
Оборудование и оснастка для формования металлических порошков
..pdfМинистерство образования и науки Российской Федерации
Государственное образовательное учреждение высшего профессионального образования «Пермский государственный технический университет»
А.П. Вакутин, М.Н. Каченюк
ОБОРУДОВАНИЕ И ОСНАСТКА ДЛЯ ФОРМОВАНИЯ МЕТАЛЛИЧЕСКИХ ПОРОШКОВ
Утверждено Редакционно-издательским советом университета
в качестве учебного пособия
Издательство Пермского государственного технического университета
2010
elib.pstu.ru
УДК 620
В14
Рецензенты:
начальник констр.-технолог. отдела металлург. производства В.Г. Александров (ЗАО «Новомет»),
д-р техн. наук, профессор Л.Д. Сиротенко (Пермский государственный технический университет)
Вакутин, А.П.
В14 Оборудование и оснастка для формования металлических порошков: учеб. пособие / А.П. Вакутин, М.Н. Каченюк. – Пермь: Изд-во Перм. гос. техн. ун-та, 2010. – 108 с.
ISBN 978-5-398-00490-8
Рассмотрены основные принципы формования заготовок из металлических порошков при помощи прессования в ручных и автоматических пресс-формах. Описаны основные моменты расчета и проектирования пресс-оснастки, а также некоторые виды прессов для прессования изделий из металлических порошков.
Предназначено для студентов кафедры «Порошковое материаловедение», а также для начинающих специалистов-конст- рукторов в области разработки пресс-оснастки для порошковой металлургии.
|
УДК 620 |
ISBN 978-5-398-00490-8 |
© ГОУ ВПО |
|
«Пермский государственный |
|
технический университет», 2010 |
2 |
|
elib.pstu.ru
ОГЛАВЛЕНИЕ |
|
Введение.................................................................................................... |
6 |
Глава 1. ПРЕСС-ФОРМЫ ДЛЯ ФОРМОВАНИЯ |
|
МЕТАЛЛИЧЕСКИХ ПОРОШКОВ, ПРОЕКТИРОВАНИЕ |
|
И РАСЧЕТ................................................................................................. |
7 |
1.1. Формование порошковых систем........................................... |
7 |
1.2. Разработка чертежа заготовки................................................ |
9 |
1.3. Пресс-формы для ручного и автоматического |
|
прессования...................................................................................... |
11 |
1.3.1. Пресс-формы для ручного прессования....................... |
13 |
1.3.1.1. Разработка сборочного чертежа пресс-форм |
|
для ручного прессования .................................................. |
13 |
1.3.1.2. Конструкция матриц ............................................ |
15 |
1.3.1.3. Конструкция подставок ....................................... |
17 |
1.3.1.4. Варианты освобождения прессовок |
|
от пуансонов....................................................................... |
19 |
1.3.1.5. Порядок прессования........................................... |
22 |
1.3.1.6. Порядок освобождения изделия.......................... |
24 |
1.3.2. Пресс-формы для автоматического прессования........ |
24 |
1.3.2.1. Матрицы................................................................ |
24 |
1.3.2.2. Пуансоны............................................................... |
25 |
1.3.2.3. Стержни................................................................. |
26 |
1.3.2.4. Контроль за ходом прессования изделия........... |
26 |
1.4. Расчет деталей пресс-форм на прочность и размеры........... |
27 |
1.4.1. Определение высоты загрузочной камеры .................. |
27 |
1.4.2. Расчет размеров рабочей полости матрицы................. |
28 |
1.4.3. Расчет стержней, оформляющих внутренний |
|
диаметр прессовки.................................................................... |
28 |
1.4.4. Расчет матрицы на прочность....................................... |
29 |
1.4.5. Расчет пуансонов на сжатие и изгиб ............................ |
30 |
1.4.6. Расчет пружин................................................................. |
31 |
1.5. Выбор посадок и допусков...................................................... |
31 |
1.6. Выбор шероховатости поверхности....................................... |
33 |
1.7. Выбор отклонения расположения поверхностей.................. |
35 |
1.8. Выбор материалов для изготовления пресс-форм................ |
35 |
1.9. Калибрование........................................................................... |
37 |
|
3 |
elib.pstu.ru
1.9.1. Калибрование сложных изделий................................... |
38 |
1.9.2. Припуск на калибрование.............................................. |
38 |
1.9.3. Смазка инструмента и изделий..................................... |
38 |
Глава 2. ПРЕССЫ ДЛЯ ФОРМОВАНИЯ МЕТАЛЛИЧЕСКИХ |
|
ПОРОШКОВ............................................................................................. |
39 |
2.1. Гидравлический пресс П-125.................................................. |
39 |
2.1.1. Технические данные....................................................... |
39 |
2.1.2. Общее устройство пресса .............................................. |
39 |
2.1.3. Нагружающее устройство.............................................. |
40 |
2.1.4. Пульт управления........................................................... |
42 |
2.1.5. Панель управления......................................................... |
42 |
2.1.6. Силоизмеритель.............................................................. |
44 |
2.1.7. Правила работы на прессе ............................................. |
46 |
2.2. Автомат механический К 8130 ............................................... |
48 |
2.2.1. Назначение и область применения............................... |
48 |
2.2.2. Общее устройство пресса .............................................. |
49 |
2.2.3. Пневмофрикционная муфта .......................................... |
52 |
2.2.4. Коробка передач............................................................. |
54 |
2.2.5. Тормоз пресса ................................................................. |
56 |
2.2.6. Главный привод пресса.................................................. |
57 |
2.2.7. Верхняя прессующая головка........................................ |
58 |
2.2.8. Выталкиватель................................................................ |
61 |
2.2.9. Привод и верхний упор центрального стержня........... |
63 |
2.2.10. Упор выталкивателя и нижний упор центрального |
|
стержня...................................................................................... |
65 |
2.2.11. Привод питателя........................................................... |
67 |
2.2.12. Пневматическая система пресса ................................. |
68 |
2.2.13. Командный аппарат...................................................... |
69 |
2.2.14. Циклограмма работы пресса........................................ |
69 |
2.2.15. Порядок монтажа и демонтажа |
|
пресс-инструмента.................................................................... |
71 |
2.3. Автомат механический КБ 8130A.......................................... |
73 |
2.3.1. Назначение и область применения............................... |
73 |
2.3.2. Кинематическая схема и устройство преcсa................ |
75 |
2.3.3. Муфта сцепления и тормоз............................................ |
77 |
2.3.4. Ползун.............................................................................. |
78 |
2.3.5. Baриатор.......................................................................... |
80 |
4
elib.pstu.ru
2.3.6. Механизм стягивания матрицы..................................... |
80 |
2.3.7. Уравновешиватель.......................................................... |
81 |
2.3.8. Упоры матрицы............................................................... |
81 |
2.3.9. Блок прессующий........................................................... |
82 |
2.3.10. Циклограмма работы пресс-автомата......................... |
83 |
2.4. Автомат механический АПФ 100........................................... |
84 |
2.4.1. Назначение и область применения............................... |
84 |
2.4.2. Общее устройство пресса .............................................. |
85 |
2.4.3. Главная рама пресса....................................................... |
87 |
2.4.4. Вариатор.......................................................................... |
89 |
2.4.5. Упор................................................................................. |
89 |
2.4.6. Цилиндр удержания ....................................................... |
89 |
2.4.7. Ползун.............................................................................. |
90 |
2.4.8. Механизм дожима........................................................... |
90 |
2.4.9. Механизм стягивания..................................................... |
91 |
2.4.10. Верхний упор положения механизма стягивания..... |
92 |
2.4.11. Устройство и принцип работы прессующего |
|
инструмента............................................................................... |
92 |
2.5. Пресс-автомат гидравлический ПА 250 ................................ |
94 |
2.5.1. Назначение и область применения............................... |
94 |
2.5.2. Общее устройство пресса .............................................. |
95 |
2.5.3. Управление прессом....................................................... |
98 |
2.5.4. Гидравлическая схема пресса........................................ |
101 |
2.5.5. Силовые регулировки пресса........................................ |
103 |
2.5.6. Описание цикла получения одного изделия................ |
104 |
СПИСОК ЛИТЕРАТУРЫ ....................................................................... |
107 |
5
elib.pstu.ru
ВВЕДЕНИЕ
Развитие машиностроения и металлобработки требует дальнейшего совершенствования технологических процессов изготовления деталей. Среди имеющихся разнообразных процессов обработки металлов порошковая металлургия успешно конкурирует с литьем, обработкой давлением, резанием и другими методами, дополняя или заменяя их.
Значительную долю в стоимости изделий из металлических порошков занимает оснастка. От того, насколько будет правильно выбрана схема прессования и конструкция оснастки, зависит ее долговечность и сложность изготовления.
При разработке оснастки учитывают способ формования, тип пресса и природу формуемого материала. Для каждого типа пресса существует определенный порядок движения рабочих органов, который должен учитываться в конструкции прессинструмента.
Чтобы четко представлять возможности пресса, необходимо знать его устройство и привязку к нему пресс-инструмента. Без хорошего знания настроек пресса невозможно грамотно сконструировать оснастку.
Настоящее учебное пособие знакомит с основами проектирования и расчета формующей и калибрующей оснастки и устройством и принципом работы гидравлических и механических пресс-автоматов, наиболее широко используемых в промышленности. Даны практические рекомендации по прессованию и настройке пресс-инструмента.
6
elib.pstu.ru
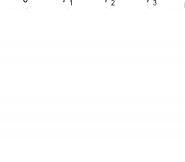
Глава 1
ПРЕСС-ФОРМЫ ДЛЯ ФОРМОВАНИЯ МЕТАЛЛИЧЕСКИХ ПОРОШКОВ, ПРОЕКТИРОВАНИЕ И РАСЧЕТ
1.1. Формование порошковых систем
Формование – процесс получения из порошка изделия определенной формы и размеров, обладающего достаточной механической прочностью. Сформованное изделие можно извлечь из пресс-формы и подвергнуть дальнейшей обработке.
Холодное прессование характеризуется величиной давления и временем приложения нагрузки.
Способ холодного прессования включает дозировку шихты, засыпку порошка в полость пресс-формы, прессование изделия, выдержку под давлением и выталкивание спрессованного изделия.
Процесс формования складывается из трех стадий (рис. 1).
На первой стадии увеличе-
ние плотности порошковой сис- темы происходит за счет пере-
мещения частиц порошка отно-
сительно друг друга, заполнения
пустот и разрушения арок.
На второй стадии наблю-
дается деформация контакт- ных участков частиц порошка и увеличение металлического
контакта между ними, разрушение конгломератов, скалывание выступов и сдирание окисных пленок.
На третьей стадии приложенное давление вызывает искажение кристаллической решетки материала порошка, что сопровождается ростом внутренних напряжений и твердости час-
7
elib.pstu.ru
тиц. Это приводит к повышению усилий формования, и прирост плотности изделия замедляется.
Порошковые металлы, в отличие от компактных, в процессе деформации изменяют первоначальный объем. Это происходит как вследствие деформации отдельных частиц, так и вследствие их смещения и заполнения ими пор. Обычно при формовании высота заготовки по отношению к высоте насыпанного порошка уменьшается в 3–4 раза и более.
В процессе прессования порошок, находящийся в полости пресс-формы, стремится к растеканию в стороны, но при этом удерживается стенками матрицы. Возникает боковое давление порошка на стенки матрицы, которое в результате внутреннего трения между частицами меньше по сравнению с осевым давлением прессования. Вместе с тем из-за наличия сил бокового давления возникают силы трения между порошком и стенкой матрицы, препятствующие получению равномерной плотности брикета.
При одностороннем прессовании повышенная плотность наблюдается под прессующим пуансоном, наименьшая – у неподвижного пуансона. При использовании схемы двухстороннего прессования пониженная плотность наблюдается примерно в середине высоты брикета.
После снятия давления прессовка в результате упругих деформаций плотно сидит в формующей полости матрицы, и для ее извлечения следует приложить усилие, составляющее 20–35 % от усилия прессования. Обычно прессовка извлекается из матрицы выталкиванием или стягиванием матрицы с изделия.
После освобождения прессовки из полости матрицы наблюдается некоторое увеличение ее размеров по высоте и диаметру. Это явление называется упругим последействием и учитывается при расчете размеров формующей полости матрицы.
Величина упругого последействия, %, рассчитывается по формуле
8
elib.pstu.ru
δ = (l1 – l0)100 / l0,
где l1 – диаметр изделия после выталкивания, мм; l0 – диаметр пресс-формы, мм.
Снизить величину упругого последействия помогают смазки, вводимые в шихту перед формованием. Смазки уменьшают трение между частицами порошка, а также между прессовкой и стенками пресс-формы. Наиболее существенное влияние на процесс прессования оказывают активные смазки, изменяющие физико-механические свойства порошковых частиц. Наряду с активными существуют инертные смазки, не оказывающие какого-либо воздействия на материал порошка. В качестве таких смазок используют стеариновую кислоту, парафин, дисульфид молибдена, масло, поливиниловый спирт, глицерин и другие вещества. Смазки вводят в шихту или смазывают ими полость пресс-формы с помощью кисти или методом распыления.
Прессование, в зависимости от схемы приложенного давления, может быть односторонним и двусторонним. Одностороннее прессование применяется при изготовлении простых деталей типа пластина или диск с отношением высоты изделия к его диаметру h/d < 1, для гладких втулок – с отношением высоты к минимальному значению толщины стенки h/smin < 3.
Схема двухстороннего прессования используется для фор-
мования изделий, протяженных по высоте. Для достижения той же плотности она требует усилия прессования меньше на
30–40 %.
1.2. Разработка чертежа заготовки
При разработке чертежа заготовки, которая представляет вид изготовляемой детали после прессования и спекания, необходимо учитывать следующие факторы:
1.Материал, из которого будет изготовляться деталь.
2.Удельное давление прессования выбранного материала, для расчета общего усилия прессования.
9
elib.pstu.ru
3.Общее усилие прессования. При усилии прессования до 160 тс выбирают прессование на механических пресс-автоматах, при общем усилии прессования более 160 тс применяют прессование на гидравлических прессах. Гидравлические прессы имеют меньшую производительность, чем механические.
4.Порошковые материалы при спекании в большинстве случаев имеют усадку, которая определяется:
–родом материала. Медные и никелевые порошки имеют большую усадку, чем железные и титановые;
–формой детали. Полые детали садятся в радиальном направлении больше, чем сплошные;
–удельным давлением прессования. Чем выше удельное давление прессования, тем меньше усадка;
–направлением прессования. Усадка в диаметральном направлении изделия составляет 1–2 %, а в осевом – 0,5–1 %;
–конструкцией пресс-формы. Разъемные матрицы, обладая меньшей жесткостью, выдают более полные размеры.
5.Шероховатость поверхности. Поверхность порошковых заготовок после спекания соответствует шероховатости Rz 20. При требовании чертежа на меньшую шероховатость следует оставлять припуск под механическую обработку или калибрование. Припуск под механическую обработку должен составлять 0,3–0,5 мм на сторону, с тем чтобы его можно было снять за один проход.
6.Точность заданных размеров. При разработке чертежа заготовки без дополнительной доработки изделия можно выполнить размеры, имеющие отклонения примерно 1 % от номинального размера, при более жестких допусках следует предусматривать припуск на механическую обработку или калибрование. Особое внимание следует обращать на выполнение межосевых размеров, они, как правило, определяют собираемость
вконструкции. Если заданная точность не обеспечивается, можно оставить больший припуск на обработку отверстий. Пример выполнения рабочего чертежа заготовки показан на рис. 2.
10
elib.pstu.ru