
Выбор и назначение оптимальных условий протягивания заготовок из тру
..pdfВ результате применения фасок на выходном торце замков лопаток стойкость твердосплавных протяжек повысилась в 2,5 раза, особенно при протягивании таких жаропрочных сплавов, как ЭИ787-ВД и ВЖЛ14.
Дополнительным мероприятием, снижающим неблагоприятные условия выхода зуба протяжки из детали, является применение наклона режущей кромки под углом λ = 20…30° к направлению движения протяжки. В результате более спокойного постепенного плавного выхода режущей кромки из детали значительно снижается величина пластической деформации и уменьшается образование заусенцев. При этом износ и выкрашивание протяжек значительно меньше, чем при расположении режущей кромки под углом 90° к направлению движения протяжки.
Таким образом, разработка новых методов борьбы с хрупким разрушением твердосплавных протяжек позволила впервые в отечественной практике широко реализовать процесс высокоинтенсивного скоростного протягивания деталей из различных труднообрабатываемых сталей и сплавов.
5.4. Разработка способа скоростного протягивания деталей ГТД твердосплавными многосекционными протяжками
При исследовании температуры (контакта) резания получены аналитические зависимости экспериментальным и расчетным методом применительно к одно- и двузубым протяжкам. В то же время обработка сложнофасонных поверхностей замков лопаток и пазов в дисках производится большим числом последовательно устанавливаемых в один или несколько блоков многозубых многосекционных протяжек. Число зубьев в таких протяжках может составлять от 10 до 100 зубьев. Число протяжек в блоке может быть от 2 до 10. Число блоков для наиболее сложных замков и глубоких пазов может составлять от 2 до 6.
Таким образом, общее число режущих зубьев всех секций протяжек, последовательно обрабатывающих за проход одну и ту же часть профиля поверхности замка или паза, может достигать бо-
281
лее 200–300 зубьев, а общее число зубьев протяжек в одном протяжном блоке может быть более 2 000. Весь протягиваемый сложный профиль разбивается на несколько более простых элементов, которые обрабатываются различными секциями протяжек, входящих в один или несколько протяжных блоков. Обычно первые по ходу блока протяжки называют предварительными, или черновыми, срезающими наибольший припуск с подачей 0,08…0,12 мм/зуб, затем идут промежуточные получистовые секции протяжек с подачами 0,04…0,06 мм/зуб и, наконец, в работу по ходу движения блока вступают чистовые секции протяжек, имеющие подачи 0,01…0,02 мм/зуб. В результате за один рабочий ход всего блока многосекционных протяжек осуществляется черновой, получистовой и чистовой переходы.
Используя известную методику А.Н. Резникова, можно аналитически рассчитать температурный прирост на каждом последующем зубе многозубой протяжки. Ранее нами было доказано, что прирост температуры на втором зубе протяжки составляет не более 1…3 % по сравнению с первым. Интересно узнать, каков прирост температуры на всех последующих зубьях многосекционной протяжки, имеющих различную подачу на зубьях, и как применить метод скоростного интенсивного протягивания для многосекционных твердосплавных протяжек. Для выяснения этих вопросов проведены экспериментальные исследования температуры резания протяжкой с числом зубьев, равным 10, а также теоретический расчет прироста температуры резания на каждом последующем зубе протяжки по методике А.Н. Резникова
(рис. 155).
Каждый зуб плоской протяжки № 0, 1, 2, …, m срезает слой толщиной а (Sz). Количество теплоты, поступающей в деталь из зоны резания первого зуба (0), определяется по формуле
Qи = (1 – b) < QА + Q2T – Q2, |
(68) |
где Qи – теплота в детали; b – доля, характеризующая часть теплоты деформации, передаваемую стружке; QА – тепловая мощность источ-
282

Рис. 156. Схема процесса резания многозубой протяжкой (вверху) и расположения источников тепла qи (внизу)
ника деформации; Q2T – тепловая мощность трения по задней грани; Q2 – тепловая мощность итоговых источников на задней грани зубьев протяжек.
При расчете температуры зубьев 1 и 2 от теплоты первого зуба 0 не учитывались форма закона распределения интенсивности этой теплоты и разница температур в точках A и В, расположенных на режущей кромке и обрабатываемой поверхности, т.к. толщина среза а (Sz) относительно величины шага to весьма незначительна.
Процесс распространения теплоты Qи в детали, схематически представленный на нижней части рис. 155, осуществляется как результат воздействия плоского источника тепла интенсивностью
qи = |
Qи |
, |
(69) |
||
b (l0 |
− l2 ) |
||||
|
|
|
быстро двигающегося на поверхности тела с адеабатической границей. В результате для движущегося источника можно записать формулу
Qmax ≈ 27,6 |
Qи |
ω |
, |
(70) |
|
λ b V |
(l0 −l2 ) |
||||
|
|
|
где ω – коэффициент теплопроводности материала детали; λ – коэффициент температуропроводности материала детали; b – ширина ре-
283
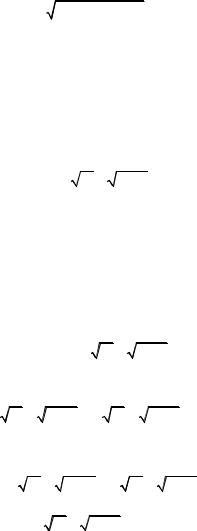
зания, мм; l2 – длина контакта по задней грани, мм; l0 – длина плоскости сдвига, мм; l0 = a/sinβi.
Угол βi можно найти по формуле
sinβi = |
cos γ |
, |
(71) |
|
ξ−2ξ sin γ +1 |
||||
|
|
|
где ξ – коэффициент продольной усадки стружки; γ – передний угол зубьев протяжки.
Обычно Qи составляет 15…25 % от общей тепловой мощности процесса. Следовательно,
|
|
|
|
|
Qи= (0,006+0,01) Pz · V. |
(72) |
|
Дополнительную температуру, возникающую в точке А под |
|||||
действием источника Qи, рассчитываем по формуле |
|
|||||
|
|
|
|
|
Q1 = Qmax ( K − K −1) , |
(73) |
где |
K ≈ |
|
to |
|
– безразмерный шаг между зубьями протяжки. |
|
l |
+ l |
2 |
|
|||
|
|
|
|
|||
|
|
0 |
|
|
|
Дополнительную температуру в следующей точке В (зуб № 2) можно рассчитать как результат суммарного влияния источника qи и источника с температурой Q1, расположенного в точке А. Для каждого из них допустимо применение последней зависимости, тогда суммарное повышение температуры для зуба № 2 составит
|
Q2 = Q1 + Q1 ( K − K −1) |
|
|
||
или |
|
|
|
|
|
Q2 |
= ( |
K − |
K −1)+ ( K − K −1)2 |
. |
(74) |
|
|
|
|
|
|
Для любого m-го зуба по аналогии получаем |
|
|
|||
Qm = Qmax |
( K − K −1)+ ( K − K −1)2 |
+ |
|||
|
|
|
|
|
(75) |
|
|
+... + ( |
K − K −1)m . |
|
|
|
|
|
|
||
|
|
|
|
|
|
284 |
|
|
|
|
|
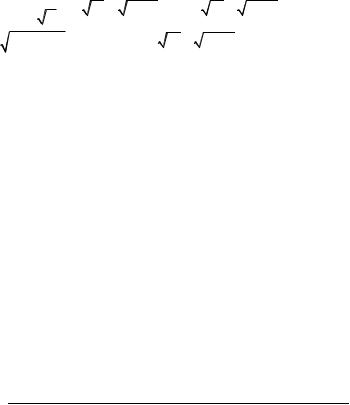
Подставив вместо Qmax его значение, получим
|
|
27,6 Qи ω |
|
( K − |
K −1) 1 |
−( K − |
K −1)m |
||
Q |
= |
|
|
|
|
|
|
. (76) |
|
λb V (l0 + l2 ) |
|
1−( |
K − K −1) |
|
|||||
m |
|
|
|
|
|
Расчет повышения температуры резания для пятизубой протяжки проведен при протягивании сплава ЭИ787-ВД со скоростью 20 м/мин, подачей Sz = 0,02 мм/зуб, шаг между зубьями to = 16 мм, передний угол – 0°, задний – 6°. Коэффициент усадки – 2.
В результате расчета найдено: Qи = 51,2 кал/с; qи = 0,044 см2/с;
K = 42,9; l0 = 0,173 мм; Qm = 35 К.
Результаты расчета дополнительной Qm и максимальной Qmax температуры сведены в табл. 21, из которой следует, что несмотря на существенное повышение общей тепловой мощности процесса температура на каждом зубе протяжки повышается незначительно (5…6 %) по сравнению с однозубой протяжкой. Причем на втором, третьем и последующих зубьях температура стабилизируется на одном уровне. Это подтверждает полученные нами ранее результаты аналитического расчета поверхностной температуры (контакта) резания двузубой протяжкой.
Таблица 2 1
Приращение температуры на зубьях протяжек
Показатели |
|
|
Номер зуба |
|
|
|
1 |
2 |
|
3 |
4 |
5 |
|
|
|
|||||
Qm, К |
0 |
+47,0 |
|
+47,26 |
+47,28 |
+47,28 |
Qmах, К |
816,5 |
863,5 |
|
863,70 |
863,70 |
863,80 |
% прироста |
0 |
5,8 |
|
5,40 |
5,40 |
5,40 |
Аналогичные результаты получены А.Н. Резниковым при зенкеровании четырехзубым зенкером стали ШХ15 и Д.К. Маргулисом при протягивании стали 45Х.
285
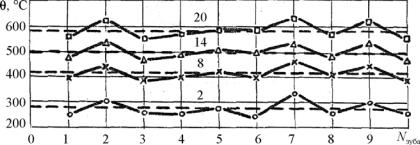
Незначительный прирост на первых зубьях и стабилизация температуры на последующих зубьях объясняются тем, что в данном случае шаг зубьев достаточно велик и теплота, передающаяся из зоны резания, успевает в значительной мере рассеяться в массе детали.
Экспериментальные исследования температуры резания, проведенные при протягивании сплава ЭИ787-ВД десятизубой протяжкой с подачей на зубьях в пределах 0,02…0,03 мм показали (рис. 156) незначительные отклонения (5…10 %) средней температуры контакта (резания) на отдельных зубьях многозубой протяжки по сравнению с однозубой протяжкой.
Рис. 156. Результаты экспериментальных исследований температуры резания при протягивании сплава ЭИ787-ВД десятизубой протяжкой с подачей на зубьях в пределах 0,02…0,03 мм
Таким образом, зависимости, полученные нами ранее в результате экспериментальных и теоретических исследований для однозубой и двузубой протяжек, с достаточной точностью могут быть использованы и при протягивании многозубыми многосекционными протяжками. Это обстоятельство позволяет разработать новый способ высокоинтенсивного скоростного протягивания твердосплавными многосекционными протяжками.
Каждая секция блока протяжек, например, при протягивании замка лопаток (рис. 157), состоит из двух-трех протяжек, обрабатывающих одновременно замок с трех сторон (секции I и III) и с двух сторон (секция II). Протяжки, входящие в секции I и II, имеют подачу на режущих зубьях 0,1 мм/зуб и называются предварительными,
286

Рис. 157. Новый способ скоростного протягивания твердосплавными многосекционными протяжками с учетом оптимальной температуры резания ХН77ТЮР-ВД,
ХН35ВТЮ-ВД,
ХН56МКЮР-ВД,
ХН35ВТЮ-ВД (при Р18)
или черновыми протяжками, а протяжки, входящие в секцию III, имеют подачу 0,02 мм/зуб и называются окончательными, или чистовыми.
287
Как показали предыдущие исследования, изменение подачи вызывает при постоянной скорости резания изменение температуры контакта (резания) на предварительных и окончательных режущих зубьях протяжек и различную степень интенсивности износа, что необходимо учитывать при назначении скорости протягивания.
Известны способы протягивания деталей с обеспечением автоматического уменьшения скорости резания в момент, когда чистовые зубья протяжки подходят к детали. Ранее мы показали, что при протягивании замков лопаток из стали ЭИ961Ш, например, скорость резания предварительными быстрорежущими протяжками устанавливалась 3 м/мин, а окончательными – 0,5 м/мин для обеспечения шероховатости Ra ≤ 1,25 мкм.
Известные способы имеют ряд существенных недостатков:
–уменьшение скорости резания чистовыми протяжками (обычно намного ниже оптимальной), согласно проведенным эксперимен- тально-теоретическими исследованиям, снижает температуру резания ниже оптимального значения и резко увеличивает интенсивность износа протяжек;
–при уменьшении скорости резания увеличивается машинное время обработки деталей;
–в результате выкрашивания твердосплавных режущих зубьев на малой скорости резания не обеспечивается стабильное физикохимическое состояние поверхностного слоя деталей.
С целью повышения производительности обработки, улучшения физико-химических свойств обработанных поверхностей и повышения стойкости протяжек разработан и осуществлен па практике способ оптимального скоростного протягивания, при котором производится автоматическое переключение скорости резания в течение одного рабочего хода протяжного блока на различных секциях протяжек до оптимального значения Vo, соответствующего оптимальной температуре резания Тo и минимальной интенсивности износа hо.з.о зубьев протяжек.
288
Расчет величины оптимальной скорости протягивания Vo для каждой секции ведется по разработанным алгоритмам расчета или по экспериментальным зависимостям для каждого обрабатываемого жаропрочного материала. Скорость резания переключается путем изменения числа оборотов главного электродвигателя при использовании протяжных станков с электромеханическим приводом типа 2МП301, 2МП400, НПЛ-1, МП2-1031, 2МП797 или путем изменения производительности гидравлического насоса при использовании протяжных станков с гидроприводом типа 7Б74, 7А540, 7Б57 и др.
Экспериментальные исследования нового способа оптимального протягивания производились на модернизированном станке мод. 7А540 в диапазоне скоростей до 30 м/мин при протягивании замковых поверхностей лопаток компрессоров из сплава ЭИ787-ВД твердосплавными протяжками (см. рис. 157). Станок модели 7А540 имеет радиально-поршневой регулируемый насос с электрогидравлическим управлением типа НР4М. Механизм управления этим насосом обеспечивает получение 4 различных скоростей перемещения штока гидроцилиндра: две различные скорости в прямом (рабочем) направлении и две скорости холостого (обратного) хода. Переключение режимов работы насоса производится электромагнитными устройствами. Сигналы на эти устройства поступают от конечных путевых индукционных переключателей, которые устанавливаются в нужном месте на станине протяжного станка вдоль хода протяжного блока. В момент перед входом в работу чистовой секции III (см. рис. 157) замыкается конечный переключатель и сигнал подается на увеличение производительности насоса (переключением электромагнитного контактора с золотником). При этом скорость протягивания возрастает. Характер изменения оптимальной скорости резания Vo различных сплавов приведен на рис. 157. При этом по сравнению с применяемым на производстве способом протягивания замков лопаток из сплава ЭИ787-ВД скорость предварительных секций протяжек увеличилась почти в 4 раза, а скорость окончательных секций – в 20 раз.
289
Общее машинное время протягивания снизилось с 40 до 6 с, т.е. более чем в 6 раз. Шероховатость обработанной поверхности несколько снизилась. Уменьшилась волнистость протянутых поверхностей замков лопаток. Аналогичные результаты получены при обработке и других сталей и сплавов.
Таким образом, разработанный принципиально новый метод скоростного протягивания на оптимальных для каждой секции протяжек скоростях резания обеспечивает помимо высокой производительности более высокую стойкость как предварительных, так и окончательных протяжек, улучшает качество поверхностного слоя, повышает стабильность технологического процесса. Все это отражается в конечном счете на повышении усталостной прочности, надежности и ресурса обрабатываемых деталей ГТД.
5.5. Статистистическая оценка надежности работы протяжек при интенсификации процесса протягивания
Исследования показали, что отказы в работе протяжного инструмента зависят от многих факторов, и поэтому могут быть и являются случайными. Это увеличивает нестабильность основных параметров качества поверхности и не позволяет автоматизировать процесс, в связи с чем для сравнительной характеристики работоспособности протяжек принята не среднеарифметическая величина стойкости, а уровень надежности.
Для протяжек, работающих в условиях неоптимального резания, характерно распределение долговечности в форме, близкой к экспоненциальной: отказы протяжек проявляются чаще через выкрашивания режущей кромки. Установлено, что в случае действия только износа для протяжек характерен нормальный закон распределения стойкости. Однако в практике часто отказ работоспособности протяжек проявляется в форме сочетания механических повреждений и износа режущих лезвий. В этих случаях кривая распределения долговечности имеет форму, промежуточную между нормальной кривой и кривой Пуассона. В качестве универсального принято трехпараметрическое
290