно расположен ных высокомолекулярных компонентов битума, ориентированных к минераль ному зерну. Толщина зоны не превышает 1—2 мкм. Диффузная зона пред ставлена слабым упорядочением высокомолекулярной части битума, перехо
дящей в объемный битум. Резкого перехода меж |
ориентированным слоем |
и объемным битумом, а также внутри слоя межд\ |
-.омами нет. В зависимости |
от природы и размера зерен, а также от содержания в битуме, асфальтенов величина ориентированного слоя может меняться от долей микрометра до нескольких микрометров (3—6 мкм). По мере приближения к поверхности минеральных материалов в связанном слое увеличивается содержание асфальтенов (табл. 10.5). Следовательно, при полном переводе битума в'асфальтобетоне из объемного в ориентированное состояние достигается наибольшая прочность системы. Поэтому асфальтовяжущее, в котором тол щина пленки менее 1 мкм, обладает значительно большей прочностью, чем асфальтовый раствор и тем более асфальтобетон. Необходимо стремиться к тому, чтобы отдельные минеральные зерна соприкасались между собой по
слою ориентированного битума.
Химическое взаимодействие битума с минеральным материалом приводит к образованию на границе раздела фаз новых химических соединений. Хемоадсорбционные процессы возникают при объединении минеральных материа лов из карбонатных и основных горных пород с битумами, содержащими анионоактивные поверхностно-активные вещества (нафтеновые, асфальтогеновые кислоты и т. д.). Между известняком и битумом, содержащим, на-
пример, асфальтогеновые кислоты, происходит реакция с образованием каль циевых мыл:
СаС03+ 2RCOOH-+Ca (RCOO) 2+ Н2С03.
Так как это соединение нерастворимо в воде, битумные пленки, образован ные на поверхности минеральных частиц, устойчивы к действию воды.
При объединении битума с кислыми минеральными материалами, богаты ми кремнеземом, хемосорбционные соединения не образуются. Прочность сцепления битумной пленки с поверхностью минеральных частиц понижен ная, особенно в присутствии воды, так как обусловлена лишь физической адсорбцией. Для образования химических соединений на границе битум — минеральный материал из кислых горных пород (гранит, песчаник) в битум вводят катионоактивные ПАВ. Только в этом случае возможно образование химических соединений:
Si02+ RNH2^ N H 30 2.
Катионактивные ПАВ улучшают прилипание битума не только к породам, богатым кремнеземом, но и к карбонатным. В известняке, например, всегда имеются примеси кремнезема, которые создают отрицательно заряженные центры на поверхности частиц. Взаимодействие катионактивного ПАВ с известняком идет по этим центрам.
Фильтрация битума и его компонентов внутрь минеральных зерен зависит главным образом от их пористости. По макропорам внутрь зерен фильтрует ся объемный битум. Наличие микропор на поверхности зерен приводит к изби рательной диффузии компонентов битума, заключающейся в следующем. Наиболее подвижный компонент битума — масла проникают по капиллярам внутрь зерен на наибольшую глубину. Смолы из-за меньшей подвижности и большей активности проникают на меньшую глубину в зерна. Поверхност ный слой битума на таких зернах обогащен асфальтенами. Взаимодействие пористых материалов с битумом приводит к тому, что битумные пленки стано вятся более жесткими и менее эластичными, а это ускоряет переход асфальто бетона в хрупкое состояние. При применении таких минеральных материалов вязкость битума должна быть меньше на 10—15%, чем битумов, применяе мых в асфальтобетонах, минеральная часть которых состоит из плотных материалов.
§ 10.4. СТРУКТУРА АСФАЛЬТОБЕТОНА
Свойства строительных материалов определяются их вещественным со ставом, состоянием и структурой. Структура материалов является наиболее важным и наиболее общим их признаком. Аналогично тому, как для хими ческого вещества важнейшее значение имеет его молекулярное строение, так для строительных материалов очень важным признаком является его структу ра, определяемая количеством и качеством минеральных составляющих, их взаимным расположением и характером связей между ними.
Впервые представления о взаимосвязи структуры и свойств асфальтобето на были изложены П. В. Сахаровым. Он считал, что многообразие свойств асфальтобетона зависит от его структуры, которая является функцией свойств частей, их относительных масс в единице объема готового материала, равномерности распределения, правильности и тщательности производст венных процессов. П. В. Сахаров предложил рассматривать асфальтобетон как материал, состоящий из двух частей — минерального остова и асфальто вяжущего вещества, состоящего из битума и минерального порошка.
Более поздние исследования, выполненные под руководством М. И. Волко ва, показали, что структуру асфальтобетона методологически целесообраз нее рассматривать как трехкомпонентную систему, состоящую из микро-, мезо- и макроструктур. Микроструктура — это структура асфальтовяжуще го вещества, мезоструктура — асфальтового раствора (песок + асфальто
вяжущее вещество), макроструктура — асфальтобетона (щебень + асфаль товый раствор).
Микроструктура асфальтобетона отражает количественное соотношение, расположение и взаимодействие битума и наиболее дисперсной и активной составляющей асфальтобетона — минерального порошка. Прочность микро структуры резко изменяется в зависимости от содержания минерального по рошка (рис. 10.2). На начальном участке / кривой изменение прочности прямо пропорционально количеству вводимого минерального порошка. В этом случае минеральные частицы с образующимися в них ориентирован ными слоями битума не взаимодействуют между собой, формируется базаль ная структура асфальтовяжущего вещества. Увеличение прочности объясня ется ростом гидродинамического сопротивления движению. С увеличением содержания минерального порошка (участок II) расстояние между отдель ными частицами становится меньше, чем сумма толщин структурированных оболочек двух соседних частиц, и свойства системы обусловливаются сте пенью взаимодействия ориентированных слоев. Это приводит к формирова нию поровой структуры материала. Высокая прочность асфальтовяжущего вещества в точке экстремума объясняется тем, что битумная пленка на зер нах толщиной 0,23—0,25 мкм полностью находится в ориентированном со стоянии под действием поверхностных сил минеральных зерен. Точка экстре мума соответствует и максимальной величине объемной массы.
При увеличении количества минерального порошка выше оптимального предела в системе увеличивается число пор, битума не хватает для обволаки вания минеральных зерен, появляются контакты по твердой поверхности (контактная структура). Все это приводит к резкому снижению прочности
(участок III).
Оптимальное количество битума взаимосвязано с его вязкостью. Так, для
битума БНД 90/130 оно составляет |
|
||||||||
16%, а для БНД 200/300 -14,5% . |
|
||||||||
Различие в оптимальном количестве би |
|
||||||||
тума объясняется прежде всего строе |
|
||||||||
нием его пленок. В высоковязких биту |
|
||||||||
мах толщина пленки на зернах всегда |
|
||||||||
больше, чем 3 менее вязких битумах. |
|
||||||||
Следовательно, |
в |
асфальтовяжущем |
|
||||||
оптимальной структуры битум и поро |
|
||||||||
шок находятся в наилучшем соотноше |
|
||||||||
нии. |
Нарушение |
этого |
соотношения |
|
|||||
приводит к снижению прочности и объ |
|
||||||||
емной |
массы |
асфальтовяжущего ве |
|
||||||
щества. |
|
|
которая |
в |
значи |
|
|||
Мезоструктуру, |
|
||||||||
тельной степени определяет прочность, |
|
||||||||
деформативность, |
плотность |
и |
другие |
|
|||||
свойства |
асфальтобетона, |
формируют |
|
||||||
зерна песка, содержащиеся в асфальто |
Рис. 10.2. Зависимость' прочности при |
||||||||
вяжущем |
вешестве. |
При |
введении |
||||||
в асфальтовя>Нущее вещество песка за |
сжатии асфальтовяжущего от содер |
||||||||
жания минерального порошка |
|||||||||
кономерно снижается |
прочность систе- |
|
мы, что в первую очередь связано с повышением неоднородности смеси и по явлением в системе объемного битума (рис. 10.3). Влияние вязкости исходно го битума на прочность уменьшается с ростом содержания в системе песча ных частиц. Прослеживается четкая зависимость отношения битума к мине ральному порошку (Б/П) от вязкости битума.
Макроструктура формируется щебнем, который рассматривается как основной структурообразующий элемент, мелко-, средне- и крупнозернистых асфальтобетонов. В песчаном асфальтобетоне макроструктура формируется зернами 5—1,25 мм. Макроструктура асфальтобетона определяется количест венным соотношением, взаимным расположением, крупностью зерен щебня, связанных в монолит асфальтовым раствором, а также характером процес сов взаимодействия на границе раздела фаз: поверхность минерального мате
риала — битум.
Структурообразующая роль щебня так же, как и песка, значительно отли чается от роли минерального порошка. Его основное назначение заключается в формировании пространственного Каркаса, обеспечивающего прочность асфальтобетона.
При незначительном содержании щебня свойства асфальтобетона опреде ляются свойствами асфальтового раствора, поскольку зерна щебня являются отдельными вкраплениями, «плавающими» в растворной части. Зерна щебня в этом случае разделены толстыми прослойками раствора и являются
|
|
|
|
|
|
|
|
|
своего |
рода |
инертным |
заполнителем; |
||||||
|
|
|
|
|
|
|
|
|
размер, |
свойства |
поверхности, |
форма |
||||||
|
|
|
|
|
|
|
|
|
зерен щебня не оказывают в этом слу |
|||||||||
|
|
|
|
|
|
|
|
|
чае существенного влияния на свойства |
|||||||||
|
|
|
|
|
|
|
|
|
асфальтобетона. Больше того, в неко |
|||||||||
|
|
|
|
|
|
|
|
|
торых случаях введение 10—20% щебня |
|||||||||
|
|
|
|
|
|
|
|
|
может привести к снижению прочности |
|||||||||
|
|
|
|
|
|
|
|
|
асфальтобетона по сравнению с проч |
|||||||||
|
|
|
|
|
|
|
|
|
ностью асфальтового раствора за счет |
|||||||||
|
|
|
|
|
|
|
|
|
снижения |
однородности |
|
системы |
||||||
|
|
|
|
|
|
|
|
|
(рис. |
10.4). |
|
|
|
|
|
|
||
Рис. 10.3. Изменение прочности при |
Дальнейший рост содержаний щеб |
|||||||||||||||||
сжатии |
асфальтового |
раствора |
при |
ня приводит |
к возникновению |
отдель |
||||||||||||
увеличении содержания |
песка (10;35 |
ных контактов между зернами через |
||||||||||||||||
|
|
и 50%): |
|
|
|
|
||||||||||||
/ — битум БНД 40/60; 2 - |
БНД 90/130; 3 - |
БНД |
тонкие пленки ориентированного биту |
|||||||||||||||
|
130/200; 4 - |
БНД 200/300 |
|
|
ма. Прочность битумных слоев настоль |
|||||||||||||
|
|
|
|
|
|
|
|
|
ко велика, что битум под нагрузкой |
|||||||||
|
|
|
|
|
|
|
|
|
практически |
не |
вытесняется. |
Однако |
||||||
|
|
|
|
|
|
|
|
|
если нагрузки при уплотнении весьма |
|||||||||
|
|
|
|
|
|
|
|
|
велики, то возможно разрушение зерен |
|||||||||
|
|
|
|
|
|
|
|
|
в зонах контакта от сосредоточенных |
|||||||||
|
|
|
|
|
|
|
|
|
контактных |
напряжений. |
При |
этом |
||||||
|
|
|
|
|
|
|
|
|
разрушается и битумная пленка, возни |
|||||||||
|
|
|
|
|
|
|
|
|
кают прямые контакты по минеральным |
|||||||||
|
|
|
|
|
|
|
|
|
зернам, что приводит к образованию |
|||||||||
. |
10 |
Z0 |
30 |
00 |
50 |
60 |
70 |
конденсационных связей. Порог форми |
||||||||||
рования |
конденсационных |
связей в |
||||||||||||||||
Содержание щебня франции 15-5 |
|
|||||||||||||||||
|
|
|
М М . °/п |
|
|
|
асфальтобетоне наступает при содержа |
|||||||||||
Рис. Ю.4. Зависимость прочности при |
|
нии |
щебня более |
45%. |
При |
увеличе |
||||||||||||
|
нии щебня до 60—65% в асфальтобето |
|||||||||||||||||
сжатии асфальтобетона от содержания |
|
|||||||||||||||||
|
|
щебня: |
|
|
|
|
не формируется пространственный кар |
|||||||||||
/-б и т у м |
БНД |
БНД 200/300 |
|
130/200; |
3 |
|
кас. |
Крупные |
минеральные |
|
зерна |
|||||||
40/60; |
2 |
БНД |
|
|
|
|
|
|
|
|
|
|
||||||
|
|
|
|
|
|
|
|
|
контактируют друг с другом |
непосред- |
ственно или через настолько тон |
|
|
|
|||
кие прослойки битума, что вяжу |
|
|
|
|||
щее в них приобретает свойства |
|
|
|
|||
твердого тела. Межзерновые пус |
|
|
|
|||
тоты упругого |
минерального кар |
|
|
|
||
каса заполнены асфальтовым рас |
|
|
|
|||
твором. |
Это |
поровая |
структура |
|
|
|
асфальтобетона. |
|
|
|
|
||
Дальнейшее увеличение коли |
|
|
|
|||
чества щебня приводит к формиро |
|
|
|
|||
ванию контактной структуры, в ко |
|
|
|
|||
торой объем пустот в щебеночном |
|
|
|
|||
каркасе |
значительно |
превышает |
|
|
|
|
объем асфальтового раствора, со |
Рис. 10.5. |
Взаимосвязь |
структур в асфаль |
|||
здает материал с большой порис |
|
тобетоне |
||||
тостью и пониженной прочностью. |
|
Получение |
асфальтобетона |
|||
Взаимосвязь структур в асфальтобетоне. |
с заданной структурой и свойствами достигается путем установления коли чественных соотношений между микро-, мезо- и макроструктурой и выдержи вания этих соотношений при производстве смесей. При этом необходимо помнить, что данной макроструктуре соответствует только определенные мезо- и микроструктуры (рис. 10.5). Так, наиболее высокие показатели прочности асфальтобетона с базальной макроструктурой (щебня<35%)^ достигаются при контактно-поровой мезоструктуре (песка >40%) и поровой микрострук туре (минерального порошка >15%). Наилучшие показатели асфальтобето на с поровой макроструктурой (щебня 50—60%) достигаются при поровобазальной мезоструктуре (песка 30—40%) и базальной микроструктуре (ми нерального порошка около 10%), а с контактной макроструктурой (щеб ня 65%) при базальной мезоструктуре (песка 30%) и базальной микрострук туре (минерального порошка 5%). Отношение битума к минеральному по рошку в асфальтобетоне с базальной макроструктурой должно быть в преде лах 0,5—0,6 с базально-поровой 0,6—0,9, с поровой и порово-контакт-
ной 0,9—1,1/ Существует зависимость, согласно которой тип структуры асфальтобето
на определяется вязкостью битума. Концентрация минерального порошка в битуме обратно пропорциональна вязкости последнего. Отношение МП:Б
для асфальтобетона, |
приготовленного на битуме СГ 70/130, максимально |
и снижается по мере |
повышения вязкости битума. Такой переход связан |
с недостаточной насыщенностью жидких битумов асфальтенами, при этом зерна минерального порошка являются центрами структурообразования и способствуют упрочнению структуры и ее стабилизации. Переход жидких битумов в структурированное состояние сопровождается возникновением ко агуляционных контактов, а при значительном насыщении битума минераль ным порошком — резким упрочнением системы и формированием вторичной
коагуляционной структуры.
Тип и свойства вяжущего определяют не только микроструктуру асфаль тобетона но и тесно увязываются со свойствами макроструктуры. С уменьше нием вязкости применяемого битума закономерно снижается оптимальное содержание щебня (табл. 10.6) и происходит переход от контактно-поровой макроструктуры к поровой, а затем к базальной. Понижение вязкости битума вызывает необходимость уменьшения содержания макроструктурах элементов и увеличения содержания асфальтового раствора. Асфальтобетон на би туме БНД 40/60 достигает наибольшей прочности при содержании щеб ня 55%, а На битуме БНД 130/200—40%.
Асфальтобетон |
Марка битума |
Оптимальное содержание |
Тип макроструктуры |
||||
щебня, % |
|
||||||
Горячий |
|
БНД 40/60 |
55 |
|
Поровая |
|
|
|
|
БНД 90/130 |
45 |
|
|
|
|
|
|
БНД |
130/200 |
40 |
|
Порово-базальная |
|
Теплый |
|
БНД 200/300 |
35 |
|
Базальная |
||
|
|
СГ 130/200 |
35 |
|
|
|
|
.Холодный |
|
СГ 70/130 |
30 |
|
|
|
|
|
|
|
|
|
|
Т а б л и ц а 10.7 |
|
|
|
Содержание минерального порошка |
|
Содержание минерального порошка |
|||
Предельная круп- |
(зерен<0,071 мм), % |
Предельная круп- |
|
(зерен<0,071 |
мм), % |
||
ность зерен |
в |
|
|
ность зерен в |
|
|
|
смеси, мм |
Горячий^ асфальто- |
Теплый асфальто |
смеси, мм |
'орячий асфальто Теплый асфальто |
|||
|
|
' бётон |
бетон |
|
|
бетон |
бетон |
35 |
|
4 |
5 |
10 |
|
9 |
12 |
25 |
|
6 |
8 |
5 |
|
12 |
15 |
15 |
|
8 |
10 |
3 |
|
14 |
18 |
Взаимосвязь между предельной крупностью зерен смеси, типом асфальто бетона и количеством минерального порошка имеет следующие закономер ности (табл. 10.7). Требуемое количество минерального порошка возрастает с уменьшением предельной крупности зерен. Для приготовления теплых асфальтобетонных смесей необходимо больше минерального порошка, чем для горячих.
Назначение состава асфальтобетона с данной структурой зависит прежде всего от условий работы. Для грузонапряженных участков дорог, участков с уклонами, перекрестками необходим асфальтобетон с удержанием 50— 60% высокопрочного щебня (поровоконтактная структура). Отличительной особенностью этих асфальтобетонов является наличие жесткого минерально го каркаса. При наличии щебня средней прочности необходимо приготавли вать асфальтобетон базальной структуры (щебня 35%). Поскольку проч ность асфальтобетона в этом случае обусловливается свойствами асфальто вого раствора, качество песка и минерального порошка должно быть доста точно высоким.
Приведенные сведения о структурах асфальтобетонов и их выборе не яв ляются исчерпывающими, поскольку эти вопросы чрезвычайно сложны. Однако принятая методология представляет возможность наметить конкрет ные пути создания асфальтобетонов с заданными структурой и свойствами.
§ 10.5. СТРУКТУРНО-МЕХАНИЧЕСКИЕ СВОЙСТВА АСФАЛЬТОБЕТОНА
Асфальтобетон, как материал с обратимыми микроструктурными связя ми, в зависимости от температуры и условий деформирования может нахо диться в следующих структурных состояниях:
упруго-хрупком, при котором минеральный остов строго фиксирован застеклованными прослойками битума. В этом случае асфальтобетон по свойст
вам приближается к цементобетону и другим искусственным материалам с кристаллизационными связями;
упруго-пластинном, когда зерна минерального остова соединены прослой ками битума, которые проявляют при напряжениях, не превышающих предел
текучести, упругие и эластические свойства, а при больших напряжениях — упруго-вязкие свойства;
вязко-пластичном, при котором зерна минерального остова соединены полужидкими прослойками битума и небольшое по величине напряжение приводит к деформированию материала.
Асфальтобетон в дорожном покрытии, кроме воздействия автомобилей, подвергается воздействию атмосферных и талых вод; вода проникает в поры асфальтобетона и ослабляет взаимную связь минеральных материалов с пленкой вяжущего. Поэтому оценку прочности асфальтобетона дают при следующих критических условиях:
максимальной для данной местности температуре асфальтобетонного по крытия, когда когезия вяжущего минимальна;
минимальной температуре, когда прочность достаточна, так как когезия вяжущего достигает наибольших значений, но при нарушении однородности структуры, особенно при повторных замораживаниях, минимальные удлине ния способствуют образованию трещин, а в отдельных случаях и выкрашива нию покрытия;
некоторых средних температурах, когда наиболее вероятно водонасыщение асфальтобетона и снижение прилипания вяжущего к минеральным мате риалам, которые могут привести к быстрому износу и хрупкому разрушению покрытия.
Под механической нагрузкой асфальтобетон проявляет комплекс слож ных свойств: упругость, пластичность, ползучесть, релаксацию напряжений, изменение прочности в зависимости от скорости деформирования, накопле ние деформации при многократных приложениях нагрузки и т. д. В зависи мости от проявления тех или иных свойств к асфальтобетону применимы законы теории упругости или теории пластичности. Свойства асфальтобето на обычно начинают рассматриваться с ведущего показателя механических свойств материала — прочности.
Прочность. Свойство асфальтобетона сопротивляться разрушению под действием механических напряжений характеризует прочность. Прочность указывает границы допустимых напряжений, возникающих в процессе эксплуатации конструкции. Для асфальтобетона как термопластичного мате риала различают два вида потери прочности: в упругой стадии, приводящую к разрушению покрытия; в пластической стадии, приводящую к возникнове нию деформаций, нарушающих нормальную эксплуатацию конструкции. Особенностью разрушения асфальтобетона по сравнению с цементобетоном и другими подобными материалами является резко выраженная зависимость прочности от времени действия нагрузки и температуры.
Разрушение асфальтобетона под действием приложенного напряжения представляет собой кинетический процесс, развивающийся во времени. Чем больше величина действующих напряжений, тем быстрее протекает процесс разрушения. Таким образом, механические свойства асфальтобето на характеризуются двумя показателями; разрушающим напряжением и ве личиной длительной прочности (время, в течение которого асфальтобетон
выдерживает заданное напряжение без разрушения).
Зависимость значений разрушающего напряжения от длительности пребывания материала Я Напряженном состоянии обусловлена процессом
усталости. Усталость характеризует постепенное снижение работоспособ ности асфальтобетона при длительно действующих или многократно повторяющихся нагрузках. Статическая усталость проявляется в сниже нии долговечности материала при многократных циклически действую щих нагрузках. Ее характеризуют числом циклов, которое выдерживает асфальтобетон до разрушения.
Основным требованием, которому должен удовлетворять асфальто бетон, работающий в условиях повышенных положительных температур, является его сдвигоустойчивость. Прочность при сдвиге асфальтобетона при повышенных температурах может быть охарактеризована видоизме ненным уравнением Кулона:
T = Ptg<pa6+ Cc + 26, |
|
|
где т _прочность асфальтобетона при статическом |
сдвиге, |
МПа; |
р__ удельная нормальная нагрузка при сдвиге, МПа; |
фа^ — угол |
внут |
реннего трения асфальтобетона с учетом смазывающего действия битума; Q _зацепление зерен при сдвиге асфальтобетона, МПа; 2 б — сцепление в'асфальтобетоне, содержащем битум в количестве б.
Из уравнения видно, что заданная прочность при сдвиге т может быть получена при различных значениях факторов, определяющих прочность и зависящих в одном случае от свойств минерального остова фаб, Сс, в дру гом — от сил сцепления 2 б, обусловливаемых свойствами битума.
На рис. 10.6 показана последовательность определения сдвиговых параметров: в результате сдвига уплотненного минерального остова тмо вначале определяется его угол внутреннего трения фмо и зацепление Сс, а затем при сдвиге асфальтобетона фаб с точно таким же минеральным остовом определяется сцепление С в асфальтобетоне и по разности С—Сс вычисляется сцепление 2 б.
При больших значениях внутреннего трения и зацепления минераль ного остова заданную прочность на сдвиг можно достичь при относитель но небольшом сцеплении, обусловливаемом высокой вязкостью битума, а также путем применения минеральных материалов с малыми значения ми фаб и Сс. Но свойства минерального материала в диапазоне эксплуата-
аб |
L |
ционных температур |
практически не ме |
||||||
|
|
няются, в то время как свойства битума |
|||||||
|
|
сильно зависят от температуры. Поэтому |
|||||||
|
|
асфальтобетон с высоким значением внут |
|||||||
|
|
реннего трения и зацепления всегда будет |
|||||||
|
|
обладать прочностью на сдвиг при высо |
|||||||
|
|
ких температурах и большой теплостой |
|||||||
|
|
костью. |
|
|
|
|
|
|
|
|
|
В табл.10.8 приведены характеристики |
|||||||
|
|
сдвига |
многощебенистого и |
малощебе |
|||||
|
|
нистого асфальтобетонов. В первом из |
|||||||
|
|
них фаб = 45° |
доли |
внутреннего |
трения, |
||||
|
|
зацепления и сцепления в сопротивлении |
|||||||
|
|
сдвигу равны соответственно 61, 30 и 9%, |
|||||||
|
|
тогда как в малощебенистом угол внут |
|||||||
|
|
реннего трения уменьшается до 32—33%, |
|||||||
|
|
а трение, зацепление и сцепление соот |
|||||||
|
|
ветственно составляют |
55, |
17 |
и |
28%. |
|||
|
|
В многощебенистом |
асфальтобетоне при |
||||||
Рис. 10.6. График для определения |
Р = 0,5 |
МПа |
каркас |
воспринимает |
91% |
||||
сдвиговых |
параметров асфальтобетона |
сдвигающей |
нагрузки и |
только |
9% |
при- |
|
Сопротивление |
Угол |
|
|
|
Сопротивлейне |
|
|
|
|
||
Нор |
сдвигу, МПа |
|
|
Нор |
Угол |
|
|
|
||||
трения в |
|
|
сдвигу, МПа |
|
|
|
||||||
мальное |
|
асфаль |
Зацеп |
Сцеп |
мальное |
|
|
трения в |
Зацеп |
Сцеп |
||
давле |
асфаль |
мине |
|
|
||||||||
тобето |
ление, |
ление, |
давле- |
асфаль |
мине |
асфаль |
ление, |
ление, |
||||
ние, |
тобе |
рального |
не, град |
МПа |
МПа |
ние, |
тобето |
МПа |
МПа |
|||
МПа |
тона |
остова |
|
|
|
МПа |
тобе |
рального |
не, град |
|
|
|
|
|
|
|
тона |
остова |
|
|
|
|
|||
|
|
|
|
|
|
|
|
|
|
|
||
Многощебенистый асфальтобетон (щебня |
Малощебенистый асфальтобетон |
(щебня |
||||||||||
|
65%, минерального порошка 6%) |
|
20%, минерального порошка |
12%) |
||||||||
0 |
0,30 |
0,25 |
43—45 |
0,25 |
|
0 |
0,20 |
0,10 |
32—33 |
0,10 |
|
|
0,2 |
0,54 |
0,47 |
0,25 |
|
0,2 |
0,40 |
0,25 |
0,10 |
|
|||
0,5 |
0,82 |
0,75 |
|
0,25 |
|
0,5 |
0,60 |
0,43 |
|
0,10 |
|
|
0,8 |
1,08 |
1,03 |
|
|
|
0,8 |
0,78 |
0,59 |
|
|
|
|
1,1 |
1,32 |
1,31 |
|
|
|
1,1 |
0,96 |
0,77 |
|
|
|
|
ходится на долю асфальтовяжущего вещества. В малощебенистом асфальто бетоне 72% приходится на каркас и 28% на долю асфальтовяжущего ве щества. При изменении скорости сдвига с 50 до 0,01 мм/мин прочность многощебенистого асфальтобетона уменьшается на 28, малощебени стого на 45%.
Испытание на сдвиг при двух сильно разнящихся скоростях лучше выявляет сдвигоустойчивость асфальтобетона с различным минеральным остовом, чем обычное испытание, и позволяет раскрыть поведение асфаль тобетона в стадии обратимых деформаций, что соответствует реальной работе материала в покрытии, которое не накапливает остаточных дефор маций.
Испытания на сдвиг асфальтобетона с 20 до 65% щебня при цикли ческом приложении нагрузки, выполненные Н. В. Горелышевым, показа ли, что при 50°С, вертикальной нагрузке 0,5 МПа и скорости деформиро
вания 50 |
мм/мин |
многощебенистый асфальтобетон при |
сдвиге работает |
в упругой |
стадии |
до т = 0,4 МПа, а малощебенистый — |
до т = 0,15 МПа. |
Таким образом, о сдвигоустойчивости асфальтобетона при повышенных температурах воздуха объективно можно судить по результатам испытаний с различной скоростью сдвига и при выделении упругой составляющей из об щей деформации. Однако испытания на сдвиг являются еще достаточно громоздкими, поэтому вместо этого испытания сдвигоустойчивость оценива ют непосредственно по прочности при сжатии. Прочность асфальтобетона принято оценивать по испытанию цилиндрических образцов на сжатие при 50, 20 и 0°С и скоро.сти деформирования 3 мм/мин. Наиболее важен показатель прочности при 50°С, по которому судят о поведении асфальтобетонного по крытия под нагрузкой в летнее время. Прочность при сжатии асфальтобетона при этой температуре должна быть не ниже величин, приведенных
в табл. 10.9.
Если при 50°С нормативными документами ограничивается нижний предел прочности (1— 1,2 МПа), то при 0°С ограничивается верхний предел прочности (не более 12 МПа). Показатель прочности при сжатии при 50°С характеризует сдвигоустойчивость асфальтобетона при высокой температуре И сопротивляемость материала образованию пластических деформаций в покрытии. Показатель прочности при 0°С косвенно характеризует трещиностойкость асфальтобетона при низкой температуре.
Для характеристики пластичности асфальтобетона при положительных температурах, когда возможно возникновение деформаций покрытий (вол ны, наплывы), может служить показатель пластичности, впервые получен-
|
Прочность асфальтобетона при сжа |
|
|
Прочность асфальтобетона при сжа |
||
Характер |
тии при 50вС, МПа |
|
|
тии при 50"С, МПа |
||
|
|
Характер |
|
|||
движения |
|
движения |
|
|||
|
малощебени- |
многощебени- |
|
|
малощебени |
многощебени |
|
стого |
стого |
|
|
стого |
стого |
Стоянка |
ав- |
|
Остановка: |
|
||
томобилей |
0,79 |
0,62 |
40 |
тяже |
|
|
4—7 ч |
лых авто |
|
||||
Перегон: |
|
|
мобилей |
1,74 |
||
40 тяже |
|
в час |
2,20 |
|||
лых авто |
|
Перекрестки: |
|
|||
мобилей в |
0,44 |
40 тяже |
|
|||
час |
0,65 |
лых авто |
|
|||
125 тяже |
|
мобилей в |
1,30 |
|||
лых авто |
|
час |
|
1,65 |
||
мобилей в |
0,70 |
125 тяже |
|
|||
час |
0,88 |
лых |
|
авто |
|
|
|
|
|
мобилей в |
1,73 |
||
|
|
|
час |
|
2,20 |
ный Н. Н. Ивановым на основе анализа результатов испытаний на сжатие при разных скоростях деформирования:
#i = /ZL
v 2
где /?! и /?2 — предел прочности при сжатии; vx и v2— скорости дефор мирования (обычно 3 и 30 мм/мин);
R
К =
v\ lg v2
Асфальтобетон считают непластичным, если при 50°С /(<0,10, нормаль ной пластичности при К = 0,154-0,24 и пластичными при /(>0,25.
Прочность асфальтобетона при растяжении определяют непосредствен ным растяжением специально приготовленного и закрепленного образца или более простым «бразильским» методом, не требующим специального приго товления образцов сложной формы. Цилиндрический образец асфальтобето на диаметром D и высотой Н подвергают сжатию по образующей. Прочность при растяжении по этому методу
где а — коэффициент, который для асфальтобетона, как пластичного тела, может быть принят равным единице (для хрупких тел — 0,63); Р — разрушающее усилие, Н; D и Н — диаметр и высота образца, см.
С понижением температуры происходит приращение прочности, что связа но со структурными изменениями в битумной пленке (рис. 10.7). Участок стабилизации прочности асфальтобетона характеризует переход битумной
пленки в хрупкое состояние. Экстре |
|
||||||
мальная точка на графике может быть |
|
||||||
названа температурой хрупкости дан- |
|
||||||
нрго асфальтобетона. В асфальтобетоне |
|
||||||
на битуме БНД 40/60 участок стаби |
|
||||||
лизации |
прочности |
при |
растяжении |
|
|||
достигается при —10°С, а в асфальто |
|
||||||
бетоне на |
БНД |
130/200 |
при |
—20°С. |
|
||
Асфальтобетон с более низкой темпе |
|
||||||
ратурой хрупкости, |
естественно, более |
|
|||||
пластичен |
при |
низких температурах. |
|
||||
Основным |
критерием прочности ас |
|
|||||
фальтобетона |
при отрицательных тем |
|
|||||
пературах являются его деформативные |
Рис. 10.7. Зависимость прочности при из |
||||||
свойства, |
характеризующие |
устойчи |
гибе асфальтобетона от температуры: |
||||
вость против образования трещин. При |
/ - БНД 60/90; 2 - БНД 130/200; 3 - БНД 200/300 |
||||||
охлаждении |
объем |
асфальтобетона |
|
сокращается, в покрытии возникают растягивающие напряжения, которые до известной степени могут компенсироваться его пластичностью. Для пред отвращения образования трещин необходимо, чтобы асфальтобетон обладал способностью деформироваться под действием растягивающих напряжений без нарушения сплошности. Для оценки обычно используют предельную отно сительную деформацию в момент разрушения. Если деформирование чисто упругое, то критическая относительная деформация не превышает 0,001. По мере повышения температуры критическое относительное удлинение увеличивается.
Деформативность асфальтобетона. Ее оценивают по относительной деформации асфальтобетонных образцов при испытании на изгиб или растя жение. Покрытие будет устойчивым против образования трещин, если асфальтобетон обладает относительным удлинением при 0°С не менее 0,004— 0,008, а при —20°С не менее 0,001—0,002 (при скорости деформации, близ
кой к 5—10 мм/мин).
Реологические свойства асфальтобетона. Показатели прочности асфаль тобетона не позволяют полностью характеризовать работу материала в по крытии, так как при нагружении в нем возникают не только обратимые, но и необратимые деформации, величина которых связана с уровнем напряже ния, временем действия напряжения и скоростью деформации. Изучением поведения материалов под действием приложенных нагрузок занимается реология — раздел механики, тесно примыкающий к физике и охватываю щий вопросы деформирования разнообразных материалов от твердых тел до
жидкостей.
Существуют различные подходы к изучению реологии асфальтобетона: теоретические преследуют цель разработки математической модели, описы вающей поведение материала; практические объясняют поведение материа ла при деформировании исходя из особенностей его структуры и состава. Эти подходы позволяют определить упругость, вязкость, пластичность мате
риала, также установить соотношение между ними.
При эксплуатации асфальтобетонного покрытия могут быть следующие режимы нагружения: постоянная нагрузка, равномерно возрастающая на грузка, деформирование с постоянной скоростью. Определение изменения свойств асфальтобетона за длительный период производят испытанием на
ползучесть.
Ползучесть и упруго-вязкие свойства асфальтобетона. Испытание асфаль тобетона на ползучесть позволяет установить изменение деформации во вре-
|
мени. Ползучесть — процесс малой не |
|||||
|
прерывной |
пластической |
деформации, |
|||
|
протекающей в материалах в условиях |
|||||
|
длительной |
статической нагрузки. При |
||||
|
испытании на ползучесть к образцу, |
|||||
|
имеющему форму цилиндра или ба- |
|||||
|
лочки, прикладывают постоянную на |
|||||
|
грузку, чтобы проследить работу мате |
|||||
|
риала в упругой (линейной) и неупру |
|||||
|
гой (нелинейной) области. |
|
||||
|
На рис. 10.8 изображены кривые |
|||||
|
ползучести: кривая 1 характеризует ра |
|||||
|
боту материала в упругой стадии, т. е. |
|||||
Рис. 10.8. Развитие деформаций в асфаль |
деформация |
|
полностью |
обратима |
||
после |
разгрузки; кривая 2 показывает |
|||||
тобетоне при напряжениях: |
налячие |
остаточной |
деформации; |
|||
/ _ 0,010—1.02 разр; 2 — 0,07—0,10 аразр; 3 — |
||||||
0,34-0,45 (/[)ЯЗр |
-кривая роста |
упругих деформаций со |
||||
|
стоит из двух частей; в первой части |
|||||
|
деформации |
|
развиваются |
по |
закону |
|
|
пропорциональности между величиной |
|||||
|
мгновенной упругой деформации и на |
|||||
|
пряжением, во второй части кривая |
|||||
|
деформации |
развивается |
во времени |
|||
|
по |
экспоненциальной |
зависимости. |
|||
|
Мгновенная |
|
упругая деформация, до |
|||
|
стигнув постоянного значения, остается |
|||||
|
постоянной весь период времени дей |
|||||
|
ствия |
нагрузки. "Упругая |
деформация, |
|||
|
развивающаяся во времени при посто |
|||||
|
янно действующем напряжении, растет |
|||||
Рис. 10.9. Зависимость деформации асфаль |
во времени |
|
с уменьшающейся |
скоро |
||
тобетона от времени приложения нагрузки: |
стью, |
асимптотически |
приближаясь |
|||
/-б и т у м БНД 130/200; 2 - битум БНД 40/60 |
к постоянному значению в течение не |
|||||
|
ограниченно большого времени. Горячий асфальтобетон при температуре^ 20°С и напряжениях, не превы
шающих 0,02сгрлзр, работает в упругой |
стадии, при напряжениях |
ДО 0,3ггр:1ф — в упруго-вязкой стадии. В этот |
период в асфальтобетоне на |
капливаются остаточные деформации. |
При напряжениях больше 0,3— |
0,4аразр деформация асфальтобетона возрастает и приводит через 5—10 мин |
|
к разрушению (кривая 3 на рис. 10.8). |
|
Кривые ползучести, построенные в логарифмическом масштабе, дают прямолинейную зависимость деформации от времени приложения нагрузки (рис. 10.9), что позволяет определить степень пластичности асфальтобетона по углу наклона линии к оси времени. Степень пластичности P = tga горячего асфальтобетона при 20°С находится в пределах 0,4—0,6. Чем ниже степень пластичности, тем в большей мере асфальтобетон приближается к упругому телу (Р = О ). Модуль упругости при сжатии цилиндрических образцов по
стоянной нагрузкой |
|
|
Еу = |
оН |
|
|
Sy • |
|
где о — нагрузка, МПа; Н — высота образца; см; |
упругая дефор- |
|
мация образин. |
|
^ F |
При определен и и модуля деформации в формуле вместо упругой деформа ции образца принимают упругую полную деформацию. Для образцов-бало- чек с нагрузкой в середине пролета
Г___ — ____
v 4 8 S V / ’
где / — расстояние между опорами-; Sy — упругий прогиб балочки; / —
момент инерции сечения (для балочки |
b, h — ширина и высота |
образца. |
^ |
Асфальто'вяжущее вещество с оптимально малым содержанием битума обладает наибольшим модулем упругости. Насыщение асфальтовяжущего мелким песком приводит к снижению модуля упругости, а введение в асфаль товый раствор зерен крупнее 1,25 мм — к новым качественным изменениям. Значение модуля упругости возрастает, так как часть'нагрузки воспринима
ется .минеральным |
остовом. |
Наибольшее |
значение модуля упругости |
||
у асфальтобетона |
на битуме |
БНД |
40/60 |
при крупности |
зерен 20 мм, |
а у асфальтобетона |
на битуме БНД |
130/200 при крупности |
10 мм. |
Релаксация напряжений. Релаксация — уменьшение напряжений в мате риале, величина деформации в котором поддерживается постоянной. Процесс релаксации заключается в «перерождении» упругой деформации в пластичную.
Релаксация напряжений в асфальтобетоне связана с наличием битума, обладающего гораздо меньшей прочностью и вязкостью, чем минеральные материалы. Температуры и вязкость битума оказывают влияние на характер релаксации напряжений в асфальтобетоне. С понижением температуры раз личие в релаксационных процессах уменьшается, с повышением — релакса ционная способность материала увеличивается. Напряжения в асфальтобе тоне при постоянной деформации делят па релаксирующие и иерелакенрующие:
п |
(Т;+ а ... |
где а — общие напряжения; |
релаксирующая часть папрм.м пищ |
ак— нерелаксирующая часть напряжений.
Релаксирующая часть напряжений описывается экспоненциальной зави симостью
ст,=--асе Л
где ао— величина релаксирующей шети напряжений в начальны!! мо
мент времени; / — время; k — постоянная.
Релаксирующая часть напряжений взаимосвязана с типом структуры асфальтовой системы. Асфальтовяжущее вещество в меньшей степени релаксирует напряжение, чем асфальтобетон. Это объясняется тем, что на крупных частицах толщина битумной пленки больше, чем на мелких.
На характер релаксации в значительной степени влияет начальное напря жение, сообщаемое материалу. При высоком начальном напряжении процесс релаксации протекает интенсивно, в материале остается мало нсотрелакспрованных напряжений, что объясняется облегчением пластического течения
по релаксационным плоскостям.
Релаксационные процессы в асфальтобетоне зависят от скорости дефор мации, (нагружения). Процесс нагружения рассматривают как совокупность двух одновременно протекающих процессов роста напряжений и их рсдак-
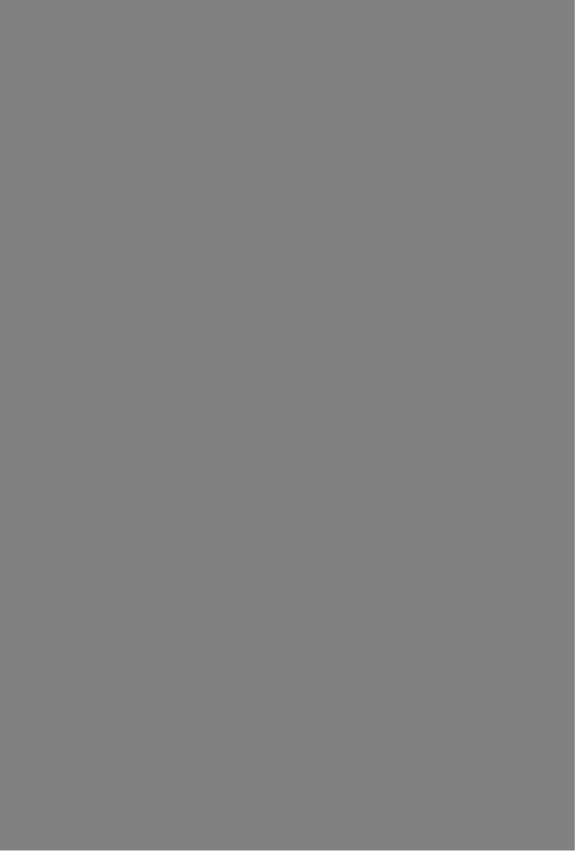
лаксирует напряжения, так как он настолько приближается к упругим телам, что релаксация,^ происходящая за счет вязкого течения, практически отсут ствует. При 50°С доля отрелаксированных напряжений наибольшая, что
вполне закономерно, так как вязкость системы снижается при повышенных температурах.
Водостойкость. Асфальтобетонные покрытия при длительном увлажнении вследствие ослабления структурных связей могут разрушаться за счет выкра шивания минеральных зерен, что приводит к повышенному износу покрытий и образованию выбоин. Водостойкость асфальтобетона зависит от его плот ности и устойчивости адгезионных связей. Вода как полярная жидкость хоро шо смачивает все минеральные материалы, а это значит, что при длительном контакте минеральных зерен, обработанных битумом, возможна диффузия воды под битумную пленку. При этом минеральные материалы с положитель ным потенциалом заряда поверхности (кальцит, доломит, известняк) в боль шей степени препятствуют вытеснению битумной пленки водой, чем материа лы с отрицательным потенциалом поверхности (кварц, гранит, андезит). Образование адсорбционного слоя воды понижает поверхностную энергию твердого тела, а следовательно, и работу по образованию новых поверх ностей при деформации. Сорбированные молекулы воды легко мигрируют по поверхностям, вновь образующимся в деформируемом материале, что при водит к его разрушению.
Вода, проникая |
в микродефекты структуры асфальтобетона, приводит |
к адсорбционному |
понижению прочности материала (эффект Ребиндера) |
за счет снижения поверхностной энергии стенок трещин и ослабления струк турных связей у вершины трещины по мере ее развития. Закономерное сниже ние прочности асфальтобетона с увеличением срока выдерживания материа ла в воде объясняется постепенной диффузией воды внутрь материала и все увеличивающимся расклинивающим действием воды. Значительно разруша ют структуру асфальтобетона его частые попеременные увлажнение и высы хание. Перемещаясь в порах, вода вызывает неравномерное распределение напряжений, что также способствует разрушению.
Пористость оказывает большое влияние на водостойкость асфальтобето на, обычно она составляет 3—7%. Поры в асфальтобетоне могут быть откры тые и замкнутые. С уменьшением размера зерен увеличивается количество
замкнутых, |
недоступных воде пор. |
|
|||||||
На рис. 10.11 приведены данные по |
|
||||||||
изменению |
водонасыщения |
асфальто |
|
||||||
вяжущего вещества, асфальтового рас |
|
||||||||
твора и асфальтобетона за длитель |
|
||||||||
ный период выдерживания в воде. Через |
|
||||||||
300 сут |
образцы |
из |
асфальтовяжуще |
2 |
|||||
го понизили прочность на 30, асфальто |
|||||||||
|
|||||||||
вого раствора на 50 и асфальтобетона |
«з |
||||||||
на 65%. |
С |
повышением |
содержания |
||||||
крупных зерен увеличиваются размеры |
* |
||||||||
«8 2 |
|||||||||
пор, растет число открытых пор, в целом |
|||||||||
повышается неоднородность материала, |
- 2 - |
||||||||
этим и объясняется меньшая водостой |
|
||||||||
кость |
асфальтобетона, чем |
асфальто |
60 |
||||||
вяжущего. |
|
|
|
|
|
Время Выдерживания в Воде, суш |
|||
Водостойкость |
определяется вели |
Рис. 10.11. Изменение водонасыщения во |
|||||||
чиной |
водонасыщения, |
набухания и |
времени (данные В. А. Головко): |
||||||
коэффициентом водостойкости Къ (от |
1 - асфальтовяжушего; 2 - асфальтового раствора; |
||||||||
ношение |
прочности |
водонасыщенных |
3 — асфальтобетона |
||||||
|

стойкости за счет вырывания щебенок из поверхности покрытия.. На покрытии в этом случае образуются оспины.
Износ покрытий из песчаного асфаль тобетона прежде всего взаимосвязан с ха рактером поверхности частиц, поэтому износ асфальтобетона на высевках извер женных горных пород всегда меньше из носа бетона на окатанном кварцевом песке. Истираемость асфальтобетонного покры тия при интенсивном автомобильном дви жении составляет 0,3—1,0 мм в год.
Износостойкость можно определить с помощью прибора ХАДИ. Образец асфаль тобетона диаметром 50 или 70 мм укрепля ют в обойме-держателе прибора. Вслед ствие вращения истирающего круга (ста льного, с наклеенным слоем резины) и
испытуемого образца в противоположные стороны процесс истирания прибли жается к процессам, происходящим в покрытии под действием автомобилей. Потеря определяется по разнице массы образца до и после испытания. Зная потерю массы и объемную массу испытываемого образца, подсчиты вают объем изнашиваемого материала.
Износостойкость асфальтобетона, изготовленного на различных материа лах, приведена на рис. 10.12. Высокую износостойкость имеют асфальтобето ны, в состав которых входит щебень с наименьшей дробимостью при уплотне нии. Износостойкость асфальтобетона, изготовленного на щебне из капилляр но-пористых известняков, повышается вследствие более прочного прилипа ния пленки битума к поверхности материала.
Асфальтобетонные покрытия с ровной, сухой и чистой поверхностью (за исключением покрытий с избытком битума) обеспечивают достаточное сцепление шин автомобиля е поверхностью покрытия. При этом шерохова тость поверхности покрытии не оказывает существенного влияния на сопро тивление скольжению шин. На покрытиях с увлаженной поверхностью степень сопротивления скольжению шин значительно снижается из-за нали чия воды в. зоне контакта шин с покрытием.
Степень сопротивления скольжению оценивается коэффициентом сопро тивления скольжению ср (коэффициент сопротивления), представляющим собой отношение силы сопротивления скольжению к нормальной нагрузке на покрытие в зоне контакта шины с покрытием. Коэффициент сцепления на сухом и мокром асфальтобетонном покрытии имеет следующие значения:
сухая |
Шероховатая поверхность |
сухая |
Гладкая поверхность: |
0,7—0,9 |
0,4—0,6 |
||
мокрая |
0,5—0,7 |
мокрая |
0,3—0,4 |
При коэффициенте сцепления менее 0,4 покрытие становится недопустимо скользким и аварийность на нем резко увеличивается. Коэффициент сцепле ния 0,4—0,5 в большинстве случаев удовлетворяет требованиям безопасно
сти движения.
Повышение коэффициента сцепления достигается за счет применения асфальтобетона поровой и контактно-поровой структуры. Шероховатость обеспечивается при содержании щебня из труднополирующихся пород в ко-
личестве 50—65% в зернистых смесях и 35—55% зерен крупнее 1,25 мм - в песчаных на дробленом песке из труднополирующихся пород, а также уменьшением до возможных пределов содержания минерального порошка (4—ю% в зернистых смесях и 8—14% — в песчаных).
Общие зависимости между шероховатостью, качеством составляющих и составом асфальтобетонных смесей следующие: степень шероховатости покрытия пропорциональна острогранности и собственной шероховатости зерен каменного материала; долговечность шероховатости тем больше, чем труднее шлифуется каменный материал, чем выше вязкость битума; чем больше дробленых зерен в смеси и чем меньше в ней минерального порошка, тем выше шероховатость.
§10.6. НОРМАТИВНЫЕ ТРЕБОВАНИЯ К АСФАЛЬТОБЕТОНУ
ИРАСЧЕТХОСТАВА
Свойства асфальтобетона и асфальтобетонных смесей должны соответ ствовать ГОСТ 9128—76 «Смеси асфальтобетонные дорожные аэродромные и асфальтобетон». Стандарт распространяется на горячие, теплые и холод ные асфальтобетонные смеси, применяемые для устройства покрытий и осно ваний автомобильных дорог, аэродромов, городских улиц и площадей, дорог промышленных предприятий.
Стандартные классификационные признаки асфальтобетона приведены в § 10.1. Имеются типы плотных горячих и теплых асфальтобетонов в зависи мости от содержания щебня и песка: А — 50—65% щебня; Б — 35—50% щебня (гравия); В — 20—35% щебня (гравия); Г — не менее 33% фрак ции 1,25—5 мм в дробленом песке; Д — не менее 14% фракции 1,25—5 мм в природном песке.
Показатели физико-механических свойств и структуры плотных горячих и теплых асфальтобетонов должны соответствовать требованиям, указанным в табл. 10.12.
Расчет состава асфальтобетона заключается в выборе рационального соотношения между составляющими материалами, обеспечивающего опти мальную плотность минерального остова при требуемом количестве битума и получение бетона с заданными техническими свойствами при определенной технологии производства работ.
Широкое распространение получил метод расчета по кривым плотных смесей. Наибольшая прочность асфальтобетона достигается при условии максимальной плотности минерального остова путем расчета гранулометри ческого состава и определения содержания оптимального количества битума и минерального порошка.
Расчет асфальтобетона по кривым плотных смесей ведут на основе зада ния, в котором должно быть указано назначение асфальтобетона и период строительства. Необходимы данные о свойствах и стоимости исходных мате риалов. Расчет состава ведут по этапам: определяют качество исходных мате риалов и оценивают соответствие их свойств установленным требованиям.
Если имеется несколько разновидностей материалов, выбирают лучший из них для конкретных условий работы асфальтобетона: рассчитывают грану лометрический состав минеральной части смеси по принципу минимума пустот; определяют оптимальное количество битума; определяют физико механические свойства рассчитанных смесей; вносят коррективы в получен ные составы смесей. Основным показателем правильности расчета минераль ной части является получение смеси с минимумом пустот. Как показали исследования В. В. Охотина и Н. Н. Иванова, между плотностью и грануло-
метрическим составом смеси имеется определенная зависимость. Оптималь ными будут составы минеральных смесей, содержащие зерна различного размера, диаметры которых уменьшаются в 2 раза:
d1 d2 |
d 3 |
2 , |
||
d2 |
d3 |
~d7 |
||
|
||||
где d j — наибольший |
диаметр |
зерна минеральной смеси, устанавливае |
мый в зависимости от типа асфальтобетона; d m— наименьший диаметр зер
на, соответствующий пылеватой фракции |
минерального порошка (обычно |
0,004—0,005 ММ). |
Т а б л и ц а 10.12 |
Нормы для асфальтобетонов марок |
|
Показатели |
III |
II |
Пористость мине рального остова, % по объему, для ас фальтобетонов типов:
А и Б
В и Г
Д
Остаточная порис тость, % по объему Водонасыщение, % по объему, для ас фальтобетонов типов:
А
Б и Г В и Д
Набухание, % по
объему, не более Предел прочности
при сжатии, Па, не менее, при температу
рах:
20° для асфальто бетонов всех ти
пов
50°С для асфаль тобетонов типов:
А
Б и В
Г
Д
0°С ДЛЯ горячих
смесей всех типов, не
более
Коэффициент водо стойкости, не менее То же при длитель ном водонасыщении,
не менее Сцепление битума
с минеральной частью асфальтобетонной
смеси
15—19 |
|
15-19 |
|
15—19 |
15—19 |
18-22 |
|
18-22 |
|
18—22 |
18—22 |
|
|
|
|
Не бс^ее 22 |
Не более 22 |
2,5—4,5 |
|
2,5—4,5 |
|
2,5—4,5/3,0—5,0 |
2,5—4,5/3,0—5,0 |
2,0—4,5 |
3,5 |
2,0-4,5 |
3,5 |
1,5-3,5/1,5-4,0 |
1,5-3,5/1,5—4,0 |
1 .5 - |
1 .5 - |
||||
1 .5 - |
3,0 |
1 .5 - |
3,0 |
1,0—3,0/1,5—4,0 |
1,0—3,0/1,5—4,0 |
0,5 |
|
1,0 |
|
1,0 |
1,5 |
|
|
|
24 • 105/20 • 101 |
22 • |
105/ 18 • 101 |
20 • 10*/18 • 101 |
16 • 105/14 • 105 |
|
9 • 105/8 • Ю5 |
8 • |
105/7 • 105 |
9 • Ю5/8 • Ю5 |
8 • 105/6 • Ю5 |
|
10 • Ю5/9 • Ю5 |
9 • 1078 • 105 |
|
|||
14 • 105/10 • 105 |
12 • 1079 • Ю5 |
10 • 105/8 • Ю5 |
8 • 105/6 • Ю5 |
||
|
12 • |
105/9 • Ю5 |
|||
120 • Ю5 |
120 • Ю5 |
120 • 105 |
'120 • 105 |
||
0,7/0,6 |
|||||
|
|
0,8/0,7 |
|||
0,9 |
|
0,85 |
|||
|
|
|
|
||
0,85/0,80 |
0,75/0,60 |
0,70/0,60 |
0,60/0,50 |
||
|
|
|
|
Выдерживает
„еннемследует придерживатьсяинжни*пределовводснасм-
Размеры зерен согласно предыдущему уравнению
do— I do— |
29 ; d т |
2т~ 1 |
\ g d { — \gm |
|
|
откуда т ■ |
\g2 |
+ |
|
Число фракций п на единицу меньше числа размеров т
|
\ % d |
1g d m |
|
|
п " |
lg 2 |
|
Соотношение соседних фракций по массе |
|||
у± |
=, у± |
= уа . |
у±__=08 |
У\ |
У2 |
Уъ"'У п - \ |
Величина, которая показывает, во сколько раз количество последующей фракции меньше предыдущей, называется коэффициентом сбега К. При коэф фициенте сбега 0,8 смесь получается с наибольшей плотностью. Однако вследствие того, что рассчитать минеральную смесь на материалах по коэф фициенту сбега 0,8 трудно, Н. Н. Иванов предложил принимать коэффициент сбега в пределах от 0,7 до 0,9, при которых смеси и получаются достаточно плотные. Зная размеры фракций,, их количество и принятый коэффициент сбега (например, АГ= 0,7), составляют уравнения такого вида:
Фракции
ё\
ё?
ё*
ёп
Массовое количество
У\
II
Уз = УзК=У1К2
уп = У п -хК-УхК*
Сумма всех фракций (по массе) равна 100%, т. е.
У\ +У\К+У\К2 + У\К3 + . |
'+У\Кп '=100, |
или |
|
у,(1+/С + /С2 + /(3 + . |
. + / Г - 1) =100. |
В скобках указана сумма геометрической прогрессии и, следовательно, количество первой фракции в смеси
Аналогично определяем процентное содержание первой фракции у { для коэффициента сбега /( = 0,9. Зная количество первой фракции у ь легко опре делить у2, Уз и т. д.
На основании полученных данных можно построить предельные кривые, соответствующие выбранным коэффициентам сбега (рис. 10.13). Кривые с коэффициентом сбега меньше 0,7 относят к составам минеральной части асфальтобетонной смеси с незначительным содержанием минерального по рошка. Составы, рассчитанные по коэффициенту сбега 0,9, содержат повы-
286
d) |
|
|
|
|
|
i юо80 |
Щ 2» |
* |
д |
|
|
§ |
щ |
ш |
|
||
|
Щ к ш . |
|
|||
К 4 |
|
|
|
|
|
*5 |
|
г ' |
|
|
|
fS 20 |
|
|
1 |
Ш щ |
|
|
|
|
|
|
|
i |
|
|
|
|
|
3 |
|
1,25 |
0,63 |
0,315 |
0,10 0,071 |
Размер зерен минерального матери |
|||||
|
|
ала. мм |
|
|
|
Рис. Ю. 13. Зерновые составы: |
|
|
|
|
|
а — мелкозернистой смеси с непрерывной гранулометрией; б — минеральной част |
горячих и тепл |
|
|
шенное количество минерального порошка. Кривая гранулометрического состава конкретной рассчитываемой смеси должна располагаться между предельными кривыми.
Высокие эксплуатационные показатели дают смеси с повышенным содер жанием щебня и уменьшенным содержанием минерального порошка. Поэто му нормативные документы рекомендуют составы, вписывающиеся между предельными кривыми с коэффициентами сбега 0,65—0,80, при этом пори стость минерального остова должна соответствовать установленным требо
ваниям (ГОСТ 9128—76).
В случае невозможности расчета плотной минеральной смеси по предель ным кривым (при отсутствии крупнозернистых песков и невозможности обогащения мелких песков высевками) необходимая плотность может быть
подобрана по принципу прерывистой гранулометрии.
Как показали исследования Союздорнии, прерывистая грануломет рия приводит к получению жесткого каркаса за счет меньшей раздвижки крупных зерен более мелкими. Асфальтобетонные смеси с прерывистой грану лометрией более сдвигоустойчивы, чем смеси с непрерывным гранулометри
ческим составом.
Составы минеральной части асфальтобетонной смеси с прерывистой гра нулометрией, в которой отсутствует фракция 5—0,63 мм, приведены
в ГОСТ 9128—76.
При использовании материалов, различающихся между собой по плот ности на величину более 0,2 г/см3, необходимо вносить поправки в соотноше
ния минеральных компонентов, |
увеличивая |
количество |
более тяжелых |
и уменьшая количество более |
легких на |
частное |
у, |
от деления —, |
|||
|
|
|
^Yo |
где у0—плотность минеральных материалов, количество которых преооладает в смеси; у, — плотность минерального материала, отличающаяся от у0
на 0,20 г/см3 и более.
На следующем этапе расчета асфальтобетона определяют оптимальное содержание битума. Существует несколько методов определения содержания битума в асфальтобетоне, но наиболее широко применяется метод, основан ный на расчете количества битума по пустотности минерального остова и за
данной пористости асфальтобетона.
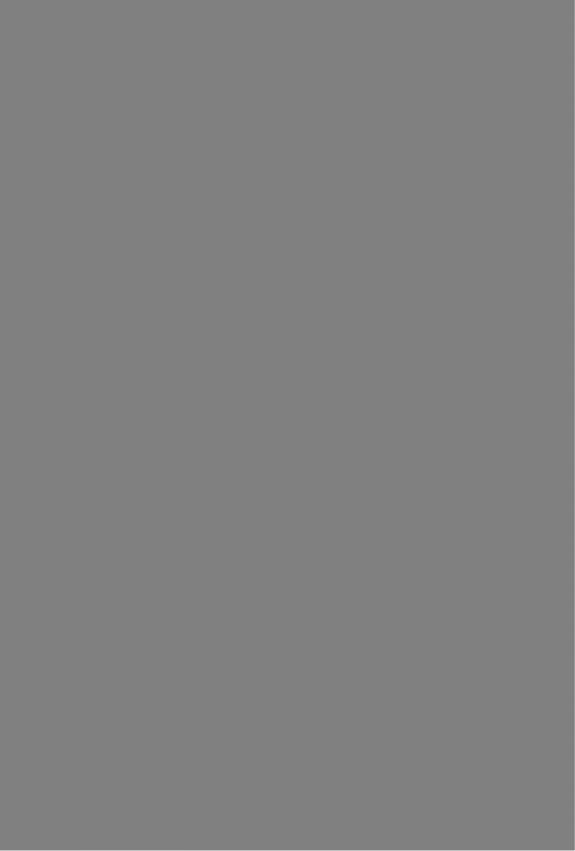
%; Pi— содержание фракции i в частях от целого; Б, — битумоемкость фракции %.
Вводят заданное количество третьей фракции (0,14—0,315 мм) и опреде ляют ее битумоемкость. Так, введением последующих фракций в смесь опре деляют битумоемкость всех фракций, входящих в состав асфальтобетонной смеси.
Так как битумоемкость является постоянной для данного минерального материала, то при применении материалов, у которых битумоемкость извест на, можно пользоваться данными, приведенными в табл. 10.13 (битум БНД 90/130). Тогда расчет сводится к определению удельной битумоемкости
каждой фракции, вычисляемой как произведение Б, на |
л оптимального |
||
содержания битума в смеси: |
|
|
|
|
Б = К2 Б'Р,. |
|
|
|
|
i = 1 |
(при БНД 60/90— |
где К — коэффициент, зависящий от марки битума |
|||
1,05; БНД 90/130—1,00; |
БНД |
130/200-0,95; БНД 200/300-0,90); Б ,— |
|
битумоемкость фракции /, |
%; |
Р ,— содержание фракции в смеси в частях |
|
от целого. |
|
|
|
На оптимальное содержание битума влияет шероховатость зерен, степень запыленности, содержание глинистых включений, активность минерального материала и битума, пустотность смеси. Поэтому оптимальное содержание битума может отклоняться от расчетного на ±5%.
Как показали испытания, для расчетного материала можно принимать битумоемкость, имеющуюся для материалов, близких по свойствам. При этом ошибка в расчете будет незначительной.
Пример. Требуется рассчитать оптимальное количество битума в мелкозернистом асфальто бетоне, приготовленном на гранитном щебне и высевках, кварцевом песке и известняковом по рошке. Минеральная часть, подобранная по предельным кривым, имеет следующий грануломет рический состав (табл. 10.14).
Зная битумоемкость каждой фракции принятых материалов (см. табл. 10.13) и количество фракций в смеси, определяют содержание битума. Для этого величину частных остатков в частях от целого умножают на битумоемкость каждой фракции материала и произведения складывают. Например, для определения удельной битумоемкости 0,332 частей гранитного щебня фрации 15— 5 мм указанную величину умножают на битумоемкость (4,3%) и получают 1,42%. Для других фракций и материалов поступают аналогично. Запись удобно производить по форме, приведен
ной в табл. |
10.15. |
|
|
|
|
|
|
|
|
Т а б л и ц а 10.13 |
|
Размеры |
Порошок, высев |
Порошок, высев |
Природный квар |
Порошок, высев |
Доломи |
ки, щебень из мел ки, щебень из плот |
цевый песок |
ки, щебень из |
товая пыль |
||
фракций, |
козернистого |
ного извест |
и гравий |
песчаника |
обожженная |
мм |
гранита |
няка |
|
|
|
<0,071 |
18,0 |
16,0 |
14,0 |
14,0 |
22,5 |
0,071—0,14 |
8,4 |
9,4 |
7,0 |
9,3 |
16,0 |
0,14—0,28 |
7,4 |
7,3 |
6,1 |
8,5 |
15,6 |
0,28-0,63 |
6,4 |
7,0 |
4,8 |
5,8 |
15,2 |
0,63—1,25 |
5,9 |
6,0 |
4,6 |
5,4 |
14,25 |
1,25—2,5 |
5,7 |
5,3 |
3,8 |
5,2 |
13,5 |
2,5 - 5 |
5,6 |
4,6 |
3,3 |
5,0 |
— |
5 -10 |
5,2 |
3,2 |
— |
4,8 |
— |
10-15 |
4,7 |
3,0 |
— |
4,5 |
— |
15-25 |
4,5 |
2,9 |
— |
4,0 |
— |
25-40 |
4,2 |
2,5 |
|
|
|
|
|
|
|
|
|
Размеры отверстий, си! мм |
|
|
|
|||
Материал |
|
|
тах, % |
5 |
3 |
1,25 |
0,63 |
0,28 |
0,14 |
0,071 |
<0,071 |
|
|
|
|
||||||||||
Гранитные |
|
Частные |
3 3 ,2 |
9 ,6 |
9 ,9 |
7,1 |
1 1 ,5 |
0,3 |
0 ,8 |
|
2 ,6 |
|
щебень и вы- |
|
3 3 ,2 |
4 2 ,8 |
5 2 ,7 |
5 9 ,8 |
7 1 ,3 |
|
|
|
— |
||
севки |
|
Полные |
7 1 ,6 |
7 2 ,4 |
|
|||||||
|
|
|
|
|
|
|
|
|
|
|
||
Кварцевый |
|
Частные |
_ |
_ |
— |
— |
— |
9 ,0 |
4 ,2 |
|
1,8 |
|
песок |
|
Полные |
— |
— |
— |
— |
— |
9 ,0 |
1 3 ,2 |
|
|
|
Известняко |
Частные |
_ |
_ |
_ |
_ |
— |
1,1 |
1,3 |
|
7 ,6 |
||
вый порошок |
|
Полные |
— |
— |
— |
— |
— |
1,1 |
2 ,4 |
|
— |
|
Сумма полных |
|
|
|
|
|
|
|
|
|
|
||
остатков |
|
|
|
3 3 ,2 |
4 2 ,8 |
5 2 ,7 |
5 9 ,8 |
7 1 ,3 |
8 1 ,7 |
8 7 ,8 |
|
|
|
|
|
|
|
|
|
||||||
|
|
|
|
|
|
1 |
|
|
|
|
|
|
|
|
|
|
|
|
|
|
|
Т а б л и ц а |
10.15 |
||
Размеры |
|
Частные остатки в частях от целого |
|
|
Битумоемкость |
|
Удельная |
би- |
||||
Гранитный |
Кварцевый |
Известняко |
|
Кварцевый |
Известняко |
тумоемкость |
||||||
фракций, мм |
Гранит |
фракций; % |
||||||||||
|
материал |
песок |
вый порошок |
песок |
|
вый порошок |
|
|
|
|||
15—5 |
|
0,332 |
|
|
|
4,3 |
_ |
|
3,2 |
|
1,42 |
|
5—3 |
|
0,096 |
___ |
— |
|
5,6 |
3,3 |
|
4,6 |
|
0,54 |
|
3— 1,25 |
|
0,099 |
___ |
— |
|
5,7 |
3,8 |
|
5,3 |
0,56 |
|
|
1,25—0,63 |
|
0,071 |
— |
— |
|
5,9 |
4,6 |
|
6,0 |
0,42 |
|
|
0,63—0,315 |
|
0,115 |
— |
— |
|
6,4 |
4,8 |
|
7,0 |
0,73 |
|
|
0,315—0,16 |
|
0,003 |
0,090 |
0,011 |
|
7,4 |
6,1 |
|
7,3 |
0,2 + 0.55 +0,08 |
||
0,16—0,071 |
|
0,008 |
0,042 |
0,013 |
|
8,4 |
7,0 |
|
9,4 |
0,067 + 0,29 + |
||
|
|
|
+ 0.12 |
|
||||||||
0,071 |
|
0,360- |
0,013 |
0,073 |
|
18,0 |
14,0 |
|
16,6 |
|
||
|
|
|
0,65 + 0,18 + |
|||||||||
|
|
|
|
|
|
|
|
|
|
М |
+ 1,17 |
|
|
|
|
|
|
|
|
|
|
|
II р> 00 |
||
|
|
|
|
|
|
|
|
|
|
|
|
о |
Таким образом определяют, что расчетное содержание битума марки БНД 90/130 в асфаль тобетоне составляет 6,8% от массы минеральной части. При определении количества битума другой марки в этой смеси необходимо полученное содержание умножить на соответствующий коэффициент К.
Асфальтобетон с рассчитанным количеством битума обладает следующими свойствами: прочность при сжатии при 50°С 1,3 МПа, при + 20°С 4 МПа; водонасыщение 1,2%; набуха ние 0,1%; коэффициент водоустойчивости 0,95.
§ 10.7. ТЕОРЕТИЧЕСКИЕ ПОЛОЖЕНИЯ ТЕХНОЛОГИИ АСФАЛЬТОБЕТОНА
Технология совокупность методов обрзботки, изготовления, изменения
свойств исходных материалов, применяемых в процессе производства для по лучения готовой продукции.
Технология — наука о способах воздействия на сырье и материаль соответствующими орудиями производства^
Технология асфальтобетона — совокупность методов подготовки щебня песка, минерального порошка и битума, их смешения, укладки и уплотнения до заданной плотности. Цель технологии асфальтобетона - полу4ние мате
своГт,Сам Г СВ°”ства“”- «ь™ запроектированы, т. е. с заданным',
Поставленная цель может быть достигнута при целенаправленном струк-
турообразовании асфальтобетона, определяемом следующими технологи ческими периодами:
подготовительный — выбор и подготовка компонентов и определение их соотношения в составе смеси (рассмотрен в предыдущем параграфе);
первый — активное структурообразование, которое протекает в момент объединения битума с минеральным материалом. В асфальтобетонной смеси формируются микроструктурные связи;
второй — сближение структурных компонентов асфальтобетонной смеси
при ее укладке и уплотнении. В асфальтобетоне формируется макро структура;
третий — стабилизация структуры и свойств асфальтобетона в покрытии под движением автомобилей. Этот период продолжает технологический про
цесс и в значительной степени определяет надежность асфальтобетонного покрытия.
Каждый период структурообразования влияет на комплекс свойств систе мы. Однако, принимая какое-либо решение, следует учитывать не только прямое, но и обратное влияние проектируемых свойств материала на выбор того или иного технологического параметра. Следовательно, чтобы получить материал с заданными свойствами, необходимо прогнозировать поведение сложной системы, управлять технологией.
Первый период технологического процесса охватывает подогрев материа ла до заданной температуры, дозирование, смешение компонентов и транс портирование смеси к месту укладки. В этот период основная задача техноло гии заключается в разрушении первичных конденсационных контактов меж ду частицами, равномерном распределении всех компонентов в смеси и обво лакивании минеральных зерен битумом. Нормальное протекание процесса структурообразования обусловливается прежде всего хорошим смачиванием битумом минерального материала.
Ухудшает смачивание наличие на поверхности минерального материала воды, адсорбируемой из воздуха, водной пленки вследствие плохого просу шивания минерального материала, загрязнения пылью зерен щебня. Улуч шение смачивания битумом минерального материала достигается предвари тельной обработкой его углеводородной жидкостью или активацией.
Смачивание минеральных материалов битумом в какой-то степени являет ся первым актдм физического и химического взаимодействия битума с поверх ностью минеральных материалов. Хорошее смачивание минеральных мате риалов — необходимое условие для получения материала с заданными свойствами, но недостаточное. Смачивание лишь обеспечивает полное обво лакивание минеральных зерен битумом, в результате чего формируется ориентированный слой битума и происходит химическое взаимодействие би
тума с минеральным материалом (см. § 10.3).
При транспортировании смеси происходит дальнейшее распределение битума в асфальтобетонной смеси, а при длительной перевозке возможно рас слоение. В этом случае необходимо подбирать смесь, устойчивую к дезинтег рации, или обычную смесь перевозить в автомобилях-мешалках.
Во второй период, который охватывает укладку и уплотнение асфальто бетонной смеси, происходит дальнейшее формирование микроструктурных связей и вследствие приложения нагрузки сближение зерен до максималь
ной плотности.
При приложении нагрузки или в результате действия собственной массы в асфальтобетонной смеси начинают происходить прежде всего структурные деформации заключающиеся во взаимном перемещении зерен. Они приво дят к уменьшению занимаемого материалом объема без деформации частиц
|
|
и всегда предшествуют упруго-пласти |
|||
|
|
ческим деформациям. При этом макро |
|||
|
|
частицы асфальтобетонной смеси пере |
|||
|
|
ходят в более устойчивое положение |
|||
|
|
равновесия с более прочной связью |
|||
|
|
между ними. Доля структурных дефор |
|||
|
|
маций1 уменьшается по мере уплотне |
|||
|
|
ния всей системы, а доля упругих дефор |
|||
|
|
маций возрастает (рис. 10.14). |
|||
|
|
При |
сближении частиц |
происходят |
|
|
|
прежде |
всего |
физические |
процессы |
Рис. 10.14. Типы деформаций при |
в пленке битума, приводящие к выжи |
||||
уплотнении |
асфальтобетонной смеси: |
манию ее из зон повышенного напряже |
|||
/ — упругие; |
2 — структурные; 3 — эластичные |
ния. Свободный битум заполняет меж |
|||
|
|
зерновое |
пространство, на |
частицах |
|
|
|
остается |
пленка |
ориентированного би |
тума, при этом коагуляционные связи в асфальтобетоне упрочняются, проч ность всей системы возрастает. В асфальтобетоне с содержанием щебня более 50% при уплотнении жестко-барабанными тяжелыми катками проис ходит частичное вырождение коагуляционных контактов в конденсационные. Ориентированный слой битума не выдавливается, а продавливается с раз рушением контактной зоны зерен щебня. Во избежание этого необходимо уплотнять асфальтобетонные смеси катками на пневматических шинах или
вибрационными.
Прочность и долговечность асфальтобетона, уплотненного до проектной плотности при сравнительно невысоких температурах, как правило, выше, чем асфальтобетона с той же плотностью, но уплотненного при высокой тем пературе. Это связано с тем, что с понижением температуры увеличивается величина ориентированного слоя битума за счет уменьшения объемного би тума на минеральных частицах. Этот битум при уплотнении почти не переме щается в межзерновое пространство. Контактные напряжения на соприка сающихся частицах релаксируются пленкой битума, минеральные зерна мало дробятся, прочность системы под действием атмосферных реагентов и нагруз ки мало изменяется.
Уплотняемость связана с природой минерального материала и битума. Так, уплотняемость асфальтобетона на известняковом материале лучше, чем на материалах из песчаника. На частицах песчаника битум располагается неравномерно и толщина пленки меняется от долей микрометра до десятков микрометров. В то же время на известняковых частицах пленка имеет одина ковую толщину. Кроме того, на зернах известняка пленка битума имеет более выраженное адсорбционно-диффузное строение. У поверхности минеральной частицы больше высокомолекулярных соединений (асфальтенов), на перифе рии больше масел, которые способствуют уплотняемости смеси. Уплотняе мость асфальтобетонных смесей связана с формой частиц. Природный ока танный песок улучшает уплотняемость смеси. Объемный битум заполняет межзерновое пространство. На частицах остается пленка ориентирован ного битума, обладающего значительно большей вязкостью, чем объемный; при этом коагуляционные связи в асфальтобетонной смеси упрочняются и прочность всей системы возрастает.
При уплотнении битумная пленка выполняет роль смазки, снижающей внутреннее тренйе в сыпучем материале; при этом работа, необходимая для уплотнения смеси, уменьшается. С увеличением содержания битума в смеси
1 Структурные деформации связаны с изменением структуры и свойств материала.
работа, |
затраченная |
на |
уплотнение, |
|
|
|
|||||
естественно уменьшается, а при умень |
|
|
|
||||||||
шении содержания, наоборот, возраста |
|
|
|
||||||||
ет. Этим и можно объяснить, что литой |
|
|
|
||||||||
асфальтобетон, |
содержащий битум и |
|
|
|
|||||||
асфальтовяжущее вещество в избытке, |
|
|
|
||||||||
уплотняется при минимуме затрат ра |
|
|
|
||||||||
боты, |
а |
холодные |
асфальтобетонные |
|
|
|
|||||
смеси — при максимуме |
(рис. |
10.15). |
|
|
|
||||||
|
Регулирование |
процессов уплотне |
|
|
|
||||||
ния возможно за счет изменения темпе |
|
|
|
||||||||
ратуры асфальтобетонной смеси. С по |
|
|
|
||||||||
вышением температуры смеси снижает |
|
|
|
||||||||
ся |
энергоемкость уплотнения. Однако |
|
|
|
|||||||
в |
случае |
недостаточной |
когезионной |
|
|
|
|||||
прочности |
при |
высокой |
температуре |
|
|
|
|||||
смеси способность ее к уплотнению по |
|
|
|
||||||||
нижается. При этом минеральные зерна |
|
|
|
||||||||
под действием |
нагрузки |
будут |
сбли |
Рис. 10.15. Схема изменения работы |
|||||||
жаться |
до предельно возможного рас |
уплотнения |
асфальтобетонной |
смеси |
|||||||
стояния, но после снятия нагрузки |
различной подвижности: |
|
|||||||||
/ — жесткая; |
2 — пластичная; 3 — очень |
плас |
|||||||||
частицы вследствие возникающих в них |
|
тичная; 4 — литая |
|
||||||||
упругих |
деформаций, |
а |
также |
рас |
|
|
|
клинивающего действия битумной пленки будут отталкиваться друг от друга, в результате чего система будет разуплотняться. Очевидно, клеящая способ ность битума при данной температуре недостаточна для фиксации минераль ных частиц в период их сближения. На практике это приводит к образованию волосных трещин после прохода катка.
Третий период характеризуется дальнейшим формированием структуры асфальтобетона под движением автомобилей, при котором происходит доуплотнение покрытия в результате увеличения вязкости битума за счет внут ренних необратимых процессов и упрочнения связей на границе раздела ми неральный материал — вяжущее; происходит дальнейшая стабилизация ориентированного слоя битума или появление новообразований в зоне кон такта. В зависимости от условий среды, а также свойств минерального мате риала и битума эти процессы проходят одновременно или возможно преобла дание одного из них. Так, в асфальтобетоне на известняковом щебне вязкость вяжущего за счет окисления последнего изменяется незначительно. Мине ральный материал из кислых горных пород не вызывает активной сорбции вяжущего, которое, находясь в свободном состоянии, будет интенсивно изме
няться под влиянием атмосферных факторов.
Если правильно выбраны составы смесей, все режимы технологических процессов выдержаны, то асфальтобетон в покрытии под воздействием авто мобилей лишь упрочняется1 Если же на каком-либо этапе допущено отклоне ние от заданного режима, то в этот заключительный период происходит раз упрочнение структуры асфальтобетона. Наиболее распространенным отступ
лением является недоуплотнение.
Массовые разрушения асфальтобетона в начальный период эксплуата
ции связаны с малой водо- и мооозостойкостью пористого асфальтобетона.
Даже малое недоуплотнение асфальтобетонной смеси, приготовленной на гидрофильных минеральных материалах, приводит к резкому снижению
водо- и морозостойкости.
1 В частности, этим отличается асфальтобетон от цементобетона.
Если правильно рассчитаны составы асфальтобетонных смесей и конст рукция дорожной одежды соответствует движущемуся транспорту, то про должительность третьего периода — периода эксплуатации асфальтобетон ного покрытия превышает 30 лет. Падение устойчивости материала объясня ется только необратимыми изменениями, происходящими в битумной пленке на зернах минерального материала.
§ 10.8. ТЕХНОЛОГИЯ ПРОИЗВОДСТВА АСФАЛЬТОБЕТОНА
Направленное структурообразование в технологическом процессе обеспе чивается созданием оптимальных условий для формирования асфальтобето на. Эти условия определяются технологическими свойствами асфальтобетон ных смесей, выбором соответствующего технологического оборудования и заданными режимами его работы.
Свойства асфальтобетонной смеси. Для получения плотного, прочного асфальтобетона необходимо затратить определенную работу при укладке, разравнивании и уплотнении смеси. 'Асфальтобетонные смеси подразделяют на литые, пластичные и жесткие.
Литые смеси обладают значительной подвижностью; при укладке их раз равнивают ручным валком и заглаживают.
Пластинные смеси обладают сравнительно невысокой подвижностью частиц и уплотняют их катками. Необходимая плотность достигается при уплотнении в процессе устройства покрытия.
Жесткие смеси обладают повышенным внутренним трением и малой под вижностью. К ним можно отнести горячие асфальтобетонные смеси с повы шенным содержанием щебня (50—65%) и холодные смеси.
Необходимая подвижность асфальтобетонной смеси, приготовляемой на вязких битумах, достигается в основном за счет повышения температуры, снижающей вязкость битума, а смесей, применяемых без подогрева, — использованием жидких битумов или битумных эмульсий.
Подвижность и рыхлость асфальтобетонной смеси зависит от ее структу ры, количества битума и качества минерального порошка. Зернистые смеси с применением дробленых минеральных материалов имеют меньшую подвиж ность, чем смеси с применением гравия и природного песка. Смеси с повышен ным содержанием минерального порошка обладают большей жесткостью; непросушенный минеральный порошок понижает подвижность смеси. Избы ток битума понижает рыхлость смеси; такая смесь слеживается при перевоз ке, растекается по кузову автомобиля-самосвала и с трудом выгружается. Образующиеся плотные комья трудно рыхлить и укладывать в покрытие.
На подвижность асфальтобетонной смеси оказывают влияние характер и качество перемешивания в смесителях; при этом смеси, приготовленные в лопастных мешалках, более удобообрабатываемые, чем смеси, приготов ленные в мешалках со свободным перемешиванием.
Введение в смесь некоторых поверхностно-активных добавок, пластифи цирующих битум, увеличивает ее подвижность. Степень подвижностц асфаль тобетонных смесей может быть оценена по методу И. А. Рыбьева, который основан на определении усилия или времени, затрачиваемого на преодоление сил сцепления и трения смеси при движении металлического конуса. Показа телем подвижности (удобообрабатываемости) является усилие, необходи мое для извлечения конуса из смеси, или время в секундах для той же цели. Величины показателя удобообрабатываемости приведены в табл. 10.16.
Показателем удобообрабатываемости является также уплотняемость смесей и покрытий под действием катков и других уплотняющих средств.
2 9 4
|
Вид асфальтобетонной смеси |
Показатели удобоукладываемости |
|
|
н |
с |
|
|
|
||
Литая |
|
0,25-0,32 |
12,5—16,0 |
Подвижная песчаная |
0,15—0,25 |
7,5-12,5 |
|
« |
мелкозернистая |
0,20—0,25 |
10,0—12,5 |
« |
среднезернистая |
0,22—0,30 |
11,0-15,0 |
Жесткая |
(при виброуплотнении) |
0,15 |
7,5 |
Уплотняемость смесей. Этот показатель зависит в основном от тех же фак торов внутреннего трения и сцепления, что и подвижность. Однако имеется и некоторое различие. Так, подвижность и рыхлость смеси понижаются с из бытком битума, в то же время увеличение содержания битума на 10—15% выше оптимального улучшает уплотняемость смесей. В значительной мере на прочность и устойчивость асфальтобетона данного состава и качества исходных материалов влияет степень уплотнения смеси (табл. 10.17).
В дорожных покрытиях после уплотнения смеси катками и последующего доуплотнения автомобилями плотность асфальтобетона соответствует, при мерно, плотности образцов, уплотненных статической нагрузкой 40 МПа в течение 3 мин при рабочей температуре смеси.
Уплотняемость асфальтобетонной смеси можно определить с помощью прибора И. В. Королева (рис. 10.16) За показатель степени уплотняемости смеси принимается число нагружений /V, необходимых для получения образ ца смеси с заданной объемной массой. С помощью этого прибора и разрабо танной методики установлены критические (минимальные) температуры эффективного уплотнения асфальтобетонных смесей при устройстве покры тий в зависимости от марки применяемого битума и гранулометрического состава минеральной смеси (рис. 10.17, табл. 10.18). Снижение минимальной
температуры конца уплотнения смесей, |
|
||||||
подобранных |
по |
коэффициенту сбега |
|
||||
0,9, связано с уменьшением величины |
|
||||||
внутреннего |
трения |
смеси. Уплотнение |
|
||||
жестких смесей горячего типа, содер |
|
||||||
жащих повышенное количество щебня, |
|
||||||
необходимо |
начинать при |
120—130°С. |
|
||||
Уплотнение |
предпочтительно начинать |
|
|||||
виброкатками |
|
на |
пневматических |
|
|||
шинах. |
|
|
по |
минералогическому |
|
||
Различные |
|
||||||
составу и структуре минеральные мате |
|
||||||
риалы оказывают влияние на степень |
|
||||||
уплотняемости |
асфальтобетонных сме |
|
|||||
сей. Минералогический состав и пори |
|
||||||
стость |
материалов |
определяют шеро |
|
||||
ховатость и форму минеральных зерен, |
|
||||||
что, в свою очередь, отражается на ве |
|
||||||
личине внутреннего трения и сцепления |
|
||||||
частиц, а следовательно, и на уплот |
|
||||||
няемости смесей. |
|
|
|
Рис. 10.16. Схема прибора для определения |
|||
Структура |
и размер пор влияют на |
||||||
степень |
отсоса |
жидких |
компонентов |
уплотняемости асфальтобетонных смесей: |
|||
/ — образец; 2 — верхний и нижний вкладыши; 3 — |
|||||||
битума |
и |
способствуют |
повышению |
форма; 4 — индикатор |
|
|
|
|
|
Уплотняющая нагрузка. МПа |
|
|
||
|
Показатели |
5 |
7,5 |
К) |
15 |
20 |
30 |
40 |
|
|
|
|
|||||||
Объемная |
масса, |
2,10 |
2,15 |
2,22 |
2,24 |
2,25 |
2,25 |
2,27 |
|
г/см3 |
|
||||||||
Водонасыщение, |
4,0 |
3,2 |
2,1 |
2,0 |
2,0 |
.1,9 |
1,7 |
||
% |
|
|
|||||||
Предел прочности |
|
|
|
|
|
|
|
||
при |
сжатии |
при |
4,5 |
4,8 |
5,2 |
5,4 |
5,6 |
5,6 |
5,7 |
20°С, |
МПа |
|
|||||||
|
|
|
|
|
|
|
|
Т а б л и ц а |
10.18 |
Тир асфальтобетона |
Марка битума |
|
Температура конца уплотнения, °С, при коэффициенте сбега смеси |
||||||
|
0,7 |
|
0,8 |
0,9 |
|
||||
|
|
|
|
|
|
|
|||
Горячий |
|
БНД 40/60 |
|
95—120 |
|
75—90 |
60—70 |
||
Теплый |
|
БНД 90/130 |
|
80—100 |
|
65—75 |
50—55 |
||
|
БНД 130/200 |
|
80—90 |
|
50—65 |
40—45 |
|||
|
|
|
БНД 200/300 |
|
70—80 |
|
35—50 |
30—40 |
|
|
|
|
СГ 130/200 |
|
— |
|
25—35 |
|
|
вязкости битумных прослоек и вязкого сопротивления смесей при уплотне нии. Так, асфальтобетонные смеси, приготовленные на металлургических шлаках, отличаются меньшей уплотняемостью, чем смеси на щебне из при родных горных пород. Асфальтобетонные смеси на щебне из пористых извест няков более жесткие, чем на плотных известняках, вследствие, значительной диффузии наиболее подвижного компонента (масел) из битума. Поэтому смеси на щебне из плотных известняков обладают лучшей уплотняемостью по сравнению со смесями на щебне из пористых известняков.
Производство асфальтобетонных смесей. Асфальтобетонные смеси изго тавливают на стационарных или передвижных асфальтобетонных заво дах (АБЗ). Для устройства и ремонта покрытий в городах устраивают стационарные заводы. Для строительства магистральных автомобильных дорог используют, как правило, временные заводы. Асфальтобетонные заво ды размещают у Железнодорожных и водных путей или непосредственно у строящейся дороги. Удаленность завода от места укладки смеси определяют продолжительностью ее транспортирования, которая не должна превы шать 1,5 ч.
Целесообразный радиус обслуживания строящихся автомобильных дорог с одного АБЗ 60—80 км.
Выбор площадки для асфальтобетонного завода в каждом случае реша ют на основе технико-экономических изысканий. Площадка для размещения завода должна быть по возможности ровной и иметь небольшой уклон для стока атмосферных вод. В состав завода входят: смесительный цех, состоя щий из машин и агрегатов, предназначаемых для приготовления асфальто бетонной смеси из подготовленных соответствующим образом материалов; битумное хозяйство, включающее битумохранилище, битумоплавильные кот лы, насосные станции, битумопроводы; помольная установка, перерабаты вающая минеральные материалы (известняк, доломит, доменные шлаки) в минеральный порошок; склады щебня, песка и минерального порошка; лаборатория, контролирующая качество материалов, технологию производ-
296
ства и качество выпускаемой продук |
|
|||||||
ции; энергосиловое и паросиловое хо |
|
|||||||
зяйства; |
средства |
для |
внутризаводско |
|
||||
го транспортирования материалов и др. |
|
|||||||
Поступающие на завод минеральные |
|
|||||||
материалы |
выгружают |
на |
специаль |
|
||||
ные площадки, которые должны иметь |
|
|||||||
твердое |
покрытие. Рекомендуется уст |
|
||||||
раивать крытые склады или навесы для |
|
|||||||
хранения 10—15-дневного запаса щеб |
|
|||||||
ня мельче 15 мм и песка. Каменный |
|
|||||||
материал для производства |
минераль |
|
||||||
ного порошка после просушки во вра |
|
|||||||
щающемся |
барабане |
размалывают |
в |
|
||||
шаровых или трубных мельницах. Хра |
|
|||||||
нят минеральный порошок в закрытых |
|
|||||||
помещениях бункерного типа или в си- |
|
|||||||
лосах. Для |
механизации |
складских |
|
|||||
операций |
обычно |
применяют автопо |
|
|||||
грузчики, ленточные конвейеры, транс |
|
|||||||
портерные эстакады и другие машины |
Рис. 10.17. Зависимость уплотняемости |
|||||||
и механизмы. |
|
|
|
|
|
асфальтобетонных смесей от температу |
||
Битум поступает на АБЗ в бункер |
ры и вязкости битума: |
|||||||
1 — смесь, приготовленная на битуме БНД 60/90; |
||||||||
ных полувагонах или цистернах и слива |
2 — то же, на битуме БНД 130/200; 3 — то же, на |
|||||||
ется в хранилища. При расположении |
битуме БНД 200/300; 4 — то же, на битуме |
|||||||
СГ 130/200 |
||||||||
нефтеперерабатывающего |
завода |
на |
|
расстоянии до 300 км битум можно доставлять на АБЗ автобитумовозами. Технологический процесс получения
асфальтобетонной смеси включает следующие основные операции: подготовку минеральных материалов (подача и предварительное их дози
рование, высушивание и нагрев до требуемой температуры, дозирование); подготовку битума (подача из хранилища в битумоплавильню, удаление содержащейся влаги и нагрев до рабочей температуры, а в необходимых случаях введение поверхностно-активных добавок или разжижителя, дозиро
вание перед подачей в мешалку смесителя); перемешивание минеральных материалов с битумом и выгрузку готовой
асфальтобетонной смеси в накопительные бункера или автомобили-само
свалы.
Основным агрегатом на асфальтобетонном заводе является асфальтосмеситель. В настоящее время асфальтосмесительное оборудование представ ляет собой комплект, включающий агрегат питания, сушильный и смеситель ный агрегаты, накопительный бункер, емкости для битума, минерального по рошка и мазута, кабину управления и все необходимые средства вертикально го и горизонтального транспорта компонентов смесей. Производительность асфальтосмесителей составляет 25—50 или 100 200 т/ч. Они могут ра о
тать в автоматическом и дистанционном режимах управления. Асфальтосмесители циклического действия принудительного перемеши
вания (табл. 10.19) являются основными, выпускаемыми промышленн
И предназначены для выпуска всех типов и видов смесей. |
|
Д |
|
Технологическая схема работы АБЗ со смесительной устан в |
|||
представлена на рис. 10.18. Предварительно дозированные |
п |
ен. |
|
попадают через питатель 1 на «холодный» ковШ°® ^” э,п |
ьГш рЯрнк / гппя |
||
ные ■ |
которым рСаГ р |
;роТы=еа"»тояОР„Яо |
|
чим» элеватором |
4 подаются на грохот о, которым р v р |
к |
|
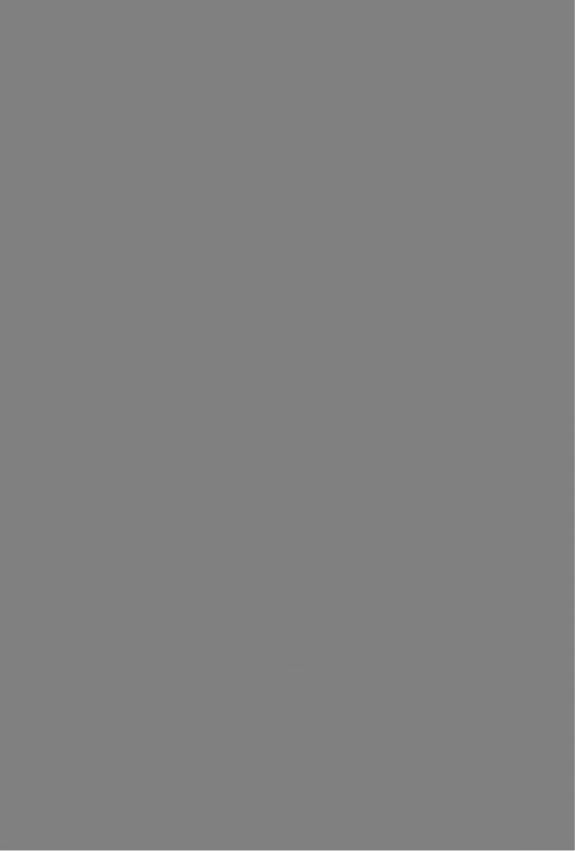
В асфальтосмесителях с мешалкой непрерывного действия (например, Д-645-3) фракционированный минеральный материал из горячих бункеров дозируют ленточными дозаторами непрерывного действия, минеральный порошок шнековым. Все материалы в требуемом соотношении посту пают в лопастную мешалку, смачиваются непрерывным потоком битума, перемешиваясь, смесь перемещается к выгрузочному отверстию. Время
и скорость перемешивания регулируется. Производительность смесителя Д-645-3 составляет 100 т/ч.
В настоящее время начат выпуск асфальтосмесителей циклического действия ДС-84-2 производительностью 200 т/ч. В них минеральные мате риалы фронтальным погрузчиком подаются в агрегат питания. С питателя щебень и песок подаются на транспортер, а затем в сушильный барабан и горячим элеватором поднимаются в смесительный агрегат.
Смесительный агрегат этого асфальтосмесителя состоит из следующих основных частей: грохота плоского, имеющего сита с отверстиями 3, 5, 12, 20, 40 мм; бункера для горячих минеральных материалов, рас
положенного |
под грохотом. Бункер имеет |
пять |
секций |
для фракций |
0 — 3, 3 — 5, |
5 — 12, 12 — 20 и 20 — 40 мм. |
Из |
бункера |
фракциониро |
ванные материалы попадают в дозатор. Минеральный порошок из силосных банок шнеком подается также в дозатор. Улавливаемая сухим способом пыль циклонов специальным элеватором подается в бункер и дозатор, взвешивается и поступает в мешалку. Соотношение между минеральным порошком и пылью циклонов, поступающими в мешалку, можно менять. Дозирование материала автоматизировано. Битум вводят в мешалку с помощью порционного дозатора жидкого битума УДЖБ-80 с объемным счетчиком, который отсчитывает требуемую дозу битума в потоке. В мешалке смешение материалов .осуществляется двумя вращающимися навстречу друг другу валами с лопастями.
Масса одной порции асфальтобетонной смеси — до 3500 кг. Смесь погружается в ковш скипового подъемника и подается в накопительные бункера. Вместимость двух накопительных бункеров 100 т. Загрузка автомобиля-самосвала смесью может осуществляться'как под накопитель ным бункером, так и под смесителем.
В накопительном бункере разрешается кратковременное хранение сме
сей (не более 4 — 6 ч).
Транспортирование горячих асфальтобетонных смесей осуществляется автомобилями-самосвалами на расстояние до 50 — 60 км. Если понижен ная температура воздуха и продолжительность транспортирования приво дят к снижению температуры готовой смеси ниже требуемой, то применяют обогрев кузова и смесь в нем покрывают брезентом.
Подготовка основания, укладка и уплотнение смесей. Подготовка осно вания включает: проверку качества основания и устранение дефектов: очистку поверхности от пыли и грязи; обработку основания вяжущим в целях обеспечения надлежащего сцепления с покрытием.
Основание, подготовленное к укладке асфальтобетонной смеси, должно иметь требуемую ширину, толщину, продольный и поперечный уклоны. Наибольший размер неровностей основания при проверке трехметровой рейкой не должен превышать 6 — 8 мм. Хорошее сцепление покрытия с основанием» а также между слоями покрытия обеспечивается за счет обработки основания или нижнего слоя покрытия битумом или битумными материалами. На обработку 1 м2 основания или нижнего слоя асфаль тобетонного покрытия соответственно расходуется 0,5 0,8 и 0,2 0,3 л битума. Если для тех же целей используется 60%-ная битумная эмульсия, то ее расход соответственно 0,6 0,9 и 0,3 0,4 л.

|
|
г'рупповой состав |
|
|
Свойства |
|
|
|
|
|
|
|
|
Место отбора пробы |
Масла |
Смолы |
|
Глубина про |
Температура |
Растяжи |
|
Асфальтены |
|||||
|
никания иглы |
размягчения, |
мость при |
|||
|
|
|
|
при 25°С |
°с |
25°С, см |
Битум из рабоче |
|
|
|
|
|
|
го котла |
51,7 |
30,2 |
18,0 |
94 |
45,0 |
133 |
Битум экстраги |
|
|
|
|
|
|
рован из смесей |
51,8 |
24,8 |
23,0 |
76 |
45,5 |
127 |
Битум экстраги |
|
|
|
|
|
|
рован из асфальто |
|
|
|
|
|
|
бетона через 5 сут |
|
|
|
|
|
|
после укладки |
51,0 |
23,2 |
25,1 |
67 |
46,5 |
121 |
циальных приборов экстракторов с последующим расчетом его содержа ния и анализом гранулометрического состава минеральной смеси.
Влияние технологических процессов на формирование структурных связей и макроструктуры асфальтобетона. В соответствии со стадийным процессом формирования структуры асфальтобетона первый период — пе риод формирования микроструктурных связей — является наиболее ответ ственным и требует особо тщательного выполнения нагрева, операций дози рования и перемешивания смесей.
Одним из важнейших элементов технологии приготовления смеси является перемешивание минеральных материалов с битумом.
Нагрев исходных материалов до рабочей температуры необходим для хорошего смачивания, растекания и прилипания вяжущего к поверхности минеральных зерен. Это облегчает перемешивание вследствие понижения вязкости битума. Недогрев и перегрев недопустимы. Изменение группового состава битума происходит уже в первые минуты его смешения с горячим минеральным материалом (табл. 10.21), поэтому асфальтобетонные смеси необходимо приготавливать при минимально возможной температуре, при которой вязкость битума была бы не более 0,5 Па.с.
По принятой технологической схеме приготовления смесей в мешалку подают горячий щебень, песок, минеральный порошок и битум. Вначале большая часть битума объединяется с минеральным порошком и в даль нейшем требуется значительная затрата энергии для того, чтобы перевести часть этого битума с поверхности порошка на поверхность крупных мине ральных составляющих. Введение минерального порошка после битума позволяет ускорить процесс перемешивания, а в некоторых случаях полу чить более высокое качество смеси. При введении минерального порошка после битума он интенсивно и достаточно полно покрывает крупные зерна, а затем адсорбирует битум на своей поверхности, структурирует его, обеспечивая в дальнейшем высокие эксплуатационные свойства асфальто бетона. Преимущество такой подачи минерального порошка—■меньшая затрата времени на перемешивание и отсутствие потерь порошка вследствие
возможного развеивания.
Продолжительность перемешивания асфальтобетонной смеси зависит от ее состава, свойств и температуры нагрева материалов, способа подачи минерального порошка и конструкции смесительной установки. Мелкозер нистые смеси с большим содержанием минерального порошка требуют более длительного перемешивания, чем крупнозернистые (табл. 10.22).
Для улучшения прилипания битума к поверхности минеральных мате риалов, облегчения распределения битума в смеси и увеличения водостой-
|
|
|
|
кости асфальтобетона |
вводят |
ПАВ. |
|
|
|
|
|
На асфальтобетонном |
заводе |
ПАВ |
|
|
|
|
|
могут быть введены в битум, на мине |
|||
|
Время приготовления смесей |
в |
ральный материал до подачи битума |
||||
|
лопастных мешалках, с |
|
в мешалку, |
в битум и |
на минераль |
||
Вид смеси |
Смешение мине |
|
|
ный материал раздельно при исполь |
|||
|
Смешение с |
би |
зовании комплексных |
ПАВ, на по |
|||
|
ральных мате |
тумом |
|
||||
|
риалов |
|
|
верхность минерального порошка в |
|||
Песчаная |
15 |
45—60 |
|
процессе его приготовления. |
|
||
Мелкозернистая |
15 |
40—50 |
|
В вязкий битум безводные ПАВ |
|||
Среднезерни |
15 |
30 -45 |
|
вводят при |
120 — 140°С. Слабооб |
||
стая |
|
водненные |
ПАВ рекомендуется вво |
||||
Крупнозерни |
|
20—30 |
|
дить порционно с тщательным пере- |
|||
стая |
— |
|
|||||
|
•мешиванием при температуре битума |
||||||
|
|
|
|
110 — 130°С. На минеральный материал ПАВ вводят в процессе сухого пере мешивания смеси.
Второй период — период формирования макроструктуры асфальтобе тона завершает цикл технологических операций и требует выполнения в заданные сроки транспортирования, укладки и уплотнения. При транс портировании и укладке асфальтобетонная смесь претерпевает некоторые физико-химические изменения. Так, с понижением температуры происходит увеличение толщины ориентированного слоя битума на минеральных частицах, что приводит к изменению вязкости внешнего слоя битумной пленки.
Процесс уплотнения — завершающая стадия активного структурообразования асфальтобетона, от эффективности которого зависят его эксплуа тационные свойства. Недоуплотненные покрытия продолжают уплотняться движущимися автомобилями, что в большинстве случаев приводит к обра зованию неровностей по поперечному профилю покрытий. Однако коли чество проходов катков сверх оптимального может привести к увеличению дефектов структуры асфальтобетона и вследствие этого к уменьшению его прочности и долговечности. Как правило, действие уплотняющих средств направлено на преодоление сопротивления жидкой фазы и внут реннего трения минерального остова. Значительную долю общего сопротив ления составляет вязкое сопротивление битумных пленок. Об этом, в част ности, свидетельствует эффективность применения вибрирующих устройств, которые при малом вертикальном давлении позволяют достигнуть плот ности асфальтобетона, иногда значительно' превышающей плотность, получаемую при уплотнении другими катками.
Исследования уплотняемости асфальтобетонных смесей показали, что нижний предел вязкости битума, при котором можно достичь проектной плотности асфальтобетонной смеси, должен быть не менее 10, а верхний — не более 25 Па.с.
Существенным фактором, определяющим качество уплотнения, считается величина изменения плотности асфальтобетона при каждом проходе катка. Уплотнение за один проход должно соответствовать приращению плотности 0,1 г/см3 При изменении плотности более чем на 0,1 г/см3 появляются волны, наплывы и другие дефекты.
К концу уплотнения минеральные частицы асфальтобетона приобретают устойчивое положение, фиксированное битумными пленками. Снижение температуры приводит к упрочнению коагуляционных связей. Происходит дальнейшее формирование диффузионно-структурированной оболочки би тума на частицах и ориентация входящих в состав битума поверхностно-ак тивных веществ. Скорость твердения асфальтобетона взаимосвязана с
температурой воздуха и вязкостью исходного битума. Быстрое охлаждение асфальтобетона ухудшает условия формирования прочных коагуляционных связей, поэтому максимальную температуру начала уплотнения в зависи мости от типа смеси и температуры воздуха следует выбирать с учетом продолжительности твердения не менее 3 — 4 ч.
§ 10.9. СТРУКТУРНО-МЕХАНИЧЕСКИЕ И ТЕХНОЛОГИЧЕСКИЕ ОСОБЕННОСТИ ТЕПЛОГО АСФАЛЬТОБЕТОНА
В теплом асфальтобетоне применяют битумы с меньшей вязкостью, чем в горячих асфальтобетонных смесях. Если теплый асфальтобетон приготавливают на битумах БНД 130/200, БНД 200/300, БНД 40/60 и БНД 60/90, смешанных с тяжелыми разжижителями нефтяного или каменноугольного происхождения, формирование структуры происходит за счет упрочнения микроструктурных связей при уплотнении и охлаждении материала в покрытии. Асфальтобетон после уплотнения и охлаждения обладает проектной плотностью и прочностью. Если же теплый асфаль тобетон приготавливают на битумах СГ 130/200, БНД 40/60 и БНД 60/90, смешанных с легкими разжижителями (начало кипения 160 — 180, конец кипения 260 — 300°С) до глубины проникания иглы при 25°С 300 — 400°, происходит относительно длительное формирование структуры асфальто
бетона. Асфальтобетон после уплотнения и |
охлаждения |
смеси |
набирает |
|||
до |
80% проектной |
плотности и |
прочности. |
Испарение |
легких |
фракций |
с |
одновременным |
доуплотнением |
транспортными средствами |
приводит |
к окончательному формированию покрытия.
Минеральные материалы для теплого асфальтобетона должны быть чистыми, зерна угловатыми и шероховатыми. Прочность при сжатии исходной горной породы должна быть не ниже 100—120 МПа. Осадочные карбонатные породы и металлургические шлаки могут быть использованы
спрочностью не ниже 80—100 МПа.
Втеплом асфальтобетоне не рекомендуется применять природный
песок и гравий. В крайнем случае содержание крупнозернистого окатан ного песка может быть не более 30% от массы дробленого песка. Искус ственный песок, получаемый при дроблении магматических горных пород и металлургических шлаков, должен содержать зерен фракции 5 — 1,25 мм
не менее 25%.
Применение в теплом асфальтобетоне битумов с меньшей вязкостью определяет особенности структурообразования и структурно-механические свойства материала — способность смесей приобретать плотность в пок рытии при более низких температурах воздуха, по сравнению с горячими смесями. Теплый асфальтобетон обладает большей трещиностойкостью при низких отрицательных температурах (табл. 10.23).
Адгезионная и когезионная прочность битума в общем случае понижается с понижением вязкости битума. Поэтому водо- и морозостойкость теплого асфальтобетона, приготовленного на обычных материалах по принятой технологии, в начальный период эксплуатации ниже, чем у горячего асфальтобетона. Следовательно, для повышения долговечности теплого асфальтобетона необходимы специальные мероприятия, заключающиеся во введении в смесь поверхностно-активных веществ и активаторов, в акти
вации минеральных материалов и др.
Процессы структурообразования в смесях, приготовленных на битумах БНД 130/200 и БНД 200/300, протекают так же, как и в горячих смесях, но с некоторым замедлением. Изменяя порядок введения минеральных
зоз
|
|
|
|
|
|
материалов, разжижителя и битума, |
|||||||
|
|
|
|
|
|
можно |
направленно |
регулировать |
|||||
|
|
|
Температура ;хрупкостн, °С |
структурообразование |
(табл. |
10.24). |
|||||||
|
|
|
|
|
|
|
|
|
|
||||
|
|
Пенет- |
битумов |
асфаль |
Введение в мешалку пластифика |
||||||||
Марка битума |
рация |
тобе |
тора с ПАВ |
непосредственно после |
|||||||||
|
|
тонов |
|||||||||||
|
|
при |
|
|
|
минеральных |
материалов обеспечи |
||||||
|
|
25°С |
по |
по Баш по Баш |
|||||||||
|
|
|
Фра- |
НИИ |
НИИ |
вает предварительную гидрофобиза- |
|||||||
|
|
|
асу |
НП |
НГ1 |
цию зерен, что создает условия для |
|||||||
|
|
|
|
|
|
||||||||
БНД |
40/60 |
49 |
- 1 3 |
- 3 6 |
- 2 5 |
более |
|
равномерного |
распределения |
||||
вяжущего по поверхности минераль |
|||||||||||||
БНД |
60/90 |
79 |
—16 |
- 3 9 |
- 3 0 |
||||||||
БНД 90/130 |
100 |
- 1 9 |
—41 |
—33 |
ных |
материалов, |
снижает |
работу |
|||||
БНД |
130/200 |
173 |
-2 1 |
- 4 3 |
—35 |
перемешивания. |
пластификатора в |
||||||
БНД 200/300 |
244 |
—22 |
45 |
- 3 7 |
При |
введении |
|||||||
П р и м е ч а н и е . Испытания по методу БашНИИ МП |
смесь |
после |
битума |
размягчается |
|||||||||
внешняя оболочка |
битумной пленки |
||||||||||||
произведены при скорости охлаждения 0,03°С/мин. |
на минеральных зернах, снижается вязкость свободного битума, уменьшается вероятность самослипания покрытых вяжущим зерен при снижении температуры смеси. Такой порядок введения материалов наиболее целесообразен для работ в осенне-зимний период.
П^и формировании структуры теплого асфальтобетона на битумах СГ 130/200 и БНД 40/60, БНД 60/90, смешанных с легкими разжижителями (лигроин, сланцевое масло, каменноугольное масло), процессы стуктурообразования протекают по типу формирования структуры холод ного асфальтобетона, но за гораздо меньший период (до 20 сут).
Сдвигоустойчивость. Главным сдерживающим началом широкого при менения теплого асфальтобетона для автомобильных дорог является возможность образования наплывов и сдвигов при движении автомобилей в летнее время. Наибольшей прочностью при сдвиге обладает асфальто вяжущее и наименьшей — асфальтобетон. По мере насыщения асфальто вого раствора щебнем (до 20%). прочность при сдвиге понижается. Даль нейшее насыщение смеси щебнем приводит к формированию пространст
венного |
каркаса, |
вследствие |
чего |
максимальная |
прочность |
при сдвиге |
|||
|
|
|
|
|
|
|
|
Т а б л и ц а 10.24 |
|
|
|
|
|
|
\ |
Водона- |
Предел прочности при сжатии, |
Коэффициент |
|
|
|
|
|
Остаточная |
|
МПа, при |
|||
Технология прнготовленн |
|
пористость, |
% сышепне, |
% |
водостоГжостн |
||||
|
|
||||||||
|
|
|
|
|
|
|
50°С |
20° С |
|
Минеральная |
часть |
|
4.0 |
|
1,6 |
1,36 |
7,25 |
0,89 |
|
|
3.0 |
|
0,75 |
1,5 |
6,5 |
0,92 |
|||
Вязкий битум (П-60) |
|
|
|||||||
|
|
|
|
|
|
|
|||
Минеральная |
часть |
|
5,0 |
|
1,2 |
1,10 |
4.0 |
1,0 |
|
Вязкий битум пластифици- |
|
||||||||
4,5 |
|
0,9 |
1,2 |
4.0 |
1,0 |
||||
эованный |
(П-260) |
|
|
||||||
|
|
|
|
|
|
|
|||
Минеральная |
часть |
|
з,'о |
|
0,9 |
1,14 |
4,0 |
0,96 |
|
Пластификатор (П-60) |
|
|
|||||||
|
2,5 |
|
0,7 |
1,2 |
3,7 |
1,0 |
|||
|
|
|
|
|
|||||
Минеральная |
часть |
|
5,0 |
|
1,2 |
0,9 |
2,50 |
0,90 |
|
Вязкий битум (П-60) |
|
|
|||||||
|
3,5 |
|
0,7 |
1,1 |
2,6 |
0,97 |
|||
|
|
|
|
|
Пластификатор
П р и м е ч а н и е . В числителе — без ПАВ, в знаменателе — с ПАВ.
теплого асфальтобетона достигается при 40% щебня, а горячего при 50%. Такое различие^ объясняется тем, что вязкий битум образует на щебенках пленку большей толщины, чем менее вязкий битум. При этом *увеличи вается вероятность образования плоскостей скольжения -по толстым пленкам и для создания сдвигоустойчивого каркаса в ‘горячем асфаль тобетоне требуется повышенное содержание щебня.
Для асфальтобетона с неизменным гранулометрическим составом проч ность при сдвиге закономерно понижается с понижением вязкости битума. Однако при переходе к асфальтобетонам, приготовленным на битумах той же вязкости, но оптимальной структуры, эта закономерность нару шается. Теплый и горячий асфальтобетоны оптимальных структур имеют практически одинаковые значения предельного сопротивления сдвигу. Это объясняется тем, что падение сдвигоустойчивости асфальтобетона, кото рое неизбежно происходит за счет снижения вязкости применяемого битума, компенсируется изменением в гранулометрии асфальтобетона, в результате чего общего падения прочности при сдвиге не наблюдается.
Трещиностойкость. Теплый асфальтобетон более пластичен при отрица тельных температурах, чем горячий. Участок стабилизации прочности, характеризующий переход асфальтобетона в хрупкое состояние, у теплого асфальтобетона смещается в область низких температур. У теплого асфаль
тобетона |
переход в хрупкое состояние происходит при —40-=— 25°С, |
у |
||||||
горячего — при |
—10-4— 20°С. Прочность |
теплого |
асфальтобетона |
на |
||||
растяжение при изгибе при 0°С |
ниже |
(/?1|ЗГ= 3,5 |
МПа), чем |
горя |
||||
чего (/?изг = 5 |
МПа), |
но горячий |
асфальтобетон |
разрушается |
прак |
|||
тически |
как |
хрупкое |
(е = 0,007), |
теплый — как |
упруго-вязкое |
тело |
(е = 0,025).
Ползучесть. При нагружении теплого асфальтобетона постоянной нагрузкой в нем возникают обратимые и необратимые деформации, вели чина которых связана с уровнем напряжения. При напряжениях, не превышающих 0,03 Rpa3f), теплый асфальтобетон работает в упругой ста дии, при напряжениях до 0,4 Rpa3p — в упруго-вязкой стадии, при этом часть деформации после снятия нагрузки не восстанавливается; в асфаль тобетоне накапливаются остаточные деформации. В материале устанавли вается стационарное течение. При напряжениях, превышающих 0,4 Яразр, деформация асфальтобетона возрастает и приводит через некоторое
время к разрушению.
Релаксация напряжений. Релаксационная способность теплого асфаль тобетона так же, как и горячего, взаимосвязана с вязкостью битума и размером минеральных зерен (табл. 10.25). Теплый асфальтобетон на
битуме БНД 200/300 в наименьшей |
степени |
релаксирует напряжения |
||||
при предельной |
крупности зерен 1,25 мм, на |
битуме |
БНД |
130/200 — при |
||
5 мм. При температуре 0°С теплые асфальтобетоны |
релаксируют 6 — 7% |
|||||
первоначального |
напряжения, в то |
время |
как |
горячий |
асфальтобетон |
при этой температуре практически не релаксирует напряжения. Поэтому температурные напряжения при понижении температуры в теплом асфаль тобетоне быстрее рассасываются, чем в горячем. Отсюда большая трещи
ностойкость теплых асфальтобетонов.
Расчет состава теплого асфальтобетона. Состав рассчитывают так же, как и горячего. Однако максимальное содержание щебня в мелкозернистом асфальтобетоне не должно превышать 60%. Минерального порошка необходимо брать больше на 15-20% , чем для соответствующего типа
горячего асфальтобетона.
Качество теплых асфальтобетонов оценивают по физико-механическим свойствам, приведенным в табл. 10.12. Теплый асфальтобетон с оптималь-
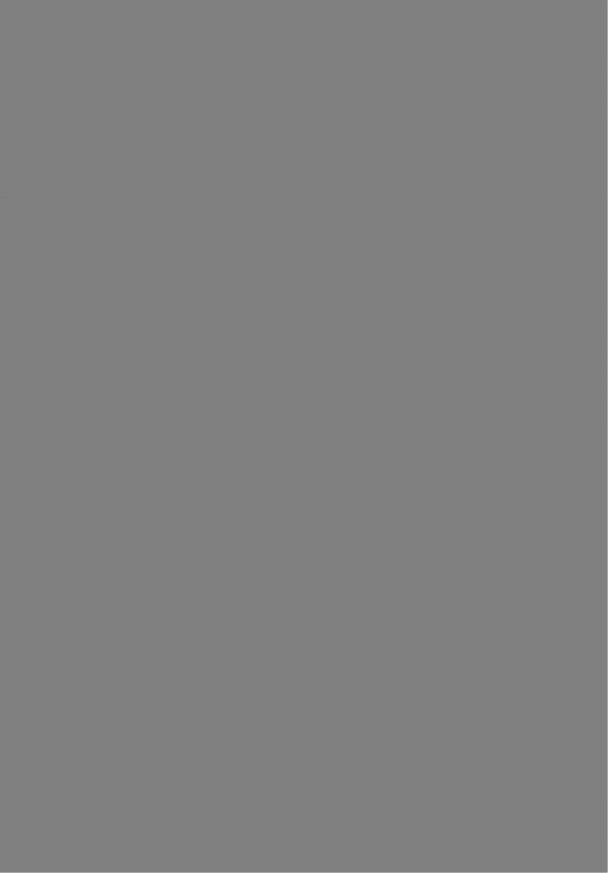
|
|
Мурка |
Температура смеси |
Время сохранения удобоукладываемости асфальтобетонной |
|||
|
|
битума |
начале укладки, 0 ' |
||||
|
|
смеси, мин, в зависимости от температуры воздуха, °С |
|||||
|
|
|
|
0 |
—5 |
- 1 0 |
- 1 5 |
БНД |
130/200 |
100 |
30 |
25 |
20 |
15 |
|
БНД |
200/300 |
90 |
35 |
30 |
25 |
20 |
|
СГ |
130/200 |
80 |
120 |
90 |
50 |
30 |
ным гранулометрическим составом по прочности не уступает асфаль тобетону, приготовленному на вязких битумах (табл. 10.26).
В обычных условиях при температуре воздуха выше 10°С структура горячего асфальтобетона в покрытии формируется относительно быстро. При температуре воздуха ниже 10°С расчетная плотность горячего асфаль
тобетона, как правило, не достигается, поэтому применяют теплый асфаль тобетон.
Температура смеси в момент доставки ее на место укладки должна быть на 20 — 30°С выше пределов, приведенных в табл. 10.27. Ориенти ровочно время, в течение которого смесь сохраняет удобоукладываемость при различных температурах воздуха, приведено в табл. 10.28. Укладку асфальтобетонной смеси производят укладчиками и только при малом объеме работ — вручную. Уплотнение должно быть закончено до того момента, когда будет достигнута критическая температура. При темпе ратуре воздуха от 0 до 10°С уплотнение начинают пятью — семью прохо дами по одному следу легких катков и заканчивают 15 — 20 проходами тяжелых. При температуре воздуха от 0 до —15° смесь уплотняют только тяжелыми катками (20 — 25 проходов по одному следу), а число катков увеличивают в 1,5 раза по сравнению с обычными условиями.
Весьма эффективно включить в звено катков самоходный каток на пневматических шинах, которым уплотняют смесь перед проходами тяже лых катков.
Область применения теплого асфальтобетона. В I дорожно-климатичес кой зоне и в северной части II зоны теплый асфальтобетон пригоден для устройства покрытий на дорогах высших категорий при производстве работ как в летнее, так и зимнее время (до —5°С).
В южной части II и III дорожно-климатических зон теплый асфальто бетон применим для устройства покрытий на дорогах II и III категорий. Технологические свойства теплых смесей позволяют значительно расширить строительный сезон и вести работы при температуре воздуха до —10°С.
В IV дорожно-климатической зоне теплый асфальтобетон целесообразно использовать в осенне-зимний период при температуре до — 15°С. При при менении угловатых зерен с шероховатой поверхностью теплый асфальто бетон, приготовленный на битуме БНД 130/200, удовлетворительно рабо тает в покрытии при интенсивном автомобильном движении.
§ 10.10. ХОЛОДНЫЙ АСФАЛЬТОБЕТОН
Характерной чертой холодного асфальтобетона, отличающей его от горя чего и теплого, является способность оставаться длительное время после приготовления в рыхлом состоянии. Эта особенность холодных асфальто бетонных смесей объясняется наличием тонкой битумной пленки на мине-
307
ральных зернах, вследствие чего микраструктурные связи в смеси нас только слабы, что небольшое усилие приводит к их разрушению. Поэ тому приготовленные смеси под действием собственной массы при хра нении в штабелях и транспортировании не слеживаются (не комкуются). Смеси в течение длительного времени (до 12 мес) остаются в рыхлом состоянии; их сравнительно легко можно перегружать в транспортные средства и распределять тонким слоем при устройстве дорожных покры тий. Незначительной слеживаемостью обладают жесткие, хорошо разрых ляющиеся смеси с ограниченным содержанием битума и достаточным содержанием минерального порошка. Слеживаемость смеси в случае необ ходимости можно уменьшить путем введения в нее в процессе перемеши вания специальных добавок в виде водных растворов нафтеновых мыл, сульфитно-спиртовой бражки и хлорного железа, известкового молока, раствора соапстока в количестве 2 — 3% по массе.
Важным технологическим свойством холодной асфальтобетонной смеси является ее уплотняемость. В. О. Гельмер предложил определять уплотняемость холодной асфальтобетонной смеси коэффициентом уплотнения_ отношение объемных масс образцов, уплотненный под различной нагрузкой:
Р = 1 £ 0 _
YO-05
где Y4O> YOos — объемные массы |
.образцов |
при уплотнении нагрузкой |
40 и 0,5 МПа в течение 3 мин при |
15 — 20°С. |
|
Степень уплотняемости можно характеризовать также величиной деформации образцов при циклическом нагружении. Уплотняемость холод ной асфальтобетонной смеси зависит от сцепления и внутренного трения смеси.
Значительное влияние на степень уплотняемости смеси оказывают коли чество и вязкость битума, а также свойства минеральных материалов, обусловливающих величину внутреннего трения.
Вследствие жесткости смеси холодный асфальтобетон в первое время после окончания уплотнения обычно не имеет достаточной плотности. В процессе эксплуатации дорожных покрытий под воздействием авто мобильного движения плотность асфальтобетона повышается, а вместе с ней повышаются его механические свойства. Нормальной плотности дорожные покрытия из холодного асфальтобетона достигают в течение первых 3 мес эксплуатации. Эта плотность соответствует плотности образ цов, уплотненных нагрузкой 40 МПа в течение 3 мин при 15 — 20°С.
Свойства холодного асфальтобетона. В дорожных покрытиях заметно изменяются свойства холодного асфальтобетона вследствие повышения вяжущих свойств жидких битумов под воздействием атмосферных факторов. Для оценки этих качественных изменений холодного асфальтобетона поль зуются показателями предела прочности при сжатии в сухом и водонасы щенном состоянии, набухания образцов, изготовленных из смеси, прогре той при 90°С. Длительность прогрева смеси устанавливают в зависимости от скорости загустевания битума.
ГОСТ 9128 — 76 холодные асфальтобетоны в зависимости от содержа ния щебня и песка подразделяют на типы: Бх — 35 — 50% щебня; Вх— 20 — 35% щебня; Дх— не менее 33% фракции 1,25 — 5 мм в дроблен ном песке. Этот же ГОСТ предусматривает две марки холодных асфаль тобетонных смесей в зависимости от класса применяемого жидкого битума и качества используемых минеральных материалов. Асфальтобетонные смеси I марки, приготавливаемые на жидких битумах класса СГ, обеспечи
вают более быстрое формирование дорожного покрытия по сравнению со сме сями II марки, содержащими медленногустеющие битумы МГ (табл. 10.29).
Гранулометрические составы холодных асфальтобетонных смесей отли чаются от составов горячих и теплых смесей в сторону повышенного содержания минерального порошка (до 20%) — частиц мельче 0,071 мм и пониженного содержания щебня (до 50%). Повышенное количество минерального порошка вызвано применением жидкого битума, требующего для структурообразования большого количества порошка, а при содержа нии щебня более 50% ухудшаются условия формирования покрытия. Наибольший размер зерен в холодном асфальтобетоне составляет 10 и 15 мм. Более крупный щебень ухудшает условия формирования покрытия.
Материалы. Для холодного асфальтобетона применяют преимуществен но дробленые минеральные материалы, имеющие угловатую форму зерен с шероховатой поверхностью. Это необходимо для повышения внутреннего трения и заклинки зерен минеральных материалов, что частично компенсит рует уменьшение прочности асфальтобетона ввиду пониженного сцепления при использовании жидких битумов.
В качестве крупной составляющей для холодного асфальтобетона используют щебень, получаемый дроблением скальных горных пород и металлургических шлаков. Эти материалы должны обладать прочностью при сжатии не менее 80 МПа, а для II марки асфальтобетона — не ниже
60МПа.
Минеральный порошок и песок для приготовления холодного асфальто
бетона применяют те же, что и для горячих смесей.
Жидкие битумы должны иметь вязкость в пределах Сб0 = 70-И30 с, что соответствует маркам СГ 70/130, МГ 70/130. Вязкость и класс битума выбирают с учетом предполагаемого срока хранения смеси на складах,
Показатели
П о р и с т о с т ь м и н ер а л ь н о го ост о в а , % по о б ъ е м у , не б о л е е , д л я а с ф а л ь т о б е т о н о в ти п ов:
Бх
Вх
Дх
О с т а т о ч н а я п о р и ст о ст ь , % по о б ъ ем у В о д о н а с ы щ е н и е , % по о б ъ ем у Н а б у х а н и е , % по о б ъ е м у , не б о л ее
П р е д е л |
п р о ч н о ст и |
при с ж а т и и , П а, не |
м ен ее, при |
т е м п е р а т |
у р е 2 0 °С : |
д о п р о г р е в а :
в о д о н а с ы щ е н н о г о а с ф а л ь т о б е т о н а
с у х |
о г о |
» |
п о с л е |
п р о гр ев а : |
|
в о д о н а с ы щ е н н о г о а с ф а л ь т о б е т о н а
с у х о г о |
» |
К о э ф ф и ц и е н т |
в о д о ст о й к о ст и , не м енее: |
до п р о г р ев а
по с л е п р о гр ев а
С л е ж и в а е м о с т ь , ч и сл о у д а р о в , не б о л ее С ц е п л е н и е б и т у м а с м и н ерал ь н ой частью
а с ф а л ь т о б е т о н н о й см еси
Т а б л и ц а 10 .29
Нормы для асфальтобетонов марок
I |
II |
|
|
18 |
|
|
|
|
18 |
|
|
||
|
|
20 |
|
|
|
|
2 |
0 |
|
|
|
|
|
21 |
|
|
|
|
|
21 |
|
|
|
|
|
6 — 10 |
|
|
|
|
6 — 10 |
|
|
||
|
|
5 — 9 |
|
|
|
|
5 — 9 |
|
|
||
|
|
1,2 |
|
|
|
|
2 ,0 |
|
|
||
11 |
• |
10 5/ |
12 |
|
105 |
7 |
. |
105/ 8 • |
|
105 |
|
15 |
• |
10 5/ |
17 |
• |
105 |
10 |
. |
10 5/ |
12 |
• |
105 |
16 |
• |
10 5/ |
18 |
• |
105 |
10 |
. |
105/ |
12 |
• |
105 |
18 |
• |
105/ 2 0 |
• |
105 |
13 |
. |
10 5/ |
15 |
• |
105 |
|
|
|
0 ,7 5 |
|
|
|
|
0 ,6 0 |
|
|
||
|
|
0 ,9 0 |
|
|
|
|
0 ,8 0 |
|
|
||
|
|
10 |
|
|
|
|
|
10 |
|
|
Выдерживает
П р и м е ч а и и с. В числителе приведем |
ателн прочности для мелкозернистых, и знаменателе — для песчан |
асфальтобетонов. |
|
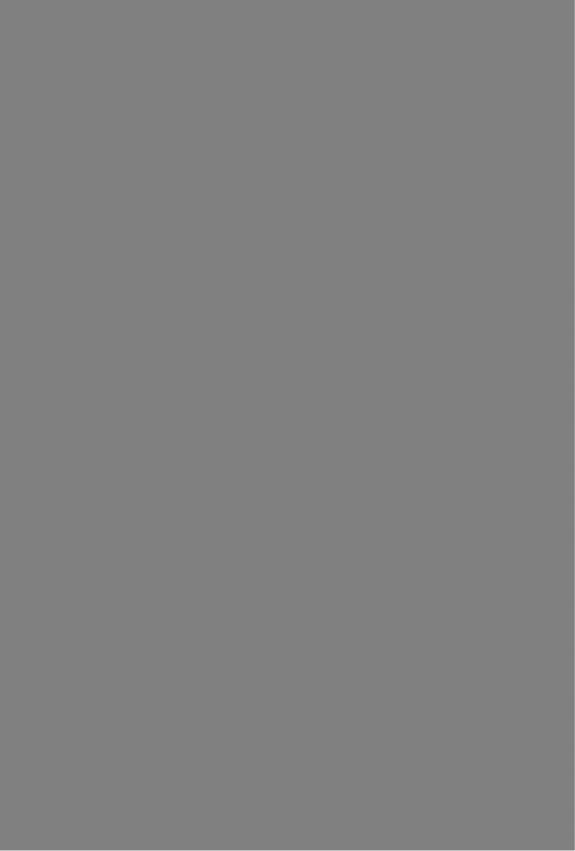
Эмульсионно-минеральные смеси (битумные шламы). Битумным шла мом называют смесь литой консистенции, состоящую из битумной пасты
или эмульсии, воды, минерального порошка и песка (песчаные шламы), а в грубозернистых — щебня.
По скорости распада эмульсий в смесях их подразделяют на медлен но-, средне- и быстрораспадающиеся. К медленнораспадающимся отно сятся анионные шламы, в которых эмульсия на анионоактивном эмуль гаторе распадается не ранее чем через 2 ч, к среднераспадающимся — через
12 ч. К быстрораспадающимся относятся катионные и анионные шламы,
вкоторых эмульсия распадается не позднее чем через 30 мин. Катионные
шламы являются быстротвердеющими, так как быстро возвращают битуму клеящие свойства. Пастовые и анионные шламы — медленнотвердеющие, так как затвердевают по мере испарения воды.
По структуре высохшего неуплотненного материала смеси подразде ляют на малопористые (остаточная пористость менее 20%), среднепористые (от 20 до 25%), пористые (более 25%).
Для приготовления битумных шламов применяют нефтяные дорожные вязкие битумы. В качестве наполнителей и эмульгаторов используют известняковые порошки, известь-пушонку, фильтр-прессную грязь, некоторые порошкообразные отходы промышленности и др. К эмульгаторам относят порошки, содержащие не менее 20% по массе CaO + MgO и не менее 60% по массе частиц мельче 0,071 мм. Применение активированных мине ральных порошков не допускается.
В качестве каменных материалов применяют дробленые и природные пески, высевки и щебень от 5 до 10 мм не ниже марки 1.000.
Для битумных шламов определяют свойства в жидком состоянии (консистенцию и расслаивание смеси) и твердом сформировавшемся состоянии (водонасыщение, набухание, износ, коэффициент шероховатости).
Битумные шламы приготавливают одно- и двустадийным способами в мешалках циклического действия. По одностадийному способу шламы готовят в мешалках с частотой вращения лопастей не менее 60, по двуста дийному — не менее 30 об/мин. Приготовление битумных шламов может быть осуществлено в асфальтосмесителе Д-508-2А, бетономешалках СБ-80, С-742, С-355 и др.
При одностадийном способе приготовления ластового битумного шлама, например в асфальтосмесителе Д-508-2А, в мешалку при постоянном пере мешивании вводят отдозированные порошкообразный эмульгатор, мине ральный порошок, песок и часть воды (70—80% от всей воды шлама), перемешивают 20—30с, после чего вводят нагретый до рабочей темпера туры битум, снова перемешивают в течение 90—120 с, затем добавляют оставшуюся воду и перемешивают 20—40 с до полной готовности шлама.
При двустадийном способе сначала приготавливают битумную пасту в мешалке, затем в нее добавляют песок и воду и после перемешивания
получают готовую смесь.
Битумные шламы транспортируют в специальных траспортных средствах, оборудованных побудителем смеси. На расстояние до 10 км песчаные шламы допускается транспортировать в автомобилях-самосвалах, при транспортировании на большее расстояние в кузов автомобиля уста навливают специальное навесное оборудование, которое состоит из побу дителя в виде лопасти, совершающей колебания, гидравлического при
вода побудителя и разгрузочного устройства.
Смесь укладывают распределителем, а при малом объеме работ вРУчо ную. Распределитель РД-902 представляет собой разделенный перегородкой на две части бездонный ящик. На задней стенке распределителя закреп
лена резиновая лента, которая обеспечивает выглаживание слоя смеси. При ремонтных работах смесь укладывают по одной полосе покрытия в направлении длижения транспортных средств. После подсыхания смеси открывают движение.
Как показали опытно-производственные работы, в южных районах страны хорошо себя зарекомендовали следующие составы пастовых шла мов: щебень фракции 10—5 мм 15—20%; высевки мельче 5 мм 40—45%; цементная пыль (как эмульгатор) 10—12%; битум БНД 60/90 11 —13%; вода (подогретая до 60°С) 20—22%. Толщина укладываемого слоя состав ляет 6—8 мм.
Битумные шламы применяют для устройства защитных слоев. Ориентировочное значение толщины замыкающего слоя для жидких смесей составляет 5—10 мм, а для высохших и частично сформировавшихся 3—8 мм. Расход песчаного и грубозернистого (со щебнем) шлама составляет соответственно 8—12 и 15—20 кг/м2.
§ 10.11. Л И Т О Й А С Ф А Л Ь ТО Б Е ТО Н
Литой асфальтобетон представляет собой специально запроектирован ную смесь щебня, песка, минерального порошка и вязкого битума, приго товленную и уложенную в покрытие в горячем состоянии без уплотнения. От горячего асфальтобетона литой отличается большим содержанием мине рального порошка и битума, технологией приготовления и методом укладки. Литой асфальтобетон применяется в качестве дорожного покрытия на автомобильных дорогах, на проезжей части мостов, а также для устройства полов в производственных зданиях.
К положительным свойствам литого асфальтобетона относят: малую массу по сравнению с другими дорожными покрытиями; небольшие зат раты работы на уплотнение; водонепроницаемость. При реконструкции дороги существующее покрытие из литого асфальтобетона может быть снова использовано в полном объеме и почти без добавления новых мате риалов.
К отрицательным свойствам литого асфальтобетона относятся прежде всего вероятность образования вздутий — пузырей на покрытии и трещинообразовании при отрицательной температуре воздуха.
Для приготовления литого асфальтобетона применяют мелкий щебень (крупностью до 10 мм), природный или дробленый песок. Щебень, высевки и песок должны быть высокосортными, как и для обычного горячего асфальтобетона. В минеральном порошке желательно повышенное содер жание частиц мельче 0,071 мм. В качестве вяжущего применяют битумы БН 20/40, БНД 40/60 и природные рысоковязкие битумы.
Литой асфальтобетон подразделяют для устройства покрытий проезжей части (жесткий) и для покрытий тротуаров. Жесткий литой асфальтобетон, в свою очередь, подразделяют на: тип I, содержащий 25—30% по массе асфальтовяжущего вещества и 45—52% щебня; тип II, содержащий соответственно 20—25 и 50—55%.
Тип I изготавливают на битумах с температурой размягчения не ниже 55°С и укладывают в покрытие при 220—240°С без уплотнения, тип II на битумах с температурой размягчения не ниже 52°С и укладывают при 200— 220°С с уплотнением вибрирующими органами асфальтоукладчика.
Примерные зерновые составы минеральной части литого асфальтобетона для проезжей части и тротуаров и содержание в них битума приведены
|
|
|
|
Содержание зерен, %, по массе. мельче, |
мм |
|
Расход |
|||
Область при |
Тип |
|
|
|
|
|
|
|
|
бнтума,% |
10 |
5 |
3 |
1,25 |
0,63 |
0,315 |
0,14 |
0,071 |
но массе |
||
менения |
смеси |
(сверх |
||||||||
|
|
|
|
|
|
|
|
|
|
100) |
П о к р ы т и е |
I |
100 |
6 0 - 7 2 |
5 0 - 5 5 |
3 8 - 4 5 |
3 2 — 38- |
2 6 - 3 2 |
2 1 - 2 6 |
1 8 - 2 0 |
7 ,5 — |
п р о е з ж е й |
|
|
|
|
|
|
|
|
|
8 ,5 |
ч асти |
II |
100 |
5 4 — 60 |
4 5 — 50 |
3 2 — 38 |
2 6 — 32 |
2 0 — 26 |
1 6 - 2 1 |
14— 18 |
6 ,5 — |
|
|
|
|
|
|
|
|
|
|
7 ,5 |
П о к р ы т и е |
I |
|
9 5 - |
7 5 - ' 4 7 — |
3 5 — |
2 5 - |
1 7 - |
9 — |
7 ,0 — |
|
т р о т у а р о в |
|
|
100 |
97 |
80 |
75 |
55 |
33 |
15 |
8 ,5 |
|
II |
9 5 - |
6 5 - |
5 5 — |
3 3 — |
2 9 — |
2 0 — |
12 — |
7 — |
6 ,0 — |
|
|
100 |
80 |
70 |
39 |
40 |
2 8 |
19 |
11 |
7 ,5 |
|
|
|
|
|
|
|
|
Т а б л и ц а |
10.31 |
Показатели
О статоч -н ая п о р и ст о ст ь , % по о б ъ ем у ,
не б о л е е
В о д о н а с ы щ е н и е , % по о б ъ ем у , не б о л ее
П р е д е л п р о ч н о ст и при |
сж а т и и |
при |
5 0 °С , М П а , не м ен ее |
|
|
Г л у б и н а в д а в л и в а н и я |
ш там п а |
при |
4 0 °С , м м , в п р е д е л а х
|
Нормы по типам для покрытий |
|
||
проезжен части |
|
тротуаров |
||
I |
II |
1 |
|
и |
1,0 |
1,0 |
сл 1 |
О |
|
0 ,5 |
1,0 |
1 ,0 — 5 ,0 |
||
— |
1,0 |
0 ,7 |
|
0 ,6 |
1— 6 |
1 - 3 |
|
|
|
П р и м е ч а н и е . Значения показателей свойств нормированы для образцов жесткого литого асфальтобетона кубической формы размером 7,07x7,07x7,07 см, изготовленных штыкованием послойно за 3 раза и заглаживанием поверхности шпателем (тип I) и внброуплотненнем под удельной нагрузкой 0,25—О.ЗХЮ5 Па в течение 20 с (тип II).
в табл. 10.30. Физико-механические свойства литого асфальтобетона должны удовлетворять требованиям табл. 10.31.
Приготовление литых асфальтобетонных смесей может осуществляться
в любых асфальтосмесителях принудительного перемешивания |
псюнион |
ного действия, например Д-597А, Д-508-2. |
порцион |
В связи с удлиненным временем перемешивания и более высокими темпе ратурами нагрева смесей производительность смесителей соответственно снижается.
Транспортирование литых асфальтобетонных смесей к месту уклалки производят в специальных передвижных котлах вместимостью до 8 т оборудованных обогревом и устройством для перемешивания В ппопргг*
транспортирования температура смеси поддерживается 220—240°Г ппи непрерывном перемешивании. ^ ПРИ
Доставленная к месту работ литая смесь выгружается в асЛальтп укладчик, которым и укладывается слоем заданной толщины П пи лянир поверхности покрытия требуемой шероховатости осуществляется втяпТ
нием черного щебня сразу же после прохода асфальтоукладчика |
Л™ |
|
втапливания распределенного по поверхности покрытия чеонпт |
„ Л |
|
используют ручные и легкие жесткобарабанные катки |
Рягупп |
Щ 2 Я |
фракции 5 -1 0 мм составляет 6 -10 кг/м2. Для придания |
шерОХОваТос™ |
покрытию из литого асфальтобетона в ГДР и ФРГ применяют катки с рифле ными вальцами.
Движение автомобилей открывается после достижения покрытием температуры наружного воздуха, но не ранее чем через 5 ч после завер шения работ.
§ 10.12. Д Е ГТЕ Б Е ТО Н
Дегтебетон в зависимости от вязкости битума и температуры смесей при укладке подразделяют на горячий и холодный.
По свойствам дегтебетон уступает асфальтобетону: он обладает меньшей прочностью, теплостойкостью. При этом, обладая повышенной износостой костью дегтевяжущего, дегтебетонное покрытие имеет повышенную шеро ховатость, более высокий коэффициент -сцепления колеса с дорогой, по вышенную безопасность движения. Это связано с меньшей вязкостью дегтей, более слабыми когезионными силами межмолекулярного взаимо действия, наличием летучих составляющих. Летучие вещества в составе дегтя ускоряют срок формирования структуры дегтебетона в покрытии, а также способствуют более интенсивному изменению его свойств. Дегтебетон менее пластичен в сравнении с асфальтобетоном, что также связано с составом и структурой дегтей, которые состоят преимущественно из ароматических углеводородов, которые образуют более жесткие струк турные связи в вяжущих материалах и при пониженных температурах плохо деформируются, вследствие чего в дегтебетонных покрытиях появ ляются трещины. Для повышения прочности, теплоустойчивости и деформативной способности при пониженных температурах дегтебетонов необходимо применять дегти с добавками полимеров, олигомеров и др.
Дегтебетоны в зависимости от вида каменного материала подразде ляют на щебеночный, гравийный и песчаный. По крупности зерен мине рального материала дегтебетон подразделяют на крупно-, средне-, мел козернистый и песчаный. По плотности они делятся на плотные с остаточной пористостью 2,5—5% и пористые с остаточной пористостью 5—10%. Плотные горячие дегтебетоны подразделяют на щебенистые (содержание щебня 40—55%), малощебенистые (содержание щебня 20—40%) и пес чаные. Плотный горячий дегтебетон в зависимости от физико-механических свойств подразделяют на три марки.
Для приготовления дегтебетона применяют те же минеральные мате риалы, что и для асфальтобетона, требования к ним аналогичные, но песок дробленый. В качестве вяжущего применяют дорожный каменноуголь ный деготь: для горячего дегтебетона — Д-6, для холодного — Д-4 и Д-5. Дегти применяют как промышленного изготовления, так и приготовленные непосредственно на асфальтобетонном заводе путем окисления или смеше ния пека с разжижителем (антраценовым маслом, каменноугольной смолой, антраценовыми фракциями и др.).
Расчет состава дегтебетона может быть выполнен так же, как и асфаль тобетона, при этом особое внимание должно быть обращено на тщательный подбор количества дегтя, так как небольшое отклонение содержания его в смеси заметно влияет на свойства дегтебетона.
Для приготовления горячего дегтебетона применяют дегти с вязкостью, значительно меньшей, чем вязкость битума для соответствующего вида асфальтобетона. Пониженная вязкость дегтя обусловливает ослабление внутренних структурных связей, что может быть компенсировано повы шением внутреннего трения минеральной части. Для этого необходимо
применять каменные материалы с зернами угловатой формы и щероховатой поверхностью, а также заменять часть или весь природный песок с окатанными зернами на высевки. Для приготовления дегтебетонных смесей можно применять щебень из более кислых пород (кварцевые песчаники, богатые кварцем граниты и др.).
Плотный дегтебетон применяют для |
устройства покрытий на дорогах |
II— IV категорий. Пористые дегтебетоны |
применяют при устройстве осно |
ваний и нижних слоев двухслойных покрытий на дорогах I—IV категорий. По санитарно-гигиеническим условиям устройство верхних слоев покрытий из дегтебетона разрешено только вне населенных пунктов. При приготов лении дегтебетонных смесей необходимо соблюдать специальные правила техники безопасности.
Дегтебетонную смесь приготавливают в асфальтобетонных установках с мешалками принудительного действия. Вследствие пониженной вязкости дегтя обволакивание им зерен минерального материала протекает лучше, чем при применении битумов, в результате чего сокращается время для смешения материалов. По этой же причине облегчается уплотнение смесей при устройстве покрытий. Коэффициент уплотнения, представляющий собой отношение толщины слоя уложенной смеси до уплотнения к толщине уплотненного покрытия, может быть принят равным 1,3—1,4. Требования
к горячему плотному и пористому дегтебетону |
приведены |
в табл. |
10.32, |
|||
к холодному дегтебетону — в табл. 10.33. |
|
|
|
|
||
|
|
|
|
Т а б л и ц а |
10.32 |
|
Показатели |
Марк!\ плотного дегтебетона |
|
Пористый |
|||
|
|
|
||||
I |
II |
ill |
дегтебетон |
|||
|
Пористость минерального остова, % по |
22 |
22 |
22 |
|||
объему, |
не более |
|
||||
Остаточная пористость, % по объему |
2,5-4,5 |
2,5-5,0 |
2,5-5,0 |
|||
Водонасыщение % по объему |
1,5—3,5 |
1,5—4 |
2 - 4 |
|||
Набухание, % по объему, не более |
1,0 |
1,5 |
2,0 |
|||
Предел прочности при сжатии, МПа, |
|
|
|
|||
не менее: |
|
|
2,2 |
2,0 |
1,6 |
|
при 20°С |
|
|
||||
» |
50° С |
водостойкости, |
не менее |
1,0 |
0,8 |
0,6 |
Коэффициент |
0,85 |
0,70 |
0,60. |
|||
Коэффициент |
водостойкости |
при дли |
0,70 |
0,60 |
0,50 |
|
тельном |
водонасыщении, не менее |
24
5,0-10,0 0 1соо
2,0
0,6
|
|
Т а б л и ц а 10.33 |
|
Норма для холодного дегтебетона, марок |
|
Показатели |
1 |
2 |
|
||
Пористость минерального остова, % по |
объему, |
|
не более |
20 |
22 |
Остаточная пористость, % по объему |
6—10 |
6— 12 |
Водонасыщение, % по объему |
5—9 |
5—11 |
Набухание, % по объему, не более |
3 |
4 |
Предел прочности при сжатии, МПа, не менее, при |
0,7 |
|
температуре 20°С |
1,2 |
|
Коэффициент водостойкости при длительном водо |
|
|
насыщении, не менее |
0,65 |
0,50 |
Коэффициент водостойкости при длительном водо |
|
|
насыщении, не менее |
0,50 |
0,40 |
Слеживаемость по числу ударов, не более |
10 |
10 |
Вид смеси |
Марка дегтя |
|
Температура, °С |
|
|
|
|
||
|
|
минерального |
|
|
|
|
материала |
|
|
Горячий |
Д-5 |
95— 110 |
80—90 |
95—110 |
Холодный |
Д-6 |
100— 115 |
80— 100 |
|
Д-4 |
80—95 |
70—90 |
80—95 |
|
|
Д-5 |
|||
|
|
|
|
укладки
смеси
70—90
Не ниже 5° весной, не ни же 10° осенью
При производстве дегтебетонной смеси необходимо строго соблюдать установленный температурный режим, так как деготь более чувствителен
кизменению температуры, чем битум (табл. 10.34).
ВХАДИ разработан вариант технологии, значительно упрощающий приготовление дегтебетонных смесей. Гранулированный или измельченный глыбовый пек в холодном виде в необходимом количестве вводится в мешал ку, в которую предварительно загружаются горячие каменные материалы. Через некоторое время (1—1,5 мин) после расплавления пека в мешалку вводят холодное каменноугольное масло или обезвоженный деготь марок Д-4, Д-5. После перемешивания готовую дегтебетонную смесь выгружают в транспортные средства.
Контроль за изготовлением дегтебетонной смеси на заводе и при устройстве дегтебетонного покрытия, а также методы испытания дегте бетона такие же, как и асфальтобетона.
§ 10.13. Б И Т У М О М И Н Е Р А Л Ь Н Ы Е И Б И Т У М О ГР У Н Т О В Ы Е СМ ЕС И И Ч Е Р Н Ы Й Щ Е Б Е Н Ь
Битумоминеральные смеси представляют собой материал, приготовлен ный путем смешения в смесительных установках в нагретом состоянии щебеночных (гравийных) материалов., природного или дробленого песка, минерального порошка и битума, взятых в определенных соотношениях. В зависимости от марки битума и температуры смесей при укладке в пок рытие их подразделяют на следующие виды (табл. 10.35).
Битумоминеральные смеси подразделяют на крупнозернистые с размером до 40 мм, среднезернистые — до 20, мелкозернистые — до 15 (10), пес чаные — до 5 мм.
Для приготовления битумоминеральных смесей можно применять мине ральные материалы более низкого качества, чем для соответствующих видов асфальтобетона. Так, марка щебня из изверженных и метамор фических горных пород по дробимости при сжатии в цилиндре допускается не ниже 600, а из осадочных — не ниже 300, износ в полочном барабане
идля щебня из изверженных пород — не более 55%, из осадочных — 60%.
Вкачестве минерального порошка, кроме известнякового, допускаются отходы асбестоцементного производства, золы уноса, фильтр-прессные отходы, пыль уноса цементных заводов.
Горячие и теплые смеси по структуре подразделяют на плотные и по
ристые. Плотные должны содержать в своем составе частицы мельче 0,071 мм, в пористых эти частицы не обязательны.
На юге УССР накоплен значительный опыт применения битумоминераль ных смесей для устройства покрытий на -дорогах I и II категорий. Смеси приготавливают из однородных по минералогическому составу дробленых
известняков и диоритов, в ряде случаев без добавления минерального порошка. Вяжущим служит битум БНД 60/90 или БН 60/90, пластифи цированный каменноугольным дегтем Д-3 до пенетрации 100. Деготь
является также добавкой, улучшающей обволакивание минеральных зерен вяжущим.
Покрытия устраивают из битумоминеральных смесей, составы которых приведены в табл. 10.36.
Эти смеси обладают следующими свойствами: предел прочности при сжатии при 20°С — не менее 2,5 МПа, при 50°С — не менее 1,0—1,2 МПа; коэффициент водостойкости — не ниже 0,85; водонасыщение — 3—6%; остаточная пористость — 4—8%.
Характерной особенностью битумоминеральных смесей, применяемых в Крыму, являются повышенное содержание щебня (50—65%), ограничен ное количество зерен мельче 0,071 мм и как следствие повышенная остаточ ная пористость (до 9%). В таких битумоминеральных смесях формируется структура, которая обеспечивает плотный контакт по щебенкам, образую щим пространственный каркас. Этим объясняется высокая сдвигоустойчивость покрытий на автомобильных дорогах с большими уклонами и интенсивным движением.
Водостойкость покрытия, несмотря на большое водонасыщение (до 7%), вполне удовлетворительна,, что объясняется малым количеством осадков. Через 2—3 мес эксплуатации покрытия из битумоминеральной смеси водонасыщение снижается до 3—5%.
Битумогрунтовые и дегтегрунтовые смеси. Применение грунтов и при родных гравийных или песчаных материалов в качестве минеральной части битумо- и дегтегрунтовых смесей имеет большое экономическое значение.
В зависимости от предъявленных к смесям требований и качества исходных материалов и другие природные материалы могут быть исполь
зованы в смесях в естественном виде или с добавками различных |
мате- |
Т а б л и ц а |
Ю.35 |
Температура смеси
Виды смесей Марка битума при укладке, °С, не ниже
Горячие
Теплые
Теплые
Холодные
БНД 40/60, |
БНД 60/90, БНД 90/130 |
120 |
|
БНД |
130/200, БНД 200/300 |
80 |
|
СГ |
130/200, МГ 130/200 |
50 |
|
СГ 70/130, |
МГ 70/130 |
10 |
|
|
|
|
|
|
|
|
|
Т а б л и ц а |
10.36 |
|
|
|
|
|
|
|
|
|
|
|
|
При |
|
|
Содержание зерен минерального материала, % данного |
|
|
мерный |
||||||
Состав |
|
|
|
|
размера, мм |
|
|
|
|
|
расход |
|
|
|
|
|
|
|
|
|
|
|
биту- |
25 |
20 |
15 |
10 |
5 |
3 |
1,25 |
0.63 |
0,15 |
0.14 |
0,071 |
ма, % |
Средне |
9 5 - |
87— |
7 6 - |
60— |
3 5 - |
2 4 - |
13 - |
8 - |
4— |
2—8 |
зернис |
100 |
93 |
84 |
70 |
50 |
38 |
24 |
17 |
12 |
|
тый |
_ |
— |
95— |
7 0 - |
40— |
2 8 - |
17— |
\ 2 - |
7— |
3—12 |
Мелко |
||||||||||
зернис |
|
|
100 |
82 |
50 |
42 |
30 |
24 |
18 |
|
тый
0 |
СП |
|
1 |
0 |
ОО |
|
1 |
4,0—
6,5
5,5—
6,5
риалов (песка, гравия, щебня и др.). Для изготовления этих смесей при-
меняют вязкие и жидкие вяжущие.
Скелетные битумо- и дегтегрунтовые смеси приготавливают из грунтов со скелетными добавками. К таким смесям относят черный грунтощебень, черный грунтогравий и др. Эти смеси, как правило, приготавливают на жидких битумах смешением материалов на полотне дороги при помощи передвижных смесителей, фрез, автогрейдеров.
Нескелетные битумо-и дегтегрунтовые смеси приготавливают путем обработки грунтов органическими вяжущими. Горячие смеси с применением вязких битумов обладают более высокими физико-механическими свойствами и приближаются по свойствам к песчаному асфальтобетону. Их приготав ливают из супесчаных и суглинистных грунтов путем обработки жидким битумом или дегтем. Наилучшие результаты получаются при оптимальном гранулометрическом составе грунта. Эти смеси применяют в горячем сос тоянии для устройства оснований, в отдельных случаях для верхних слоев покрытий облегченного типа.
Битумо- и дегтегрунтовые смеси должны удовлетворять требованиям, приведенным в табл. 10.37. Лучшими физико-механическими свойствами обладают смеси, изготовленные из супесчаных грунтов. При использовании песков необходима добавка пылеватых фракций грунта в таком количестве, чтобы пылеватых частиц в минеральной смеси содержалось около 25—30%.
В связнных |
грунтах |
имеет значение их агрегатность (наличие комочков, |
|||||
сцементированных .коллоидноглинистым веществом). |
|
|
|||||
|
|
|
|
|
|
Т а б л и ц а 10.37 |
|
|
|
|
Грунты, укрепленные |
|
|
||
|
жидкими битумами или |
жидкими битумами, дегтями |
битумными |
||||
|
дегтями |
с примене»тем |
добавок |
эмульсиями |
|||
Показатели |
|
|
|
|
|
|
|
|
Нижние |
Верхние слои |
Нижние слон |
Верхние слои |
Нижние |
Верхние |
|
|
слои |
оснований или |
осно |
|
оснований |
слои |
слои |
|
оснований |
покрытий |
ваний |
или покрытий |
оснований |
оснований |
|
Предел проч |
|
|
|
|
|
|
|
ности при сжа |
|
|
|
|
|
|
|
тии образцов, |
|
|
|
|
|
|
|
МПа, не менее: |
|
|
|
|
|
|
|
сухих при |
Не опреде |
|
Не опреде |
|
|
Не опреде |
|
20°С |
ляется |
0,8 |
ляется |
|
1,2 |
ляется |
1,5 |
сухих при |
|
|
|
|
|
|
|
50°С |
То же |
0,5 |
То же |
|
0,7 |
То же |
0,8 |
водонасы |
|
|
|
|
|
|
|
щенных |
|
|
|
|
|
|
|
при 20°С |
|
0,4 |
|
|
0,6 |
|
0,7 |
Капиллярное |
|
|
|
|
|
|
|
водонасыщение, |
|
|
|
|
|
|
|
% по объему, |
6 |
Не опреде |
4 |
Не опреде |
5 |
Не опреде |
|
4е более |
|
ляется |
|
ляется |
|
ляется |
|
Набухание, . |
|
|
|
|
|
|
|
%, не более |
Не опреде |
6 |
Не опреде |
|
4 |
Не опреде |
4 |
|
ляется |
|
ляется |
|
|
ляется |
|
Пр и ме ч а н и я . |
I. Показатели |
даны для образцов 7-суточного |
возраста при |
укреплении битумами, |
|||
и применении добавок, для 10-суточного возраста — при укреплении битумными эмульсиями. |
|
||||||
2. Набухание в IV и V дорожно-клнматнческнх зонах не определяется. |
V дорожно- |
зонах — при |
|||||
3. Предел прочности при сжатии водонасыщенных образцов в |
IV |
||||||
капиллярном водонасыщении образцов. |
|
|
|
|
|
||
4. Грунты, укрепленные жидкими |
битумами и дегтями без добавок, применяют в |
III —V дорожно-клнматнческнх |
зонах преимущественно в нижних слоях оснований, а также в покрытиях на дорогах с небольшой интенсивностью движения.
|
Обработка материалов |
|
Показатели |
|
жидки и битумами или |
жидкими битумами или |
дегтями с добавками или |
|
|
дсгтямн (для образцов |
битумными эмульсиями |
|
7-суточного возраста) |
(для образцов |
|
|
10-суточного |
|
|
возраста) |
Предел прочности при сжа |
|
|
тии образцов при 20°С, МПа, |
|
|
не менее: |
|
|
сухих |
0,8 |
1,5 |
водонасы щенных |
0,5 |
0,9 |
Набухание, %, не более |
3 |
2 |
Грунтогравийные и грунтощебеночные смеси, укрепленные органичес кими вяжущими материалами, должны удовлетворять требованиям, при веденным в табл. 10.38.
Черный щебень. Щебень, обработанный органическим вяжущим, назы вается черным. Этот материал применяют для устройства покрытий на дорогах II—IV категорий, а также для устройства оснований.
По вязкости битума и способу укладки черный щебень разделяют на три вида: горячий, изготавливаемый на битумах БНД 60/90, БНД 90/130 и дегте Д-6 и укладываемый в горячем состоянии при 120—140°С; теплый, изго тавливаемый на битумах БНД 130/200, БНД 200/300, СГ 130/200 и дегте Д-5 И укладываемый в теплом состоянии при 50—80°С; холодный, изготавли ваемый на жидких битумах МГ 130/200, МГ 70/130 и дегте Д-4 и уклады ваемый в холодном состоянии в сухую погоду при температуре воздуха 10—25°С. Для приготовления черного щебня применяют щебень, получен ный из горных пород с прочностью не ниже 80 МПа.
Обработанный вяжущим щебень по крупности делят на: крупный размером 40—25 мм; средний — 25—15; мелкий— 15—5 мм; высевки — мельче 5 мм. Количество вяжущего в смеси в зависимости от крупности щебня и свойств (плотности, характера поверхности) принимают в пре делах 2—4% по массе.
Черный щебень приготавливают в смесительных установках с прину дительным или свободным перемешиванием. Технология устройства слоев одежды из черного щебня включает: подготовку основания, распределе ние щебня фракции 40—25 мм, уплотнение, россыпь щебня фракции 15—25 мм, уплотнение, расклинцовку поверхности мелким щебнем 15—5 мм И уплотнение.
§ 10.14. РЕГЕНЕРАЦИЯ АСФ АЛЬТО БЕТО НА
Одним из резервов снижения стоимости дорожного строительства явля ется продление срока службы асфальтобетонного покрытия путем восста новления первоначальных свойств непосредственно в покрытии или путем повторного использования старого материала для приготовления асфаль
тобетонных и других смесей.
При эксплуатации дорожного покрытия происходит старение битума, Приводящее к повышению его вязкости, потере пластичности и проявлению хрупкости. Все это приводит к ухудшению свойств асфальтобетона, пони жается деформативная способность материала, повышается жесткость.
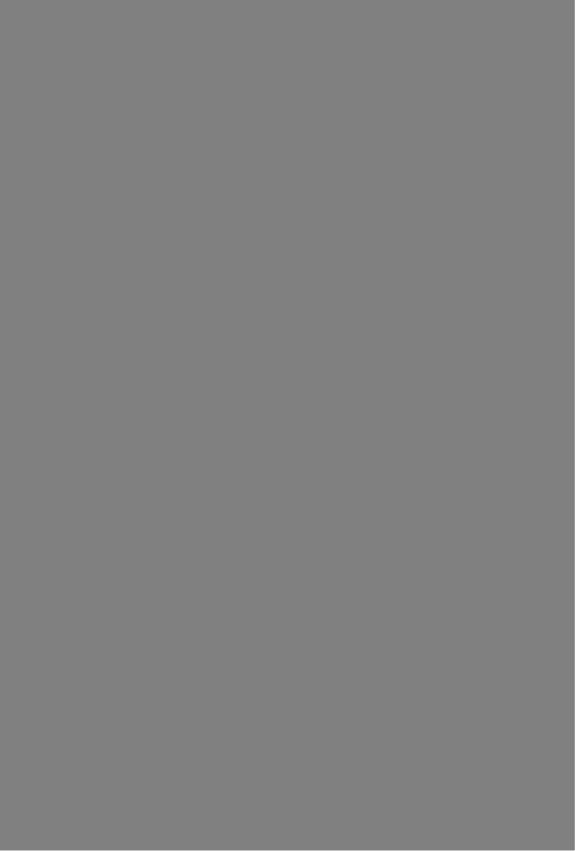
k |
5 |
6 |
Рис. 10.21. Схема машины для восстановления асфальтобетонных покрытий:
/ — нагревательные панели; 2 — бункер |
для новой смеси; 3 — транспортер; |
4 — бак для топлива; 5 резервуары |
с сжиженным газом; 6 двигатель; 7 |
взрыхляющая балка; 8 — шнековый |
распределитель; 9 — разравнивающий |
|
отвал; 10 — трамбующая балка |
|
Имеются и более совершенные машины для ремонта и восстановления асфальтобетонных покрытий. Одной из последних моделей является «Репавер»— самоходный агрегат на пневматических шинах длиной около 13 м и массой до 30 т (рис. 10.21). В головной части машины находится бункер, принимающий новую асфальтобетонную смесь. За ним расположена первая группа панелей инфракрасного излучения. Позади передней управляемой оси машины расположена вторая группа панелей того же назначения. За ней находится взрыхляющая балка, разделенная на четыре сегмента, каждый сегмент имеет пять рядов взрыхляющих ножей. Сегменты неза висимо друг от друга могут быть переставлены на высоте. За балкой расположены шнековый распределитель и разравнивающий отвал. За ними следует третья группа панелей инфракрасного облучения. Позади задней приводной оси расположено устройство для новой с'меси, которое состоит из двух шнеков и комбинированной вибрационной и трамбующей балки.
Расположенный в передней части бункер соединен с комбинирован ной балкой проходящим вдоль всего агрегата подогреваемым инфра красными горелками транспортером.
Агрегат работает следующим образом. Первая и вторая группы панелей разогревают асфальтобетонное покрытие. Блок с элементами рыхления и рядами ножей взрыхляет разогретый слой покрытия, который перемеши вается расположенным за ним шнековым распределителем и распределяется им равномерно по всей ширине полосы. Отвалом смесь разравнивается, и одновременно устанавливается норма нанесения новой смеси. Третья группа панелей разогревает спланированную смесь до заданной темпера-
туры.
Транспортер подает смесь из бункера к комбинированной балке, где смесь равномерно распределяется по всей площади старой спланирован ной смеси. После этого оба слоя подгоняют под существующий профиль и предварительно уплотняют вибрационной и трамбующей балкой. Оконча тельное уплотнение осуществляется самоходными катками.
Асфальтобетонное покрытие может быть взрыхлено на глубину 4 см. Полученный при этом материал используется частично или полностью для восстановления покрытия. Ремонтируемый участок асфальтобетонного покрытия при ширине 3,75 м может составлять ежедневно около 1000 м. В результате повторного разогрева асфальтобетона вязкость битума в нем
возрастает на 10—15%.
В СССР имеется опыт регенерации асфальтобетона в установке. На реконструируемом участке городской дороги старое асфальтобетонное
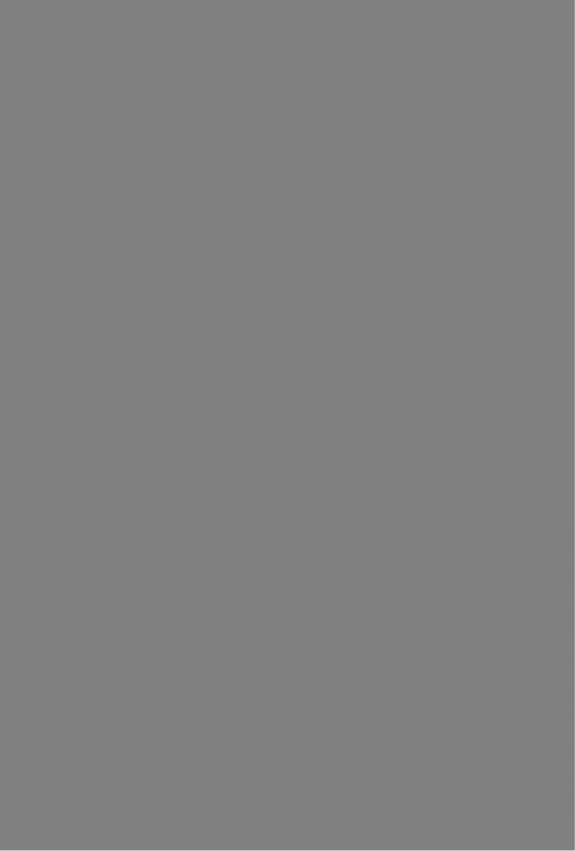
Первый барабан работает по системе прямотока, а второй — противо тока, что позволяет в начальный период при подаче холодного материала в первый барабан поддерживать высокую температуру (до 700°С) без опа сения перегрева, а в стадии завершения разогрева — во втором барабане довести температуру до оптимальной, создающей возможности разогрева асфальтобетонной смеси до 150—160°С.
Из разгрузочной камеры второго барабана разогретая асфальтобетонная смесь поступает на грохот, где из смеси отделяются частицы крупнее 40 мм (отходы). Асфальтобетонная смесь и отходы поступают после грохота в соответствующие отсеки двухсекционного бункера. Из бункера асфальто бетонная смесь и отходы попадают в скиповый подъемник, который подает их на промежуточную бункерную эстакаду, состоящую из приемной воронки и двухсекционного накопительного бункера.'Из бункера асфальтобетон ная смесь подается в автомобили и транспортируется к месту производства работ.
К переработке допускается асфальтобетон из зернистых и песчаных сме сей, поставляемый и складируемый отдельно по указанным типам. Куски старого асфальтобетона должны быть без загрязнения побочными мине ральными включениями. Допускается содержание песчаных примесей до 30% по массе, а глинистых — не более 0,5%. Переработка асфальтобетона производится с добавлением щебня до 25% по массе или песка до 15% в зависимости от вида исходного материала.
Регенерированные смеси по содержанию в них щебня подразделяются на два типа: тип I — с содержанием зерен щебня или гравия крупнее 5 мм от 20 до 30% по массе: тип II — то же, от 30 до 65% по массе.
Готовая асфальтобетонная смесь должна быть однородной; не допус кается наличие слежавшихся комьев, сгустков вяжущего, отдельных зерен, не покрытых битумом. Свойства регенерируемого асфальтобетона должны соответствовать свойствам пористого асфальтобетона и приближаться по свойствам к плотному асфальтобетону типа А и Б III марки.
Регенерированные смеси применяют для устройства нижнего слоя двух слойного асфальтобетонного покрытия. Для дорог местного значения, авто
мобильных |
стоянок, а также тротуаров допускается устройство верх |
него слоя |
покрытия из регенерированных асфальтобетонных смесей |
I типа.
Охрана труда. Основные требования охраны труда при производстве асфальтобетона и других битумоминеральных материалов изложены в «Пра вилах техники безопасности при строительстве, ремонте и содержании ав томобильных дорог» (М., Транспорт, 1978), а также в «Руководстве по строительству дорожных асфальтобетонных покрытий» (М., Транспорт, 1978).
Особенностью производства асфальтобетона является работа с горячими минеральными материалами, битумом и асфальтобетонной смесью. Поэтому необходимо строго соблюдать температурный режим, чтобы избежать вос пламенения битума, разжижителей, пластификаторов. При работе с ка менноугольным дегтем и пеком необходимо соблюдать дополнительные требования техники безопасности и охраны труда исходя из их токсичности
и канцерогенности.
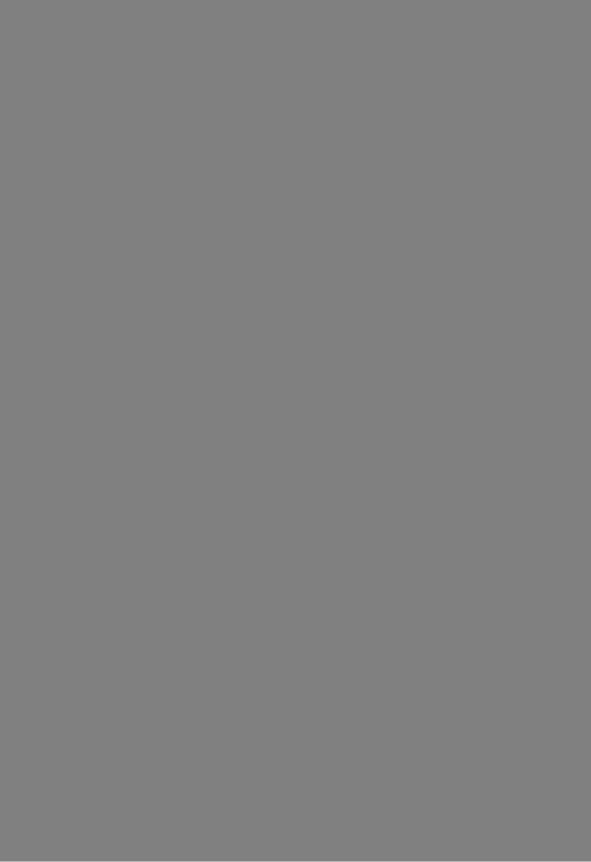
Толь кровельный беспокровный — рулонный картон, пропитанный ка менноугольным дегтем с температурой размягчения не ниже 34°С; после отжатия излишнего дегтя на валках машины ленту охлаждают и скаты вают в рулоны. Толь беспокровный выпускают рулонами шириной 60—105 см, общей площадью 20 м2 и массой 8—20 кг (см. табл. 11.2).
Толь покровный применяют в верхнем слое мягкой кровли. В качестве подкладочного материала служит толь беспокровный. Для увеличения срока службы кровли верхний слой периодически покрывают горячим или разжиженным дегтем с последующей посыпкой мелкозернистым песком. Толь беспокровный применяют и как гидроизоляционный материал.
Гудрокамовый или гидроизоляционный рубероид (РГМ) изготавливают путем пропитки с обеих сторон кровельного картона гудрокамом (продуктом окисления в специальных установках смеси нефтебитума с антраценовым маслом). Гудроком — вещество черного цвета с раковистым изломом и тем пературой размягчения 65—75°С. Гудрокамовый кровельный материал выпускают в рулонах шириной 65—105 см массой 30 кг и площадью 20 м2 с количеством пропиточной массы не менее 600 г/м2. Он гибок и теплостоек; обладает водонасыщением при 35°С не более 2%, прочностью при разрыве стандартной полоски не менее 3 МПа.
Дегтебитумные кровельные материалы изготавливают способом про питки кровельного картона дегтем, а затем покрытием его с обеих сторон нефтяным битумом с последующей минеральной посыпкой: крупнозернистой (ДББ) или чешуйчатой (ДБЧ) для верхних слоев кровельного ковра и мелкозернистой (ДБМ) для подкладочных слоев гидро- и пароизоляции
(см. табл. 11.2).
Дегтебитумные кровельные материалы выпускают шириной полотна 65—105 см и площадью 20 м2 Свойства этих материалов следующие: марка ДГ-350, масса рулона не менее 30 кг, количество покровной массы не менее 600 г/м2, водонасыщение при 35°С не менее 5%, прочность при растяжении стандартной полоски не менее 3 МПа. Материал теплостоек,
гибок.
Листовые материалы изготавливают на основе битумов. Они представ
ляют собой |
фасонные листы |
марок ЛБ-500 |
и ЛБ-600 |
с температурой |
||||
|
|
|
|
|
|
|
Т а б л и ц а 11.1 |
|
|
Водонепроницаемость |
|
|
Теплостойкость |
|
|||
|
|
|
|
|
|
|||
|
при |
гидростатическом |
Разрывной |
|
|
|
||
|
|
давлении |
груз при |
|
|
|
||
|
Марка |
|
|
растяже |
темпера |
время |
потеря |
|
Материал |
|
|
нии полос |
|||||
|
время по |
тура испы |
испыта |
в массе %, |
||||
|
давление, |
ки |
шири |
|||||
|
пытаиня, |
ной 50 мм, |
таний, °С |
ния, ч |
не более |
|||
|
|
Па |
мин, не ме |
|
|
|
||
|
|
кН, не ме |
|
|
|
|||
|
|
|
нее |
|
нее |
|
|
|
|
|
|
|
|
|
|
|
Рубероид с по сыпкой:
крупнозер
нистой
чешуйчатой мелкоми-
неральной
Пергамин
Гидроизол
Р К -4 2 0 |
17 |
10 |
3 4 0 |
8 0 |
Р К -3 5 0 |
17 |
10 |
3 2 0 |
8 0 |
Р Ч -3 5 0 |
17 |
10 |
3 2 0 |
80 |
Р Ч -3 5 0 |
17 |
10 |
3 2 0 |
8 0 |
Р М -3 5 0 |
17 |
10 |
3 2 0 |
8 0 |
Р П -2 5 0 |
14 |
5 |
180 |
8 0 |
П -3 5 0 |
|
|
2 7 0 |
|
|
|
220 |
|
|
П -3 0 0 |
|
|
|
|
|
|
|
3 5 0 |
|
Г И -Г |
300 |
|
Г И -К |
||
|
2 |
0 ,5 |
2 |
0 ,5 |
2 |
0 ,5 |
2 |
0 ,5 |
2 |
0 ,5 |
2 |
0 ,5 |
|
|
|
|
Т а б л и ц а 11.2 |
|
|
|
Водонопрсшицлс- |
|
Разрывное усилие |
|
|
|
мость под давлени |
Водопоглощение |
||
|
|
при растяжении по |
|||
Материал |
Марка |
ем столба воды вы |
при атмосферном |
||
сотой 5 см, сут, |
давлении за 24 ч. |
лоски шириной |
|||
|
|
не менее |
%, не более |
50 мм, Н, не менее |
|
Толь с посыпкой крупно |
ТВК-420 |
|
|
300 |
|
ТВК-350 |
|
|
|||
зернистой |
|
|
380 |
||
песочной |
ТП-350 |
|
|
||
|
|
280 |
|||
Толь кровельный |
ТК-350 |
6 |
|
||
25 |
300 |
||||
ТГ-350 |
|||||
беспокровный |
|
|
400 |
||
Дегтебитумные |
|
|
|
||
ДБ-350 |
|
|
|
||
материалы |
|
|
300 |
||
|
|
|
размягчения пропиточной массы не ниже 6 0 °С . Неармированные плиты изготавливают прессованием горячей мастики или горячей асЛальтпА™
ной смеси, армированные - из тех же смесей, но армируют предварительно пропитанной битумом стеклотканью или металлической сеткой Л и с т о в
материалы применяют для лицевых покрытий кровли, заполнения леЛпп мационных швов. дефир-
§11.2 ГИДРОИЗОЛЯЦИОННЫЕ МАТЕРИАЛЫ
Сп ец и альн ы е ги др ои зол я ц и он н ы е м атериалы д ел я т на обмазочные окле
ечные и пластичные. Д л я |
о б м а зо ч н о й |
ги др ои зол я ц и и прим еняю т |
хол одн ы е |
|||||||||||||||||||||
окраски |
и гор яч и е обм а зк и . В к ач еств е хол одн ы х ок р асок |
и сп ол ьзую т |
строи |
|||||||||||||||||||||
тельны е битум ы |
м арок |
БН |
5 0 /5 0 и Б Н 7 0 /3 0 , р а зж и ж е н и е л егк оул етуч и в аю - |
|||||||||||||||||||||
щ им ися |
р аствор и тел я м и , а |
т а к ж е дегтев ы е |
лак и . |
|
|
|
|
|
|
|
J |
|
||||||||||||
Д л я |
горячи х |
о б м а зо к |
|
п ри м ен яю т |
м астики,' наприм ер |
|
|
см есь |
би тум а |
|||||||||||||||
с м елким |
асбестов ы м |
волокном |
( 2 0 — 3 0 % ) . |
Д л я |
л уч ш его |
|
сц еп лен и я по |
|||||||||||||||||
в ер хн ость, |
на к оторую |
н ан оси тся |
о б м а зк а , |
п р едв ар и тел ьн о |
|
п одсуш и в ается |
||||||||||||||||||
и п одгр ун тов ы вается р а зж и ж ен н ы м |
би тум ом |
или эм ул ьси ей |
Г орячие о б м а з |
|||||||||||||||||||||
ки н ан ося т |
тонким |
р авном ерны м |
сл оем |
в горячем состоян и и |
|
К |
оклеечны м |
|||||||||||||||||
ги др ои золяц и он н ы м |
м атер и ал ам |
|
отн осят |
ги др ои зол , |
ткани |
|
ги д о о и зо л я |
|||||||||||||||||
ционны е, |
м ет ал л ои зол . |
|
|
|
|
|
|
|
|
|
|
|
|
|
|
|
|
|
д ^ и л и л я - |
|||||
Гидроизол — асбестов ы й |
или |
а сбестоц ел л ю л озн ы й |
рулонны й |
картон |
||||||||||||||||||||
пропитанны й неф тяны м |
би тум ом с тем п ер атур ой |
р азм я гч ен и я |
|
не н и ж е 50°с’ |
||||||||||||||||||||
Г и др ои зол |
п рим еняю т дл я |
м н огосл ой н ой |
ги др ои зол я ц и и |
п одзем н ы х |
эл ем ен |
|||||||||||||||||||
тов со о р у ж ен и й . |
Э тот |
м атери ал |
б о л ее |
д ол гов еч ен , |
чем |
р у б ер о и д |
|
|
||||||||||||||||
Ткани гидроизоляционные |
(х л о п ч а т о б у м а ж н ы е, |
дж у т о в ы е |
|
асб ест о в ы е) |
||||||||||||||||||||
пропитанны е неф тяны м |
би тум ом с тем п ер атур ой |
р азм я гч ен и я |
|
не н и ж е 50°С |
||||||||||||||||||||
п рим еняю т |
д л я м н огосл ой н ой |
ги др ои зол я ц и и |
в |
соч етан и и |
с |
ги др ои зол ом |
||||||||||||||||||
дл я п одзем н ы х эл ем ен тов |
со о р у ж ен и й , |
т р у б о п р о в о д о в |
и |
д л я |
со о р у ж ен и й |
|||||||||||||||||||
п од в ер га ю щ и х ся |
ударны м |
в оздей ств и я м . |
|
|
|
|
|
|
|
|
|
|
|
|
|
|||||||||
Металлоизол — ал ю м и н и ев ая ф ольга толщ и н ой 0 ,2 мм, покры тая с об еи х |
||||||||||||||||||||||||
стор он неф тяны м |
би тум ом |
с т ем п ер атур ой |
р азм ягч ен и я |
не |
н и ж е |
6 5 °С |
Э тот |
|||||||||||||||||
м атери ал |
прим еняю т |
дл я ги др ои зол я ц и и |
п одзем н ы х |
эл ем ен тов |
со о р у ж ен и й |
|||||||||||||||||||
и ги др отехн и ческ и х со о р у ж ен и й |
1-го к л а сса . У клады вая м етал л ои зол |
в д е л о |
||||||||||||||||||||||
н ео б х о д и м о |
сл еди ть |
за |
тем , |
чтобы |
не |
п овреди ть |
тонкий |
слой |
би тум н ой |
|||||||||||||||
о б м а зк и , |
которая |
за щ и щ а е т |
м еталл |
от |
к орр ози и . |
|
|
|
|
|
|
|
|
J |
|
|||||||||
К пластичны м |
ги др ои золяц и он н ы м |
м атер и ал ам |
отн ося т |
|
изол |
б л и зпл |
||||||||||||||||||
бор ул и н . |
|
|
|
|
|
|
|
|
|
|
|
|
|
|
|
|
|
|
|
|
|
’ |
Н |
’’ |
Изол изготовляется из резинобитумного связующего, полученного тер момеханической обработкой девулканизированной резины, нефтяного биту ма, минерального наполнителя и антисептика с последующей прокаткой массы на каландрах в полотнища заданной толщины. Применяется изол для оклеечной гидроизоляции фундаментов и других конструкций зданий и сооружений.
Бризол получается прокаткой на каландрах массы, приготовленной сме шиванием нефтяного битума, дробленой резины, асбестового волокна и плас тификатора. Используется он для антикоррозионной защиты металлических трубопроводов.
Барулин изготовляется из смеси мелкого асбестового волокна и нефтя ного битума с последующей прокаткой на каландрах в полотнища площадью 5 м2. Борулин применяют для Гидроизоляции и заделки температурных швов в цементобетонных дорожных покрытиях.
§ 11.3. ПРИКЛЕЕННЫЕ МАСТИКИ
Мастиками называют смеси нефтяных битумов или дегтей с тонкоизмельченными минеральными или органическими наполнителями.
По виду связующего мастики подразделяют на битумные, битумно-поли
мерные и |
битумно-резиновые, а по способу |
применения — на горячие |
и холодные. |
битумные мастики разогревают до |
160— 180°С, а дегтевые — |
Горячие |
до 130—150°С. При нанесении на поверхность они должны образовать ровный слой толщиной до 2 мм. При 18°С горячие мастики должны обла дать твердой консистенцией, а при 100°С — не вспениваться (для этого их обезвоживают) и сохранять однородность. При приготовлении и исполь зовании мастик необходимо строго соблюдать правила техники безопасно сти и противопожарные мероприятия.
Необходимая теплостойкость мастик обеспечивается введением в них минерального порошка, количество которого устанавливается лаборатор ным подбором и бывает примерно в следующих пределах: волокнистого до 20%, пылевидного до 30 и комбинированного (волокнистого + пылевид ного) до 40%. В качестве минерального порошка применяют те же мате риалы, что и для изготовления асфальтобетонных смесей. При лабораторном подборе состава мастик определяют их теплостойкость при 45°С, гибкость при 20°С, клеящую способность и однородность (табл. 11.3).
Холодные мастики представляют собой вязкую смесь разжиженного зеленым маслом или лаккойлем нефтяного битума и минерального порошка. Они должны быть однородны по составу, вязкими при 18°С, обладать
способностью при перемешивании разжижаться |
и загустевать в состоянии |
|||
|
|
|
|
Т а б л и ц а 11.3 |
Мастики |
Состав |
А\арка |
Теплостой- |
Гибкость — диа |
кость°С |
метр стержня, мм |
|||
Битумные |
Нефтяной битум, наполни |
МБК-Г-65 |
65 |
15 |
|
тель, антисептик |
МКБ-Г-75 |
75 |
20 |
|
|
МБК-Г-85 |
85 |
30 |
|
|
МБК-Г-90 |
90 |
35 |
Дегтевые |
Каменноугольные, дегтс- |
МДК-Г-50 |
50 |
25 |
|
продукты, наполнитель |
МДК-Г-60 |
60 |
30 |
|
|
МДК-Г-70 |
70 |
40 |
покоя. Качество холодных мастик определяют теплостойкостью при 70°С, консистенцией при 20°С, гибкостью при 10°С, липкостью при 20°С и сро ками схватывания в сутках. Качество мастик (их липкость) может быть улучшено введением в битум или деготь до 10—15% отходов коксохими ческого производства —1нефтеполимерной смолы (продукт переработки кубовых остатков пиролизной смолы) или каменноугольной смолы (про дукт кубовых остатков ректификации сырого бензола).
Битумно-полимерные мастики содержат добавку каучука или синтети ческой смолы, придающей эластичность на морозе и теплостойкость.
Битумно-резиновые мастики представляют собой сплав из битума, порошка резины и некоторых добавок. Их применяют как горячими, так и холодными с растворителем.
Для огрунтовки поверхности применяют битумные и дегтевые грунтовки, которые представляют собой жидкий раствор битума или каменноуголь ного растворителя (зеленого масла, лаккойля, полихлоридов бензола, керо сина; керосин применяют только для битума). Для огрунтовки свежеуложенной цементной стяжки могут быть использованыгрунтовки сос
тавов: строительный битум БН 70/30 |
или |
БН 90/10 — 40% и |
зеленое |
|||
масло — 60%; |
битум БН 50/50 — 55% |
и |
зеленое |
масло — 45%; |
битум |
|
70/30 или БН |
90/10 — 35% и лаккойль — 65%; |
пек — 45% и |
зеленое |
|||
масло — 55%. |
Для огрунтовки созревшей цементной стяжки применяют |
|||||
более вязкие грунтовки, |
например битум БН 70/30 |
или БН 90/10 — 50% |
||||
и зеленое масло— 50%. |
Огрунтовку металлических поверхностей |
произ |
водят менее вязкими составами, например битум БН 70/30 или БН 90/10 — 30% и зеленое масло — 70%. В последние годы для огрунтовки поверх ности свежеуложенной цементной стяжки применяют также битумные или дегтевые эмульсии.
К работам с мастиками и грунтовками (в особенности при их изготов лении) рабочие допускаются только после ознакомления с правилами тех ники безопасности и противопожарной безопасности.
При приготовлении мастики в целях противопожарной безопасности необходимо загружать котел не более чем на 2/3 по высоте, запасы топли ва и растворителей хранить в отведенных местах на расстоянии не менее 25 м от котла, при введении растворителя в котел предварительно удалить топливо из топки и затушить его водой. Огнетушители и ящики с песком и лопатами должны быть вблизи котлов и иметь свободный доступ к ним. В случае вспышки в котле необходимо закрыть котел металлической крышкой и прекратить топку, вытекающую из котла массу засыпать пес ком и залить пеной из огнетушителя. Нельзя горящую массу заливать водой. Для курения должны быть оборудованы специальные места. Обслу живающий персонал должен быть снабжен специальной одеждой и рука вицами. До начала работы надо смазать лицо и руки пастой (смесь окиси цинка, талька и воды в равных частях и 3% салола). После работы необ ходимо вымыть лицо и руки горячей водой с мылом.
Глава 12
ЛАКОКРАСОЧНЫЕ МАТЕРИАЛЫ
12.1. СОСТАВЛЯЮЩИЕ КРАСОК И ЛАКОВ
Составляющими красок и лаков являются связующие вещества и пиг менты. В состав некоторых лакокрасочных материалов входят вспомога тельные компоненты (сиккативы, растворители, разбавители).
Связывающие (пленкообразующие) вещества. Связующими в красоч ных составах служат вещества, обеспечивающие сцепление частиц пиг мента между собой и способные образовывать прочные пленки толщиной от размеров молекулы до сотен микрометров.
Высокомолекулярные пленкообразующие вещества подразделяются на непревращаемые (пленки образуются из раствора в результате испарения растворителя) и на превращаемые (образование пленок сопровождается переходом линейных молекул в трехмерные пространственные полимеры). К первым относятся низкомолекулярные природные смолы, синтетические термопластичные смолы, белковые вещества, эфиры целлюлозы, ко вто= рым — высыхающие растительные масла, синтетические термореактивные смолы типа резольных формальдегидных и каучуки. Растительные масла в лакокрасочных составах применяют преимущественно в виде олиф: нату ральных, полунатуральных и искусственных.
Натуральные олифы получают путем варки льняного или конопляного масла при температуре до 200°С. Образование пленок на окрашенной по верхности происходит вследствие окисления кислородом воздуха тонкого слоя олифы. Пленка олифы после окисления становится устойчивой по отношению к веществам, растворяющим олифу.
Олифы полунатуральные получают обработкой растительных масел нагреванием до полимеризации или продуванием воздуха. Для придания полученным вязким продуктам необходимой жидкой консистенции их раз бавляют органическими растворителями. Олифы полунатуральные выпу скают следующих наименований: олифа полимеризованная, олифа оксоль, оксоль-смесь. Они содержат до 55% уплотненных масел и 45% раствори теля. Полунатуральные олифы в настоящее время наиболее широко при меняются в строительстве.
Искусственные олифы — это связующие, получаемые химической обра боткой различных органических веществ. Они не содержат растительные масла или содержат их не более 35%. Из большого ассортимента искус ственных олиф в строительстве применяются следующие виды: глифталевая — раствор глифталевой синтетической смолы в органических раство рителях с некоторым количеством (до 35%) растительных масел; синтоловая — продукт окисления керосина кислородом воздуха и последующего растворения его в органических растворителях; олифа-карболь — раствор алюминиевых и кальциевых солей органических кислот в уайт-спирите или других легких растворителях.
Лаки представляют собой растворы природных или синтетических смол в легких растворителях. Их разделяют на масляно-смоляные, синтетичес кие, канифольные, битумные, пековые. Лаки масляно-смоляные представ ляют собой растворы в органических растворителях синтетических смол, модифицированных Высыхающими маслами. Синтетические лаки — раствор
синтетических смол в органических растворителях. Наибольшее применение в строительстве нашли перхлорвиниловый, глифталевый и другие синтети
ческие лаки.
Глифталевый лак изготавливают из глифталевои смолы, сиккатива
и растворителя.
Канифольный лак получают растворением канифоли, обработанной глицериновым эфиром в скипидаре или спирте. Он применяется для кра сящих составов, используемых при окраске внутренних помещений.
Битумные лаки — однородная смесь твердых битумов с легким раст ворителем. Для придания большей стойкости в смесь прибавляют ^высы хающие масла и синтетические смолы. Битумные лаки имеют черный цвет и применяются для окраски металлических элементов конструкций, чугун
ных труб и др.
Животные клеи (мездровый и костный) применяют в качестве связую щих веществ водоклеевых красочных составов, для клеевых грунтовок и шпаклевок. Мездровый клей изготавливают развариванием в воде кожных покровов животных с последующей сушкой раствора. Костный клей изго тавливают путем переработки клеящего вещества, извлекаемого из обез жиренных костей. Качество клея проверяют отсутствием гнилостного запаха, налетов и плесени; реакция клея должна быть нейтральной.
Казеиновый клей изготавливают путем воздействия кислот на снятое молоко с последующей сушкой продукта. Качество клея проверяют отсутст вием гнилостного запаха и следов плесени. При смешении 1 части клея с 2 частями воды при 18—20°С должен образоваться однородный раствор.
Казеиновый клей применяют в качестве связывающего для клеевых грунтовок, шпаклевок и красочных составов со щелочно-устойчивыми пигментами.
Растительные клеи (декстрин, крахмал пшеничный и картофельный) применяются для водорастворимых красочных составов, клеевых грунтовок и шпаклевок. Декстрин получают при обработке крахмала кислотой и наг ревании до 150—200°С.
Пигменты. Это окрашенные химические соединения, способные в порош кообразном состоянии смешиваться с жидкими связывающими и образо вывать красочные составы.
Различают пигменты минеральные (искусственные и природные), орга нические и металлические. В строительстве используют главным образом минеральные пигменты, обладающие большой химической стойкостью, атмосферо- и светостойкостью, что особенно важно при покрасках наруж ных частей зданий и сооружений.
Пигменты характеризуются показателями основных свойств: укрывистости, красящей способности, тонкости помола, свето-, атмосферо- и огне стойкости. Укрываемость, или кроющая способность, характеризуется коли чеством пигмента в красящем составе, способным перекрыть цвет 1 м2 по верхности. Красящая способность — это интенсивность окраски, характе ризующаяся^ минимальным количеством пигмента, необходимым для при дания белой краске цветного тона. От красящей способности пигмента зависит его расход для получения тона в красочном составе.
Светостойкость характеризует способность пигмента сохранять свой
цвет под действием света; по изменению окраски судят о степени све тостойкости пигмента.
Пигменты минеральные природные включают в себя пигменты белые (мел, каолин), желтые (охра, сиена), красные (сурик железный, мумия), коричневые (умбра), серые (графит). Мел и каолин отмученные применяют в красящих составах на клеевых, казеиновых, силикатных и известковых ззо
связующих; их применяют и в качестве наполнителя грунтовок и шпаклевок. Охра — природный пигмент; состоящий из глины и окиси железа от 10 до 25%. Она свето- и щелочестойка, применяется в масляных, клеевых, эмале вых и других составах.
Сиена натуральная отличается от охры повышенным содержанием окиси железа (35—70% Fe20 3). Сурик железный Fe20 3 • FeO — светостойкий пигмент, обладающий антикоррозионными свойствами, применяется для окраски металлических крыш. Его получают при помоле железной руды.
Мумия природная представляет собой тонкий порошок глины, окрашен ный окислами железа. Содержание последних должно быть не менее 35%. Она свето- и щелочестойка. Применяют мумию в масляных и водных составах.
Умбра — глина, окрашенная окислами железа и марганца. Окислов железа должно быть в ней не менее 48%, а окислов марганца 7—14%. Умбра широко применяется в клеевых красках, используется также в виде масляной краски.
Графит — природный пигмент серовато-черного цвета с характерным металлическим жирным блеском. Графит отличается устойчивостью к действию высоких температур и кислот; применяется он в масляных красках.
Пигменты минеральные искусственные бывают белые (свинцовые, цин ковые, титановые белила), красные (сурик свинцовый), желтые (крон свинцовый, крон цинковый), черный (сажа), синие (ультрамарин, лазурь), зеленые (окись хрома) и др.
Свинцовые белила — основной углекислый свинец состава 2РЬС03Х ХРЬ(ОН)2. Они очень укрывисты, свето- и атмосферостойки, обладают высокими антикоррозионными свойствами. Недостатком их является токсичность.
Цинковые белила — окись цинка ZnO — получают из металлического цинка или цинковых руд переводом металла при высокой температуре в парообразное состояние с последующим окислением паров цинка. Они обладают хорошей укрывистостью, неядовиты, светостойки и сравнительно щелочестойки.
Титановые белила представляют собой двуокись титана ТЮ2, получае мую путем сложной переработки титановых руд. Титановые белила обла дают высокой кроющей способностью, химической стойкостью, не чувстви тельны к действию света.
Сурик свинцовый РЬ30 4 — продукт окисления свинцового глета. Цвет — от оранжевого до красного. Этот пигмент обладает стойкостью к дей ствию щелочей, но в кислотах растворяется; хорошо защищает от
коррозии.
Крон свинцовый — хромовокислый свинец РЬСг04 — получают при взаимодействии хромпика с солями свинца. Содержание в кроне серно кислого свинца (до 20%) дает возможность придавать ему разные оттенки — от светло-лимонного до темно-желтого; широко применяют для масляной и лаковой окраски металла и дерева.
Крон цинковый — смесь хромовокислого цинка с небольшим количест вом хромового ангидрида. Кроны цинковые более светостойки, чем свинцо вые, обладают высокими антикоррозионными свойствами.
Сажа |
является |
продуктом |
неполного |
сгорания органических |
веществ. |
||
Она |
обладает |
хорошей укрывистостью |
и высокой красящей |
способно |
|||
стью, |
а |
также |
устойчивостью |
к действию щелочей и кислот. Применяют |
|||
сажу |
в |
масляных, |
лаковых, |
клеевых и |
известковых красочных соста |
||
вах. |
|
|
|
|
|
|
|
Ультрамарин — искусственный синий пигмент, обладающий средней светостойкостью, щелочестоек, его применяют в основном для подцветки белых масляных и побелочных клеевых покрасок, для устранения их желтого
оттенка.
Окись хрома Сг2Оэ получают в результате нагревания хромпика К2Сг20 7 с восстановителем. Этот пигмент обладает абсолютной стойкостью к дей ствию света и большой стойкостью к действию высоких температур; приме няют его для приготовления всех видов красок.
Вспомогательные материалы. Сиккативы представляют собой растворы металлических солей жирных кислот в органических растворителях. Их при меняют как добавки к олифам и масляным красочным составам для ускоре ния высыхания. Избыток сиккатива сокращает срок службы красящей пленки вследствие преждевременного старения.
Растворители в зависимости от назначения подразделяются: для масля ных красочных составов и лаков; для глифталевых и битумных лаков и кра сок; для эпоксидных, перхлорвиниловых лаков и красок. Наиболее распро страненными растворителями, применяемыми в строительстве, являются скипидар, уайт-спирит, сольвент каменноугольный и ацетон.
Скипидар — продукт перегонки смолистрй древесины сосны, подвергну тый химической очистке. Скипидар — бесцветная или слабоокрашенная прозрачная жидкость с характерным запахом, является растворителем
большинства натуральных |
смол и применяется для разведения масляных |
и лаковых составов. |
перегонки нефти — средняя фракция между |
Уайт-спирит — продукт |
тяжелым бензином и керосином; применяется в качестве растворителя масел и лаков.
Ацетон — бесцветная легкоулетучивающаяся жидкость с резким запа хом, низкой температурой кипения (56,2°С); получается при перегонке дре весины и синтетических смол. Ацетон легко смешивается с водой, спиртом, эфиром; является хорошим растворителем жиров некоторых синтетических смол.
Разбавители представляют собой жидкости, в которых связующее ве
щество не растворяется. Они служат для уменьшения вязкости красочного состава.
Наполнители представляют собой высокодисперсные минеральные по рошки, добавляемые в красочные составы для экономии пигментов и повы шения прочности, огнестойкости и других свойств красочных составов.
Для^ клеевых красочных составов светлых тонов применяется тонко молотый каолин, для приготовлений шпаклевочных составов — тальк, тонкомолотый кварц, андезит.
§ 12.2. КРАСО Ч НЫ Е СО СТАВЫ
Красочные составы в зависимости от вида связующего вещества бывают масляные, эмалевые, водные и эмульсионные.
Масляные краски. Масляные красочные составы представляют собой суспензии пигментов в олифе, в которые вводят также наполнители. Масля ные краски вырабатываются двух видов: густотертые и жидкотертые (гото вые к употреблению). Густотертые краски содержат минимальное количе ство олифы; на месте работ к ним нужно добавить олифу для получения со става рабочей консистенции. Густотертые краски содержат олифы 12—25%,
жидкотертые — 30—50%. |
|
||
Масляные |
краски |
применяют |
для наружных и внутренних покрасок |
по металлу, |
дереву и |
просохшей |
штукатурке. Качество масляных красок |
332
оценивается по содержанию и свойствам пигмента, наполнителя и олифы. Содержание олифы определяют экстрагированием ее из краски раствори телями. Размер частиц пигмента и наполнителя не должен превышать 40 мкм.
Полное высыхание пленки масляных красок при температуре 8±2°С должно наступать в течение 24 ч.
Красочные составы для антикоррозионных окрасок затирают и разбав ляют натуральными олифами. Лучшими антикоррозионными пигментами являются свинцовый сурик, свинцовые белила. Наиболее экономичным
составом для наружных покрасок металла является железный сурик, тер тый на олифе.
Масляные краски хранят и перевозят в стальной или деревянной плотно закрытой таре.
Эмалевые краски. Они представляют собой готовые к употреблению суспензии органических или минеральных пигментов на специальных син тетических связующих веществах. Наиболее широкое применение в строи тельстве находят нитроглифталевые, алкидностирольные, эпоксидные, карбоидные и другие краски.
Нитроглифталевые эмалевые краски представляют собой раствор нитро глюкозы, глифталевой синтетической смолы, пигмента и пластификатора в органических растворителях; применяются для окраски внутренних помещений.
на |
Алкидностирольные эмалевые краски состоят из суспензии |
пигментов |
алкидностирольном лаке. Они обладают повышенной водостойкостью |
||
и |
химической стойкостью, поэтому применяются для окраски |
металлов |
с целью защиты от воздействия агрессивных сред. |
|
Эпоксидные эмалевые краски представляют собой суспензию пигмен тов в растворе эпоксидной смолы. Они обладают повышенной химической стойкостью, высокой водостойкостью, поэтому используются для окраски металлических поверхностей в помещениях с повышенной влажностью и для наружных покрасок по металлу и дереву.
Карбомидные эмалевые краски состоят из пигмента, диспергированного в мочевино-формальдегидной смоле. Перед применением в нее добавляют кислотный отвердитель. Эти краски применяют для окраски внутренних помещений.
Водные краски. Водные и малярные краски для строительства бывают двух видов: водно-клеевые и водно-известковые. Водно-клеевые краски состоят из мела с пигментом и раствора клея в воде. В качестве связую щего употребляют клей мездровый (для темных красок) и клей костный (для светлых красок). При приготовлении водно-клеевых составов пигмент размешивают с водой и вводят в замоченный мел, после чего добавляют 10%-ный раствор клея. Красочный состав пропускают через сито с отвер стиями 0,15 мм. Водно-клеевые красочные составы применяют для окраски оштукатуренных поверхностей внутри зданий.
Водно-известковые краски состоят из щелочеустойчивого минерального пигмента и известкового молока. Краски готовят на месте производства работ, используют воздушную или гидравлическую известь. Для лучшего сохранения влаги в красочные составы вводят небольшое количество доба вок поваренной соли. Красочный слой наносится кистью или краско пультом на увлажненную поверхность, которая предварительно очищается от старой краски и огрунтовывается. Водно-известковые краски применяют
для окраски кирпичных и бетонных поверхностей. |
|
краски. |
||
Более |
долговечны и |
атмосфероустойчивы водно-цементные |
||
В их состав входят следующие компоненты: белый цемент |
75 90 |
частей |
||
по массе, |
известь-пушонка |
0—15, хлористый кальций 2 4, |
стеарит каль- |
ззз
ция 1, щелочестойкие пигменты 2—8 и асбестовая пыль 1 часть. В краску в качестве наполнителей можно вводить тонкомолотый кварцевый песок (до 40 частей по массе) и трепел (до 5 частей). Для повышения водостой кости в краску вводят гидрофобные добавки. Водно-цементные краски применяют для отделки фасадов и внутренних помещений с повышенной влажностью.
Силикатные краски состоят из растворимого калийного стекла мине ральных щелочестойких пигментов и кремнеземистых добавок. Силикатные краски применяют для окраски кирпичных и бетонных поверхностей. Наи более атмосферостойкие покрытия получают при нанесении силикатной ,краски на основания, содержащие свободную известь, например на по верхность свежего бетона.
Эмульсионные краски. Они состоят из суспензии пигмента и эмульсии синтетических смол и являются водоразбавителями. Наиболее известны поливинилацетатные, бутадиенстирольные и полиметилметакрилатные эмульсионные краски. Их чаще всего выпускают в виде тщательно про тертой жидкой пасты, которую на месте работ разводят водой до малярной консистенции. Эмульсионные краски образуют матовую поверхность, при меняются для окраски внутренних помещений.
Поливинилацетатная краска используется для внутренней и наружной окраски бетона, оштукатуренной поверхности и древесины, не рекомен дуется для окраски полов и наружных окрасок.
Бутадиенстирольная краска применяется для внутренней и неответствен ной наружной покраски различных поверхностей.
Глава 13
СТРОИТЕЛЬНЫЕ МАТЕРИАЛЫ ИЗ ДРЕВЕСИНЫ
§ 13.1. СТРОЕНИЕ ДЕРЕВА
Дерево относится к многолетним растениям. В нем различают ствол, крону и корни. Ветви, листья или хвоя образуют крону дерева. Корни слу жат для укрепления дерева в грунте, а также для получения из почвы воды и растворенных в ней минеральных веществ. Ствол удерживает крону дерева и служит для перемещения воды и растворов солей от корней к листьям, а от них в обратном направлении — к корням органических веществ, кото рые частично откладываются в стволе.
Ствол составляет главную массу дерева (от 50 до 90%) и является основ ной частью, используемой для строительных целей, корни составляют от 5 до 25%, ветви — от 5 до 20% объема дерева. Дерево по мере роста обычно освобождается в нижней части от ветвей, ствол же увеличивается как по длине, так и по толщине. Прирост объема ствола вначале проис ходит довольно быстро, но после достижения некоторого возраста посте пенно уменьшается.
Строение древесины. Микроструктура — видимое в микроскоп строение древесины. Как всякое растение, дерево состоит из сросшихся между собой клеток, преимущественно мертвых. Растительная клетка имеет тонкую про ницаемую оболочку 7, заполненную протоплазмой 2 с полостью 4, внутри которой находится ядро 3 (рис. 13.1). Протоплазма и ядро представляют собой зернистую прозрачную, тягучую слизь (сложный растительный белок). Оболочка клетки в основном состоит из природного высокомолекулярного вещества целлюлозы или клетчатки (C6H10O5)„. По мере роста клетки оболочка претерпевает различные изменения в строении и составе, в резуль тате чего происходит ее одеревенение или опробкование.
При одеревенении в оболочке клетки образуется особое вещество — лиг нин, который содержит значительное количество углерода, при этом уве личиваются прочность и твердость, но уменьшаются упругость, способность к разбуханию и пр. Одеревенение клеток происходит преимущественно в стволе.
Микроструктуру одеревеневших клеточных стенок древесины можно представить как природный композиционный материал, состоящий из воло кон целлюлозы в матрице лигнина. Волокна целлюлозы обладают высокой прочностью на разрыв, но легко изгибаются. Лигнин связывает их в еди ное целое и придает древесине жесткость.
Ткани. Совокупность клеток одинакового строения, выполняющие одну и ту же функцию, образуют ткани, которые разделяются на несколько групп:
запасающие, служащие для накопления й хранения питательных ве ществ. Они располагаются в основном в сердцевинных лучах;
опорные или механические, состоящие из одеревеневших длинных и толстостенных клеток длиной от 0,7 до 1,6 м и шириной от 0,05 до 0,2- мм. Клетки этой ткани обладают сравнительно высокой механической проч
ностью; проводящие или сосудистые, предназначенные проводить растворенные
в воде минеральные и органические соединения.
В зависимости от расположения проводящих со судов лиственные породы делят на кольцесосудистые,
|
|
в ранней древесине которых расположены крупные, |
||||
|
|
а в поздней мелкие сосуды, и рассеяннососудистые, |
||||
|
|
где мелкие сосуды равномерно рассеяны по всей ши |
||||
|
|
рине годичного слоя. Дуб, ясень, вяз являются коль |
||||
|
|
цесосудистыми; береза, осина, клен, липа — рассеян |
||||
|
|
нососудистыми. |
|
|
||
|
|
У хвойных деревьев сосудов нет, а древесина их |
||||
|
|
состоит из замкнутых удлиненных клеток — трахеид, |
||||
|
|
которые выполняют роль как проводящих, так и ме |
||||
|
|
ханических |
тканей. |
Межклеточные |
пространства |
|
|
|
заполняются смолой, образуя смоляные ходы. |
||||
|
|
Строение ствола дерева. Ствол — основная и на |
||||
|
|
иболее ценная часть дерева. Верхняя, наиболее тон |
||||
|
|
кая часть ствола, называется вершиной, нижняя уто |
||||
|
|
лщенная — комлем. Поверхность среза дерева по |
||||
|
|
перек ствола |
называется торцом. |
|
||
|
|
Строение древесины на поверхностях ее разре |
||||
|
|
зов и свойства в различных направлениях по отно |
||||
|
|
шению к оси ствола различны. Различают три основ |
||||
|
|
ных разреза |
ствола |
(рис. 13.2): поперечный — тор |
||
|
|
цовый, проходит перпендикулярно к оси ствола; ра |
||||
|
|
диальный — продольный, проходящий через сердце- |
||||
|
|
вину; тангенциальный — продольный, |
проходящий |
|||
Рис. 13.1. Клетка |
древе |
на некотором расстоянии от сердцевины. На основ |
||||
ных разрезах ствола различают следующие основ |
||||||
сины |
|
|||||
|
|
ные части: кору, луб, камбий, заболонь, ядро, сердце- |
||||
YT |
|
вину, сердцевидные лучи и годичные слои (рис. 13.3). |
Кора служит для защиты дерева от неблагоприятных влияний внешней среды и механических повреждений. Она состоит из клеток с опробковавшейся оболочкой. У различных пород кора составляет от 7 до 20% объема ствола, причем с увеличением толщины дерева относительный объем коры уменьшается. Из коры некоторых пород (пробковый дуб, бархатное
дерево) изготовляют пробку, теплоизоляционные изделия, дубильные ве щества и пр.
Луб — тонкая внутренняя часть коры обычно светлого цвета, состоит из ситовидных трубок и лубяных волокон и служит для перемещения орга нических веществ, выработанных листьями (нисходящий ток).
Камбий располагается непосредственно за лубом в виде тонкого слоя живых клеток. Каждая клетка камбия при размножении делится на две, одна из которых, более тонкостенная, располагается по направлению к пе риферии ствола, а другая клетка — толстостенная и одеревеневшая — рас полагается по направлению к середине. В вегетационный период камбий усиленно образует широкие клетки с тонкой оболочкой — так называемую раннюю древесину, назначение которой — быстрее проводить влагу и пита тельные вещества, нужные дереву для роста, когда оно нагружено разви вающимися побегами и листьями. Камбий образует и механическую ткань,
состоящую из толстостенных сплюснутых клеток, которые и составляют главную часть поздней древесины.
Образовавшиеся в течение вегетационного периода слои ранней и позд ней древесины называются годичными слоями или кольцами. У многих пород, например у дуба, они хорошо видны на поперечном разрезе ствола в виде концентрически расположенных слоев. Ширина годичных слоев у разных
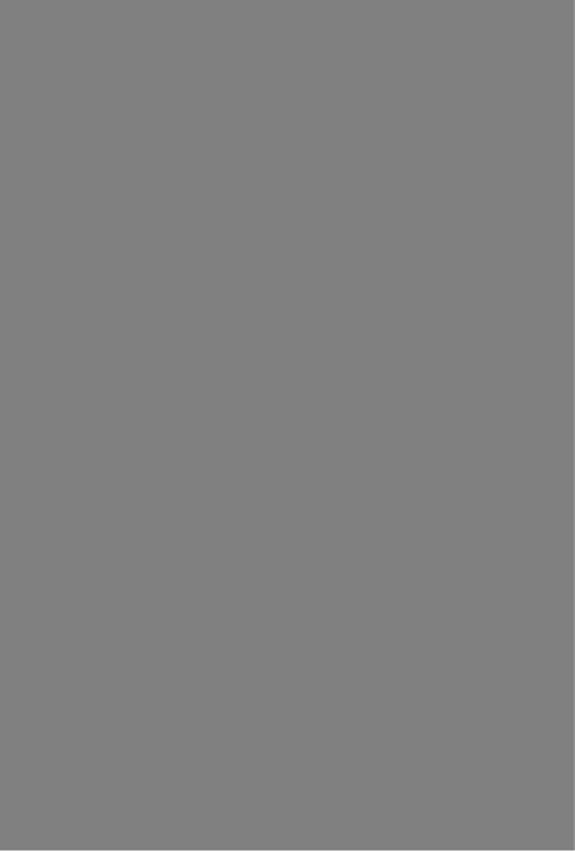
Для накопления и проведения питательных веществ в поперечном нап равлении служат сосудисто-волокнистые ткани, которые называются сердце
винными лучами.
Величина сердцевинных лучей у разных пород различна и зависит от усло вий роста дерева. По сердцевинным лучам древесина легко раскалывается, по ним же проходят трещины усушки.
§ 13.2. ХАРАКТЕРИСТИКА ДРЕВЕСИНЫ ОСНОВНЫХ ПОРОД, ПРИМЕНЯЕМЫХ В СТРОИТЕЛЬСТВЕ
Хвойные породы. Все древесные породы разделяются на хвойные и лиственные. Леса Советского Союза на 3/4 состоят из хвойных пород. Наибольшее значение имеют сосна, ель, лиственница, кедр и пихта. Древе сина хвойных пород обладает меньшей плотностью по сравнению с листвен ными и легче обрабатывается. Она имеет резко выраженные очертания годичных слоев, повышенную смолистость и стойкость против загнивания. Хвойные породы обычно имеют правильную форму ствола, что позволяет полнее использовать их в строительстве.
Сосна (обыкновенная) — ядровая порода. Цвет ядра розоватый, жел товатый или буроватый; он особенно выделяется при высыхании древе сины; заболонь — желтовато-белого цвета. Древесина сосны мягкая, легкая, малоупругая и хорошо колется. Сосна, произрастающая на сухих песчаных
почвах, называется рудовой или кондовой; у |
нее плотная, |
смолистая |
и мелкослойная древесина желто-красноватого |
цвета. Сосна, |
выросшая |
в сырых местах, называется мяндовой; древесина ее менее прочная, крупно слойная с сильно развитой заболонью. В густом насаждении сосна имеет высокий прямой ствол почти без сучьев. Продолжительность жизни сосны до 300 лет. Лучшую древесину она дает в возрасте 80—120 лет. Древесину сосны широко применяют в различных областях строительства: в мостост роении, для изготовления столбов, досок, шпал, столярных изделий, раз личных вспомогательных конструкций, опалубки и т. д.
Ель— порода спелодревесная. Древесина ели белого цвета с блеском и широкой заболонью, мягкая, легкая, менее смолистая, чем у сосны, поэтому относительно быстрее загнивает. В сухих местах древесина ели может со храняться продолжительное время. Ель, так же как сосна, является весьма распространенной на территории СССР хвойной породой. Продолжитель ность жизни ели 250—300 лет. Лучший возраст для рубки между 100 и 150 годами. Ель применяют меньше, чем сосну, так как качество ее хуже.
Древесина ели хорошо колется и применяется в виде круглого и пиле ного леса.
Лиственница — ядровая порода. Древесина ее имеет красновато-бурое ядро и узкую заболонь белого цвета с буроватым оттенком. Древесина лиственницы мелкослойная, плотная, тяжелая, прочная, твердая и обильно пропитана смолой. Лиственница широко распространена в Сибири, в бас сейнах рек Камы, Печоры, Северной Двины, а также на Урале. Она отно сится к быстрорастущим породам и к 60—80 годам достигает полного раз вития. Ствол у лиственницы стройный, прямой с незначительным количе ством сучьев. Древесина лиственницы мало коробится и трескается при высыхании, стойка против загнивания, не поражается насекомыми, хорошо сохраняется на воздухе и под водой, причем, находясь продолжительное время под водой, она увеличивает свою механическую прочность. Листвен
ницу применяют в различны/Х областях строительства: мостостроении, для изготовления стволов, шпал, фанеры.
Кедр (сибирский) — порода ядровая. Древесина кедра имеет желто вато-красноватое ядро и тонкую желтовато-бурую заболонь; она мелкослойна, мягка и довольно прочна. Ствол кедра прямой, высокий, правиль ный, продолжительность жизни около 700 лет. Кедр распространен главным образом в Сибири. По качеству древесина кедра близка к древесине сосны.
Пихта имеет спелую древесину белого цвета почти без смоляных хо дов. Древесина пихты мягче и слабее, чем у других хвойных пород. Это самое легкое дерево СССР. Родина пихты — Сибирь. В европейской части
СССР пихта встречается на Урале и в северо-восточных областях. По
техническим качествам древесина |
пихты приближается к древесине ели |
и применяется в строительстве для |
тех же целей, что и ель. |
Лиственные породы. По запасам древесины лиственные породы усту пают хвойным и составляют около 1/4 площади всех лесов. Однако они превосходят их многочисленностью пород, разнообразием свойств, харак тером применения.
По строению древесины лиственные породы делятся на две группы: кольцесосудистые и рассеянно-сосудистые.
К лиственным кольцесосудистым породам, в которых сосуды хорошо заметны и расположены в ранней древесине годичного слоя в виде колец, относятся следующие породы.
Дуб — ядровая порода, имеет узкую (8—10 годовых слоев) желтовато белую заболонь. Растет он в средней и южной полосе. Корни дуба уходят глубоко в грунт. Средняя продолжительность жизни дуба 500—600 лет. В густом лесу дуб образует прямой высокий ствол почти без сучьев. Древеси на дуба плотная, прочная и упругая, с хорошо развитыми сердцевинными лучами; при высыхании она обладает значительной усадкой и склонна к обра зованию трещин; хорошо сохраняется на воздухе и под водой. Дуб. находя щийся длительное время под водой, приобретает большую твердость, при этом древесина его чернеет под влиянием взаимодействия дубильной кислоты с солями железа, находящимися в воде.
Древесину дуба, обладающую высокими механическими свойствами, при меняют в мостостроении, в гидротехническом строительстве, для изготовле ния конструкций зданий, паркета, шпал, для различных отделочных работ, изготовления мебели, фанеры и др.
Вяз — также ядровая порода, ядро серо-бурое, заболонь широкая, светло-желтая, древесина тяжелая, прочная, упругая, средней твердости и хорошо сопротивляется ударной нагрузке. Особой прочностью отличается древесина вяза в сооружениях под водой — на воздухе она сохраняется хуже. Вяз применяют в гидротехнических сооружениях, в машиностроении, для изготовления облицовочной фанеры и др.
Лиственные рассеянно-сосудистые породы характеризуются тем, что мел кие и крупные сосуды распределены равномерно по всему годичному слою.
К ним относятся следующие породы. |
и тяжелой древесиной |
белого |
Береза — порода заболонная, с твердой |
||
и желтоватого цвета. Сердцевинные лучи |
очень тонкие и имеют |
блеск |
в радиальном разрезе. Древесина березы вязкая, довольно прочная, но мало устойчива против загнивания, медленно сохнет и легко коробится. Продол жительность жизни березы 100 лет. В густом насаждении береза образует высокий, прямой почти без сучков ствол с белой корой (берестой). Белый цвет коры обусловливается наличием в ней смолистого вещества — бетулина, благодаря которому береста не пропускает влаги и не гниет. Шоколадный цвет древесины свидетельствует о начале загнивания. Древесину березы при меняют для изготовления мебели, фанеры, токарных изделий.
Для отделочных работ особенно ценится карельская береза, у которой вследствие извилистого расположения волокон на разрезе получается живо писный рисунок, красивый цвет и блеск. Она прочна и тверда.
Ольха (черная) — порода заболонная. Древесина ольхи легкая и мяг кая, ломкая и сильно коробящаяся. Свежесрубленная древесина ольхи бело го цвета, но на воздухе быстро принимает красноватую окраску и сравни тельно скоро портится. Однако, если древесина ольхи в свежесрубленном состоянии применяется для подводных сооружений, она прочна и сохраняет ся не хуже дуба. В строительстве ольха применяется реже; ее часто высажи вают в грунт для укрепления откосов каналов, плотин и других подобных
сооружений.
Осина — спелодревесная порода, древесина ее с сильным блеском, легкая и мягкая, белого цвета с бледно-зеленоватым оттенком. В сухой среде осина довольно прочна, но во влажном состоянии быстро загнивает. Ствол прямой, круглый. Для улучшения качества древесины осину завяливают на корню, для чего за год до рубки с нее снимают кольцом часть коры. Древесина осины хорошо колется, легко и чисто обтачивается на токарном станке, мало коро бится и мало трескается при высыхании. Осину применяют для изготовления фанеры, гонта (тонкие дощечки для кровель), спичек, тары и пр.
Клен (остролистный) — порода заболонная; древесина белого, краснова того или желтого цвета с шелковистым блеском и красным рисунком, часто встречаются темные или цветные пятна, являющиеся признаком загнивания древесины. Древесина клена прочная, плотная, мало коробится, почти не трескается при высыхании и хорошо обрабатывается; при'переменной влаж ности склонна к загниванию. Клен применяют для отделочных работ, для то карных изделий, для изготовления облицовочной фанеры и т. д.
Бук — порода спелодревесная, имеет тяжелую, твердую древесину белого цвета с красноватым оттенком и многочисленными широкими сердцевинными лучами более темного цвета, чем остальная часть древесины. В свежем со стоянии древесина бука сравнительно легко обрабатывается, но в старой, су хой древесине это свойство утрачивается. При высыхании древесина коробит ся и трескается. Вследствие назначительного распространения (Крым, Кар паты, Кавказ) применение бука ограничено: его используют в строительстве для изготовления свай, фанеры, паркета, шпал (с пропиткой антисептиками) и др.
Граб — порода заболонная; древесина твердая, тяжелая, вязкая, белого цвета, трудно раскалывается. Годичные кольца располагаются в виде вол нистых линий. На открытом воздухе древесина граба сравнительно быстро загнивает. В строительстве граб находит ограниченное применение и употреб ляется на мелкие поделки, требующие большой твердости.
§ 13.3. СВОЙСТВА ДРЕВЕСИНЫ
Технические свойства древесины зависят от ее породы, строения и влаж ности.
Физические свойства древесины. Цвет древесины зависит в основном от присутствия красящих и дубильных веществ, возраста и условий роста дере ва. Древесина пород умеренной климатической зоны имеет сравнительно однообразную окраску — от светлой до коричневой. Появление серой, зелено ватой, синей и красной сплошной (полосатой и пятнистой) окраски для пород умеренной климатической зоны указывает на болезненное состояние древеси ны, вызванное гнилями и грибами. Древесина каждой породы имеет своеоб разный запах вследствие наличия в ней смол, эфирных масел, дубильных
340
и других веществ. При загнивании древесина обычно приобретает неприят ный затхлый запах.
Текстура, или рисунок, древесины зависит от наличия тех или иных волокон, их величины и взаимного расположения. Наличие сучков, сви леватости и других пороков обусловливает различную текстуру древеси ны. В зависимости от направления среза получается также различная текстура. Почти совершенно лишены рисунка осина, липа, тополь, ива, так как они не имеют широких сердцевидных лучей и отличаются посте пенным переходом от ранней древесины годичного слоя к поздней.
Плотность древесного вещества для всех древесных пород почти оди накова и равна 1540—1560 кг/м3, что объясняется одинаковым химиче ским составом древесины различных пород (абсолютно сухая древесина содержит углерода 49,5%, водорода 6,3, кислорода и азота 44,2 и мине ральных веществ 0,2—1,7%). Эту величину можно назвать также абсолют ной плотностью древесины.
Плотность (объемная масса) древесины есть масса одного кубического метра древесины в ее естественном состоянии, т. е. вместе с порами, пусто тами и влагой. Для различных пород она различна. Плотность неодина кова для древесины одной породы и даже одного ствола. На величину плот ности влияют: влажность древесины, ширина годичных слоев, положение древесины в стволе, возраст, порода, условия роста дерева и другие причи ны. Сравнивать по плотности древесину разных пород можно только при одинаковой влажности, равной 15%.
По плотности древесину делят на следующие группы (кг/м3): очень лег кая — с плотностью меньше 450 (кедр сибирский, пихта); легкая — с плот ностью 460—600(вяз, ель, липа, осина, сосна); среднетяжелая — с плот ностью 610—750 (береза, бук, груша, дуб, лиственница, тис, яблоня, ясень); тяжелая — с плотностью 760—900 (граб); очень тяжелая — с плот ностью 910 и более (кизил, самшит).
Плотность древесины характеризует ее физико-химические свойства; ею пользуются для определения коэффициента конструктивного качества, пред ставляющего собой отношение предела прочности при сжатии к плотности. Так, например, коэффициент конструктивного качества сосны равен 0,6, ду ба — 0,57.
Объем пор, заключенных в единице объема древесины, характеризует ее пористость. Кроме общего количества пор, важной характеристикой явля ются величина отдельных пор и их расположение в теле древесины или однородность строения. Этим определяются возможность пропитки древе сины, отношение к воде, тепло-, звуко- и электропроводность й другие свойства.
Важцым свойством древесины является ее отношение к воде. К этим свойствам относят влажность, водопоглощение, водопроницаемость, паропроводность, гигроскопичность и др.
Вода в древесине заполняет полости клеток и межклеточные пространства и может быть в форме капиллярной (или свободной), коллоидно-связанной (или гигроскопической) и химически связанной.
Капиллярная (свободная) вода заполняет сосуды и межклеточные про странства древесины. Коллоидно-связанная (гигроскопическая) вода удер живается в межклеточном пространстве и в оболочках клеток. Наконец, химически связанная вода входит в состав отдельных веществ древесины.
В заболони растущего дерева вода находится |
во всех формах, в ядре |
же — только коллоидно- и химически связанная. |
(свободной и гигроскопи |
Влажностью называют отношение массы влаги |
ческой), находящейся в данный момент в древесине, к массе ее в сухом состоянии.
В практике по степени влажности различают древесину: мокрую — дли тельное время находящуюся в воде — влажность выше 100%; свежерубленную — влажность 50—100%; сырую — влажность 23—50%; воздушно сухую— долгое время хранившуюся на воздухе — влажность 15—20%; комнатно-сухую — влажность 8—12% и абсолютно сухую — влажность около 0%.
Влажность древесины ствола растущего дерева в комле и вершине боль ше, чем в средней части. Содержание влаги в различных частях поперечного сечения ствола ядровых и спелодревесных пород различна, а у заболонных пород — равномерная. Свежесрубленное окоренное дерево, оставаясь на открытом месте, высыхает очень медленно, достигая воздушно-сухого состоя ния через 1,5—2 года. Хвойные породы высыхают быстрее лиственных. В процессе высыхания древесины вначале испаряется свободная вода, а затем очень медленно коллоидно-связанная. Состояние древесины, при котором стенки клеток еще насыщены влагой, а свободная вода уже удалена, называется пределом гигроскопичности, или точкой насыщения волокон.
Это состояние влажности для различных древесных пород находится в пределах 23—30%. Предел гигроскопичности имеет большое практическое значение, так как удаление свободной воды почти не сказывается на свой ствах древесины; с момента же испарения связанной воды начинается умень шение объема (объемная усушка) и размера (линейная усушка) древесины, что приводит к ее уплотнению и увеличению прочности.
Объемная усушка свежесрубленного дерева при высыхании до сухого состояния, так называемая полная усушка, колеблется у различных пород от 8,5 до 15%. Древесина тяжелых и твердых пород имеет большую усушку, чем древесина легких и мягких пород.
Кроме объемной или линейной усушки, определяют коэффициент объем ной усушки как отношение показателя усушки к разности начальной и конечной влажности. Коэффициент объемной усушки для различных пород колеблется от 0,2 до 0J5% . Уменьшение объема древесины вследствие испарения воды происходит неодинаково в различных направлениях: наи меньшая усушка — в продольном, а наибольшая — в тангенциальном. Неравномерная усушка древесины в различных направлениях вызывает различное напряжение, вследствие чего древесина коробится и покрывается трещинами. Медленное высыхание дерева приводит к более равномерной усушке и дает меньше трещин. Срубленное дерево, оставленное в коре, высы хает медленнее, чем без коры.
В бревне трещины располагаются радиально. Изменение размера сорти мента вследствие неравномерного высыхания зависит от его формы и от того, из какой части ствола он вырезан. Например, чем ближе доска выре зана к середине ствола, тем она меньше коробится, и, наоборот, чем дальше от сердцевины, тем больше у нее выпуклость к сердцевине. Свойство нерав номерного изменения линейных размеров в различных направлениях являет ся одним из самых отрицательных строительных свойств древесины.
Влажность древесины зависит от температуры и относительной влажности окружающего воздуха. Если высушенную древесину поместить в среду с по вышенной влажностью, древесина постепенно начнет поглощать влагу и увеличиваться в объеме — разбухать. Способность древесины поглощать из воздуха парообразную воду называют гигроскопичностью. Разбухание древесины, как и усушка, также происходит неравномерно в различных направлениях: наименьшее — вдоль волокон, наибольшее — поперек воло кон в тангенциальном направлении.
Сухая древесина в зависимости от температуры и влажности окружающей среды может поглощать влагу до определенного предела, т. е. до равно весной влажности, когда древесина не испаряет и не поглощает влагу.
Способность древесины поглощать воду называется водопоглощением, которое в известной мере зависит от плотности древесины: наиболее легкая поглощает большее количество воды, наиболее тяжелая — меньшее.
Теплопроводность древесины сравнительно мала и зависит от плотности, характера пористости и влажности; теплопроводность древесины неодинако вая в различных направлениях. В направлении поперек волокон теплопровод ность меньше, чем вдоль волокон [Х = 0,16+0,25 Вт/(м • К)]. С увеличением плотности и влажности уменьшается количество воздуха, находящегося
впустотах, вследствие чего теплопроводность древесины увеличивается. Звукопроводность древесины характеризуется скоростью распростране
ния в ней звука. Древесина является хорошим проводником звука, который в ней распространяется в 2—17 раз быстрее, чем в воздухе. Быстрее всего звук распространяется вдоль волокон, медленнее — в радиальном и еще мед леннее — в тангенциальном направлениях. Звукопроводность древесины по сравнению с другими материалами приведена в табл. 13.1.
Удельная теплота сгорания древесины — количество тепла, которое мо жет выделиться при полном сгорании единицы ее массы (1 кг). Удельная теп лота сгорания дров различных пород при одной и той же влажности в сред нем колеблется в пределах 1,97—2,10 кДж на 1 кг древесины.
Механические свойства древесины. Древесина — анизотропный матери ал, т. е. свойства имеют различное значение по различным направлениям, что учитывают при определении механических свойств. Все показатели проч ности древесины приводят к 15%-ной влажности.
Механическая прочность — спо собность древесины сопротивляться сжимающим, растягивающим, изги бающим и другим усилиям стати ческого и динамического воздейст вия. Прочность увеличивается с уве личением плотности сухой древесины, а также при правильном расположе нии волокон (прямолинейности), мелкослойности (у хвойных пород), отсутствии сучков, малой влажности, увеличении возраста (для сосны, например, 80—120 лет).
Сопротивление сжатию. Во мно гих конструктивных элементах дре весина работает на сжатие (сваи,
колонны, стойки).
Усилия к конструктивному эле менту могут быть приложены с уче том строения древесины вдоль или поперек волокон, поэтому различают сжатие вдоль и поперек волокон.
Колебания величины предела прочности при сжатии даже для од ной и той же породы весьма значи
тельны. , i , 0/
юг;, для---дуба---л 1 ^15%О/ -МАИнойг т влажностип м / п Л ' предел прочности при сжатии впппк волокон колеблется примерно от 32,0 до 68,5 МПа. Прочность при сжатии пп перек волокон составляет 27% от прочности при сжатии вдоль волокон для хвойных пород и 40% для лиственных пород (табл. 13 2)
Сопротивление растяжению. Наибольшей прочностью древесина обладает при работе на растяжение вдоль волокон (табл. 13.3). Вследствие трудности передачи усилий, т. е. закрепления концов детали, древесину сравнительно редко используют для конструкций, работающих на растяжение. Трудность передачи усилий заключается в том, что в закрепленных концах деревянной детали возникают напряжения скалывания и смятия, которым древесина плохо сопротивляется.
Сопротивление раскалыванию. Способность древесины раскалываться вдоль волокон под действием клина, вбиваемого в торец, представляет собой сложное явление, но по характеру близкое к растяжению поперек волокон.
|
|
|
|
|
|
|
|
|
|
Т а б л и ц а |
13.3 |
|
|
|
Предел прочности при |
|
|
Предел прочности при |
|
||||||
|
|
растяжении, МПа |
|
|
|
|
растяжении, МПа |
|
||||
Порода |
вдоль |
|
поперек волокон |
|
Порода |
вдоль |
поперек волокон |
|||||
древесины |
волокон |
в направлении |
древесины |
волокон |
в направлении |
|
||||||
|
|
|
радиаль |
|
танген |
|
|
радиаль |
та иген’- |
|||
|
|
|
ном |
|
циальном |
|
|
ном |
циальном |
|||
Сосна |
127,8 |
|
2,56 |
|
|
1,96 |
|
Береза |
156,0 |
8,23 |
10,63 |
|
Ель |
145,8 |
|
2,20 |
|
|
2,97 |
|
Ольха |
140,0 |
3,29 |
1,75 |
|
Лиственница |
120,8 |
|
6,20 |
|
|
— |
|
Осина |
145,0 |
1,71 |
4,14 |
|
Бук |
134,0 |
|
8,85 |
|
|
7,52 |
|
Граб |
189,0 |
10,07 |
6,08 |
|
Дуб |
149,0 |
|
5,82 |
|
|
4,06 |
|
Клен |
168,2 |
7,19 |
3,71 |
|
|
|
|
|
|
|
|
|
Ясень |
110,9 |
2,18 |
4,08 |
|
|
|
|
|
|
|
|
|
|
|
Т а б л и ц а |
13.4 |
|
Порода |
Плот |
Предел |
Порода |
Плотность, |
Предел |
Порода |
Плот но.сть, |
Предел |
||||
прочности |
прочности |
прочности |
||||||||||
древесины |
ность |
при |
стати |
древесины |
кг/м3 |
при стати |
древесины |
кг/м3 |
при стати |
|||
|
кг/м3 |
ческом из |
|
|
|
|
ческом из |
|
|
ческим |
из |
|
|
|
гибе, МПа |
|
|
|
|
гибе, МПа |
|
|
гибе, |
МПа |
|
Дуб |
700 |
|
84 |
Ольха |
500 |
81 |
Сосна |
500 |
79 |
|
||
Береза |
630 |
|
86 |
Ильм |
|
660 |
92 |
Пихта |
400 |
65 |
|
|
Бук |
690 |
|
66 |
Ель |
|
|
460 |
70 |
Лист |
660 |
92 |
|
Граб |
800 |
|
ПО |
Осина |
480 |
74 |
венница |
|
||||
Тис |
630 |
|
79 |
Клен |
|
|
610 |
82 |
Вяз |
520 |
71 |
|
|
|
|
|
Ясень |
|
620 |
98 |
|
|
|
|
|
|
|
|
|
|
|
|
|
|
|
Т а б л и ц а |
13.5 |
|
Порода |
Плотность, |
Удельное сопротивление |
Порода |
Плотность, |
Удельное сопротивление |
|||||||
выдергиванию в |
|
выдергиванию в |
||||||||||
древесины |
кг/м3 |
|
направлении |
древесины |
кг/м3 |
направлении |
|
|||||
|
|
|
радиальном |
торцовом |
|
|
радиальном |
торцовом |
||||
Граб |
800 |
|
100 |
|
|
89 |
Сосна |
500 |
63 |
42 |
||
Бук |
670 |
|
96 |
|
|
70 |
Ель |
440 |
44 |
29 |
||
Береза |
660 |
|
92 |
|
|
65 |
Липа |
410 |
39 |
27 |
||
Ясень |
640 |
|
88 |
|
|
75 |
Осина |
480 |
39 |
30 |
||
Дуб |
700 |
|
75 |
|
|
64 |
Тополь |
340 |
37 |
28 |
По степени раскалывания древесные породы делят на следующие группы: весьма трудно раскалывающиеся (самшит, граб, вяз, ильм, тис); трудно раскалывающиеся (клен, ясень, каштан); сравнительно легко раскалываю щиеся (ольха, сосна, осина, дуб, липа); очень легко раскалывающиеся (ель, пихта, тополь, веймутовая сосна, ива).
Сопротивление древесины статическому изгибу. Древесина оказывает большое сопротивление статическому изгибу, поэтому ее широко применяют при строительстве мостов, устройстве ферм, балок, подмостей. Среднее значе ние прочности при статическом изгибе для некоторых древесных пород приве дено в табл. 13.4.
Упругость древесины. Древесина обладает большой упругостью. Наибо лее упруга,древе,сина тяжелых пород: белой акации, тиса, клена. Влажная древесина хвойных пород обладает упругостью почти наполовину меньшей, чем воздушно-сухая.
Твердость древесины. Этот показатель имеет существенное значение при ее обработке. Кроме того, чем тверже древесина, тем меньше она изнашива ется, что важно для полов, настилов на мостах. Твердость обычно характери зуется статической твердостью. В зависимости от того, в какую поверхность вдавливается п-уансон, различают твердость торцовую, радиальную и танген циальную.
У большинства пород торцовая твердость выше боковой. По данным Бринелля-Янка, древесину различных пород по торцовой твердости клас сифицируют на:
Очень мягкую |
<35 МПа |
Мягкую |
35.1— 50 МПа |
Средней твердости |
50.1—65 МПа |
Твердую |
65,1 — 100 МПа |
Очень твердую |
>100 МПа |
Удельное сопротивление древесины выдергиванию металлических креп лений (гвоздей, шурупов, костылей, скоб и др.). Оно зависит от породы и упругости древесины, сопротивления сжатию и растяжению, от трения меж ду поверхностями металлического крепления и древесины и т. п. Для харак теристики удельного сопротивления древесины выдергиванию гвоздей в табл. 13.5 приводится ряд сравнительных показателей, причем сопротивле ние для граба в радиальном направлении принято за 100.
§ 13.4. ПОРОКИ ДРЕВЕСИНЫ
Отклонения от нормального строения и повреждения древесины, пони жающие ее качество и ограничивающие применение, называются пороками. Пороки древесины механического происхождения, возникающие в процессе заготовки, транспортирования, сортировки, штабелирования и механической обработки, называются дефектами.
Влияние порока на качество древесины зависит от его вида, размера, рас положения в сортименте и назначения последнего. Как правило, пороки снижают прочность и декоративность лесоматериалов, поэтому сорт древеси ны устанавливают с обязательным учетом имеющихся в ней пороков.
Большинство пороков образуется в растущем дереве вследствие ненор мальных условий его роста, климатических воздействий, а также различных механических повреждений. Значительное количество пороков может образо ваться в заготовленной древесине (трещины, повреждения насекомыми).

Морозные — радиально направленные трещины, проходящие из заболо ни в ядро и имеющие значительную протяженность; возникают также в расту щем дереве.
Трещины усушки — радиально направленные трещины, возникающие в срубленной древесине при ее просыхании. От метиковых и морозных трещин они отличаются меньшей протяженностью (обычно не более 1 м).
Отлупные трещины образуются между годичными слоями в ядре или спелой древесине в растущем дереве. На торцах наблюдаются в виде дугооб разных и кольцевых трещин.
По положению в сортименте в зависимости от выхода на поверхность тре щины подразделяют на боковые, пластовые, кромочные, торцовые. По глуби не трещины делят на неглубокие, глубокие и сквозные, по ширине на сомкнув шиеся (ширина не более 0,2 мм) и разошедшиеся.
Пороки формы ствола по видам разделяют на (рис. 13.5): сбежистость — уменьшение толщины ствола на всем его протяжении на величину, превы шающую нормальный сбег 1 см на 1 м длины;
закомелистость — резкое увеличение диаметра комлевой части, которая может быть округлой или ребристой;
нарост — резкое местное утолщение ствола различной формы и размера; кривизна — искривление продольной оси ствола с одним или несколькими
изгибами.
Пороки строения древесины разделяют по следующим видам.
Наклон волокон — непараллельность волокон древесины продольной оси, которая может быть в тангенциальной или радиальной плоскости.
Крень — местное изменение строения тройных пород в сжатой зоне ство лов; появляется в виде кажущегося резкого уширения поздней древесины годичных слоев. Крень может быть местная или сплошная.
Тяговая древесина — местное изменение строения древесины лиственных пород в растянутой зоне стволов. Проявляется в резком увеличении ширины годичных слоев и более светлой окраске.
Свилеватость разделяют на волнистую с извилистым и путаную с беспо рядочным расположением волокон древесины.
Завиток — местное искривление годичных слоев, обусловленное влиянием сучков или проростей. В зависимости от выхода завитка на стороны сортамен та различают односторонний и сквозной завиток.
Глазки — следы неразвившихся в побег спящих почек с диаметром ме нее 5 мм. В зависимости от расположения различают разбросанные или груп повые глазки, а по цвету — светлые или темные.
Смоляной кармашек — полость внутри годичного слоя, заполненная смо лой. В зависимости от выхода на поверхности сортамента различают одно сторонний и сквозной смоляной кармашек.
С е р д ц е в и н а — узкая центральная часть ствола, состоящая из рых лой ткани с бурым или более светлым, чем окружающая древесина, цветом.
Двойная сердцевина — наличие в сортименте двух сердцевин.
Пасынок — отставшая в росте или отмершая вторая вершина, пронизы вающая на значительном протяжении сортимент под острым углом к его про
дольной оси.
Сухобокость — омертвевший в растущем дереве участок поверхности
ствола.
Прорость — обросший древесиной участок поверхности ствола с отмерши ми тканями и отходящая от него радиальная'трещина; возникает в растущем дереве при зарастании нанесенных повреждений. По расположению и глубине прорости различают: открытую, одностороннюю открытую, сквозную откры тую, закрытую, сросшуюся; а по цвету: светлую и темную.
Рак _ рана, возникшая на поверхности ствола растущего дерева в ре зультате деятельности паразитных грибков и бактерий. По разновидности рак различают: открытый — незаросшая рана с плоским или углубленным дном, ступенчатыми краями и наплывами по периферии; закрытый зарос шая рана с ненормальными утолщениями тканей коры и древесины возле
пораженных мест.
Засмолок — участок древесины, обильно пропитанный смолой; присущ
хвойной древесине.
Ложное ядро — темная окраска внутренней части ствола, возникающая
в растущих деревьях (береза, бук, ольха и др.).
Пятнистость — местная окраска заболони в виде пятен и полос; возника ет в растущих деревьях. В зависимости от характера распространения на сор тименте различают тангенциальную или радиальную пятнистость, а также прожилки разбросанные, групповые и следы от прожилок.
Внутренняя заболонь — группа смежных годичных слоев, расположен ных в зоне ядра, -окраска и свойства которых близки к окраске и свойствам заболони.
Водослой — участки ядра или спе лой древесины ненормальной темной окраски, возникающие в растущем де реве при резком увеличении их влаж ности.
Химические окраски — ненормаль ные окраски, возникающие в срублен
ной древесине в результате развития химических и биохимических процессов (чаще всего окисление дубильных веществ). В зависимости от цвета и харак тера различают: продубину, дубильные потеки, желтизну, светлые или тем ные окраски.
Грибные поражения весьма многочисленные и могут возникать как в древесине растущих деревьев, так и в срубленных. Грибы относятся к про стейшим растительным организмам и принадлежат к группе споровых расте ний. Споры с помощью ветра или воды попадают на здоровую древесину и начинают там развиваться. Для их развития благоприятным условием Яв ляется влажность 25—35%. При влажности ниже 20% грибы развиваться не могут. Невозможно развитие грибов и при полном насыщении водой, так как в ней недостает воздуха. При температуре ниже 2°С и выше 40—45°С раз витие грибов прекращается, а при 60°С большинство грибов погибает. Пита тельным веществом для грибов является целлюлоза клеток. Под воздействи ем грибов в древесине происходят изменения двоякого рода. В одном случае грибы изменяют лишь цвет древесины. Такие грибы называют деревоокрашивающими.
В других случаях, кроме изменения цвета древесины (в начальной ста дии), грибы приводят к ее разрушению (гниению) и называются дерев0разрушающими.
Некоторые грибы развиваются только на растущих деревьях, другие ,_ только на срубленных, а есть грибы, которые развиваются как на*растущих, так и на срубленных, например гниль дуба белая или бурая, гниль листвен ных пород белая и др. Грибы, вызывакЯдие загнивание древесины непосред ственно в зданиях, называются домовыми. Наиболее опасными, быстро раз рушающими древесину являются грибы: настоящий, белый, пленчатцд, пластинчатый.
В соответствии с ГОСТ 2140—81 грибные поражения разделяются на сле дующие виды.
Грибные ядровые пятна и полосы — участки ненормальной окраски ядра; существенно не влияют на механические свойства древесины, портят лишь внешний вид.
Ядровая гниль — участки ненормальной окраски ядра с пониженной твер достью. По разновидностям гниль бывает: пестрая ситовая, бурая трещинова тая и белая волокнистая. Ядровая гниль снижает механическую прочность.
Плесень — поверхностное окрашивание древесины в различные цвета (сине-зеленый, голубой, черный, розовый и др.). Она не влияет на механи ческие свойства древесины, но ухудшает ее внешний вид.
Заболонные грибные окраски — ненормальные по окраске участки забо лони без снижения ее твердости. В зависимости от цвета, его интенсивности и глубины они ухудшают внешний вид без изменения механических свойств.
Побурение — бурая окраска древесины заболони; мало изменяет проч ность и твердость, но ухудшает ее внешний вид.
Заболонная гниль — ненормальные по окраске участки заболони. Разли чают твердую или мягкую заболонную гниль соответственно с меньшим и большим снижением прочности.
Наружная трухлявая гниль — участки ненормальной окраски, структуры и твердости древесины, возникающие при хранении лесоматериалов под воз действием сильных дереворазрушающих грибов. Пораженная древесина рас падается на части и растирается в порошок.
Повреждения насекомыми могут быть у деревьев на корню и у спиленных. Насекомые поражают преимущественно неокоренные свежесрубленные лесо материалы. К наиболее распространенным видам насекомых, поражающих срубленную древесину, относятся личинки жуков и бабочек, осы, жуки, тер миты. Некоторые из них проделывают ходы только в коре, другие (древесин ники, древогризы, точильщики) углубляются в древесину. Совокупность хо дов и отверстий, проделанных в древесине насекомыми, называется червото чиной. В зависимости от глубины проникания и размеров ходов червоточина бывает: поверхностная, неглубокая, глубокая, сквозная, некрупная и круп ная. Поверхностная червоточина не влияет на механические свойства древе сины. Остальные виды червоточины снижают ее механические свойства и способствуют заражению грибами.
Инородные включения и дефекты подразделяются на инородные включе ния, механические повреждения, обугленность и ряд других.
Инородные включения представляют собой присутствие в древесине инородных тел (камней, песка, металлических предметов). Наличие их за трудняет обработку древесины.
Механические |
повреждения — повреждения древесины механизмами |
и инструментами |
при заготовке, подсечке, транспортировании, сортировке |
иобработке. К механическим повреждениям относятся: обдир коры, заруб
изапил, карра (повреждение ствола при подсечке), отщип, скол и вырыв, багорные наколы. Механические повреждения снижают качество древесины.
Обугленность — обгорелые и обуглившиеся участки древесины.
Скос пропила — неперпендикулярность торца древесины к продольной оси сортимента.
Обзол — участок боковой поверхности, сохранившийся на обрезном пило материале. Различают обзол тупой и острый.
Закорина — участок коры, сохранившийся на поверхности шпона. Дефекты обработки резанием — повреждения поверхности сортимента
режущим инструментом. Различают следующие дефекты: риски, волнистость, ворсистость, мшистость, рябь шпона, задиры и выщербины, бахрома, ожог.
Деформация (покоробленность) — искривление пилопродукции при вы пиловке, сушке или хранении. Различают следующие основные разновидности покоробленности: продольная по пласти, простая и сложная по пласти, про дольная по кромке, поперечная, крыловатость (спиральное искривление сор
тимента по длине).
Рассмотренные пороки и дефекты в зависимости от их вида и размера снижают качество древесины.
§ 13.5. ЗАГОТОВКА И СУШКА ДРЕВЕСИНЫ
Древесину можно заготавливать круглый год, но лучшим временем для заготовки считается осенне-зимний период. К этому периоду количество пита тельных соков уменьшается и наружная поверхность древесины закрыта по следним годичным слоем, состоящим из плотной летней древесины.
Заготовка древесины состоит из валки деревьев, очистки их от сучков и раскряжевки. Лесозаготовки ведутся механизированно, валку и раскряжев ку выполняют цепными бензомоторными или электрическими пилами, трелев ку (перемещение сваленных деревьев) — тракторами, лебедками.
Основной (нижний) склад лесозаготовительного предприятия располага ется у железной дороги или сплавной реки и представляет собой механизиро ванный цех, оснащенный окорочными станками, балансирными и цепными пилами, шпалорезными установками и другими механизмами для переработ ки древесины.
Свежесрубленная древесина легко загнивает и имеет меньшую прочность, чем сухая. Влажная древесина хуже обрабатывается и имеет большую плот ность, что увеличивает транспортные расходы. Высушивание древесины до определенной влажности (12—18%) предохраняет ее от коробления и рас трескивания, а также облегчает обработку и склеивание. Процесс сушки заключается в удалении из древесины влаги путем испарения, при этом пол ностью удаляется капиллярная и часть гигроскопической влаги. Чтобы избе жать неравномерности распределения влаги при сушке, что приводит к появ лению трещин и короблению, интенсивность испарения влаги с поверхности древесины не должна превышать скорость перемещения ее внутри.
Различают сушку: воздушную, камерную, контактную, в электрическом поле высокой частоты и в жидких средах.
Воздушная сушка древесины — это самый простой и недорогой способ. При воздушной сушке древесину укладывают в проветриваемые штабеля на открытом воздухе или под навесом. Древесина высыхает медленно и рав номерно, практически без коробления и с минимальной усушкой.
Продолжительность воздушной сушки зависит от породы, толщины древе сины, а также от климата и погоды во время сушки и составляет 1—2 мес при влажности воздуха 60%, а при большей влажности — до 1 года. При этом
возможно поражение древесины грибами и гнилями, особенно при повышен ной влажности.
Камерная сушка позволяет получить пиломатериал любой заданной ко
нечной влажности, а процесс сушки сокращается примерно в 10 раз по срав нению с воздушной сушкой. F
Камерная сушка пиломатериалов осуществляется в сушильных камерах периодического и непрерывного действия воздухом или газами (в основном топочными) при температуре от 45 до 120°С. Для предотвращения неравно мерного высыхания по толщине и появления коробления и трещин сушка пиломатериалов происходит при определенном температурно-влажностном режиме. Продолжительность камерной сушки (при начальной влажности
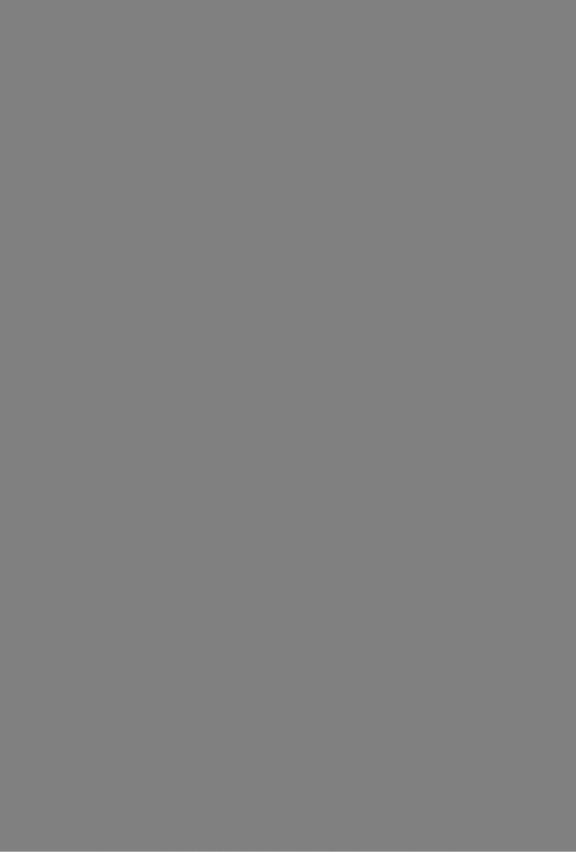
При продольном распиливании бревна по одному или двум взаимно перпендикулярным диаметрам получают соответственно пластины и четвер
тины (рис. 13.6).
Доски получают при продольном распиливании бревна, но когда образую щаяся пилопродукция имеет отношение ширины к толщине более двух. Если это отношение менее двух, получают бруски (рейки)-; при ширине и толщине пиломатериала более 100 мм — брусья.
Горбыль — крайние спилы бревен, получаемые как остатки при распилов ке бревен на доски или брусья.
Шпалы— продукция, получаемая при продольном распиливании бревен с поперечным сечением, близким к брусьям, длиной 1,35—2,7 м. Шпалы при меняют в железнодорожном строительстве.
Шашка из древесины представляет собой бруски четырехили шестигран ной формы. Высота шашки для полов 60—80 мм, для дорожных мостовых по крытий 100—120 мм, ширина 50—100 мм. Влажность древесины для шашки должна быть не более 25%. Шашки изготавливают из древесины хвойных и твердых лиственных пород, за исключением пихты, березы, бука и дуба. Учитывают шашку в квадратных метрах их.торцовой поверхности,
В зависимости от чистоты обработки пилопродукция делится на односто роннеобрезную, обрезную и необрезную с различной степенью непропилов (обзелов).
Полуфабрикаты, заготовки и изделия. Полуфабрикаты и заготовки —
это доски или бруски, прирезанные применительно к заданным |
размерам, |
с соответствующими припусками на механическую обработку |
и усушку. |
К ним относятся шпунтованные доски для полов, плинтусы, галтели для за делки пространства между полом и стенами, наличники для обшивки окон ных и дверных коробок.
Фанера — это тонкий листовой материал, который получают склеиванием древесного шпона в три и более слоев во взаимно перпендикулярном направ лении волокон. Шпон получают на специальных станках путем срезания слоя древесины в виде широкой ленты с вращающегося, предварительно распарен ного кряжа березы, дуба, ольхи, сосны. В зависимости от вида применяемого клея получают фанеру: водостойкую (ФСФ), склеенную фенолоформальдегидными клеями; средней водостойкости (ФК), склеенную карбомидными клеями; ограниченной водостойкости (ФБА), склеенную альбуминоказеино выми или белковыми клеями.
Строительные детали — это элементы сборных домов, различные столяр ные изделия, изготовленные на специализированных заводах. Наиболее про грессивными являются клееные деревянные конструкции, которые применя ют в покрытиях, перекрытиях, мостах в качестве балок, арок, металлодере вянных ферм и других конструкций.
Клееные конструкции изготавливают путем склеивания досок (брусков) фанеры с применением водостойких фенолоформальдегидных и других
клеев, обеспечивающих получение швов большей прочности, чем прочность самой древесины.
Древесноволокнистые плиты изготавливают в процессе горячего прессова ния или сушки массы из древесного волокна. Сырьем для производства плит служит неделовая древесина, отходы хвойных и лиственных пород, а также
стебли некоторых сельскохозяйственных растений (пшеницы, хлопчатника, кенафа и др.).
Сверхтвердые плиты изготавливают с применением полимеров. Для при дания древесноволокнистым плитам водо-, био- и температуростойкости
волокнистую массу обрабатывают гидрофобными эмульсиями, антисептика ми и антипиренами.
В зависимости от объемной массы и прочности древесноволокнистые пли ты подразделяют на мягкие (М-4, М-12, М-20), полутвердые (ПТ-100), твердые (Т-350, Т-400), сверхтвердые (СТ-500). В условном обозначении марки древесноволокнистых плит буквы обозначают вид плиты, цифры — предел прочности при изгибе. Основные свойства этих плит приведены в табл. 13.6.
Древесноволокнистые плиты выпускают толщиной от 2,5 (сверхтвердые) до 25 мм (мягкие), длиной 1200—5500 и шириной 1000—2140 мм.
Мягкие древесноволокнистые плиты применяют для тепло- и звукоизоля ции стен, потолков, полов, перегородок жилых зданий, при утеплении бесчердачных кровель промышленных сооружений.
Т а б л и ц а 13.6
|
|
|
Нормы для плит марок |
|
|
||
Показатели |
|
Мягкие |
|
Полутвердые |
Твердые |
Сверхтвердые |
|
|
М-4 |
М-12 |
М-20 |
ПТ-100 1 |
Т-350 |
Т-400 |
Т-500 |
Объемная |
До 150 |
Не более |
Не более * |
400—800 |
Не менее |
Не менее |
Не менее |
масса, кг/м3 |
350 |
350 |
850 |
850 |
950 |
||
Предел |
|
|
|
|
|
|
|
прочности, |
|
|
|
|
|
|
|
при изгибе, |
|
|
|
|
|
40 |
|
МПа не менее |
0,4 |
1,2 |
2 |
10 |
35 |
50 |
|
Коэффици |
|
|
|
|
|
|
|
ент теплопро |
|
|
|
|
|
|
|
водности, |
0,055 |
0,07 |
0,093 |
|
Не норм!нруется |
|
|
Вт/ (М • К) |
|
|
Твердые и сверхтвердые плиты используют в строительстве для покрытий полов, перегородок, а также в производстве мебели, автомобиле- и вагоно строении и др.
Древесностружечные плиты изготавливают горячим прессованием специально приготовленной древесной стружки с добавкой полимеров. Для древесной стружки используют неделовую древесину, отходы лесопиле ния и деревообрабатывающих производств. В качестве связующего применя ют термореактивные полимеры — фенольные, карбамидные в количестве 6— 12% от массы сухой стружки. Для улучшения свойств в сырьевую смесь до бавляют гидрофобизаторы, антисептики и антипирены.
Выпускают однослойные и многослойные сплошные и многопустотные/ древесностружечные плиты. По объемной массе древесностружечные плиты делят на мягкие с плотностью 250—400 кг/м3, полутяжелые — 400— 800 кг/м3 и тяжелые — 800—1200 кг/м3 Древесностружечные плиты исполь зуются в строительстве для настила полов, отделки стен и потолков, а также
вмебельной промышленности.
§13.7. КОНСЕРВИРОВАНИЕ ДРЕВЕСИНЫ
Взависимости от условий службы (наличия влаги, промерзания, загряз ненности органического характера и др.) древесина подвергается разруше нию и гниению. Для увеличения срока службы, предохранения от загнивания древесину подвергают консервированию, обрабатывают ее антисептиками.
12 Зак. 107 |
353 |
Типы и |
|
|
|
|
|
|
|
|
классы ан |
|
|
|
|
|
|
|
|
тисептиков |
Наименование |
Индекс |
|
Состав |
Характеристика |
|
||
по раство |
|
|
||||||
антисептиков |
|
|
||||||
римости# и |
|
|
|
|
|
|
|
|
|
|
|
|
|
|
|
|
|
вы мывас- |
|
|
|
|
|
|
|
|
мости |
|
|
|
|
|
|
|
|
1 |
2 |
3 |
|
|
4 |
|
5 |
|
ВР-ЛВ |
Кремнефтори |
КФА |
(NH4)2SiF |
Растворимость в воде 18— 19%, |
||||
|
стый аммоний |
|
|
|
|
без запаха, не окрашивает древе |
||
|
|
|
|
|
|
сину, вызывает коррозию черных |
||
|
|
|
|
|
|
металлов |
|
|
ВР-ЛВ |
Препарат ББК-3 |
ББК-3 |
Бура |
техниче |
Растворимость в воде 24%, без |
|||
|
|
|
ская |
|
(Na2 B40 7X |
запаха, не окрашивает |
древесину, |
|
|
|
|
X 10 Н20) и бор |
не вызывает коррозии черных ме |
||||
|
|
|
ная |
кислота |
таллов |
|
|
|
|
|
|
(Н3ВО3) |
|
|
|
||
ВР-ЛВ . |
Фтористый нат |
ФН |
|
|
NaF |
Растворимость в воде 3,5%, без |
||
|
рий |
|
|
|
|
запаха, не |
окрашивает |
древесину, |
|
|
|
|
|
|
вызывает коррозию черных метал |
||
|
|
|
|
|
|
лов |
|
|
ВР-В |
Паста ФН-П |
ФН-П |
Фтористый нат |
Вызывает |
коррозию |
металлов, |
||
|
|
|
рий |
NaF + као- |
загрязняет поверхность древесины |
|||
|
|
|
лин |
+ |
каменно |
|
|
|
|
|
|
угольный лак + |
|
|
|
||
|
|
|
-1-вода |
|
|
|
||
ВР-В |
Препарат ГР-48 |
ГР-48 |
Пентахлорфено- |
Растворимость до 20%, не вы |
||||
|
|
|
лят натрия 4-сода |
зывает коррозии металлов |
||||
|
|
|
кальцинирован |
|
|
|
||
|
|
|
ная |
|
|
|
|
|
ВР-В
ВР-ТВ
ВР-ТВ
ВР-ТВ
ВР-НВ
л-нв м-нв
Л-НВ
м-нв
Кремнефторис |
КФН |
Na2SiF6 |
Растворимость |
в |
|
воде |
0,65%, |
||||||||
тый натрий |
|
|
|
без запаха, окрашивает древесину, |
|||||||||||
|
|
|
|
вызывает коррозию металлов |
|
|
|||||||||
Хромхлорцинко- |
ХХЦ |
Цинк хлористый |
Растворимость в воде более 10%, |
||||||||||||
вый препарат |
|
ZnCI2 + 6 H x p o M a T |
без |
запаха, |
вызывает |
коррозию |
|||||||||
|
|
натрия |
|
металлов, |
снижает |
прочность |
дре |
||||||||
|
|
Na2Cr20 7 • 2Н20 |
весины |
|
|
|
|
|
|
|
|
|
|
||
Меднохром- |
МХХЦ |
Цинк хлористый |
Растворимость в воде более 10%, |
||||||||||||
хлорцинковый |
|
ZnCl2 + медный |
без |
запаха, |
слегка, |
окрашивает |
|||||||||
препарат |
|
купорос |
CuS04 • |
древесину, |
вызывает коррозию ме |
||||||||||
|
|
• 5Н20 + бихро- |
таллов, |
снижает |
|
прочность |
|
дре |
|||||||
|
|
мат натрия |
весины |
|
|
|
|
|
|
|
|
|
|
||
|
|
Na2Cr20 7 • 2Н20 |
|
|
|
|
|
|
|
|
|
|
|
|
|
Пентахлорфено- |
ПХФН |
C6Cl5ONa • Н20 |
Растворимость в воде 25%, дре |
||||||||||||
лят натрия |
|
|
|
весина |
темнеет, |
вызывает |
корро |
||||||||
|
|
|
|
зию меди, латуни |
|
|
|
|
|
|
|
||||
Хромомедный |
ХМ-5 |
Медный купорос |
Растворимость |
в |
воде |
|
более |
||||||||
препарат |
|
CuS0 4 • 5H20 -f |
1 0 %, |
окрашивает |
древесину, |
вы |
|||||||||
|
|
4-бихромат нат |
зывает коррозию металлов и сни |
||||||||||||
|
|
рия |
|
жает прочность древесины |
|
|
|
||||||||
|
|
Na2Cr20 7 • 2Н20 |
|
|
|
|
|
|
|
|
|
|
|
|
|
Препарат пента- |
ПХФ |
Пентахлорфенол |
Окрашивает древесину, |
не |
вызы |
||||||||||
хлорфенола |
|
С6С13ОН + орга |
вает коррозии |
металлов, сообщает |
|||||||||||
|
|
нические раство |
древесине |
водоотталкивающие |
|||||||||||
Нефтенат меди |
НМ |
рители |
|
свойства |
|
|
|
|
|
не |
вызы |
||||
Содержит не ме |
Окрашивает древесину, |
||||||||||||||
|
|
нее 9% |
металли |
вает коррозии |
металлов |
|
|
|
|
||||||
|
|
ческой |
меди |
|
|
|
|
|
|
|
|
|
|
|
|
/
1 |
2 |
3 |
М-ТВ |
Сланцевое масло |
СМ |
м - н в |
Кремнеугольное |
КМ |
|
пропиточное мас |
|
|
ло |
|
м - н в ' |
Антраценовое |
AM |
|
масл*) |
|
|
4 |
5 |
|
Продукт перера |
Окрашивает древесину в темный |
||
ботки |
горючих |
цвет, не вызывает коррозии ме |
|
сланцев |
фракций |
таллов |
|
210—350°С |
|
||
Продукт перера |
|
||
ботки |
каменно |
То же |
|
угольной |
смолы |
|
|
фракции |
2 1 0 — |
|
|
360°С |
|
|
|
То же |
|
|
П р и м е ч а н и е . Растворимость и воде указана при 20°С
Антисептиками называют вещества, применяемые для защиты древесины от гниения. Они должны обладать высокой токсичностью к разрушающим грибам и быть безвредными для человека и домашних животных, хорошо проникать в древесину, не вымываться водой и не вызывать коррозию метал
лов. |
|
|
|
|
|
|
на классы: |
||
I |
По стойкости к гниению породы древесины подразделяют |
||||||||
— стойкие (сосна, ясень, ядро дуба |
и лиственницы); |
|
ядро |
||||||
II |
— среднестойкие |
(ель, |
пихта, |
заболонь |
кедра |
и лиственницы, |
|||
|
бука); |
(заболонь березы, |
бука, |
граба, |
дуба и |
клена, |
ядро |
||
III — малостойкие |
|||||||||
|
вяза); |
|
|
|
|
|
|
|
|
IV — нестойкие (ольха, осина, заболонь липы, ядро березы). |
|
|
|||||||
на |
По пропитываемости антисептиками древесные породы подразделяют |
||||||||
группы: |
|
(заболонь березы, бука и сосны) |
|
|
|||||
1- я — легкопропитываемые |
граба, |
дуба, |
|||||||
2- я — умереннопропитываемые (кедр, |
ольха, |
осина, |
заболонь |
||||||
3- |
клена, липы, лиственницы); |
лиственница, пихта, ядро |
березы, |
бука, |
|||||
я — труднопропитываемые (ель, |
|||||||||
|
дуба). |
|
|
|
|
|
|
|
|
|
Антисептики делят на следующие типы: водорастворимые — ВР; раство |
римые в легких органических растворителях — Д; растворимые в маслах и тяжелых нефтепродуктах — М. Кроме этого, антисептики характеризуются вязкостью, водоотталкивающими и окрашивающими свойствами. По вымываемости антисептики делят на классы: легковымываемые — ЛВ, трудновымываемые — ТВ, вымываемые — В, невымываемые — НВ. Краткая характе ристика применяемых антисептиков приведена в табл. 13.7.
Основные способы пропитки древесины. Способы пропитки древесины за висят от характера увлажнения деревянных деталей (постоянное, перемен ное) и условий их работы. Различают три основных вида пропитки: диф фузионную, капиллярную и под давлением.
Диффузионная пропитка в зависимости от способа нанесения на поверх ность осуществляется обмазыванием, опрыскиванием и погружением. Для этого применяют древесину с влажностью 40% и выше. Водораствори мые антисептики наносят на поверхность кистью, при помощи опрыскивате лей или погружением в ванну. Антисептик растворяется и диффундирует
втолщу древесины на глубину 1—2 мм.
Кдиффузионному виду относится бандажный способ обработки, который
заключается в том, что защищаемый участок сортимента обвертывают банда-
|
|
Средний срок службы древесины. лет |
|
Порода дерева |
непропитанной |
пропитанной креозотовым |
пропитанной хлористым |
|
маслом |
цинком |
|
Сосна |
6 - 8 |
20 |
15 |
Лиственница |
8 — 10 |
20 |
— |
Ель |
4—5 |
— |
10 |
Дуб |
12—15 |
25 |
18 |
Бук |
2—3 |
30 |
10 |
жом из двух слоев, между которыми наносят антисептик — пасту. Наружную поверхность ткани обмазывают водонепроницаемым веществом. При этом способе почвенная вода, попадающая в дерево через его нижнюю часть, пере двигается вверх вследствие высыхания надземной части столба или сваи. По мере движения вода растворяет поступающий антисептик и пропитывает им верхнюю часть столба или сваи.
Капиллярная пропитка осуществляется антисептиками, растворимыми как в воде, так и в органических растворителях. Более длительное (несколько дней) выдерживание древесины в пропиточных растворах позволяет полу чить требуемую глубину пропитки.
Пропитка под давлением осуществляется в горяче-холодных ваннах или в автоклавах. При пропитке в горяче-холодных ваннах древесину сначала помещают на несколько часов в ванну с раствором антисептика* имеющего температуру 85—95°С, а потом быстро перекладывают в ванну с раствором, имеющим температуру 20—25°С. В горячей ванне воздух и вода, находящие ся в древесине, расширяются и частично выделяются из древесины. Когда древесину перемещают в ванну с холодным антисептиком, воздух и влага, охлаждаясь, уменьшаются в объеме, и антисептик засасывается внутрь.
При этом способе пропитки можно применить антисептики, растворимые как в воде, так и в органических растворйтелях и маслах. Пропитка в горяче холодных ваннах продолжается в течение 8—12 ч.
Пропитку в автоклавах производят под действием вакуума (разряженно го воздуха) и давления. Пропитка состоит из следующих процессов: лесома териал загружают в пропиточный бак и герметически закрывают крышкой. В баке создается вакуум, при котором материал выдерживают 20—30 мин для удаления воздуха из древесины и бака; затем бак наполняют антисепти ком и создают в нем давление 0,6—0,8 МПа, которое выдерживают 60 мин. После этого давление снижают и создают кратковременный вакуум на 10— 15 мин. Затем создают нормальное давление, выпускают антисептик и извле кают из бака пропитанный антисептиком лесоматериал.
При пропитке древесины маслянистыми антисептиками (например, крео зотовым маслом) их предварительно подогревают до определенной темпера туры для того, чтобы температура антисептика в баке при пропитке не снижа лась ниже установленного предела. Пропитывать древесину можно в ваккумных установках.
Защиту древесины антисептиками применяют в мостовом и дорожном строительстве. Антисептиками пропитывают деревянные части мостов, трубы, лотки, столбы и другие конструктивные элементы.
В табл. 13.8 приведены данные о сроках службы в неблагоприятных усло виях древесины (шпал), непропитанной и пропитанной креозотовым маслом и хлористым цинком
Легкая воспламеняемость дерева — один из существенных его недостат ков. При действии на древесину высоких температур она претерпевает ряд глубоких химических изменений. С химической точки зрения древесина не способна гореть — горят лишь продукты ее распада. Вначале должно быть затрачено тепло для достижения первой фазы распада древесины, затем наступает вторая фаза, при которой выделяется тепло. Хотя в пределах 100— 200°С древесина улучшает свои свойства за счет образования некоторых высокомолекулярных веществ, но уже при 165°С древесина разлагается с вы делением горючих газов. Горючие газы появляются при 170—200°С, бурное же их выделение происходит при 275—280°С. Точки воспламенения для от дельных пород древесины находятся в различных температурных пределах: для сухой сосны, например, она равна 130°С, для дуба — 245°С.
Применяемые в настоящее время различные способы предохранения древесины от огня уменьшают только ее воспламеняемость, но способность тлеть дерево при этом не утрачивает. Для предохранения древесины от воз горания ее обрабатывают смешанными химическими веществами — антипи ренами. При нагревании древесины, пропитанной антипиренами, они разлага ются с образованием сильных кислот (фосфорной, серной), которые, дегид ратируя древесину, препятствуют образованию высококалорийных газов и предохраняют ее от горения. Некоторые антипирены при нагревании пла вятся и образуют защитные пленки или выделяют негорючие газы, препят ствующие поступлению кислорода к поверхности древесины.
Наибольшее применение в качестве антипиренов имеют диаммонийфосфат, сульфат аммония, бура, борная кислота. Диаммонийфосфат и сульфат аммония растворяются в воде (70—75%), применяются в смеси с другими антипиренами. Бура растворяется в воде при температуре 20°С до 25%, при 80°С до 31%. Применяется она в смеси с борной кислотой.
Огнезащитные краски по составу делят на силикатные, перхлорвиниловые (ПХВО). Силикатные огнезащитные краски представляют собой смесь жидкого стекла с наполнителем (тонкомолотый мел, полевой шпат) и пигмен: том.
Перхлорвиниловая огнезащитная краска состоит из перхлорвиниловой смолы, растворителя, пигмента (сурика, алюминиевой пудры). Краска атмос феростойкая, может быть различного цвета.
Для обработки древесины антипиренами применяют пропитку, обмазку и покраску. Пропитка в автоклавах или горяче-холодных ваннах является наиболее надежным способом защиты древесины. Нередко применяют по верхностную пропитку вымачиванием древесины в растворах антипиренов или нанесением их гидропультом, кистью. Обмазку производят специальными огнезащитными настами, которые наносят кистями слоем 2—3 мм. Сцепление (адгезия) обмазочных паст невелико, и их необходимо периодически обнов
лять.
Покраску древесины огнестойкими силикатными и перхлорвиниловыми красками производят кистями или гидропультами. При введении в состав краски пигментов (белил, охры и др.) улучшается внешний вид окрашивае мой поверхности.
Огнезащитную обработку древесины сочетают с пропиткой антисептика
ми.
Большинство антисептиков и инсектицидов вредно действует на человека, поэтому при работе с ними необходимо соблюдать меры предосторожности: работать в защитных очках, костюмах, перчатках и в респираторе.
Глава 14 МЕТАЛЛИЧЕСКИЕ МАТЕРИАЛЫ
§14.1. ОБЩИЕ СВЕДЕНИЯ
Кметаллам относится большая группа химических элементов — из 109 известных 82 являются металлами. Наиболее распространенные металлы^: алюминий (содержание в земной коре 8,8%), железо (5,1%), кальций (3,62%), натрий, калий, магний, титан. Содержание остальных металлов составляет около 2%. Ряд металлов (цинк, олово, никель, свинец, кобальт,
вольфрам, молибден, ванадий) содержится в тысячных долях процента, но имеют большое значение для получения высококачественных сплавов. Такие металлы, как кальций, натрий, калий, не применяют в качестве кон струкционных. В зависимости от свойств металлы разделяют на:
черные — железо и его сплавы, которые в зависимости от вида и количест ва примесей (углерода, марганца, никеля, хрома, титана и др.) обладают различными свойствами и составляют 85—90% всего металла, применяемого в народном хозяйстве;
цветные — большая группа металлических материалов (алюминий, медь, магний, свинец, олово, цинк, а также их сплавы).
В последнее время все большее распространение в строительстве получа ет алюминий. Не окисляющиеся на воздухе металлы (золото, платина, сереб ро) называются благородными.
§ J4.2. СТРУКТУРА И СВОЙСТВА МЕТАЛЛОВ
Характерная особенность строения металлов — наличие металлической связи между атомами. Атомы металлов на внешней оболочке содержат не большое количество слабосвязанных электронов. Электронные облака атомов перекрываются, поэтому внешние электроны могут свободно перемещаться и являются как бы общими, не связанными с отдельными атомами. Таким образом, общие электроны образуют электронный газ,, который свободно двигается между ионами и скрепляет их друг с другом. Эта особенность оп ределяет стремление атомов металла располагаться как можно плотнее. Ком пактная упаковка атомов приводит к повышенной плотности металлов.
Металлы и сплавы в твердом состоянии имеют кристаллическое строение которое характеризуется определенным, закономерным расположением атомов. Атомы в кристалле металла образуют пространственную кристал лическую решетку, состоящую из многократно повторяющихся ячеек, имею щих относительно простую форму.
Большинство металлов имеет кубическую объемно-центрированную
икубическую гранецентрированную решетку. Например, хром, ванадий, мо либден, вольфрам и некоторые другие металлы имеют кубическую объемно. центрированную решетку (ОЦК), а алюминий, медь, никель, свинец, золот0
исеребро — кубическую с центрированными гранями (ГЦК). Некоторые металлы, например железо, могут существовать в нескольких кристалли ческих формах с различным расположением атомов. Это явление называется
Внаписании гл. 14 принимала участие проф. С. С. Дьяченко.
аллотропией, |
или полиморфизмом, а само |
превращение |
одной решетки |
|
в другую — полиморфным превращением |
(рис. 14.1). |
количестве для |
||
Железо в |
чистом виде применяется |
в |
ограниченном |
специальных целей. Высокая прочность, твердость в широком интервале тем ператур, устойчивость от коррозии достигаются только в сплавах. Компонен тами сплавов могут быть металлы —железо, медь, алюминий, свинец, цинк, олово, никель и другие, а также металлоиды — углерод, кремний.
В'зависимости от сродства (взаимодействия) между компонентами спла вы (в жидком состоянии чаще всего представляющие собой растворы) при затвердевании и кристаллизации могут образовывать химическое соединение, твердый раствор или механическую смесь.
Химические соединения получают при строго определенном соотношении компонентов, они образуют новые кристаллические решетки, отличные от ре шеток входящих компонентов. Примером химического соединения является соединение железа с углеродом Fe3C — карбид железа, или цементит. Хими ческое соединение, как правило, намного тверже компонентов, из которых оно образовалось.
Твердые растворы представляют собой сплавы, в которых сохраняется
решетка растворителя, а атомы растворенного |
элемента внедряются |
в кристаллическую решетку (растворы внедрения) |
или замещают в ней |
атомы растворителя (растворы замещения). |
|
Механическая смесь состоит из смеси кристалликов чистых элементов, твердых растворов или химических соединений.
Исследование особенностей структуры показало, что большинство метал лов имеет зернистую структуру. Зерна имеют неправильную форму размером в десятые доли миллиметра и представ ляют собой отдельные кристаллы. Та ким образом, даже малый образец ме талла состоит из большого числа раз личным образом ориентированных кри сталлов, соединяющихся между собой общими для них границами (рис. 14.2).
При охлаждении металла ниже температуры плавления кристалличе ские зерна растут, практически смы каясь с ближайшими соседями, и гра ница между ними вырождается в по верхность раздела, толщина которой не превышает одного-двух межатомных
расстояний.
Структура реальных сплавов в зна чительной степени отличается от иде ального строения кристаллов. В реаль ном металле всегда имеются нару шения макро- и микроскопического характера (поры, газовые и неметалли ческие включения, микротрещины и пр.), а также дефекты кристаллического строения, связанные с нарушением правильного расположения атомов в са мой кристаллической решетке. Все эти виды нарушений заметно влияют на свойства, причем наиболее велика роль несовершенства кристаллического стро-
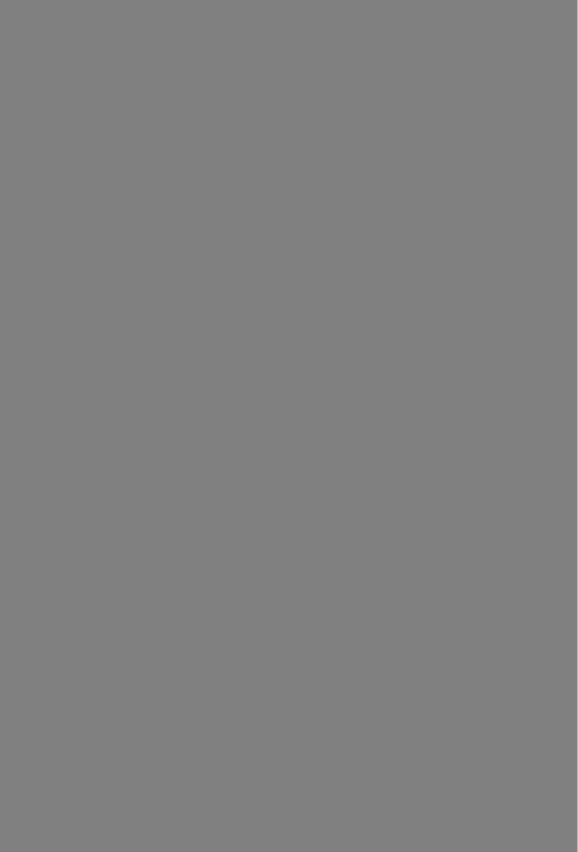
серый чугун, который содержит до 4% углерода, находящегося частично в связанном, частично в свободном состоянии в виде графита. Структура серых чугунов определяется металлической основой (ферритная, перлитная, перлитно-цементная) и графитными включениями, которые тоже различают ся по форме, расположению и содержанию. Таким образом, механические свойства чугуна обусловлены его металлической основой, а также формой
исодержанием графита.
Взависимости от структуры и свойств чугуны разделяются на следующие виды:.
серый чугун с пластинчатым графитом маркируется буквами с последую щей цифрой, указывающей предел прочности при растяжении, который изме
няется от |
L до 4,5 |
МПа |
(например, СЧ 25); |
высокопрочный |
чугун |
с шаровидным графитом маркируется буквами |
|
и цифрами |
(ВЧ 10—2), которые указывают предел прочности при растяже |
нии (в кге/мм2) и относительное удлинение в процентах. Прочность изменя ется от 380 до 1200 МПа, а относительное удлинение от 17 до 2%;
ковкий чугун получают из белого чугуна термической обработкой. В зави симости от металлической основы его разделяют на ферритный (Ф) и перлит ный (П). Ковкий чугун маркируется буквами и цифрами (КЧ 50—5). Цифры указывают соответственно временное сопротивление разрыву (в МПа) и от носительное удлинение (в процентах).
Чугун применяется в строительстве меньше, чем сталь. Изготовление изде лий из него производят методом литья (трубы, тюбинги, колонны, решетки, ограждения), из ковкого чугуна методом прокатки получают кровельный лист.
§ 14.3. СТАЛИ, ПРЙМЕНЯЕМЫЕ В СТРОИТЕЛЬСТВЕ
Сталями называются сплавы на основе железа, содержащие менее 2,14% углерода. Обычно это многокомпонентные системы, в которых наряду с основ ными элементами присутствуют сера, фосфор, кремний, марганец, газы. Сера и фосфор являются вредными и трудно удаляемыми примесями, охрупчивающими сталь. В зависимости от качества стали их количество колеблет ся от 0,025 до 0,06%. Марганец и кремний содержатся в сталях в количестве соответственно 0,5—0,8 и 0,3—0,5% и добавляются в качестве раскислителей, а марганец еще и для нейтрализации вредного действия серы.
На свойства стали очень большое влияние оказывает углерод. С увеличе нием его содержания все прочностные показатели растут, а пластичность и ударная вязкость снижаются. В связи с этим в качестве конструкционных
сталей, которые должны иметь достаточно высокий уровень |
пластичности |
и ударной вязкости, применяются мало- и среднеуглеродистые |
(<0,7% С). |
Стали с большим содержанием углерода по своему назначению являются
инструментальными.
При выплавке в сталь могут добавляться легирующие элементы — хром, марганец, кремний, никель. Такие стали называют легированными. В качест ве строительных применяют как углеродистые, так и легированные стали
(табл. 14.1).
Углеродистые стали. Широкое применение в строительстве находят так называемые стали обыкновенного качества. Эти стали делятся на три группы: А, Б и В. Стали группы А поставляются с гарантированными механическими свойствами, группы Б — с гарантированным химическим составом, груп пы В — с гарантированными свойствами и химическим составом. Маркиру
ются эти |
стали так: группа |
А — СтО, Ст1 |
Стб; группа Б Б СтО, |
Б Ст1 |
Б Стб; группа В — |
В СтЗ В Ст5. |
|
|
<7П, МПа |
от, МПа, |
Относнтель- |
Марка стали |
ав, МПа |
от, МПа, |
Относитель |
Марка стали |
■ше удлинение, |
ное удлине |
|||||
|
не менее |
%, не менее |
|
|
нс менее |
ни е^, не ме |
|
|
|
|
|
||||
|
|
|
|
|
|
|
нее |
Ст 0 |
320 |
— |
2 2 |
Ст 4, |
420—520 |
260 |
2 5 - 2 3 ' |
Ст 1 , Ст 1 кп |
320—400 |
|
33 |
Ст 4 кп |
500—620 |
280 |
21— 19 |
— |
Ст 5 |
||||||
Ст 2, Ст 2кп |
320-400 |
2 2 0 |
31 |
Ст 6 |
600—720 |
310 |
16— 14 |
Ст 3, Ст Зкп |
380—470 |
240 |
27—25 |
Ст 7 |
700—750 |
— |
11 — 19 |
Здесь цифры представляют собой порядковые номера. С увеличением но мера механические свойства сталей и содержание в них углерода возрастают. В зависимости' от степени раскисления стали делятся на спокойные, полуспокойные и кипящие, что отражается в марках буквами сп, пс и кп (соответ ственно), например: СтЗсп, Ст1кп. Кипящие стали более хрупки. Температу ра охрупчивания для спокойных сталей — 20°С, для полуспокойных 0°С, а для кипящих 20°С. Это следует иметь в виду и рекомендовать сталь для конструк ций с учетом условий их эксплуатации, в частности рабочих температур.
Поскольку в строительстве очень широко используется сварка, одним из основных требований, предъявляемых к строительным сталям, является их свариваемость, т. е. способность образовывать качественный, не содержащий трещин шов. Свариваемость ухудшается с увеличением содержания углеро да, так как углерод охрупчивает сталь и увеличивается вероятность образо вания трещин в процессе сварки. Поэтому к строительным относятся главным образом малоуглеродистые стали (с содержанием углерода 0,1—0,25%) ма рок СтО, Ст1, Ст2 и СтЗ. Эти стали поставляются в горячекатаном состоянии и широко используются при строительстве мостов, газо- и нефтепроводов, различных ферм, лестничных маршей и т. д. Для сварных конструкций особен но благоприятны стали группы В, в которой гарантируются свойства и хими ческий состав. Обычно для указанных малоуглеродистых сталей предел теку чести не превышает 240 МПа. В том же случае, если сварка не производится, могут использоваться стали с большим содержанием углерода, а следователь но, с более высокими прочностными свойствами.
«Легированные стали. Вводимые в сталь легирующие элементы изменяют ее механические, физические и химические свойства. В зависимости от содер жания легирующих элементов стали делятся на низколегированные (сумма легирующих элементов<2,5%), среднелегированные (от 2,5 до 10%) и высо колегированные (>10% ). В строительстве наиболее широко применяются низколегированные стали.
Маркировка легированной стали по ГОСТу предусматривает следующие буквенные обозначения легирующих элементов: X — хром, Н — никель, Г — марганец, С — кремний, В — вольфрам, М — молибден, Ф — ванадий, К — кобальт, Т — титан, А — азот, Ю — алюминий, Ц — цирконий, Д — медь, Б — ниобий, Р — бор. Для обозначения состава легированной стали принята следующая маркировка: две первые цифры указывают среднее содержание углерода в сотых долях процента, а цифры, следующие за буквами, — процентное содержание легирующих элементов в стали.
Например, сталь марки 14Г2 содержит |
0,1—0,18% углерода и около |
2% Мп. Если после буквы цифра отсутствует, |
то для таких элементов, как Мп, |
Si, Сг, Си, |
Ni, это соответствует примерно 1% легирующего элемента, |
для V, Zr — |
примерно 0,1 %, для Nb, N — 0,01—0,04%. Так, в стали 16Г2АФ |
содержится |
примерно 0,16% С,около 2% Мп, 0,01% N и около 0,1% V. |
Легирование стали повышает ее прочность, что позволяет уменьшить рас ход металла. Так, повышение предела текучести с 240 (углеродистые стали) до 350 МПа (при легировании марганцем) позволяет сэкономить 15% метал ла, до 400 МПа — 25—30% металла. Стали, легированные Мп и Si, обеспе чивают предел текучести 450 МПа. Поэтому в настоящее время легирован ные стали находят более широкое применение в строительстве, хотя их стои мость выше углеродистых. Наиболее широко применяются стали марок 09Г2, 14Г2, 19Г, 17ГС, 14ХГС, 15ХСНД, 18Г2АФ, 25Г2С. Медь особого влияния на механические свойства не оказывает, однако повышает коррозионную стойкость стали. Особо следует отметить полезное влияние никеля, легирова ние которым резко снижает температуру охрупчивания стали. Поэтому в сталях для северных районов, где конструкции работают при низких темпе ратурах, никель весьма полезен и в ряде случаев совершенно незаменим. Однако никель дорог и применять стали, легированные никелем, следует толь ко в тех случаях, когда это действительно необходимо.
§ 14.4. ТЕРМИЧЕСКАЯ ОБРАБОТКА СТАЛЕЙ
Как было замечено в § 14.2, железо испытывает полиморфные превраще ния. Ниже 911°С оно существует в решетке ОЦК, и такая модификация назы вается Fa. Выше 911 °С железо имеет решетку ГЦК и называется Fy. Наличие полиморфизма обусловливает возможность применения термиче ской обработки для сплавов на основе железа.
Первой операцией термической обработки является нагрев стали в об
ласть существования F . Температура |
перехода в у-состояние зависит |
от содержания углерода. Так, в чистом |
железе она равна 911 °С, в стали |
с 0,4% С—780°С, с 0,8% С—727°С. Зная содержание углерода, назначают температуру нагрева стали и в результате этой операции получают структуру, называемую аустенитом (твердый раствор углерода и других элементов в Fey. После определенной выдержки при этой температуре производят охлаждение. Б зависимости от скорости охлаждения различают три основ ных вида термической обработки: закалку, нормализацию и отжиг. При за калке охлаждение осуществляется в воде или масле, при нормализации — на воздухе, при отжиге — вместе с печью. Чем быстрее скорость охлаждения, тем выше прочность стали. После закалки применяют еще одну термическую операцию, называемую отпуском. Отпуск заключается в нагреве стали ниже температуры полиморфного превращения, т. е. в области существова ния Fey. В зависимости от температуры различают низкий (до 250°С), средний (250—500°С) и высокий (>500°С) отпуск. Чем выше температура отпуска, тем ниже прочность, но выше пластичность и ударная вязкость. Для строительных сталей чаще всего применяют высокий отпуск. Сочетание закалки с высоким отпуском получило название улучшения. При высоком отпуске снимаются закалочные напряжения и повышается пластичность и ударная вязкость стали. Поэтому закалка с высоким отпуском позволяет получить наилучшее сочетание свойств: достаточно высокий предел теку чести, высокие характеристики пластичности и ударной вязкости.
Термическая обработка влияет на порог хладноломкости. Так, для стали СтЗ в горячекатаном состоянии Т =0°С, в нормализованном снижается до -г-20°С, в улучшенном до —40°С.
Для углеродистых строительных сталей с невысоким содержанием углеро да (<0,25%) характеристики прочности после нормализации остаются прак тически такими же, как и для горячекатаной стали (~240 МПа). Это объяс няется одинаковыми условиями охлаждения сталей после горячей прокатки
и после нормализации (на воздухе). Улучшением удается повысить проч ность углеродистых строительных сталей (для СтЗ до ат 280—300 МПа). Больший выигрыш в свойствах получается для легированных сталей. Напри мер, для стали 17ГС предел текучести в горячекатаном состоянии равен 350 МПа, в нормализованном 400 и в улучшенном 450 МПа. Поэтому легиро ванные стали поставляются промышленностью не только в горячекатаном состоянии, но и после того или иного вида термической обработки.
В последнее время для легированных строительных сталей широко приме няется высокотемпературная термомеханическая обработка (ВТМО). Этот метод заключается в сочетании горячей пластической деформации с закал кой. Стальной профиль непосредственно после горячей прокатки подвергает ся закалке с последующим отпуском, что позволяет получить еще более высо кий комплекс свойств. Для сталей после ВТМО характерны высокие проч ность, пластичность и ударная вязкость.
§ 14.5. АРМАТУРНЫЕ СТАЛИ
Для армирования железобетонных конструкций со сварными каркасами и с предварительно напряженной арматурой применяют горячекатаную сталь круглого и периодического профилей. По механическим свойствам арматурная сталь делится на восемь классов: A-I, А-Н, ..., А-III. Стерж ни арматурной стали A-I выпускают круглыми и гладкими, а остальных клас сов — периодического профиля. Для различия сталей каждому классу соот ветствует определенный внешний вид периодического профиля (выступы, идущие по винтовым линиям, в виде елочки и т. д.), а также производится окрашивание концов стержней в разные цвета. В табл. 14.2 приведены свой ства арматурной стали разных классов.
Арматурная сталь классов A-I, А-П и A-III применяется для ненап ряженных конструкций, а сталь остальных классов — для предварительно напряженных. Кроме стержней, железобетонные конструкции армируются еще и проволокой из углеродистой и легированной стали с 0,6—0,8% углеро да. Но свариваемость стали сильно зависит от содержания углерода, ухуд шаясь с увеличением его количества, поэтому при назначении стали для конкретной конструкции это обстоятельство следует учитывать. Например, если для сварной конструкции необходима арматурная сталь IV класса, то следует остановиться на малоуглеродистой стали 20ХГ2Ц. Если же конст рукция не подвергается сварке, железобетон можно армировать высокопроч ной проволокой 80С.
|
|
|
|
Т а б л и ц а |
14.2 |
|
|
|
|
|
Марка стали |
|
|
Класс стали |
МПа |
оп,2. МПа |
6. % |
горячеката |
термоупроч- |
|
|
|
|
|
|||
\ |
|
|
|
ной |
ненной |
|
|
|
|
|
|
|
|
A-I |
380 |
240 |
25 |
Ст 3 |
_ |
|
А-П |
500 |
300 |
19 |
Ст 5 18 Г2 С |
|
|
А-Ш |
600 |
400 |
14 |
35 ГС 25 ГС2 |
_ |
|
A-IV |
900 |
600 |
6 |
20ХГ2Ц 80 С |
Ст 5 |
ГС |
A-V |
1050 |
800 |
6 |
23Х2Г2Т |
Ст 5 35 |
|
A-VI |
1 2 0 0 |
1 0 0 0 |
5 |
_ |
Ст 6 35 ГС |
|
А-VII |
1400 |
1 2 0 0 |
5 |
_ |
45 С |
|
A-VIII |
1600 |
1400 |
4 |
— |
45 ГС |
|
Впромышленности и строительстве широко применяют цветные металлы
исплавы, которые обладают рядом особых свойств: пластичностью, высокой электро- и теплопроводностью, антикоррозионной стойкостью, малой плот ностью (табл. 14.3).
Кредким металлам относят вольфрам, молибден, ванадий, ниобий, цирко
ний. Все они имеют температуру плавления выше 1700°С и применяются в качестве специальных добавок при производстве стали. К редким радио активным металлам относятся уран, торий, актиний, протактиний. В связи с развитием атомной энергии применение их резко возросло. В строительстве из цветных металлов наиболее широко применяют сплавы алюминия и меди.
Алюминий и его сплавы. В связи с открытием нового способа выплавки алюминия непосредственно из руды значительно снизилась стоимость про изводства алюминиевых сплавов и изделий из него. Алюминиевые сплавы рекомендуются для:
несущих конструкций зданий и сооружений (оболочки, рамы, фер мы и т. д.), конструкций для химических предприятий с агрессивной средой (кроме воздействия влажной и щелочной среды, растворов серной кислоты и ее солей), опор линий электропередачи;
ограждающих конструкций, кровельных панелей, подвесных потолков, витрин, переплетов и т. д.
Элементы конструкций из алюминиевых сплавов можно соединять на за клепках, болтах или сваркой. Сварные соединения выполняются механизиро ванной или ручной электродуговой сваркой в защитной среде аргона, электри ческой контактной сваркой, сваркой под слоем флюса и газовой сваркой.
Чистая медь находит применение как электротехнический материал, обла дающий малым удельным электросопротивлением. В строительстве применя ются сплавы меди — латуни и бронзы. Латунями называются сплавы меди с цинком (до 40%), бронзами — с оловом, алюминием, марганцем, никелем. Латуни маркируются буквой Л и цифрами, указывающими содержание меди (Л68—68% Си, 32% Zn). Если в латунь добавлены легирующие элементы, они маркируются буквами, а их количество (в %) — цифрами, например ЛС59-1: 59% С u, 1% РЬ, остальные Zn. Легирующие элементы добавляются в латунь для придания определенных свойств (свинец улучшает обрабатывае мость резанием, олово повышает коррозионную стойкость).
Латунь хорошо обрабатывается прессованием, прокаткой, штамповкой, волочением. Из латуни изготавливают ленту, лист, проволоку, трубы, прутки.
Бронзы обозначаются Бр, буквами и цифрами, указывающими, какой элемент и в каком количестве введен в сплав. Например, марка Бр ОЦС 5-5-5 означает, что в сплаве содержится 5% Sn, 5% Zn, 5% РЬ, а остальное — медь. Бронза — прочный, пластичный материал, хорошо сопротивляющийся коррозии. Свойства бронз зависят от легирующих добавок.
К числу сплавов, хорошо зарекомендовавших и наиболее широко исполь зуемых в строительстве, относятся дюралюмин — сплав алюминия с медью (3,8—4,8%) и магнием (0,5—1,5%), в который для повышения коррозионной стойкости добавляется марганец (0,3—0,9%). Наиболее распространенные марки дюралюминов Д 1 и Д 16. Дюралюмин хорошо деформируется в горя чем и холодном состоянии, производится в виде листов, прутков, профилей и используется в строительных конструкциях для изготовления ферм, силовых каркасов, *в качестве облицовочного материала. Дюралюмин подвергается упрочняющей термической обработке, состоящей в закалке от 500°С и после дующим естественном или искусственном старении. Естественное старение заключается в выдерживании закаленного изделия при комнатной темпера-
Свойства металлов |
|
|
Тяжелые |
|
|
Легкие |
||
Медь |
Никель |
Свинец |
Олово |
Цинк |
Алюминий |
Магний |
||
|
||||||||
Плотность, г/см3 |
8,93 |
8,90 |
11,37 |
7,29 |
7,10 |
2,70 |
1,74 |
|
Температура плавле |
1084 |
1455 |
327 |
231 |
419 |
660 |
651 |
|
ния, °С |
||||||||
Твердость по: |
368 |
950 |
30 |
50 |
350 |
150—300 |
300—400 |
|
Бринеллю, МПа |
||||||||
прочность, МПа |
2 2 0 |
390 |
16 |
28 |
128 |
90—120 |
80—170 |
|
Теплопроводность, |
0,94 |
0,14 |
0,08 |
0,15 |
0,27 |
0,82 |
0,35 |
|
кал/см • с • град |
туре в течение 4—5 сут, искусственное — при температуре 150°С в течение 16—20 ч. В результате такой термической обработки удается значительно повысить механические свойства.
Применение алюминиевых сплавов в строительстве производится с целью уменьшения массы конструкции, удобства монтажа, повышения коррозион ной стойкости и уменьшения эксплуатационных расходов. Медь и ее сплавы (бронза и латунь) применяют для отделочных работ в сооружениях I класса.
Титан и его сплавы. Титан — относительно легкий металл (его плотность равна 4,5 г/см3), по прочности близкий к железу (сгв = 250 МПа). Особен ностью титана является хорошая коррозионная стойкость. В сплавах на осно ве титана может быть достигнут высокий уровень прочностных характери стик (до 1000—1200 МПа). Малая плотность и значительная прочность тита новых сплавов обусловили их широкое применение в авиационной и косми ческой технике.
Одно из важных преимуществ титана — отсутствие охрупчивания при низких температурах. В настоящее время разработан ряд сплавов на основе титана, предназначенных для конструкций, работающих в районах Заполярья и Крайнего Севера.
Титан и его сплавы пока еще мало применяются в строительстве. Это связано с трудоемкостью и техническими сложностями получения титана из руд, что обусловливает довольно высокую его стоимость.
§ 14.7. ОБРАБОТКА МЕТАЛЛОВ ДАВЛЕНИЕМ
Обработка металлов давлением основывается на использовании их пластических свойств, т. е. способности металлов деформироваться под действием внешних сил и сохранять приданную им форму. При обработке
металлов давлением изменяются не только форма исходной заготовки, но и их структура и механические свойства. Для облегчения обработки метал лов и сплавов давлением их предварительно нагревают. Каждый металл и сплав имеет оптимальную температурную зону нагрева: алюминиевые сплавы 350—500, сплавы меди 800—1000, стали 1000—1250°С (в зависимо сти от химического состава). Правильный нагрев металла перед обработкой давлением обеспечивает получение мелкозернистой структуры, а пласти ческая деформация устраняет дефекты литой структуры, приводит к уплотне нию металла и повышению его механических свойств.
Основные виды обработки металлов давлением — прокатка, волочение, прессование, ковка, горячая объемная и листовая штамповка.
Прокатка — деформирование металла путем пропускания заготовки меж ду вращающимися валками, зазор между которыми меньше толщины обраба тываемой заготовки. Металл захватывается валками (благодаря трению между металлом и валками), и происходят деформация и движение заготов ки в направлении подачи (рис. 14.3). При прокатке плоской заготовки толщи на ее уменьшается, а длина и ширина увеличиваются. Прокаткой получают листовой и сортовой прокат простого и фасонного профилей.
Волочение — протягивание заготовки (прутка или трубы) через кони ческое отверстие размером, несколько меньшим, чем сечение заготовки (рис. 14.4). Многократным волочением изготовляют высокопрочную прово локу, трубы и т. д.
Прессование — выдавливание металла заготовки главным образом из цветных металлов и сплавов через профильное отверстие замкнутой формы для получения изделия определенной формы и сечения.
Ковка (свободная) — свободное деформирование нагретой заготовки последовательными ударами молота или нажимами пресса. Свободная ковка является наиболее простым и широко распространенным видом обработки давлением.
Горячая объемная штамповка — деформирование нагретой заготовки в штампе, по форме соответствующем конфигурации изделия. Производи тельность объемной штамповки по сравнению со свободной ковкой выше в 50 раз и более. Этот метод намного экономичнее свободной ковки, при этом качество и точность поковок повышаются.
Листовая штамповка выполняется преимущественно на прессах для об работки листового, ленточного и полосового материала в виде вырезки поло сы, вытяжки пустотелых, открытых с одной стороны изделий и т. д. В послед нее время внедряется штамповка массивных деталей методом взрыва, кото рый является более экономичным по сравнению с другими методами.
Сортамент стали, В зависимости от методов обработки сортамент строи
тельных сталей можно |
разделить на три группы: I — горячего проката, |
II — холодной вытяжки, |
III — комбинированной обработки. |
Сортамент стали горячего проката (рис. 14.5) получил широкое распрост ранение в производстве строительных работ. Сортамент сталей холодной вы тяжки состоит из высокопрочных холоднотянутых проволок круглого и перио дического сечения. К сортаменту стали комбинированной обработки отно сятся гнутые профили (рис. 14.6) и сталь периодического профиля.
Применение стали. Стали низколегированные и углеродистые обыкновен ного качества являются основными материалами для изготовления несущих металлических конструкций: мостовых ферм, ферм для перекрытия цехов, опор электропередач, арматурных каркасов в железобетонных конструкци ях и т. д. При выборе стали для изготовления конструкций и деталей необхо димо вначале ознакомиться с ее механическими свойствами и химическим Составом, которые определяют прочность и свариваемость стали, а также
Рис. 14.5. Основной сортамент стальных профилей:
/ — круглая сталь; 2 — квадратная; 3 — полосовая; 4 — шинная; 5 — равнобокий уголок; 6 — неравнобокий уголок;
7 зетовый профиль; 8.9 — тавровые; 10 — двутавровый; |
11 — швеллер; 12 — рельс; 13 — колонный; 14 — корытный; |
15 ~ оконный; |
16 — шпунтовый |
Рис. 14.6. Основной сортамент гнутого профиля:
6. () для несущих конструкций; |
оконные; с - для поручней; з — для резервуаров; ж. |
м — для |
|
металлической оснастки |
|
учесть ее физические и химические свойства, от которых зависит возмож ность использования данной стали в определенных средах.
Марку стали выбирают с учетом условий работы конструкции или детали: для несущих конструкций применяют стали марок СтЗ, Ст4, Ст5, 25ГС, кото рые имеют достаточно высокий предел текучести и прочности, хорошую свари ваемость: для мостостроения, изготовления резервуаров и трубопроводов применяют малоуглеродистую сталь марок СтЗ, Ст2кп, СтЗкп, которые мало
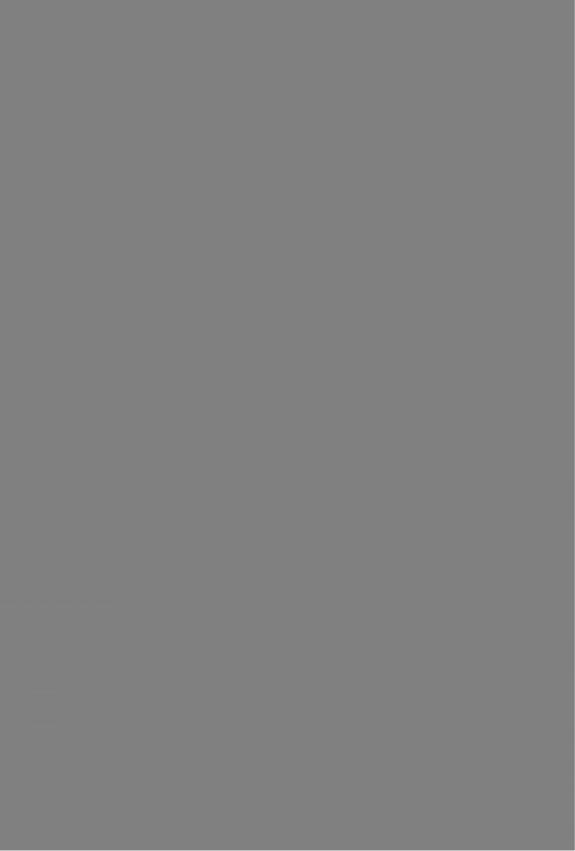
Зуборезные станки предназначены для обработки зубчатых колес. При этом инструмент совершает одновременно вращательное и поступатель ное движение, а деталь — только вращательное.
Протяжные станки срезают с обрабатываемой поверхности стружку с по мощью многолезвенного режущего инструмента — протяжки. Главное прямолинейное движение сообщается инструменту (рис. 14.7, е).
Автоматические линии позволяют как бы соединить ряд отдельных стан ков и силовых головок в единое целое с широким использованием различных транспортирующих устройств. В автоматических линиях станки располагают ся в строгой последовательности в соответствии с технологическим процес сом и заготовка автоматически передается от операции к операции.
При обработке металлов резанием необходимо обращать особое внимание на технику безопасности. Основными причинами травматизма при холодной обработке металлов являются: движущиеся механизмы станка, отходящая стружка, обрабатываемая деталь, режущий инструмент, токоведущие части электроустановок и плохая организация рабочего места.
§ 14.9. СВАРКА И РЕЗКА МЕТАЛЛОВ
Сварка — процесс получения неразъемного соединения с местным нагре вом или без него при использовании сил молекулярного сцепления. Примене ние сварки дает экономию металла. Она намного экономичнее клепки, литья. Сварка широко применяется в промышленности и строительстве. С примене нием сварки изготавливают: металлические конструкции, арматурные карка сы, металлические резервуары, мостовые фермы и другие изделия.
При сварке различают следующие виды соединений: стыковые, внахлест ку, угловые и тавровые (рис. 14.8). Стыковые соединения образуются свар кой торцовых поверхностей, кромки которых подготавливают в зависимости от толщины свариваемого металла. Соединения внахлестку производят угло выми швами. Величина нахлестки берется равной трех-, пятикратной толщи не свариваемых элементов. Угловые и тавровые соединения выполняются путем приварки одного элемента изделия к другому под углом 90°
В зависимости от состояния металла в момент сварки различают два основных ее вида: сварка давлением, когда металл доводят до пластичного состояния; сварка плавлением, при которой металл нагревают выше темпе ратуры плавления, после чего сваривают без применения механического воздействия.
Структура сварного соединения. Высокий местный нагрев при сварке вызывает значительное изменение в структуре металла. При сварке углеро дистых сталей металл в зоне термического воздействия нагревается до темпе ратур выше критических, т. е. переходит в аустенитную структуру, так что в процессе последующего охлаждения в этой зоне происходит перекристал лизация с образованием новых структур, соответствующих скорости охлаж дения.
В зависимости от температуры нагрева вся зона термического воздействия разделяется на шесть участков:
1)неполного расплавления металла — узкая полоска, по которой прохо дит граница между наплавленным и основным металлом. При дуговой сварке этот участок резко выделяется в виде тонкой линии на макрошлифе. При га зовой сварке линия сплавления на макрошлифе расплывчата;
2)перегрева. Здесь наблюдается крупнозернистая структура*. При дуго вой сварке участок перегрева занимает небольшую часть всей зоны влияния. При газовой сварке этот участок является преобладающим;
3)нормализации. На этом участке при обычных условиях сварки образу ется мелкозернистая структура. При дуговой сварке участок нормализации является преобладающим, при газо вой — слабо выраженным вследствие значительно большего объема нагре ваемого металла;
4)неполной перекристаллизации.
Структура получает промежуточный характер. Наряду с крупными зернами
имеются мелкие, прошедшие превра щения;
5) рекристаллизации. Нагрев до 400—700°С, структура подобна основ ному металлу.
Чем меньше околошовная зона тер мического воздействия, тем выше свойства сварного шва. Зона терми ческого воздействия зависит от вида
сварки: при механической и электронно-лучевой сварке она наименьшая, при электросварке она меньше, чем при газовой.
В зависимости от источника нагрева различают электрическую, хими ческую, механическую сварки. Это деление является в известной мере услов ным.
Электрическая сварка. Эта сварка основана на использовании тепла, выделяемого при прохождении электрического тока. Электрическая сварка подразделяется на сварку сопротивления (или контактную), при которой электрический ток выделяет тепло за счет омического сопротивления (в кон тактах свариваемых деталей), и электродуговую, т. е. с использованием при сварке тепла, выделяемого электрической дугой.
Источником тепла при электродуговой сварке является электрическая ду га, открытая в 1902 г. проф. В. В. Петровым. При этом температура, разви вающаяся в центре столба дуги, достигает 6000°С.
Практическое применение электрической дуги для сварки металлов было осуществлено русскими инженерами Н. Н. Бенардосом и Н. Г Славяновым. По способу Бенардоса электрическая дуга возбуждается в атмосфере между угольным электродом и свариваемой деталью (рис. 14.9, а). При этом способе пользуются постоянным током. Положительный полюс присоединяют к свари ваемому изделию, отрицательный — к угольному электроду. Присадочный материал вводят отдельно. Этот способ сварки широко применяется при свар ке цветных металлов. Способ Славянова — основной вид сварки, применяе мый для соединения элементов металлических строительных конструкций
(рис. 14.9, б).
При контакте изделия и электрода между ними возникает электрическая дуга температурой выше 5000°С. При этой температуре металл электрода пе реходит в мелкокапельное жидкое состояние и переносится на свариваемое изделие. Металл изделия также расплавляется на некоторую глубину, кото рая называется глубиной провара, образуя с наплавленным металлом одно родный сплав, в результате чего соединение приобретает высокую прочность. Несмотря на большую распространенность, электродуговая сварка имеет ряд существенных недостатков. К ним относятся: малая скорость сварки за счет большой зоны разогрева металла, что, в свою очередь, вызывает коробление изделия; пористость шва и выгорание легирующих компонентов из сплавов
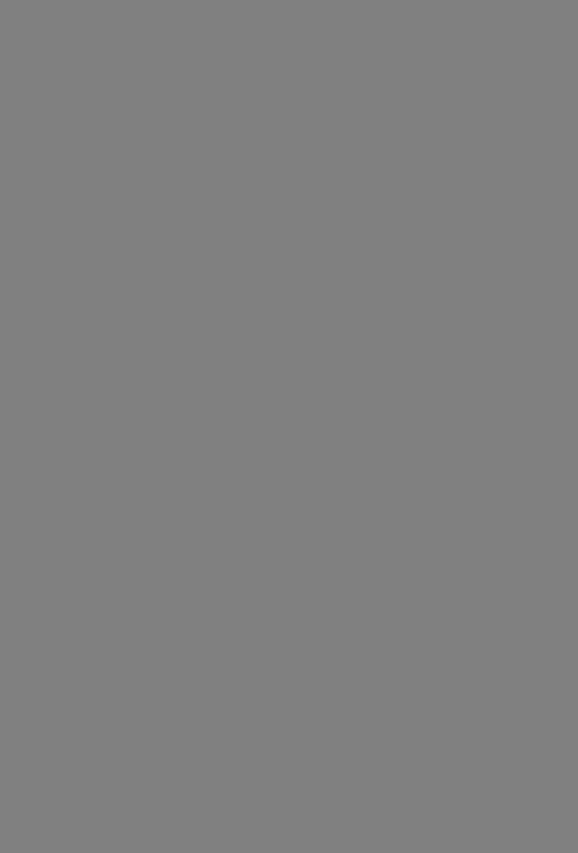
благоприятные условия для получения высококачественного, однородного по структуре наплавленного металла, а с другой — значительная экономия тепла дуги.
При сварке под флюсом на плавление металла электрода и основного ме талла расходуется 68% всего тепла дуги, а при обычной сварке — только 25%. Поскольку дуга невидима, создаются благоприятные условия для работы сварщика и для обеспечения ровности накладываемого с боль шой скоростью шва. Этот метод сварки применяется при монтаже металли ческих конструкций и для устройства стальных пролетных строений мостов.
При дуговой сварке под водой применяют электроды с более толстой (до 1 мм) и водонепроницаемой обмазкой, устраняющей электролиз. Сила тока при этом требуется несколько большая, чем при сварке на воздухе. При применении постоянного тока получаются лучшие результаты.
При контактной сварке, или сварке методом сопротивления, электри ческий ток подводится к двум свариваемым изделиям. При их контакте ис пользуется выделяющееся тепло, которое размягчает металл, и при сближе нии под нагрузкой они свариваются. Изменяя силу тока и время его прохож дения через свариваемое изделие, можно регулировать количество выделяе мого тепла. В 'настоящее-время применяются три вида контактной сварки:
точечная сварка служит для соединения внахлестку арматурных сеток и каркасов. Суммарная толщина металла обычно не превышает 20 мм. Свариваемая арматура или листы укладываются внахлестку или соединяют ся при помощи накладки и зажимаются между двумя медными электродами. При включении тока часть металла, находящегося между электродами, на гревается до сварочной температуры и затем быстро и сильно сдавливается электродами.
В настоящее время для точечной сварки применяются различные высоко производительные сварочные машины;
роликовой сваркой соединяют главным образом листовой металл с целью получения не только прочного, но и плотного герметичного соединения. В отличие от точечной сварки в ней стержневые электроды заменены вращаю щимися роликами, которые захватывают свариваемые листы и создают непрерывный шов. При прохождении тока металл под роликами нагревается и сваривается под влиянием давления роликов. Максимальная суммарная толщина свариваемых листов составляет 6 мм. Роликовая сварка находит применение при массовом изготовлении деталей, требующих прочного и плот ной соединения;
стыковая сварка используется для металлических стержней (арматуры) и выполняется по методам сопротивления и оплавления.
При сварке по методу сопротивления торцы свариваемых стержней зажи мают в держателях электросварочной машины, прижимают друг к другу, затем включают электрический ток, кот'орый разогревает металл в месте кон такта и в прилегающих участках до сварочной температуры. В месте сварки образуется утолщение, которое усиливает соединение стержней.
При сварке методом оплавления концы стержней закрепляют в электрод ных зажимах и включают ток, затем концы стержней сводят до соприкосно вения и снова разводят для образования между ними искрения, которое вызы вает оплавление стыка по всему сечению. После оплавления торцов ток вы ключают и сваривают под давлением, приложенным по оси стержней.
Химическая сварка. Эта сварка производится за счет тепла химических реакций и делится на газовую и термитную.
Газовая сварка. При газовой сварке тепловым источником служит тепло продуктов сгорания смеси кислорода с горючим газом или жидким распылен ным топливом. В настоящее время применяются следующие горючие газы:
ацетилен, водород, нефтегаз, природный газ, газ горючих жидкостей, а также пары бензина, бензола, керосина и др.
Ацетилено-кислородная сварка наиболее экономична и эффективна из всех видов газовой сварки. Ацетилен С2Н2 — бесцветный газ с плотностью 0,906, который получают путем воздействия воды на карбид кальция CaC2-f + 2Н20-^С2Н2 + Са (ОН)2. При давлении 17,5 МПа и выше ацетилен взрыво опасен.
Карбид кальция активно соединяется с водой и разлагается даже от действия паров воды, находящихся в воздухе, поэтому его транспортируют в герметически закрытых железных барабанах.
Ацетилен получают в газогенераторах,- различающихся по величине рабо чего давления на газогенераторы низкого, среднего и высокого давления. Процесс полного сгорания ацетилена в кислороде следующий: 2С2Н2 + 502->- ->4Ср2 + 2Н20. При сварке ацетилен и кислород подают по объему в отно шении 1: (0,9—1,6). В зависимости от вида пламени недостающее количество кислорода (около 1,4 части по объему) для полного сгорания не подается из баллона, а поглощается из воздуха.
При полном сгорании ацетилена в кислороде образуется пламя из трех зон, называемое нейтральным. Наивысшая температура (около 3200°С) находится во второй зоне на расстоянии 3—7 мм от конца ядра пламени. Этим участком пламени обычно и производится сварка.
Металлы свариваются приборами — сварочными горелками,* в которых ацетилен смешивается с кислородом (рис. 14.10). Ацетилен сгорает у выхода из горелки.
Процесс сварки осуществляется направлением присадочного металла на оплавленной ацетилено-кислородным пламенем шов. Присадочным мате-
Рис. 14.10. Схема газовой сварки металла и сварочной горелки:
. |
а |
- схема сварки; 6 — горелка; |
|
||
присадочным |
материал; 2 — свариваемый |
металл; 3 |
наплавленный |
металл; 4 — корпус горелки; 5, 6 — шланги |
|
|
ацетилена и кислорода; 7 — ацетиленовый генератор; |
8 |
баллон с кислородом |
риалом при газовой сварке служит чистая стальная проволока диаметром от 2 до 8 мм с содержанием углерода от 0,15 до 1,5% в зависимости от состава свариваемого металла. Для уменьшения степени окисления шва во время сварки применяются флюсы (бура и борная кислота).
Газовую сварку обычно применяют для изделий толщиной не более 30 мм. При большей толщине свариваемого изделия целесообразно применять электродуговую сварку. Для массовой сварки деталей сравнительно простых форм (стальных, катков, баков, паровых и водяных радиаторов, глушителей), допускающих применение шаблонов, широко используют различные свароч ные машины-автоматы.
Для сварки стыков стальных трубопроводов диаметром от 50 до 600 мм в последние/оды получила широкое распространение газопрессовая сварка, при которой металл нагревают ацетилено-кислородным пламенем при помо щи специальной горелки до перехода его в пластичное состояние или до оплавления и сваривают приложением давления.
Термитная сварка использует тепло химической реакции смеси алюминие вого порошка (22%) и чистой железной руды или окалины (78%). При горе
нии термита протекает |
экзотермическая |
реакция |
2А1+ Fe20 3->-2Fe + |
+ A120 3+Q. Температура |
достигает 3000°С. |
Концы |
деталей свариваются |
с заполнением зазора восстановленным железом. Термитную сварку приме няют для сварки труб, рельсов, при ремонтных работах.
Свариваемость сталей и дефекты сварного шва. Свариваемость металлов при одном и том же виде сварки зависит от ряда факторов, главными из кото рых являются химический состав и свойства свариваемых металлов и приме няемых электродов, режим сварки, термическая обработка до и после сварки.
Окисление отдельных элементов (например, углерода) может дать газо образные продукты и вызвать пористость шва. Кроме того, содержание угле рода влияет на закаливаемость стали в зоне термического воздействия свар ки. При содержании углерода до 0,25% стали свариваются хорошо, при боль шем его содержании в процессе охлаждения формируются структуры зака лочного типа. В связи с этим для предотвращения образования трещин реко мендуется предварительный и сопутствующий подогрев. Другие элементы, содержащиеся в стали, например кремний, алюминий, могут образовывать тугоплавкие окислы, которые в наплавленном металле остаются в виде неме таллических включений и снижают качество сварки.
Основными дефектами свариваемых швов являются: непровар вследствие неправильного режима сварки; пористость из-за насыщения металла газами; трещины в наплавленном и основном металле из-за появления внутренних напряжений в процессе сварки (они возникают при неправильном ведении сварки, большом количестве наплавленного металла и др..); пережог вслед-4 ствие окисления при слишком большой длине дуги (при дуговой сварке) или при избытке кислорода (при газовой сварке).
Контроль сварки. Возникающие дефекты сварки должны быть обнаруже ны и устранены. Выбор способа контроля сварных швов определяется харак тером конструкции и ее ответственностью.
Контроль сварных швов ведут в следующем порядке:
внешний осмотр — выявление тех дефектов, которые можно обнаружить путем осмотра (с лупой) и обмера. Такое освидетельствование обязательно для всех типов свариваемых соединений строительных конструкций;
испытание на прочность с помощью специальных приборов и датчиков, устанавливаемых на деталях конструкций, по которым определяются напря жения и деформации (прогибы);
испытание на плотность гидравлическим испытанием или керосиновой пробой;
определение скрытых дефектов ультразвуковым методом, электромагнит ным исследованием, просвечиванием лучами Рентгена;
определение структуры сварного шва с помощью металлографического
анализа.
Резка металла. В строительстве широко применяется газовая резка метал ла, которая заключается в нагревании металла до температуры воспламене ния в среде кислорода, сжигании его и выдувании образовавшихся окислов струей кислорода. Температура горения железоуглеродистых сплавов с со держанием углерода до 0,7% ниже температуры их плавления, и они хорошо поддаются резке, а с повышением содержания .углерода (более 0,7%) темпе ратура горения сплава приближается к температуре плавления, и они плохо поддаются резке. Для резки высоколегированных сталей и чугунов применя ют флюсо-кислородную резку.
Газовую резку ведут на обычном газосварочном оборудовании, только сварочную горелку заменяют режущей, подающей газовую смесь для подо грева и кислород для сжигания металла. В качестве горючего газа чаще всего применяют ацетилен, но могут быть использованы и другие газы, а так же пары бензина или керосина.
Газовую резку можно выполнять вручную и при помощи специальных машин — полуавтоматов и автоматов. В полуавтоматах резка возможна только в определенном направлении, а в автоматах режущая горелка имеет движение по любому контуру. В СССР для автоматической резки изготавли вают автоскопы, которыми можно резать по шаблону и по чертежу.
Техника безопасности при сварке и резке металла. Основными опасностя ми при электродуговой и газовой сварке и резке металла являются: пораже ние током, ожог дугой, расплавленным металлом или факелом, повреждение зрения излучением сварочной дуги или пламенем горелки, загрязнение возду ха вредными парами, газами и пылью.
Для предупреждения поражения работающих электрическим током про вода для подключения сварочных аппаратов к сети должны быть изолирова ны, заключены в резиновые трубки и не иметь механических повреждений, а кожухи сварочных аппаратов — надежно заземлены.
При ручной сварке конструкция рукоятки электродержателя должна поз волять смену электродов при снятом напряжении. Она выполняется из огне стойкого, малотеплопроводного и диэлектрического материала. При работе
в сложных условиях, когда возникает опасность прикосновения сварщика
жзаземленным конструкциям, необходимо производить работы в резиновых
перчатках, ботах или на коврике, в шлемах, с налокотниками и наколенника ми.
Для предупреждения ожогов и повреждения зрения рабочие, производя щие горячую резку и сварку металлов, должны быть одеты в брезентовую спецодежду и рукавицы, а также снабжены светозащитными очками и щитка
ми со светофильтрами. Рабочее Место сварщиков ограждается шторами или щитками.
Работая с газовыми аппаратами, необходимо перед началом работы про верить исправность ацетиленовых аппаратов, пригодность к эксплуатации шлангов и горелок. Ацетиленовые генераторы должны быть установлены
в отдельных изолированных помещениях несгораемого или трудносгораемого здания.
В связи с образованием при сварке вредных паров, газов и пыли следует обеспечивать проветривание зоны, где происходят работы по резке и сварке металла. При резке металлов, окрашенных свинцовыми красками, сварщики
должны работать в особых шлемах или масках с подачей воздуха для дыха ния.
Коррозией называется процесс разрушения металла вследствие физико химического влияния на него внешней среды. Коррозия наносит большой ущерб народному хозяйству; O K O J I O 10— 1 2 % ежегодно производимого чер ного металла теряется от коррозии.. Разрушение металлов и сплавов от коррозии в основном зависит от природы металла, его химического сос тава, содержания агрессивных веществ в окружающей среде и температу ры. Коррозия делится на химическую и электрохимическую.
Химическая коррозия — это разрушение металлов от воздействия на них сухих газов или неэлектролитов (бензина, масел и др.). Примером хими ческой коррозии является окисление металлов при высоких температурах. Во время химической коррозии на поверхности металла появляется плен ка окислов, которая в большинстве случаев является защитной. Защит ная пленка предохраняет от коррозии лежащий под ней металл. Такие пас сивные к окружающей среде пленки образуются на поверхности алюми ния, свинца, олова, никеля, хрома.
Электрохимическая коррозия — разрушение металлов и сплавов под воз действием электролитов. Электролитами могут быть растворы солей, кис лот, природные воды, влажный воздух.
Металлические конструкции, работающие на воздухе, покрываются тон кой пленкой влаги с растворенными в ней различными веществами (в за висимости от характера производственной среды) , в результате чего на по верхности металла образуется пленка электролита. На ^зделия, находя щиеся в почве (трубы, кабели, конструкции оснований и фундаментов), так же действуют растворы солей, кислот, щелочей. Электрохимический вид кор-, розии является наиболее распространенным.
Ввиду неоднородности структуры сплавов, разности состояний по его зернам и границам в присутствии электролита между этими разнородными участками образуются как бы микроэлементы, а в каждом из них — свой анод й катод. Таким образом, при соприкосновении металлических крис таллов с раствором электролита ион металла покидает решетку метал лического кристалла и переходит в раствор. В результате металл оказыва ется заряженным отрицательно, а раствор — положительно, так как в нем получается избыток катионов.
Разрядка происходит путем перемещения свободного электрона к тем местам, где имеются катионы электролита (например, ионы водорода, полу чающиеся от диссоциации водного раствора электролита). В результате взаимодействия электрона с ионом водорода появляются нейтральные ато мы водорода.
Весь процесс выражается уравнением: металл + ион водорода = ион металла + атом водорода. Практически это равновесное состояние в силу ряда причин наступить не может и процесс растворения металла будет происходить до полного его разрушения.
Стремление атомов данного металла перейти в ионную форму и раст вориться в жидком электролите определяется величиной электрохимичес кого потенциала. Эти свойства металла называются упругостью растворе ния. Каждый металл обладает присущей ему упругостью растворения. Та ким образом, по величине потенциала данного металла в данном электро лите можно определить, будет ли этот металл корродировать или нет.
Чем отрицательнее нормальный электрохимический потенциал, тем бо лее резко выражено стремление металла к растворению в электролитах. Так, например, олово будет растворяться в растворе серной кислоты быст рее, чем железо, а цИнк наооборот.
Защитное действие всегда оказывает более активный металл. Цинк, как более активный, должен защищать железо, олово — усиливать его корро
зию.
Действие оловянного покрова (лужение изделия для предохранения его от коррозии) чисто механическое, и достаточно в одном месте нарушить цельность оловянного покрова, как железо начнет усиленно корродировать вследствие образования гальванической пары олово — железо. Иначе об стоит дело с цинковым покровом: до тех пор, пока не растворится весь
цинк, железо не корродирует.
Защита металла от коррозии. В настоящее время применяются сле дующие способы защиты металлов от коррозии.
Защита легированием, т. е. введением в металл легирующих элемен тов, повышающих сопротивление сплава коррозии, например введением никеля и хрома в нержавеющие кислотоупорные стали, меди — в строи
тельные стали.
Существует много разновидностей стали с различным содержанием Сг и Ni, Мо и Си, а также Ti, обладающих повышенной стойкостью в агрес сивных средах.
Защита оксидными пленками — оксидирование и фосфатирование, ко торые производятся путем кипячения изделий в специальных составах (се литры, едкого натра и перекиси марганца или фосфорной кислоты и ее же лезных и марганцевых солей). Образующиеся пленки темного цвета обла дают хорошей коррозионной устойчивостью.
Защита металла покрытием пленкой из другого металла имеет следую щие разновидности: катодное покрытие, т. е. покрытие металлом, который является более электроположительным (менее активным), чем основной металл изделия (в этом случае пленка является только механической защи той); анодное покрытие, т. е. покрытие основного металла металлом с более отрицательным электродным потенциалом. В этом случае пленка является электрохимической защитой.
По методу нанесения металлической пленки различают: горячее покры тие, т. е. покрытие, наносимое путем погружения детали в ванну с рас плавленным металлом (цинк, олово, свинец); гальваническое покрытие, по лученное путем электролитического осаждения на поверхности основного металла (катода) его солей из водного раствора (анода); металлизация — нанесение путем разбрызгивания слоя расплавленного металла под дав лением сжатого воздуха.
Покрытие металлических изделий слоем лака или краски имеет целью изолировать основной металл от окружающей его влажной среды. Этот метод самый простой и распространенный, широко применяется для защиты всех строительных конструкций и деталей (ферм, колонн, листов и т. д.).
При изготовлении железобетонных конструкций в зависимости от вида бетона и вяжущего необходимо предусматривать определенные меры за щиты арматуры и закладных деталей от коррозии. Гипсовые и другие серо содержащие вяжущие вызывают коррозию арматуры и практически для из готовления железобетонных изделий не применяются. Для характеристики агрессивности сред, подобных бетонным, принято определять концентра цию водородных ионов, т. е. pH. В кислых средах с pH менее 4,3 коррозия идет очень быстро. В слабокислых и слабоосновных средах с pH от 4,3 до 10 скорость коррозии меньше и почти не зависит от pH. В щелочных растворах с pH больше 10 коррозия протекает медленно и зависит от pH. Так, коррозия при pH = 12 в 2 раза меньше, чем при pH = 10.
Проведенные многочисленные исследования показывают, что pH поровой жидкости портландцемента 11,25—11,8, шлакопортландцемента 10,4—
10,8. Таким образом, pH паровой жидкости портландцемента не вызывает коррозии, и плотный бетон является хорошей защитой арматуры от кор розии. Однако арматура в Легких и пористых бетонах при работе во влаж ных и агрессивных средах/требует антикоррозионной защиты.
Для защиты арматурьв от коррозии ее покрывают защитными пленка ми: цементно-казеиновыми обмазками, жидким стеклом, керамическими эмалями. Для защиты более ответственных элементов, закладных деталей применяют цинкование. И органическим защитным пленкам относятся би тумные, битумоцементныё и другие покрытия на основе искусственных по лимеров, смол, латексов /например, цементно-поливинил-ацетатная, цемент- но-полистирольная и др.1. Основными методами нанесения антикоррозион ного покрытие являются/окунание, полив, обрызгивание. В последнее время предложен метод окражи в электрическом поле, в котором частицы по крытия ионизируются и притягиваются к осадительному электроду — ар матуре.
.Наиболее широкое/применение для, защиты металлов от коррозии по лучили методы нанесения полимерных пленок. В США около 25% всех
выпускаемых |
синтетических смол |
и пленок идут |
на защитные покрытия. |
В ФРГ около |
15% всего проката |
выпускаются с |
защитными покрытиями. |
В качестве покрытия йа малоуглеродистой стали чаще всего применяется по ливинилхлоридная пленка, а также полиэтилен, полиамиды и другие пласт массы. Получаемый/новый конструкционный материал — металлопласт — обладает комплексом свойств, присущих металлу и пластмассам, и легко поддается механической обработке. Металлопласт примерно в 6 раз дешев ле и значительно долговечнее нержавеющей стали. Этот метод защиты ме талла от коррозии является прогрессивным и в дальнейшем должен полу чить самое широкое распространение.
В последние годы в соответствии с разработками Института химии сили катов АН СССР для защиты от коррозии металлоконструкций, работа ющих в агрессивных средах, применяются органосиликатные краски. Опыт их применения показывает высокую эффективность таких покрытий.
Б а ж е н о в Ю. М. Технология бетона. |
М., Стройиздат, 1978. 380 с. |
|
|
|
1974. |
||||||||
В о л к о в |
М. И. Методы испытания |
строительных материалов. М., Стройиздат, |
|||||||||||
304 с. |
|
|
Г. И. Строительные материалы. М., |
\ |
1981. 412 с. |
|
|
||||||
Г о р ч а к о в |
Высшащ школа, |
растяже |
|||||||||||
Г р у ш к о |
И. М., И л ь и н |
А. Г., Р а ш е в с к и й |
С. Т. Прочность |
бетона |
на |
||||||||
ние. Харьков, ХГУ, 1973. 160 с. |
|
|
|
\ |
|
|
Под ред. |
||||||
Дорожные пластбетоны. /Г. К. Сюньи, В. Д. Ставицкий, В. Н. Ковалевич и др.; |
|||||||||||||
Г К. Сюньи. М., Транспорт, |
1976. 208 с. |
|
|
; |
|
|
|
|
|||||
Дорожный асфальтобетон /Н. Н. Иванов, Л. Б. Гезейцвей, ИЗ В. Королев и др.; Под ред. |
|||||||||||||
Л. Б. Гезенцвея. М., Транспорт, 1976. 336 с. |
асфальтобетонбв. Харьков, Вища'школа, |
||||||||||||
З о л о т а р е в |
В. А. Долговечность дорожных |
||||||||||||
1977. 115 с. |
|
|
|
А. |
С., |
М и х а й л о в В. |
В. |
Дорожные битумы. М., |
|
|
1 |
||
К о л б а н о в с к а я |
Транспорт, |
||||||||||||
1973. 261 с. |
|
И. В. Дорожный теплый |
асфальтобетон. Киев, Вища |
школа, |
1975. |
156 с. |
|||||||
К о р о л е в |
|||||||||||||
К у ч м а |
М. И. Поверхностно-активные вещества |
в дорожном строительстве. М., |
Тран |
||||||||||
спорт, 1980. |
189 с. |
|
|
|
О. П. Химия неорганических строительных материалов. М., |
||||||||
М ч е д л о в - П е т р о с я н |
|||||||||||||
Стройиздат, |
1971. |
224 с. |
|
|
|
|
|
|
|
1981. |
303 с. |
||
П о п ч е н к о |
С. Н. Гидроизоляция сооружений и зданий. Л., Стройиздат, |
||||||||||||
Р у д е н с к и й |
А. |
В., Р у д е нс к а я |
И. М. Реологические свойства битумоминераль |
||||||||||
ных материалов. М., Высшая |
школа, 1971. |
132 с. |
|
|
|
|
|
|
С и д е н к о В. М., Г р у ш к о И. М. Основы научных исследований. Харьков, Вища школа, 1979. 200 с.
Строительство автомобильных дорог. /Н. Н. Иванов, В. К. Некрасов, С. М. Полосин-
Никитин и |
др.; Под |
ред. В. |
К. Некрасова. 2-е |
изд., перераб. |
и доп. М., Транспорт, |
1980. |
||||
416 с. |
Н. Б. Высококонцентрированные дисперсные |
системы. М., |
Химия, |
1980. |
320 |
с. |
||||
У р ь е в |
||||||||||
Ш е с т о п е р о в |
С. В. |
Контроль качества |
бетона. |
М., |
Высшая |
школа, |
1981. |
247 |
с. |
Введение |
|
|
|
|
|
|
|
|
|
|
|
|
|
|
|
|
3 |
|
Г л а в а |
1. |
Состав, |
|
структура |
и |
основные |
свойства |
дорожно-строительных |
|
|||||||||
материалов |
|
|
|
|
I. |
|
|
|
|
|
|
|
|
|
5 |
|||
§ 1.1. |
Свойства дорожнсжтроительных материалов |
|
|
5 |
||||||||||||||
§ |
1.2. |
Структура |
|
материала |
|
|
|
|
|
|
|
|
15 |
|||||
§ 1.3. Классификация |
J основные технологические принципы получения строи |
19 |
||||||||||||||||
|
|
тельных |
материков |
с |
заданными |
свойствами |
|
|||||||||||
§ 1.4. Оценка |
качества строительных |
материалов |
|
|
27 |
|||||||||||||
Г л а в а |
2. |
Природные |
шменные |
материалы |
|
|
|
30 |
||||||||||
§ |
2.1. |
Общие |
сведет* |
|
|
|
|
|
|
|
|
|
|
30 |
||||
§ 2.2. |
Горные породы!как сырье для производства каменных материалов |
30 |
||||||||||||||||
§ |
2.3. |
Породообразующие |
минералы |
|
|
|
|
|
35 |
|||||||||
§ 2.4. |
Техническая жрактеристика главнейших скальных и обломочных горных |
37 |
||||||||||||||||
|
|
пород |
|
|
.1 |
|
|
|
|
горных |
пород и определение их качества |
|||||||
§ 2.5. Обследование^месторождений |
51 |
|||||||||||||||||
§ |
2.6. Разработка |
месторождений |
и |
переработка |
горной |
породы |
55 |
|||||||||||
§ |
2.7. Предохранение |
каменных |
материаловот коррозии |
|
63 |
|||||||||||||
§ 2.8. Приемка каменных материалов |
|
|
|
|
|
64 |
||||||||||||
Г л а в а |
3. Искусственные каменные обжиговые материалы и изделия |
65 |
||||||||||||||||
§ |
3.1. |
Керамические |
материалы |
и |
изделия |
|
|
|
65 |
|||||||||
§ |
3.2. Сырьевые |
|
(Материалы |
|
|
изделий |
|
|
|
65 |
||||||||
§ 3.3. |
Производство |
керамических |
|
|
. |
69 |
||||||||||||
§ |
3.4. Стеновые |
керамические |
материалы |
|
изделия |
73 |
||||||||||||
§ 3.5. Клинкерный |
кирпич |
и |
|
другие |
плотные |
грубой строительной |
75 |
|||||||||||
|
|
керамики |
|
|
|
|
|
|
|
|
|
|
|
|
|
|||
§ |
3.6. Искусственные |
заполнители на основеглинистого сырья |
77 |
|||||||||||||||
§ |
3.7. |
Шлаковые |
|
строительные |
материалы |
|
|
|
80 |
|||||||||
§ |
3.8. |
Камнелитные |
изделия |
|
|
|
|
|
|
|
|
88 |
||||||
§ 3.9. |
Материалы и изделия из стекла |
|
|
|
|
88 |
||||||||||||
Г л а в а |
4. |
Минеральные |
вяжущие |
материалы |
|
|
|
91 |
||||||||||
§ |
4.1. Характеристика минеральных вяжущих материалов |
|
91 |
|||||||||||||||
§ |
4.2. |
Воздушная |
известь |
|
|
|
|
|
|
|
|
|
91 |
|||||
§ 4.3. |
Гипсовые |
вяжущие |
материалы |
|
|
|
|
95 |
||||||||||
§ 4.4. |
Магнезиальные |
вяжущие |
материалы |
|
|
|
97 |
|||||||||||
§ |
4.5. |
Растворимое |
стекло |
|
|
ироманцемент |
|
|
97 |
|||||||||
§ |
4.6.Гидравлическая |
известь |
|
|
|
98 |
||||||||||||
§ |
4.7.Портландцемент |
|
|
|
|
его |
применение |
|
|
99 |
||||||||
§ 4.8. Свойства портландцемента и |
|
|
108 |
|||||||||||||||
§ 4.9. Особые виды портландцемента |
|
|
|
|
ПО |
|||||||||||||
§ |
4.10. Пуццолановые |
портландцементы |
|
, |
|
|
112 |
|||||||||||
§ 4.11. Шлаковые |
цементы |
|
|
|
|
|
|
|
|
114 |
||||||||
§ |
4.12. Глиноземистые |
(алюминатные) |
цементы |
|
|
116 |
||||||||||||
Г л а в а 5. Искусственные материалы на основе минеральных вяжущих и мелкозернистых |
119 |
|||||||||||||||||
заполнителей |
|
|
материалы |
|
|
|
|
|
|
|
|
|||||||
§ |
5.1. Силикатные |
|
|
|
|
|
|
|
|
119 |
||||||||
§ |
5.2.Гипсовые и гипсобетонные изделия |
|
|
|
122 |
|||||||||||||
§ |
5.3.Асбоцементные |
изделия |
|
|
|
|
|
|
|
|
122 |
|||||||
§ |
5.4.Магнезиальные |
материалы |
|
|
|
|
|
|
123 |
|||||||||
§ |
5.5.Строительные |
растворы |
|
|
|
|
|
|
|
|
123 |
|||||||
Г л а в а |
6. |
Бетоны |
|
(цементобетоны) |
|
|
|
требования и классификация |
130 |
|||||||||
§ 6.1. Определение, |
основные |
технические |
130 |
§ 6.2. Свойства бетонных смесей |
|
|
|
|
|
|
|
|
132 |
|||||||||||||
§ |
6.3. Обычный |
(тяжелый) |
бетон |
|
|
|
|
|
|
|
135 |
|||||||||||
§ |
6:4. Материалы |
для |
бетона |
|
|
|
|
|
|
|
|
|
1 4 4 |
|||||||||
§ |
6.5. Технология |
бетонных |
работ |
|
|
|
|
|
|
|
149 |
|||||||||||
§ 6.6. Особенности |
бетонных работ при низких температурах воздуха |
|
156 |
|||||||||||||||||||
§ |
6.7. Дорожный |
цементобетон |
|
|
|
|
|
|
|
|
158 |
|||||||||||
§ 6.8. Специальные виды тяжелых бетонов |
|
|
|
|
|
|
161 |
|||||||||||||||
§ 6.9. |
|
Легкие |
бетоны |
|
|
|
|
|
|
|
|
|
|
|
|
|
|
162 |
||||
Г л а в а |
7. Сборные бетонные и железобетонные изделия |
|
|
|
|
165 |
||||||||||||||||
§ 7.1. Общие сведения о |
железобетоне. Классификация, изделий |
|
|
165 |
||||||||||||||||||
§ 7.2. Технологические схемы производства железобетонных изделий |
|
166 |
||||||||||||||||||||
§ 7.3. Особенности |
технологии производства сборных ' *°тонных ц железобе |
167 |
||||||||||||||||||||
§ 7.4. |
|
тонных |
изделий |
|
|
|
|
|
|
|
|
|
|
|
|
|
||||||
|
Твердение железобетонных изделий |
|
|
|
|
|
|
|
173 |
|||||||||||||
§ 7.5. |
|
Оптимизация технологии и управление качеством изделий |
|
|
179 |
|||||||||||||||||
Г л а в а |
8. Материалы и изделия из пластмасс |
|
|
|
|
|
185 |
|||||||||||||||
§ 8.1. |
|
Характеристика |
пластмасс |
|
|
|
|
|
|
|
|
185 |
||||||||||
§ *8.2. Строение |
и |
свойства |
высокомолекулярных |
соединенйй |
(полимеров) |
185 |
||||||||||||||||
§ |
8.3. Наполнители и |
другие |
компоненты |
|
|
|
[ |
|
|
|
1 9 4 |
|||||||||||
§ 8.4. Основные свойства материалов и изделий из пластмасс |
|
|
|
195 |
||||||||||||||||||
§8.5. |
|
Полимерцементобетон |
|
|
|
|
|
|
|
|
|
|
|
1 9 6 |
||||||||
§ 8.6. |
|
Пластбетоны |
|
|
. |
|
|
|
|
|
|
|
|
|
|
198 |
||||||
§ 8.7. Стеклопластики |
|
|
|
|
|
|
|
|
|
|
. |
|
201 |
|||||||||
§ 8.8. Газонаполненные |
пластмассы |
|
|
|
|
|
|
203 |
||||||||||||||
§ 8.9. Пластмассы |
для маркировки дорожных и аэродромных покрытий |
|
204 |
|||||||||||||||||||
§ |
8.10 Пленки |
и |
пленкообразующие вещества в дорожном и аэродромном |
206 |
||||||||||||||||||
|
|
|
строительстве |
|
|
|
|
|
|
' |
|
|
|
|
|
|
|
|||||
Г л а в а 9. |
Органические |
вяжущие |
материалы |
|
|
|
|
|
|
|
209 |
|||||||||||
§ |
9.1 |
Определение |
и |
классификация |
|
|
|
|
|
|
|
209 |
||||||||||
§ 9.2. |
Состав органических вяжущих материалов |
|
|
|
|
|
210 |
|||||||||||||||
§ 9.3. |
Основные физико-механические свойства органических пяжущих |
|
214 |
|||||||||||||||||||
§ 9.4. |
Состав, гструктура |
и |
свойства органических |
вяжущих материалов |
|
220 |
||||||||||||||||
§ 9.5. |
Нефть и методы ее переработки |
|
|
|
|
|
|
|
224 |
|||||||||||||
§• |
9.6. |
|
Производство |
нефтяных |
битумов |
|
|
|
|
|
|
|
226 |
|||||||||
§ 9.7. |
Битумы нефтяные вязкие и твердые |
|
|
|
|
|
|
|
231 |
|||||||||||||
§ |
9.8. |
|
Битумы |
нефтяные |
жидкие |
|
|
|
|
|
|
|
|
233 |
||||||||
§ 9.9 |
Природные |
|
битумы |
|
|
|
|
|
|
|
|
|
|
|
236 |
|||||||
§ 9.10. Сланцевые |
битумы |
|
|
|
|
|
|
|
|
|
|
|
237 |
|||||||||
§ |
9.11. Каменноугольные |
дегти |
|
|
|
|
|
|
|
|
|
238 |
||||||||||
§ |
9.12. Дорожные |
эмульсии |
|
вяжущих |
и |
методы |
повышения |
их стабильности |
244 |
|||||||||||||
§ |
9.13. Старение |
органических |
248 |
|||||||||||||||||||
§ 9.14. Добавки, вводимые в |
органические |
вяжущие |
материалы |
|
|
251 |
||||||||||||||||
§ |
9.15. Перевозка |
и хранение органических вяжущих материалов |
|
257 |
||||||||||||||||||
Г л а в а |
|
10. Асфальтобетон |
|
|
|
|
|
|
|
|
|
|
|
|
260 |
|||||||
§ |
10.1. Определение, классификация и область применения асфальтобетона |
260 |
||||||||||||||||||||
§ |
10.2. Материалы |
для |
асфальтобетона . |
|
|
его |
взаимодействие с |
минераль |
262 |
|||||||||||||
§ |
10.3. Распределение |
битума |
в |
асфальтобетоне и |
264 |
|||||||||||||||||
§ |
|
|
ными материалами |
|
|
|
|
|
|
|
|
|
|
|
||||||||
10.4. Структура |
|
асфальтобетона |
|
|
|
|
|
|
|
|
268 |
|||||||||||
§ |
10.5. Структурно-механические |
свойства |
асфальтобетона |
|
|
|
г п |
|||||||||||||||
§ |
10.6. Нормативные |
требования |
к асфальтобетону |
и расчет состава |
|
284 |
||||||||||||||||
|
290 |
|||||||||||||||||||||
§ |
10.7 Теоретические |
положения |
технологии |
асфальтобетона |
|
|
|
|||||||||||||||
|
|
|
294 |
|||||||||||||||||||
§ |
10 8. |
Технология |
производства |
асфальтобетона |
|
|
|
|
|
|||||||||||||
|
|
|
|
|
|
|||||||||||||||||
§ |
10.9. Структурно-механические |
и |
технологические |
особенности |
теплого |
Асфальто |
303 |
|||||||||||||||
|
|
|
бетона |
|
|
асфальтобетон |
|
|
|
|
|
|
|
|
307 |
|||||||
§ 10.10. Холодный |
|
|
|
|
|
|
|
|
312 |
|||||||||||||
§ |
10.11. Литой |
асфальтобетон |
|
|
|
|
|
|
|
|
|
|
||||||||||
|
|
|
|
|
|
|
|
|
|
314 |
||||||||||||
§ |
1012 |
Дегтебетон |
|
|
|
|
и |
би+умогрунтовые смеси |
и черный |
щебень |
316 |
|||||||||||
§ |
10.13. Битумоминеральные |
319 |
||||||||||||||||||||
§ |
10.14. Регенерация |
асфальтобетона |
|
|
|
|
|
|
|
|||||||||||||
|
|
|
|
|
|
|
|
|||||||||||||||
Г л а в а |
II. Рулонные и листовые кровельные и гидроизоляционные |
материалы |
324 |
|||||||||||||||||||
324 |
||||||||||||||||||||||
§ |
11.1. Рулонные |
и листовые |
битумные и дегтевые материалы |
|
|
|
||||||||||||||||
|
|
|
|
§ |
11.2. Гидроизоляционные |
материалы |
326 |
|||||||||
§ |
11.3. Приклеенные |
мастики |
|
|
327 |
|||||||
Г л а в а |
12. |
Лакокрасочные |
материалы |
|
329 |
|||||||
§ |
12.1. Составляющие |
красок |
и лаков |
329 |
||||||||
§ |
12.2. Красочные |
|
составы |
|
|
332 |
||||||
Г л а в а |
13. |
Строительные |
материалы |
из древесины |
335 |
|||||||
§ |
13.1. Строение |
|
дерева |
|
|
|
|
335 |
||||
§ |
13.2. Характеристика древесины основных пород, применяемых в строительстве |
338 |
||||||||||
§ |
13.3. Свойства |
|
древесины |
|
|
340 |
||||||
§ |
13.4. Пороки |
древесины |
|
|
|
345 |
||||||
§ |
13.5. Заготовка и сушка древесины |
350 |
||||||||||
§ |
13.6. Материалы и полуфабрикаты из древесины |
351 |
||||||||||
§ |
13.7 |
Консервирование |
|
древесины |
|
353 |
||||||
§ 13.8. Предохранение древесины от возгорания |
357 |
|||||||||||
Г л а в а |
14. |
Металлические |
|
материалы |
|
358 |
||||||
§ |
14.1. Общие |
сведения |
|
|
|
358 |
||||||
§ |
14.2. Структура и свойства металлов |
358 |
||||||||||
§ |
14.3. Стали, применяемые в строительстве |
361 |
||||||||||
§ |
14.4. Термическая |
обработка |
сталей |
363 |
||||||||
§ |
14.5. Арматурные |
стали |
сплавы |
|
364 |
|||||||
§.14.6. Цветные |
металлы |
и |
|
365 |
||||||||
§ 14.7. Обработка металлов давлением |
366 |
|||||||||||
§ |
14.8. Обработка |
металлов резанием |
369 |
|||||||||
§ |
14.9. Сваркай |
резка |
металлов |
защиты |
370 |
|||||||
§ 14.10. Коррозия |
металлов и |
методы |
377 |
|||||||||
|
Список |
литературы |
|
|
|
|
|
380 |
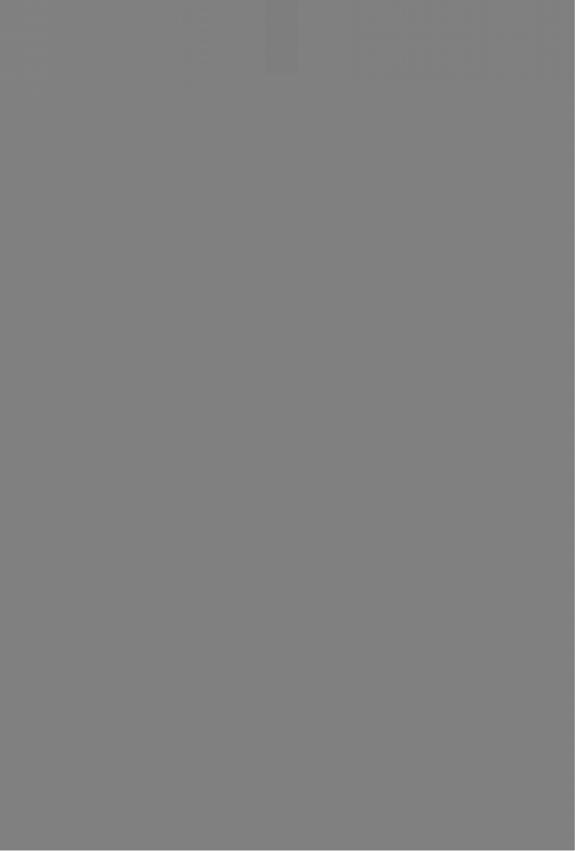