
- •Предисловие
- •1.2. Критерии малоциклового разрушения, учитывающие историю нагружения
- •4.2. Напряженно-деформированное состояние и долговечность образцов с зонами концентрации при непропорциональном нагружении
- •4.3. Исследование местных деформаций и долговечности в зонах концентрации при наличии анизотропии
- •5.2. Малоцикловая усталость сильфонных компенсаторов при неизотермическом нагружении
- •СПИСОК ЛИТЕРАТУРЫ
- •ОГЛАВЛЕНИЕ
D штампа для основного и аварийного режимов штамповки. Коэффициент асимметрии цикла по деформациям в анализи руемых точках штампа в основном режиме составлял г = - оо, в аварийном г = —1. Видно, что при аварийном режиме штам повки вследствие увеличения уровня и размаха температуры существенно увеличивается размах деформаций и снижается стойкость штампа по сравнению с основным режимом штам повки.
Таблица 5.2 Расчетные значения размахов деформаций и стойкости штампа
Режим |
Эле |
т |
Д т, |
|
|
|
|
Стой |
|
Д вх , % |
|
& Г х у |
Д е , - , % |
кость |
|||||
штам |
менты |
1 шах» |
Д Еу , % |
К |
|||||
°с |
°с |
% |
|||||||
повки |
(точки) |
|
|
|
|||||
|
|
|
|
|
|
циклы |
|||
|
|
|
|
|
|
|
|
||
Основ |
А |
450 |
170 |
0,41 |
0,58 |
0,14 |
0,35 |
ю4 |
|
ной |
В |
440 |
160 |
0,30 |
0,69 |
0,16 |
0,41 |
4-103 |
|
|
|||||||||
|
С |
430 |
150 |
0,31 |
0,72 |
0,16 |
0,42 |
2.5103 |
|
|
D |
435 |
155 |
0,30 |
0,56 |
0,07 |
0,32 |
104 |
|
Ава |
А |
550 |
270 |
0,57 |
0,73 |
0,18 |
0,45 |
2103 |
|
рий |
В |
540 |
260 |
0,50 |
0,90 |
0,18 |
0,53 |
103 |
|
ный |
|||||||||
С |
530 |
250 |
0,50 |
0,94 |
0,19 |
0,55 |
103 |
||
|
|||||||||
|
D |
535 |
255 |
0,50 |
0,80 |
0,38 |
0,51 |
2-103 |
5.2. Малоцикловая усталость сильфонных компенсаторов при неизотермическом нагружении
Для обеспечения надежной работы различных трубопровод ных систем и предохранения их от температурных деформаций часто используют компенсирующие элементы, обладающие малой жесткостью и воспринимающие на себя основную часть теплового расширения трубопровода. Широкое распростране ние получили компенсаторы сильфонного типа (рис. 5.8, а), способные в силу особенностей своей конструкции восприни мать значительные осевые перемещения и имеющие при этом достаточно высокие прочностные характеристики. Выход силь фонов из строя часто обусловлен малоцикловой усталостью,
возникающей в результате знакопеременного упругопластичес кого деформирования материала в максимально нагруженных зонах —впадине и вершине гофров. В ряде случаев эксплуата ция сильфонных компенсаторов осуществляется в условиях высоких температур. При этом чередование режимов работы конструкции, пуски, остановы, аварийные ситуации вызывают значительные изменения уровня температуры в процессе де формирования сильфона. В зависимости от характера измене ния температуры по длине трубопровода во времени, а также места расположения компенсатора, возможны различные ком бинации циклов перемещение-температура.
по ее длине (б) при нагреве пропусканием тока
Для исследования долговечности сильфонов в условиях тер момеханического нагружения были проведены испытания, в которых осуществлялось независимое деформирование и на грев сильфонов по заданной программе, включавшей синфаз ное нагружение при температуре Т= 650 <±150 °С и противо фазное при Т = 150^650 °С. С целью сопоставления были также проведены испытания при постоянных температурах 150 и 650 °С. Нагружение осуществляли растяжением—сжатием с симметричным циклом по перемещениям.
Для изготовления образцов использовали двухслойную гоф рированную оболочку Ду 40 из стали 12Х18Н10Т. Каждый слой имел продольный сварной шов, выполненный внахлест кон тактной роликовой сваркой. Длина образцов, вырезанных из
такой оболочки составляла 30 мм, что соответствует семи пол ным гофрам. Крайние гофры прижимались накладками к пере ходникам (рис. 5.9), устанавливаемым в захваты испытательной машины (УМЭ-ЮТП). Нагрев сильфонов осуществлялся про пусканием электрического тока. В связи с тем, что сильфонный компенсатор исследуемого типа имеет мелкие гофры и срав нительно небольшой диаметр при использовании данного спо соба нагрева, удалось получить достаточно равномерное тем пературное поле в зоне разрушения —впадине между гофрами в центральной части образца (см. рис. 5.8, б). Длительность цикла нагружения составляла 4 мин.
Вода
Рис. 5.9. Схема крепления сильфонного компенсатора в переходниках
Кривые усталости (по моменту образования трещины)>по лученные при исследованных режимах нагружения, представ лены на рис. 5.10. По оси ординат отложена величина местного перемещения, приходящегося на один гофр, которое измеряли между соседними вершинами гофров, смежными с зоной раз
рушения. Как следует из полученных результатов, повышение уровня температуры в изотермических испытаниях со 150 до 650 °С приводит к значительному снижению долговечности. При неизотермическом синфазном и противофазном нагруже ниях при линейном изменении температуры и перемещений во времени снижение долговечности было в 1,5—2 раза по сравнению с испытаниями при Т = 650 °С = const.
Рис. 5.10. Режимы неизотермического нагружения (о) и кривые малоцикловой усталости сильфонных компенсаторов (6)
Для определения напряженно-деформированного состоя ния использовался метод конечных элементов. Гофрированная оболочка моделировалась тонкостенными оболочечными ко нечными элементами постоянной толщины. В силу круговой симметрии рассматривался сектор, ограниченный углом 1,8°, включающий в осевом направлении четыре полугофра.
Граничные условия задавались в виде двух жестких заделок, одна из которых была неподвижна, а вторая смещалась в осевом направлении на заданную величину. Расчет показал, что для средних полугофров, влиянием граничных условий на которые можно пренебречь, максимум деформаций приходится на се редину впадины (рис. 5.11), которая является местом появления трещины (точка 2).
Разрушение первого и второго слоев, как показали резуль таты обследования внутренней поверхности сильфона, проис ходило практически одновременно. Это подтверждается и ре зультатами расчета — различие в деформациях, являющееся
следствием несколько большего радиуса впадины во внутрен нем слое, составляет около 10%, что существенно не сказыва ется на долговечности. Взаимодействием слоев при рассматри ваемом способе нагружения пренебрегали.
ё/
4.5
3,0
1.5
О |
2 |
4 |
6 |
8 |
10 |
12 |
14 |
S |
Рис. 5.11. Распределение относительных деформаций в первом и втором слоях по длине меридиана
Вследствие особенностей процесса изготовления сильфонов гидроформовкой толщина стенки не является постоянной. Для данного типоразмера максимальная толщина наблюдается во впадине, а минимальная в вершине гофра. Отличие составляет около 12 %. В расчете указанное изменение не учитывалось. Толщина стенки принималась постоянной и равной соответ ствующему значению во впадине, что, как показано в [97], не вносит существенных погрешностей в определение максималь ных деформаций.
Так как условия нагружения компенсатора исключают на копление значительных односторонних необратимых деформа ций (на это указывает также характер наблюдавшихся разру шений), при расчете режим деформирования, реализуемый в максимально нагруженных зонах, рассматривался как жесткий.
В связи с отсутствием исходных деформационных и проч ностных характеристик листовой стали 12Х18Н10Т, используе мой при изготовлении сильфонов, их получали на сплошных образцах корсетного типа. Нагружение осуществлялось растя жением-сжатием при жестком цикле изменения деформаций.
При неизотермическом нагружении были получены кривые усталости, соответствующие синфазному и противофазному со четанию деформации и температуры в цикле. Как показано на рис. 1.14, синфазный режим является более повреждающим, чем противофазный и нагружения при Т = 650 °С = const.
С учетом данных работы [98] влияние продольного сварного шва на деформацию и усталостную прочность сильфона учи тывалось при расчете увеличением толщины стенки в зоне сварного шва. Возможность такого подхода объясняется высо ким качеством контактной сварки, а также тем, что при на гружении сварного соединения, выполненного внахлест, мак симальные деформации возникают в основном металле на по верхности сильфона.
Материал компенсатора в процессе изготовления подверга ется наклепу до 10...15 %. Влияние наклепа на прочностные характеристики материала сильфонного компенсатора иссле довалось в [99] и, как показано, является несущественным. В большей степени оно сказывается на деформационных свой ствах, в связи с чем кривые циклического деформирования получали после предварительного статического растяжения об разца до указанного значения деформации. Сталь 12Х18Н10Т после наклепа разупрочнялась в течение 10... 15 циклов нагру жения, а затем достигала стабилизированного состояния. В связи с незначительным влиянием периода разупрочнения на долговечность при расчете НДС сильфона его не рассматрива ли. Решение задачи получали для стабилизированного после наклепа состояния, используя соответствующие кривые цик лического деформирования.
Расчет НДС сильфона в стабильном цикле при Т = const осуществляли по кривым циклического деформирования, по строенным в координатах S - е , совпадающих с началом раз грузки в полуцикле. Циклические свойства материала при не изотермическом нагружении описывались на основе представ лений о поверхности термомеханического нагружения. Расчет НДС в этом случае проводили с использованием кривых де формирования, соответствующих конечным значениям темпе ратуры в полуциклах. Полученные для максимально нагружен
ной точки сильфона значения деформаций при изотермичес ком и неизотермическом нагружениях представлены в табл. 5.3.
По значениям деформаций на основе кривых усталости стали 12Х18Н10Т для соответствующих режимов нагружения (см. рис. 1.2) было определено расчетное число циклов до разрушения jVp (табл. 5.3). Как следует из представленных данных, соответствие расчетных jVp и экспериментально полу ченных N3 значений долговечности оказывается удовлетвори тельным, расхождение не более чем в 2 раза.
Таблица 5.3
Параметры нагружения и долговечность сильфонных компенсаторов
Uv мм |
Д Е/ , % |
Д С / р , % |
Np, циклы |
N3, циклы |
Режим |
0,50 |
4,1 |
3,90 |
25 |
24 |
Т = 650 °С = const |
0,30 |
2,0 |
1,80 |
70 |
60 |
|
0,25 |
1,5 |
1,30 |
150 |
100 |
|
0,15 |
0,6 |
0,40 |
700 |
950 |
i |
0,12 |
0,4 |
0,26 |
2000 |
4000 |
|
0,50 |
3,9 |
3,60 |
10 |
14 |
Т = 650 s±150 °С |
0,25 |
1,3 |
1,00 |
40 |
60 |
(синфазный) |
|
|||||
0,15 |
0,6 |
0,40 |
300 |
550 |
|
0,12 |
0,4 |
0,22 |
600 |
- |
|
0,50 |
3,8 |
3,65 |
10 |
14 |
Т= 650 г 150 °С |
0,25 |
1,2 |
1,00 |
40 |
60 |
(противофазный) |
|
|||||
0,15 |
0,5 |
0,35 |
350 |
550 |
|
0,12 |
0,4 |
0,22 |
600 |
- |
|
Так как оболочка сильфона подвергается в основном изгибным деформациям, то при синфазном режиме перемеще ние-температура на наружной, а при противофазном — на внутренней поверхности впадины (являющейся зоной разру шения) реализуется наиболее повреждающий синфазный цикл деформация—температура. В силу этого при исследованных режимах неизотермического нагружения долговечности отли чались незначительно.
5.3.Напряженно-деформированное состояние
ициклическая прочность замковых резьбовых соединений бурильных труб
Наиболее высоконагруженными элементами бурильной ко лонны являются замковые резьбовые соединения (ЗРС) труб. Выполненный в работе [100] анализ причин аварий с буриль ными трубами показывает, что более чем в 50% случаев аварии вызваны разрушениями по резьбе.
Нагружение ЗРС носит достаточно сложный характер. На этапе свинчивания муфты и ниппеля возникают значительные напряжения на упорных торцах, во впадинах резьбы, зонах перехода от резьбовой к гладкой части ЗРС, которые могут превышать предел текучести материала. На указанные предва рительные напряжения накладываются эксплуатационные на пряжения, вызываемые действием растягивающей нагрузки (вес бурильной колонны, нагрузка на долото), наружное и внутреннее (избыточное) давления в трубе, изгибающий и кру тящий моменты, а также вибрационные и динамические на грузки.
Ниже приводятся результата анализа циклической нагруженности и долговечности ЗРС с учетом повторного свинчи вания-развинчивания, воздействия внешнего и внутреннего давлений, а также осевого растягивающего усилия [101]. В этом случае напряженно-деформированное состояние (НДС), воз никающее в ЗРС, может с достаточной степенью точности рассматриваться как осесимметричное, что позволяет исполь зовать двухмерную схему расчета. Расчет напряженно-дефор мированного состояния в ЗРС осуществляли методом конеч ных элементов. Взаимодействие ниппеля и муфты на торце и в резьбе моделировали контактными конечными элементами, позволяющими учесть проскальзывание и изменение границ контактирующих поверхностей при действии нагрузки. Рас смотрен вариант ЗРС, имеющий наружный диаметр 209,6 мм и внутренний 71,4 мм с конической резьбой типа NC56 и зарезьбовыми канавками (ЗРК) на ниппеле и муфте с радиу сами перехода R = 6,4 мм.
Соответствующая схема разбиения расчетной модели ЗРС на конечные элемента приведена на рис. 5.12. Число конечных
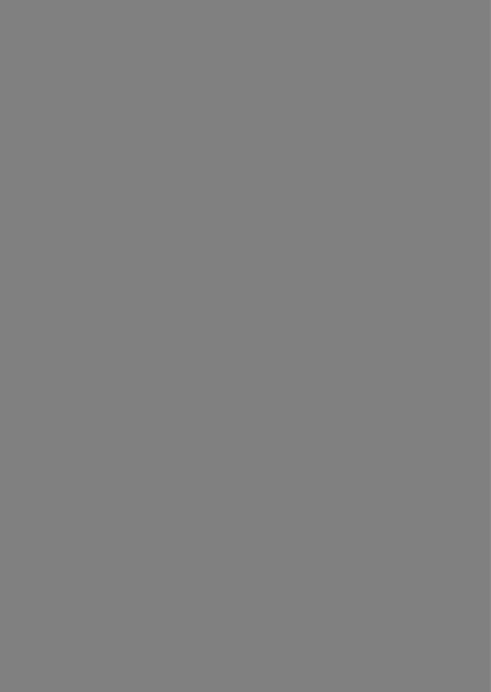
Было выполнено несколько вариантов расчета. При расчете варьировалась величина температурного расширения I, = = 0,1125...0,585 мм. Максимальное значение прикладываемых осевых напряжений во всех случаях составляло 100 МПа, гидростатическое давление —80 МПа, избыточное внутреннее давление —20 МПа.
Анализ полученных результатов расчета НДС показал, что характер изменения напряжений и деформаций в различных зонах ЗРС существенно отличается и зависит от степени за тяжки (величины температурного расширения /,) и свойств материала.
В качестве примера на рис. 5.13 показано изменение осевых напряжений во времени для различных зон ЗРС (I, = 0,585 мм, сталь 38ХНЗМФА). Кривая 1 соответствует зоне перехода ЗРК к торцу ниппеля; 2 — первой впадине резьбы ниппеля; 3 — второй впадине резьбы ниппеля; 4 - одиннадцатой впадине резьбы ниппеля; 5 —первой впадине резьбы муфты (отчет числа впадин на резьбе ниппеля проводится, начиная от упорного торца ниппеля; на муфте нумерация начинается со стороны гладкой части трубы).
О |
1 |
2 |
3 |
4 |
5 |
6 |
7 |
8 |
9 |
10 111 |
Рис. 5.13. Изменение во времени напряжений в различных зонах ЗРС
При свинчивании ЗРС (этап 0...1) осевые напряжения воз растают, причем в наиболее напряженных зонах они превыша ют предел текучести материала. Последующее приложение дав
ления и осевой нагрузки к ЗРС вызывает дальнейшее увеличе ние напряжений (этапы 1...4). На этапах 5...7 происходит раз грузка и повторное приложение осевой нагрузки по отнулевому циклу, при этом в локальных зонах осевые напряжения изме няются в упругой области и процесс деформирования стаби лизируется. При снятии давления, осевой нагрузки и развин чивании ЗРС (этапы 8... 10) в наиболее нагруженных зонах (соответствующих кривым 1, 2, 3) возникают остаточные на пряжения сжатия. При последующем свинчивании и приложе нии давления и осевой нагрузки (этап 10... 11) напряжения возрастают. На рис. 5.14 для наиболее нагруженной зоны ЗРС - первой впадине резьбы ниппеля в координатах осевое напря жение—осевая деформация —показан процесс деформирования для рассмотренной последовательности изменения нагрузок. На кривых деформирования указаны точки с номерами, соот ветствующими номерам этапов нагружения. Распределение осевых напряжений в зоне первой впадины ниппеля в конце 11-го этапа нагружения показано на рис. 5.15 (сталь 38ХНЗМФА). При данных видах внешних нагрузок характер деформирования в зонах концентрации близок к пропорцио нальному (рис. 5.16).
Из анализа НДС вытекает, что в наиболее напряженных зонах в результате повторных свинчиваний—развинчиваний
Зла
2400
1600
800
О
-800
О |
0,4 |
0,8 |
1,2 |
1,6 |
2,0 |
V- 96
Рис. 5.14. Характер упругопластического деформирования в первой впадине резьбы ниппеля при затяжке ЗРС и воздействии внешних нагрузок
ЗРС (число которых в процессе эксплуатации достигает 300— 500) происходит знакопременное упругопластическое деформи рование. Воздействие внешних нагрузок приводит к многократ ному циклическому изменению упругих локальных напряже ний, характеризующемуся высокой асимметрией цикла. Вслед ствие этого в ЗРС могут возникать повреждения от малоцик ловой и многоцикловой усталости.
Рис. 5.15. Распределение осевых напряжений (в МПа) в зоне первой впадины резьбы ниппеля
Влияние степени предварительной затяжки резьбы, задавае мой в расчете температурным расширением /,, на величину размахов осевой упругопластической деформации (вследствие свинчивания—развинчивания ЗРС), размахи осевого напряже ния Д о и среднее напряжение цикла ат , соответствующих
отнулевому циклу изменения осевой нагрузки (сгн =
= 0...100 МПа) в наиболее напряженной зоне ЗРС —первой впадине резьбы ниппеля, показаны на рис. 5.17 и 5.18.
Как следует из представленных данных, с увеличением сте пени предварительной затяжки резьбы увеличиваются размахи упругопластических деформаций в цикле свинчивание—развин-
Рис. 5.16. Изменение осевых (ст^), радиальных (ах) и тангенциальных (аг)
напряжений в первой впадине резьбы ниппеля для заданной последовательности приложения нагрузок
Дб,
%
1,0
0,5
0,1 0,2 0,3 0,4 0,5 If, мм
Рис. 5.17. Зависимость размахов упругопластичес ких деформаций Д еи пределов выносливости <т0
от степени затяжки резьбы:
1 - сталь 40ХГНМФ; 2 - сталь 40; 3 - сталь 38ХНЗМФА
чивание ЗРС. Величина затяжки оказывает также существенное влияние на размахи и среднее напряжение цикла упругих на пряжений, вызванных растягивающей осевой нагрузкой. С ее увеличением значительно уменьшаются размахи напряжений и увеличивается среднее напряжение (см. рис. 5.18; три верхние кривые — стм ; три нижние кривые —Д а). Данный результат
является логичным, так как с увеличением /, повышается жест кость ЗРС и соединение воспринимает действующую нагрузку как одно целое. При снижении предела текучести материала (при одинаковой затяжке ЗРС) происходит снижение среднего напря жения цикла, в то время как размахи напряжений сохраняются
практически постояными. |
Да,стт , |
|
|
|||||
|
,-г |
|
|
результаты |
|
|
||
|
Полученные |
мпа |
|
|
||||
позволяют |
оценить |
допусти- |
1750 |
|
|
|||
мое |
число |
циклов |
свинчива |
|
|
|
||
ния-развинчивания и значе |
1500 |
|
|
|||||
ния |
предела |
выносливости |
|
|
||||
ЗРС в зависимости от степени |
>250 |
|
|
|||||
затяжки |
резьбы. Допустимое |
|
|
|||||
число циклов |
свинчивания- |
1000 |
|
|
||||
развинчивания |
определяется |
|
|
|||||
на |
основе |
соответствующих |
|
|
|
|||
кривых малоцикловой усталое- |
|
|
|
|||||
ти материала ЗРС. Для стали |
|
|
|
|||||
38ХНЗМФА на рис. 5.19 пред |
500 |
|
|
|||||
ставлена кривая малоцикловой |
|
|
||||||
усталости |
1 по моменту обра |
250 |
|
|
||||
зования трещины, полученная |
|
|
||||||
в условиях жесткого нагруже |
о, / |
0,2 |
0,3 0,4 0,51,, мм |
|||||
ния |
при |
растяжении—сжатии |
||||||
(нижняя |
огибающая). Кривая |
|
|
|
||||
допустимых значений размахов |
Рис. 5.18. Зависимость размахов осе- |
|||||||
деформаций 2 соответствует де- |
вого Д а И среднего напряжений цикла |
|||||||
сятикратному запасу прочности |
в пеРВ0Йвпадине резьбы ниппеля |
|||||||
по числу циклов и двукратному |
от стеяени затяжки резьбы; |
|||||||
по деформациям [102]. При из- |
|
|
2_сталь40; J " сталь |
|||||
менении степени затяжки резь |
I, = 0,1125-0,585 мм, размахи |
|||||||
бы |
в диапазоне, |
определяемом |
||||||
деформаций |
находятся в пределах Де |
= |
0,546...1,52% (см. |
рис. 5.17) и допустимое число свинчиваний—развинчиваний ЗРС составляет от 60 до 1500 циклов.
Рис. 5.19. Кривые малоцикловой усталости материала ЗРС:
1 и 2 - соответственно нижняя огибающая и расчетная кривые для стали 38ХНЗМФА; 3 - нормативная кривая
В области многоцикловых нагрузок влияние конструктив ных особенностей замковых резьбовых соединений (уровень концентрации напряжений, масштабный фактор, вид нагруже ния) на средние значения и коэффициенты вариации пределов выносливости ЗРС наиболее полно может быть учтено на ос нове теории подобия усталостного разрушения [103]. В соот ветствии с данным подходом, в основе которого лежит теория прочности «наиболее слабого звена» Вейбулла, функция рас пределения пределов выносливости имеет вид
/= - 2 ,3 l g ( l -/>) = [ qmax/(*> Я - «] ” dF |
(5-3) |
FJ |
|
где Р — Р (сгтах) —вероятность появления усталостной трещины
в ЗРС при максимальном первом главном напряжении в зоне концентрации, не превышающем заданное значение отах;
f(x, у ) —безразмерная функция, описывающая эпюру распре деления первого главного напряжения по поперечному сече-
нию; и, SQ, т — параметры распределения Вейбулла; Fu - зона интегрирования, определяемая условием атах > и ; и - мини
мальная граница пределов выносливости; F0 - площадь еди ничного элемента (F0 = 1).
При линейной аппроксимации распределения напряжений в зоне интегрирования из (5.3) после выполнения ряда преобразо ваний в [103] получено уравнение подобия в форме, соответст вующей нормальному распределению величины х = lg(£ - 1),
|
lg($ - |
1) = -v 0 lge + upS, |
где ^ = ■max ; 0 = |
— относительный критерий подобия |
|
u |
(L/G)о |
|
усталостного разрушения; (L/GQ) = 88,3 мм2 - значение кри терия L/G для гладкого лабораторного образца диаметром d = = 7,5 мм при изгибе с вращением; L — периметр рабочего сечения детали; G - относительный градиент напряжений, мм-1; vc —характеристика материала, определяющая его чув
ствительность к концентрации напряжений и масштабному фактору; ир —квантиль нормального распределения, соответ ствующий вероятности разрушения (появления трещины) Р, %; S —среднее квадратическое отклонение случайной величи ны х = lg(5 - 1).
На основе данных соотношений ниже приведен расчет пре делов выносливости ЗРС из сталей 38ХНЗМФА, 40ХГНМФ и стали 45 в зависимости от степени затяжки резьбы. В связи с отсутствием прямых опытных данных для стали 38ХНЗМФА, используя рекомендации [103], получены следующие парамет ры: vc = 0,04; Ч»в = 0,225.
Для пластичных металлов и = 0,5o_i, где ст_] - медианное
значение предела выносливости гладкого лабораторного образ ца диаметром 7,5 мм при изгибе с вращением. Значение о_j
приближенно можно оценить по корреляционной зависимости: = (0,55 - 0,0001ал) = 624 МПа, откуда и = 312 МПа.
Величина S определяется соотношением
= |
0,62 |
0,025. |
|
l/ve - 0,36 |
|
|
|
По данным расчета НДС для наиболее опасного сечения ЗРС —по первой впадине резьбы на ниппеле L /G = 612 мм2; lg0 = 0,841.
Таким образом, для рассматриваемого сечения получим следующее уравнение подобия:
№ ~ 1) = ~0,841va + 0,025ыр. Для вероятности разрушения 50% (ир = 0)
lg($ - 1) = "0,0336.
Отсюда %= 1,93, а максимальное значение напряжений для симметричного цикла составляет отах = и £ = 602 МПа.
С учетом влияния среднего напряжения цикла ат предель ная амплитуда напряжений выражается зависимостью
а Л = « £ - ¥ а ам ,
где коэффициент Т0 , характеризующий влияние асимметрии цикла, по данным [103], можно принять равным '¥а = 0,225.
Учитывая, что коэффициент концентрации напряжений в рас сматриваемой зоне ЗРС составляет а ст = А а / А ап , получим сле
дующее выражение для величины предела выносливости ЗРС при отнулевом цикле номинальных напряжений ст0 = стл/ а 0 .
Полученная на основе данных соотношений зависимость величины ст0 от 1( показана в виде кривой с экстремумом на
рис. 5.17. Величина затяжки lt , соответствующая максималь ному значению предела выносливости, является оптимальной.
Аналогичные расчеты выполнены для стали 40ХГНМФ
(ст_! = 450 МПа, va = |
0,065, |
= 0,225) и стали 45 (CT_J = |
= 307 МПа, v0 = 0,1, |
= 0,15). Соответствующие кривые |
|
ст0 —lt показаны на рис. 5.17. |
|
Полученные значения пределов выносливости соответству ют полированной поверхности резьбовых канавок. Учет фак
тического качества поверхности и поверхностного упрочнения можно провести по изложенной в [103] методике.
Хотя расчет пределов выносливости ЗРС выполнен для случая нагружения осевой растягивающей силой, основные выводы о влиянии степени затяжки, конструкционных особен ностей, типа материала на усталостные характеристики ЗРС сохраняют свое значение и при изгибных нагрузках, так как различия в данных видах нагружения не носят принципиаль ного характера.
При эксплуатационных напряжениях ниже предела уста лости долговечность ЗРС будет определяться малоцикловыми повреждениями, возникающими вследствие процессов свинчи вания-развинчивания. В связи с этим вопрос о выборе опти мальной степени затяжки резьбы должен решаться в зависи мости от особенностей эксплуатации ЗРС не только исходя из условия обеспечения максимальных значений предела вынос ливости, но и с учетом возможного числа свинчиваний-раз винчиваний ЗРС, так как оно при затяжке, соответствующей экстремуму на кривых ст0 - , является достаточно ограничен
ным. Для стали 38ХНЗМФА оно составляет 450 циклов при Д е = 0,75 % (см. рис. 5.19, кривая 2). Для стали 40ХГНМФ и стали 45 оно определялось по нормативной кривой [102], пред ставленной на рис. 5.19 в деформациях (кривая 3) и составляет соответственно 120 циклов (Д е = 0,75 %) и 90 циклов (Д е = = 0,85 %).