
Выбор и назначение оптимальных условий протягивания заготовок из тру
..pdf(см. табл. 27).Усталостные испытания показали, что предел выносливости «елочных» замков лопаток в этом случае составляет 160 МПа.
Таким образом, увеличение числа проходов с плавным снижением глубины шлифования позволяет повысить предел выносливости замков лопаток турбин. На рис. 174 изображена гистограмма зависимости σ–1 от числа проходов, построенная по результатам экспериментальных исследований. С увеличением числа проходов от 3 до 9 предел выносливости σ–1 удалось увеличить практически в 1,5–2 раза.
Для обеспечения предела выносливости σ–1 = 100 МПа лопаток из более пластичного высокожаропрочного сплава ЖС26ВСНК потребовалось увеличение числа проходов до 14. Проведен анализ интенсивности изменения нагрузки на шпиндели шлифовальных станков и обрабатываемые детали в зависимости от глубины шлифования и числа проходов. Для этого в процессе глубинного шлифования производилась запись действующей нагрузки на оба шпинделя станка SS13L с помощью датчиков станка и осциллографа Н115 на ленту УФ последовательно на всех 14 проходах. Кроме того, с помощью использования специального пакета программ «Юниграфикс» на рабочих станциях ЭВМ «Индиго-2» фирмы «Силикон Графикс» (США) в режиме САД/САМ/САЕ произведен расчет объема снимаемого металла Q (мм3) и площади снимаемой стружки S (мм2) в зависимости от номера прохода и глубины шлифования на каждом проходе. Применение 9-го и 14-го проходов вместо 3-го и 4-го приводит к плавному снижению объема снимаемой стружки и, соответственно, нагрузки на режущих зернах, особенно на последних проходах. Это создает более благоприятные параметры качества поверхностного слоя и обеспечивает выполнение требований по усталостной прочности. Так, внедрение 14 проходов при глубинном шлифовании позволило обеспечить стабильность качества и требуемого предела выносливости σ–1 = 100 МПа.
Проведенный статистический анализ и математическая обработка результатов методом планирования экспериментов позволила
341
вывести следующую зависимость предела выносливости от режимов шлифования сплавов ЖС6К и ЖС6УВИ кругами фирмы «Тиролит»:
σ−1 = |
V 0,22 |
V 0,3 |
|
||
|
кр |
дет |
, |
(90) |
|
|
|
|
|||
|
|
tcp |
|
||
где Vдет – скорость детали, мм/мин; |
Vкр – скорость круга, м/сек; tср – |
||||
средняя глубина шлифования, |
tср = |
t / n; |
t – общий припуск, мм; |
nпрох –число проходов.
Из этой зависимости видно, что с увеличением скорости детали Vдет, скорости круга Vкр, числа проходов n и уменьшением глубины шлифования tср предел выносливости σ–1 увеличивается. Приведенная зависимость действительна для условий шлифования «елочного» профиля кругами фирмы «Тиролит» в диапазоне скоростей
круга Vкр = 15…25 м/с, Vдет = 100…500 мм/мин, tср = 0,6…0,8 мм.
Подбор оптимальных соотношений Vкр, Vдет, tср позволяет оптимизировать процесс глубинного шлифования на основе обеспечения требуемого предела выносливости σ–1 и максимальной производительности обработки.
6.4. Сравнительная оценка показателей производительности, качества и себестоимости при интенсификации различных процессов резания замков турбинных лопаток
Целесообразность применения того или иного варианта технологического процесса оценивается обычно с технической и экономической сторон. Сравнение вариантов с технической стороны оценивается по показателям качества поверхностного слоя и усталостной прочности деталей. Экономическая оценка вариантов обработки типовых деталей производится путем расчета и сравнения себестоимости обработки деталей по различным вариантам при обеспечении требуемых показателей качества и производительности обработки. Кроме того, при сравнении необходимо учитывать и стабильность
342
обеспечения основных технологических требований того или иного варианта обработки.
Как уже отмечалось, обработка «елочных» замков турбинных лопаток газотурбинных двигателей на различных предприятиях производится различными методами. В данной работе нами рассмотрены варианты обработки этих деталей методами скоростного протягивания, скоростного фрезерования и глубинного шлифования на оптимальных режимах резания.
С целью определения наиболее рационального варианта обработки проведем сравнение по качественным и экономическим показателям. Сравнение качественных показателей произведено по результатам исследования шероховатости, остаточных напряжений наклепа и микроструктуры поверхностного слоя замков лопаток турбины из жаропрочного литейного сплава ЖС6К, обработанных на оптимальных режимах скоростного протягивания, скоростного фрезерования и глубинного шлифования. Значения оптимальных режимов резания приведены в предыдущих разделах данной главы. Результаты исследований приведены в табл. 29 и на рис. 175, а. Анализ результатов сравнительных исследований показал, что наименьшая шероховатость Ra = 0,32…0,38 мкм обеспечивается при скоростных режимах лезвийной обработки протягиванием и фрезерованием. При глубинном шлифовании высота микронеровноcтей несколько больше: Ra = 0,63…1,25мкм. Кроме того, при глубинном шлифовании обнаружены глубокие продольные риски вдоль всей длины обработки. При протягивании и фрезеровании также образуются случайно расположенные риски, но они менее глубокие и короткие. Наличие глубоких продольных рисок на поверхности замков лопаток, обработанных глубинным шлифованием, можно объяснить врезным характером правки шлифовальных кругов и шлифования «елочного» профиля.
Правящие алмазные ролики имеют на наружной поверхности большое число алмазных зерен, скрепленных никелевой связкой. Величина алмазных зерен обычно составляет 400…500 мкм. Несмотря на то, что при доводке алмазных роликов разновысотность высту-
343
пающих алмазных зерен выравнивается, в процессе правки и износа ролика могут появиться новые острые режущие зерна, которые образуют на шлифовальном круге глубокие впадины и выступы. В свою очередь выступающие режущие зерна при профильном врезном шлифовании образуют глубокие, случайно расположенные риски, которые могут быть значительными концентраторами напряжений и снижать усталостную прочность детали.
Таблица 2 9
Показатели качества обработки «елочных» замков лопаток
|
Еди- |
Варианты обработки |
|||
Показатели |
ницы |
Скоростное |
|
Скоростное |
Глубинное |
изме- |
|
||||
|
рения |
протягивание |
|
фрезерование |
шлифование |
Шероховатость |
мкм |
0,38…0,55 |
|
0,32…0,63 |
0,63…1,25 |
поверхности |
|
||||
|
|
|
|
|
|
|
|
Риски длинные, |
|
Риски |
Риски |
Наличие рисок |
— |
прерывистые, |
|
короткие, |
длинные, |
|
|
неглубокие |
|
неглубокие |
глубокие |
|
Остаточные напряжения |
|
|||
σmax |
МПа |
–250…–350 |
|
+150…+200 |
–400…–500 |
* |
мкм |
10…15 |
|
10…20 |
5…15 |
hσ max |
|
||||
|
|
Наклеп |
|
|
|
Степень наклепа |
% |
25…30 |
|
40…50 |
18…20 |
Глубина наклепа |
мкм |
50…80 |
|
110…140 |
25…35 |
|
|
Точность профиля |
|
|
|
По шагу |
мм |
0,005…0,010 |
|
0,005–0,015 |
0,001…0,008 |
По углу |
мин |
10…45 |
|
5…15 |
5…10 |
По радиусам |
мм |
0,05…0,10 |
|
0,05…0,10 |
0,05…0,10 |
По смещению |
мм |
0,015…0,020 |
|
0,015…0,020 |
0,01…0,02 |
Прямолинейность |
мм |
0,01…0,02 |
|
0,005…0,020 |
0,005…0,010 |
Неплоскостность |
мм |
0,005…0,010 |
|
0,005…0,020 |
0,003…0,005 |
По роликам |
мм |
0,01…0,05 |
|
0,01…0,06 |
0,005…0,010 |
* hσ max – глубина расположения максимального значения остаточных напряжений.
344
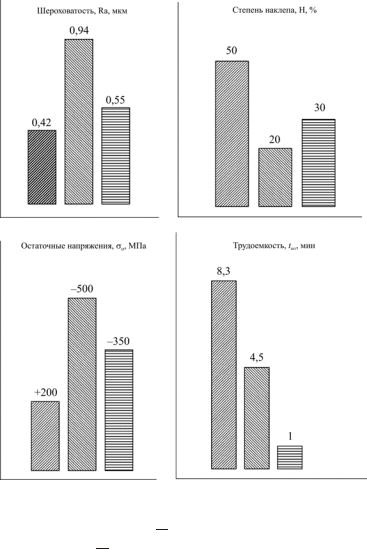
Рис. 175. Результаты исследования параметров качества поверхностного слоя
– фрезерование,
– глубинное шлифование,
– скоростное протягивание
При протягивании и фрезеровании рисочность на деталях образуется от микронеровностей режущих кромок протяжек и фрез. Заточка твердосплавных протяжек и фрез производится обычно алмазными
345
кругами зернистостью 63…80 мкм. Шероховатость режущих граней и кромок после заточки находится в пределах Ra = 0,16…0,40 мкм. В процессе протягивания и фрезерования на режущих кромках может образовываться и периодически срываться нарост. Поэтому риски могут быть чаще всего прерывистыми и неглубокими.
Малые подачи на чистовых зубьях протяжек Sz = 0,005…0,010 мм/зуб и зубьях фрез Sz = 0,03 мм/зуб также способствуют уменьшению шероховатости поверхности деталей. Известно, что с уменьшением шероховатости усталостная прочность деталей повышается.
Таким образом, с позиции обеспечения большей усталостной прочности характер шероховатости и рисочности поверхности замков лопаток, обработанных скоростным протягиванием и фрезерованием, является более предпочтительным, чем при глубинном шлифовании.
Характер образования остаточных напряжений также различный. При фрезеровании в тонком поверхностном слое 10…20 мкм образуются в основном незначительные растягивающие остаточные напряжения – до +200 МПа. При скоростном протягивании в поверхностном слое 10…15 мкм обнаружены преимущественно сжимающие остаточные напряжения до –350 МПа. Глубинное шлифование «елочных» замков лопаток способствует образованию стабильных сжимающих остаточных напряжений до –500 МПа в весьма тонком поверхностном слое 5…15 мкм.
Отличие в характере образования остаточных напряжений можно объяснить превалированием действия силового или теплового фактора процесса резания. Образование сжимающих остаточных напряжений при протягивании и глубинном шлифовании объясняется превалирующим действием силового фактора и термоупрочнением при интенсивном охлаждении зоны резания. В процессе фрезерования действие силового фактора меньше, а интенсивность охлаждения зоны резания невысокая. В результате повышается роль теплового фактора в формировании растягивающих остаточных напряжений.
346
С позиции обеспечения высокой усталостной прочности более благоприятным считается формирование сжимающих остаточных напряжений при скоростном протягивании и глубинном шлифовании, нежели формирование растягивающих остаточных напряжений при фрезеровании. Нужно отметить стабильность характера остаточных напряжений при глубинном шлифовании.
Оценивая характер образования наклепа при различных вариантах обработки «елочных» замков, можно увидеть незначительную разницу по степени наклепа 20…50 %, но существенное отличие по глубине наклепа. Наименьшая глубина наклепа обнаружена при глубинном шлифовании – (25…35 мкм), а наибольшая – при фрезеровании (до 140 мкм и более). Для жаропрочных литейных сплавов типа ЖС6К, применяемых в высотемпературных условиях эксплуатации, более предпочтительными с позиции усталостной прочности являются небольшие значения степени и глубины наклепа.
Анализ состояния микроструктуры поверхностного слоя замков лопаток, обработанных по различным вариантам, не выявил существенных отличий. Не обнаружены структурно-фазовые превращения, изменения размеров зерен кристаллов при всех вариантах обработки.
При сравнительном анализе выполнения точностных параметров «елочного» профиля установлено, что наиболее точным и стабильным является процесс глубинного шлифования. При скоростном протягивании и фрезеровании по мере износа режущих инструментов размерные параметры «елочного» профиля изменяются в 2–3 раза быстрее, чем при глубинном шлифовании. Это можно объяснить более частой правкой шлифовальных кругов в процессе глубинного шлифования по сравнению с временем периода переточек лезвийного инструмента. Если при глубинном шлифовании правка кругов производится перед каждым проходом, то переточка фрез – через 15–20 деталей,
апереточка протяжек – через составляет 150–200 деталей.
Вто же время нужно отметить, что за период стойкости фрез
ипротяжек геометрические размеры «елочного» профиля обрабо-
347
танных деталей находятся в пределах допуска на размеры. При глубинном шлифовании изменение размеров профиля может постепенно нарастать по мере износа алмазного ролика. Практика глубинного шлифования показала, что период стойкости алмазных роликов составляет 1 500–2 000 деталей. Незначительные изменения в геометрии возможны от первой к четвертой детали из-за износа шлифовального круга. Общий ресурс шлифовальных кругов обычно составляет 150–200 деталей.
Таким образом, с позиции более стабильного и более длительного обеспечения точностных параметров «елочного» профиля предпочтительным является процесс глубинного шлифования. Эти выводы касаются только обработки замков лопаток из литейных жаропрочных сталей. При обработке замков лопаток из деформируемых жаропрочных сплавов типа ЭИ437БУ-ВД, ЭИ787-ВД и других более предпочтителен процесс оптимального скоростного протягивания.
Сравнительные усталостные испытания замков лопаток, обработанных по различным вариантам, показали преимущество лезвийной обработки перед шлифованием. Как уже указывалось ранее, при протягивании и фрезеровании обеспечивается предел выносливости 140 МПа, а при глубинном шлифовании на рекомендованных режимах предел выносливости составляет 80…90 МПа. Снижение предела выносливости можно объяснить появлением глубоких продольных рисок, особенно в первом, самом нагруженном пазу «елочного» профиля при глубинном шлифовании. Для повышения предела выносливости замков лопаток после глубинного шлифования потребовалось увеличить в 2–3 раза число проходов с постепенным уменьшением глубины шлифования до0,010…0,002 ммнапоследнихпроходах.
Кроме того, для обеспечения стабильности усталостной прочности замков лопаток, обработанных глубинным шлифованием, потребовалось введение упрочняющей дробеструйной обработки металлическими микрошариками. Но даже и после введения дробеструйного упрочнения при периодических усталостных испытаниях наблюдались выпады деталей в брак из-за низкого предела выносливости, что вновь
348
потребовало разработки дополнительных мероприятий по совершенствованию процесса глубинного шлифования. Это снижает производительность, стабильность и увеличивает затраты на производство. Поэтому с позиции обеспечения усталостной прочности процессы лезвийной обработки – скоростное протягивание и фрезерование – более предпочтительны, чем процесс глубинного шлифования.
Эффективность технологического процесса обработки чаще всего оценивается по ее себестоимости, поскольку это важнейший показатель работы. Постоянное снижение себестоимости отражает интенсивность роста технического прогресса, повышение производительности обработки. Кроме того, снижение себестоимости продукции отражает улучшение использования оборудования, усовершенствование технологии и организации производства.
Оценка различных вариантов техпроцессов производится обычно по технологической себестоимости. C этой целью замки лопаток турбин из сплава ЖC6К обрабатывались скоростным протягиванием, фрезерованием и глубинным шлифованием. Протягивание производилось одновременно с двух сторон на горизонтально-протяжном станке мод. 7А540, модернизированном для скоростей резания до 0,5 м/с. Протяжки изготавливались спластинками твердого сплава ВК8. Для фрезерования замков лопаток использовался горизонтально-фрезерный станок мод. 6Н83Г ствердосплавными фрезами из ВК6М. Фрезерование проводилосьпоследовательнопооднойсторонепрофиля.
Одновременная двусторонняя обработка четырех замков лопаток глубинным шлифованием проводилась на станках-полуавтоматах с ЧПУ мод. SS13L фирмы «Элб-Шлифф». В качестве режущего инструмента использовались высокопориcтые шлифовальные круги из электрокорунда белого. Периодическая правка кругов проводилась алмазными роликами отечественного производства. Обработка деталей проводилась на оптимальных режимах резания, обеспечивающих величину шероховатости Ra ≤ 2,5 мкм, отсутствие трещин и прижогов на поверхности, незначительные по величине остаточные напря-
349
жения и наклеп, предел выносливости не менее 140 МПа. Точность «елочного» профиля обеспечивается в пределах 0,005…0,010 мм.
Расчет технико-экономических показателей применения различных вариантов обработки «елочных» замков лопаток турбин проводился в соответствии с известной методикой определения экономической эффективности капитальных вложений и новой техники. Данная методика рекомендует сравнивать себестоимость продукции и капитальных вложений по каждому рассматриваемому варианту, определяя величину приведенных затрат.
Аналогичные расчеты проводились сотрудниками НИИД
иММПО «Красный Октябрь» при замене процессов фрезерования
имаятникового шлифования на процесс протягивания «елочных» замков лопаток ротора турбины из жаропрочного сплава ЭИ929.
Приведенные затраты по каждому варианту рассчитываются по формуле
Cпр = С + Кобщ · Kэф.н, |
(91) |
где С – себестоимость годового объема продукции по рассматриваемому варианту техпроцесса, Кобщ – общие капвложения, Kэф.н – нормативный коэффициент эффективности, Спр – приведенная себестоимость.
Наиболее экономичным считается вариант, дающий наименьшие приведенные затраты. По результатам расчета строятся совмещенные графики годовых приведенных затрат в зависимости от программы выпуска лопаток. В табл. 30 приведены исходные данные для расчета, взятые из результатов предыдущих исследований и анализа статистических данных обработки лопаток турбин на ОАО «Пермский моторный завод».
Расчет годовых приведенных затрат по каждому из трех вариантов приведены в табл. 31. Для построения графиков приведенных затрат приняты две годовые программы производства лопаток N1 = 20 000 и N2 = 200 000 деталей. Расчеты приведены в дореформенных ценах 1991 года, как наиболее стабильных.
350