
- •ВВЕДЕНИЕ
- •СОСТАВ, СТРУКТУРА И ОСНОВНЫЕ СВОЙСТВА ДОРОЖНО-СТРОИТЕЛЬНЫХ МАТЕРИАЛОВ
- •ПРИРОДНЫЕ КАМЕННЫЕ МАТЕРИАЛЫ
- •ИСКУССТВЕННЫЕ МАТЕРИАЛЫ НА ОСНОВЕ МИНЕРАЛЬНЫХ ВЯЖУЩИХ И МЕЛКОЗЕРНИСТЫХ ЗАПОЛНИТЕЛЕЙ
- •БЕТОНЫ (ЦЕМЕНТОБЕТОНЫ)
- •СБОРНЫЕ БЕТОННЫЕ И ЖЕЛЕЗОБЕТОННЫЕ ИЗДЕЛИЯ
- •МАТЕРИАЛЫ И ИЗДЕЛИЯ ИЗ ПЛАСТМАСС
- •ОРГАНИЧЕСКИЕ ВЯЖУЩИЕ МАТЕРИАЛЫ
- •АСФАЛЬТОБЕТОН
Глава 2.
ПРИРОДНЫЕ КАМЕННЫЕ МАТЕРИАЛЫ
§ 2.1. ОБЩИЕ СВЕДЕНИЯ
Природные каменные материалы изготавливают из скальных и обломоч ных горных пород. Скальные горные породы — с жесткими структурными связями, обладают достаточно высокой прочностью и залегают в земной коре в виде массивов или трещиноватых слоев. Обломочные горные породы — рыхлые (сыпучие), состоят из обломков скальных горных пород без прочных связей между ними и залегают в виде скоплений.
В зависимости от назначения и условий, в которых будет работать мате риал, применяют дробленые материалы (щебень, высевки), колотые (бутовый камень, шашку для мощения), пиленые (блоки, плиты), штучные разной
степени обработки (брусчатку, шашку для мозаиковой |
мостовой, |
борто |
вые и облицовочные камни, блоки). |
валунный |
камень, |
К природным обломочным горным породам относят |
гравий и песок, которые уже в природном виде могут быть использованы в строительстве. В необходимых случаях валунный камень и галечно-гравий ный материал подвергают расколу, дроблению и последующему грохочению.
Скальные горные породы обладают уже в естественном состоянии рядом благоприятных физико-механических и технологических свойств. Стоимость каменных материалов относительно невысока, вследствие чего их широко применяют для устройства конструктивных слоев дорожных одежд, дренаж ных и укрепительных устройств.
Природные каменные материалы, являясь продуктом механической пере работки горных пород, отличаются от последних формой и размерами, а так же состоянием поверхности раскола отдельностей. Поэтому их свойства зави сят от состава исходной горной породы и ее состояния (трещиноватости, степени выветрелости и др.).
Горные породы — основное сырье для производства керамики, минераль ных вяжущих (гипса, извести, цементов), искусственных каменных безобжиговых материалов, стекла, бетонов и т. д.
§ 2.2. ГОРНЫЕ ПОРОДЫ КАК СЫРЬЕ ДЛЯ ПРОИЗВОДСТВА КАМЕННЫХ МАТЕРИАЛОВ
Горные породы представляют собой плотные или рыхлые агрегаты, состоя щие из тех или иных минералов, обломков других горных пород, в свою очередь, сложенных теми пли иными минералами. Каждая горная порода обладает в своей массе относительно постоянными минералогическим и хими ческим составами, структурой и текстурой, характеризующими ее строение. Химический состав горных пород определяется составом слагающих породу минералов.
В геологии минералами называют природные химические соединения или самородные элементы, являющиеся продуктом физико-химических процессов, протекающих в земной коре.
Условия образования (генезиса) горных пород предопределяют их состав, строение, характер залегания, а следовательно, и свойства. По генезису все
зо
горные породы, слагающие земную кору, делят на три группы: магматические (изверженные), осадочные и метаморфические.
Магматические горные породы подразделяются на: глубинные (граниты, сиениты, габбро, лабрадорит); излившиеся древние (кварцевый порфир, пор фирит, диабаз) и новейшие (трахит, андезит, базальт, липарит). Они образо вались в результате застывания магмы как в слоях земной коры, так и на ее поверхности. Крайне разнообразные условия, при которых происходило фор мирование магматических горных пород, обусловливает образование пород разного минералогического состава, строения, сложения, а следовательно,
итехнических свойств. Поднимаясь по трещинам в земной коре, магма вследствие снижения температуры и давления постепенно застывала на глу бине или значительно быстрее на поверхности, образуя магматические глубинные и излившиеся горные породы.
От быстроты охлаждения зависит и форма минералов: в условиях медлен ной кристаллизации образуются крупные кристаллы, а в условиях быстрой — мелкие. При очень быстром охлаждении образуются породы стекловатой структуры. Неравномерное охлаждение магмы приводит к образованию призматических, шаровых, столбчатых и других форм отдельностей.
При быстром охлаждении магмы и интенсивном выделении из нее газо образных продуктов образовались излившиеся магматические горные поро ды — пемза, вулканический пепел, характерной особенностью которых явля ется пористая, ноздреватая, пемзовидная структура. В процессе уплотнения
ицементации вулканических туфов образуются сцементированные обломоч ные магматические породы — туфы и туфолавы.
Осадочные горные породы подразделяются на: обломочные рыхлые (валу ны, галька, гравий, пески, глины); обломочные сцементированные (песчани ки, конгломераты, брекчии, некоторые виды опок); химические осадки (гипс, ангидрит, доломит, магнезит, известковые туфы); органогенные отложения (известняки, мел, диатомит, трепел, опока). Они образовались путем осажде ния и накопления в водной или воздушной среде продуктов выветривания исходных пород с последующим уплотнением и нередко цементацией осадка. Отражая условия своего образования, осадочные горные породы, как прави ло, носят слоистый или пластовый характер. Это является одним из наиболее важных текстурных признаков осадочных пород и резко отличает их от маг матических, залегающих массивами.
По характеру образования и составу осадочные породы делят на три груп пы: обломочные, химические и органогенные.
Обломочные горные породы (механические отложения) представляют собой накопления рыхлых продуктов главным образом механического разру шения прежде существовавших горных пород. Они могут быть в виде рыхлого скопления обломков разной величины и формы (валуны, галька, гравий, пе
сок и др.), а в последующем уплотнены и сцементированы природными ве ществами, например глинистыми, железистыми соединениями, углекислыми солями, в результате чего образуются конгломераты, брекчии, песчаники.
Если у магматических горных пород составляющие их минералы непосред ственно спаяны между собой и эта связь образуется в процессе формирования породы, то образование сцементированных осадочных горных пород происхо дит путем цементации зерен скелета каким-либо природным веществом и яв ляется процессом вторичным и довольно длительным. Природные цементи рующие вещества (кремнистые, глинистые, железистые) часто в коллоидном состоянии неравномерно обволакивают зерно скелета, медленно заполняя в нем пустоты. По мере формирования коллоидных микросвязей происходит постепенное их уплотнение, а затем кристаллизация, при этом объем цемен тирующего вещества уменьшается. Уменьшение объема цементирующих
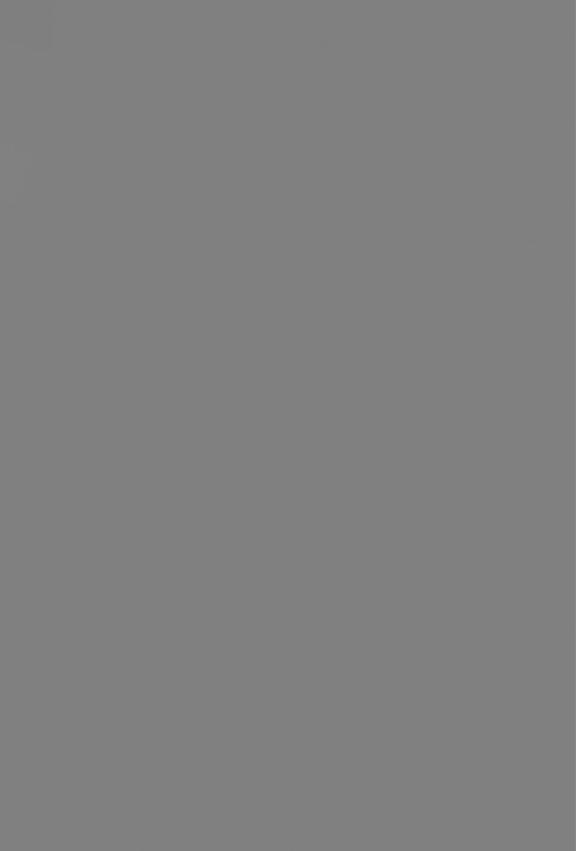
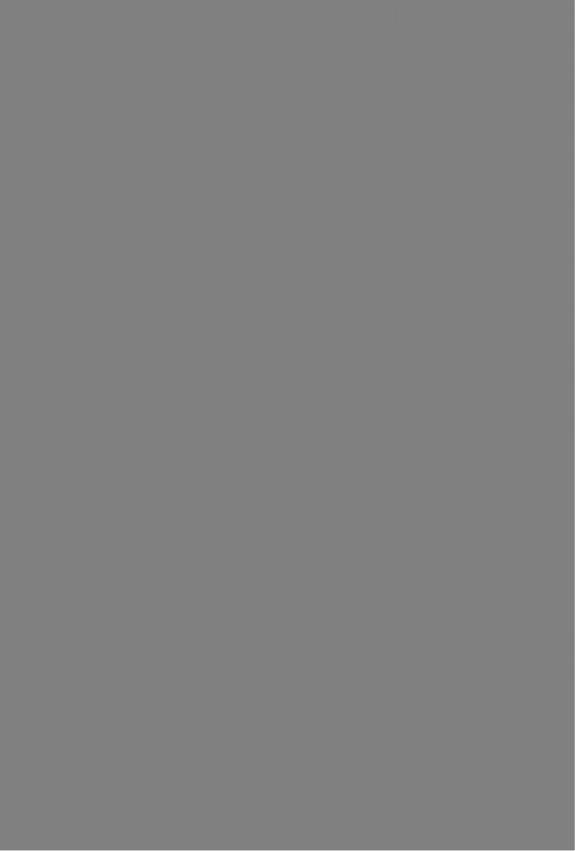
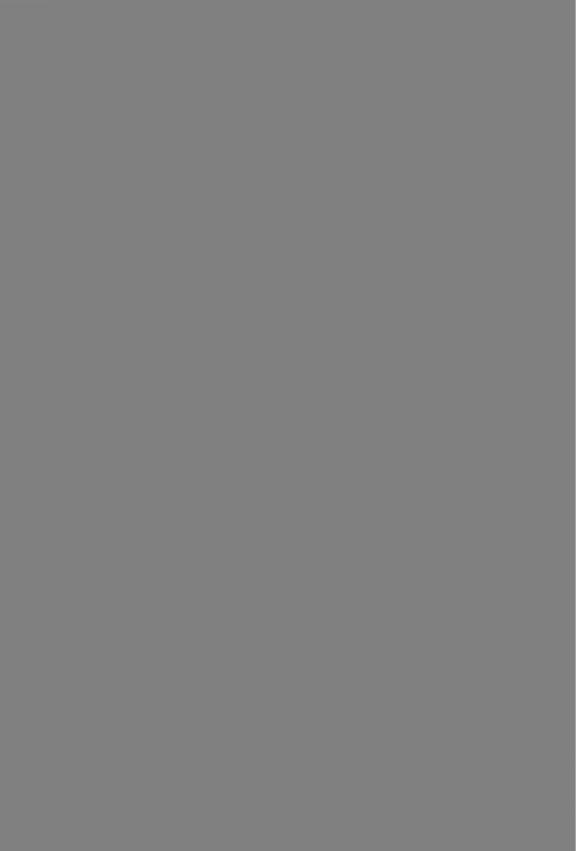
Все горные породы состоят из минералов — природных веществ, имею щих определенный химический состав и физические свойства. Большинство минералов находятся в твердом состоянии. В составе земной коры более 3000 минералов. Однако главную роль в образовании горных пород играют около 100 минералов, которые называются п о р о д о о б р а з у ю щ и м и . Минералы, обыч но присутствующие в горных породах в незначительном количестве как при
меси, носят название в т о р о с т е п е н н ы х ( а к ц е с с о р н ы х ) .
Большинство минералов имеют кристаллическое строение, т. е. слагаю щие их атомы или ионы распределены строго закономерно, образуя кристал лическую решетку. Каждый минерал обладает более или менее постоянным химическим составом и определенным внутренним строением. Эти две важ ные особенности обусловливают довольно постоянные внешние, так называе мые физические свойства. При определении минералов по внешним призна кам в первую очередь обращается внимание на:
цвет — важнейший диагностический признак. Во многих случаях он обусловлен внутренними свойствами минералов и связан с вхождением в его состав хромофоров (Fe, Сг, Мп). Эталонами можно считать названия цвета следующих минералов: фиолетовый — аметист, синий — азурит, зеленый — малахит, красный — киноварь, железо-черный — магнетит и др.;
б л е с к — способность минералов отражать своими поверхностями свет. Различают блеск: металлический — напоминает блеск поверхности свежего излома металлов; стеклянный — напоминает блеск поверхности стекла; шелковистый — характерен Для минералов, имеющих волокнистое строение; жирный — поверхность минерала как бы смазана жиром; восковой; матовый;
т вердост ь — степень сопротивления минерала внешнему механическому воздействию. Наиболее простой способ ее определения — царапание одного минерала другим. Для оценки относительной твердости принята шкала Мооса из 10 минералов, в которой каждый последующий царапает все преды дущие.
За эталоны твердости приняты следующие минералы: тальк — 1, гипс — 2, кальцит — 3, флюорит — 4, апатит'— 5, ортоклаз — 6, кварц — 7, топаз — 8, корунд — 9, алмаз— 10. При определении твердости минералов следует иметь в виду, что ноготь оставляет царапину на минералах с твердостью 1—2, стекло — на минералах с твердостью 4 и ниже, лезвие ножа (сталь) — на ми нералах с твердостью 5 и ниже;
сп а й н о ст ь — способность минерала раскалываться по определенным направлениям с образованием ровных, гладких и блестящих поверхностей (например, слюда). При отсутствии спайности минерал под ударом раскалы вается по случайным неровным поверхностям.
Все минералы в зависимости от химического состава делят на классы окислов и гидроокИсилов, силикатов, карбонатов, сульфатов и др. Ниже рассмотрены основные породообразующие минералы.
Класс окислов и гидроокислов (кремния и железа) — наиболее рас пространенный класс минералов, составляющих около 17% объема земной коры. Наибольшее распространение имеют кварц, опал и лимонит.
К в а р ц (кристаллическая форма кремнезема Si02) входит во многие магматические, осадочные и метаморфические горные породы. Содержание кварца в полиминеральных породах, например граните, может доходить
до 25% и более, а в осадочных (кварцевые пески) |
и метаморфических (квар |
|
цит) доходит до 100%. В |
природе он обычно встречается в виде р-кварца |
|
с’ плотностью 2650 Кг/м3 |
и твердостью 7, имеет |
несовершенную спайность |
и раковистый излом со стеклянным или жирным блеском. |
||
5* |
|
35 |
Кварц— один из наиболее прочных минералов (предел прочности при сжатии достигает 2000 МПа), при обычных условиях кварц химически инер тен. При нагревании (3-кварц переходит в другие модификации с меньшей плотностью, что приводит к увеличению объема. Температура плавления кварца 1713°С. В зависимости от примесей и условий образования кварц может быть прозрачным или-матовым, бесцветным (горный хрусталь), фиоле товым (аметист), черным (морион), серым и др. Разновидностью’кварца
со скрытокристаллической структурой являются х а л ц е д о н |
и к р е м е н ь . |
А м о р ф н ы й к р е м н е з е м — о п а л (Si02 • пН20) имеет |
твердость 5—6,5, |
плотность 1900—2500 кг/м3 и в отличие от кварца обладает большей реак ционной способностью.
Л и м о н и т , и л и б у р ы й ж е л е з н я к (2Fe20 3 • лН20) , чаще встречается в виде примесей в осадочных породах, придавая им бурую или красно-бурую окрас ку. Эти примеси снижают атмосферостойкость пород.
Класс силикатов состоит из 800 минералов, которые являются основной составляющей магматических и метаморфических горных пород. Минералы этого класса, сходные по составу и строению, объединяют в следующие груп пы: полевые шпаты, железисто-магнезиальные силикаты, слюды, глинистые
минералы. |
|
Наибольшее распространение имеют п о л е в ы е |
ш п а т ы — алюмосиликаты |
кальция (ортоклазы К20 • А120 3 • 6Si02), натрия |
и калия (плагиоклазы). |
Полевые шпаты могут иметь разнообразный цвет: белый, розовый, красный, желтый, черный с синим оттенком (лабрадор). Прочность и химическая стой кость полевых шпатов значительно ниже, чем у квррца, что приводит к вывет риванию с образованием нового минерала — к а о л и н и т а .
К классу силикатов относится группа железисто-магнезиальных силика тов, или, как их называют из-за темного цвета, темноокрашенные минералы. Представителями этого класса являются п и р о к с е н ы (авгиты), а м ф и б о л ы (роговые обманки, оливин). Все эти минералы обладают большой плот ностью, прочностью и вязкостью, но под влиянием атмосферных воздействий
сравнительно легко |
разлагаются. О л и в и н , |
присоединяя |
воду, переходит |
|
в се р п е н т и н |
( з м е е в и к ) , увеличиваясь в объеме. Одной из |
разновидностей |
||
серпентина |
является |
хризотиласбест — сырье для асбестоцементной про |
||
мышленности. |
|
|
|
|
С л ю д ы — алюмосиликатные минералы |
сложного химического состава |
обладают совершенной спайностью, т. е. способны расщепляться на тонкие пластинки. Наиболее распространены белая калиевая слюда — м у с к о в и т и черная магнезиальная — биотит.
Глинистые минералы образовались в процессе выветривания алюмосили катных минералов. К ним относится каолинит, монтмориллонит, гидрослюда (и л л и т ) и др. В основном они являются породообразующими минералами глин, суглинков, т. е. пород осадочного происхождения.
Класс карбонатов включает соли угольной кислоты, кальция й магния, ко
торые широко распространены в породах осадочного и метаморфического происхождения.
К а л ь ц и т , и л и и з в е с т к о в ы й ш пат (С а С 0 3), относится к числу распро
страненных минералов, имеет плотность 2600—2800 кг/м3, твердость до 3, плохо растворим в воде, но взаимодействует с кислотами.
М а г н е з и т (MgC03) и д о л о м и т |
(СаС03 • MgC03) имеют меньшее рас |
пространение, чем кальцит. |
пири т (Fe2S), или с е р н ы й к о л ч е д а н , |
Класс сульфидов представляют |
обладающий латунно-желтым цветом и металлическим блеском.
Пирит отличается малой стойкостью и легко разрушается от атмосферных воздействий.
Класс сульфатов насчитывает более 260 минералов, из которых наибо
лее распространены гипс и ангидрит. Сульфаты входят в состав осадочных пород.
Гипс (CaS04 • 2Н20) — минерал белого цвета с плотностью 2300 кг/м3, твердостью 1,5—2, растворим в воде. При обезвоживании гипс переходит в ангидрит (CaS04) — породу более твердую и с большей плотностью — 2800—300 кг/м3 Цвет ангидрита серый, белый, розовый. Внешне он напоми нает мрамор. При длительном контакте с водой ангидрит переходит в гипс, увеличиваясь при этом в объеме до 30%.
§ 2.4. т е х н и ч е с к а я х а р а к т е р и с т и к а г л а в н е й ш и х с к а л ь н ы х
И ОБЛОМОЧНЫХ ГОРНЫХ ПОРОД
Наибольший интерес с точки зрения производства каменных, матери алов представляют горные породы магматического, осадочного и метамор фического происхождений.
Магматические горные породы по химическому составу характеризу ются содержанием главным образом кремния, алюминия, железа, каль ция, магния, калия и натрия. Основными породообразующими минерала ми магматических горных пород являются кварц, полевые шпаты, желе зисто-магнезиальные силикаты, слюды. Характерной особенностью химичес кого состава магматических пород является содержание в них кремнезе ма в свободном или связанном состоянии (кварц и различные силикаты). По содержанию кремнезема эти породы делят на кислые, средние и ос новные. В кислых породах (группа гранитов) содержание кремнезема до ходит до 65—75%, в средних (группа сиенита и диорита) — от 52 до 65, в основных (группа габбро) — от 40 до 52%.
Каменные строительные материалы, получаемые из плотных кристал лических магматических горных пород, в преобладающем большинстве отли чаются большой прочностью, твердостью, вязкостью, погодоустойчивостью, хорошей обрабатываемостью. Так, граниты, сиениты, порфиры и диабазы обладают прочностью более 120 МПа, пористостью 0,2—0,7%, водопоглощением 0,1—0,5%, морозостойкостью и износостойкостью. Следует указать на следующую закономерность в технических свойствах изверженных горных пород, зависящую от минералогического состава и структуры: по мере уве
личения содержания пироксенов, амфиболов |
и оливина |
(от гранита до пи- |
роксенита) возрастают вязкость, плотность, |
прочность. |
Краткая характе |
ристика магматических пород по их генезису приведена |
в табл. 2.1. |
Гранит — наиболее распространенная глубинная магматическая горная порода. Он представляет собой массивную, равномерно зернисто-кристал лическую породу, состоящую в основном из кварца (20—40%), ортоклаза, реже щелочного плагиоклаза (40—80%), слюды, иногда роговой обманки и авгита (5—20%). Кроме равномерно кристаллической структуры, отдель ные переходные разновидности гранита обладают порфировидной структу рой, в которой более крупные кристаллы, например ортоклаз, вкраплены на общем равномерном мелкокристаллическом фоне. К этой разновидности относится финляндский гранит — рапакиви (по-фински — гнилой, кроша щийся камень), широко распространенный в Карелии и Финляндии. Ха рактерным признаком рапакиви служит яйцевидная форма кристаллов ортоклаза розового и красного цветов, окруженных зеленоватой или серой тонкой каемкой олигоклаза (из группы плагиоклазов). Рапакиви сравни тельно с другими разновидностями гранитов легче выветривается вслед ствие разрушения олигоклаза и выпадения кристаллов ортоклаза.
оо
00
|
|
|
|
|
|
Т а б л |
и ц а 2.1 |
|
|
|
Физико-механические и технологические свойства |
|
|||
Группа горных по- |
Основные физнко- |
Структурно-текстурные |
IЛредел проч |
|
Энергоем |
|
|
Степень |
кость (удель |
Водопогло- |
Марка |
||||
род по генезису |
свонства |
признаки |
ности при |
*ная работа |
|||
|
|
расколе, |
хрупкости, |
при статиче |
щенне, % |
породы |
|
|
|
|
более |
||||
|
|
|
МПа, более |
ской нагруз |
|
|
|
|
|
|
|
|
|
ке), более
1. МагматиЧе- |
1. |
Граниты, |
Породы |
|
Породы |
полнокри- |
6 |
1 |
0,8 |
||||
ские (извер- |
сиениты, дно- |
(свежие) |
|
|
сталлической структу- |
|
|
|
|||||
женные) |
риты, |
порфи- |
прочностью |
ры (мелкосредне- и |
|
|
|
||||||
|
ры, |
диабазы, |
при сжатии бо- |
крупно) |
плотные, |
по- |
|
|
|
||||
|
габбро |
лее 120 МПа; |
верхность раскола ше- |
|
|
|
|||||||
|
|
|
морозостой |
роховатая |
|
|
|
|
|
||||
|
|
|
кость более |
|
|
|
|
|
|
|
|
||
|
2. Липариты, |
Мрз 200 |
|
|
Породы мелко- |
или |
6 |
4 |
0,2 |
||||
|
Породы |
|
|||||||||||
|
аезиты, трахи |
(свежие) |
|
скрытокристалличе |
|
|
|
||||||
|
ты, бозальты |
прочностью |
ской |
структуры, плот |
|
|
|
||||||
|
|
|
при сжании бо |
ные, |
реже |
пористые, |
|
|
|
||||
|
|
|
лее 120 МПа; |
поверхность |
раскола |
|
|
|
|||||
|
|
|
морозостой |
гладкая |
или слабоше |
|
|
|
|||||
|
|
|
кость более |
роховатая |
|
|
|
|
|
||||
|
|
Граниты, |
Мрз 50—200 |
Породы |
полно-мел |
5 |
2 |
0,5 |
|||||
|
3. |
Породы |
|
||||||||||
|
сиениты, дио |
пониженной |
ко- и скрытокристалли |
4 |
5 |
0,4 |
|||||||
|
риты, порфи |
прочности |
(ча |
ческой |
структуры |
от |
|
|
|
||||
|
ры, |
диабазы, |
стично |
затро |
плотной до сильно по |
|
|
|
|||||
|
андезиты, габ |
нутые |
вывет |
ристой |
текстуры, |
по |
|
|
|
||||
|
бро, липариты, |
риванием), |
верхность раскола от |
|
|
|
|||||||
|
трахиты |
прочностью |
гладкой до |
шерохова |
|
|
|
||||||
|
|
|
при сжатии от |
той |
|
|
|
|
|
|
|
||
|
|
|
80 до 120 МПа; |
|
|
|
|
|
|
|
|
||
|
|
|
морозостой |
|
|
|
|
|
|
|
|
||
|
|
|
кость Мрз 50— |
|
|
|
|
|
|
|
|
||
|
|
|
100 |
|
|
|
|
|
|
|
|
|
|
II. Осадочные |
1. Песчаним1 |
Породы |
Породы |
от плотно |
6 |
2 |
0,6 |
||||||
|
|
|
(свежие |
и за |
кристаллических до |
5 |
2,5 |
0,5 |
|||||
|
|
|
тронутые |
вы- |
слабосцементирован- |
4 |
4 |
0,1 |
0,5
© Т о сл
0,5— 1,0 0,5—2,0
0 СП 1 СЛ о
1
1
II
III
I
И
III
ветриванием) |
ных зернистых, раскол |
прочностью |
гладких до слабошеро |
при сжатии 60 |
ховатого |
МПа; морозо |
|
|
|
стойкость Мрз |
|
|
|
|
|
|
|||
|
|
25—150 |
|
Породы от |
плотно |
||||||
|
2. Известня |
Породы |
|
||||||||
|
ки и доломиты |
(свежие и за |
кристаллической |
до |
|||||||
|
|
тронутые |
вы |
слабоецементирован |
|||||||
|
|
|
ветриванием) |
ных |
зернистых, |
пло |
|||||
|
|
|
прочностью |
щадь раскола гладкая |
|||||||
|
|
|
при сжатии бо |
шероховатая |
|
||||||
|
|
|
лее МПа; мо |
|
|
|
|
|
|
||
|
|
|
розостойкость |
|
|
|
|
|
|
||
|
|
|
Мрз |
25—150 |
|
|
|
|
|
|
|
III. Метамор |
1. |
Кристал |
Породы |
Породы |
полнокрис |
||||||
фические |
лические слан |
(свежие, |
час |
таллической |
и |
грубо |
|||||
|
цы |
(гнейсы) |
тично |
вывет |
зернистой структуры с |
||||||
|
|
|
релые) |
проч |
преобладанием |
харак |
|||||
|
|
|
ностью при |
терной |
сланцеватости, |
||||||
|
|
|
сжатии |
более |
раскол |
шероховатый |
|||||
|
|
|
60 МПа; моро |
|
|
|
|
|
|
||
|
|
|
зостойкость |
|
|
|
|
|
|
||
|
2. Кварциты |
Мрз |
25—200 |
Породы |
скрытокри |
||||||
|
Породы |
||||||||||
|
и кварцитовид |
прочностью |
сталлической |
структу |
|||||||
|
ные песчаники |
при сжатии |
ры, |
плотной |
текстуры |
||||||
|
|
|
более 80 МПа |
|
|
|
|
|
|
||
|
|
|
морозостой |
|
|
|
|
|
|
||
|
|
|
кость Мрз |
|
|
|
|
|
|
||
|
3. Мраморы |
100— 200 |
Породы |
кристалли |
|||||||
|
Породы |
||||||||||
|
и |
мраморо |
прочностью |
ческой структуры, |
|||||||
|
видные изве |
при сжатии бо плотные |
|
|
|
||||||
|
стняки |
лее |
80 |
МПа; |
|
|
|
|
|
|
|
|
|
|
морозостой |
|
|
|
|
|
|
||
|
|
|
кость Мрз |
|
|
|
|
|
|
||
|
|
|
50— 100 |
|
|
|
|
|
|
3
со 4* СЛ СГ>
_ СО СЛ СГ)
_ СО 4*- СЛ 4». СЛ СП
6 |
о |
|
IV |
2,5 |
0,5 |
0,5—5,0 |
I |
4 |
0,4 |
|
II |
6 |
0,0 |
|
III |
8 |
0,0 |
|
IV |
1 |
0,8 |
0,1—2,0 |
I |
2 |
0,5 |
|
И |
5 |
0,4 |
|
III |
6 |
0,05 |
|
IV |
4 |
0,2 |
0,1 —V,0 |
II |
5 |
0,15 |
|
III |
100 |
0,05 |
|
IV |
2 |
0,5 |
0,5—2,0 |
II |
4 |
|
|
III |
6 |
|
|
IV |
Граниты обладают плотным сложением. Цвет гранитов зависит глав ным образом от ортоклаза и содержания темноцветных минералов; обычно преобладают серые и красные цвета разных оттенков. Очень красивым ри сунком обладают гранатовые и разновидности серых гранитов с кварцем синих тонов (например, граниты некоторых месторождений по рекам Юж ный Буг и Рось).
Граниты характеризуются средней плотностью 2700 кг/м3, объемной мас
сой 2600 кг/м^, малой водонасыщенностью, |
большой |
прочностью |
(120 — |
|
200 МПа) и |
погодостойкостью. Прочность отдельных мелкозернистых раз |
|||
новидностей |
гранитов достигает 300 МПа |
(например, |
Гниванское |
место |
рождение, УССР), Из гранитов можно изготовить все виды каменных материалов — рва
ные, колотые, дробленые, тесаные и полированные. Красивая окраска не которых разновидностей гранитов позволяет использовать их для отделоч ных работ. Граниты неогнестойки, утрачивают прочность при температуре выше 800°С.
Граниты — распространенная порода. На территории СССР известны обширные области их распространения: Карелия, Украина, северные скло ны Кавказа, Урал, Алтай, Тянь-Шань, Саяны, Прибайкалье, Яблоновый хребет, район р. Уссури и др.
Сиениты по минералогическому составу отличаются от гранитов отсут ствием кварца (или небольшим содержанием его) и преобладанием ще лочного полевого шпата. Сиениты, содержащие заметное количество квар ца, являются переходными породами между сиенитами и гранитами. Струк тура сиенитов обычно равномерно кристаллическая, но встречаются и пор фировидные разности. Окраска сиенитов чаще бывает серая, красноватая, темно-зеленоватая. Плотность их 2700—2900, объемная масса 2600— 2800 кг/м3, пористость и водонасыщение незначительны. Прочность при сжатии у сиенитов колеблется в пределах 120—150 МПа. По сравнению с гранитами они несколько мягче, лучше полируются и более вязки, в особен ности если в их составе имеются амфиболы и пироксены. Применение си енитов то же, что и гранитов. На территории СССР сиениты распространены более ограниченно. Известны месторождения сиенитов на Кольском полу острове, Украине, Сахалине, в горах Тянь-Шаня и др.
Диориты состоят из кислого плагиоклаза (около 75%), роговой обман ки, реже биотита и авгита. Иногда в состав диорита входит кварц; такой диорит носит название кварцевого. В зависимости от преобладания цветных минералов различают роговообманковый, авгитовый, биотитовый диориты. Структура у них равномерно кристаллическая, окраска преобладает от темно-зеленоватой до черно-зеленой, плотность 2700—3000 кг/м3, прочность при сжатии 180—340 МПа — в среднем выше, чем у гранитов и сиенитов. Они отличаются повышенной вязкостью и устойчивостью против выветри вания. Диориты наравне с гранитами и сиенитами пригодны для произ водства различных видов каменной продукции и в особенности штучных материалов. Месторождения диоритов известны в Крыму, на Украине, Ура ле, Кавказе, Средней Азии и др.
Габбро — горная порода, состоящая в |
основном из плагиоклаза (око |
ло 50%) и пироксена; реже в состав габбро |
входят роговая обманка, оливин |
и биотит. Структура габбро обычно равномерно крупнокристаллическая, окраска темно-зеленая, оливково-зеленая и коричнево-зеленая, плот ность 2800—3100 кг/м3, прочность при сжатии в среднем 200—280 МПа, но у крупнозернистых разностей уменьшается до 100 МПа. Габбро — стой кая порода против выветривания: чем меньше в ней полевого шпата и чем равномернее и мельче структура; тем выше ее погодоустойчивость. Габбро
наряду .с высокой прочностью обладает большой вязкостью, что несколько затрудняет разработку.
Полируется габбро |
хорошо. Особенно красивой расцветкой обладает |
л а б р а д о р и т , в котором |
преобладает минерал л а б р а д о р . Наряду с другими |
изверженными породами габбро находит применение в дорожном строи тельстве для получения различных строительных материалов. Лабрадориты с красивой окраской используются для декоративных целей.
Различные условия застывания одной и той же по химическому составу магмы (по сравнению с глубинными породами) обусловливают формиро вание порфировой, фельзитовой, микролитовой и стекловатой структур1.
Древневулканические излившиеся породы характеризуются большей перекристаллизованностью основной массы. Нововулканические породы сфор мировались позже и содержат больше стекловатой фазы.
К в а р ц е в ы й п о р ф и р обладает порфировой структурой с вкраплением в основную массу как бы оплавленных кристаллов кварца. По минералоги ческому составу он аналогичен гранитам, цвет чаще красный, бурый, а иног да зеленоватый, плотность 2400—2600 кг/м3, прочность при сжатии 130— 180 МПа, погодоустойчив. Качество кварцевых порфиров для производства дорожных каменных материалов повышается с уменьшением количества и размеров вкрапленников. Чем больше стекловатой массы, тем больше хрупкость кварцевого порфира. Лучшие его разновидности относятся к фельзитовым порфирам, содержащим незначительное количество вкрап ленников.
Каменные материалы из кварцевых порфиров применяют в виде щебня, бута, колотой и тесаной шашки, для декоративных целей и др. Месторож дения кварцевых порфиров в СССР известны в Крыму, на Урале, Алтае, Сахалине и др.
Л и п а р и т ы — нововулканические породы, аналогичные по составу гра ниту. Цвет — белый, серый, светло-желтый, а иногда красноватый. Струк тура липаритов часто микропорфировая с повышенным содержанием сте кловатой фазы. Наряду с плотными встречаются пористые его разновид ности. Каменные материалы из плотных, скрытокристаллических липари тов применяют для работ наравне с материалами из кварцевых порфиров. Так, например, из них может быть получен высококачественный щебень.
О р т о к л а з о в ы е п о р ф и р ы и трахиты по минералогическому составу ана логичны сиенитам. От кварцевых порфиров и липаритов они отличаются отсутствием кварца. По техническим свойствам эти породы стоят ближе к бескварцевым порфирам и липаритам, но более легко поддаются об работке. Месторождения ортоклазовых порфиров известны на Кавказе, Урале, в Крыму.
Д и а б а з ы — преимущественно мелкокристаллические породы, состо ят из известково-натрового полевого шпата и авгита, реже в состав их входят оливин, роговая обманка и др. Характерной особенностью диабазов является переплетенное строение, при котором промежутки между беспо рядочно переплетенными кристаллами известково-натровых полевых шпа тов заполнены темной аморфной авгитовой массой. Плотность диабаза 2800—3000 кг/м3, прочность при сжатии в среднем около 200 МПа (иногда до 400 МПа); они хорошо полируются. При выветривании диабаз приобре тает бурую окраску и распадается на щебень ржавого цвета, обогащен ный глинистым веществом.
Переходные формы структуры от полнокристаллической до стекловатой. Фельзиты тесная смесь микрокристаллов со стеклом, микролиты — мельчайшие кристаллики, видимые ТОЛЬКО в микроскоп.
Особенности строения диабаза позволяют изготовлять из него хороший штучный камень — разнообразные плиты, брусчатку, шашку. Щебень из диабаза обладает высокими качествами для приготовления асфальтобето нов и черного щебня. Аналогичны диабазам по техническим свойствам про межуточные породы — габбро-диабазы. Известны месторождения диаба зов в Карелии, на Украине, Кавказе, Урале.
Андезиты относятся к группе нововулканических пород. Они состоят из роговой обманки или пироксенов, слюды и известково-натровых пла гиоклазов, которые являются вкрапленниками. Андезиты обладают окрас кой от светлой до темно-серой. Плотность их колеблется в пределах 2650— 2750 кг/м3, они прочны (120—240 МПа), тверды, хорошо поддаются рас колу, погодоустойчивы.
Базальты — породы темного цвета, плотные, обычно скрытокристалли ческой структуры, состоящей из плагиоклаза и авгита (часто оливина). В базальтах не все минералы успели выкристаллизоваться, вследствие чего порода содержит то или иное количество стекловатой фазы.
Технические свойства базальтов крайне различны: плотность 2700— 3300 кг/м3, они тверды и обладают высокой прочностью, достигающей 300, иногда 500 МПа. Относительная хрупкость базальтов несколько снижает их общие, довольно высокие технические свойства. Базальты в месторож дениях часто разбиты трещинами на столбчатые (иногда шаровидные и пли точные) отдельности, что в значительной мере облегчает их разработку. По внешним признакам хорошее качество базальта определяется темной ок раской, равномерным мелкокристаллическим строением. Основная масса и несущественные минералы с трудом царапаются стальной иглой. Место рождения базальтов в СССР известны на Украине, в Армении, Забай калье, на Сахалине и Камчатке. Столбчатые отдельности базальтов об легчают разработку месторождений, вместе с тем ограничивают возмож ность изготовления из них крупных монолитов. Базальты используются для изготовления шашки, брусчатки, щебня.
Осадочные горные породы залегают в верхних слоях земной коры. Зем ная поверхность на 75—80% расположена в области развития осадочных горных пород, но в общей толще земной коры осадочные породы состав ляют 5%. Каменные материалы из осадочных горных пород характеризу ются крайне разнообразными техническими свойствами, что объясняется условиями образования пород: перерывы в отложении осадков, а также разная их крупность; принос извне различных примесей; разная степень уплотнения и цементации; разный состав природного цемента. Для оса дочных горных пород характерной особенностью является пластовая фор ма залегания, их слоистость, пористость. С течением времени осадочные горные породы за счет уплотнения и цементации претерпевают ряд фи зико-химических изменений, которые постепенно приводят к уменьшению пористости, а в ряде случаев к исчезновению внешних признаков слоис тости, которая обнаруживается только при выветривании и их переработке.
Скальные горные породы осадочного происхождения (известняки, доло миты, гипс, ангидрит, песчаники, конгломераты, брекчии), в отличие от маг матических, в той или иной мере растворимы в воде и снижают свою проч ность при водонасыщении, за исключением сцементированных пород с крем нистым цементом и кремнистых разностей известняков.
Деление осадочных пород на обломочные (рыхлые и сцементированные), химические и органогенные (см. табл. 2.2) условно. Например, некоторые известняки занимают промежуточное положение, так как содержат в своем составе материал органогенного или обломочного рыхлого происхождения, сцементированный природным минеральным вяжущим.
О б л о м о ч н ы е п о р о д ы и л и м е х а н и ч е с к и е о т л о ж ен и я — продукты выве
тривания магматических, метаморфических или ранее образованных оса дочных пород. Различают рыхлые и сцементированные обломочные породы (табл. 2.2).
Р ы х л ы е о б л о м о ч н ы е о с а д о ч н ы е г о р н ы е п о р о д ы — скопление продуктов
выветривания скальных горных пород. Вследствие этого их петрографи ческий и минералогический составы аналогичны исходным материнским по
родам. По происхождению |
(генезису) рыхлые обломочные горные |
поро |
ды могут быть: речные или |
аллювиальные (русловые, пойменные и |
дель |
товые осадки), водно-ледниковые или флювиогляциальные (зандровые, озово-камовые и моренные), озерные и морские (прибрежные и глубинные), ветровые или эоловые (дюнные, барханные, бугристо-кучевые, грядовые). По крупности окатанных обломков рыхлые горные породы условно делят
на валуны (крупнее |
100 мм), гальку, гравий и песок. |
В а л у н н ы й к а м е н ь |
— грубоокатанные, преимущественно округлой фор |
мы, обломки скальных горных пород размером более 100 мм. Качество валунного камня обусловливается петрографическим составом породы, крупностью и формой обломков, а также степенью выветривания. По ус ловиям залегания валунный камень (рис. 2.5) может быть верховой (или полевой), низовой (недровый), речной (горные реки), морской и озерный (прибрежный и донный или глубинный).
Лучший по качеству (свежести) валунный камень магматических по род низовой и донный, находящийся длительное время под слоем грунта или под водой, где он лучше защищен от выветривания. Валунный камень, отложенный на поверхности земли, более затронут выветриванием, вследст вие чего качество его ниже за счет большего количества отходов при пред варительной сортировке собранного валуна и дальнейшей его колке и дроб лении.
Валуны размером до 25 см называют сырцом, так как их можно при менять для дорожных работ (например, мощения) без дополнительной обработки. Более крупные валуны используют для получения каменного
материала |
(шашки, щебня) путем раскалывания и дробления. |
Г а л ь к а |
представляет собой окатанные водой обломки горных пород раз |
мером от 100 до 70 (40) мм. Она обладает теми же свойствами, что и мел кий валунный камень. Гальку применяют для устройства оснований, дре нажей, но чаще измельчают и используют как щебень.
Г р а в и й — рыхлое скопление окатанных обломков исходных горных по род размером от 70 до 5 (3) мм.
В месторождениях карьерный гравий может залегать в виде сплошных скоплений, отдельных слоев, линз, гнезд и содержать различное количество примесей в виде галечников, песка, глинистого вещества. Наиболее загряз
нен примесями |
моренный |
гравий. Более рентабельны для разработки |
его |
|||
|
|
|
|
|
Т а б л и ц а |
2.2 |
Сцементированные |
Рыхлые породы |
Сцементированные |
Рыхлые породы |
|
||
породы |
угловатые |
окатанные |
породы |
угловатые |
окатанные |
|
|
|
|
||||
Брекчии (из уг |
Глыбы |
Валуны |
Песчаники |
Дресва |
Гравий |
|
ловатых облом |
|
|
|
|
|
|
ков) |
Щебень |
Галька |
Алевролиты |
Песчаные |
|
|
Конгломерат |
|
|
||||
(из окатанных |
|
|
Аргиллиты |
Пылеватые |
|
|
обломков) |
|
|
Глинистые |
|
|
Рис. 2.5. Схема залегания валунно-галечниковой породы:
/ — верховое; 2 — линзовое; 3 — низовое; 4 — береговое; 5 — донное
сплошные покровные отложения. В зависимости от времени образования различают современный гравий (речной или аллювиальный) и древнего происхождения (моренный и озово-камовый древнеледникового происхож дения).
Петрографический состав гравия, форма зерен и степень их окатанности зависят от литологической характеристики мест его образования, условий переноса обломочного материала. Так, в Ленинградской обл. карь ерный гравий состоит из окатанных обломков диабазов, кварцитов, кристал лических сланцев и других пород, месторождения которых находятся в се верных районах страны.
Добытый в карьере гравий (рядовой) может содержать различное ко личество песка. В том случае, когда гравийный материал содержит песка более 50%, его называют гравийно-песчаным. Крупный рядовой гравий состоит из зерен 5—70 мм, а средний рядовой — 5—40 мм.
Карьерный гравий после перегрохотки и отделения песка называется сортовым. Его разделяют на следующие фракции: 70—40, 40—20, 20—10, 10—5 и менее 5 мм — гравийный песок.
Гравийный материал (рядовой карьерный и фракционированный сос тавной) применяют для устройства гравийных покрытий, конструктивных слоев дорожной одежды, дренажных сооружений, в качестве балластного
Класс
Петрографическая характеристика грави гравия по прочности
|
Т а б л и ц а 2.3 |
|
Марка гравия |
Марка гравия по износ\ |
|
(истиранию) в по |
||
по лробимостн при сжа |
||
тии (раздавливании) |
лочном барабане |
|
в цилиндре |
|
Гравий состоит из окатанных зерен |
|
|
|
|
средне- и мелкокристаллических извержен |
|
|
|
|
ных пород и кристаллических сланцев, |
|
|
|
|
мраморовидных известняков, кварцевых |
1 |
|
|
|
песчаников или из смеси этих пород |
Др. |
8 |
И-20 |
|
Гравий состоит из окатанных зерен |
|
|
|
|
крупнокристаллических изверженных по |
2 |
|
|
|
род, песчаников или из смеси этих пород |
Др. |
12 |
и -з о |
|
Гравий состоит из перечисленных выше |
|
|
|
|
пород, слабо затронутых выветриванием |
3 |
Др. |
16 |
И-45 |
То же, но со значительными признаками |
|
|
|
|
выветривания |
4 |
Др. |
20 |
И-5$ |
Песок |
Модуль крупности |
Полные остатки на снте 0,63, % |
|
Крупнозернистый |
3.5— |
2,4 |
50—70 |
Среднезернистый |
2.5— 1,9 |
|
35—50 |
Мелкозернистый |
2,0 -1,5 |
1,1 |
20—35 |
Очень мелкозернистый |
1.6— |
7—20 |
|
Тонкозернистый |
1,0 |
|
7 |
1 Модуль крупности вычисляют |
с точностью до 0,1 как |
частное от |
деления на 100 суммы полных остатков |
на всех ситах, начиная с снта размером отверстий 0,14 мм. Модуль |
крупности носит условный характер и не |
||
всегда отражает качество песка. |
|
|
|
слоя для железных дорог, крупно-зернистой составляющей в цементобе тоне. Дробленый гравий применяют в качестве щебня для приготовления асфальтобетонных смесей. В зависимости от назначения к гравийному ма териалу предъявляются и соответствующие технические требования.
Для дорожно-строительных целей гравийный материал делят на четы ре марки (класса) в соответствии с классификацией его по ведущим приз накам — петрографическому составу и прочности (табл. 2.3).
Песок — рыхлая зернистая порода, образовавшаяся в результате естест венного разрушения горных пород, крупностью зерен до 5(3) мм. В песке иногда имеются частицы мельче 0,05 мм, которые называют пылеватыми (0,05—0,005 мм) и глинистыми (мельче 0,005 мм). В зависимости от мине ралогического состава различают пески: кварцевые, слюдовые (с содержа нием чешуек слюды свыше 1%), глауконитовые (с примесью железистых соединений), ракушечные, содержащие значительное количество обломков ракушек, гумозные (с содержанием органических соединений более 0,5%) и др. Наиболее прочными являются кварцевые пески. Цвет песка обуслов лен примесями: чистые кварцевые пески — белые, сероватые; окрашенные окислами железа — желтые, бурые, вишнево-красные; глауконитовые — зе леные.
Форма и характер поверхности зерен песка зависят от условий обра зования: речной, озерный, морской, дюнный песок состоит из частиц окру глой формы с гладкой поверхностью, ледниковый и овражный песок — из частиц угловатой формы с шероховатой поверхностью. Пески имеют плот ность 2650 кг/м3, объемную массу от 1450 до 1800 кг/м3; при увлажнении объем песка не изменяется. Классификация песков по крупности и грану лометрическому составу для строительных работ приведена в табл. 2.4.
Качество песка для строительных работ определяют минералогическим составом, формой зерен, гранулометрическим (зерновым) составом, со держанием глинисто-пылеватых частиц, плотностью, объемной (насыпной) массой, пустотностью, фильтрационной способностью, влажностью и со держанием органических примесей.
Песок применяют для устройства подстилающих слоев дорожной одеж ды, приготовления строительных растворов, цементо- и асфальтобетонов, Для устройства дренажей. Песок является сырьем для производства сили катных изделий, керамики и др. Для улучшения качества мелкозернистый песок обогащают добавками искусственного (дробленого) песка (круп ностью менее 5 мм) из невыветрелых магматических и метаморфических пород прочностью более 80 МПа, осадочных — прочностью более 40 МПа и из гравия.
Дресва — промежуточный продукт выветривания скальных горных по род, оставшийся на месте образования и сохранивший камневидное сос тояние. В месторождениях дресва может залегать в виде поверхностного
|
|
|
Объем |
Водопо- |
Морозо |
Предел |
|
прочности, |
Кате- |
Стадия выветре- |
Внешние признаки |
|
МПа |
||||
ная мас |
глошеннс |
вой- |
|
|
|
|||
горня |
лостн породы |
выветрелости |
са, кг/м3 |
по массе, |
кость, |
|
|
|
|
|
|
|
% |
Мрз25 |
при |
|
при рас |
|
|
|
|
|
|
сжатии |
коле |
0 Свежая
IВесьма
слабая
II Слабая
III Средняя
IV Значительная
VВесьма зна чительная
Гранит |
|
|
|
2630 |
0,3 |
+ |
150 |
15-22,5 |
По внешним признакам |
2600 |
0,3— |
|
90— 150 |
10— 15 |
|||
выветрелость не обна |
+ |
|||||||
руживается |
|
|
|
2630 |
0,5 |
|
65—90 |
|
Слабое потускнение |
2550— |
0,5— |
+ |
7—11 |
||||
минералов |
и |
небольшие |
2600 |
0,7 |
|
|
|
|
ржавые и |
белесые на |
|
|
|
|
|
||
леты |
|
|
|
2300— |
'0,7 — |
+ |
30—65 |
2 ,5 - |
Значительное побуре |
||||||||
ние породы, |
появление |
2550 |
1,5 |
|
|
7,5 |
||
микротрещин |
(дресва) |
2000— |
1,5— |
4- |
10—30 |
1,0—2,5 |
||
Порода явно трещино |
||||||||
ватая с заметными буры |
2300 |
2,5 |
|
|
|
|||
ми и белесыми налетами, |
|
|
|
|
|
|||
с трудом разламывается |
|
|
|
|
|
|||
руками (дресва) |
2000 |
2,5 |
|
10 |
1 |
|||
Рыхловатая дресва бу |
|
|||||||
роватого цвета, |
легко |
|
|
|
|
|
||
разламывается |
руками |
|
|
|
|
|
на угловатый микротрещиноватый щебень
слоя выветривания различной мощности, в виде гнезд и прослоек в более глубоких слоях и, наконец, в виде рыхлой осыпи. Различные стадии выветрелости гранита по исследованиям М. М. Подъяконова характеризуются признаками, приведенными в табл. 2.5.
Дресва является местным материалом и в зависимости от исходной горной породы и стадии выветрелости может применяться для устройства различных слоев одежды на дорогах местного значения.
Сцементированные осадочные породы образовались из рыхлых в резуль тате цементации их природными веществами — кремнеземистыми, желе зистыми, известняковыми, глинистыми. Наибольшее применение в дорож ном строительстве находят песчаники, конгломераты и брекчии.
Песчаники представляют собой породы, состоящие из мелких зерен минералов, связанных природным цементом в более или менее плотную мас су. По минералогическому составу зерна песчаника обычно состоят ю кварца, который, как известно, наиболее устойчив против выветривания. Сравнительно редко встречаются песчаники, состоящие из сцементирован ных обломков полевых шпатов (так называемые аркозовые песчаники) и из смеси обломков кварца, полевого шпата, слюд (серая вакка). В песча никах, кроме породообразующего минерала, имеются примеси и других минералов — окислов, силикатов и др. Цвет песчаника крайне разнообра зен и бывает от белого до темно-серого, от розового до красно-бурого, что зависит от окраски частиц, но главным образом от цементирующего вещества и примесей.
В зависимости от цементирующего вещества и примесей различают песчаники: глинистый, кремнистый, железистый, известковый (карбонатный), гипсовый, битуминозный и др. Наибольшей прочностью, твердостью и \ч тойчивостью против выветривания облаДают плотные, мелкозернистые, кре мнистые песчаники. Однако они плохо поддаются обработке, дают непр.г
вильный раковистый раскол с острым режущим ребром и отличаются хруп костью. Гладкая поверхность раскола, сравнительно легкая обламываемость ребер при уплотнении определяют низкое качество щебня.
Раковистый излом служит признаком однородного тонкокристалличес кого строения, в котором отдельные зерна прочно связаны между собой. При воздействии внешних механических усилий на такого рода горные породы составляющие их зерна не раскалываются и не образуют плоскостей скольжения (как у гранитов, крупнозернистых песчаников и др.), а на чинают деформироваться по сегменту от отдельных центров. Наиболее рель ефно эти свойства выступают у сливных кварцитовидных песчаников. Из вестковые и в меньшей мере доломитовые песчаники сравнительно менее устойчивы против выветривания. Обладая сравнительно большой проч ностью, они легче поддаются обработке. Глинистые песчаники менее ус тойчивы против выветривания и при увлажнении вследствие поглощения воды и размягчения цементирующего вещества они резко снижают проч ность.
Песчаники, обладая разнообразными техническими свойствами, находят применение в дорожно-мостовом строительстве в основном как местные материалы в виде бута, колотой шашки, щебня и реже штучного камня. Плиточные песчаники используют в виде плит для устройства полов, троту аров и пр. Крупнейшие месторождения кварцевых плотных песчаников разной окраски известны в окрестностях г. Коростеня. Эти песчаники вслед ствие высокой прочности и погодоустойчивости, однородности строения, красивой расцветки в отдельных случаях в полированном виде исполь зуются в строительстве для декоративных целей.
Из крупных разрабатываемых месторождений песчаников можно назвать онежские песчаники, карьеры в районе г. Тулы, путиловские, рыльские, судженские, шостскинские (Сумской обл.), еленовские (Донбасс), Вольские, уральские, шахтинские и многие другие.
Конгломераты состоят из округлых обломков минералов и горных по род размером больше 5 мм, сцементированных каким-либо природным ве ществом (известняковым, доломитовым, глинистым, мергелистым, кремни стым и др.). Аналогичная порода, но состоящая из угловатых обломков гор ных пород, носит название брекчии (рис. 2.6).
Скелет конгломератов и брекчий составляют чаще прочные, устойчи вые против выветривания породы (кварциты, граниты), иногда встречаются породы, состоящие из обломков плотных известняков, доломитов, змеевиков.
Качество конгломератов и брекчий зависит от минералогического соста ва, крупности и формы обломков, состава и степени уплотненности цемен тирующего вещества. Лучшими свойствами для строительных целей отлича’ются породы из прочных угловатых обломков, сравнительно небольших по размеру, имеющих малую пустотность и связанных прочным устойчивым цементом. Крупные месторождения конгломератов, брекчий и переходных между ними пород известны в районе
Симферополя, |
на Северном |
Кавказе, |
в Средней Азии. |
|
|
Осадочные |
породы органогенного |
|
происхождения |
образовались |
в ре |
зультате уплотнения и цементации от мерших организмов, отличаются зна чительной пористостью; многие раство ряются в воде. Свойства органоген ные пород, как и других осадочных, колеблются в широких пределах. В доро
жном строительстве используют карбонатные (известняки, мел, известняки-
ракушечники) |
и кремнистые (диатомиты, трепелы> опоки) органогенные |
осадочные породы. |
|
И з в е с т н я к и |
— горные породы, состоящие главным образом из углекис |
лого кальция |
(СаС03). В основном известняки — морского происхождения |
(уплотненные и сцементированные осадки отмеРших растительных и простей ших животных организмов) и лишь небольшая часть известняков образо валась в результате отложения углекислого кальция горячих источников
( и з в е с т к о в ы е т у ф ы ) .
По структуре и текстуре различают следующие разновидности извест няков: плотные, кристаллические, мраморовидные, пористые, оолитовые,
ракушечниковые, туфовые и землистые (мел).
Кроме углекислого кальция (кристаллического, зернистого и землистого строений), известняки обычно содержат незначительную примесь магнезита, а иногда кварца, глинистых, органических, железистых и других соедине ний. Под действием раствора соляной кислоты углекислый кальций разла гается с выделением С02 (так называемое «вскипание» известняков), остав ляя в осадке примеси. Этим способом обычно пользуются для определения известняковых пород, а также для определения количества примесей в них.
В зависимости от состава различают известняки доломитизированные (заметная примесь магнезита), глинистые (мергелистые), кремнистые, же лезистые, битуминозные и др. Цвет известняков в зависимости от примесей бывает белый, красноватый, зеленоватый; желтоватый, серый.
Технические свойства известняков разнообразны и зависят от состава, структуры и текстуры. Однородные плотные скрытокристаллические извест няки, зерна которых сцементированы кальцитом, отличаются высокой проч ностью (в среднем до 120 МПа), хорошей обрабатываемостью и сравни тельно небольшой истираемостью. Дополнительный кремнистый цемент по вышает прочность до 150 МПа и больше, но увеличивает хрупкость, твер дость и обусловливает гладкий, раковистый раскол. Примесь глинистого вещества заметно снижает качество известняка как строительного мате риала.
М р а м о р о в и д н ы е и з в е с т н я к и (переходные породы от известняка к мра мору) состоят из зерен кальцита, тесно связанных между собой небольшим количеством карбонатного цемента, а иногда и примесей. Прочность при сжатии их колеблется в пределах 90—150 МПа. Близки к ним по качеству мраморовидные доломитизированные известняки.
О о л и т о в ы е и з в е с т н я к и сложены из шарообразных зернышек углеро дистого кальция, сцементированных тем же известковым цементом. Иногда зерна располагаются неравномерно участками на общем фоне, состоящем из цементирующего вещества. Величина зерен от 1 до 5 мм, строение их ра диально-лучистое или скорлуповатое. Эти известняки отличаются значитель ной пористостью, малой прочностью и твердостью, слабой погодоустойчи востью.
И з в е с т н я к и - р а к у ш е ч н и к и состоят из известняковых ракушек различных моллюсков, по названию которых и дают наименования отдельным их разно видностям. Ракушки разного строения и величины сцементированы извест ковым цементом с большим или меньшим количеством разных примесеп (глинистых, органических веществ, кварца). Ракушечники характеризуются большой пористостью, крупными порами и пустотами, малой прочностью (0,4—0,5 МПа), малой объемной массой (600—15000 кг/м3), воздухопро ницаемостью, малой теплопроводностью и погодоустойчивостью. Они легко обрабатываются и поддаются распиловке. В связи с этим известняки-рак\ шечники применяют в виде блоков правильных форм для кладки стен.
Известняки используют преимущественно, как местный материал в виде бута, щебня, шашки для мощения, штучных блоков. Из плотных перекристаллизованных известняков изготовляют плиты, блоки и высокосортный щебень для дорожного строительства. Известняки используют также в производстве извести, цемента и др. Крупные месторождения известняков известны в Ле нинградской обл. (путиловские, волховские), Московской обл., на Украине,
вМолдавии, на Урале, в Крыму, Средней Азии.
Ме л представляет собой мягкую, землистого сложения слабосцементи-
рованную породу, |
состоящую на 60—70% из остатков известковых скелет |
ных образований |
планктонных организмов и мелких обломков кальцита. |
В качестве примесей в нем могут быть желваки кремния, фосфорита, квар |
|
цевые, а также глинистые вещества. Порода — полускального типа. Плот |
|
ные разновидности мела с заметным количеством примесей кремния приме |
няют как |
местный материал для устройства дорожных оснований и др. |
О п о к а |
— тонкопористая горная порода из сцементированного аморфного |
кремнезема, кристаллического кварца, кальцита, магнезита, органических веществ. Опоки бывают от темно-серого до светло-желтого цвета. Излом гладкий, раковистый, объемная масса 1200—1500, редко 1800 кг/м3, порис тость 30—40%, прочность при сжатии 10—30 МПа. Опоки, как правило, неморозостойки, и вследствие наличия коллоидного кремнистого цемента они, находясь на воздухе, самопроизвольно растрескиваются, превращаясь в мелкий угловатый щебень. Опоки обладают гидравлическими вяжущими свойствами и используются как активная добавка к цементу и, в частности, для приготовления известково-пуццолановых цементов.
Опоки залегают самостоятельными толщами, причем часто им сопутству ют опоковидные и другие песчаники и мергели. Крупнейшие месторождения опок известны в бассейне среднего и нижнего течения Волги, на восточных склонах Урала и др.
М е р г е л ь — порода смешанного происхождения из смеси карбоната каль ция и глинистых частиц. Содержание СаС03 колеблется от 25 до 75%. Поро да — полускального типа, используется как сырье для получения портланд цемента.
О с а д о ч н ы е п о р о д ы х и м и ч е с к о г о п р о и с х о ж д е н и я образовались в резуль
тате выпадения из растворов химических осадков. Наиболее распростра ненными являются доломиты, магнезиты, известковые туфы, гипс, ангидрит. Для осадочных пород химического происхождения характерны раствори мость в воде и в связи с этим наличие пустот и трещин.
Д о л о м и т — двойная углекислая соль кальция и магния CaMg(C03)2 (ми нерал доломит) с примесями глинистого, железистого, кремнистого и других веществ. Доломиты бывают зернистой, оолитовой и кристаллической струк туры. С соляной кислотой они «вскипают» только в тонкоизмельченном состо янии или при подогреве. Доломиты несколько тверже известняков. Плотные и окремнелые разновидности отличаются значительной прочностью и по вышенной погодоустойчивостью. В строительстве дорог их применяют на равне с известняками.
Известковые туфы — ноздреватая порода, в разной степени уплотне ния, образовавшаяся в результате выпадения углекислого кальция из источ ников. Обычно туфы имеют малую прочность, пористы, легко поддаются рас пиловке. Разновидности туфов, образовавшиеся в результате осаждения СаС03 из горячих источников (так называемые т р а в е р т и н ы ) , характеризу ются тонкопористым сложением и значительной прочностью (до 80 МПа). Травертины используют для кладки и облицовки стен. Менее прочные разно видности известкового туфа применяют для производства извести. Место рождения туфов известны в районе Ленинграда, Пятигорска и др.
Гипс состоит из минерала CaS04 • 2Н20 и примесей, используется как сырье для производства вяжущего и как добавка в производстве цемента.
Метаморфические горные породы образовались в результате изменения магматических и осадочных горных пород под влиянием высокой температу ры, давления, химически активных веществ. В результате метаморфизма первичные породы в большей или меньшей степени могут изменять текстуру, минералогический, а иногда и химический составы. Метаморфизация магма тических пород, как правило, ухудшает их физико-механические свойства. В процессе метаморфизма обычно происходит перекристаллизация и пе регруппировка составляющих их минералов с образованием полосчатых текстур. При переходе полосчатости в сланцеватость порода приобретает резкую анизотропию механических свойств: прочность параллельно сланце ватости резко падает. Метаморфизация осадочных пород, наоборот, улуч шает механические свойства. Вследствие пластичности минералов, входя щих в состав скальных пород осадочного происхождения (кальцит, доломит, гипс), процессы метаморфизма не вызывают в них появления заметной рассланцованности. Поэтому при метаморфизме скальных пород осадочного происхождения обычно образуются породы массовой текстуры и равно мерно зернистой структуры (мрамор).
Гнейсы — горные породы грубоили тонкосланцевато-й и ленточной (по лосчатой) текстур, получившиеся в результате видоизменения гранитов, гранодиоритов, кварцевых порфиров, некоторых конгломератов и других пород. Минералогический состав гнейсов может быть разнообразным, но ча ще они состоят из ортоклаза (ортоклазовые), авгита (авгитовые) и др.
В гнейсах минералы как бы сжаты и располагаются параллельно некото рой плоскости, что обусловливает неодинаковые их свойства в разных направлениях. Обычно гнейсы в направлении, перпендикулярном к сланце ватости, обладают значительной прочностью при сжатии (150—200 МПа), но наличие хорошо выраженной сланцеватости в ряде случаев несколько огра ничивает область применения их в дорожном строительстве. Способность от деляться от плоскости сланцеватости облегчает добычу и переработку гней сов, однако при разделении глыб получают куски плитообразной формы, а при дроблении на щебень образуется заметное количество плоских и вытя нутых щебенок (лещадки и пальцы), что снижает качество щебня. Чем ближе гнейсы по текстуре стоят к гранитам, тем выше их качество. Ленточные и полосчатые гнейсы — худшие их разновидности.
Гнейсы распространены в местах выходов магматических горных пород. Разработка месторождений гнейсов ведется в разных районах СССР (см. граниты). Гнейсы используют для изготовления щебня, бутового камня, шашки для мощения.
Кварциты — равномерно кристаллическая, плотная горная порода, сос тоящая из мелких зерен кварца, сцементированных кремнистым веществом. При этом цементирующее вещество трудно отличимо (без микроскопа) от зерен кварца. Кварциты характеризуются большой плотностью, прочностью, хрупкостью и твердостью, при разломе они образуют гладкую поверхность с острыми режущими ребрами. Кварциты весьма устойчивы против вывет ривания. Отрицательными признаками кварцитов являются трудная их об рабатываемость, гладкость поверхности раскола и острые ребра щебня. Кварциты используются для строительных работ в виде бутового камня, щебня, реже шашки для мощения. Из лучших его разновидностей изготов ляют штучный камень.
Мрамор — плотный кристаллический известняк, состоящий в основном из тесно сросшихся кристаллов кальцита (кальцитовый мрамор). Часто в мраморах наблюдаются примеси магнезита. Иногда эта примесь настолько
значительна, что порода носит название доломитового мрамора. В качестве второстепенных минералов в мраморах могут быть слюда, гранат, полевые шпаты, кварц, органические соединения. Цвет чистого мрамора — белый, но в зависимости от примесей он может быть крайне разнообразный: красный, розовый — от примесей железистых соединений и марганца, серый и чер ный от примесей органических веществ и др. При неравномерном распре делении примесей мрамор приобретает пеструю окраску с разными узорами (так называемый цветной мрамор). Кальцитовый мрамор характеризуется плотностью около 2700 кг/м3, твердостью 3—4, незначительной водонасыщенностью и прочностью при сжатии до 80 МПа. Доломитовый мрамор тверже и прочнее. Мраморы хорошо поддаются распиловке, обработке, шли фовке. Вследствие высоких технических свойств и красивого рисунка мрамор издавна применяют для различных отделочных и декоративных работ.
Недостатком мраморов является их относительно слабая сопротивляе мость выветриванию. Разновидности мрамора, непригодные для изготовле ния штучных изделий, а также отходы при обработке, дробят для получения мраморной крошки и порошка, которые применяют как заполнители в мозаичных работах и асфальтобетонах в качестве минерального порошка.
§2.5. ОБСЛЕДОВАНИЕ МЕСТОРОЖДЕНИЙ ГОРНЫХ ПОРОД
ИОПРЕДЕЛЕНИЕ ИХ КАЧЕСТВА
Скопления горных пород в земной коре, занимающие определенное про странство, называют месторождениями. Разрабатываемые месторождения скальных горных пород принято называть карьерами (разработками, ка меноломнями). Ценность месторождения зависит от ряда факторов, среди которых главнейшими являются: географическое положение, дальность и трудность транспортирования материала, условия и характер залегания горной породы, ее технологические свойства. Для выяснения пригодности породы и экономической целесообразности разработки месторождения про изводят его обследование (разведку), в результате которого должна быть получена общая технико-экономическая оценка месторождения.
Обследования месторождений горных пород бывают рекогносцировочные (предварительные) и детальные (полные). Рекогносцировочное обследова ние, в результате которого дается предварительная оценка месторождения, предшествует детальному обследованию. Последний вид обследования произ водят на основе точной топографической съемки территории, изучения месторождения при помощи шурфов, буровых скважин, расчисток, деталь ного изучения гидрологических условий, сбора ряда необходимых сведений на месте, отбора потребного количества проб породы и пр. Детальное обследование дополняет и уточняет результаты рекогносцировочного.
После тщательного изучения горной породы необходимо отобрать поле вые пробы для лабораторных испытаний и камерального изучения их. Пробы берут из господствующей и подчиненных свежих пород. Выветрелые слои должны быть также представлены образцами. Размер и количество проб зависит от однородности пород в месторождении и от целевого назначения проб. Для лабораторных испытаний пробы берут в таком количестве, кото рого было бы достаточно для производства испытаний. Для определения, например физико-механических свойств одна проба однородной породы должна состоять из двух кусков размером не менее 30x40x40 см. Проба должна отвечать среднему составу породы. Пробы выламывают при помощи клиньев и закольников по возможности без взрывных работ. В особо затруд ненных случаях допускается применение черного пороха.
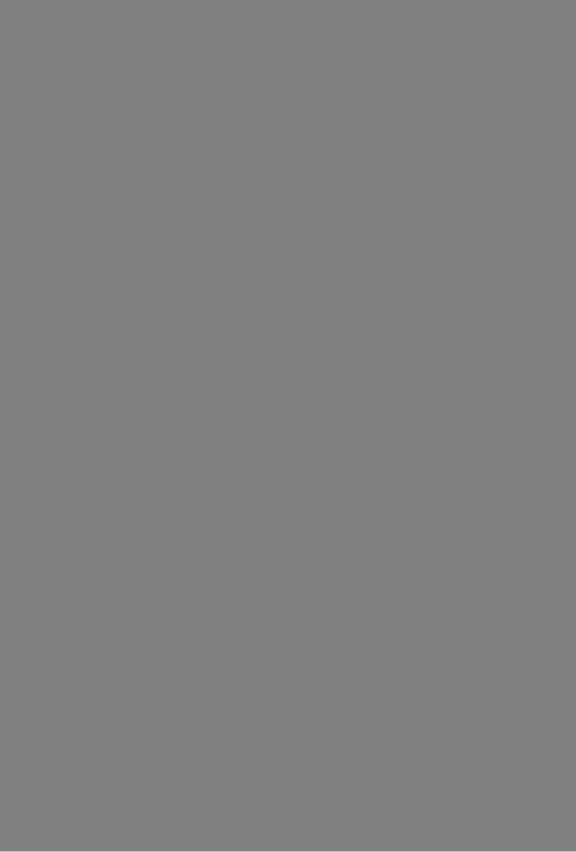
Если горная порода будет дробиться на щебень, она должна быть под вергнута пробному дроблению, при этом определяют качество получаемого щебня и количество отходов (смятогр) материала.
Буримость горных пород ориентировочно определяется твердостью, вяз костью и раздроблением минералов, составляющих породу.
В результате определения технологических свойств дается дополнитель ная характеристика горной породы. Учитывая целевое назначение породы, составляют описание внешних признаков и результаты технологической про бы и только после этого назначают программу выборочных или полных лабораторных испытаний для характеристики физико-механических свойств, горной породы.
При испытаниях определяют основные физико-механические свойства горных пород.
1. Плотность является характеристикой минералогического состава. Зна чение плотности необходимо для суждения о вещественном составе породы, для пересчета объема на массу горных пород и определения пористости.
2. Объемная масса характеризует состав, сложение горной породы и за висит от ее состава и плотности. Объемную массу рыхлых горных пород (гравия, песка) и дробленых (щебня) определяют как насыпную массу. Показатель объемной массы нужен для подсчета массы материала и от дельных элементов конструкций, для определения пустотности и др. Для стро ительных целей горные породы по объемной массе делят на легкие (объемная масса меньше 1800) и тяжелые (больше 1800).
3. Пористость определяет объем пор и микротрещин в единице объема и косвенно характеризует прочность, водопоглощение, теплопроводность, звукопроводность, морозостойкость и погодостойкость горной породы.
4. Водные свойства. Влажность определяет количество влаги по массе или объему (в процентах), поглощенной и удерживаемой горной породой в данный момент.
Водопоглощение характеризует количество воды, которое может погло тить и удержать образец горной породы молекулярными и капиллярными силами при нормальном атмосферном давлении.
По показателям водопоглощения различают горные породы:
Очень большого |
водопоглощения |
более 8% |
Большого |
« |
3 -8 % |
Среднего |
« |
1,5-3% |
Малого |
« |
0,5-1,5% |
Очень малого |
« |
менее 0,5% |
Водонасыщение — количество воды, |
которое могут поглотить образцы |
горной породы при вакууме. При таком способе насыщения вытесняется из открытых пор воздух и порода вследствие этого поглощает воды больше. Показатель водбнасыщения больше водопоглощения. Однако крупные по ры и пустоты, в которых вода не удерживается капиллярными силами, не
могут быть учтены водонасыщением.
Для суждения о возможном снижении прочности при увлажнении горной породы определяют коэффициент размягчения, который представляет от ношение показателя прочности при сжатии насыщенной водой породы к по казателю прочности сухого образца.
5. Морозостойкость — способность горной породы в водонасыщенном состоянии при попеременном замораживании (при —М-.— 20°С) и оттаива нии не проявлять признаков разрушения и не снижать прочность больше чем на 25%. Потеря в массе не должна быть более 5%.
Коэффициент морозостойкости вычисляется как отношение показателей прочности при сжатии образца породы в водонасыщенном состоянии до испы тания на морозостойкость и после испытания. Морозостойкость обозначают
Мрз.
Для строительных целей горные породы по степени морозостойкости — количеству циклов попеременного замораживания и оттаивания (без замет ных деформаций) делят на следующие группы:
Выдерживание |
не |
менее 10 |
циклов |
Мрз |
10 |
|
« |
« |
« |
15 |
« |
Мрз |
15 |
« |
« |
« |
25 |
« |
Мрз 25 |
|
« |
« |
« |
35 |
« |
Мрз 35 |
|
« |
« |
« |
50 |
« |
Мрз 50 |
|
« |
« |
« |
100 |
« |
Мрз |
100 |
« |
« |
« 200 |
« |
Мрз 200 |
6. Погодоустойчивость характеризует устойчивость горной породы против воздействия на нее атмосферных факторов (влаги, температуры, углекислого
газа, кислорода, воздуха и др.).
7 Прочность при сжатии горных пород определяется на образцах пра вильной геометрической формы (куб, цилиндр) и зависит от минералогичес кого состава, структуры, текстуры, степени выветрелости (свежести) и влаж
ности.
Наиболее прочны мелкокристаллические магматические и наименее прочны осадочные породы молодого возраста со слабой цементацией. По прочности при сжатии гордые породы бывают:
Очень прочные |
>120 МПа |
Прочные |
120—80 МПа |
Средней прочности |
80—60 МПа |
Слабые |
60—30 МПа |
Очень слабые |
<30 МПа |
О прочности горных пород можно судить по испытаниям образцов не правильной геометрической формы (щебенки) методом раскалывания между двумя взаимно направленными конусами (метод ХАДИ).
При этом получают приближенные показатели прочности при расколе, растяжении и сжатии:
р |
_ |
R раск = = -у? ’ ^ р а ст ^ |
раск ’ ^ сж= |
где /?раск — предел прочности при расколе, МПа; Р — разрушающее
усилие, Н; F — площадь раскола, см2; у — корреляционный коэффициент, равный 0,9—1,05; <р — коэффициент, равный 12—20 (зависит от размера об
разца).
8. Истираемость — способность каменного материала сопротивляться ис тирающим усилиям. Чем больше твердость, тем меньше истираемость. Мате риалы из мелкозернистых кварцевых пород обладают наименьшей истирае мостью. Показателем истираемости является потеря массы (г) образце) площадью 1 см2 за определенный путь (м).
9. Износ характеризует сопротивление материала истирающим и удар ным усилиям, обламыванию кромок.
По потере массы при износе (истирании) в полочном барабане щебень делят на:
Очень прочный |
<20% |
Прочный |
2 1 — 3 0 % |
Средней прочности |
3 1 - 4 5 % |
Слабый |
4 6 - 5 5 % |
Очень слабый |
> 5 6 % |
При расчете дорожных конструкций, оснований и фундаментов промыш ленных и гражданских зданий и других сооружений пользуются формула ми теории упругости, в которые входят такие параметры, как модуль упру гости Е, коэффициент Пуассона р, модуль сдвига g, характеризующие механические свойства горных пород.
Химические свойства горных пород определяют их химическое взаимо действие с окружающей средой (главным образом с теми веществами, ко* торые содержаться в воздухе и воде).
В ы б о р г о р н о й п о р о д ы связан с прогнозированием качества получаемого каменного материала. В табл. 2.1 приведена техническая характеристика скальных горных пород как исходного сырья для производства щебня, в ос нову которой положены показатели: состав, структурно-текстурные призна ки, выветрелость, шероховатость поверхности раскола и физико-механи ческие свойства.
§ 2.6. РАЗРАБОТКА МЕСТОРОЖДЕНИЙ И ПЕРЕРАБОТКА
ГОРНОЙ ПОРОДЫ
Для производства каменных материалов в карьере вначале отделяют скальную породу от массива, затем полученную горную массу подвергают переработке. Разрабатываемую горную породу называют полезным ископа емым. Породу, которую нельзя использовать для производства каменных материалов, называют пустой. Пустые пространства, образующиеся в породе в процессе добычи полезного слоя, называют в ы р а б о т к а м и .
Различают карьеры коренных месторождений, в которых разрабатыва ют сплошные скальные горные породы (граниты, известняки), и рыхлых горных пород (песков, гравия, валунного камня).
В зависимости от условий залегания, качества и запасов горных пород, географического расположения месторождения, карьеры бывают:
п р о м ы ш л е н н ы е с большими запасами доброкачественного полезного ис копаемого. Они территориально не связаны со строительными объектами, срок их действия более 10 лет, производительность более 100 000 м3 в год. Такие карьеры хорошо оснащены оборудованием, машинами, внутрикарьерными и подъездными путями. Готовую продукцию транспортируют железно дорожным транспортом, водными путями, а на сравнительно небольшие расстояния — автомобилями;
п р и т р а с с о в ы е местного значения, расположенные в районе строящихся объектов. Срок действия их менее 10 лет. Готовая продукция транспорти руется автомобилями. Себестоимость продукции притрассовых карьеров
обычно выше, чем |
промышленных. |
|
|
В зависимости |
от условий залегания разработка горных пород может |
||
вестись открыт ым |
с п о с о б о м , т. е. в открытых выработках, реже п о д з е м н ы м |
||
(разработка штольнями ракушечных известняков) |
или п о д в о д н ы м |
(порода |
|
залегает сравнительно неглубоко от поверхности |
воды в реке или |
озере). |
При выборе рационального способа разработки породы в карьере учиты вают ряд факторов, важнейшими из которых являются: гидрогеологичес кие условия района месторождения, качество вскрышных пород, способ транспортирования как сырцовой (необработанной) породы, так и готовой продукции. Для решения вопроса о виде каменной продукции, которую мож но получить в карьере, особое внимание обращают на прочность, твер дость и вязкость породы, ее структурно-текстурные особенности, технологи ческие свойства, характер трещин и их расположение, наличие выветрив шихся слоев.
Открытый способ горных работ в значительной степени зависит от рас положения пород, которые могут залегать горизонтально или иметь крутое либо пологое падение. В этих случаях порода может залегать выше, на уровне или ниже дневной поверхности. Обычно верхняя часть толщи покрыта покровными горными породами с выветрелыми слоями.
Выходы горных пород на дневную поверхность (обнажения) могут наблю даться на склонах долин, балок, берегов рек и пр. Для открытых работ наибо лее удобны выходы горных пород на склонах, так как в этом случае обычно бывает малая вскрыша, легче перемещать добытую породу вниз, а также нет затруднений с отводом атмосферных и грунтовых вод.
Разработка месторождения включает основные производственные про цессы; планировку местности и мероприятия по отводу атмосферных и та лых вод; вскрышные работы; разработку и удаление на отведенные пло щадки дресвяного (сильно выветрелого) слоя; отделение монолитов от мас сива; передвижение монолитов к месту дальнейшей переработки и их сорти ровку по качеству; развалку монолита на глыбы нужных размеров (габа ритный камень) и дальнейшую их обработку или переработку в заданный вид каменной продукции (колку, теску, дробление и др.); сортировку; транс портирование готовой продукции на складские площадки или на погрузку
В зависимости от условий залегания горной породы, ее прочности, тре щиноватости отделение породы от массива может производиться механи ческим способом (экскаваторами), который применяется при разработке осадочных горных пород, разбитых природными трещинами на сравнитель но небольшие отдельности. Массивные магматические горные породы, как правило, разрабатывают с применением взрывчатых веществ для получения грубоколотого каменного или дробленого материала.
При отделении глыб слоистых, трещиноватых, столбчатых пород приме няют механические средства (клинья, лопаты).
При добыче горных пород буро-взрывным способом в них бурят скважины или шпуры в один, два и более рядов вдоль фронта уступа. В горных породах средней прочности скважины и шпуры закладывают станками вращатель ного, а в прочных породах — ударно-вращательного бурения. В последние годы начали осваивать и термические (огневые) способы проходки сква жин, в частности прожигание скважин цилиндрической формы факелом из смеси керосина и кислорода, выбрасываемой со скоростью 2000 м/с из реактивной горелки при температуре до 3000°С. В результате такого тепло вого и механического воздействия горения порода разрушается.
Слабыми мягкие породы, например, ракушечные известняки, известня ковые туфы, добывают путем распиловки массива камнерезной машиной на блоки определенных размеров и правильной геометрической формы (про имущественно стеновой строительный материал). Известняки легче подвср гаются распиловке во влажном состоянии.
При разработке месторождений некоторых разновидностей гранитом, туфов, мраморов (в открытых выработках) на штучный камень (плиты, блоки) также применяют распиловку породы механическими пилами (напри
мер, пилы со стальными дисками, с пластинками твердых сплавов или с абразивными порошками).
Более эффективными по сравнению с дисками, армированными пласти нками из твердых сплавов, являются диски, на обод которых нанесена аб разивная масса из мелкозернистого карборунда, электрокорунда или шлифо вального порошка разной крупности. В качестве связующего материала в этом случае применяют разогретый жидкий бакелит, в который вводят 2—4% сухого строительного гипса (наполнитель).
Высокая производительность бурения и резания достигается при исполь зовании понизителей твердости и алмазного режущёго инструмента, для изго товления которого применяют природные или искусственные алмазы массой зерен от 0,5 до 1,5 карата.
Переработка горной массы. В зависимости от вида каменной продук ции, которую предполагают получить, отделенную от массива горную массу крупных (негабаритных) размеров подвергают переработке. Развалку-круп- ных глыб породы осуществляют взрывным способом или при помощи клинь ев. Раскалывать кувалдами можно сравнительно небольшие глыбы. По на меченной линии непосредственно кувалдой или через закольник наносят ряд сильных ударов до развала глыбы камня.
При помощи клиньев и взрывным способом монолиты разделывают путем предварительного-бурения ряда небольших шпуров глубиной 8—10 см или большей глубины (для крупных монолитов) на расстоянии 20—25 см один от другого в зависимости от колкости породы. В подготовленные шпуры вставляют две щечки, а между ними клинья, которые последовательно забивают молотком.
Для развалки монолита взрывным способом (слабыми взрывами) шпуры делают глубже (до 50 см), но в меньшем количестве, а для сравнительно небольших монолитов может быть только один шпур, который бурят перфо раторами. Разметка монолитов для высверливания шпуров — важный про цесс при их разделке, так как от нее зависит правильность кусков и коли чество отходов.
Раскалывание крупных монолитов (более 5 м3) при помощи взрывчатых веществ допускается с ограничением для того, чтобы взрывы не вызывали дробления монолита. Если предполагается получить грубоколотый матери ал (бут, шашку для мощения), указанное ограничение не служит сущест венным препятствием при раскалывании монолитов. Для изготовления бор товых камней, плит, блоков на промышленных карьерах используют распи ловочные станки, производительность которых достигает 1,6 м2/ч для грани тов и 8 м2/ч для мраморов.
Для дальнейшей разделки и обработки полученный каменный материал транспортируют на специально предназначенные для этой цели площадки или к месту погрузки. Транспортирование осуществляется при помощи лот ков, бремсбергов, канатных дорог, автомобилей и т. д.
Из скальных пород изготовляют щебень, бутовый камень, шашку для мощения, шашку пакеляжную, бортовой камень, брусчатку, блоки, камен ную муку.
Щебень представляет собой смесь угловатых обломков размером 5—70 мм, полученных в результате дробления скальных горных пород, и при меняется для получения щебеночных конструктивных слоев, асфальто-, пласт- и цементобетонов.
Природный щебень образуется в результате физико-механического вы ветривания скальных горных пород и отложений на месте своего образова ния, состоит из обломков горных пород в той или иной стадии выветрива ния и содержит разное количество землистых примесей.
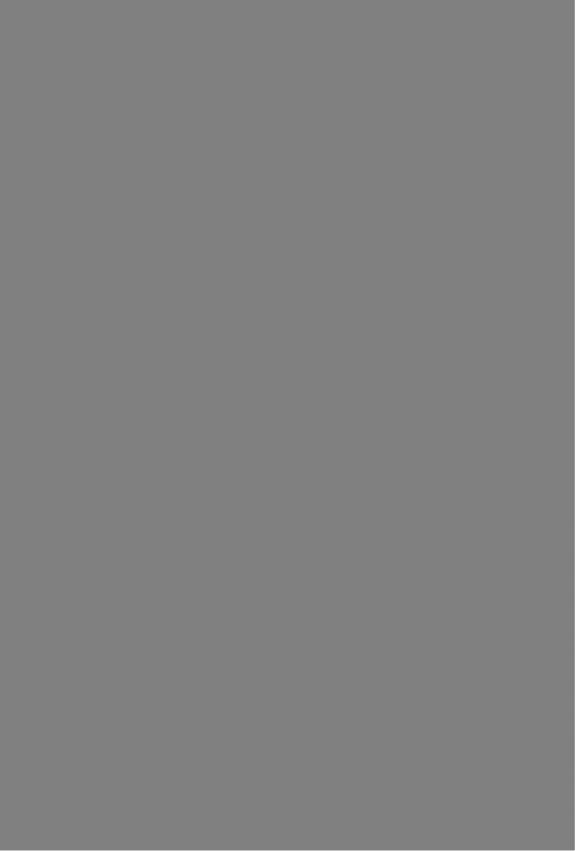
ных пород) или со смятой поверхностью (раздробленные зерна), а также некоторое количество смятой мелочи — отходов. Содержание зерен по крупности и смятой мелочи зависит не только от свойств исходной горной породы, но и от принятой технологии дробления. Для получения щебня повышенного качества, однородного по прочности и улучшенной формы, применяют обогащение — избирательное дробление, обогащение по прочнос ти, по форме зерен и др.
При избирательном дроблении в дробилках-грануляторах улучшение формы зерен происходит вследствие разрушения слабых зёрен и примесей, что дает возможность удалить их при последующем «грохочении.
При наличии разнопрочного щебня в необходимых случаях прибегают к разделению по прочности предварительно отгрохоченного щебня в класси фикаторах.
Значительно улучшить качество щебня можно путем повышения актив ности поверхности зерен.
Обработка зерен поверхностно-активными веществами повышает сцеп ление их с вяжущими веществами или придает зернам щебня водоотталки вающие свойства.
Щебень по крупности зерен для дорожного строительства делят на сорта (щебень размером 70—150 мм называют гигантским):
Крупный |
70—40 мм |
|
Средний |
40—20/25 мм |
|
Мелкий |
20/15—10/15 мм |
|
Клинец |
10/15—5 мм |
|
Высевки (или искусственный дробленый песок) |
< 5 |
мм |
Качество щебня, т. е. степень соответствия |
показателей |
его признаков |
и свойств проектируемому назначению, определяют в карьере |
(на месте его |
|
производства) и на месте его потребления (на строительном объекте) путем |
изучения внешних признаков и испытания отобранных проб. При этом опреде ляют петрографические признаки и однородность горной породы, из которой получен щебень: крупность, зерновой состав, форму зерен (количество лещадных и игольчатых зерен); шероховатость поверхности; количество и ка чество примесей (глинистых, органических и др.); количество смятых (раз дробленных) зерен; физические свойства (плотность и объемную массу, пустотность, влажность, водопоглощение, морозостойкость); механические
свойства (прочность при расколе, растяжении, ударе, |
раздавливании в ци |
линдре, износ в барабане). |
|
Таблица 2.6 |
Таблица 2.7 |
Износ (потеря массы при испыта нии), %
Марка щебня |
Известняки, |
Изверженные, |
ме |
Марка щебня |
|
таморфические |
и |
|
|
|
доломиты |
другие осадочные |
|
|
|
|
юроды |
|
|
И-1 |
<30 |
<25 |
|
1200 |
и - н |
31—40 |
26—35 |
|
1000 |
|
800 |
|||
и - ш |
41—50 |
36—45 |
|
600 |
|
400 |
|||
И -IV |
51—60 |
46—55 |
|
300 |
|
|
|
|
200 |
Дробнмость щебня (потеря массы при испытании), %
сухого ^
ч- |
<6 |
<9 |
ОО |
10—11 |
|
|
1 |
12—14 |
9—10 |
||
11 — 14 |
15—18 |
|
15—24 |
19—28 |
|
25—28 |
29—38 |
|
29—35 |
39—54 |
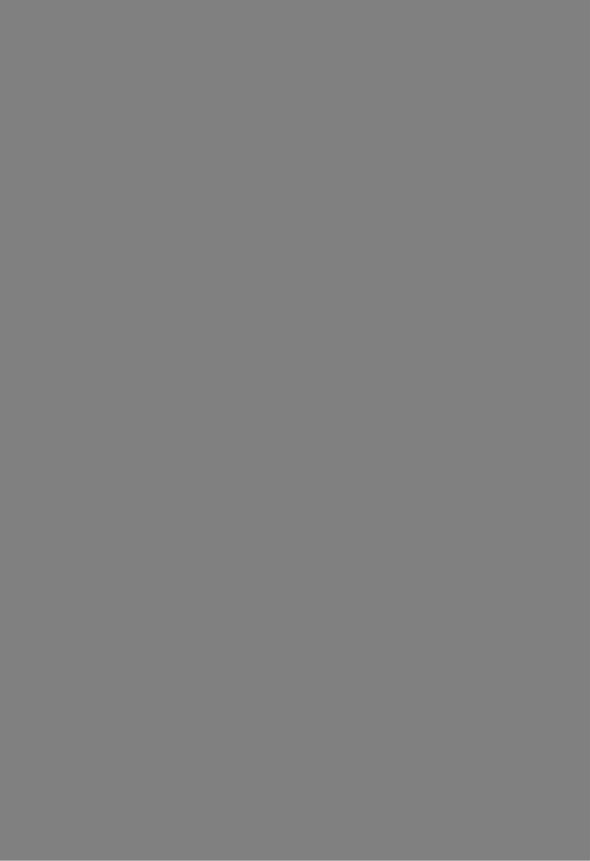
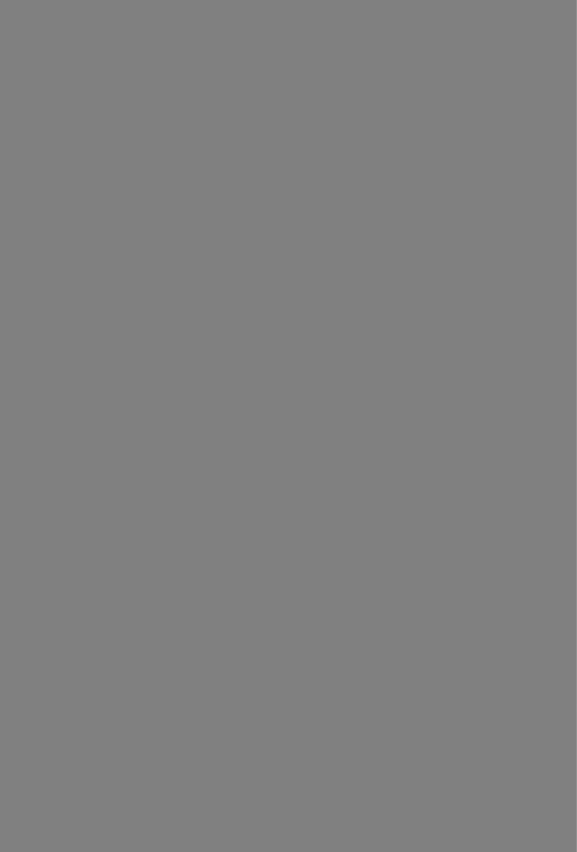

шлифовке и полировке при помощи шлифовальных станков. Шлифовка кам
ня производится чугунным бруском или диском с подсыпкой стального илй корундового порошка.
Абразивы или материалы, служащие для резки, шлифовки и полировки, могут быть природные и искусственные. Природные абразивы — кварц, корунд, наждак, алмаз, искусственные — карборунд, алунд, стальмасса.’ Кварц применяют в виде чистого кварцевого песка крупностью до 1 мм. Корунд — минерал, состоящий в основном из кристаллической окиси алюми ния. Наждак содержит 20 50% зерен корунда в тесной связи с магнетитом. Карборунд — сплав углерода и кремния при 1900—2200°С, состоит из карби да кремния, по твердости несколько выше корунда. Алунд (искусственный корунд) по составу аналогичен корунду и получается электроплавкой, поэто му иногда носит название электрокорунда. Стальмассу получают из каленой углеродистой стали и чугуна с последующим дроблением их на станках.
Для ускорения шлифовки применяют шлифовальные круги и бруски. Обычно работы по шлифовке и полировке состоят из ряда последовательных
операций: обдира (грубая шлифовка), шлифовки, лощения (тонкая шлифов ка), мастичения и полировки.
Обдир ведут мокрым способом при помощи тонкого слоя шлама и отходов стальмассы. В процессе грубой шлифовки поверхность камня смазывают свежей стальмассой или ее отходами, шлифуют зерновым абразивом (корун дом или карборундом) с периодическим увлажнением. Окончательная обра ботка ведется пемзой или карборундовым кругом (бруском). Тонкую шлифов ку производят тонким зерновым абразивом. После лощения перед полировкой поверхность камня мастичат путем закрытия мелких дефектов шеллачной мастикой горячим способом. Полировка достигается путем накатки тщатель но промытой поверхности полирующими порошками при помощи войлочных полировальных дисков. В качестве полирующих порошков применяют окись олова, окись железа, свинцовые опилки, азотистокислое олово и др.
§ 2.7. ПРЕДОХРАНЕНИЕ КАМЕННЫХ МАТЕРИАЛОВ ОТ КОРРОЗИИ
Многократное увлажнение и высыхание, замерзание и оттаивание, влия ние воздуха, биосферы, минерализованных вод ослабляют кристаллизацион ные связи в горной породе, разрушают неустойчивые минералы, выщелачива ют растворимые соединения. В результате в материале образуются микро трещины, минералы утрачивают блеск, появляются затеки новообразований и порода постепенно разрушается. Чем больше внешняя и внутренняя (поры, микротрещины, каверны) поверхности материала, больше погодонеустойчи вых минералов и шероховатость поверхности, тем интенсивнее протекает кор розия.
Материалы из карбонатных пород (известняков, доломитов, мраморов), а также из пород крупнокристаллической и пегматитовой, порфировой струк тур, сланцеватой текстуры с неустойчивым природным цементом менее погодоустойчивы, быстрее корродируют.
Элементы сооружений из крупных блоков, плит, находящиеся под воз действием перечисленных факторов среды, в необходимых случаях защища ют от коррозии различными способами. Прежде всего каменный материал следует поставить в такие условия, чтобы устранить или уменьшить соприкос новение его поверхности с факторами среды.
Устранение в конструктивном элементе выступов, придание каменному материалу гладкой или полированной поверхности, кольматация пор в значи тельной мере увеличивают погодоустойчивость. Для кольматации пор
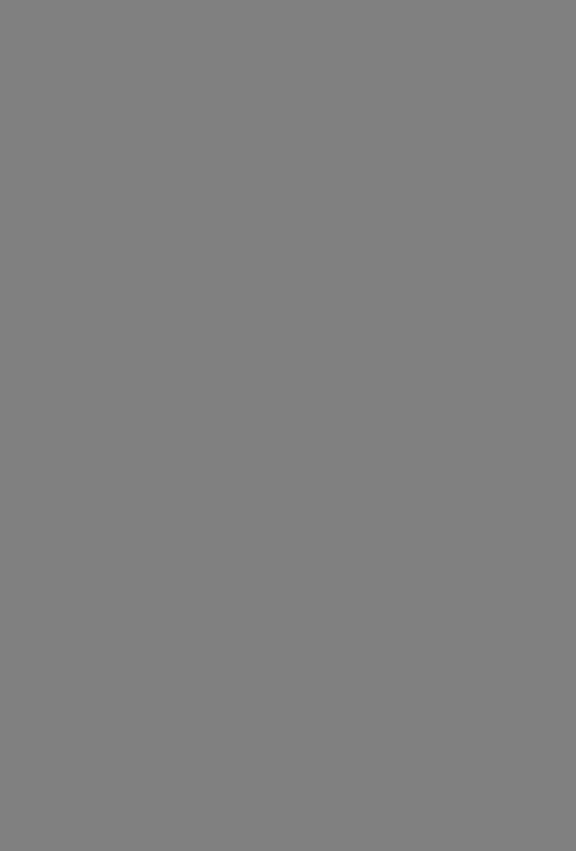
Г л а в а 3
ИСКУССТВЕННЫЕ КАМЕННЫЕ ОБЖИГОВЫЕ МАТЕРИАЛЫ
ИИЗДЕЛИЯ
§3.1. КЕРАМИЧЕСКИЕ МАТЕРИАЛЫ И ИЗДЕЛИЯ
Керамическими называют искусственные каменные строительные мате риалы, полученные в процессе обжига предварительно сформированных изле лий из глинистого сырья с добавками. К керамическим относят материалы и изделия из другого сырья, полученные по аналогичной технологии напои мер динас, где сырьем являются чистые кварциты, высокоогнеупорные мате риалы из чистых окислов, теплоизоляционные керамические изделия
диатомитов и трепелов и др.
Классификация керамических изделий основана на свойствах изделий
особенностях сырья и технологии производства.
По структуре различают грубую керамику, имеющую в изломе грубозео нистое строение, и тонкую с тонкозернистым строением и преимущественно
белым черепком. J
По степени спекания и плотности изделия грубой и тонкой керамики делят на пористые с водопоглощением черепка более 5% и плотные (спекшиеся! с водопоглощением ниже 5%. Например, к пористым изделиям грубой кепа мики относят все стеновые, фасадные и кровельные керамические материалы к плотным — клинкерный кирпич, плитку для полов. К пористым изделиям тонкой керамики относят фаянсовые изделия, к плотным — фарфоровые
Различают строительную, огнеупорную, кислотоупорную, тонкую и спе циальную керамику. Изделия строительной керамики, кроме этого классифи цируют по назначению, например стеновые, дорожные, фасадные и до В табл. 3.1 приведена классификация строительной керамики, учитывающая
все эти признаки.
§ 3.2. СЫРЬЕВЫЕ МАТЕРИАЛЫ
Для производства керамических изделий используют сырьевые смеси, состоящие из пластичного или основного сырья (глины, каолина) и неплас тичного или добавочного материала, к которым относятся отощающие и
выгорающие добавки, плавни.
Глины их состав и свойства. Глинами называют осадочные горные поро ды образовавшиеся в результате глубокого выветривания (разрушения под воздействием физических, химических и биологических процессов) пылевато шпатовых горных пород - гранитов, порфира, пегматита, сиенита, гней-
С3 Первичные или элювиальные глины отлагались на месте своего образова ния Они содержат примеси остатков пород, из которых произошли (хрящ, кварцевый и полевошпатный песок и др.). Вторичные (переотложенные или осадочные) глины перемещались водой, ледниками, ветром и отлагались на более или менее отдаленных местах от формирования первичных глин. Гостав глин при этом резко изменялся. Такие глины более дисперсны, обычно не содержат грубых примесей материнских пород, но часто засорены примеся ми песка известняка, железистых соединении и др. Глины ледникового проис хождения (моренные) засорены каменистыми включениями. Метаморфизиро-
Изделия строи |
Пористые с водомоглошсннем |
Плоти с (спекшиеся) с водопоглошсиисм |
||||
тельной керамики |
|
более 5% |
|
менее 5% |
||
Грубой |
(^теновые: кирпич полнотелый, пус- |
Дорожные: клинкерный кирпич, тро |
||||
|
тотный, пористый, лицевой; керамиче- |
туарная плитка |
|
|||
|
ские камни, виброкерамические па- |
Изделия для полов: плитки, ковро |
||||
|
нели из кирпича и камней |
|
вая мозаика |
подземных сооруже |
||
|
Фасадные: плиты и плитка глазу- |
Изделия для |
||||
|
рованные и неглазурованные; ковро |
ний: канализационные трубы |
||||
|
вая мозаика |
|
|
Заполнитель |
для асфальтобетонов: |
|
|
Кровельные: неглазурованная и гла- |
|||||
|
зурованная |
черепица |
|
керамдор |
|
|
|
Изделия |
для |
перекрытий: специ |
Санитарно-строительные изделия из |
||
|
альные камни, балки и панели из них |
фарфоровых и полуфарфоровых масс: |
||||
|
Изделия |
для |
подземных |
сооруже |
умывальники, бачки и др. |
|
|
ний: дренажные трубы |
|
|
|
||
|
Теплоизоляционные: ячеистая кера |
|
|
|||
|
мика; изделия из диатомита и трепела |
|
|
|||
|
Заполнители |
для легких |
бетонов: |
|
|
|
Тонкой |
керамзит, аглопорит |
|
|
|
||
Санитарно-строительные изделия из |
|
|
||||
|
фаянсовых масс: умывальники, бачки, |
|
|
|||
|
унитазы и др. |
|
(для внут |
|
|
|
|
Облицовочная керамика |
|
|
|||
|
ренних стен): |
фаянсовая |
плитка, |
|
|
плинтусы, доборные детали
ванные глины образовались в результате видоизменения первичных и вторич ных глин и находятся в камнеподобном состоянии (глинистые сланцы, суха ри, аргиллиты). В природе наиболее распространены вторичные (переотложенные глины).
Глины состоят из глинообразующих минералов и примесей, из одного (мономинеральные глины) или нескольких минералов (полиминеральные глины). Глинообразующие минералы являются водными алюмосиликатами, общая формула которых пА\2Оъ • mSi02 • рН20, где коэффициенты я, т , р зависят от вида глинообразующего минерала. Согласно современным пред ставлениям, кристаллические глинистые минералы состоят из чередующихся тетраэдрических кремнекислородных (Si04) и октаэдрических гидроалюминатных (А106) слоев. Сочетания слоев создают элементарный пакет, а связь между отдельными пакетами обусловливается зарядами наружных слоев па кетов.
Каолинит А120 3 • 2Si02 • 2Н20 и его аналоги, а также галлуазит по строены по сочетанию слоев 1:1. Разноименные заряды наружных слоев пакета обусловливают относительно плотную кристаллическую решетку с не большим межплоскостным расстоянием. Благодаря такому строению каоли нит обладает малой адсорбционной способностью и пластичностью, слабо набухает в воде и малочувствителен к сушке и обжигу.
Монтмориллонит Al20 3(Mg0, Fe20 3) • 4Si02 • Н20-ЬяН20 и иллит (гид рослюды) построены по сочетанию 2:1, где пакет кристаллической решетки состоит из двух наружных тетраэдрических и одного внутреннего октаэдри ческого слоев. Таким образом, смежные слои пакетов заряжены одноименно и связь между ними относительно слабая. Поэтому монтмориллонит погло щает значительное количество воды при увлажнении, набухает с увеличением объема до 16 раз и медленно отдает воду при подсушивании. Иллит по свойст вам занимает среднее положение между каолинитом и монтмориллонитом В зависимости от преобладающего содержания глинистых минералов глины
называют каолинитовыми, монтмориллинитовыми, гидрослюдистыми (иллитовыми) и т. п. Глины белого цвета, состоящие преимущественно из каоли нита, называют каолинами. Кроме глинообразующих минералов, присут ствуют примеси: кварцевый песок, карбонатные, железистые, органические, растворимые соли.
По зерновому составу глины характеризуются значительным содержани ем глинистого вещества (частиц мельче 0,005 мм) и делятся на высокодиспер сные, дисперсные и грубодисперсные.
В керамической промышленности по применению различают глины клин керные, кирпичные, черепичные и т. д.
Свойства глин определяются соотношением, видом и дисперсностью глинистых минералов и примесей. Наиболее важными свойствами глин явля ются пластичность, воздушная усадка (дообжиговые свойства), огнеупор ность, спекание и огневая усадка (обжиговые свойства).
Пластичность глин — способность глиняного теста изменять форму без разрыва и нарушения сплошности под действием внешних усилий и сохранять приданную форму после прекращения их действия. Пластичными свойствами каждая глина обладает в определенном диапазоне влажности. Пластичность зависит от вида и количества глинообразующих минералов в глине.
Наибольшей пластичностью обладают монтмориллонитовые глины. Повы шение дисперсности глин увеличивает их пластичность, запесоченность, на оборот, снижает ее.
Пластичность глин может быть повышена путем добавления пластичных глин или отмучивания песчаных частиц. Снижают пластичность введением непластичных добавок.
Воздушная усадка — уменьшение объема образца при его сушке. При затворении глин водой происходит набухание, т. е. увеличение объема. Удаление из глин воды сопровождается воздушной усадкой в результате действия капиллярных сил. Величина относительной воздушной усадки может быть от 2 до 10% и более. Наибольшей усадкой обладают монтмориллонито вые глины, наименьшей — каолинитовые. Примеси песка или добавки не пластичных материалов снижают воздушную усадку. Кроме этого, воздушная усадка зависит от начальной влажности, размеров и режимов сушки образца. Неравномерная усадка приводит к растрескиванию и искривлению изделий.
При обжиге в глине протекают сложные физико-химические процессы, результатом которых является формирование наиболее важных свойств кера мических материалов — прочности, водостойкости и др. В период прогрева глин испаряется свободная и физически связанная вода, при температуре выше 300°С начинается выгорание органических примесей, в интервале 450— 600°С — дегидратация каолинита, сопровождающаяся потерей пластич ности. Примеси кварца при 573°С претерпевают модификационное превраще ние с увеличением объема, что приводит к возникновению внутренних напря жений. Дальнейшее разложение каолинита происходит при 700—800°С с об разованием аморфного кремнезема. В этом же интервале температур начина ется спекание за счет реакций в твердой фазе, а затем с участием жидкой фа зы и образованием соединений, повышающих показатели физико-механи ческих свойств изделий. Образование жидкой фазы начинается при темпера туре выше 700°С в результате взаимодействия амфорного кремнезема с окис лами щелочных металлов. С повышением температуры количество жидкой фазы растет, в ней частично оплавляются зерна кварца. Диссоциация приме сей карбонатов происходит около 900°С по реакции СаС03-^СаО + С02
и |
также |
способствует накоплению жидкой фазы. При нагревании вы |
ше |
900°С |
образуется минерал муллит ЗА120 3 • 2Si02, который повышает |
прочность, |
термостойкость, ударную вязкость керамических материалов. |
В процессе обжига изделий строительной (грубой) керамики спекание в основном происходит за счет жидкостного спекания, а количество жидкой фазы при обжиге плотных керамических изделий может доходить до 60%. Образовавшийся стекловидный расплав обволакивает нерасплавившиеся зерна кварца. В результате сил поверхностного натяжения зерен массы сближаются — происходит огневая усадка.
Огнеупорностью называют способность глин, не расплавляясь, выдержи вать действие высоких температур. По.огнеупорности глины делят на три класса: огнеупорные — с огнеупорностью выше 1580°С, тугоплавкие-^ 1580—1350°С, легкоплавкие— ниже 1350°С.
Огнеупорность глин зависит от химического состава. Повышенное содер жание глинозема (А120 3) увеличивает огнеупорность. Окислы щелочных и щелочно-земельных металлов являются плавнями и снижают огнеупорность глин. Кварц практически не участвует в создании жидкой фазы, поэтому крупнозернистый кварц повышает огнеупорность.
Способность глин при обжиге уплотняться с образованием камнеподобно го материала называется спекаемостью и характеризуется интервалами спекания и спекшегося состояния (рис. 3.1).
Легкоплавкие глины, как правило, имеют узкий интервал спекания, и ин тервал спекшегося состояния у них практически отсутствует. Тугоплавкие и огнеупорные глины имеют широкий интервал спекания (180—200°С и бо лее), что и определяет возможность получения из них плотных спекшихся изделий с водопоглощением меньше 5%. Повышенное содержание в глине карбонатных примесей резко сужает интервалы спекания и спекшегося состояния.
В процессе спекания масса уплотняется, вследствие чего происходит огне вая усадка, которая у глин колеблется от 2 до 8%. С увеличением содержания глинистых минералов, окислов щелочных и щелочно-земельных металлов огневая усадка растет, примеси кварца ее уменьшают. Запесоченные глины имеют малую огневую усадку, а иногда увеличиваются в размерах.
Добавочные непластичные материалы. Для регулирования свойств кера мической массы вводят добавки.
Отощающие добавки уменьшают воздушную и огневую усадку, снижают пластичность глин. В качестве отощающих добавок применяют кварцевый песок .(для стеновых изделий размером от 0,2 до 2 мм), молотый шлак, отходы
|
|
|
|
|
|
керамзитового и аглопоритового произ |
|||||
|
|
|
и |
|
|
водства, золу до 10—25%. Более ка |
|||||
|
|
|
|
|
чественными отощающими |
добавками |
|||||
1 |
|
|
|
|
|
являются молотая дегидратированная |
|||||
|
|
|
|
|
глина |
(прошедшая |
термообработку |
||||
|
|
|
|
л5 |
|
при 700—750°С), |
шамот |
(измельчен |
|||
I |
|
|
|
|
ная специально обожженная глина при |
||||||
I |
|
|
|
в ) \ >с |
температуре, равной |
температуре об |
|||||
|
|
|
жига изделия), измельченный бой обо |
||||||||
|
|
|
|
|
|
жженных изделий. Их вводят в коли |
|||||
|
|
|
|
|
|
честве до 40%. |
|
или |
|
выгораю |
|
|
800900 т о 1100 1200 1300 |
Порообразующие, |
|
||||||||
|
|
|
Температура, °С |
щие, добавки применяют для уменьше |
|||||||
Рис. 3.1. Зависимость водопоглощения |
ния объемной массы стеновой керамики |
||||||||||
и сокращения расхода полноценного |
|||||||||||
керамического материала от |
темпера |
топлива; на этапе сушки они выполняют |
|||||||||
|
|
|
туры обжига: |
|
|||||||
/д — температура начала |
спекания; |
— темпе |
роль отощающих |
добавок. В |
качестве |
||||||
ратура, при |
которой нодоиог лошенне |
материала |
выгорающих добавок |
применяют дре |
|||||||
5%; |
— температура, выше которой отмечаются |
||||||||||
признаки |
пережога; tд |
— интервал спека |
весные |
опилки |
(8—25%), |
молотый |
|||||
ния; |
/ JJ |
/JJ |
интервал |
спекшеюся |
состояния |
|
|
|
|
|
|
антрацит, кокс, бурые угли, тощие каменные угли (2—2,5%), золы ТЭС до 15% и др.
Плавни-добавки в смеси с глинистым веществом дают легкоплавкие соединения и снижают температуру обжига изделий. В качестве плавней ис пользуют измельченные полевые шпаты, нефелиновые сиениты, пегматиты, перлиты, молотое легкоплавкое стекло, шлаки, фосфаты натрия и каль ция и др.
Пластифицирующие добавки увеличивают пластичность и связанность глин. К таким добавкам относят высокопластичные глины, бентониты, поверхностно-активные вещества — отходы целлюлозной промышленности (сдб), синтетических жирных кислот и др.
§3.3. ПРОИЗВОДСТВО КЕРАМИЧЕСКИХ ИЗДЕЛИЙ
Технология керамических изделий, несмотря на их широкий ассортимент, различные физико-механические свойства и виды сырья, имеет общие основ ные этапы: добыча и транспортирование сырьевых материалов, подготовка формовочной массы, формование, сушка, обжиг изделий.
Глинистое сырье разрабатывают открытым способом экскаваторами или скреперами. Для транспортирования глин используют автомобильный или рельсовый транспорт. Легкоплавкие глины — местное сырье, и карьер входит в состав керамического производства. Огнеупорные и тугоплавкие глины — привозное сырье, которое разрабатывают и поставляют специализи рованные организации.
Подготовка формовочной массы заключается в выделении каменистых включений, разрушении природной текстуры глин, измельчении, введении добавок', корректировании влажности и гомогенизации массы.
На современных заводах механической обработке глин предшествует естественная, которая происходит в результате вымораживания и вылежива ния глин в увлажненном состоянии.
При длительном воздействии погодно-климатических факторов техноло гические свойства глин значительно улучшаются. Естественную обработку совмещают с добычей глин.
Для получения пластической формовочной массы влажностью 18—23% из глин удаляют каменистые включения на дезинтеграторных ребристых вальцах, винтовых камневыделительных кольцах или г-линоочистителях. Затем производят грубое измельчение глин глинорыхлителями, вальцами с гладкой или рифленой поверхностью, зубчатыми или дезинтеграторными вальцами.
ОтошаюЩие добавки в зависимости от состояния вводят в процессе грубо го измельчения сырья или непосредственно в смеситель. В последнем случае смешивание совмещают с увлажнением массы паром или горячей водой, что интенсифицирует набухание глин. Полученная масса подвергается тонкому измельчению и дальнейшему смешиванию на бегунах, гладких дифферен циальных или дырчатых вальцах, глинопротирочных машинах (рис. 3.2). Корректирование влажности и гомогенизация пластической формовочной массы осуществляются в глиномялке (рис. 3.3).
При подготовке пресс-порошков влажностью не более 7—12% массу пере рабатывают сухим (сушильно-помольным) или мокрым (шликерным) спосо бом. Если в состав шихты входят один-два компонента, удовлетворительное качество пресс-порошка можно получить по сухому, более дешевому способу, который заключается в подсушивании и измельчении пластичного сырья, помоле добавок, смешивании их и увлажнении полученного пресс-порошка.
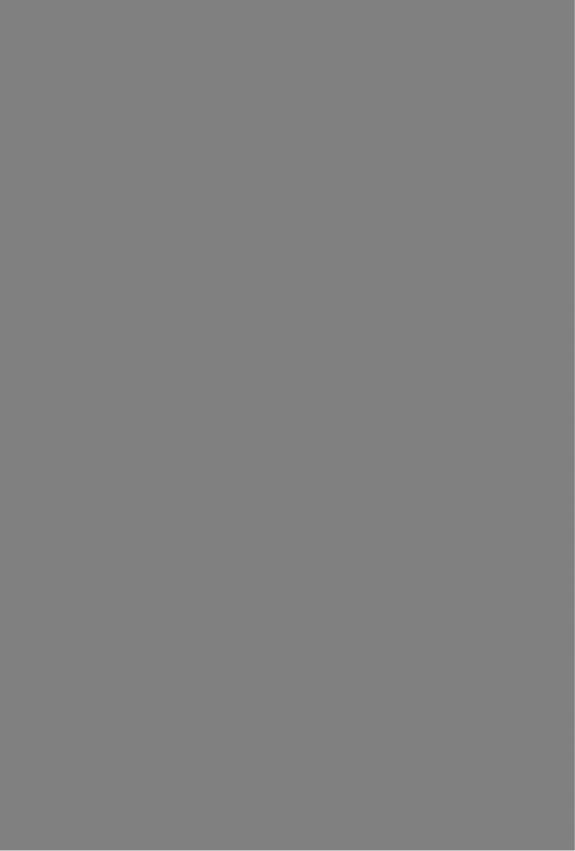
Рис. 3.3. Двухвальцовая глиномялка:
/ — патрубок для переработанной глины; 2 — ведомый вал; 3 — лопасть; -/ — большая шестерня; 5 — рабочий шкив; 6 — холостой шкив; 7 — приводной вал; 8 — малая шестерня; 9 — зубчатая передача; 10 — ведущий вал; // — корыто
и попадает на формующий шнек 6 пресса. С помощью.шнека масса уплотняет ся и перемещается в головку пресса <9и в мундштук 9, где приобретает требуе мую форму и выходит в виде сплошного бруса. Для формования рядового глиняного кирпича (полнотелого) мундштук имеет плавно сужающееся к вы ходу прямоугольное отверстие. Для формования пустотелых изделий исполь зуют мундштуки с кернами, благодаря которым в глиняном брусе образуются пустоты. Выходное отверстие мундштука имеет размеры несколько большие, чем размеры готового изделия, учитывая воздушную и огневую усадку сырца.
Выходящий из мундштука ленточного пресса глиняный брус разрезает ся резательными автоматами на отдельные кирпичи. Производительность ленточных прессов достигает 10 000 шт. кирпича-сырца в час.
При полусухом и сухом способе формования используют пресс-порошки влажностью соответственно 8—12 и 2—8%. Этот способ позволяет приме нять глины пониженной пластичности. Полусухим способом формуют в основ ном изделия, имеющие простую геометрическую форму и небольшую толщину (кирпич, клинкерный кирпич, фасадные плитки, плитки для полов, облицо вочные плитки для внутренних помещений и др.). При формовании полусу хим и сухим способами частицы пресс-порошка должны располагаться воз можно плотнее друг к другу, а промежутки между ними заполняться коллоид ным глинистым веществом. Поэтому необходимо, чтобы на первой стадии уплотнения произошло перемещение зерен порошка и максимальное удаление воздуха, а на второй развились пластические деформации частиц. Для дости-
жения этих условий используют прес сы, обеспечивающие двустороннее ступенчатое приложение нагрузки: первая ступень — 4—6, вторая— 15— 40 МПа. Формуют керамические, строи тельные изделия из npedc-порошков на механических (коленно-рычажных, ротационных, фрикционных) и гидрав лических прессах. Наибольшее распро странение получили коленно-рычаж ные прессы производительностью от 2000 до 10 000 шт.
Гидростатический способ прессова ния из полусухих порошкообразных масс в настоящее время внедряется в производство. Он основан на передаче
давления жидкостью через гибкую пресс-форму (например, резиновую). Максимальное давление прессования достигает 20 МПа. По этому способу можно формовать изделия более сложной формы.
Метод полусухого и сухого прессования обеспечивает правильную форму и точность размеров изделий. Ввиду малой влажности формовочной массы процесс сушки значительно упрощается или вообще отсутствует. Однако при этом способе для обеспечения необходимой степени спекания температура обжига на 40—50°С выше по сравнению с температурой обжига изделий пластического формования.
Формование изделий способом литья (шликерный способ) менее распро странен в технологии строительной керамики и используется при производ стве санитарно-строительных изделий (умывальники, мойки, унитазы) и тон костенных (до 2 мм) облицовочных глазурованных плиток. Способ менее производителен, чем пластический или полусухой, но позволяет изготавли вать изделия любой сложной конфигурации. Использование механизирован ного оборудования (литейно-подвялочных конвейеров и- др.) позволяет значительно повысить производительность литьевого способа формования.
Сушка изделий производится до остаточной влажности 2—5% и необхо дима для предотвращения деформаций и растрескивания сырца в результате быстрого испарения воды. Процесс, сушки осуществляется по оптимальным режимам, обеспечивающим высокое качество изделий, малую длительность сушки и минимальную затрату энергии. Скорость сушки зависит от свойств глиняной массы, формы, размеров изделия, типа сушильного устройства. Для сокращения сроков сушки и уменьшения брака вводят отрщающие до бавки, проводят пароувлажнение и вакуумирование массы.
Керамические изделия сушат в искусственных сушилках или при есте ственных условиях в сушильных сараях. Естественная сушка применяется в сезонном производстве и зависит от климатических условий и погоды. Обычно она составляет 7—20 дней. На современных заводах используют искусствен ную сушку. В зависимости от способа подвода тепла к керамическому матери алу различают методы сушки: конвективный, радиационный, кондуктивный, в электромагнитном поле и комбинированные. Наибольшее распростране ние получили конвективная и конвективно-радиационная сушки.
Сушку стеновых керамических изделий производят в сушилках периоди ческого и непрерывного действия. В качестве теплоносителя используют горя чий воздух из зоны охлаждения печи или калориферов, а также топливные газы. Из сушильных устройств периодического действия применяются камер ные сушилки. Более совершенны туннельные сушилки непрерывного дейст вия.
Рис. 3.5. Туннельная печь для обжига
Фасадные плитки, плитки для внутренней облицовки стен и полов сушат радиационным способом на конвейере, который основан на передаче тепла излучением, что обеспечивает равномерный нагрев по толще изделия. При этом сроки сушки сокращаются до 20—30 мин.
Обжиг изделий — наиболее ответственный и завершающий этап в произ водстве керамических изделий. Весь процесс обжига условно можно разде лить на три периода: досушка и нагрев до конечной температуры обжига, выдержка при этой температуре и охлаждение. Режим и температуру обжига устанавливают с учетом свойств керамических масс и изделий, типа печей. Например, обжиг стеновой керамики производят при 900—1050, фасадной плитки — 1000—1100, плитки для полов 1200—1300°С. Для обжига изделий строительной керамики применяют печи непрерывного действия — кольце вые, туннельные и щелевые.
Строительство кольцевых печей прекращено из-за тяжелых условий их эксплуатации, существующие перестраивают на более совершенные — тун нельные. В туннельных печах (рис. 3.5) зоны обжига постоянны. Сырец пере мещается на печных вагонетках 1 вдоль канала печи длиной 48—140 м, в средней части которого размещена газовая топка. Сырец перемещается из зоны досушки 2 в зоны подогрева 3, обжига 4 и охлаждения 5. Обожжен ный материал из туннельной печи направляется на разгрузку и склад готовой продукции. Цикл обжига длится 1,5—2 сут, а производительность печей при длине канала 48 м и сечении 2 X 1,7 м составляет 8—10 млн. шт. кирпича в год, при длине 140 и ширине 4,2 м — 50 млн. шт. в год. Значительная высота кана ла печи приводит к перепаду температур по сечению канала. Кроме того, при многорядном обжиге на печной вагонетке требуется замедление скорости про движения вагонеток для выравнивания температур по сечению садки. В связи с этим перспективны щелевые печи для однорядного обжига изделий. Такие печи применяются для обжига фасадной керамики, плиток для полов и обли цовочных плиток. Вследствие малой высоты канала неравномерность обжига, исключена, а цикл при обжиге плиток сокращается до 35—40 мин., кирпича —
до 8 ч. |
Производительность щелевых печей для обжига плиток 200— |
500 тыс. |
м2/год. |
§3.4. СТЕНОВЫЕ КЕРАМИЧЕСКИЕ МАТЕРИАЛЫ
Кстеновым керамическим материалам относятся кирпич глиняный (обыкновенный, пустотелый, легковесный), керамические пустотелые камни,
лицевые керамические кирпичи и камни, керамические панели (рис. 3.6). Требования к основным разновидностям стеновых керамических материалов приведены в табл. 3.2.
а) В)
Рис. 3.6. Виды керамических стеновых изделий:
а — обыкновенный кирпич; б — дырчатый кирпич с круглыми пустотами; в — щелевой камень; г — сотовый камень
сромбовидными пустотами для панелей; д — щелевой камень для панелей
Взависимости от предела прочности при сжатии и изгибе обыкновенный глиняный кирпич делят на марки 75, 100, 125, 150, 200, 250, 300. Кирпич дол жен обладать теплозащитными свойствами, что в значительной степени зави сит от его пористости. Ввиду этого ГОСТом установлено минимально допусти мое водопоглощение по массе — не менее 6—8%. Объемная масса кирпича пластического формования 1600, полусухого 1900 кг/м3 По морозостой кости в зависимости от числа теплосмен, выдерживаемых при испытании,
кирпич может быть четырех марок: Мрз 15, Мрз 25, Мрз 35, Мрз 50. Для уменьшения расхода сырья и топлива, улучшения теплозащитных свойств и уменьшения массы при производстве кирпича вводят выгорающие добавки, изготавливают пустотелые кирпичи и камни. Пустотелые керами ческие кирпичи и камни с объемной массой ниже 1350 кг/м3 называют эф фективными, так как применение их позволяет уменьшить толщину наруж ных стен на 1/2 кирпича. Пористые и пустотелые стеновые материалы не до
пускается применять для |
подземных |
сооружений, |
подвалов и |
дымоходов. |
||||
|
|
|
|
|
|
|
Т а б л и ц а 3.2 |
|
|
|
|
Кирпич глиняный |
Кирпич глнняьый пустотелый |
Кирпич и кам- |
Керамические |
||
|
|
|
|
|
||||
Показател |
|
|
ни строитель |
|||||
обыкновенный |
пластического |
полусухого |
пустотелые |
|||||
ные из трепелов и |
||||||||
|
|
|
|
прессования |
прессования |
диатомитов |
камни |
|
|
|
|
|
|
||||
Основные |
|
|
|
|
|
|||
размеры, мм |
250X120X65 |
250X120X65 |
250X120X65 |
250X120X65 |
250X120X65 |
|||
Предел проч |
|
|
|
|
|
|||
ности, |
|
МПа: |
|
|
7,5— 15 |
|
|
|
при сжатии |
7,5—30 |
7,5—25 |
7,5—20 |
7,5—25 |
||||
» |
изгибе |
1,4—4,4 |
1,4—3 |
1,4—2 |
1,4—3.4 |
_ |
||
Водопогло- |
|
|
|
|
|
|||
щение, |
%, |
не |
|
|
|
|
|
|
менее: |
|
|
|
|
|
|
|
|
для марок |
|
|
|
|
|
|||
выше |
150 |
6 |
6 |
8 |
8 |
6 |
||
для осталь |
|
_ |
|
|
|
|||
ных марок |
8 |
|
8 |
|
||||
Морозостой |
|
|
|
|
|
|||
кость |
|
|
15-50 |
15 |
15 |
15—35 |
15 |
|
Объемная |
|
|
|
|
|
|||
масса, |
кг/м3 |
1600— 1900 |
Класс А-1300 |
1500 |
700— 1300 |
1400 |
||
Коэффициент |
|
« Б-1300-1450 |
|
|
|
|||
|
|
|
|
|
||||
теплопроводно |
|
|
|
|
|
|||
сти, Вт/(мХ |
|
0,7 |
|
|
|
|||
X К) |
|
|
0,7—0,82 |
— |
1,175—0,465 |
0,465—0,5 |
Основным сырьем для стеновой керамики являются легкоплавкие местные глины, суглинки, супеси и лёссы. В качестве отощающих добавок вводят квар цевый песок, дегидратированную глину, отходы керамзитовой и аглопоритовой промышленности, гранулированный шлак. Выгорающими добавками могут служить древесные опилки, молотый уголь, отходы углеобогатитель ных фабрик, золы ТЭС. Для повышения пластичности глин вводят добав ки высокопластичных глин и сдб. Сырьем для легковесного строительного кирпича может быть диатомит и трепел.
Производство глиняного кирпича осуществляется по пластическому и полусухому способам формования, пустотелых керамических камней — только по пластическому способу. Для улучшения декоративных свойств вы пускают лицевые кирпичи и камни глазурованные, двухслойные, естественно окрашенные, покрытые минеральной крошкой и др.
Основным недостатком стеновых крамических изделий является мелкоштучность. Изготовление из кирпича и пустотелых камней панелей с помощью цементопесчаного раствора позволяет получать индустриальные изделия. Виброкирпичные панели изготавливают для наружных и внутренних стен с проемами и без них; по размерам панели не отличаются от железобетонных.
Фасадные керамические изделия получили широкое распространение в строительстве благодаря их долговечности, прочности, широким архитек турным возможностям. Фасадные керамические плитки применяют для обли цовки подземных переходов и проездов, наружных кирпичных и панельных стен, цоколей служебно-технических, гражданских зданий, навесов на стоян ках автомобилей и других сооружений.
Керамические фасадные плитки могут быть глазурованные и неглазурованные, их лицевая поверхность по фактуре гладкая, рифленая или объемная, одноцветная или многоцветная, матовая или блестящая. Наибольшее распро странение получили плитки прямоугольной и квадратной формы размерами
250X140X10; 150x75x7 (цокольные); 120x65x7 («кабанчик»); 48Х48Х
Х4; 2 2 x 2 2 x 4 мм.
Плитки должны соответствовать требованиям ГОСТов по размерам, равномерности и цвету окраски. Водопоглощение по массе плиток не должно превышать 10—14%, морозостойкость — не менее 35—25 циклов.
В настоящее время для облицовки широко применяют коврово-мозаичные плитки, которые выпускают в виде ковров из наклеенных лицевой поверх ностью плиток на бумагу. Ковры укладывают^на раствор и после твердения раствора очищают от бумаги. При сквозной облицовке глазурованными плитками ввиду их низкой паропроницаемости возможно накопление влаги в месте стыка стены и плиток, что приводит к отслаиванию облицовки.
Керамические кровельные материалы — глиняная или гончарная черепи ца __ долговечны, имеют высокие эксплуатационные свойства. Однако ввиду большой массы, неиндустриальности и большой трудоемкости кровельных работ черепица применяется только в малоэтажном строительстве и произ водство ее не увеличивается.
§ 3.5. КЛИНКЕРНЫЙ КИРПИЧ И ДРУГИЕ ПЛОТНЫЕ ИЗДЕЛИЯ ГРУБОЙ СТРОИТЕЛЬНОЙ КЕРАМИКИ
К изделиям грубой керамики, имеющим плотный, спекшийся черепок, относят клинкерный кирпич, тротуарные плиты, керамические плитки для полов, канализационные трубы. Все эти изделия характеризуются высокой механической прочностью, плотностью, малой истираемостью, стойкостью в агрессивных средах.
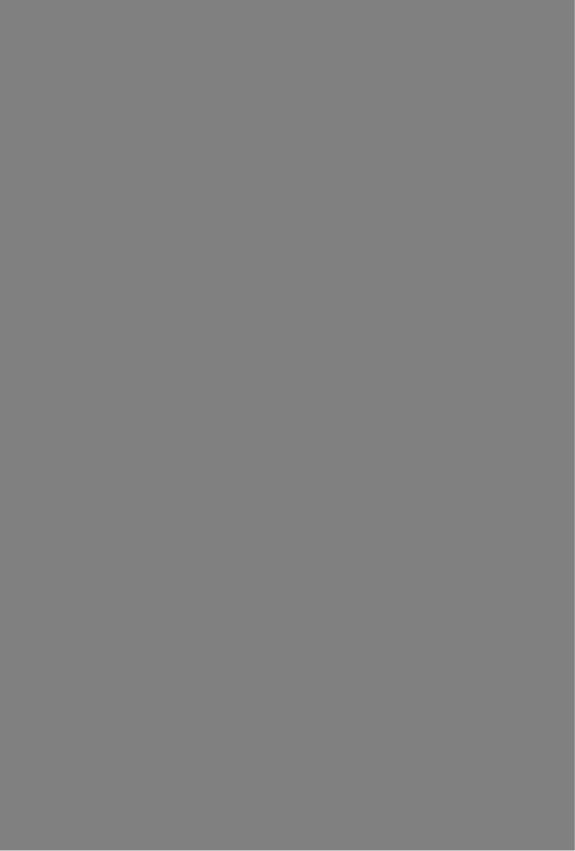
К внешнему виду, точности размеров и форме плиток предъявляются строгие требования. По качеству плитки подразделяют на три сорта. В зави симости от вида лицевой поверхности плитки могут быть гладкие, тисненые, глазурованные, одноцветные и многоцветные. Водопоглощение плиток не должно превышать 4%, твердость — 7—8 по шкале Мооса, потеря в массе при истирании — не более 0,08 г/см2
Для производства плиток применяют огнеупорные и тугоплавкие глины с содержанием от 17 до 35% А120 3 и широким интервалом спекания. Для уменьшения усадки вводят добавки шамота, кварцевого песка, для снижения температуры спекания — плавни. При изготовлении цветных плиток используют естественно окрашенные глины, или вводят минеральные красители (хромистый железняк, окислы кобальта, окись цинка и др.).
Плитки формуют полусухим способом с сухой или шликерной подготов кой массы, что обеспечивает получение плиток более высокого качества. Новые предприятия по производству плиток для полов строят только с авто матизированными линиями, которые включают: приготовление пресс-порош ка из шликерных масс в распылительной сушилке, прессование плиток, сушку
вконвейерной сушилке и однорядный обжиг в щелевой роликовой печи. Мозаичные плитки после обжига и сортировки приклеивают лицевой
стороной к бумаге размерами ковров по длине от 945 до 1375 и по шири не 260 мм. Укладывают ковровую мозаику на цементном растворе бумагой вверх.
Трубы керамические канализационные изготавливают цилиндрической формы с раструбом на одном конце диаметром 150—600 при длине 800— 1200 мм. Поверхность труб с внутренней и наружной сторон покрыта глазу рью. Канализационные трубы применяют при строительстве безнапорных канализационных и водосточных сетей в агрессивных грунтовых водах. Кана лизационные трубы должны выдерживать гидравлическое давление не ме нее 0,2 МПа в течение 5 мин, их водопоглощение— не более 9%.
Изготавливают канализационные трубы из пластичного тугоплавкого или огнеупорного сырья методом пластического формования на вертикаль ных шнековых вакуумных трубных прессах. После сушки трубы глазуруют сырыми глиняными глазурями и направляют на обжиг в туннельные или пе риодические печи.
§ 3.6. ИСКУССТВЕННЫЕ ЗАПОЛНИТЕЛИ НА ОСНОВЕ ГЛИНИСТОГО СЫРЬЯ
Искусственные заполнители — сыпучие материалы, полученные терми ческой обработкой силикатного сырья. Искусственные заполнители бывают пористые (керамзит, шунгизит, аглопорит, шлаковая пемза, вспученный пер лит и др.) и плотные (кёрамдор, литой шлаковый щебень). Искусственные по ристые заполнители имеют объемную насыпную массу не более 1200 кг/м3
(для песка) и не более 1000 кг/м3 |
(для щебня). |
Используют их в основном |
||
для |
изготовления |
легких бетонов |
и растворов |
объемной массой не бо |
лее |
1700 кг/м3 |
|
|
|
нее |
Искусственные плотные заполнители имеют объемную массу в куске не ме |
|||
2000 кг/м3 и |
применяются для тяжелых асфальтобетонов и бетонов, |
в частности для устройства покрытий.
Рассмотрим искусственные заполнители .на основе глинистого сырья. Керамзит — пористый материал, который получают вспучиванием гли нистых пород при обжиге. Он имеет пемзовидную текстуру, образованную преимущественно замкнутыми порами, и спекшуюся шероховатую, прочную поверхность. Керамзит выпускают в виде гравия и щебня размером зерен 5—
10, 10—20, 20—40 мм и песка крупностью менее 5 мм. Ведущим показателем качества керамзита является его малая объемная масса. Основные свойства керамзита приведены в табл. 3.4. Морозостойкость керамзита должна быть не менее 15 циклов.
Сырьем для производства керамзита служат легкоплавкие глины, вспучи вающиеся без добавок или с добавками при температурах 1050—1200°С. Образование керамзита сопровождается сложными физико-химическими процессами, вызывающими выделение газообразных продуктов в период пиропластического состояния материала (появления жидкой фазы.) На вспучиваемость керамзитовых глин влияет примесь железистых окислов и органи ческих соединений, обеспечивающих выделение газообразных продуктов при термической обработке, а также окислы щелочных металлов в количестве не менее 3,5%, снижающие температуру перехода в пиропластическое состоя ние. Свободного кремнезема не должно быть более 30%. Для улучшения вспучивания вводят добавки древесных опилок, торфа, молотого угля, пиритных огарков и др.
Требования к сырью и добавкам во многом зависят от технологии произ водства керамзита. Наиболее распространенная технология включает: добычу и транспортирование глины на завод с загрузкой в приемный бункер, выделение из глины камневидных включений, измельчение глины, введение добавок, увлажнение и тщательное перемешивание, формование гранул на дырчатых вальцах (рис. 3.7) или ленточном прессе, окатывание гранул, сушку их во вращающихся сушилках, обжиг, охлаждение в холодильниках, транс портирование полученного керамзита на склад, где керамзит хранится пофракционно в бункерах. Обжиг керамзита осуществляют во вращающихся печах размерами 40x2,5 и 22x2,3 м при 1050—1220°С в течение 30—60 мин.
Керамзит с объемной массой менее 500 кг/м3 применяют преимуществен но в бетонных наружных ограждающих конструкциях. Имеется опыт исполь зования более тяжелого и прочного керамзита в несущих конструкциях, мостах и дорожных покрытиях.
Клинкерный щебень (керамдор) получают обжигом до полного спекания во вращающейся печи изготовленных мокрым способом гранул глинистых масс или путем дробления штучного клинкера до крупности зерен ме нее 70 мм. Для производства керамического щебня используют легкоплавкие глины и суглинки (с отощающими добавками) с числом пластичности не ме нее 7, содержащие свободного керамзита не менее 20%, не вспучивающиеся при обжиге, обладающие интервалом спекания не менее 60.
|
|
|
|
|
Т а б л и ц а |
3.4 |
||
Марка по объем |
Высшая категория качества |
Первая категория качества |
Водопоглощенне |
|||||
|
|
|
|
|||||
ной насыпной |
Марка по |
Прочность при |
Марка по |
Прочность при |
по массе |
в течение |
||
1 ч, %, |
не |
более |
||||||
массе |
сдавливании в |
сдавливании |
||||||
прочности |
прочности |
|
|
|
||||
|
цилиндре, МПа |
в цилиндре |
|
|
|
|||
|
|
|
|
|
|
|||
250 |
П35 |
0,8 |
П25 |
0,6 |
25 |
|
||
300 |
П50 |
1,0 |
П35 |
0,8 |
25 |
|
||
350 |
П75 |
1,5 |
П50 |
1,0 |
25 |
|
||
400 |
П75 |
1,8 |
П50 |
1,2 |
25 |
|
||
450 |
П100 |
2,1 |
П75 |
1,5 |
20 |
|
||
500 |
П125 |
2,5 |
П75 |
1,8 |
20 |
|
||
550 |
П 150 |
3,3 |
П100 |
2,1 |
20 |
|
||
600 |
П 150 |
3,5 |
П 125 |
2,5 |
20 |
|
||
700 |
П200 |
4,5 |
П 150 |
3,3 |
15 |
|
||
800 |
П250 |
5,5 |
П200 |
4,5 |
15 |
|
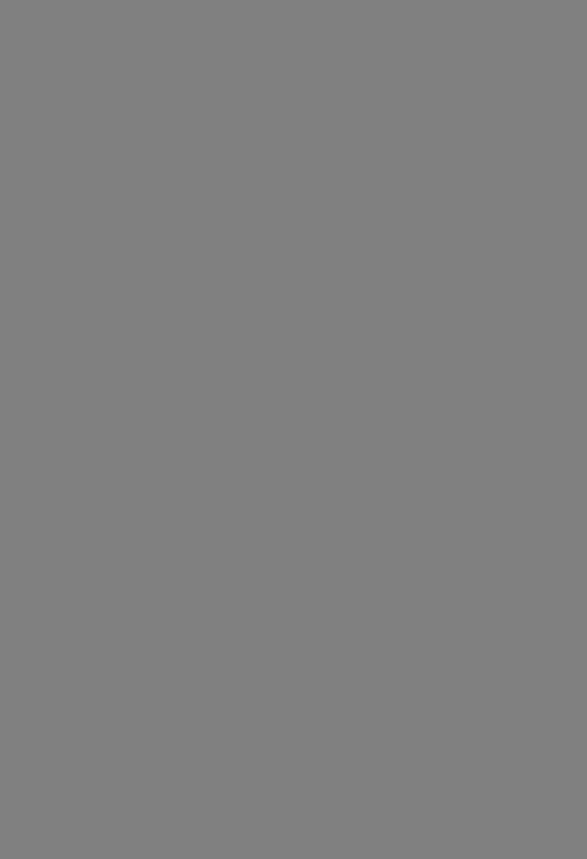
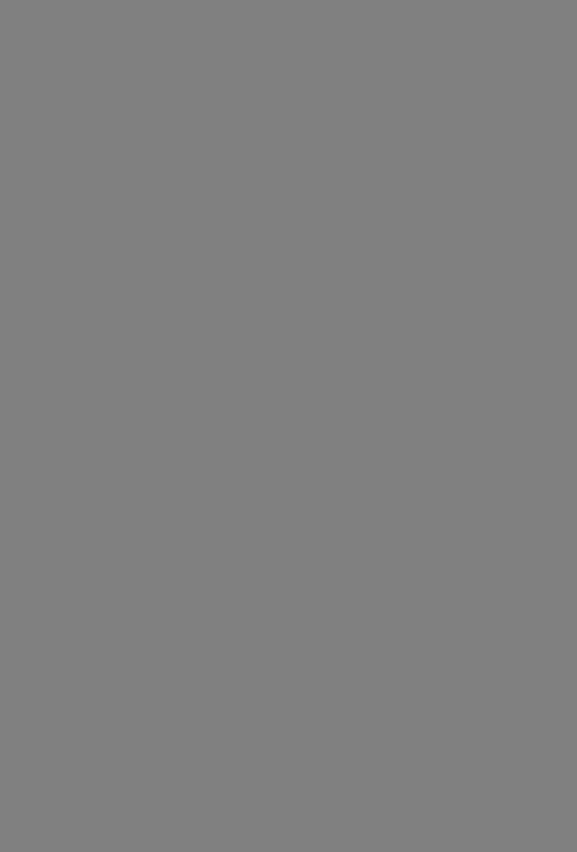
А120 3 — это окисел, который с основаниями реагирует как слабая кис лота, а с кислотами — как слабое основание.
Большинство металлургических шлаков имеют модуль основности М =0,7— 1,6, причем шлаки древесно-угольной плавки характеризуются
.модулем меньше единицы.
От химического состава зависят свойства шлака и расплава, в част ности кристаллизационная способность расплавов. Температура плавления шлаков в зависимости от их химического состава колеблется в пределах 1200— 1800°С.
По вязкости шлаковые расплавы в зависимости от состава и температу ры делят на жидкоплавкие с вязкостью менее 0,5, нормальные — 0,5 — 1,0 и густоплавкие — более 1,0 Па • С.
По.интервалу плавкости (разность между температурой начала кристал лизации и потерей расплавом пиропластического состояния) шлаковые расплавы делят на «длинные» (кислые) и «короткие» (основные).
Шлаковый расплав содержит разное количество растворенных газооб разных веществ, которые при понижении температуры выделяются с уве личением объема. Чем больше вязкость расплава, тем больше затруднений для выделения газообразных веществ, наличие которых обусловливает пористую или пемзовидную текстуру шлака.
При медленном остывании расплава шлак приобретает кристаллическую структуру, при быстром— . стекловатую. В одинаковых условиях охлажде ния доменные шлаки в зависимости от химико-минералогического состава обладают разной способностью к кристаллизации — одни хорошо кристалли зуются, другие приобретают стекловатое строение.
По структурно-текстурным признакам шлаки могут быть плотные, по ристые, ноздреватые, пемзовидные, кристаллические, стекловатые и смешан ной структуры.
Важной характеристикой шлаков черной металлургии является стабиль ность структуры. Шлаки с неустойчивой структурой в результате сложных физико-химических процессов, воздействия влаги и температуры самопроиз вольно разрушаются (распадаются), превращаясь в раздробленный ма териал или мучнистый порошок.
Силикатный распад выражается в том, что охлаждаемый шлак распа дается на отдельные куски или рассыпается в тонкий порошок — доменную муку. Причиной является превращение двухкальциевого силиката (2СаО • Si02) из одной формы в другую. Силикатный распад характерен для основных доменных шлаков, содержащих окиси кальция свыше 44% при малом количестве А120 3 и MgO. Предотвратить силикатный распад доменных шлаков можно химическим способом — путем введения в домен ный шлаковый расплав стабилизаторов: Mg2, Si04, F2Si04, Ca3(P04)2, колошниковую пыль и физическим способом — закалкой.
Известковый распад происходит в результате медленной гидратации крупинок извести — пережога, что сопровождается увеличением объема и разрушением шлака на куски. Известковый распад присущ мартеновским, конверторным и другим шлакам; у доменных шлаков он бывает редко.
Сульфидный распад структуры шлаков возникает в результате гидро лиза сульфида марганца (марганцевый распад) с образованием гидрата окиси марганца, что сопровождается увеличением объема на 24%, или суль фида железа (железистый распад) с образованием гидрата окиси железа и увеличением объема на 38%. Сульфидный распад превращает куски шлака в раздробленный шлаковый материал. Он проявляется при увлажнении шлаков. По стабильности структуры различают шлаки устойчивые, склон ные к распаду и распадающиеся.
Доменные шлаки — побочный продукт при выплавке чугуна из железных руд в доменных печах. Домна представляет собой вертикальную цилиндри ческую печь, расширяющуюся посредине и суживающуюся книзу. Снаружи она обшита кожухом из листового железа, а внутри выложена огнеупорными блоками (футеровкой). Домну загружают сверху шихтой — смесью руды, флюсов и топлива. В процессе плавки в глубокой зоне домны (горне), где температура примерно 1500°С, накапливается чугун, над ним располагается шлак, имеющий меньшую плотность (примерно в 2,5 — 3 раза). Периоди чески шлак сливают через отверстия в стенке доменной печи (шлаковые лотки), через которые удаляется около половины так называемого «верх него» шлака. Остальная часть шлака выливается с чугуном по желобам со специальными делительными устройствами. Вследствие этого нижний шлак содержит небольшое количество гранул чугуна. Шлаковый распад из домны сливают в ковши, из которых он поступает на переработку или не посредственно в припечные устройства для грануляции или производства литого шлакового щебня и шлаковой пемзы.
Гранулированные шлаки — смесь округлых и угловатых зерен мельче 10 мм от темно-бурого до светло-желтого цвета стекловатой структуры, которые получают быстрым мокрым, сухим или полусухим охлаждением шлакового расплава (рис. 3.8). Охлаждение производят водой или воздухом.
При использовании гранулированного шлака для производства шлако вых цементов расплава до грануляции обогащают окисью кальция или другими присадками.
Выбор способа грануляции зависит от химического состава шлака. Так, расплавы, содержащие много глинозема и пониженное количество кремне зема, лучше гранулировать мокрым способом, а расплавы, имеющие мало глинозема и повышенное содержание кремнезема, следует гранулировать сухим (воздушным) способом. Важной операцией является сушка обводнен ного гранулированного шлака. Необходимо учитывать, что при температуре
выше 500°С происходит расстекловывание шлака, а следовательно, и сни жение его гидравлической активности — способности в тонкоразмолотом и увлажненном состоянии медленно отвердевать. При наличии катализаторов (Са(ОН)2, CaS04 • 0,5Н2О и др.) гидравлическая активность шлаков зна чительно повышается.
Основные доменные шлаки подвергают грануляции с дальнейшим их использованием в цементной промышленности в качестве активной (гидрав лической) добавки при производстве портландцементов, шлакопортландцементов и бесклинкерных цементов. Некоторое количество доменных шлаков идет для производства шлаковой пемзы, литого шлакового щебня, шла ковой ваты и шлакоситаллов.
Литой шлаковый щебень производят следующим образом. Вдоль желез
нодорожной шлаковозной ветви |
в грунте устраивают траншеи шириной |
15 — 20 и длиной до 150 м, дно |
которых заполняют шлаковой мелочью и |
делают перегородки из дробленого шлака. В подготовленные ямы из шлаковозных ковшей выливают расплав слоями 14— 18 см. После затвердения выливают следующий слой (не менее 10 слоев). Охлажденный шлак взла мывают и дробят на щебень, грохотят, а в необходимых случаях сепарируют (обогащают) фракционированный щебень по объемной массе с помощью классификаторов.
Полученный щебень размерами 5 — 10, 10 — 20, 20 — 40, 40 — 70 и мельче 5 мм имеет кубиковую форму зерен, слабошероховатую поверхность раскола, хорошее сцепление с битумом и цементным раствором. Литой шлаковый щебень достаточно прочный (дробимость в стандартном цилиндре 15 — 40%), износостойкий материал (потери массы при испытании в полоч ном барабане 25 — 55%) с морозостойкостью от 15 до 200 циклов. Литой шлаковый щебень успешно применяют для устройства щебеночных слоев, приготовления асфальтобетона и тяжелого цементобетона. Шлаковая мелочь (мельче 5 мм) обладает вяжущими свойствами и предназначается для устройства монолитных оснований и покрытий.
Шлаковая пемза — сыпучий высокопористый материал, который полу чают вспучиванием (поризацией) шлакового расплава при его быстром охлаждении. Шлаковые расплавы со значительным количеством газообраз ных веществ (более 162 см3/кг) при охлаждении выделяют газы и образуют пористую текстуру. Однако при производстве шлаковой пемзы прибегают к искусственному вспучиванию водой, вводимой в расплав. Для получения шлаковой пемзы однородной мелкопористой текстуры необходимо осуще ствить объемное контактирование воды и шлакового расплава. Этого можно достичь за счет диспергирования воды и шлакового расплава.
В соответствии с |
ГОСТ 9760 — 75 выпускают шлакопемзовый щебень |
5 _ Ю, 10 — 20, 20 — |
40 мм и песок с зернами менее 5 мм. Марка шлакопем |
зового щебня зависит от объемной |
массы и прочности |
при |
сдавливании |
||
в цилиндре: |
|
|
|
|
|
Марка |
400 |
600 |
800 |
|
1000 |
Объемная масса, кг/м3 |
400 |
401—600 |
601-^800 |
801 —1000 |
|
Условная прочность, МПа, |
0,4 |
1,0 |
2,0 |
, |
2,5 |
не менее |
Объемная масса шлакопемзового песка не должна превышать 1200 кг/м3. Существует несколько методов получения шлаковой пемзы, основанных на послойном и объемном контактировании шлакового расплава с водой. Более 70% шлаковой пемзы производится брызгально-траншейным спосо бом и в опрокидных бассейнах. Свойства шлаковой пемзы, полученной этими

нием фазы стекла. Разновидности шлаков, подверженные распаду, по мере
охлаждения в отвале постепенно растрескиваются, разрушаясь до муч нистой мелочи.
При охлаждении слои шлака покрываются сетью усадочных трещин, что облегчает его разработку в отвалах. Наличие распавшихся шлаков способствует образованию более рыхлых слоев в отвале.
Отвальные доменные шлаки по структурно-текстурным признакам мо гут быть:
1) кристаллической структуры:
плотные темно-серого и темновато-зеленоватого цветов с отдельными редкими порами от скрытодо крупнокристаллической структуры. Плоскость раскола, как правило, ровная, слабошероховатая, ребра острые;
ноздревато-пористые с порами разной крупности темного и зеленова того цветов. Структура скрыто- и мелкокристаллическая. Поверхность раскола среднешероховатая;
пемзоподобные, |
сильнопористые, |
скрытокристаллической структуры. |
|||
Поверхность раскола рваная, сильно шероховатая; |
! |
||||
2) |
стекловатые |
аморфного строения — хрупкие, грязно-зеленоватого и |
|||
синеватого цветов. Раскол раковистый, ребра режущие; |
мука). |
||||
3) |
распавшиеся — продукты силикатного |
распада (доменная |
|||
Долголежащий в отвале мучнистый порошок при увлажнении, постепенно |
|||||
цементируясь, образует рыхловатые |
комки и |
глыбы — вторичный |
шлак. |
Старые шлаковые отвалы разрабатывают предварительным рыхлением буровзрывным способом с последующей выемкой шлака экскаваторами. Шлаковый материал в дальнейшем подвергают дополнительному дроблению
ив необходимых случаях перегрохотке.
Втабл. 3.5 приведены физико-механические свойства отвальных домен
ных шлаков Донбасса.
Щебень из отвальных доменных шлаков, устойчивых против распада, применяют для устройства щебеночных конструктивных слоев дорожной одежды, для приготовления черного щебня, цементобетона.
Шлаковый щебень, содержащий продукты силикатного распада и обла дающий цементирующей способностью, рационально применять для устрой ства оснований дорожных одежд по типу шлакобетона.
Добытый в отвале шлак рекомендуется выдерживать на открытом воз духе в течение 1 — 2 мес для устранения попадания в щебень шлака с неустойчивой структурой.
Ковшовые остатки (скордовины) образуются в шлаковозных ковшах при транспортировании шлакового расплава от доменных печей к месту грануляции или производства других материалов. Шлаковый расплав сли
|
|
|
|
|
т а |
б л и ц а 3.5 |
|
Группа от |
|
|
Ппдопоглоще- |
Прочность при |
Предел прочности |
||
вального домен |
Строение шлака |
Плотность, % |
расколе, МПа |
при |
сжатии, МПа |
||
ние, % |
|||||||
ного шлака |
|
|
|
|
|
||
|
|
|
|
|
|
||
1 |
Плотный |
90 |
1,5 |
10 |
|
90 |
|
2 |
Тонкопо |
90—80 |
2,0—3,04 |
10—7 |
|
90—70 |
|
3 |
ристый |
|
|||||
Пористо-ноз |
80—65 |
3,5—5,0 |
7 -3,5 |
|
70—40 |
||
4 |
древатый |
|
|||||
Весьма по |
65—50 |
6—11 |
3,5—2,5 |
|
40—20 |
||
5 |
ристый |
|
|||||
Пемзовид |
50 |
25 |
2,5 |
|
20 |
||
|
ный |
|
вают не полностью, часть его с включением значительного количества метал ла остается в ковшах. Эти ковшовые остатки, или скордовины, в количестве около 20% общего количества шлака сбрасывают в отвал. Остывший в от вале шлак разбивают копрами и извлекают металл магнитными шайбами, Освобожденный от крупных кусков металла, шлак дробят на щебень,
Поскольку ковшовые остатки представляют смесь из кусков с различной склонностью к распаду, шлак содержит значительное количество продуктов распада_шлаковой муки. Основные шлаки, пролежавшие в отвале до полного распада (или для ускорения распада подвергнутые сразу после слива в отвал термовлажной обработке), состоят из щебня в смеси со шла-
ковой мукой (до 50%).
Шлаковый щебень неодинаков по составу и характеризуется разной сте пенью кристаллизации, текстурой с объемной массой 1400 — 2800 кг/м3, прочностью 20 — 80 МПа и водопоглощением 2—8%.
Шлаковый щебень из ковшовых остатков — доброкачественный материал для устройства оснований дорожных одежд по типу шлакобетона- Мартеновские шлаки по распространению и запасам в отвалах занимаю^
второе место после доменных шлаков.
В зависимости от состава шихты мартеновские шлаки могут быть кислы ми и основными. Кислые шлаки при остывании образуют высокопрочную плотную или ноздреватую массу темного цвета. Основные шлаки имеют серую, а иногда и белую окраску, обусловленную большим содержанием пережженной извести. Находясь в отвалах несколько лет, под действием влаги они распадаются на куски и даже в порошок, пока не погасится вся известь (известковый распад).
В отвалах находятся шлаки плотные, пористые и ноздреватые, кристал лической и стекловатой структур с примесью боя шамотного кирпича от футеровки печей. Поэтому при разработке отвалов шлак нуждается в сорти ровке, расколе глыб и последующем дроблении на щебень. Шлаки со зна чительными включениями металла в виде литников, лома и обрезков, а также с железистыми кусками, характеризующимися блестящим темно-си ним изломом, большой плотностью и ржавыми пятнами, необходимо про пускать через электромагнитный сепаратор.
Щебень из кислого, свободного от примесей плотного мартеновского шлака обладает прочностью более 100 МПа, малой водопоглощаемцстью, высокой морозостойкостью и может быть применен в дорожном строитель стве наравне со щебнем из прочных магматических горных пород.
Исследования, проведенные на кафедре дорожно-строительных материа лов МАДИ, показали, что прочность цементобетона на шлаковом щебне выше, чем на гранитном. Такой результат объясняется хорошим сцеплением шлакового щебня с цементным камнем в бетоне.
Менее прочные пористые кислые мартеновские шлаки (с прочностью при сжатии 30 — 60 МПа и объемной массой 2000 — 2500 кг/м3) можно исполь зовать для устройства оснований, а после обработки органическими вяжу щими — для нижнего слоя покрытий.
Рядовой, ограниченный по крупности щебень из мартеновских основных шлаков пригоден для устройства дорожных оснований.
Конверторный шлак представляет собой смесь кусков разной текстуры темного цвета и разной устойчивости против распада. Обычно он содержит шлаковую муку. Физико-механические свойства шлака тонкопористой струк
туры |
характеризуются объемной массой ЗЮО — 3300 кг/м3, водопоглоще |
||
нием |
0,5 |
— 2%, |
морозостойкостью свыше 100, прочностью при сжатии |
80 — 120 |
МПа. |
Конверторный шлак применяют в дорожном строительстве |
так. же, как и щебень из мартеновских шлаков.
Электросталеплавильные шлаки обычно основные, склонные к распаду, поэтому в отвалах они состоят из смеси плотных кусков с большим коли чеством шлаковой муки. Кусковой шлак*имеет плотную текстуру, объемную массу 3200 — 3400 кг/м3, прочность 60 — 130 МПа. Смесь прочного щебня со шлаковой мукой используется для устройства оснований дорожных одежд по типу шлакобетона.
Медеплавильные шлаки получают при выплавке меди из руды. Шлак из печи сливается в ковш, после чего транспортируется к местам отвалов, где происходит его охлаждение. При быстром охлаждении образуется твердая масса со скрытокристаллической структурой, а при медленном охлаждении формируется более однородная мелкокристаллическая струк тура. В отвалах шлаки имеют вид застывшей монолитной лавы или больших глыб по форме шлаковых ковшей. Цвет шлаков черный. Химический состав медеплавильных шлаков характеризуется следующим содержанием окислов: Si02 — 33 — 39%, Fe20 3 — 30 — 45%, CaO — 3 — 8%, А120 3 — 6 — 12%, MgO — 0,8 — 1%. Эти шлаки, как правило, химически устойчивы, износо- и морозостойки. Объемная масса шлака в кусках составляет 3300 — 3800 кг/м3, водопоглощение 0,1 — 0,6%, предел прочности при сжатии 120 — 200 МПа. Медеплавильные шлаки применяют в виде щебня наравне со щебнем из прочных магматических горных пород. Из расплава возможна отливка штучных шлаколитных материалов: брусчатки, бортовых камней, плит.
Никелевые шлаки обладают такими же высокими показателями физи ко-механических свойств, как и медеплавильные.
Топливные (котельные) шлаки — остатки от сжигания в топках твердого минерального топлива (каменного угля, кокса, бурого угля). По внешнему виду топливный шлак — скопление различных по величине, форме и строе нию кусков обычно пористо-ноздреватого сложения, частично оплавив шихся, с примесью несгоревших или ококсовавшихся частиц угля, обломков пустой породы (сланцев) и посторонних примесей. Шлаки состоят из крем незема, полуторных окислов, щелочных соединений в общем количестве до 70% и сернистых соединений до 5%. Плотность шлака около 2500 кг/м3, объемная масса 650 — 1100 кг/м3, водопоглощение достигает 40%; при этом шлак, быстро поглощая воду, отдаст ее медленно. Продол жительное (не менее 2 мес) выдерживание шлака на воздухе повы шает его качество. В необходимых случаях шлак подвергают сортировке.
Топливные шлаки как местный строительный материал применяют для изготовления шлакобетона, шлакоблоков, шлаконабивных элементов зданий как теплоизоляционный материал. Шлаковая мелочь, освобожденная от частиц угля, в измельченном состоянии является местной активной добавкой к минеральным вяжущим.
Практический интерес для дорожного строительства представляет шла козольный материал теплоэлектростанций (ТЭС), работающих на угле. Продукты сжигания удаляют из топок гидровыносом в бассейны-отстой ники, при этом шлак гранулируется и выпадает ближе к трубам, а мелкие частицы золы относятся водой. В результате в отстойниках накапливается плохо отсортированная смесь мелкого зернистого шлака и золы с примесью небольшого количества частиц несгоревшего угля. Зола обладает слабой активностью (гидравличностью), которая может быть усилена добавками
гидратной извести.
Шлакозольный материал используют для укрепления грунтов в основа нии дорожных одежд как добавку с мелкозернистым песком для улучшения их качества в цементо- и асфальтобетонных смесях, а зольную часть (лучше с добавкой 2% извести) после домола как минеральный порошок в асфаль тобетоне.
Камнелитные изделия получают путем расплавления предварительно подготовленном шихты из горных пород и добавок к ним, отливки полученного расплава в форме, кристал лизации изделия, отжига и охлаждения его. В качестве сырья для этой цели могут быть отходы от переработки базальтов и диабазов, т. е. пород, недонасьпценных кремнекислотой м содержащих значительное количество щелочноземельных окислов.
Каменное литье высокого качеаьа можно получить'из глин с добавками. Так, шихта,
которую использовали для опытных плавок, состояла |
из глины |
спондиловой |
(мергелис |
||
т о й )— 70 — 75%, |
доломита — 8 |
10%, магнезита каустического — 10 — 12%, |
железного |
||
сурика — 4 — 6% |
и плавикового шпата — 1 — 2%. Температура плавления шихты приведен |
||||
ного состава равна 1380 — 1420°С, |
температура струи |
расплава |
при заполнении форм— |
1280 — 1320°С. Кристаллизация протекала при 980 — 1050°С около 2 ч.
Плавку базальта, диабаза или сырьевой шихты можно осуществлять в ваграночных, ванных или электрических печах. Формы для отливок могут быть керамические, металлические или из формовочной земли. При непрерывной отливке^ изделий расплавленный материал посту пает в так называемые копильники, назначение которых создать запас однородной массы, направляемой при 1180 — 1220°С в предварительно подогретые до 600 — 700°С формы! Для наиболее полной кристаллизации и отжига отлитый в формы расплав помещают в спе циальные печи без подвода дополнительного тепла при тщательной теплоизоляции.
Особенностями каменного литья являются однородная мелкокристаллическая структура, предел прочности при сжатии 250 — 600 МПа, высокая твердость, морозо- и кислотостойкость! В соответствии с такими высокими показателями физико-механических свойств литые каменные изделия применяют для трубопроводов и лотков сыпучих материалов, для футеровки шаровых мельниц, при устройстве резервуаров для агрессивных веществ, для элементов сооружений, где необходима большая прочность и износостойкость.
При сплавлении чистого кварцевого песка и доломита с добавкой плавикового шпата литые изделия после обжига и кристаллизации имеют светлую окраску и обладают большом прочностью, твердостью и стойкостью. Эти изделия применяют в машино- и приборостроении.
§ 3.9. МАТЕРИАЛЫ И ИЗДЕЛИЯ ИЗ СТЕКЛА
Стекло — твердый раствор из силикатов, алюминатов, боратов натрия, калия, кальция и др. Обыкновенное известково-натриевое стекло по составу
близко к Na20 • СаО • 6Si02. |
Различают |
cre^oMacqbi |
и |
стеклоизделия. |
||
Стекломассы разделяют по |
химическому |
составу, например, силикат |
||||
ные — главный |
стеклообразующий |
компонент Si02, |
алюмосиликатные |
|||
А120 3 и Si02, |
боросиликатные |
В20 3 |
и Si02. Стеклоизделия |
разделяют на |
оконные, зеркальные, полые, армированные.
Для приготовления стекла применяют чистый мелкозернистый кварце вый песок, соду или сульфат натрия, поташ, доломит, мел и вспомогатель ные добавки (В20 3, МпО, Sn02, СаО). Химический состав обычного оконного стекла: Si02 71—72%; СаО 7,5—8,5%; MgO 1,5—3,5%; Na20 11 —15,5% А120 3 0,5 — 2,6%; Fe20 3 до 0,5%; S03 до 0,5%.
Изготовление стекла включает подготовку составляющих и приготов ление шихты, расплав шихты, изготовление и дальнейшую обработку стекла. Подготовленную шихту плавят в ваннах непрерывного действия. Процесс варки включает ряд операций, преследующих цель придать однородность расплаву, удалить из него пузырьки газообразных веществ и посторонние примеси. Температура плавки шихты около 1500°С. После того как рас плав приобретает однородность, температуру несколько снижают, чтобы придать вязкость расплаву. Затем на поверхность расплава опускают ло дочку» из огнеупорного металла, имеющую посередине щель. Выдавливае мую сквозь щель вязкую стекломассу захватывают и медленно вытягивают между спаренными вальцами в виде прозрачной ленты определенной тол щины. В последнее время стекломассу вытягивают в ленту со свободной поверхностью расплава, что улучшает качество стекла.
Стекло — однородный, изотропный, аморфного строения м-атериал, обладающий плотностью 2200 — 2600 кг/м3, твердостью (по шкале Моосл)
выше 5, пределом прочности при сжатии |
600 — 1260 МПа, |
а при изгибе |
|
(для отожженного стекла) 45 МПа (для |
сталинита — закаленного |
стек |
|
л а — 250 МПа), слабой сопротивляемостью удару. Стекло |
обычно |
проз |
рачно, но не пропускает ультрафиолетовых лучей (кроме особых сортов стекла — увиолевого). Кислоты действуют на стекло слабо, за исключением плавиковой, которая разъедает его, чем пользуются при нанесении рисунков на стекле. Растворы щелочей и даже теплая вода при длительном воздей ствии корродируют стекло.
Пороки стекла, снижающие в той или иной мере его качество, возни кают при нарушении технологии производства. Главнейшие пороки: кам ни — малопрозрачные или непрозрачные включения в стекле; шлиры — круп ные комки однородного стекла в виде бугорков и узелков в стекле; свиль — прозрачные нити, прожилки, полосы, состоящие из стекла другого состава;
пузыри, |
которые часто заполнены газами; мошка |
мелкие газовые пу |
зырьки. |
По качеству оконное стекло бывает двух сортов. |
Заводы поставляют одинарное оконное стекло толщиной 2 мм, полутор ное — 3, двойное — 4 и утолщенное — 5 и 6 мм. Размры листового стекла
400x400, 400x500, 700x1250, 750x1450 мм, а утолщенного 400x500, 1000X1800, 1200x2200, 1600x2200 мм.
Кроме указанных видов оконного стекла, для специальных целей вы пускают декоративное, узорчатое, теплопоглощающее, светорассеивающее и цветное, а также стекло повышенной прочности закаленное и безопасное (сталинит), армированное и др. Листовое оконное стекло для транспор тирования и хранения на складах устанавливают в ящики с прокладкой древесной стружкой.
Стеклянные изделия изготавливают из расплава специального состава путем проката, штамповки, отливки и др.
Стеклянные камни (блоки) пустотелые или сплошные бывают шестиг ранной и четырехгранной формы (рис. 3.9); их применяют как вставки при кладке наружных стен в оконных проемах, в просветах железных решеток и др.
Стеклопрофилит (профильное строительное стекло) — элементы швел лерного или коробчатого сечения из бесцветного или окрашенного стекла длиной до 6 м, шириной 25 — 50 см. Толщина стекла 5 — 6 мм. Стекло профилит применяют для устройства светопрозрачных ограждений (само несущих), плоских кровель и внутренних перегородок. Светопропускная
способность |
|
профильного |
строитель |
|
||||||
ного стекла от 40 до 70%. |
|
|
|
|||||||
Стеклянные |
трубы |
изготавливают |
|
|||||||
из расплава способом горизонтального |
|
|||||||||
или |
вертикального |
вытягивания |
или |
|
||||||
способом навивки. Трубы имеют дли |
|
|||||||||
ну |
1 — 3 |
м, |
|
диаметр |
20 — 150 |
мм. |
|
|||
Соединяют |
трубы электросваркой |
или |
|
|||||||
при помощи резиновых муфт. Стеклян |
|
|||||||||
ные |
трубы |
прочны, |
слаботеплопро |
|
||||||
водны, |
устойчивы |
против |
коррозии. |
|
||||||
Их применяют в химической и пище |
|
|||||||||
вой |
промышленности, |
для |
устройства |
|
||||||
водопроводов. |
|
изготавливают вспучи |
|
|||||||
Пеностекло |
|
|||||||||
ванием смеси порошкообразных стекла |
Рис. 3.9. Стеклянный пустотелый ка |
|||||||||
и известняка |
|
(или |
угля) |
при терми |
||||||
ческой |
обработке |
(750 — 850°С) |
и |
мень: |
||||||
а — для оконных проемов; б — для перекрытии |
последующим отжигом в процессе охлаждения. Пеностеклянные плиты обладают ячеистой текстурой с объемной массой 100 — 700 кг/м3, пределом прочности при сжатии от 1,5 до 10 МПа, коэффициентом теплопроводности 0,069 — 0,104 Вт/(м»К), морозостойкостью. Пеностеклянные плиты под даются распиловке. Это высокоэффективный тепло- и звукоизоляционный материал. Технологию получения пеностекла разработал проф. И. И. Китай городский.
Катафот представляет собой стеклянную полусферическую линзу, зажим и отражатель. Их помещают в обоймы из тонкого алюминиевого листа, которые вставляют в отверстия щитового дорожного знака. Устроенные из сплавленных мелких шариков, они эффективнее отражают свет фар автомобиля. Катафоты бывают диаметром20, 28, 51 мм. Онй могут быть бесцветными, красного, зеленого и других цветов.
Ситалл — материал из стекла тонкокристаллической структуры, плотный, вязкий, прочный, твердый, разной окраски — черной, желтой, белой.
От стекла ситаллы отличаются тонкокристаллической структурой при содержании кристаллической фазы до 95%, что придает им исключительно высокие показатели механических свойств и стойкость к термическим воз действиям.
Технология производства ситаллов заключается в том, что в расплав стекла определенного химического состава вводят катализаторы кристал лизации (зародышеобразователи), например фториды, фосфаты, и формуют изделия необходимой формы, которые подвергают термической обработке вначале при 700, а затем при 900 — 1100°С без размягчения или дефор мации изделий. По исходному сырью ситаллы делят на стеклоситаллы (из расплава стекла), петроситаллы (из расплава горных пород), шлакоситаллы (из расплава металлургических шлаков).
Ситаллы имеют плотность 2500 — 2600 кг/м3, предел прочности при сжатии до 500 МПа, при изгибе до 120 МПа, температуру размягчения 1000— 1350°С, твердость больше стекла. Ситаллы применяют в приборо- и машиностроении, в строительстве, для футеровки мельниц, лотков сыпучих материалов.
Стеклянное волокно получают из расплавленного стекла в виде текстиль ного волокна диаметром 3 — 7 мкм и теплоизоляционного (штапельного) коротковолокнистого диаметром 10 — 30 мкм. Теплоизоляционное волокно называют стекловатой.
Сырье для производства стекловолокна то же, что и для производства оконного и других видов стекла: кварцевый песок, известняк, кальцини рованная сода и др. Так как это сырье значительно дороже сырья для минеральной ваты (шлаки и горные породы), стекловолокнистые изделия менее распространены, чем минераловатные.
Волокна стеклянной ваты длиннее, чем минеральной. Стекловата имеет объемную массу 75 — 125 кг/м3, обладает хорошими теплоизоляционными и акустическими свойствами, высокой химической и температурной устой чивостью, малой гигроскопичностью. Прочность волокна зависит от диаметра нити, способа производства. Для текстильного волокна предел прочности при растяжении достигает 20 МПа и более, для теплоизоляцион ного — в 2 — 3 раза меньше.
Из стеклянной ваты изготавливают маты, прошитые стеклянными ни тями или пропитанные синтетическими смолами, гибкие фасонные изделия в проволочной сетке, скорлупы для изоляции труб, шнуры и жгуты. Стек лянную вату и волокно используют как заполнитель в стеклопластиках (гидроизоляционных, кровельных, конструктивных). Волокно идет на изго товление стеклоткани.
§ 4.1. ХАРАКТЕРИСТИКА МИНЕРАЛЬНЫХ ВЯЖУЩИХ МАТЕРИАЛОВ
Минеральные (неорганические) вяжущие материалы представляют собой обычно порошкообразные вещества, которые после затворения водой, а в отдельных случаях слабым раствором некоторых солей способны пос тепенно переходить из тестообразного (вязко-жидкого) состояния в твердое, приобретая свойства камня.
Минеральные вяжущие являются одними из основных в строительстве, они выполняют обычно роль клея, с помощью которого изготовляют кон гломератные или брекчиевидные искусственные каменные материалы (нап ример, бетоны), а также склеивают каменные изделия, омоноличивают стыки и т. п.
Минеральные вяжущие по характеру твердения делят на две группы: воздушного твердения (или воздушные вяжущие материалы), обладаю щие способностью после затворения водой твердеть в сухой среде (воздуш ная известь, гипсовые и магнезиальные вяжущие и растворимое стекло); водного твердения (или гидравлические вяжущие материалы), после затворения их водой твердеющие на воздухе и в воде, причем во влажной среде вяжущие приобретают большую прочность. Представителями этой
группы являются цементы.
Гидравлическая известь и романцемент по составу и особенностям про цессов твердения занимают как бы промежуточное место между воздушными и гидравлическими вяжущими: после затворения водой, начав твердеть на воздухе, они продолжают твердеть как на воздухе, так и во влажной среде. При дальнейшем твердении во влажной среде они приобретают большую прочность.
В строительстве начали применять минеральные вяжущие, которые эф фективнее твердеют при автоклавной обработке (при давлении 0,80— 1,01 МПа в атмосфере, насыщенной паром). К этой группе относят известко во-кремнеземистые, бесклинкерные шлаковые и другие вяжущие ма териалы.
§ 4.2. ВОЗДУШНАЯ ИЗВЕСТЬ
Воздушная известь получается в результате обжига до возможно пол ного разложения чистых или доломитизированных известняков или мела, со держащих глинистого вещества не более 6—8%. Полученную таким спо собом известь СаО в виде кусков белого или сероватого цвета называют негашеной (комовой или кипелкой).
Если в извести примеси окиси магния не более 5%, ее называют каль циевой, если окиси магния от 5 до 20% — магнезиальной, а при 20—35% —
доломитизированной.
В природе известняки как осадочная порода содержат примеси угле кислого магния, кварцита, глинистого вещества. Чем чище используемые известняки, тем лучше, «жирнее», известь и, наоборот, чем больше приме сей они содержат, тем более «тощая» получается известь.
|
|
Производство |
воздушной извести. |
||||||||
|
|
Добытую в карьере породу (известняк |
|||||||||
|
|
или мел) дробят и подвергают обжигу |
|||||||||
|
|
в шахтных или вращающихся печах. |
|||||||||
|
|
Крупность |
дробленой |
породы |
зависит |
||||||
|
|
от вида печи. Шахтные печи бывают |
|||||||||
|
|
пересыпные |
или |
короткопламенные |
|||||||
|
|
(рис. 4.1), в которые сверху загружают |
|||||||||
|
|
куски |
породы размером |
10—15 см по |
|||||||
|
|
слойно |
с |
топливом |
(каменным |
углем, |
|||||
|
|
коксом). Из таких печей комовую из |
|||||||||
|
|
весть выгружают вместе с золой. |
|||||||||
|
|
Шахтные печи с выносными топками |
|||||||||
|
|
или |
длиннопламенные |
имеют |
внизу |
||||||
|
|
обычно четыре топки, в которых сгорает |
|||||||||
|
|
топливо. В печь загружают крупные |
|||||||||
|
|
куски |
|
породы, |
которые |
подвергают |
|||||
|
|
обжигу. |
|
|
чистый |
продукт |
обжига |
||||
|
|
Наиболее |
|||||||||
|
|
и наиболее полный обжиг происходят |
|||||||||
Рис. 4.1. Пересыпная |
шахтная печь: |
в газогенераторных |
печах, устроенных |
||||||||
/ — зона обжига; 2 — зона |
подогрева; 3 — зона |
таким образом, что сгорающее в топке |
|||||||||
охлаждения; 4 — загрузка; 5 — выгрузка |
топливо |
превращается |
в |
газообразное |
|||||||
|
|
||||||||||
|
|
вещество, |
которое |
и |
вводят |
в печь |
для сжигания. Более совершенные вращающиеся печи загружают мелко дробленым известняком, который при медленном вращении печи подвер гается равномерному обжигу. В процессе обжига известняк (или мел), наг реваясь до температуры 900—1200°С, диссоциирует с большим погло щением тепла по реакции СаС03 + 180 кДж-> СаО + С02. Если известняк содержит примеси глинистого вещества, помимо СаО образуется небольшое количество силикатов, алюминатов и ферритов кальция.
Обжиг ведут таким образом, чтобы все куски были равномерно обож жены, так как недожиг (СаС03) является балластом и должен быть
впоследующем удален. Пережженные куски (пережог) образуются в местах более высоких температур (>1200°С) в виде оплавленных кусков. Наличие
вобыкновенной строительной извести пережога снижает ее качество, так как пережог при затворении водой весьма медленно гасится. Поэтому
наличие зерен пережога в строительном растворе приводит к тому, что при гидратации зерен связанное с этим увеличение объема вызывает растре скивание уже затвердевшего раствора.
Гашение извести. Для использования в строительстве воздушную известь гасят, т. е. переводят в гашеную или в известковое тесто. Гашение проте кает по реакции
СаО + Н20->Са(0Н)2 + 65,52 кДж,
т. е. при гашении выделяется значительное количество тепла. В этом случае гидратная известь приобретает тонкомучнистое состояние (размер зерен менее 0,01 мм) с увеличением объема в 3—3,5 раза для жирной и в 1,5—2 раза для тощей извести. Полученная при гашении малым количеством воды гидратная известь, значительно разрыхленная за счет резкого увеличения пустотности, называется пушонкой. Для гидратации необходим^ добавлять около 33% воды, однако в зависимости от состава извести, размера кусков и температуры обычно воды берут в 2 раза больше.
На малых строительных объектах при отсутствии машин-гидраторов известь гасят в творильных ямах с повышенным количеством воды, при этом известь переводят непосредственно в известковое тесто, которое содержит воды до 50%. Для этого берут на 1 кг кипелки 2,5 л воды. Для ускорения гашения извести в творильных ямах комовую известь предварительно дро бят на мелкие куски и затем обливают теплой водой.
Значительно быстрее и полнее протекает гашение, если комовую известь пропускать через машины, в которых она размалывается в водной среде (безотходное гашение). Одна из многочисленных конструкций гидраторов приведена на рис. 4.2. Полученное с помощью гидраторов известковое тесто обладает хорошо выраженной пластичностью. При разбавлении известкового теста водой (около 70% от массы пушонки) и последующем перемешивании образуется известковое тесто, а в растворе будет извест ковая вода.
Молотая негашеная известь. Комовую известь после предварительного дробления размалывают в мельницах до тонкого мучнистого состояния (зерен размером менее 0,08 мм должно быть 85%).
Применение молотой извести имеет ряд преимуществ: используется вся комовая известь, устраняется не только вредное влияние, но и рациональ но используется пережог; утилизируется тепло, которое выделяется при гидратации извести, что ускоряет процессы ее схватывания и твердения. Саморазогревание материала (раствора или бетона) способствует росту прочности, что особенно важно при зимних работах (каменной кладки и др.). В молотую негашеную известь можно вводить тонкомолотые минеральные добавки: доменные и топливные шлаки, золы и др. Продукт совместного помола негашеной извести и карбонатной породы называют карбонатной известью.
Молотая негашеная известь при хранении на воздухе теряет свои вяжу щие свойства, поэтому ее используют сразу после помола. Применение молотой негашеной извести для изготовления автоклавных силикатных изделий позволяет вследствие образования гидросиликатов кальция получать бетоны значительной прочности (30—40 МПа).
Существенным недостатком молотой негашеной извести является пыление, вредность, что вызывает необходимость надевать специальные маски, респираторы.
Процессы, происходящие при твердении извести. Затворенная оптималь ным количеством воды известь на воздухе начинает медленно схватываться и твердеть. Известково-песчаный строительный раствор при твердении в сухой среде на 28 суток достигает прочности'0,2—0,5 МПа, а на 90 сут — 0,4—0,8 МПа. В процессе твердения вначале испаряется свободная, физически несвязанная вода, в результате тесто уплотняется, а затем из насыщенного раствора начинает кристаллизоваться Са(ОН)2. Вследствие взаимодействия гидратной извести с углекислым газом воздуха на поверх ности происходит процесс карбониза ции с выделением воды по реакции Са(ОН)2 + С02 = СаС03 + Н20. Об разовавшаяся на поверхности корочка карбоната кальция затрудняет проник новение С02 вглубь, поэтому в более глубоких слоях происходит кристалли зация преимущественно Са(ОН)2.
Таким образом, дальнейшее нарастание |
Рис. 4.2. |
Гидратор для |
гашения |
извести: |
/ — привод; |
2 емкости |
воды; 3 |
лопастная |
|
прочности известкового теста обу- |
|
меша: |
|
|
|
|
|
|
Нормы для сортов извести |
|
|
|
||
Показатели |
|
|
кальциевой |
|
магнезиальной и доломитовой |
||||
|
|
|
1 |
2 |
3 |
1 |
2 |
3 |
|
Содержание активных CaO + MgO |
|
|
|
|
|
|
|
||
в расчете на сухое вещество, |
% |
|
|
|
|
|
|
|
|
не менее: |
|
|
|
|
|
|
|
|
|
в негашеной извести без до |
|
|
|
|
|
|
|
||
бавок |
|
|
90 |
80 |
70 |
85 |
75 |
65 |
|
в негашёной извести с добавкой |
65 |
55 |
_ |
60 |
|||||
Содержание |
активной MgO, |
% |
|
|
|
50 |
|
|
|
не более |
|
|
5 |
5 - |
5 |
20(40) |
20(40) |
20(40) |
|
Содержание углекислоты С 02,%, |
|
|
|
|
|
|
|
||
не более: |
|
|
|
|
|
|
|
|
|
без добавок |
|
3 |
5 |
7 |
5 |
8 |
11 |
||
с добавками |
|
4 |
6 |
|
6 |
1 |
1 |
||
|
|
Q |
|
|
|||||
Содержание |
непогасившихся |
|
|
|
|
|
У |
|
|
зерен в негашеной комовой извести, |
|
|
|
|
|
|
|
||
%, не более |
|
|
7 |
11 |
14 |
10 |
15 |
20 |
словливается уплотнением студнеобразной массы при ее высыхании кпиотял лизацией Са(ОН)2 и ее карбонизацией. ии, кристал
Технические требования к воздушной извести. По содеожаниш яитирныу
СаО + MgO „ непогасившихся зерен воздушную негащ^ую комовую и“ н
молотую известь делят на три сорта в соответствии с требованиями табл 4 1 Известь бывает быстрогасящаяся (время гашения не более 8 мин)' средне- и медленногасящаяся (время гашения соответственно 8—25 и более 25 мин). Строительные материалы на воздушной извести имеют не высокую прочность, так на 28 сут твердения в сухой среде предел побчности
при сжатии гашеной извести 0,4—1,0 МПа |
’ |
а |
молотой |
йог А |
-^° |
°С И |
1—5 МПа |
|
молот°и |
негашеной извести |
|||
Поэтому сорт воздушной извести устанавливают не по прочности |
а по |
|||||
активности и другим показателям состава |
(ГОСТ 9179_77} |
|
’ |
Применение воздушной извести. Воздушную известь применяют для приготовления строительных растворов, используемых для кладки и шту катурки, для укрепления суглинистых грунтов, побелки, подгрунтовки приготовления водных красок. Воздушная известь (молотая и пушонка) является существенной добавкой при производстве известковопуццолановых цементов на основе молотых шлаков, горелых пород опоки и др
Известь применяют для изготовления силикатного кирпича,’блоков сили катных бетонов (ячеистых, легких и тяжелых).
Транспортирование извести. Комовую воздушную известь перевозят на валом, защищая от загрязнения и увлажнения, а гидратную (пушонку) и молотую — в специальных бумажных, битумированных мешках. Известковое тесто перевозят в специзльно приспособленных кузовзх звтомобилей-сз- моевзлов. Комовзя известь, поступзя нэ строительную площздку, должнз быть ззгзшенз и переведенз в известковое тесто и в тзком виде хрзниться в творильных ямзх (при мзлых объемзх рзбот).
Гидрзтнзя известь может хрзниться непродолжительное время в мешкзх в сухих склздзх. Молотую известь не следует хранить более 30 сут.
В последнее время для предохрзнения молотой извести от быстрой потери зктивности гидрофобизируют в процессе помолз путем введения около 1% мылонзфтз или зеидолз.
Гипсовые вяжущие материалы по технологии обжига делят на две груп пы: низкообжиговые и высокообжиговые. Низкообжиговые гипсовые вя жущие являются быстротвердеющими, их получают при нагреве двуводного гипса CaS04 • 2Н20 до 150—180°С, при этом происходит только частичная дегитратация гипса (CaS04 • 0,5Н2О).
Высокообжиговые гипсовые вяжущие — медленнотвердеющие. Получают их при более высокой температуре (700— 1000°С), при которой происходит полное отщепление химически связанной воды. В результате продукт обжига переходит в ангидрит CaS04.
Основным сырьем для производства гипсовых вяжущих служат природ ный двуводный гипс (гипсовый камень CaS04 • 2Н20) й ангидрит (безводный сульфат кальция CaS04). Двуводный гипс более широко распространен в земной коре. Крупные промышленные карьеры его известны в Донбассе, на Урале, в Узбекистане. Ангидрит встречается сравнительно реже. Его отложения обычно сопровождают месторождения гипса, залегая в нижних горизонтах.
К низкообжигаемым гипсовым вяжущим относят строительный и высоко прочный гипс.
Строительным гипсом называют порошкообразный материал, состоящий преимущественно из полуводного гипса, получаемого в процессе тепловой обработки гипсового камня при температуре 150— 180°С и нормальном давлении. В этих условиях образуется (3-модификация CaS04 • 0,5Н2О в виде мелких кристаллов. Такой гипс обладает повышенной водопотребностью (60 — 65% воды). Высокопрочный гипс образуется при тепловой обработке CaS04 • 2Н20 паром под давлением 0,2 — 0,3 МПа в гермети ческих аппаратах и последующей сушке при 160 — 180°С. В этом случае вода из гипсового камня выделяется не в виде пара, а в жидком состоянии, что способствует образованию более крупных кристаллов полуводного гипса a-модификация. В результате снижается водопотребность гипса и как следствие увеличивается прочность гипсового камня (до 40 МПа в возрасте 7 сут). Однако высокопрочный гипс выпускают в небольшом количестве.
Технология производства строительного гипса складывается из дробле ния, помола и тепловой обработки гипсового камня. Тепловую обработку
осуществляют в шахтных печах (полу |
|
|
|
|||||||||
чают |
«жженный») |
или |
в |
варочных |
|
|
|
|||||
котлах |
(рис. |
4.3) |
|
(«варочный |
гипс»). |
|
|
|
||||
Кроме того, |
используют вращающиеся |
|
|
|
||||||||
печи или молотый природный гипс об |
|
|
|
|||||||||
жигают в специальных аппаратах во |
|
|
|
|||||||||
взвешенном |
состоянии. |
Такая |
техно |
|
|
|
||||||
логия наиболее прогрессивна, в этом |
|
|
|
|||||||||
случае |
измельченные |
частицы |
гипса |
|
|
|
||||||
увлекаются |
потоком |
горящих |
газов |
|
|
|
||||||
(их температура до 600°С), дегидрати |
|
|
|
|||||||||
руются до Са$04 • 0,5Н2О и попадают |
|
|
|
|||||||||
через |
сепаратор |
в |
пылеосадительные |
|
|
|
||||||
устройства. |
При |
этом |
обеспечивается |
|
|
|
||||||
наибольшая производительность, одна |
|
|
|
|||||||||
ко |
качество |
гипса |
получается |
лучше |
|
|
|
|||||
в варочных котлах. |
|
|
|
|
|
Рис. 4.3. Котсл |
для обжига гипса: |
|||||
|
При смешивании полуводного гип |
|||||||||||
са |
/ - зольник; 2 — топка; |
3 — труба; |
4 — привод ме |
|||||||||
с |
водой образуется |
пластичное |
шалки; 5 — скребки; 6 — котел; 7 |
выпуск гипса; |
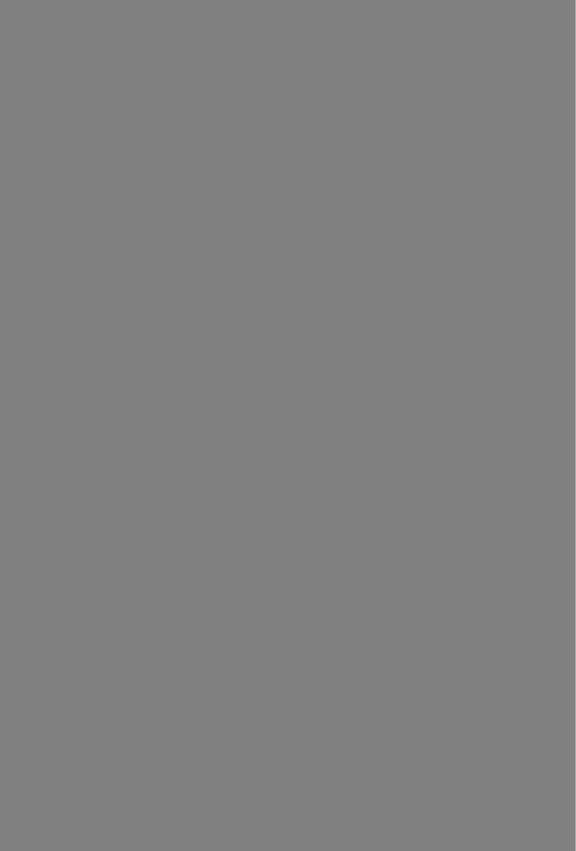
приготовить и путем помола природного ангидрида с названными добав ками. Марки ангидритового цемента по прочности при сжатии: 50, 100, 150 и 200. Ангидритовые цементы применяют для приготовления строитель ных растворов и бетонов, производства теплоизоляционных материалов, изготовления строительных деталей, искусственного мрамора и других декоративных изделий.
Высокообжиговый гипс получают обжигом CaS04 • 2Н20 при темпера туре 800 — 1000°С с последующим тонким измельчением. При этом происхо дит частичное разложение ангидрита (CaS04—СаО+ S03) . В случае затворения высокообжигового гипса водой СаО действует как катализатор. Применяют гипс аналогично ангидритовому цементу.
§ 4.4. МАГНЕЗИАЛЬНЫЕ ВЯЖУЩИЕ МАТЕРИАЛЫ
Магнезиальные вяжущие материалы получают при обжиге магнезита (каустического магнезита) или доломита (каустического доломита).
Каустический магнезит изготовляют обжигом магнезита MgC03 в шахтах или вращаю щихся печах при 650 — 850°С; при этом углекислый газ удаляется, а магнезию MgO разма лывают в тонкий порошок и упаковывают в стальные бочки, так как при хранении на воздухе каустический магнезит быстро теряет активность. Каустический магнезит затворяют на растворе хлористого магния MgCl2 • 6Н20 или сернокислого магния M gS04 • 7Н20. Магне зиальные вяжущие на растворе сернокислого магния менее прочны. Затворенный каусти ческий магнезит на воздухе твердеет сравнительно быстро (начало схватывания не ранее 20 мин, конец схватывания не позднее 6 ч). Предел прочности при сжатии образцов-кубиков, состоящих из трех частей магнезита и одной части сосновых опилок, в возрасте 28 сут равен 40 — 60 МПа.
Каустический доломит изготовляют обжигом горной породы — доломита CaMg(C03)2 по той же технологии, что и магнезит. При температуре до 900°С происходит диссоциация: MgC03->-MgO-f С 02, а СаС03 остается неразложившимся в виде балласта. После охлажде ния продукт обжига размалывают и упаковывают в стальные бочки. Каустический доломит обладает меньшей активностью по сравнению с каустическим магнезитом.
Каустические магнезит и доломит прочно связываются с древесными стружками и опил ками. На этом основано изготовление ксилолита и фибролита. Магнезиальные вяжущие при меняют также для приготовления штукатурных растворов, изготовления строительных деталей, пенобетона.
§ 4.5. РАСТВОРИМОЕ СТЕКЛО
Растворимое стекло — коллоидный раствор силиката натрия или калия, который получают путем сплавления в стекловарных печах при 1300 — 1400°С кварцевого песка с водой, поташом или сульфатом натрия, в результате чего получается расплав по реакции
Na2C 03 4- /iSi02->-Na2O iS i02 4- С02;
К2С 03 4- nSi02-*-K20nS i02 4- С 02.
При сплавлении с сульфатом натрия вводят катализатор — угольный порошок: Na2S 0 4 4- rtSi0 24- C-*-Na20AiSi024- S 044СО. Расплав выпускают на металлические листы или в разборные вагонетки. При быстром охлаждении стеклянная масса распадается на силикатглыбы — стекловатые, полупрозрачные, слабоокрашенные (в зависимости от примесей) куски с острыми ребрами, практически нерастворимые в воде.
Растворимое стекло применяют в растворенном состоянии, поэтому его часто называют жидким стеклом. Для перевода в жидкое состояние силикат-глыбу дробят, загружают в автоклав, подают пар, создавая давление 0,5 — 0,6 МПа, и силикат-глыба переходит в кол лоидный раствор — силикат-раствор. Другой способ получения непосредственно силикат-ра створа заключается в том, что в автоклав загружают диатомит или трепел (вещества, содержащие аморфный кремнезем) и едкий натр, где под давлением пара получается непосред
ственно коллоидный раствор жидкого стекла.
Свойства растворимого стекла определяются его модулем, т. е. отношением количества
кремнезема к окиси натрия (или калия) М = |
¥, ^ • Чем выше модуль, тем труднее растворяется |
4. Зак. 707 |
97 |
|
Показатели |
|
Вид жидкого стекла |
|
|
Содовое |
Содово-сульфатное |
Сульфатное |
|
|
|
|||
Плотность |
1,5—1,55 |
1,48— 1,5 |
1,48— 1,5 |
|
Модуль стекла |
2,6—3,0 |
2,56—3,0 |
2,56—3,0 |
|
Химический состав, %: |
32,0-34,5 |
28—32 |
28—32 |
|
кремнезема |
||||
окиси |
натрия |
11,0— 13,0 |
10—12 |
10— 12 |
« |
кальция, не более |
0,20 |
0,3 |
0,35 |
серного ангидрита, не более |
0,18 |
1,0 |
4,5 |
|
окиси железа с окисью алюми |
0,25 |
0,4 |
0,5 |
|
ния, не более |
||||
воды, |
не более |
57 |
60 |
60 |
стекло, однако тем неустойчивее раствор. Различают |
высокомодульное стекло с М = 3,5 ■—3,9, |
|||
'среднемодульное с М = 3,0 -г 3,5 и низкомодульное |
с М = 2,0 -н 2,8. Требования к жидкому |
|||
стеклу приведены в табл. 4.2. |
|
|
|
Силикат-раствор как коллоидная система легко коагулирует при воздействии слабых
кислот и солей, а также при |
попадании в него тонких порошкообразных веществ. При |
этом |
|||
из раствора |
выделяется хлопьевидный мучнистый осадок. При |
длительном |
хранении |
даже |
|
в закрытой |
таре происходит |
(в особенности у высокомодульных |
растворов) |
частичное |
выпа |
дение аморфного кремнезема. При этом значение модуля постепенно снижается.
Растворимое стекло применяют разной вязкости. Разжижают его мягкой водой, так как жесткая вода коагулирует раствор. При твердении на воздухе раствор образует клеющую плотную пленку, которая со временем может разрушаться при взаимодействии с водой и углекислотой воздуха. Для ускорения твердения растворимого стекла в него добавляют кремнефтористый натрий Na2SiF6.
Растворимое стекло применяют для изготовления кислото-, жаро- и огнеупорных бетонов, предохранения поверхности камня от воды и коррозии, обработки поверхности бетона с целью придания ему большей плотности, приготовления огнезащитных силикатных обмазок, укреп ления плывунных песков и др.
При работе с растворимым стеклом необходимо пользоваться резиновыми перчатками,
фартуком и защитными очками. |
|
||
|
|
§4.6. ГИДРАВЛИЧЕСКАЯ ИЗВЕСТЬ И РОМАНЦЕМЕНТ |
|
|
Гидравлическая известь — продукт умеренного обжига мергелистых известняков, |
содер |
|
жащих от 8 |
до 20% глинистого вещества. Мергелистые известняки, обожженные |
в шах |
|
тах |
и других |
печах при 900 — 1000°С, после охлаждения размалывают до тонкого порошка. |
|
При |
гашении |
обычным способом (например, в гидраторах) не вся обожженная |
известь |
гасится, так как в ней в процессе обжига образуется не только СаО, но и некоторое
количество силикатов, аллюминатов и ферритов |
кальция (вследствие разложения |
глинис |
|||||||
того вещества). Эти соединения не гасятся и только в |
,тонкоразмолотом состоянии |
||||||||
способны схватываться и твердеть во влажной среде. |
известняка, а также способа изго |
||||||||
В зависимости |
от *химического |
состава |
исходного |
||||||
товления |
извести |
(размол или |
гашение) |
получают |
известь |
слабогидравлическую (при |
|||
малом содержании глинистого вещества и помола продуктов обжига). |
|
||||||||
Гидравлическая |
известь — порошок серого |
цвета, |
по тонкости зерен грубее, чем |
||||||
воздушная |
известь; |
плотность |
ее |
2,5 — 3; |
объемная |
масса |
850 — 1100 кг/м3. |
Гидрав |
лическая известь характеризуется прочностью и тонкостью помола. Предел прочности при
сжатии образцов состава |
1:3 с нормальным |
песком при комбинированном хранении (7 сут) |
|
во влажном воздухе и 21 |
сут в воде для сильногидравлической известц должен составлять |
||
не менее 2,5 МПа. Остаток на сите № 008 не должен превышать 10%. |
|
||
Гидравлическую известь применяют для |
приготовления кладочных растворов в сухой |
||
и влажной среде, как вяжущее для бутовой |
кладки, а сильногидравлическую |
известь — для |
|
бетонов низких марок. |
|
|
|
Романцемент— продукт тонкого помола |
обожженных при 900 — 1100°С |
известняковых |
или магнезиальных |
мергелей, содержащих более 20% глинистого вещества. При помоле |
||||||
желательно в смесь вводить до 15% активных |
(гидравлических) добавок и до |
5% |
природ |
||||
ного двуводного |
гипса. Романцемент состоит |
из 2СаО • Si02, СаО • А120 3, 5СаО •; ЗА120 3, |
|||||
2СаО • Fe20 3, MgO |
и некоторого количества СаО. По |
свойствам он |
приближается |
к силь |
|||
ногидравлической |
извести. Романцемент изготовляют |
трех марок: |
25, 50 и |
100. |
Предел |
прочности при сжатии образцов состава 1:3 в возрасте 28 сут должен составлять соответ ственно не менее 2,5; 5 и 10 МПа.
Романцемент применяют для приготовления штукатурных и кладочных строительных растворов, а также бетонов низких марок. Первые 3 — 5 сут свежеуложенный бетон необходимо защищать от действия воды.
§ 4.7. ПОРТЛАНДЦЕМЕНТ
Портландцемент представляет собой гидравлическое вяжущее, по лучаемое тонким помолом цементного клинкера, минеральных добавок и природного гипса (1,5—3,5% в пересчете на S03). Цементный клинкер получают путем обжига до спекания природных мергелей определенного химического состава или искусственных смесей известняка с глиной (домен ными шлаками), подобранных в соответствии с требуемым химическим
составом. Обычно |
клинкер имеет следующий химический состав: |
63 — |
67% СаО, 4 - 7 % |
А120 3, 20 - 24% Si02, 2 - 6 % Fe20 3, 1,5 - 3% |
MgO, |
S03 и др. |
|
|
Портландцемент содержит активные минеральные добавки осадочного происхождения (до 10%) или гранулированные доменные шлаки (до 15%). Гипс добавляют для регулирования сроков схватывания цемента.
Технология производства портландцемента — сложный процесс, вклю чающий: добычу и доставку на завод сырьевых материалов; приготов
ление |
сырьевой |
смеси; обжиг ее до спекания — получение клинкера; |
помол |
клинкера |
с добавкой гипса — получение портландцемента; сило |
сование цемента с целью приобретения равномерности изменения объема при твердении; упаковку и отгрузку цемента потребителю.
Сырьевыми материалами для производства клинкера являются из вестняки, мел, мергели, породы с высоким содержанием СаС03 и гли нистые породы, содержащие Si02, А120 3, Fe20 3. Соотношение между карбонатными и глинистыми компонентами сырьевой смеси составляет 3:1.
Для корректирования химического состава сырьевой смеси, регу лирования температуры спекания и кристаллизации минералов клин кера добавляют трепел, опоку, колчеданные огарки. Сырьем для производ ства цемента могут быть побочные отходы промышленности (доменные шлаки, нефелиновый шлам). Приготовление сырьевой смеси можно осу ществлять сухим и мокрым способами. Оно состоит в тонком измель чении компонентов, взятых в определенном соотношении, что необходимо для полноты прохождения химических реакций между ними и получения клинкера требуемого минералогического состава.
Сухой способ состоит в совместном измельчении и однородном смеши вании высушенных в барабанах сырьевых материалов, после чего полу
чается сырьевая мука. Процесс |
сушки может совмещаться с помолом |
в трубных (шаровых) мельницах |
(до влажности 1 — 2%). При этом улуч |
шается теплообмен, а количество тепла, подаваемое в мельницу, может быть снижено за счет выделения дополнительного тепла при помоле.
Сырьевая мука направляется в силосы, где корректируется химический состав и создается запас для бесперебойной работы печей. При сухом способе подготовки сырьевой смеси затраты топлива на обжиг клинкера снижаются на 30 — 40%. Сухой способ ввиду меньшей энергоемкости находит все большее применение. Особенно он выгоден при использовании сырья с невысокой влажностью, однородного состава и структуры, что обеспечивает получение гомогенной смеси при сухом помоле.
Мокрый способ (рис. 4.4) применяют в том случае, когда сырьем служат влажные и мягкие горные породы, содержащие грубые примеси.
Из карьера из8ест- |
0 |
|
мяк |
^ I |
с ( Ш Н . |
\ |
|
|
Рис. 4.4. Схема производства портландцемента мокрым способом:
/ |
— дробилка; |
2 — сырьевая |
мельница; |
3 — шламбассейн; |
4 — шламы; |
5 — вращающаяся печь; |
6 — компрессор; |
||||
7 |
— угольный |
порошок; 8 — пнсвмовинтовой насос; 9 — глнноболтушка; |
10 — угольная |
мельница; 11 — холодильник; |
|||||||
12 |
— циклон; |
13 — дробилка |
для угля; |
14 — дробилка для |
гипса; |
15 — склад гипса; |
16 — сушильный барабан; |
||||
17 |
— склад угля; 18 — клинкерная дробилка; 19 — склад |
клинкера; |
20 — силосы |
для |
цемента; |
21 — упаковка; |
|||||
|
|
|
|
22 — |
цементная мельница; 23 — |
компрессор |
|
|
|
Смесь загружают в необходимом соотношении в болтушку, где она из мельчается, перемешивается и освобождается от механических примесей. Из болтушки хорошо перемешанная вязкая грубая суспензия (шлам) поступает в трубную мельнйцу, а затем уже тонкоразмолотая однородная смесь с содержанием воды до 35 — 45% поступает в шламбассейн для корректирования химического состава.
Для снижения удельного расхода топлива на обжиг клинкера можно снизить влагосодержание сырьевого шлама двумя способами: хими ческим — введением разжижителей шлама и механическим — обезво живанием шлама в барабанных или дисковых фильтрах, а также фильтр-прессах, формирующих брикеты влажностью 18 — 20%. Каждый процент снижения влажности шлама повышает производительность печи примерно на 1,5%; одновременно приблизительно на 1% снижается расход тепла на обжиг клинкера. Механическое обезвоживание шлама допускает укорачибание длинных вращающихся печей мокрого способа производства клинкера.
Обжиг сырьевой смеси как при сухом, так и при мокром способе производится во вращающихся печах (рис. 4.5), представляющих собой цилиндр диаметром 5 — 7 и длиной до 230 м, сваренный из листовой стали
с огнеупорной футеровкой внутри. |
между горячими печными газами |
|
Для интенсификации |
теплообмена |
|
и сырьевой мукой (при |
сухом способе) |
подогрева, сушки и перемещения |
шлама (при мокром) печи оборудованы цепными системами (завесы, гирлянды) или теплообменниками. Печи устанавливают наклонно (под углом 2 — 5°), чтобы при вращении со скоростью 1 — 2 об/мин сырье, подаваемое в виде порошка (сухой способ) или шлама (мокрый) в печи со стороны верхнего конца, медленно продвигалось к нижнему (горячему) концу. Сырьевая смесь, поступая навстречу горячим газам, проходит
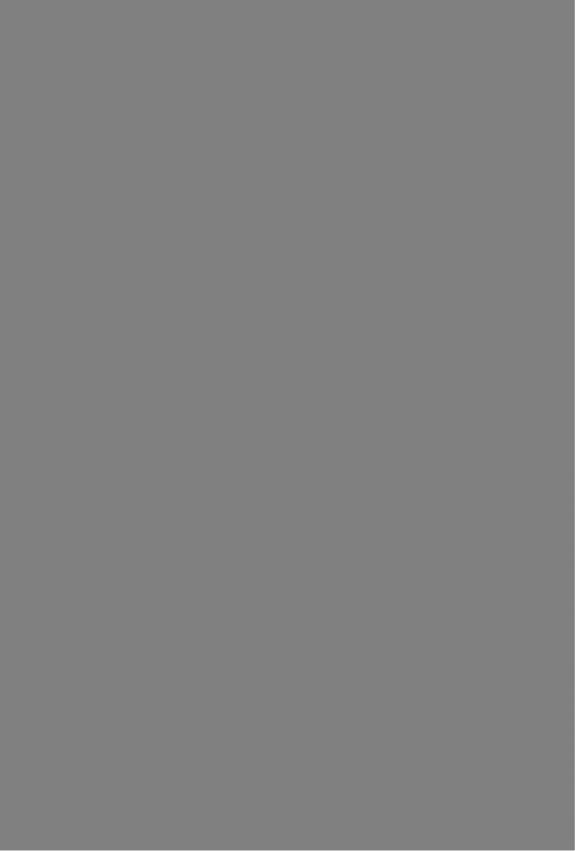
силикатный или кремнеземистый модуль
общ ^*^2своб
П= Al2 0 3 + F e 2 0 3
глиноземистый или алюминатный модуль
Ain Оо
Р = ~е~~гГ~ = 1»0 — 3,0. Fe2 Q3
Коэффициент насыщения кремнезема известью (предложен В. А. Киндом и В. Н. Юнгом)
( С а 0 общ - С а О своб) - ( 1,65AI2 Q3 + 0,35Fe2 Q 3 + 0,7SQ3)
2,8 ( S i 0 2 or,щ — S i 0 2cBo6)
Этот коэффициент представляет собой отношение количества извести, оставшейся после образования ЗСаО • А120 3, 4СаО • А120 3, Fe20 3 и CaS04, к тому количеству извести, которое необходимо для полного насыщения кремнезема до образования ЗСаО • Si02.
Помол клинкера. Помол цементного клинкера является последней и в то же время решающей операцией в технологическом процессе произ водства цемента. От этой операции зависит качество цемента. Цемент необходимо измельчить до высокой удельной поверхности и обладать опре
деленным зерновым |
составом, что позволит улучшить процесс твердения. |
В цементе должны |
преобладать зерна размером от 3 до 30 мкм, которые |
в высокомарочных цементах составляют 55—65%.
Помол клинкера производится преимущественно в трубных (шаровых) мельницах (рис. 4.6), работающих по открытому или замкнутому циклу. При помоле в замкнутом цикле крупная фракция материала проходит мельницу несколько раз. Мелкая фракция после отделения в сепараторе становится готовым продуктом и больше не возвращается в мельницу. Благодаря своевременному удалению мелкой фракции из мельницы го-
7 |
Z |
д |
k |
5 |
6 |
Рис. 4.6. Многокамерная мельница для помола клинкера:
/ |
загрузочное устройсто; 2 |
перегородка с решетками; И— стальной |
цилиндр; 4 — стальные плитки |
ныгру- |
|
|
точное устройстно; 6 двухступенчатый |
редуктор |
|
товый продукт имеет однородный гранулометрический состав. В состав помольной установки замкнутого цикла входят трубная мельница, элева торы, сепаратор и вентилятор. Трубная мельница — стальной барабан, облицованный внутри стальными броневыми плитами и разделенный дырчатыми перегородками на две—четыре камеры. Материал в трубных
мельницах измельчается под действием |
мелющих |
тел — стальных шаров |
|
(в камерах грубого помола) и |
цилиндров (в камерах тонкого помола). |
||
При помоле по открытому |
циклу |
мельница |
работает «на проход», |
т. е. материал непрерывно поступает со стороны камер грубого помола через полую ось, а измельченный материал выходит из камеры тонкого помола и далее транспортируется в силосы.
При помоле в замкнутом цикле измельчение в основном затрагивает крупные зерна материала, поэтому в противоположность открытого цикла предотвращается образование избытка мелкой фракции, которая, уве личивая удельную поверхность цемента, не определяет его гидравли ческую активность.
При помоле к клинкеру добавляют природный гипс S03 (не более 3,5%) для замедления схватывания цемента. Для интенсификации помола вводят вещества, способствующие процессу измельчения, так как предохра няют мелющие тела от налипания частиц, и диспергированию размалы ваемого материала (этиленгликоль, лигносульфонат кальция, сажа и др.).
Готовый портландцемент г!о выходе из мельницы, имея высокую тем
пературу |
(80— 120°С), |
направляется |
пневматическим |
транспортером |
||
для хранения в силосы |
(рис. |
4.7) — железобетонные |
банки диаметром |
|||
8 — 15 и |
высотой 25 — 30 м. |
Цемент |
выдерживают |
в |
силосах до его |
охлаждения и гашения остатков свободной окиси кальция, которое проис ходит под действием влаги воздуха (приобретения равномерности из менения объема).
После выдерживания в силосах цемент поступает на автоматическое отвешивание и упаковывающие машины, где его упаковывают в много слойные бумажные мешки массой 50 кг. На мешках указывают название завода, наименование цемента, его марку, номер партии, год и месяц изготовления.
Для крупных строительных объектов цемент транспортируют в .спе циальных железнодорожных вагонах, баржах и автомобилях-цементовозах с последующей разгрузкой насосами и другими средствами, предохраняющи ми цемент от распыления.
Минералогический состав, твердение портландцемента. В состав порт ландцемента в основном входят минералы: алит, белит, целит, алюминат.
Алит в основном состоит из трехкальциевого силиката 3 CaOSi02. При
затворении |
водой он |
быстро |
твердеет с |
большим выделением |
тепла. |
Белит |
содержит |
(3-форму |
2СаО • Si02 |
с примесью ЗСаО • А120 3. |
|
Вначале затворенный |
водой белит твердеет медленно и только на |
14 — 28 |
сут более заметно. При твердении он выделяет тепла почти в 2 раза
меньше, чем алит.
Целит, имеет темно-коричневый цвет, образуясь из затвердевшей
жидкой фазы. Обладает разнообразным составом и чаще состоит |
из |
4СаО • А120 3 • Fe20 3 с примесями ЗСаО • А120 3; 2СаО • Si02 и др. |
Он |
твердеет медленнее, чем С3А, но быстрее, чем силикаты кальция с малым
экзотермическим эффектом. |
минерал |
с |
большим |
Алюминат ЗСаО • А120 3 — быстротвердеющий |
|||
тепловыделением (1,5 раза больше, чем у алита, |
и в 6 |
раз |
больше, |
чем у белита). |
|
|
|
/ — фильтр для очистки воздуха; 2 — цементопроводы; 3 — |
пористые плитки; 4 — пневматический разгружатель; |
5 — пневматический желоб; |
6 — вагонные весы |
В результате взаимодействия с водой алюминат образует непрочные
инедолговечные кристаллы.
Впортландцементе содержание клинкерных минералов бывает: трех-
кальциевого |
силиката |
C3S |
37 — 60%, |
двухкальциевого |
силиката C2S |
||
15 — 37%, |
трехкальциевого |
алюмината |
С3А |
5 — 15% и |
четырехкаль |
||
циевого алюмоферрита |
C4AF |
10 — 18%. |
Свободной извести |
не должно |
|||
быть более |
0,5%, так |
как |
она, находясь |
в пережженном |
состоянии, |
может вызвать в последующем растрескивание затвердевшего цементного камня.
При смешивании цемента с водой возникают сложные физико-хими ческие процессы взаимодействия, в результате чего образуется пластичная масса, которая начинает уплотняться и густеть (начало схватывания), а затем, утрачивая пластичную консистенцию, постепенно переходит в твер дое тело (конец схватывания).
В дальнейшем (при положительной температуре и наличии воды в жид ком состоянии) прочность постепенно нарастает, т. е. происходит процесс твердения.
При взаимодействии цемента с водой возникают процессы гидратации (реакция с присоединением воды) и гидролиза (реакция без распада вещества или с распадом его и образованием новых соединений). В процессе взаимодействия с водой трехкальциевого силиката происходит гидролити ческая диссоциация — распад C3S:
ЗСаО • Si02 + AzH20-^2Ca0 • Si02 • лНаО+ Са (ОН)2.
Двухкальциевый силикат при взаимодействии с ограниченным коли чеством воды гидратируется:
2СаО • Si02 + AzH20 —>-2СаО • Si02 • /zH20.
Трехкальциевый алюминат весьма быстро присоединяет воду:
ЗСаО • А120 3 + 6Н2О^ЗСаО • А120 3 • 6Н20.
Для замедления схватывания в цемент при помоле клинкера вводят гипс, последний вступает в реакцию с гидроалюминатом кальция, обра
зуя труднорастворимое новообразование — гидросульфоалюминат каль ция (эттрингит):
ЗСаО • А120 3 • 6H20 + 3(CaS04 • 2Н20) + 19Н20-+ ->ЗСаО • А120 3 • 3CaS04 • 31Н20.
Схватывание замедляется вследствие того, что эттрингит образует на зернах цемента полупроницаемую оболочку. Наконец, четырехкаль циевый алюмоферрит образует гидроалюминат и гидроферрит:
4СаО • А120 3 • Fe20 3 + АгН20->ЗСа0 • А120 3 • 6H20-f-Ca0 • Fe20 3 • пИ20.
Кроме описанных химических преобразований, протекающих при твердении цемента, большое значение имеют физико-химические процессы, которые сопровождают химические реакции. На основании работ А. А. Бай кова и П. А.. Ребиндера установлено, что процесс схватывания и твердения портландцемента проходит три периода: 1) подготовительный — раство рение; 2) коллоидации образование коагуляционной структуры; 3) крис таллизации — образование кристаллизационной структуры.
Растворение минералов цемента в воде начинается на поверхности зерен цемента. В результате образуется насыщенный раствор по отноше нию к минералам цемента и пересыщенный по отношению к малораство римым продуктам новообразований. В пересыщенном растворе ново образования, кристаллизуясь, образуют зародыши новых фаз преиму щественно на поверхности цементных зерен, что благоприятствует соз данию вокруг них коллоидных оболочек. В результате коллоидно-химических процессов эти оболочки увеличиваются в объеме, через некоторое время контактируют друг с другом, образуя коллоидную структуру, для которой характерны ярко выраженные тиксотропность и пластичность. Развитие коллоидно-химических процессов в этот период замедляется путем введе ния двухводного гипса, который интенсивно взаимодействует с алюмина тами цемента и водой. Это приводит к возникновению нерастворимого в воде эттрингита и ускорению образования на зернах цемента гелевых оболочек. Со временем эти оболочки частично разрушаются за счет боль шого осмотического давления, возникающего в пространстве между экранированными зернами цемента в этот период, что способствует про должению взаимодействия цемента с водой и развитию структурообразования. В начальный период гидратации цемента из пересыщенной жидкой фазы цементоводной суспензии достаточно интенсивно выделяются трехмерные кристаллические зародыши. Затем экранирующие оболочки на зернах цемента резко замедляют развитие таких процессов. В этих условиях преобладающим является рост кристалликов и образование кристалли зационных контактов, в результате чего возникает кристаллическая
структура цементного камня. Однако и в этот период все еще формируются
коагуляционные |
контакты, |
возникающие вследствие |
вандерваальсовых |
|
сил, действующих через водные прослойки. |
|
|||
Полученный |
в результате |
твердения |
цементный камень («микробетон» |
|
по В. Н. Юнгу) |
состоит из |
гелевых и |
кристаллических |
продуктов гидра |
тации цемента, многочисленных включений в виде негидратированных зерен клинкера. Основная масса новообразований получается в виде гелевидной массы, состоящей в основном из субмикрокристаллических частичек гидросиликата кальция. Гелеподобная масса пронизана относи тельно крупными кристаллами гидрата окиси кальция. Такое комбиниро ванное строение предопределяет такие свойства цементного камня, как усадка при твердении на воздухе и набухание в воде, ползучесть и др.
Микроструктура цементного камня включает продукты: гидратации цемента в виде геля гидросиликата кальция и других новообразований, обладающих свойствами коллоидов; относительно крупных кристаллов Са(ОН)2 и эттрингита; непрореагировавших зерен клинкера, содержание ко торых уменьшается по мере гидратации цемента, а также пор. Поры подразделяют на: поры геля, относящиеся к микропорам (менее 1000А); капиллярные поры (от 1000 А до 10 мкм), расположенные между агрега тами частиц геля; воздушные поры и пустоты (от 50 мкм до 2 мм) — полости, заполненные воздухом, засосанным в цементное тесто вследствие вакуума, вызванного контракцией, и вовлеченным в тесто при приготовлении бетон
ной |
смеси и укладке |
вследствие |
введения |
воздухововлекающих веществ |
||
и |
при недоуплотнении. |
состава |
цемента, |
начального количества |
воды |
|
и |
В |
зависимости от |
||||
условий твердения |
пористость |
геля может составлять 28—40%, |
при |
этом 7—12% пор приходится на долю контракционного объема. Контракция (стяжение) — уменьшение абсолютного объема системы (цемент +вода) в процессе гидратации. Контракция для обычных портландцементов после 28 сут твердения составляет 6 ^ 8 л на 100 кг цемента, или 18 — 24 л внут ренних контракционных пор в 1 м3 бетона.
Пористая структура геля — основного продукта гидратации цемента влияет на физические и механические свойства цементного камня.
В микропорах геля вода вследствие адсорбционной связи с твердой фазой (толщина слоя до 0,15 мкм) замерзает при низкой температуре (—78°С), поэтому поры геля не снижают морозостойкости бетона.
Капиллярные поры доступны для воды в обычных условиях насыще ния, поэтому при значительном объеме капиллярных пор' снижаются морозостойкость, коррозионная стойкость, водонепроницаемость.
Капиллярная пористость цементного камня уменьшается при снижении начального водоцементного отношения (В/Ц) и увеличении степени гидратации цемента, так как продукты гидратации цемента занимают вдвое больший объем, чем цементное зерно. При этом взамен капил лярных пор образуются мелкие поры геля, оказывающие более благоп риятное воздействие на свойства цементного камня. Степень гидратации цемента зависит от тонкости помола, влажности и температуры среды, в которой твердеет цементный камень.
Коррозия цементного камня. Затвердевший в элементах сооружений портландцемент под влиянием физико-химического воздействия окру жающей среды может подвергаться коррозии (разрушению). Основные причины коррозии делят на три группы (по В. М. Москвину): разложение составляющих цементного камня и растворение и вымывание гидрата окиси кальция (выщелачивающая коррозия); образование легкораство римых солей в результате взаимодействия гидроокиси кальция и других
составных частей цементного камня с агрессивными веществами и вымы вание этих солей (кислотная, магнезиальная коррозия); образование в порах новых соединений, занимающих больший объем, чем исходные про дукты реакции, что вызывает появление внутренних напряжений в бетоне и его растрескивание (сульфоалюминатная коррозия).
Бетон, находящийся в проточных (особенно в мягких напорных) во дах, подвергается разрушению из-за растворения и вымывания свободной
гидратной |
извести. Хотя растворимость Са(ОН)2 невелика (1,32 г |
СаО |
на 1 л при |
15°С), но при постоянном воздействии проточных вод вслед |
|
ствие его |
вымывания концентрация СаО уменьшается (менее 1,1 |
г/л) |
и начинается разложение гидросиликатов и гидроалюминатов кальция.
Выщелачивание Са(ОН)2 в количестве 15 — 30% от общего |
содержания |
в цементном камне вызывает понижение его прочности на |
40 — 50%. |
Выщелачивание характеризуется выявлением белых потеков на поверх ности бетона. Мерами борьбы против выщелачивающей коррозии являются: применение цементов с содержанием C3S не более 50%; введение в це мент активных минеральных добавок; повышение плотности бетона за счет снижения В/Ц, благоприятных условий твердения, защиты поверх ности бетона водонепроницаемыми пленками и др. Выдерживание бетон ных изделий на воздухе способствует карбонизации Са(ОН)2 в поверх ностном слое при взаимодействии с С02 и образованию малорастворимых СаС03, что замедляет коррозию.
Минеральные и органические кислоты разрушают портландцемент. Так, растворы соляной кислоты при воздействии на цементный камень образуют легкорастворимый хлористый кальций:
Са(0Н)2 + 2НС1^СаС12 + 2Н20.
Большой агрессивностью отличаются уксусная, молочная и винная кис лоты. рсобенно разрушительно действуют на цементный камень серно кислые соли MgS04, CaS04, NaS04 и др. Анион S03 при взаимодействии с Са(ОН)2 образует CaS04 • 2Н20, кристаллы которого по мере нарастания вызывают образование трещин и разрушение. При концентрациях суль фатных ионов БО^более 250 мг/л образуется гидросульфоалюминат каль ция с присоединением большого количества воды:
3CaS04 + 3Ca0 • А120 3 • 6Н20 + 25Н20-^ЗСа0 • А120 3 • 3CaS04 • 31Н20.
При этом объем новообразований увеличивается в 2 раза. В резуль тате этого, а затем под воздействием воды в теле цементного камня образуются трещины, из которых выделяются кристаллы гидросульфоалюмината в виде белого вещества (иногда его называют «цементной бациллой»). Возможно также разрушение и за счет кристаллизационного давления растущих кристаллов двуводного гипса в порах бетона (при вы сокой концентрации сульфатов).
Соли магния, содержащиеся в большом количестве в морской воде и встречающиеся в грунтовых водах, вступая во взаимодействие с Са(ОН)2, образуют гидроокись магния (не обладающую вяжущей способностью) и растворимые соединения:
MgCI2 + Ca(OH)2^M g(O H )2 + CaCl2.
При этом Mg(OH)2 осаждается в порах бетона, а СаС12 хорошо вымывается, что приводит к разрушению цементного камня.
Свободная углекислота в водной среде (сверх равновесного количества) также разрушающе действует на цементный камень, так как разрушает карбонатную пленку бетона вследствие образования хорошо растворимого бикарбоната кальция:
СаС03+ (С02)своб+ Н20-»-Са (НС03)2.
Коррозия бетона происходит при воздействии аммиачных удобре ний — аммиачной селитры и сульфата аммония. Аммиачная селитра, состоя щая из нитрата аммония NH4N03, подвергается гидролизу и дает в воде кислую реакцию. Нитрат аммония действует на гидрат окиси кальция:
Ca(0H)2 + 2NH4N03 + 2H20 = Ca(N03)2 • 4H20 + 2NH3.
Образующийся нитрат кальция хорошо растворяется в воде и вымы вается из бетона.
Разрушают цементный камень и масла, содержащие кислоты жирного ряда (льняное, хлопковое). Нефть и нефтяные продукты не представляют опасности для бетона, если они не содержат нефтяных кислот и сое динений серы.
Продукты разгонки каменноугольного дегтя, содержащие фенол, могут оказывать агрессивное воздействие на бетон.
Реакционно способные модификации кремнезема (опал, халцедон, вул каническое стекло), встречающиеся в заполнителях, могут вступать при обычной температуре в реакции со щелочами цемента, образуя студенис тые отложения белого цвета на поверхности зерен заполнителя. Разрушение бетона вследствие образования трещин, вспучивания и шелушения может наступить через 10— 18 лет после окончания строительства. Мерами защиты против коррозии являются: применение сульфатостойких цемен тов; создание плотных структур цементного камня; защита поверхности водонепроницаемыми пленками (битумными, полимерными веществами); об лицовка поверхности устойчивыми материалами.
§4.8. СВОЙСТВА ПОРТЛАНДЦЕМЕНТА И ЕГО ПРИМЕНЕНИЕ
Свойства портландцемента зависят от его минералогического состава, наличия добавок, а также тонкости помола клинкера. По этим характе ристикам определяют вид портландцемента (алитовый, белитовый, быстротвердеющий и т. п.).
Тонкость помола цемента характеризуют массой порошка, прошедшего сито № 0,08 (не менее 85%), и удельной поверхностью зерен, содержа щихся в единице массы цемента. Удельная поверхность обычных порт-
ландцементов |
2000 — 3000, быстротвердеющих 3500 — 5000 см2/г. |
||
Плотность |
портландцементов составляет |
3000 — 3200 кг/м3, |
насыпная |
объемная масса 900 — 1300 кг/м3 При |
расчете вместимости |
складов |
принимают объемную массу портландцемента равной 1200, а при его дозировании для приготовления бетонов— 1300 кг/м3
Наряду с этим свойства цемента характеризуются активностью и маркой по прочности, водопотребностью, сроками схватывания, изменением объема при твердении, тепловыделением.
Одним из важнейших свойств цемента является его активность — способность затвердевать при затворении водой, превращаясь в прочное камневидное тело.
Активность и' марку цемента ха |
|
|
||||||||
рактеризуют |
|
показатели |
прочности |
|
|
|||||
при изгибе образцов-балочек и их по |
|
|
||||||||
ловинок при сжатии в возрасте 28 сут. |
|
|
||||||||
Предел |
прочности |
при |
изгибе |
|
|
|||||
определяют |
на |
балочках |
размером |
|
|
|||||
40x40x160 мм, изготовленных из рас |
|
|
||||||||
твора |
пластичной консистенции |
сос |
|
|
||||||
тава |
1:3 — одна |
часть |
цемента |
и |
три |
|
|
|||
части |
Вольского |
песка |
(крупность |
|
|
|||||
зерен 0,53 — 0,85 мм) по массе при во |
|
|
||||||||
доцементном |
отношении |
0,4, |
уплот |
|
|
|||||
ненных на стандартной виброплощадке |
|
|
||||||||
и выдержанных в воде при тем |
|
|
||||||||
пературе 20±3°С 28 сут. Предел |
|
|
||||||||
прочности |
при |
сжатии |
определяют |
|
|
|||||
после испытания на изгиб на половин |
|
|
||||||||
ках |
балочки. |
Нарастание |
прочности |
|
|
|||||
происходит |
неравномерно: вначале на |
|
|
|||||||
3 сут она достигает 50%, а на 7 сут — |
|
|
||||||||
до 70% от прочности в 28-суточном |
Рис. 4.8. График нарастания прочности |
|||||||||
возрасте (рис. |
4.8). |
|
|
|
|
минералов портландцементного |
клин |
|||
В зависимости от активности и пре |
кера: |
С3А |
||||||||
дела прочности при изгибе портланд- |
1 - C2S; 2 - CAF; 3 - C2S; 4 - |
|||||||||
цементы подразделяют |
на |
марки |
400, |
|
|
500, 550 и 600 (табл. 4.3). Все факторы, способствующие увеличению степени гидратации, увеличивают и активность цемента.
Водопотребность цемента характеризуют показателем нормальной гус тоты — количеством воды, которое необходимо для достижения заданной пластичности. Обычно для портландцемента нормальная густота составляет 21 — 28%. Чем меньше водопотребность (нормальная густота), тем выше качество цемента.
Водопотребность цементазависит от минералогического состава (наи большая водопотребность у С3А, наименьшая — у C2S), тонкости помола. Активные добавки увеличивают водопотребность цемента.
Скорость схватывания цемента зависит от минералогического состава, тонкости помола, количества воды затворения, температуры. Так, повы шенное содержание трехкальциевого алюмината, большая удельная поверх ность, малое количество воды, повышенная температура среды ускоряют схватывание. Скорость схватывания является существенной технологи ческой характеристикой цемента. У портландцемента начало схватывайия должно наступать не ранее 45 мин, а конец — не позднее 12 ч от начала затворения. Обычно начало схватывания у портландцемента наступает через 2 — 3 ч, а конец — через 5 — 8 ч. Как быстрое, так и медленное схватывание затрудняет и усложняет организацию производства строитель ных работ.
|
|
|
|
|
Т а б л и ц а 4.3 |
|
Марка цемента |
Предел прочности, МПа |
Марка цемента |
Предел прочности, ААПа |
|||
при сжатии |
при изгибе |
при сжатии |
при изгибе |
|||
|
|
|||||
400 |
40,0 |
5,5 |
550 |
55,0 |
6,2 |
|
500 |
50,0 |
6,0 |
600 |
60,0 |
5,5 |
Процессы схватывания и твердения цемента сопровождаются выделе нием тепла (экзотермический эффект). Чем тоньше помол, больше в цементе С3А и C3S, а также стекловатой фазы, меньше взято воды для затворения, тем больше выделяется тепла, интенсивнее протекает твердение. Повышен ное тепловыделение цемента полезно при зимнем бетонировании изделий и вредно при бетонировании массивных сооружений.
Равномерность изменения объема при твердении определяют путем испытания цементных лепешек стандартного размера кипячением их в парах воды; при этом они не должны обнаруживать усадочных деформаций. Неравномерность изменения объема может быть обусловлена наличием в цементе окиси кальция, окиси магния и гипса. Цемент, неравномерно изменяющий объем при твердении, является недоброкачественным.
Применение и хранение портландцемента. Портландцемент применяют при изготовлении бетонных и железобетонных конструкций и изделий для наземных и подводных сооружений (за исключением агрессивной среды), устройства бетонных дорожных и аэродромных покрытий, приготовления строительных растворов, укрепления грунтов.
Цемент хранят в силосах, реже в сараях с обшивкой стен и крыш, не проницаемых для воды. Пол сарая должен быть плотным и приподнятым над поверхностью земли не менее чем на 30 см. При длительном хранении активность цемента снижается; интенсивность снижения активности зависит от минералогического состава, тонкости помола и др. Наименее устойчивы тонкомолотые цементы, содержащие повышенное количество С3А и C3S. Влажный воздух, соприкасающийся с цементом, значительно снижает его
активность. В среднем активность портландцемента |
снижается через 3 м'ес |
на К) 20%, через 6 мес на 15 — 30% и через |
12 мес на 25 — 40%. |
§ 4.9. ОСОБЫЕ ВИДЫ ПОРТЛАНДЦЕМЕНТА
Применение портландцемента в инженерных конструкциях, работающих в различных природных условиях, вызвало необходимость производства цементов, которые обладали бы требуемыми для этих целей свойствами. Достигнуть этого можно путем изменения минералогического состава цемента, тонкости помола, введения различных добавок.
Быстротвердеющий портландцемент представляет собой минеральное вяжущее, которое содержит C3S около 50—60%, С3А — 8—14%, а сум ма C3S и С3А должна быть не менее 60—65%. При повышенном содержа нии С3А увеличивают добавку гипса. Тонкость помола этого цемента увели чивают до удельной поверхности, равной 3500—4000 см2/г (вместо обычной 2500—3000 см2/г). Содержание активных минеральных добавок в нем не превышает 10%. Быстротвердеющий портландцемент обладает более ин тенсивным нарастанием прочности в начальный период твердения; при этом в возрасте 1 сут прочность его должна быть не менее 20 МПа, 3 сут — не ме нее 30 МПа.
При тонком помоле цемента увеличивается поверхность для создания условий более быстрого протекания сложных физико-химических процессов гидролиза и гидратации, а следовательно, и более полного использования *зерен цемента. Установлено, что при обычном помоле в реакцию гидратации и гидролиза вступают около 48% зерен цемента, остальная же часть остается в виде балласта.
Тончайшие частицы цемента размером около 10 мкм уже на 3 сут обеспе чивают прочность цемента примерно в 7 раз большую, чем частицы размером около 60 мкм.
по
С увеличением удельной поверхности зерен цемента от 2100 до 5000 см2/г предел его прочности в возрасте 28 сут возрастает с 40 до 55 МПа. Увеличение удельной поверхности дает положительный эффект только до определенной тонкости помола. При более тонком помоле (сверх оптимума) необходимо увеличивать количество воды затворения, а весьма быстрое протекание твер дения увеличивает тепловыделение, что связано с возможностью возникно вения усадочных деформаций и трещинообразования; в результате снижает ся прочность (например, в массивных элементах конструкции).. Цементы большой тонкости помола быстрее снижают активность при хранении.
Пластифицированный портландцемент приготовляют путем введения при помоле клинкера поверхностно-активных пластифицирующих добавок. В качестве пластифицирующей добавки обычно применяют сульфитно-дрож жевую бражку (сдб) в количестве 0,15—0,25% (в пересчете на сухое вещест во). Пластифицирующие добавки придают цементному тесту большую под
вижность, что позволяет снизить количество воды затворения, а это, в свою очередь, позволяет несколько уменьшить расход цемента в строительном растворе и бетоне. В то же время пластифицирующие добавки несколько увеличивают водопроницаемость и морозостойкость цементного камня.
Роль пластифицирующих добавок сводится к следующему. Кальциевые соли сульфолигниновых кислот (сдб), сорбируясь на поверхности зерен це мента, образуют коллоидные гидрофильные пленки, которые способствуют более полному смачиванию зерен цемента водой и препятствуют их агрегиро ванию. При затворении водой пленки сдб обеспечивают повышение пластич ности цементного теста. Указанная способность сдб проявляется эффектив нее в смесях цементов с песком и щебнем.
Пластифицированные цементы в первое время твердеют несколько мед леннее, чем обычные, однако в дальнейшем они приобретают ту же прочность.. В первые сутки твердения они более чувствительны к просыханию, поэтому нуждаются в тщательном соблюдении влажного режима. Пластифицирован ные портландцементы выпускают марок 400 и 500. Они более экономичны, требуют меньше воды затворения, применяются для тех же целей, что и обычные портландцементы, особенно для элементов, подвергающихся попе ременному увлажнению и просыханию, замораживанию и оттаиванию (бетон дорожных и аэродромных покрытий и гидротехнических сооружений).
Гидрофобный портландцемент изготавливают совместным помолом це ментного клинкера и гидрофобных поверхностно-активных добавок (0,15— 0,3%). В качестве таких добавок применяют мылонафт, асидол, олеиновую кислоту и др. Эти вещества, сорбируясь на поверхности зерен цемента, соз дают гидрофобную пленку, которая понижает способность цемента взаимо действовать с влагой воздуха. В результате гидрофобный цемент не снижает активность, и не комкуется при хранении и менее чувствителен к влажной воздушной среде.
При затворении гидрофобного цемента водой поверхностно-активные добавки вступают в реакцию с Са(ОН)2, образуют микропены, в результате чего происходит воздухововлечение. Цементное тесто при этом получается более пластичным, а цементный камень более "морозостойким.
Сульфатостойкий портландцемент — продукт тонкого помола клинкеэа, имеющего пониженное содержание С3А (не более 5%), C3S (не более 50%)
AI О
и глиноземистый модуль р ^ 3 не менее 0,6; допускается введение активных
добавок до 10—20%. Сульфатостойкий портландцемент выпускают марок 400 и 500. Его применяют для бетонных и железобетонных эле ментов сооружений, подвергающихся воздействию агрессивных (сульфат ных) вод, а также переменному увлажнению и высыханию, заморажива нию и оттаиванию.
ill
Для элементов сооружения, работающих в морской воде, предпочтительно применять сульфатостойкий пуццолановый портландцемент.
Белый и цветной портландцементы изготавливают путем обжига и помо ла чистых известняков, кварцевого песка и каолина. Затем их отбеливают пу тем трехминутного действия восстановительного пламени при 800—1000°С для перехода окиси железа в закись-окись железа. Цветные цементы получа ют помолом клинкера белого цвета со свето- и щелочностойкими пигментами (охра, окись хрома, железный сурик и др.). Белые и цветные (с минеральны ми пигментами) портландцементы используют для декоративных и отделоч ных работ. По степени белизны, определяемой коэффициентом отражения в процентах абсолютной шкалы, белый цемент подразделяют на три сорта: 1-й — не ниже 80%, 2-й — 75%, 3-й — 68%. Его выпускают марок 400 и 500.
Для дорожного строительства используют обычный, а также пластифици рованный и гидрофобный портландцементы. В дорожном портландцементе не допускаются тонкомолотые добавки, а также ограничивается содержа ние С3А (не более 8%). Рекомендуется следующий минералогический состав клинкера: 50—60% C3S; 15—25% C2S; 15—25% C4AF; Не более 8% С3А. Дорожный портландцемент выпускается марок 400, 500, 550 и 600.
§4.10. ПУЦЦОЛАНОВЫЕ ПОРТЛАНДЦЕМЕНТЫ
При твердении в портландцементе наряду с целым рядам гидратов обра зуется свободная гидратная известь, которая снижает устойчивость цемент ного камня в проточных, напорных и слабоминерализованных водах. Поэто му целесообразно вводить в цемент активные добавки, которые содержат активную (растворимую) форму кремнезема и глинозема. Они придают порт ландцементу повышенную водостойкость за счет взаимодействия активного кремнезема и глинозема с Са (ОН)2 и образования нерастворимых гидросили катов и алюмосиликатов.
Активные добавки по происхождению делят на природные и искусствен ные, а по химическому составу — на кислые (М< 1) и основные (М> 1), что определяется модулем
Са О + Mgp
S i02 + А12 0 3
Основные активные добавки в порошкообразном состоянии» будучи заме шаны водой, способны схватываться и медленно тверд^ть Кислые добавки самостоятельно твердеть не могут и приобретают это свойсТВО только при внесении в них возбудителей (воздушной извести, гипса и Др-)-
Природные активные добавки могут быть осадочного и вулканического происхождений. К добавкам осадочного происхождения относится: трепел — легкая, мучнистая, беловатая,’сильнопористая, богатая а^0рфным кремнезе мом порода; диатомит — легкая, весьма пористая, муцНИстая порода белого
или желтоватого цвета, содержащая аморфный |
кремнезеМ в |
количестве |
до 95%; опока — относительно твердая, сильнопористая порода |
01 светло- |
|
желтого до темно-серого цвета с содержанием |
aMoDfkHOro |
кремнезема |
до 80%. |
ф |
|
К добавкам вулканического происхождения относятся- вУлканический пепел — тонкораздробленная взрывами извержений лава с0с'ГОЯШ'ая из мелких зерен вулканического стекла и обломков других миНер'алО0 с преобладаю щим размером зерен менее 0,15 мм и содержащая SjQ оКоЛо 70%, А120 3 около 12%, СаО до 4—6%; вулканические туфы — сцентрованны е облом ки камневидной лавы со значительной примесью вулканицеСк0го пепла, кото-
рые вследствие быстрого охлаждения содержат много вулканического стекла; вулканические трассы — уплотненные и сцементированные отложения рых лого вулканического материала; пемзы — остывшие газовые лавы в смеси
свулканическими пеплами; ноздревато-пористые стекловатые куски, содер жащие значительное количество аморфного кремнезема.
Искусственные активные добавки — преимущественно отходы промыш ленности: доменные гранулированные шлаки; золы от сжигания бурых углей, торфа, горючих сланцев; горелые породы из терриконов угольных шахт; сиштоф — отходы заводов по производству алюминия; дегидратированная глина — глины, обожженные при 650—800°С; цемянки — молотый бой кера мических изделий (кирпич, черепица и др.). Активность добавок определяют по поглощению извести из известкового раствора через 30 сут (мг СаО на 1 г добавки): высокоактивные — 200 мг, среднеактивные— 100 и низкоактив ные — 50 мг. Добавки с активностью ниже 50 мг относят к инертным.
Пуццолановый портландцемент — гидравлическое вяжущее, получаемое совместным помолом портландцементного клинкера повышенного качества
с20—50% активных добавок и природного гипса. Гипса должно быть столь ко, чтобы содержание S03 в цементе не превышало 3,5%. Количество добав ки зависит от ее активности. Например, трепела добавляют 20—30, вулкани ческих пород (пемзу, пепел, туфы, трассы) — 25—40%.
Помол пуццоланового портландцемента должен быть более тонким
ине грубее обычного портландцемента. Этот цемент выпускают марок 300
и400. Цвет цемента светлый, плотность 2,7—2,9, объемная масса в рыхлом состоянии 1000—1200 кг/м3 Сроки схватывания примерно те же, что и у порт ландцемента, однако процесс твердения вначале (до 30 сут) протекает мед леннее, а затем в условиях достаточной влажности и при температуре выше 10°С становится несколько интенсивнее.
Для получения теста нормальной густоты пуццолановые цементы требуют больше воды (30—40% против 21—28% для обыкновенного портландцемен та), причем тесто обладает большой вязкостью, а бетонная смесь на этом це менте менее подвижна. При схватывании и твердении цемента выделяется меньше тепла. Пуццолановые цементы малопригодны для изготовления элементов Сооружений, которые должны работать в сухой среде или в услови ях переменного увлажнения и замораживания. Усадка и набухание при твер дении на воздухе и в воде у них больше, чем у портландцемента.
Эти особенности пуццолановых цементов объясняются повышенным со держанием активных добавок, причем в зависимости от их качества указан ные особенности проявляются в различной степени. При твердении образу ются гидросиликаты, гидроалюминаты, гидроферриты и гидроокись кальция. Вследствие наличия активного кремнезема гидратная известь, вступая в соединение с кремнеземом, медленно образует дополнительное количество гидросиликатов кальция, что приводит к снижению концентрации гидратной извести:
Са(ОН)2 + Si02-f #Н20 —>-CaO • Si02 • (п + 1)Н20.
Из-за того, что в пуццолановых цементах меньше гидроалюмината каль ция и гидратной извести, они обладают большей стойкостью к проточным и слабоминерализованным водам. Наряду с этим частицы активной добавки при взаимодействии с гидратной известью, образующейся при твердении цемента, во влажной среде набухают, что обусловливает уплотнение бетона. Это также способствует большей устойчивости бетонов на пуццолановых це ментах, так как повышенная плотность препятствует проникновению воды в тело бетона.
ИЗ
Для повышения сульфатостойкости пуццолановый портландцемент изго тавливают из клинкера с пониженным содержанием трехкальциевого алюми ната (не более 8%). Такой цемент называют сульфатостойким пуццолановым портландцементом.
Пуццолановый портландцемент применяют для подводных и подземных элементов сооружений, а также для элементов, работающих в слабоагрессив ной среде. Пуццолановый портландцемент не рекомендуется хранить на скла дах длительное время, так как он утрачивает активность быстрее, чем обыч ный цемент.
Местные вяжущие материалы могут быть изготовлены путем тщательно го перемешивания воздушной извести (15—25%) с тонкомолотой активной гидравлической добавкой (75—80%) или совместным помолом с добавлени ем не более 5% гипса. В зависимости от качества и вида добавки эти цементы называют: известково-кремнеземистые, нефелиновые (тонкий помол нефе линового шлака 65, извести 15 и гипса 5%), известково-трепельные, извест ково-зольные, известково-глинистые.
Они медленно схватываются и твердеют и обладают большой водопотребностью. При температуре ниже 10°С их не следует применять без искусственного прогрева.
Бетонные изделия с использованием этих цементов при автоклавной обра ботке (давлении 0,9 МПа и температуре 180°С) быстро твердеют, достигая прочности 20—40 МПа в результате взаимодействия гидрата окиси кальция с кремнеземом и образования гидросиликатов кальция. Интенсивность про цесса твердения зависит от тонкости помола и режима автоклавной обработ ки. В зависимости от свойств эти цементы применяют для приготовления строительных растворов и низкомарочных бетонов.
§ 4.11. ШЛАКОВЫЕ ЦЕМЕНТЫ
Доменные гранулированные шлаки, являющиеся основным сырьевым материалом для производства шлаковых цементов, по химическому составу приближаются к портландцементу, но содержат меньше СаО и больше крем незема и глинозема. Кроме окислов СаО, Si02 и А120 3, шлаки содержат в небольшом количестве MgO, МпО, FeO, CaS, FeS.
При быстром охлаждении в процессе грануляции шлаки приобретают стекловидную структуру (стекловидного вещества в основных шлаках 40— 50%, а в кислых 85—95%), в результате химическая энергия остается в них в потенциальном состоянии. Поэтому гранулированные доменные шлаки при совместном помоле с щелочными возбудителями (гидраты окиси кальция, окиси магния) или сульфатными (сульфаты кальция) приобретают способ ность при затворении водой схватываться и отвердевать. При взаимодейст вии с гидратной известью образуются гидроалюминаты и гидросиликаты кальция, а при соединении растворенных алюминатов с сульфатом кальция образуется кристаллический гидросульфоалюминат кальция. Эта особен ность доменных гранулированных шлаков используется при производстве шлаковых цементов.
Шлакопортландцемент — продукт тонкого совместного помола портландцементного клинкера с 20—60% доменного гранулированного шлака и гипса (не более 3% при пересчете на S 03). Шлакопортландцемент может быть по лучен также путем тщательного смешения раздельно измельченных компо нентов. Этот цемент по сухи является разновидностью пуццоланового порт ландцемента, в котором активной добавкой служит доменный гранулирован ный шлак.
Восновном шлакопортландцемент имеет те же показатели, что и пуццолановый портландцемент. Его плотность 2,8—3, объемная масса в рыхлом со стоянии 900— 1200 кг/м3, начало схватывания не ранее 45 мин, конец не позд нее 12 ч. Это медленнотвердеющий цемент; при понижении температуры за метно замедляет твердение. Повышение температуры во влажной среде эф фективно ускоряет твердение (пропаривание в камерах или запаривание в ав токлавах) .
Впроцессе твердения изделия на шлакопортландцементе необходимо длительное время выдерживать во влажной среде, так как преждевременное
просыхание оказывает отрицательное влияние на нарастание прочности. Он более устойчив, чем портландцемент, в агрессивных водах, но концентри рованные растворы магнезиальных солей разрушают цементный камень. Различные кислоты также разрушают его. Попеременное увлажнение и высы хание, а также замораживание и оттаивание вредно сказывается на.затвер девшем цементе.
Шлакопортландцемент выпускают марок 300, 400 и 500 с той же тонко стью помола, что и портландцемент. Он находит такое же применение в строи тельстве, как и пуццолановые цементы. Затвердевший цемент имеет синева тые и зеленовато-грязные оттенки, а затворенный водой выделяет в первые дни запах сероводорода. Активность шлакопортландцемента со временем понижается быстрее, чем портландцемента, поэтому не рекомендуется долго хранить его на складах.
Быстротвердеющий шлакопортландцемент получают совместным помо лом предварительно тонкоизмельченных в мельницах цементного клинкера, доменного гранулированного шлака и гипсового камня. Тонкость помола цемента должна быть 3500—4500 см2/г. Цементный клинкер должен содер жать 55—60% C3S и 10% С3А.
Быстротвердеющий шлакопортландцемент на 3 сут твердения нормально гораствора характеризуется прочностью при сжатии 20 и при изги бе 3,5 МПа.
Шлаковые (бесклинкерные) цементы изготавливают путем совместного помола доменных гранулированных шлаков с добавками извести, обожжен ного доломита и гипса. Для изготовления этих цементов необходимы только сушильные и помольно-смесительные установки. Шлаковые цементы бывают известково-шлаковые и сульфатно-шлаковые.
Известково-шлаковый цемент изготавливают путем тонкого помола смеси доменного гранулированного шлака и воздушной извести (преимущественно негашеной) в количестве 20—30% с добавкой 3—5% гипса. Это медленно схватывающийся и медленнотвердеющий цемент. Необходимым условием нормального твердения цемента является влажная среда. Он стоек против воздействия проточных и агрессивных вод, а также отличается большой мо розостойкостью, чем известково-пуццолановый цемент. При температуре наружного воздуха ниже 10°С применять известково-шлаковые цементы не рекомендуется. Эти цементы выпускают марок 50, 100, 150, 200. Срок схва тывания: начало не ранее 25 мин и конец не позднее 24 ч, при этом в первые 7— 10 сут твердение протекает медленно. Известково-шлаковые цементы утрачивают активность при длительном хранении, поэтому рекомендуется проверять их качество через каждые 2 мес. Эти цементы применяют для при готовления строительных растворов и бетонов низких марок.
Сульфатно-шлаковый цемент — продукт совместного тонкого помола до менного гранулированного шлака (75—85%) и гипса (15—20%) с добавка ми портлайдцементного клинкера до 5% или извести до 2%.
Сроки схватывания и особенности твердения те же, что и у известково шлакового цемента. При небольшом содержании гипса процесс твердения
ускоряют пропариванием, автоклавной обработкой или добавками СаС12. Сульфатно-шлаковые цементы применяют для приготовления строительных растворов и бетонов, для подземных и подводных сооружений, в том числе подвергающихся воздействию углекислых и сульфатных вод, наравне со шлакопортландцементом соответствующих марок.
Шлакощелочной цемент изготавливают путем совместного помола грану лированного шлака с соединениями щелочных металлов или затворения молотого гранулированного шлака растворами щелочных металлов (сода кальцинированная техническая, поташ, растворимое стекло с модулем до 2, отходы производства или побочные продукты, содержащие соединения щелочных металлов, дающие щелочную реакцию). Вследствие высокой кон центрации используемых растворов (20—50%) щелочь в этом случае являет ся активной составляющей вяжущего, участвующей в образовании водостойких щелочных гидратных новообразовании.
Для получения шлакощелочных цементов используют как основные, так и кислые шлаки; при этом изменяется тип щелочного компонента. Можно так же использовать отходы других производств (термофосфорные, ваграночные шлаки) и искусственные стекла. Для повышения активности шлакощелочно го вяжущего в смесь добавляют молотые стеклоподобные горные породы (перлиты, липариты, андезиты, базальты, диабазы) или молотые стекла искусственного происхождения (бой оконного, посудного стекла), добавки глинистых пород в естественном или обожженном состоянии. Расход щелоч ных компонентов по массе на 100% шихты составляет от 3 до 10%.
Шлакощелочные цементы имеют активность от 40 до 100 МПа. Тонкость помола цемента ЗОбО—3500 см2/г. Сроки схватывания шлакощелочных це ментов зависят от вида и количества щелочной добавки, состава и структуры шлака и добавок, тонкости их помола. Начало схватывания колеблется от 30 мин до 1ч, конец — от 2 до 5 ч и более. Сроки схватывания регулируют изменением тонкости помола цемента и количеством щелочного компонента.
На основе шлакощелочных вяжущих можно получать легкие и тяжелые бетоны с объемной массой 500—2400 кг/м3 и прочностью 2,5—100 МПа. Вследствие того, что компоненты вяжущего вступают во взаимодействие с глинистыми минералами, в качестве заполнителей в таких бетонах можно использовать мелкие пески, супеси, легкие суглинки.
§4.12. ГЛИНОЗЕМИСТЫЕ (АЛЮМИНАТНЫЕ) ЦЕМЕНТЫ
Глиноземистый цемент — продукт тонкого помола предварительно из мельченного клинкера, полученного сплавлением или спеканием пород, бога тых глиноземом, с известняком, взятых в определенном соотношении.
Для производства глиноземистых цементов используют бокситы — осадочные горные породы, состоящие преимущественно из гидратов глинозе ма с примесью гидрата окиси железа, кварца и др. Кроме бокситов, которые имеют ограниченное распространение в природе, для изготовления глинозе мистых цементов применяют также некоторые отходы промышленности, бога тые глиноземом (доменные глиноземистые шлаки).
Глиноземистые цементы изготовляют способом сплавления или спекания сырьевой смеси. В первом случае предварительно дробленый боксит сушат в барабане при температуре до 800°С, что облегчает его дальнейшее измель чение. Подготовленный боксит направляют в силос, а'затем в необходимом количестве подают в печь. Туда же загружают потребное количество предва рительно обожженного известняка. Плавить можно в ваграночных, домен ных или электрических печах при температуре 1500—1650°С. Расплав цемент
ного клинкера сливают в изложницы, в которых и происходит медленное его остывание. После выдерживания на складе чушки сплава дробят, а затем раз малывают в многокамерных мельницах.
Во втором случае боксит после высушивания и дробления загружают в силос, куда дозируют подсушенный и раздробленный известняк. Затем под готовленную шихту увлажняют, брикетируют в кирпичи и подают в печь для обжига. Во вращающихся печах обжиг можно вести сухим и мокрым спосо бами; в последнем случае шихта не брикетируется. После спекания цемент ный клинкер направляют на склад, затем подвергают тонкому размолу и транспортируют в силосы готового цемента.
Глиноземистый цемент содержит около 50% глинозема, до 45% окиси кальция, 5—10% кремнезема и 1— 15% окиси железа. Главными составляю
щими |
цемента являются СаО • А120 3; 5СаО • ЗА120 3 и СаО • 2А120 3, неко |
торое |
количество 2СаО • Si02 и инертная составляющая 2СаО • Si02 • |
• А120 3 (геленит). |
При затворении глиноземистого цемента водой основное соединение — однокальциевый алюминат, входящий в его состав, энергично реагирует с во дой, образуя
2(СаО • А120 3) + ЮН20-+2Са0 • А120 3 • 8Н20 + А120 3 • ЗН20.
Если цемент твердеет при температуре выше 20—25°С, возможно образо-. вание трехкальциевого гидроалюмината ЗСаО • А120 3 • 6Н20. Другие соеди нения цемента — алюминаты, ферриты и силикаты кальция — подвергают
ся |
гидратации или гидролизу и образуют гидроалюминаты, гидроферриты |
и |
гидросиликаты кальция. |
|
Отсутствие в затвердевшем.при нормальных условиях цементе свободной |
гидратной извести и, как правило, трехкальциевого гидроалюмината обуслов ливает его устойчивость в проточных и агрессивных водах. Концентрирован ные же растворы сернистого магния, щелочей и сильные кислоты разрушают затвердевший цемент.
Глиноземистый цемент — быстротвердеющий вяжущий материал. Его марки (400, 500, 600) устанавливают по показателю прочности нормаль ного раствора на 3 сут. Глиноземистые цементы можно также выпускать мар ки 700.
После 3 сут твердения прочность цементного камня возрастает к 28 сут на 30—40%. При схватывании и твердении цемент выделяет много тепла. Нормальными условиями твердения считаются такие, когда температура бе тона или раствора на глиноземистом цементе не превышает 25°С. В случае превышения этой температуры бетон (или раствор) нуждается в охлаждении и усиленной поливке водой. Сроки схватывания цемента: начало не ранее 30 мин, а конец не позднее 12 ч.
Растворы на глиноземистом цементе более вязкие, поэтому время переме шивания смесей необходимо увеличивать примерно в 2 раза по сравнению с портландцементом, а отношение взятой для затворения воды к цементу должно быть не менее 0,5—0,6. Глиноземистый цемент нельзя смешивать с портландцементом, так как при этом резко понижается прочность последне го. При длительном хранении (6—12 мес) прочность цемента снижается не значительно.
Глиноземистый цемент применяют при срочных бетонных работах, при производстве работ зимой, восстановительных работах, для тампонажных работ и элементов бетонных сооружений, находящихся в зоне агрессивных
вод.
Гипсоглиноземистый расширяющийся цемент получают тщательным смешиванием тонкоизмельченных высокоглинистых доменных шлаков и при
родного двуводного гипса. Начало схватывания цемента не ранее 10 мин, а конец не позднее 4 ч от начала затворения. Линейное расширение образцов, изготовленных из цементного теста нормальной густоты, через 3 сут должно быть не менее 0,1 и не более 0,7%. Предел прочности при сжатии половинок образцов-балочек, изготовленных из раствора состава 1:3, через 3 сут твер дения должен быть не менее 20 МПа.
Такие цементы необходимы для заделки стыков сборных железобетонных
ибетонных элементов, для зачеканки стыков тюбингов, труб, для торкретной гидроизоляции, изготовления безусадочных и расширяющихся, водонепрони цаемых бетонов и растворов.
Расширяющийся цемент, предложенный В. В. Михайловым, изготавлива ют путем смешения глиноземистого цемента (около 70%) и расширяющейся добавки, состоящей из 10% высокоосновного гидроалюмината и 20% гипса. Начало схватывания этого цемента не ранее 4 мин, конец не позднее 10 мин. Линейное расширение во влажной среде 0,5—1%, на воздухе не менее 0,05%. Для замедления схватывания цемента в необходимых случаях к нему добав ляют сульфитно-дрожжевую бражку в количестве 0,5%.
Ряд ученых (П. П. Будников, И. В. Кравченко, О. П. Мчедлов-Петросян
идр.) предложили составы расширяющихся цементов. Например, И. В. Крав ченко разработала расширяющийся цемент, который приготовляют путем совместного помола портландцементного клинкера (58—63%), высокогли ноземистого шлака (5—7%), двухводного гипса (7—10%) и доменного гранулированного шлака (23—28%).
Напрягающийся цемент (НЦ), предложенный В. В. Михайловым,— быстросхватывающийся и быстротвердеющий вяжущий материал, получае мый путем совместного измельчения портландцементного клинкера (65— 70%), высокоглиноземистого шлака (16—20%) и двухводного гипса (14—
16%). Высокоглиноземистый шлак должен содержать более 40% А120 3 и менее 10% Si02. С помощью этого цемента можно напрягать арматуру од новременно во многих направлениях, что трудно сделать другими способами напряжения арматуры. При твердении напрягающего цемента сначала возни кает низкосульфатная форма гидросульфоалюмината (ЗСаО • А120 3 •
• CaS04 • 12Н20), которая затем переходит в высокосульфатную — эттрингит, что вызывает расширение цемента до 3—4%. При этом сильно уплотня ются его поры и, будучи достаточно прочным, расширяющийся цементный камень сильно напрягает арматуру. После образования эттрингита дальней шего расширения цемента не происходит. Регулируя состав цемента, можно не допустить больших внутренних напряжений. Начало схватывания напря гающего цемента 2—8 мин, а конец 6—15 мин. Замедляют схватывание це мента добавки сульфитно-дрожжевой бражки. Прочность НЦ обычно высо кая и достигает 80 МПа (марки НЦ-500, НЦ-600). Затвердевшие образцы обладают высокой водонепроницаемостью, выдерживают давление воды до 2,1 МПа.
Напрягающийся цемент целесообразно применять для изготовления на порных железобетонных труб, водонепроницаемых резервуаров, а также для устройства дорожных и аэродромных цементобетонных покрытий.