
Оборудование и оснастка для формования металлических порошков
..pdfПуансоны длиной l > 3d необходимо проверять на предельный изгиб. Сила, при которой может начаться изгиб пуансона, называется критической Pкрит, Н,
Pкрит = 2 · π2 Eмин I/L2,
где L – длина свободной части пуансона, м;
I – момент инерции наименьшего сечения пуансона.
P ≤ Pкрит/n,
где Р – допускаемое усилие прессования, Н; n = 2…3.
1.4.6. Расчет пружин
Осадка для винтовой цилиндрической пружины сжатия
Lконечн, м, при предельно допускаемой нагрузке Pконечн, кН, составит:
Lконечн = 8 PконечнD3i |
, |
Gd 4 |
|
где D – средний диаметр пружины, м; |
|
d – диаметр проволоки пружины, м; |
|
I – число рабочих витков, шт.; |
|
G – модуль сдвига для материала |
пружины, МПа, G = |
= 80000 МПа. |
|
1.5. Выбор посадок и допусков
Пресс-формы для холодного прессования являются достаточно сложным видом технологической оснастки. При изготовлении пресс-формы необходимо правильно выдержать допуски на размеры с целью обеспечения оптимальных зазоров между рабочими частями пресс-формы. Так, пуансоны должны свободно перемещаться относительно матрицы, а элементы составной неразборной матрицы быть относительно друг друга неподвижными.
Для подвижных посадок диаметр вала должен быть меньше диаметра отверстия, то есть между валом и отверстием должен
31
elib.pstu.ru
быть некоторый зазор. Для неподвижных посадок диаметр вала должен быть больше диаметра отверстия, положительная разность между размером вала и отверстием называется натягом.
Характер соединения деталей, определяемый величиной получающихся в нем зазоров или натягов, в машиностроении называют посадкой.
Выбор посадки при проектировании пресс-форм определяется зернистостью порошковой шихты. При прессовании мелких изделий из порошков средней и тонкой зернистости зазор между матрицей и пуансонами или пуансонами и стержнем должен быть не более 0,013–0,012 мм. При прессовании грубозернистых порошков или при изготовлении изделий диаметром более 50 мм зазор может быть увеличен. Следует помнить, что зазор должен обеспечивать свободный выход воздуха из полости пресс-формы при уплотнении порошка.
В промышленности для осуществления разных посадок чаще применяют систему отверстия, при которой для всех посадок одного класса точности при одинаковых номинальных размерах предельные размеры отверстия остаются постоянными, а осуществление разных посадок достигается за счет соответствующего изменения предельных размеров вала.
Для условного обозначения допусков в стандарте СтСЭВ 145–75 используются латинские буквы и цифры. Так, положительные отклонения отверстий обозначаются прописными буквами A, В, C, D, E, F, Q, H, а отрицательные отклонения валов – соответственно строчными буквами a, b, c, d, e и т.д. Кроме того, допуски, величина которых зависит от номинальных размеров, обозначаются цифрами (квалитет).
Таким образом, размер, для которого указывается поле допуска, обозначается числом (например, номинальным диаметром), за которым следует условное обозначение допуска, состоящее из буквы и цифры: 24g6; 24Н7.
Посадки с гарантированным зазором (подвижные) применяют при сопряжениях пуансон – матрица, пуансон – пуансон,
32
elib.pstu.ru
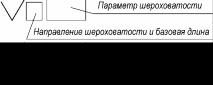
пуансон – стержень. Посадки H7/h6, H8/h7 используют в прессформах небольших размеров и для мелких порошков, посадки H8/h7, H8/f7 – для пресс-форм больших размеров и крупных порошков, а также для автоматических пресс-форм. Посадки с гарантированным зазором позволяют исключить заклинивание подвижных частей пресс-формы при наличии некоторой несоосности в автоматических пресс-блоках.
Для сопряжения деталей подставка – упор используется по-
садка H9/h8; H11/h11.
Посадки с гарантированным натягом используют в случае неразборных матриц для сопряжения внутренней и наружной обойм, для сочленения комбинированных стержней и в других случаях, когда требуются неподвижные соединения. H8/u7 – тяжелая посадка для тяжело нагруженного соединения, H8/s7 – средняя посадка для соединения со средней по величине нагрузкой.
Величины допусков на валы и отверстия автоматически выбираются при выполнении чертежей в системе «Компас».
1.6.Выбор шероховатости поверхности
Всвязи с применением очень малых зазоров между сопрягающимися поверхностями последние обрабатывают до высокой чистоты, которая необходима также для снижения сил трения, возникающих при прессовании порошка и выталкивании спрессованных изделий.
Структура обозначения шероховатости поверхности приведена на рис. 14.
Шероховатость поверхности, обеспечиваемая
разными методами механи- ческой обработки, показана Рис. 14. Структура обозначения
в табл. 2.
шероховатости поверхности
33
elib.pstu.ru
Таблица 2
Виды механической обработки и создаваемая шероховатость поверхности
Методы |
|
|
|
|
Параметры шероховатости |
|
|
|
||||||||
|
|
Rz |
|
|
|
|
|
|
Ra |
|
|
|
||||
обработки |
|
|
|
|
|
|
|
|
|
|
|
|||||
320 |
160 |
|
80 |
40 |
20 |
|
2,5 |
1,25 |
0,63 |
0,32 |
0,16 |
0,08 |
0,04 |
|||
|
предва- |
|
|
|
|
|
|
|
|
|
|
|
|
|
|
|
|
ритель- |
+ |
+ |
|
+ |
+ |
|
|
|
|
|
|
|
|
|
|
Обтачи- |
ное |
|
|
|
|
|
|
|
|
|
|
|
|
|
|
|
вание |
чисто- |
|
|
|
+ |
+ |
+ |
|
+ |
+ |
|
|
|
|
|
|
|
вое |
|
|
|
|
|
|
|
|
|
|
|||||
|
|
|
|
|
|
|
|
|
|
|
|
|
|
|
|
|
|
тонкое |
|
|
|
|
|
|
|
|
+ |
+ |
+ |
|
|
|
|
|
предва- |
|
|
|
|
|
|
|
|
|
|
|
|
|
|
|
|
ритель- |
|
|
|
|
|
|
|
+ |
+ |
|
|
|
|
|
|
Шлифо- |
ное |
|
|
|
|
|
|
|
|
|
|
|
|
|
|
|
вание |
чисто- |
|
|
|
|
|
|
|
|
|
+ |
+ |
|
|
|
|
|
вое |
|
|
|
|
|
|
|
|
|
|
|
|
|
||
|
|
|
|
|
|
|
|
|
|
|
|
|
|
|
|
|
|
тонкое |
|
|
|
|
|
|
|
|
|
|
+ |
|
+ |
|
|
Притир- |
грубая |
|
|
|
|
|
|
|
|
|
+ |
+ |
|
|
|
|
средняя |
|
|
|
|
|
|
|
|
|
|
+ |
|
+ |
|
|
|
ка |
|
|
|
|
|
|
|
|
|
|
|
|
|
|||
тонкая |
|
|
|
|
|
|
|
|
|
|
|
|
+ |
+ |
+ |
|
|
|
|
|
|
|
|
|
|
|
|
|
|
||||
Шлифование – |
|
|
|
|
|
|
|
|
|
|
|
|
+ |
+ |
+ |
|
отделка |
|
|
|
|
|
|
|
|
|
|
|
|
|
|||
|
|
|
|
|
|
|
|
|
|
|
|
|
|
|
|
|
|
|
|
|
|
|
|
|
|
|
|
|
|
|
|
|
|
Вид обработки поверхности указывают в обозначении шероховатости только в случаях, когда он является единственным применимым для получения требуемого качества поверхности.
Внутреннюю поверхность матриц для уменьшения сил трения обрабатывают на шероховатость Ra 0,1, на последней стадии обработки используют притирку и полировку. Боковые поверхности пуансонов, стержней обрабатывают на шероховатость Ra 0,16; 0,08. Желательно, чтобы направление рисок при последней операции шлифования или притирки совпадало с направлением прессования или выпрессовки изделия. Сопрягаемые поверхности внутренней и наружной обойм разборной матрицы имеют шероховатость Ra 2,5.
34
elib.pstu.ru

1.7. Выбор отклонения расположения поверхностей
Для обеспечения надежной работы пресс-форм необходимо руководствоваться следующими техническими требованиями:
–отклонение от плоскостности верхней торцевой поверхности матрицы должно быть не более 0,02 мм на длине 100 мм;
–отклонение от параллельности торцевых плоскостей матрицы должно быть не более 0,01 мм на длине 100 мм;
–отклонение от перпендикулярности образующей внутренней поверхности матрицы к верхней торцевой поверхности – не более 0,02 мм на длине 100 мм;
–отклонение от параллельности опорных плоскостей верхнего и нижнего пуансонов и центрального стержня относительно верхней торцевой поверхности матрицы – не более 0,01 мм на длине 100 мм;
Рис. 15. Условное обозначение отклонений расположения поверхностей
Примеры обозначения отклонения расположения поверхностей показаны на рис. 15.
1.8. Выбор материалов для изготовления пресс-форм
Стали, рекомендуемые для изготовления деталей прессформ, указаны в табл. 3.
Высокохромистые стали Х12Ф и XI2M в закаленном состоянии благодаря наличию большого количества карбидов отличаются очень высокой стойкостью на истирание. Закалка с температуры 950–970 °С с охлаждением в масле дает на этих сталях сквозную прокаливаемость толщиной 70–80 мм.
35
elib.pstu.ru
Таблица 3 Стали, рекомендуемые для изготовления деталей пресс-форм
Наименование |
|
Марка стали |
Твердость, |
||
деталей пресс-форм |
|
Основная |
Заменитель |
HRC |
|
Пуансоны и матрицы простой |
ХВГ, ХГ, 9ХС |
У8А, 9Х, Х |
54–58 |
||
и средней сложности |
|
|
|
|
|
Пуансоны и матрицы слож- |
Х12Ф, Х12М |
У10А, 8ХФ |
|
||
ной конфигурации, работаю- |
ХВ5, 4ХВ2С |
54–58 |
|||
щие при больших нагрузках |
|
|
|||
Пуансоны и |
матрицы |
для |
ВК6, Х12М, |
9ХС, ХВ5 |
|
прессования |
порошков |
твер- |
Х12Ф |
58–62 |
|
дых сплавов |
|
|
|
|
|
|
|
|
|
|
|
Вспомогательные детали |
|
У7А |
Ст. 45 |
40–50 |
Величины натягов для запрессовки цилиндрических твердосплавных матриц в обойму приведены в табл. 4.
Таблица 4 Величины натягов под запрессовку матриц из твердого сплава
Наружный |
Натяг |
Наружный |
Натяг |
||
диаметр встав- |
диаметр встав- |
||||
под запрессовку, |
под запрессовку, |
||||
ки из твердого |
мм |
ки из твердого |
мм |
||
сплава, мм |
сплава, мм |
||||
|
|
||||
От 11 до 14 |
От 0,03 до 0,04 |
От 45 |
до 51 |
От 0,11 до 0,13 |
|
От 14 до 17 |
От 0,04 до 0,05 |
От 51 |
до 76 |
От 0,11 до 0,14 |
|
От 17 до 21 |
От 0,05 до 0,06 |
От 76 |
до 89 |
От 0,14 до 0,19 |
|
От 21 до 24 |
От 0,07 до 0,08 |
От 85 |
до 102 |
От 0,17 до 0,20 |
|
От 24 до 29 |
От 0,08 до 0,09 |
От 102 до 127 |
От 0,18 до 0,23 |
||
От 29 до 35 |
От 0,09 до 0,11 |
От 127 до 153 |
От 0,20 до 0,25 |
||
От 35 до 45 |
От 0,10 до 0,11 |
От 153 до 178 |
От 0,23 до 0,25 |
Прессующий инструмент, изготовленный из твердых сплавов, обладает наибольшей износостойкостью. Твердость этих сплавов намного выше, чем твердость инструментальных ста-
36
elib.pstu.ru
лей. Твердые сплавы, обладая высокой прочностью на сжатие, плохо работают на растяжение. Поэтому матрицы всегда стягиваются обоймами. В качестве материала для обойм рекомендуются стали У8, 40Х, закаленные на твердость НRС 40–44.
1.9. Калибрование
Спеченное изделие при приложении давления деформируется значительно меньше, чем порошок, поэтому нельзя получить обжатием такую же размерную точность, какая получается у сырых изделий после прессования.
Обычно инструмент для калибрования аналогичен по конструкции инструменту для прессования. Давление при калибровании на 50–60 % выше, чем при прессовании порошка.
Для выполнения калибровки могут использоваться кривошипные и кривошипно-коленные прессы. При одинаковой мощности кривошипно-коленные прессы имеют значительно меньший ход ползуна и обеспечивают большее количество ходов в единицу времени. Для калибрования могут быть использованы автоматические пресс-автоматы типа КО и др.
Пресс-формы для допрессовки и калибрования проектируются с учетом следующих требований:
–матрица, пуансоны и стержни должны обладать максимальной жесткостью;
–размеры наружных поверхностей следует калибровать раньше, чем размеры отверстий. Откалиброванная поверхность должна находиться в контакте с калибрующей поверхностью инструмента, пока не закончится последняя стадия калибрования;
–входная кромка калибровочного стержня выполняется конусной с углом наклона 1–2°. Место перехода от конусной поверхности к цилиндрической скругляется по радиусу, равному высоте рабочей части. С увеличением угла наклона возрастают сдвигающие усилия, что вызывает разрыхление поверхностных слоев материала и даже сквозных поясных трещин.
37
elib.pstu.ru
1.9.1. Калибрование сложных изделий
Калибрование сложных изделий имеет специфические особенности, которые необходимо учитывать при проектировании пресс-форм:
–ось плунжера пресса должна совпадать с центром давления по сечению детали;
–при калибровании изделия с параллельными отверстиями стержни, закрепленные на одном основании, обладают малой жесткостью, поэтому следует тщательно контролировать размер между центрами отверстий;
–калибрование втулки с буртом осуществляют в два этапа: сначала калибруют поверхность по наружному диаметру с образованием фаски на торце втулки и конуса в месте перехода втулка – бурт, а затем производят окончательное калибрование по всей длине;
–отверстия изделий должны иметь отрицательный припуск на калибрование, чтобы стержни могли войти в отверстия свободно, прежде чем начнется калибрование наружной поверхности.
1.9.2. Припуск на калибрование
Припуск должен быть минимальным, чтобы усилия калибрования были невелики. Необходимо, чтобы величина уплотнения изделия при калибровании изменялась не более чем на
1–3 %.
1.9.3. Смазка инструмента и изделий
При калибровании применяют следующие способы смазки:
–смазка поверхности изделия жидкой распыленной смазкой;
–сухая смазка поверхности изделия во вращающемся барабане;
–пропитка изделия маслом;
–смазка рабочих поверхностей матрицы и стержня.
38
elib.pstu.ru
Глава 2
ПРЕССЫ ДЛЯ ФОРМОВАНИЯ МЕТАЛЛИЧЕСКИХ ПОРОШКОВ
2.1. Гидравлический пресс П-125
2.1.1. Технические данные
Гидравлический пресс П-125 предназначен для испытания материалов на сжатие, а также прессования заготовок из порошковой шихты в металлических пресс-формах.
Наибольшая предельная нагрузка, тс |
125 |
Высота рабочего пространства между опорными плитами, мм |
800 |
Ширина рабочего пространства, мм |
410 |
Скорость перемещения рабочего стола без нагрузки, мм/мин |
20 |
Скорость движения подвижной траверсы, мм/мин |
200 |
Длина перемещения рабочего стола, мм |
50 |
Мощность электродвигателя подвижной траверсы, кВт |
1,1 |
Мощность электродвигателя привода насоса высокого давления, |
2,2 |
кВт |
|
Вес пресса, кг |
2200 |
Габаритные размеры, мм: |
|
длина |
1920 |
ширина |
820 |
высота |
2180 |
Тип силоизмерителя – торсионный гидравлический.
2.1.2. Общее устройство пресса
Общий вид пресс П-125 представлен на рис. 16. Установка состоит из нагружающего устройства и пульта управления. Нагружающее устройство предназначено для механического деформирования или разрушения образцов. С пульта управления можно задавать и контролировать режимы деформации и разрушения.
39
elib.pstu.ru

Рис. 16. Общий вид гидравлического пресса П-125: 1 – нагружающее устройство; 2 – пульт управления; 3 – шкала силоизмерителя; 4 – стрелка, показывающая нагружающее усилие; 5 – контрольная стрелка для фиксирования нагружающего усилия; 6 – переключатель диапазонов нагрузки; 7 – подвижная траверса пресса; 8 – рабочий стол пресса; 9 – пресс-форма; 10 – кнопка перемещения верхней плиты пресса вверх; 11 – кнопка пуска гидростанции; 12 – штурвал регулирования скорости перемещения рабочего стола пресса; 13 – кнопка перемещения верхней плиты пресса вниз; 14 – кнопка выключения гидростанции
2.1.3. Нагружающее устройство
Нагружающее устройство, или собственно пресс, представляет собой раму (рис. 17), состоящую из основания 10, верхней траверсы 1 и двух резьбовых колонн 2.
На колоннах смонтирована подвижная траверса 3. Ее перемещение осуществляется с помощью электрического двигателя
40
elib.pstu.ru