
- •ВВЕДЕНИЕ
- •СОСТАВ, СТРУКТУРА И ОСНОВНЫЕ СВОЙСТВА ДОРОЖНО-СТРОИТЕЛЬНЫХ МАТЕРИАЛОВ
- •ПРИРОДНЫЕ КАМЕННЫЕ МАТЕРИАЛЫ
- •ИСКУССТВЕННЫЕ МАТЕРИАЛЫ НА ОСНОВЕ МИНЕРАЛЬНЫХ ВЯЖУЩИХ И МЕЛКОЗЕРНИСТЫХ ЗАПОЛНИТЕЛЕЙ
- •БЕТОНЫ (ЦЕМЕНТОБЕТОНЫ)
- •СБОРНЫЕ БЕТОННЫЕ И ЖЕЛЕЗОБЕТОННЫЕ ИЗДЕЛИЯ
- •МАТЕРИАЛЫ И ИЗДЕЛИЯ ИЗ ПЛАСТМАСС
- •ОРГАНИЧЕСКИЕ ВЯЖУЩИЕ МАТЕРИАЛЫ
- •АСФАЛЬТОБЕТОН
Г л а в а 5
ИСКУССТВЕННЫЕ МАТЕРИАЛЫ НА ОСНОВЕ МИНЕРАЛЬНЫХ ВЯЖУЩИХ И МЕЛКОЗЕРНИСТЫХ ЗАПОЛНИТЕЛЕЙ
§ 5.1. СИЛИКАТНЫЕ МАТЕРИАЛЫ
Минеральные вяжущие материалы используются в строительстве преиму щественно для создания искусственных каменных материалов с конгломератной структурой, в которых они выполняют роль минерального клея вслед ствие их способности образовывать пластичное тесто и при затвердевании склеивать в монолит зерна различных заполнителей — рыхлых каменных материалов (гальки, гравия, щебня). Склеивание зерен заполнителя обуслов лено хорошей адгезией или химическими реакциями вяжущего с поверх ностью зерен заполнителя. Минеральные вяжущие, взаимодействуя с водой, затвердевают, однако в этом случае образовавшийся камень обладает повы шенной усадкой, ползучестью, трещиноватостью, недостаточной коррозион ной стойкостью, повышенной .тепло- и звукопроводностью. Смешение вяжу-, щих с заполнителями позволяет получить искусственный камень со значи тельно лучшими свойствами. Например, камень, образованный в результате взаимодействия воды и извести, обладает невысокой прочностью. В то же время смесь из извести, воды и песка, особенно молотого, затвердевая при определенных условиях, образует прочный искусственный камень (50 МПа и более). Если необходимо улучшить звукоили теплоизоляционные свойства, используют заполнители из пористых шлаков, перлитов и т. д. Наряду с улуч шением свойств значительно снижается стоимость изделий, изготовленных из смеси вяжущего и заполнителей; последние в несколько раз дешевле из вести, гипса и особенно цемента.
По виду вяжущего различают силикатные, гипсовые, цементные и другие материалы. Иногда наименование материала учитывает заполнитель (асбо цемент, перлитобетон и т. п.). Выделяют одно-, двух-, трех- и более компо нентные материалы, мелко-, средне- и крупнозернистые (соответственно круп ность зерен заполнителей менее 5, 20 и более 20 мм).
Несмотря на многообразие искусственных каменных материалов, получен ных на основе минеральных вяжущих, технологический процесс обычно вклю чает такие операции: подготовка компонентов и их дозирование; приготовле ние смеси; формование изделий с уплотнением смесей; твердение заформованных изделий в благоприятных условиях. В результате затвердевания в искусственных каменных материалах образуется сложная структура.
К' искусственным каменным материалам с мелкозернистой структурой можно отнести силикатные, гипсовые, магнезиальные, асбестоцементные материалы и строительные растворы. В большинстве случаев это двухком понентные материалы. В силикатных материалах, чтобы получить высокую прочность, необходима большая удельная поверхность взаимодействия квар цевого песка и извести, поэтому в ряде случаев песок размалывают до 2000— 2500 см2/г, что ограничивает крупность зерен песка. В строительных раство рах крупность заполнителей зависит от условий их применения (толщины
шва, слоя штукатурки и др.).
Повышение крупности зерен заполнителей больше 10 мм не рекоменду ется в силикатных материалах вследствие возникновения в них больших внут ренних напряжений. Используются мелкозернистые заполнители также и в других двухкомпонеитиых материалах.
Силикатные (известково-песчаные) изделия изготавливают из смеси кварцевого песка и воздушной извести (иногда и добавок) с последующим
перемешиванием, |
механической формовкой и запариванием в автоклаве |
при температуре |
180°С и давлении до 1 МПа. |
Наличие в большинстве районов основного сырья (кварцевого песка, воз душной извести), сравнительно небольшой расход топлива, а также возмож ность полной механизации и автоматизации технологии изготовления явились факторами быстрого роста производства силикатных изделий раз личного вида. Этому способствовали исследования А. В. Волженского,
П.П. Будникова, Ю. М. Бутта, П. И. Боженова, О. П. Мчедлова-Петросяна,
И.А. Хинта и др.
Сущность технологии производства силикатных изделий заключается в следующем. При тщательном перемешивании кварцевого песка с воздуш ной известью, влажности смеси 7—10% и дальнейшем ее уплотнении сырцо вое изделие при выдерживании на воздухе медленно затвердевает, достигая прочности 1-—2 МПа. Гидратная известь вступает в реакцию с кремнеземом, образуя в общем случае гиросиликат кальция:
Са (OH)2-f Si02-h т Н 20 —>-CaOSi02 • мН20.
В зависимости от температуры среды и состава смеси при взаимодействии водного раствора извести с Si02 в щелочной среде образуются различные кристаллохимические формы гидросиликатов кальция, преобладание которых обусловливает свойства готовых изделий. В процессе автоклавной обработки лишь часть гидратной извести вступает в физико-химическое взаимодействие, образуя гидросиликат кальция — основное цементирующее вещество. Значи тельная часть гидратной извести остается свободной и при дальнейшем вы держивании изделий на воздухе в поверхностных слоях вступает в реакцию с углекислым газом воздуха, т. е. карбонизируется. Остальная часть извести постепенно кристаллизуется, увеличивая со временем прочность изделий. Для ускорения твердения при запаривании в автоклаве в сырцовую смесь иногда добавляют небольшое количество сульфата натрия или магния.
В настоящее время изготавливают силикатный кирпич, силикатные бето ны (тяжелые, легкие и ячеистые).
Силикатный кирпич получают из смеси чистого кварцевого песка, воздушной извести (5—8%) и воды (около 7%). Из нее формуЮт СЬф ц0Вые’ ИЗделиЯ) которые подвергают автоклавной обработке с последующим выдерживанием на воздухе. Песок должен быть чистым кварцевым, равномерным по зерново му составу, без полевого шпата, слюды и гипса. Небольщ0е количество пыле ватых зерен (менее 0,15 мм) является положительным признаком. Смесь песка и воздушной извести подготавливают гидратным или сухим способом. При гидратном способе песок смешивают с гидратной известью (пушонкой или известковым тестом). Более распространен сухой способ, при котором в песок добавляют тонкомолотую негашеную известь и тщательно перемеши вают в мешалках с увлажнением смеси. Далее смесь транспортируют в силосы, где она выдерживается 8—10 ч до полного гашения извести. Эффективно используется тепло, выделяемое при гидратации извести Дополнительный подогрев смеси паром сокращает процесс силосования На 2_4 ч.
Сухую смесь можно подготовить в вращающихся барабанах_ГИДрат0рах? где гашение извести протекает в течение 30 мин. ПодогреТую смесь перемеши вают (дополнительно на бегунах), формуют кирпичи на механических прес сах с вращающимся столом (рис. 5.1) и осторожно з а г р у ^ ^ ваГ0нетки для перемещения в автоклавы (цилиндры длиной 20 и диаметром 2 м). В автокла вах кирпич выдерживается при температуре 175°С в течение 10 ч (1—2 ч
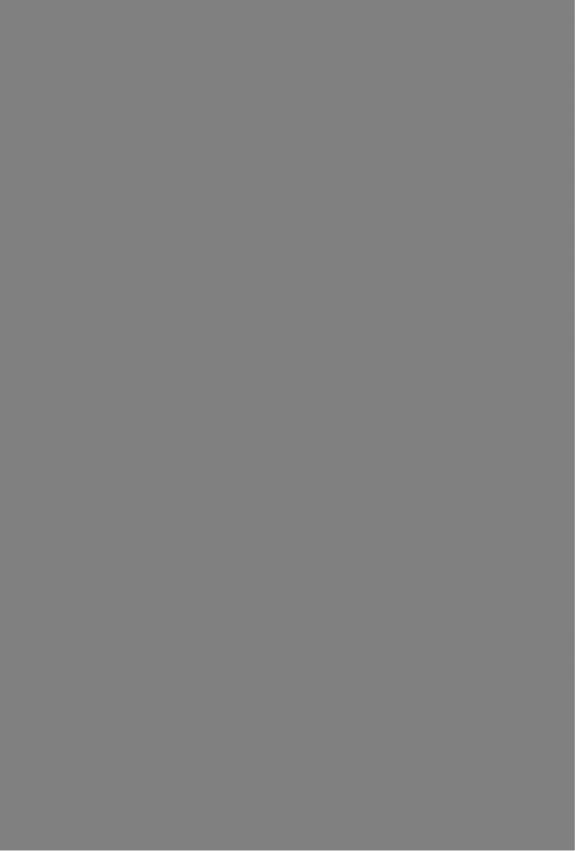
Гипсовые изделия изготавливают из гипсового теста и небольшого коли чества тонкомолотых органических заполнителей, а гипсобетонные изде лия — из гипсового теста и пористых заполнителей (предельная крупность зе рен не больше 10 мм), которые могут быть минеральными (шлаки, ракушеч ники) и органическими (опилки, сечка из камыша и др.). В ряде случаев изде лия из гипса армируют деревянными рейками, камышом и т. п. СУальную арматуру не применяют вследствие ее коррозии в гипсовом камне. Гипсовые изделия характеризуются хорошими тепло- и звукоизоляционными показате лями, легко обрабатываются, окрашиваются. Они не водостойки, поэтому их применяют в помещениях с относительной влажностью воздуха менее 60%. К гипсобетонным изделиям относят панели, плиты перегородок, камни для стен, перекрытий, облицовочные листы (гипсовая сухая штукатурка). Гипсо вые и гипсобетонные изделия изготавливают по технологической схеме: под готовка и дозирование компонентов смеси; перемешивание смеси; формова ние и твердение изделий — сушка до воздушно-сухого состояния. При этом изделия формуют литьем, вибрированием, прессованием, прокатом.
Особенно широкое распространение получил непрерывный прокат пане лей, однако возможно использование кассет и других способов. Прочность гипсовых изделий от 3,5 до 10 МПа при влажности до 8%.
Гипсовая сухая штукатурка состоит из тонкого слоя затвердевшего гипса, покрытого с обеих сторон картоном. Обычно листы изготавливают на специ альном конвейере.
Для кладки стен и зданий невысокой долговечности используют гипсовый камень как местный строительный материал. Прочность гипсовых камней 3,5—7 МПа, они должны выдерживать 15-кратные попеременные заморажи вания и оттаивания.
Гипсовые изделия применяют также в качестве вкладышей для заполне ния перекрытий жилых зданий.
§ 5.3. АСБОЦЕМЕНТНЫЕ ИЗДЕЛИЯ
Асбоцементные изделия изготавливают из смеси волокнистого асбеста цемента, воды, а в необходимых случаях и добавок. Такую тщательно пере мешанную смесь после формовки пропаривают с последующим выдержива нием на складе. В качестве составляющих для изготовления асбоцементных изделий применяют волокнистый хризотил-асбест (водНЬ1д силикат магния) с длиной волокон от 2 до 22 мм и портландцемент марок 400—500 содержа щий не менее 50% ЗСаО • Si02 и 6—12%ЗСаО • А12о з.
Асбест обладает высокой сорбирующей способностью энергично погло щая на поверхности волокон продукты гидролиза и гидратации цемента. Кроме того, он выполняет роль как бы арматуры, воспринимая в основном растягивающие напряжения. Эти свойства асбеста °бусЛ0ВЛИвают ВЫС(Жую прочность асбоцементных изделий при растяжении. В Зависимости от вида
асбоцементных изделий количество асбеста принимают в пределах 9_18% а для труб до 20%. °’
Изготовление асбоцементных изделий состоит из следующих технологи ческих процессов: распушивание асбеста вначале на бегунах до возможно более тонких волокон; дальнейшее его распушивание в специальной мешалке в смеси с цементом и водой; разжижение смеси водой в.Металлической ваннеизготовление листовых изделий на формовочной йащице. разрезание листа на плитки требуемых размеров; прессование на гиДРа’ВЛИЧ£ском прессе;
обрезка и пробивка отверстий для крепежа; пропаривание и выдерживание в теплой среде в течение 5—7 сут.
Для изготовления профилированных асбоцементных листов смесь укла дывают равномерным слоем в металлические формы и раскатывают при по мощи скалок. Асбоцементные трубы изготавливают на трубоформовочных машинах со съемными форматными барабанами. Трубы больших диаметров до пропаривания выдерживают 2 сут, предварительно освобождая от сердеч ников через 2—6 ч после изготовления.
Для ускорения процессов твердения асбоцементные изделия вместо про паривания подвергают автоклавной обработке. В этом случае целесообразно вводить в смесь тонкомолотый песок или продукт тонкого помола портландцементного клинкера с кварцевым песком.
Асбоцементные изделия обладают высокими прочностью (при сжатии 60—100, при растяжении 10—25 МПа), морозостойкостью, огнестойкостью, долговечностью, малой водопроницаемостью. Объемная масса асбоцемент ных изделий 1600—2100 кг/м5 Кровельные материалы из них можно изго тавливать цветными, покрывая цветной глазурью, или вводя в смесь щелоче стойкие пигменты.
Асбоцементные заводы выпускают плитки кровельные плоские, листы про фильные, листы облицовочные плоские, трубы водопроводные (напорные) и канализационные (безнапорные) и др. Стыки труб соединяют асбоцемент ными муфтами или делают трубы с монолитными раструбами.
§ 5.4. МАГНЕЗИАЛЬНЫЕ МАТЕРИАЛЫ
Магнезиальные материалы изготавливают из смеси древесных опилок или стружек и каусти ческого магнезита (каустического доломита), затворенных преимущественно раствором хло ристого магния. После уплотнения магнезиальные материалы выдерживают до затвердевания в теплой среде. Наиболее распространенными магнезиальными материалами являются ксилолит (в переводе с греческого языка — деревокамень) и фибролит (волокнистый камень).
Ксилолит изготавливают из смеси магнезиальных вяжущих и древесных опилок (сосны, ели, осины) в соотношении по объему 1:2 или 1:4 (на одну часть вяжущего две или четыре части опилок), затворяя раствором хлористого магния. В необходимых случаях в смесь добавляют минеральные краски (мумию, охру, железный сурик и др.) Для увеличения износостойкости ксилолита в смесь вводят до 20% асбеста, шлаковой ваты и др.
При устройстве ксилолитовых бесшовных полов и ступеней на основание наносят в один-два слоя смесь, уплотняют и после затвердевания в теплой среде выравнивают, затирают жидким магнезиальным тестом и шлифуют. Для увеличения водостойкости ксилолитовый пол после от делки примерно через 1 мес необходимо обработать олифой и натереть воском. Ксилолитовые полы можно устраивать сборными из плиток, изготовленных путем прессования массы под давлением до 30 МПа. Плитки укладывают на строительный раствор магнезиального цемента или портландцемента. Ксилолитовые плитки с наполнителем из дробленого мрамора или дру гих цветных пород называют террацоксилолитом.
Из ксилолита, кроме полов, изготавливают подоконные плиты, отделывают стены. Ксилолит обладает объемной массой около 1200 кг/м3, пределом прочности при сжатии 20—40 МПа,
а прессованный — около 60 МПа.
Фибролит изготавливают из древесных стружек (или растительной костры) с магнезиаль ным вяжущим, затворенным водным раствором хлористого магния. Из смеси прессуют плиты, а затем их сушат. Плиты изготавливают размерами 200x50, 200x70 и 150x50 см при тол щине 5 и 10,7 см. Объемная масса фибролитовых изделий 500— 550 кг/м3, предел прочности при изгибе не менее 1 МПа, влажность не более 25%. Фибролитовые плиты применяют в каче стве стенового, перегородочного и утепляющего материала.
§ 5.5. СТРОИТЕЛЬНЫЕ РАСТВОРЫ
Строительные растворы — рационально составленные смеси вяжущего (цемента, гипса, извести и др.), песка, воды и добавок. В зависимости от на значения строительные растворы бывают:
кладочные — для кладки стен, столбов, фундаментов, сводов, в качестве материала, скрепляющего кирпичи, бутовые камни и блоки в монолит;
штукатурные — для штукатурки (придания ровности) внутренних и внеш них поверхностей конструктивных элементов сооружений;
растворы для изготовления блоков, панелей, плит и устройства полов;
специальные — тепло- и гидроизоляционные, акустические, декоратив ные и др.
По роду вяжущего строительные растворы бывают: цементные, гипсовые, известковые; простые — при использовании одного вида вяжущего материа ла, сложные — двух и более.
По условиям твердения различают растворы гидравлические (на цемен тах) и воздушные (на извести, гипсе, растворимом стекле).
Для придания необходимых свойств в -них вводят добавки: пластифици рующие, гидрофобизирующие, наполнители, пигменты и др.
Основные свойства растворов. Качество свежеприготовленных растворов определяется подвижностью, расслаиваемостью, водоудерживающей способ ностью и объемной массой.
Подвижностью растворной смеси называют ее способность растекаться под действием собственной массы или приложенных к ней внешних сил. Подвижность определяют с помощью стандартного прибора (рис. 5.2) по глу бине свободного погружения конуса в растворную смесь. Степень подвиж ности выбирают в зависимости от условий применения смеси, от состава и свойств исходных материалов. Степень подвижности возрастает с увеличе нием расхода воды в смеси. Однако содержание воды в смеси не должно пре вышать определенного предела, выше которого происходит расслаивание.
Расслаиваемость растворной смеси характеризуется ее неоднородностью по толщине слоя, образующейся при хранении или вибрировании.
Неоднородность смеси определяют по разности объемов погруженного конуса в образцы уплотненной в сосуде вибрированием растворной сМеси, взятой из верхней и нижней частей сосуда.
Расслаиваемость растворных смесей в значительной мере определяется их водоудерживающей способно стью, характеризуемой количеством воды, которая прочно удерживается поверхностью минеральных зерен. Смесь становится малоподвижной, когда легко отделяется вода.
Это снижает производительность труда, ухудшает качество раствора, уменьшает степень сцепления раст вора с основанием.
•Водоудерживающую способность оценивают раз ницей в прочности стандартных образцов, выдержан ных на пористом и плотном основании. Хорошей удобоукладываемостью (удовлетворительные показатели по движности, расслаиваемости и водоудерживающей способности) обладают цементные растворы состава 1:3—1:4. Однако стоимость этих растворов велика, поэтому применяют более тощие растворы. Чтобы повысить водоудерживающую способность, уменьшить расслаиваемость в толщине растворной смеси, вводят тонкоизмельчен^ые добавки (золу, шлак, трепел и др.), а также известковое и глиняное /тесто. Удобоукладываемость растворимых смесей можно значительно улучшить путем введения в них поверхностно-активных веществ (0,1—0,3% от массы цемента).
Прочность затвердевшего раствора определяют испытанием на сжатие образцов-кубиков размером 7,07 см в возрасте, установленном в стандарте на данный вид раствора. Образцы растворной смеси подвижностью менее 5 см изготавливают в формах с поддоном, а из смеси подвижностью 5 см и более — в формах без поддона на пористом о с 11(>и«i мин (на поверхности сухого кир пича). Строительные растворы по п р о ч н о сти и 28-суточном возрасте при сжа тии делят по маркам: 4, 10, 25, 50, 75, 100, 150, 200.
Прочность затвердевшего раствори и основном зависит от активности вяжущего, его количества, водовяжупцто отношения, объемной массы и условий твердения. При отсутствии отсоса воды пористым основанием проч ность цементного раствора в возрасте 28 сут можно определить по эмпи рической зависимости, предложенной проф. Н. А. Поповым:
Яраст = 0,25/?ц(Ц /В -0,5),
где /?ц — активность цемента; Ц/В — цементно-водное отношение.
Если растворы твердеют на пористом основании, то их прочность увеличи вается примерно в 1,5 раза. Для смешанных растворов прочность в аналогич ных условиях может быть определена по формуле
D |
_n 95_____ —___ |
Ц + Д |
0,4 |
1 |
« р а с т - U . ^ j + /Cj д щ |
В |
|||
|
|
|
|
где Д /U — отношение добавки к цементу по массе; К\ — коэффициент для различных добавок, составляет 1,3—2.
При укладке раствора на пористое основание основным фактором проч ности является относительное содержание вяжущего материала. В соответ ствии с этим для цементных растворов ориентировочно прочность можно определить по формуле
Яраст = */? ц (//-0 ,0 5 )+ 4 ,
где Ц — расход цемента на 1 м3 песка, м3; k — коэффициент, равный 0,8 для среднезернистого и 0,5—0,7 для мелкозернистого песков.
Морозостойкость растворов зависит от свойств вяжущего, водовяжущего отношения, условий твердения растворов. Установлено девять марок раство ра по морозостойкости — от 10 до 300. Определяют морозостойкость на тех же образцах, что и прочность растворов.
Материалы для строительных растворов. В растворах используют портландцементы, пуццолановые и шлакопортландцементы невысокой актив ности. Экономичные составы растворов получаются, если R JR paCT = = 3,5—4. С целью экономии гидравлических вяжущих и улучшения техноло гических свойств растворных смесей применяют смешанные вяжущие (цемент и известь, цемент и глину и др.). \
Известь для строительных растворов применяют в виде молотого (нега шеного) порошка или известкового теста. Можно применять жирную и то щую известь. Гипс используют главным образом в штукатурных растворах как добавку к извести. В кладочных растворах гипс применяется редко.
В растворах обычно применяются природные (тяжелые) пески — кварце вые, полевошпатные и искусственные (легкие) — из туфа, пемзы, шлака и др. Для высоких марок растворов (больше 100) пески должны удовлетворять тем же требованиям в отношении содержания вредных примесей, что и пески для бетона. Для растворов марок 50 и менее допускаются пески с содержани ем до 10% пылеватых и глинистых частиц, но без органических примесей.
Крупность песков выбирают с учетом толщины шва в кладке. Крупнозер нистые пески предельной крупностью 5 мм применяют только при бутовой кладке. Для кладки кирпича и других камней применяют пески предельной крупностью менее 2 мк.
Для улучшения удобоукладываемости в растворные смеси вводят пласти фицирующие добавки. В качестве такой добавки в цементных и известковых растворах может быть эффективно использована глина, но ее не должно быть больше, чем вяжущего. Глину в раствор вводят ввиде глиняного молока или (что хуже) тонкомолотого порошка. Глина как пластифицирующая добавка не должна содержать органических Ьримесей и легкорастворимых солей. В растворы могут быть введены тонкомолотые гидравлические добавки трепе ла, вулканического пепла и др.
Для улучшения технологических свойств в растворные смеси вводят по верхностно-активные вещества, например сульфитно-спиртовую бражку (0,1—0,3% от массы вяжущего), омыленный древесный пек, мылонафт и др. Эти добавки улучшают морозостойкость, уменьшают водопоглощение и усад ку растворов. При использовании зимой в растворы вводят ускорители твер дения и понизители температуры замерзания (хлористый кальций и хло ристый натрий), а также материалы, выделяющие тепло (хлорная известь, известь-кипелка, поташ).
Растворы для каменной кладки. Подвижность кладочных растворов выби рают в зависимости от вида кладки, свойств основания (камня), уплотнения
итемпературы воздуха (табл. 5.1).
Вусловиях влажности и агрессивной среды, а также если требуется высо кая прочность раствора, применяют гидравлические растворы, в которых ис пользуются цементы средней и низкой активности и различные добавки-
пластификаторы. При постоянном и переменном увлажнении конструкций в растворы вводят гидрофобные поверхностно-активные добавки.
Известковые растворы используются для каменных кладок с небольшой прочностью, не подверженных увлажнению и температуре более 70°С. Проч ность этих растворов при сжатии составляет около 0,2—0,4 МПа. Для повы шения прочности и водостойкости в известковые растворы вводят добавки цемента. В известковых растворах экономичнее применять известковое тесто, чем известь-пушонку вследствие ее более глубокой дисперсности.
Марку раствора для укладки устанавливают проектом. При этом обычно руководствуются данными табл. 5.2. Составы растворов низких марок (до 50) выбирают по специальным таблицам (табл. 5.3). Количество воды в растворах устанавливают опытным путем .в зависимости от необходимой подвижности.
Состав растворов высоких марок рассчитывают с последующей проверкой их опытным путем. Расчет ведется следующим образом.
Т а б л и ц а 5.1
|
Подвижность раствора, определяемая погруже |
|||
|
|
нием конуса, см |
||
Вид кладки |
при пористом основа |
при |
плотном основа |
|
|
||||
|
нии |
или в жаркую |
нии |
или в холодную |
|
|
погоду |
|
погоду |
Кирпичная |
|
8—12 |
|
6—8 |
Шлакоблочная |
|
7 -1 0 |
|
5—7 |
Бутовая с уплотнением вручную |
|
4 - 6 |
|
3 - 5 |
То же, вибраторами |
|
2—3 |
|
1—2 |
1. Ориентировочный расход цемента на 1 м3 песка
и= 4 F ' OOO'
1\Кц
где /?раст, Rn— соответственно прочность раствора и активность цемен та; К — коэффициент для крупнозернистого песка 1,3—1,6, среднезернистого 1,0—1,3 и мелкозернистого 0,8—1,0:
2. Если введение известкового или глиняного теста допустимо, его содер жание
Д = 170/1-0,002 Ц/Ym,
где ут— объемная масса теста.
3. Количество воды подбирают по заданной подвижности смеси, начиная с наименьшего водновяжущего отношения (0,8—0,9) и nocfeneHHo увеличи вая воду порциями по 5% от первоначально принятого* количества.
Выбор вяжущего зависит от назначения раствора и его марки. Для раст воров марки 10 используют в качестве вяжущего воздушную или гидравли ческую известь, известково-шлаковые вяжущие, романцемент. Для растворов
марки 25 и |
выше — портландцемент, пластифицированный и |
гидрофобный |
|||||||||||
портландцементы, |
шлакопортландцемент, |
пуццолановый |
портландцемент. |
||||||||||
|
|
|
|
|
|
|
|
|
|
|
Т а б л и ц а |
5.2 |
|
|
|
|
Назначение раствора |
|
|
|
Рекомендуемая марка раствора |
||||||
Кладка наружных стен зданий при относительной влажности возду |
|
4—25 |
|
|
|||||||||
ха менее 60% |
|
|
|
|
|
|
|
|
|
|
|
|
|
То же, при влажности более 60% |
|
|
|
|
|
|
|
25—50 |
|
|
|||
Кладка столбов, |
простенков, карнизов |
|
|
|
|
|
25-100 |
|
|||||
Изготовление крупных блоков из кирпича и других камней |
|
|
25 |
|
|
||||||||
Расшивка швов в стенках из крупных блоков и панелей |
|
|
|
50 |
|
|
|||||||
|
|
|
|
|
|
|
|
|
|
|
Т а б л и ц а |
5.3 |
|
|
|
|
|
|
|
Марка |
раствора |
|
|
|
|
|
|
М арка цемента |
|
|
50 |
|
|
25 |
|
|
10 |
|
4 |
|
|
|
|
|
|
|
|
|
|
|
|||||
|
|
|
Цементно-известковые |
|
|
|
|
— |
|
|
|||
5 0 0 |
1 |
1 : 8 |
|
— |
|
|
— |
|
|
|
|
||
4 0 0 |
1 |
0 ,7 |
6 |
1 |
1,7 |
12 |
|
— |
|
|
— |
|
|
3 0 0 |
1 |
0 ,4 |
4 ,5 |
1 |
1,2 |
9 |
|
— |
|
|
— |
|
|
2 0 0 |
1 |
0 , 1 : 2 ,5 |
1 |
0 ,5 |
6 |
1 |
1,7 |
12 |
|
— |
|
|
|
150 |
|
|
|
1 |
0 ,3 |
3 ,5 |
1 |
1,2 |
9 |
1 |
1,7 |
12 |
|
|
|
|
Цементно-глиняные |
|
|
|
|
|
|
|
|||
5 0 0 |
1 |
1 : 8 |
|
|
— |
|
|
— |
|
|
— |
|
|
4 0 0 |
1 |
0 ,7 |
6 |
1 1 1 1 |
|
|
_ |
|
|
— |
|
|
|
3 0 0 |
1 |
0 ,4 |
4 ,5 |
1 |
1 : 9 |
|
|
— |
|
|
— |
|
|
2 0 0 |
1 |
0,1 |
2 ,5 |
1 |
0 ,5 |
5 |
1 |
1 |
9 |
|
|
|
|
150 |
|
|
— |
1 |
0 ,3 |
3 ,5 |
1 |
1 |
9 |
1 |
1 : 9 |
|
|
П р и м с ч а и и с. Для надземных конструкции при относнтельн й нлажностн помещений до 60% и для фундаментов в маловлажпых грунтах.
Растворы для штукатурных работ. К штукатурным растворам предъявля ют требования по удобоукладываемости, прилипанию растворной смеси и сцеплению затвердевшего раствора с основанием. При твердении в раство рах не должны появляться усадочные трещины. Прочность штукатурных растворов незначительна (0,2—0,4 МПа), так как они не являются несущи ми. В отдельных случаях к штукатурным растворам предъявляют требования повышенной плотности, водонепроницаемости и водостойкости.
Штукатурные растворы применяют с повышенной подвижностью, так как их наносят тонким слоем на пористое основание. Для подготовительного слоя (набрызга) подвижность смеси должна составлять 11 —13, для основного слоя (грунта) — 7—8 см. Отделочный слой (накрывку) устраивают из смеси с подвижностью 7—10 см.
Штукатурные растворы готовят из тех же материалов, что и растворы для каменной кладки, но более высокого качества: известь должна быть хорошо очищена от непогасившихся зерен; гипс просеивают сквозь сито с отверстия ми 1,2 мм; песок должен быть чистым с предельной крупностью зерен не бо лее 1—2 мм.
Наружные и внутренние кирпичные и каменные стены оштукатуривают известковыми растворами (для подготовительных слоев состав 1:3, а для от делочных— 1:2). Известковые растворы обладают хорошим сцеплением с кирпичом, достаточной долговечностью и малой изменяемостью объема. Для оштукатуривания поверхностей сооружений, подвергающихся система тическому увлажнению, применяют цементно-известковые растворы с добав кой гидрофобных пластификаторов. Для этой цели применяют растворы составов 1:1:6 или 1:1:5 для наружных штукатурок и 1:2:9 для внутренних.
Для внутренних штукатурок сухих стен зданий используют известковые, а для оштукатуривания потолков и деревянных стен — известково-гипсбвые растворы. Количество гипса в этих растворах составляет 0,2—1 объемную часть на одну объемную часть известкового теста.
Водонепроницаемые штукатурные растворы используют для защиты со оружений от постоянного воздействия влаги (опоры мостов, стены каналов и др.). Для этой цели применяют цементные растворы состава 1:2—1:3 на шлаковых и пуццолановых цементах с гидрофобными добавками. Водо непроницаемость растворов может быть увеличена за счет нанесения их на ос нование торкретированием. Раствор наносят цемент-пушкой, выбрасываю щей сжатым воздухом сухую смесь цемента и песка. Смесь при выходе из на конечника увлажняется водой. Такой штукатурный слой выдерживает давле ние воды 2 МПа, прочно соединяется с.поверхностью бетона и имеет повышен ную прочность (30—50 МПа), однако в этом случае теряется до 30—50% ис ходных материалов.
Специальные растворы. Растворы для заполнения швов между элемента ми железобетонных изделий иМеют подвижность 7—8 см, марку 100 и выше. Их изготавливают из портландцементов высоких марок и кварцевых песков. Состав таких растворов 1:3—1:4. Еще более прочными (не менее 300) изго тавливают инъекционные растворы для заполнения каналов в предваритель но напряженных конструкциях.
Цемент для таких растворов применяют марки 400 и вьцне, а расход це мента составляет до 1000 кг на 1 м3
Растворы для полов подразделяют на цементные, металлоцементные, цементно-опилочные и полимерцементные. Они характеризуются повышен ными марками (более 100) и подвижностью (10—13 см). Их используют для стяжки поверхности полов, а также для устройства полов из брусчатки, клин керного кирпича, бетонных и керамических плиток.
Металлоцементные растворы готовят из обезжиренной металлической стружки крупностью до 3 мм, цемента, песка, воды. Марка металлорастворов 300—500, подвижность 1—3 см, они хорошо сопротивляются истиранию.
Цементно-опилочные растворы состоят из портландцемента, песка, древесных опилок и воды, их применяют для устройства оснований под полы (марка 50).
Гидроизоляционные растворы характеризуются высокой маркой (300 и выше) и составами 1:2—1:3. Их готовят из сульфатостойких портландцементов, пуццолановых портландцементов высоких марок, крупно- и средне зернистых кварцевых или искусственных песков. Часто их наносят на изоли руемые поверхности торкретированием. В эти растворы иногда вводят поли мерные или битумные эмульсии.
Тампонажными растворами закрепляют и гидроизолируют нефтяные, га зовые и другие скважины. Они характеризуются маркой 20—100, высокой подвижностью, позволяющей их нагнетать в скважины (подвижность бо лее 12 см). Эти растворы изготавливают из тампонажных и сульфатостойких портландцементов, шлакопортландцементов, пуццолановых портландцемен тов и кварцевых песков. В ряде случаев для повышения водонепроницае мости в растворы вводят суглинки в виде суспензии. Для тампонажных раст воров характерны высокие водоцементные отношения (£ /// = 0,5-М ,5), со ставы 1:1—1:3. В эти растворы обычно вводят поверхностно-активные ве щества и добавки-ускорители твердения.
Рентгенозащитные растворы применяют для оштукатуривания стен и по толков рентгеновских и подобных помещений. Вяжущие — портландцемент, шлакопортландцемент, а заполнители — барит и другие тяжелые породы
ввиде песка крупностью до 1,25 мм и пыли. Для улучшения защитных свойств
врастворные смеси вводят добавки, содержащие легкие элементы (водород, литий, кадмий, а также боросодержащие элементы).
Приготовление строительных растворов. Технология приготовления раст
воров включает операции: подготовку исходных материалов, дозирование и смешение. Подготовка материалов необходима для того, чтобы не допустить попадания в раствор неоднородных и засоренных вредными примесями мате риалов, получить песок необходимой крупности и влажности. Песок для тяжелых растворов предварительно просеивают сквозь сито с отверстиями 20 мм, а шлаковые и пемзовые пески измельчают и просеивают.
Известковое тесто должно содержать 60—65% воды. Если в раствор вводят глину, то в виде теста подвижностью 14—15 см. Материалы обычно дозируют по объему, а цемент по массе. Отдозированные материалы смеши вают в растворомешалках вместимостью 150, 375 и 750 л, снабженных вращающимися лопастями. При использовании обычных кварцевых песков продолжительность перемешивания раствора 1—2 мин, а в случае примене ния легких песков — 2,5—3 мин. При введении в растворы тонкомолотых материалов продолжительность перемешивания растворов увеличивается
до 3—4 мин.
Растворы (кладочные и штукатурные) готовят централизованно на заво дах или передвижных растворосмесительных установках. Растворы (товар ные) поступают на стройку в виде сухих смесей или готовых растворов опре деленной консистенции, марки и качества.
Готовые штукатурные растворы перевозят в специально оборудованных автомобилях-самосвалах. На строительных объектах раствор транспорти
руют с помощью растворонасосов.
Контроль качества при приготовлении растворов заключается в проверке качества исходных материалов, их дозирования, времени перемешивания, определении удобоукладываемости растворной смеси, марки растрора.