
3068
.pdf
Важным технологическим преимуществом такого построения операции является обеспечение высокой точности относительного положения поверхностей, получаемых с одной установки при использовании различного режущего инструмента. Этообъясняетсятем, что при обработке нескольких поверхностей с одной установки погрешность установки заготовки не влияет на точность их относительного положения. Ге- ометрическая точность станка и точность позиционирования его рабочих органов по заданной программе обеспечивают высокуюточностьистабильностьавтоматического выполнения статической настройки.
Применение многоцелевых станков в автоматизированных участках в ряде случаев позволяет выполнить полную обработку заготовки с одной установкиприбазированииеенаспутнике по черным необрабатываемым поверхностям. Полная обработка заготовки может быть выполнена на одном, двух или трехмногоцелевыхстанках. Приэтомобработка осуществляется без перезакрепления заготовки на одном спутнике, который последовательно переходит от одного станка на другой. Построениетехнологиче-
ского процесса может осуществляться по гибкой структуре с использованием обходных технологий, позволяющих использовать взаимозаменяемые и взаимодополняемые станки, что существенно повышает производительностьзасчетуменьшениявлиянияпростояоборудования.
281
Важным вопросом при этом является выбор технологических баз, при котором обеспечивается требуемое положение обрабатываемых поверхностей относительно необрабатываемых и равномерность припуска на большинстве обрабатываемых поверхностей. Выполнение рабочих переходов на многоцелевых станках фрезерно-расточного типа происходит в такой последовательности: вначале производят предварительноеиокончательноефрезерованиеплоскихповерхностей, затем обрабатывают главные отверстия – сверлят, зенкеруют, растачивают, развертывают, – а в заключение сверлят мелкие отверстия, зенкером снимаются фаски и нарезают метчиками необходимую резьбу.
Если обработка детали с одной установки невозможна, то выполнение технологического процесса осуществляют по этапам. На первой операции обрабатывают поверхности, используемые в дальнейшем в качестве общих технологических баз. А затем после переустановки заготовки на спутнике на последующих операциях обрабатывают практическивсеоставшиесяповерхностейдеталисполученныхобщихбаз.
Таким образом, между первым и вторым этапом происходит организованная смена баз, то есть переустановка детали на обработанные поверхности. В качестве общих технологических баз могут быть приняты как основные базы детали, так и другие удобные для этого поверхности, геометрическиепараметрыкоторыхотвечаюттребованиямвыборабаздетали. Длясозданияудобныхтехнологическихбазнадеталииногдапредусматривают специальные технологические приливы, платики, которые обрабатывают на первой операции. Наиболее удобными технологическими базами для большинства операций являются: три плоскости, образующие координатный угол (базирование по трем плоскостям); плоскость и два отверстия, материализующие схему базирования по плоскости и двум базовым пальцам; плоскость и одно отверстие сравнительно большого диаметра, обеспечивающие схему базирования по плоскости, центрирующему бурту (двойная опорная база) и опорной базе. Эти схемы базирования получили наибольшее распространение. Таким образом, основной задачей первой операцииприизготовлениидеталейнамногоцелевыхстанкахявляетсяподготовка удобных технологических баз, обеспечивающих возможность осуществления всей последующей обработки поверхностей деталей с общих поверхностей. Решениеэтойзадачиобеспечиваетнаиболееполноеиспользованиепринципаединствабаз, врезультатечегодоминимумасокращается влияниепогрешностиустановкинаточностьобработки.
282

Подготовливаемыенапервойоперациитехнологическиебазыдолжны обеспечить возможность последующей обработки заготовки с пяти сторон (четырех горизонтальных направлений и вертикального). При этом необходимо получить доступность режущего инструмента ко всем обрабатываемым поверхностям. Одним из решений этой задачи является использование подкладных плит (адаптеров), на которые устанавливают заготовки при закреплении их на спутнике (рис. 12.15). Подкладная плита поднимает заготовку над рабочей поверхностью спутника, ее габаритныеразмерыменьшеразмеровустановочнойбазызаготовки, что
позволяет выполнять фрезерование заготовки на проход с четырех сторон, не задевая поверхность
спутника.
Для уменьшения влияния погрешности установки наиболее ответственные поверхности детали, между которыми проставлены жесткие по допускам размеры, следует обрабатыватьнаодномстанке с одной установки спутника. Это относится в первую очередь к обработке главных отверстий, где необходимо обеспечить требуемую точность межосевых расстояний, точность положения осей отвер-
стий и торцовых поверхностей, а также к обработке комплекта основных баз детали и получению поверхностей вспомогательных баз, требующих точного расположения относительно основных баз.
Влияние погрешности установки спутника на точность относительного положения поверхностей, полученных при обработке на двух станках, можно определить заранее путем расчета. Например, если главное отверстие обрабатывается на одном многоцелевом станке, а мелкие отверстия по торцу и сверлятся, и нарезается резьба на другом станке, то погрешность установки спутника у = (aу, bу, cу, у,у, у) будет влиять на смещение центра резьбовых отверстий относительно оси главного отверстия (см. рис. 12.15). Смещение по трем ко-
283
ординатам x, y, z можно определить по формуле приведенной погрешности установки
|
|
|
'x |
|
|
|
ɚɭ |
|
|
|
|
0 |
|
Jɭ |
Eɭ |
|
|
|
|
X |
|
|
|
||
|
|
|
|
|
|
|
|
|
|
||||||||||||||||
|
|
|
|
|
|
|
|
|
|
|
|
|
|
|
|||||||||||
|
|
|
'ɭ |
|
|
|
bɭ |
|
|
|
Ȗɭ |
|
0 |
O |
|
|
Y |
|
(12.1) |
||||||
|
|
|
|
|
|
|
|
|
|
|
|
|
|
|
|
|
|
|
|
|
|
, |
|
||
где X, Y, Z – |
|
'z |
|
|
|
ɫɭ |
|
|
|
|
ȕ |
ɭ |
Ȝɭ |
0 |
|
|
|
|
Z |
|
|
|
|||
|
координаты |
|
|
|
отверстия в системе координат спутника. |
|
|||||||||||||||||||
Координаты X, Y, Z зависят от положения ноля детали на спутнике |
|||||||||||||||||||||||||
Xд, Yд, ZдиотположенияотверстиявсистемекоординатдеталиXо, Yо, Zо: |
|||||||||||||||||||||||||
|
|
|
|
|
X = Xд |
+ Xо; Y = Yд, + Yо; Z = Zд |
+ Zо . |
|
в, |
в) |
|||||||||||||||
Принеобходимостиопределенияпредельныхотклонений( в, |
|||||||||||||||||||||||||
и ( нx, нy, |
|
|
|
|
|
|
|
|
|
|
|
|
|
|
|
|
|
|
|
|
|
|
x |
y |
z |
нz) в формулу (12.1) следует подставить соответствующие |
|||||||||||||||||||||||||
матрицыпредельныхсмещений(aв, bв, cв) и(aв, bв, cв) матрицыугловых |
|||||||||||||||||||||||||
|
|
|
|
|
|
|
|
|
|
|
|
|
y |
y |
y |
y y |
|
|
y |
|
|
|
|||
преобразований для верхних πв и нижних πн |
отклонений: |
|
|
|
|||||||||||||||||||||
|
|
|
|
|
Jɧy |
|
|
|
|
y |
|
|
|
y |
|
Jɧy |
Eɜy |
|
|
||||||
|
0 |
|
|
|
Eɜy |
|
|
|
|
0 |
|
|
|||||||||||||
Sɜɭ |
|
|
Jɜy |
0 |
|
|
Oɧy |
; Sɜɭ |
|
|
Jɜy |
0 |
Oɧy |
. |
|
||||||||||
|
Eɧy |
|
Oɜy |
0 |
|
|
|
Eɧy |
|
|
Oɜy |
0 |
|
|
Выбор последовательности обработки, выполняемой в соответствии с задачами изготовления детали и возможностями оборудования, преследует цель такого построения технологической операции, при котором суммарные затраты времени на выполнение основных и вспомогательных технологических переходов будут минимальными. Для этого на деталивыявляетсясовокупностьобрабатываемыхповерхностейиихгеометрическихэлементов. Всоответствиисэтимопределяютсоставрежущего инструмента, необходимогодлявыполненияпредварительнойичистовой обработок. Рассматриваются зоны расположения обрабатываемых геометрических элементов, определяют состав и повторяющуюся потребность применения соответствующего инструмента для выполнения обработки в каждой из зон. Выявляют позиции, занимаемые заготовкой и режущим инструментомпривыполненииобработкивкаждойиззон.
Используятакойподход, определяютсовокупностьэлементовдетали, находящихся в данной зоне и объединенных общим инструментом, что позволяет запрограммировать фрагмент операции, выполняемый по отдельнойподпрограммеодниминструментом. Наосновеэтогопредставляется возможным объединение нескольких подобных подпрограмм в комплекснуюпрограммупообработкезаготовкисоднойустановкисиспользованием различных режущих инструментов. Таким образом, операция,
284
формируемаянакаждомстанке, представляетсобойкомплексноесочетание необходимых фрезерных, сверлильных, расточных и других переходов, выполняемыхсиспользованиемстандартныхцикловиподпрограмм.
У многих корпусных деталей на одной стороне может быть расположено несколько одинаковых поверхностей, например отверстий одинакового диаметра, пазов одинаковой ширины или одинаковых по размерам плоскостей, требующих применения одного режущего инструмента. В этом случае, как правило, целесообразно одним инструментом последовательно обрабатывать все одинаковые поверхности, расположенные по одной стороне, а затем заменить режущий инструмент. Однако при больших размерах детали, когда время относительного перемещения с одной позиции на другую значительно больше, чемвремяназаменуинструмента, целесообразнозаменитьинструмент и выполнить все переходы по обработке одной поверхности, а затем перейти к обработке другого участка детали.
Таким образом, последовательность выполнения технологических переходовнеобходимоназначатьисходяиззадачидостижениятребуемой точности детали наиболее коротким путем с наименьшими затратами основного и вспомогательного времени на замену инструмента и выполнение холостых ходов.
При наличии на поверхностях заготовки неравномерного или завышенного припуска фрезерование необходимо выполнять за несколько проходовсприменениемфрезменьшегодиаметра. Всеэтоспособствует уменьшению вибраций, уменьшению сил резания и величины упругих перемещений, что благоприятно сказывается на точности обработки.
На станках с ЧПУ сверление отверстий выполняют по программируемым координатам без применения кондукторов с направляющими втулками. Поэтому для уменьшения увода сверла перед сверлением рекомендуется выполнять зацентровку, что позволяет обеспечить достижение более высокой точности положения оси отверстия. Для зацентровки можно использовать сверла диаметром 10...12 мм или специальныецентровочныесверладиаметром4…10 мм. Дляотверстийподрезьбу диаметром более 25...30 мм помимо сверления выполняют зенкерованиеилирастачивание. Торцыотверстиймалогодиаметраобрабатываютсосевойподачейцековкамиилиподрезнымирезцами. Переднарезаниемрезьбывотверстияхснимаютфаскуконическимизенковками, резцами или сверлами большого диаметра. Нарезание резьбы выполняют с принудительной осевой подачей, равной шагу резьбы. Обработку группы крепежных отверстий целесообразно выполнять с помощью малых
285
многошпиндельных сверлильных головок, которые, так же как и одиночный инструмент, помещают в инструментальный магазин станка.
Для обработки главных отверстий, полученных литьем, в качестве первого перехода рекомендуется расточка резцом вместо зенкерования. Это позволяет уменьшить отклонение оси отверстия вследствие неравномерного припуска на обработку.
На станках с ЧПУ, имеющих систему круговой интерполяции, обработку отверстий возможно осуществить методом планитарного фрезерованияс применением концевой фрезы. Такаяобработкапрограммируется стандартным циклом. После заглубления на требуемую величину вращающаяся фреза совершает планитарное перемещение по периметру отверстия, а затем выводится в исходное положение. Цикл обработки может предусматривать предварительное и чистовое фрезерования. В результате достигают 8 – 7-й квалитет точности отверстия и шероховатость поверхности по Ra = 1,25 ... 0,8 мкм. Основным преимуществомэтогометодаявляетсявозможностьвыполненияпредварительной, чистовой и отделочной обработок одним инструментом широкого диапазона больших отверстий, диаметром более 80 мм. При этом отпадает необходимость приобретения дорогостоящих зенкеров и разверток большого диаметра, изготавливаемых под один диаметральный размер.
Для гарантированного достижения требуемой точности положения нескольких отверстий и плоскостей относительно одной базы все эти поверхностиследуетобрабатыватьнаодномстанкезаоднуустановку. Аналогичноследуетстроитьпроцесспринеобходимостидостижениятребуемой соосности и параллельности осей отверстий, обрабатываемых с двух илинесколькихсторонприповоротедеталисоспутникомнастолестанка.
Ниже рассматривается пример разработки технологического процесса изготовления корпусной детали на многоцелевых станках автоматизированного участка. Технические требования на изготавливаемый корпус приведены на эскизе (рис. 12.16). Заготовкой для корпуса является отливка, материал – серый чугун СЧ21.
Анализконструкцииитехническихтребованийпоказывает, чтообработкубольшинстваповерхностейкорпусаследуетвыполнятьприбазировании по плоскости основания (плоскость А), являющейся основной конструкторской базой, относительно которой определено положение отверстий и других плоских поверхностей. Для этого на плоскости А необходимосделатьдвабазовыхотверстия, чтопозволитосуществитьбазирование корпуса по плоскости и двум базовым отверстиям. В соответствии с изложенным, определена общая последовательность обработки. На пер-
286

вой операции следует обработать плоскость А и два базовых отверстия Φ10 Н7, анавторой– остальныеповерхностидетали(см. рис. 12.16).
Рис. 12.16. Эскиз корпусной детали, изготавливаемой на многоцелевом станке
Таким образом, обработку корпуса можно выполнить на двух многоцелевых станках автоматизированного участка. Исходными для подробной разработки технологических операций, управляющих программ являются чертеж детали, чертеж заготовки, последовательность обработки поверхностей, представленная в виде маршрута, и технологические данные применяемых многоцелевых станков и необходимых наладок для каждого из станков с ЧПУ.
На первом многоцелевом станке с вертикальным расположением шпинделяможновыполнитьпервуюоперациюпообработкеоснованияи двухбазовыхотверстий. Анавтороммногоцелевомстанкесгоризонтальным расположением шпинделя и поворотным столом можно последовательно обрабатывать фрезерованием плоские поверхности со всех четырехсторон, азатемобработатьвсерасположенныенанихотверстия.
Заготовку обрабатывают на спутнике, который базируется на станках в координатный угол. Ориентация и закрепление спутника осуществляется с помощью автоматического приспособления, установленного на столе станка. Заготовку на спутнике закрепляет рабочий на участке установки и выверки, после чего заготовка со спутником автоматически транспортируется к требуемому станку.
Определив задачи, выполняемые на каждой операции, и выбрав технологическиебазы, разрабатываютсхемуустановкизаготовкинастанке.
На первой операции заготовку базируют по трем плоскостям, при этом выставку ее на спутнике осуществляют по разметке с применением координатно-измерительной машины (рис. 12.17). Установка заготовки с использованием упрощенной разметки позволяет обеспечить решение задач базирования на первой операции.
287
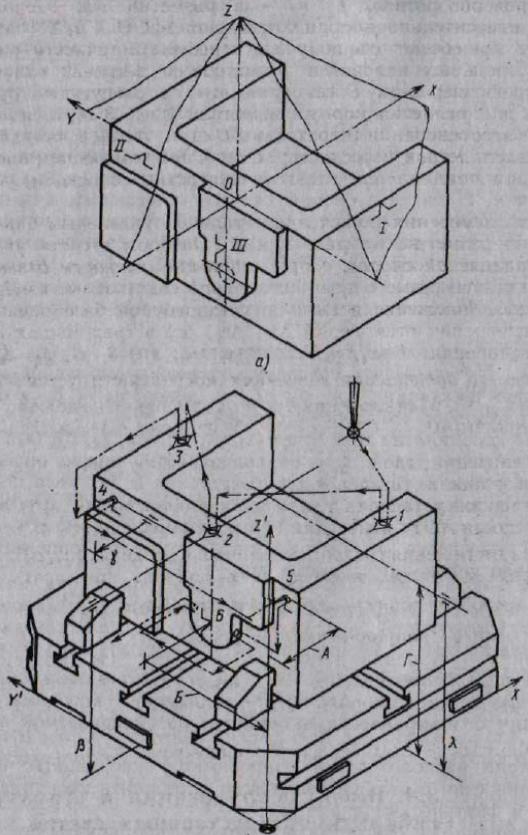
б)
Рис. 12.17. Установка заготовки на спутнике по разметке с применением координатно-измерительной машины: а – координатная система баз заготовки;
б – измерение положения заготовки при ее установке
288
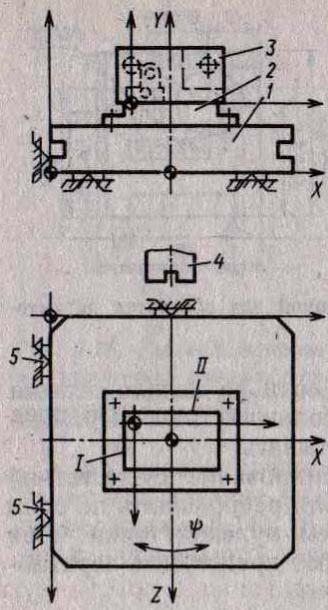
На второй операции заготовку базируют по плоскости и двум базовым отверстиям (рис. 12.18). При этом заготовку устанавливают на под-
кладную плиту (адаптер), ко- |
|
||
торая в свою очередь закре- |
|
||
пляется на спутнике. При на- |
|
||
личии поворотного стола та- |
|
||
кая схема базирования позво- |
|
||
ляет выполнить фрезерование |
|
||
плоских поверхностей с четы- |
|
||
рехстороннапроход, азатем– |
|
||
обработать все отверстия. На |
|
||
рис. 12.18 показаны также ко- |
|
||
ординатные системы приспо- |
|
||
собления, спутника и детали, |
|
||
между которыми |
установле- |
|
|
ны определенные размерные |
|
||
связи, позволяющие согласо- |
|
||
вать положение нолей отсче- |
|
||
та станка, приспособления, |
|
||
спутника и детали. |
|
|
|
Для каждой из обраба- |
|
||
тываемых сторон на основе |
|
||
чертежа разрабатывают гео- |
|
||
метрический план |
обработ- |
|
|
ки и определяют последова- |
|
||
тельность выполнения тех- |
|
||
нологических |
переходов. |
|
|
План обработки корпуса на |
Рис. 12.18. Установка заготовки на спут- |
||
второй операции |
|
представ- |
|
лен на рис. 12.19. |
Каждому |
нике для выполнения второй операции |
отверстиюнапланеобработкиприсваиваютопределенныйномер, который соответствует последовательности обработки отверстия. В соответствии с принятой схемой базирования на плане обработки указывается координатная система детали, начало отсчета которой называется «ноль детали». Относительно этой координатной системы производят пересчет размеров, определяющих положение обрабатываемых поверхностей заготовки. При составлении программы обра-
289

ботки необходимо задавать средние размеры детали. В случае несимметричного расположения допусков относительно номиналов средние размеры необходимо рассчитывать по формуле:
|
|
ǻɜ |
ǻɧ |
|
|
Acɪ |
Ⱥ |
|
|
, |
(12.2) |
2 |
|
||||
|
|
|
|
|
|
где А – номинальный размер; |
в, н – верхнее и нижнее предельные от- |
||||
клонения размера. |
|
|
|
|
|
а) б)
Рис. 12.19. План обработки заготовки на многоцелевом станке: а – со стороны главного вида; б – со стороны вида сбоку
Врезультате составляют таблицу координат положения отверстий длякаждогопланаобработки. Приобработкезаготовкинавторомстанке в качестве координатных плоскостей начала отсчета приняты плоскость А, выполняющая роль установочной базы (XOZ), и перпендикулярные к ней две плоскости симметрии XOY и YOZ (см. рис. 12.19). Такое положение начала отсчета означает наличие как положительных, так и отрицательных координат отверстий, что, однако, не вызывает затруднений при разработке программы для системы ЧПУ с плавающим нолем. Для фрезерования поверхности задают координаты положения центра фрезы, соответствующие началу и концу рабочих ходов. При этом учитывают величину врезания и перебега фрезы.
Всоответствии с намеченными переходами выбирают необходимый режущий инструмент и определяют режимы резания. В результате выполнения этого этапа составляют операционную карту механической обработки резанием, в которой отражается последовательность выполнениятехнологическихпереходовнакаждойсторонедетали, состав применяемого инструмента и технологической оснастки, режимы
290