
3068
.pdf6)шлифованиецилиндрическихповерхностейвала(круглошлифовальный станок);
7)отделка шлицев шлифованием (шлицешлифовальный станок). Оборудование в технологически замкнутых участках нередко свя-
зывают при помощи подъемно-транспортных устройств в виде подвесных балок с электротельферами, рольгангов, склизов, специальной тарыдляперевозкидеталейнебольшихразмеров. Этоспособствуетповышению производительности труда рабочих, сокращению цикла производства и повышению других технико-экономических показателей.
Во главе каждого из таких организационно оформленных участков стоит мастер, который в целом отвечает за сроки и качество изготовления определенной номенклатуры деталей. Относительно малая номенклатурадеталей, закрепленныхзакаждымизтехнологическиучастков, позволяет существенно упростить задачи организации и планирования производства.
В процессе изготовления изделие находится в пределах одного участка и проходит короткий путь, что сокращает расходы и потребностьприменениятранспортныхсредств. Уменьшаетсятакжевремяна перенастройку оборудования при переходе от обработки одного изделия к другому, близкому по конфигурации и технологическому процессу. Результатом этого являются более высокие технико-экономические показателипосравнениюспоказателями, получаемымипригрупповой расстановке оборудования.
Определенным недостатком организации технологически замкнутых участков является недогрузка станков, следствием чего является болеенизкийкоэффициентиспользованияоборудованияпосравнению с организацией участков с расположением оборудования по группам станков. Так, например, если на участке валов происходит изготовлениегладкихваловбезшлицевыхпазов, тошлицефрезерныйишлицешлифовальный станки простаивают.
Однако, несмотря на это, благодаря другим значительно более вы- сокимтехнико-экономическимпоказателям, даннаяформаорганизации производства и расстановки оборудования находит широкое применение не только на заводах, производящих ограниченную номенклатуру изделий, нотакжеинапредприятиях, изготовляющихбольшуюноменклатуру изделий при относительно небольших количествах.
Рассмотренные выше формы организации производственного про-
121
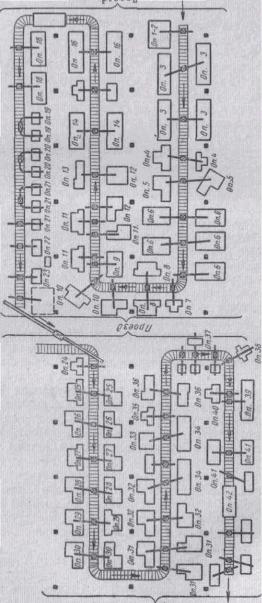
цесса относятся к непоточному виду, когда отсутствует непрерывность движения изготовляемых изделий и их равномерный выпуск с соблюдением постоянного такта.
С увеличением количества изготавливаемых изделий и уменьшением их номенклатуры осуществляют переход на следующую, еще более качественную ступень – поточную форму организации производственного процесса. С этой целью на основе технологически замкнутых участков создают поточные линии по изготовлению определенных изделий.
|
В поточных линиях оборудова- |
||
|
ние также расставляют в последова- |
||
|
тельности |
выполняемых |
технологи- |
|
ческих операций, что позволяет до |
||
|
минимума сократить длину пути, про- |
||
|
ходимого |
обрабатываемой деталью, |
|
|
и обеспечить возможность осущест- |
||
|
вления многостаночного обслужива- |
||
|
ния. Оборудование поточной линии |
||
|
связывают при помощи транспортных |
||
|
устройств, обеспечивающих переда- |
||
|
чу обрабатываемой заготовки с одной |
||
|
операции на другую. Технологиче- |
||
|
ский процесс разрабатывается таким |
||
|
образом, |
чтобы продолжительность |
|
|
каждой из операций поточной линии |
||
|
была по возможности равна или крат- |
||
|
на такту выпуска. Это позволяет наи- |
||
|
лучшим образом использовать произ- |
||
|
водственную площадь, наиболее пол- |
||
|
но использовать оборудование поточ- |
||
|
ной линии и создает предпосылки для |
||
|
последующей полной автоматизации |
||
|
технологического процесса. |
||
|
В качестве примера на рис. 10.1 |
||
Рис. 10.1. Расстановка оборудо- |
показана |
планировка |
расстановки |
вания поточной линии для изготов- |
оборудования поточной линии для из- |
||
ления коленчатого вала |
готовления коленчатого вала. Переме- |
122
щение заготовок от одного станка к другому осуществляется по рольгангу. Передача заготовок с рольганга на станки и обратно на рольганг, а также их установка в приспособления осуществляются при помощи подвесных электротельферов. Полная обработка коленчатого вала предусматривает выполнение 42 операций, обозначение которых приведено непосредственно на применяемом оборудовании (см. рис. 10.1).
На поточной линии каждая деталь, прошедшая какую-либо операцию, сразу передается рабочим на транспортер для доставки на следующий станок, минуя склад. Время на передачу детали в таких случаях включается в норму времени. В отдельных случаях, с целью компенсации колебаний времени, затрачиваемого рабочими на выполнение отдельных операций, на рабочих позициях или на транспортных устройствахпредусматриваютнебольшиемежоперационныезаделы. Наличие промежуточных заделов позволяет также уменьшить возможные простои оборудования, которые могут возникнуть из-за случайной остановки одного из станков. Промежуточные заделы обычно размещают после нескольких единиц оборудования, деля, таким образом, всю поточную линию на ряд отдельных участков, каждый из которых может работать определенное время автономно, независимо от других. Контрольные операции, также как и обычные технологические операции, включаютвпоточнуюлиниюпоходупроцессакакотдельныепозиции.
На поточных линиях, как правило, широко применяют многостаночноеобслуживание. Рабочиеобычнообслуживаютнесколькоединиц одинакового или различного оборудования, совмещая, таким образом, различные профессии. Так, например, как показано на рис. 10.1, один рабочий обслуживает несколько одинаковых станков на операции № 6 (Оп. 6 ) идваразныхстанканаоперациях№11 (Оп.11 ), №12 (Оп. 12 ).
В цехах поточного производства обычно размещают не одну, а несколько поточных линий, детали которых, как показано на рис. 10.1, непосредственно поступают на конвейер, где осуществляется сборка изделия. При этом отсутствует пересечение грузопотоков. Изготовление деталей на поточных линиях значительно упрощает организацию
ипланирование производства, упрощает распределение и учет работ
исокращает оформление документации. Ответственность за работу одной или нескольких поточных линий поручают мастеру, который следит также за качеством и ритмичностью выпуска готовых деталей или сборочных единиц.
123

Объединение нескольких поточных линий позволяет создавать комплексные предметно-замкнутые участки, в которых осуществляется как изготовление комплектующих деталей, так и сборка готовых изделий.
Вкачестве примеров комплексных участков могут быть участки по изготовлению на станкостроительных заводах узлов гидроаппаратуры – гидропанелей, гидрозолотников, – а также участки по изготовлению сборного режущего инструмента.
Вкрупносерийном и массовом производстве для изготовления в больших объемах одного изделия создают автоматические линии, в которых станки, располагаемые по ходу технологического процесса, связываютжесткойтранспортнойсистемой, обеспечивающейавтоматическую передачу заготовок от одного станка к другому. Работа станков и транспортной системы в автоматических линиях синхронизирована в соответствии с заданным тактом выпуска изделий.
10.3.Расчет количества необходимого станочного оборудования
икоэффициентов его загрузки
Номинальный фонд времени Фн для единицы оборудования рассчитывается по формуле
Фн = (Dрtсут – Dрс'tс) (1100– Kпр |
), |
(10.3) |
где Dp – число рабочих дней в планируемый период; tсут |
– число рабо- |
|
чих часов в сутки; Dpc' – число рабочих дней сокращенной продолжи- |
||
тельности; tc – число рабочих часов, на которые сокращены рабочие |
||
сутки; Кпр – процент планируемого времени простоя оборудования, что |
||
необходимо для профилактики и ремонта. |
|
Для универсального оборудования принимают Kпр = (3÷8) %, для |
|
специального оборудования Kпр = (10÷12) %. |
|
Действительный фонд работы оборудования Fc |
отличается от но- |
минального фонда на величину потерь фонда времени: |
|
Fc = Фн – Fn. |
(10.4) |
Такие потери могут быть технологическими и организационны-
ми. Принимаемый действительный годовой фонд работы оборудования Fc при 1-ой смене Fc = 2030 ч, потери (2 %). При двухсменной работе Fc = 4015 ч, потери (3 %). При трехсменной работе – Fc = 5960 ч, потери (4 %).
В зависимости от потребности работа производства может быть
124
организована в одну, две или три смены. При этом сборочные цеха могутработатьводнусмену, амеханообрабатывающиеподразделения– в две смены. В 2-3 смены обычно организуют работу уникального дорогостоящего оборудования или оборудования, которое по производительности лимитирует производственный процесс предприятия.
Расчет количества станков, необходимых для выполнения определенной операции, при годовом объеме выпуска деталей N осуществляется по формуле
Cр = |
F |
∙ N, |
(10.5) |
|
tшт.к |
|
|
где Tшт.к – штучно-калькуляционное время на данную операцию; Fc – действительный годовой фонд работы оборудования.
Расчетное число станков Cp округляется до ближайшего целого |
|||
числа и получают Cn – принятое число станков Cp |
Cn. |
||
Зная значения расчетного и принятого числа станков определяют |
|||
коэффициент загрузки станка (оборудования): |
|
||
C |
|
||
Kз.об = |
p |
. |
(10.6) |
Cn |
|||
Коэффициент загрузки оборудования Kз.об. в среднем не должен |
быть ниже 0,85, то есть желательно обеспечить Kз.об. > 0,85.
ПриKз.об. < 0,85 имеетместонедогрузкаоборудования, егопростои. Вэтомслучаенеобходимоискатьтехнико-организационныемероприя- тия увеличения коэффициента загрузки оборудования. Такими мероприятиями являются:
1)поиск взаимодополняемого и взаимозаменяемого оборудования;
2)корректировки программы выпуска изделий.
Так как в процессе изготовления детали заготовка обычно проходит несколько различных станков, расположенных на участке, то следует рассчитывать средний коэффициент загрузки оборудования Kз.об.ср. по участку, для чего используют формулу
|
i¦n |
ɋpi |
(10.7) |
Kɡ.ɨɛ.ɫɪ. |
i 1 |
|
|
i¦n ɋni |
|
i 1
где n – количество станков, расположенных на участке;
Cpi, Cni – соответственно расчетное и принятое число станков. Количество станков, обслуживаемое одним рабочим, рассчитыва-
ют по формуле (9.40).
125

Зная Tшт.к, затраченное на выполнение операции при обработке детали на соответствующем станке, определяют суммарную станкоемкость
механообработки детали To∑ [ст-ч] , для чего используют формулу
i¦n tɲɬ.ɤ N
To6 |
|
i |
1 |
|
, |
(10.8) |
|
|
60 |
|
|||
где Tшт.к – время обработки на соответствующем станке; |
|
|||||
n – количество станков, проходимых заготовкой; |
|
|||||
N – годовой объем выпуска деталей. |
|
|
|
|||
Расчет количества рабочих |
|
|
|
|
|
|
Количество производственных рабочих Pp определяют по формуле |
||||||
Pp = |
|
|
Fp |
, |
|
(10.9) |
|
Tшт.к ∙ N |
|
|
|
||
|
|
|
|
|
|
|
где Fp – действительный фонд времени работы одного рабочего. Действительныйфондвремениработыодногорабочегосоставляетв
год Fp = 1820 при 4- часовой неделе, продолжительности смены 8,2 ч. и продолжительности отпуска 24 дня.
Расчетное число рабочих округляют до целого числа и получают принятое число рабочих Pn. Коэффициент загрузки рабочих Kp определяют по формуле
P
Kp = Ppn. (10.10)
Повышение коэффициента загрузки рабочих достигают путем введения многостаночного обслуживания, для чего необходимо рабочих обучить смежным профессиям.
Трудоемкость изготовления изделия для серийного и мелкосерийного производств определяют по формуле
i n j m |
|
Tɢ ¦ ¦tɲɬ.ɤ, |
(10.11) |
i 1 j 1 |
|
где n – количество изготавливаемых деталей в изделии; |
|
m – количество выполняемых операций при изготовлении детали. Трудоемкость изготовления детали обычно превышает ее станкоемкость, так как помимо времени ее изготовления на станке вручную
выполняют зачистку заусенцев, клеймение и др.
В условиях многономенклатурного производства расчеты выпол-
няют с использованием приведенной программы выпуска Nпр: |
|
Nпр = Кпр N, |
(10.12) |
где Кпр – общий коэффициент приведения, определяемый как произведение коэффициентов приведения по массе Км, по серийности Ксер, по сложности Ксл., то есть Кпр = Км Ксер Ксл.
126
Число вспомогательных рабочих обычно принимается в пределах 25 % от основных рабочих, при этом 60 % вспомогательных рабочих предназначается для обслуживания оборудования, а 40 % – для обслуживания цеха. Вспомогательные рабочие в цехе выполняют уборку стружки, уборку помещений, работают электриками, сторожами. Число руководителей производства составляет обычно не более 5 % от общего числа основных и вспомогательных рабочих. Число специалистов – 10 % от общего числа основных и вспомогательных рабочих, а число служащих – 2 % от общего числа основных и вспомогательных рабочих.
10.4. Типизация технологических процессов. Групповая обработка заготовок
Одним из эффективных средств дальнейшего увеличения производительности труда и внедрения в производство наиболее производительных и экономичных технологических процессов, обеспечивающих требуемое качество выпускаемых изделий, является типизация технологических процессов.
Под типизацией технологических процессов понимается разработка технологических процессов на изготовление типовых деталей и сборку машин, в которых наиболее полно используются достижения наукиитехникиипередовойопытмашиностроительныхпредприятий.
Работу по типизации технологических процессов выполняют в два этапа:
•на первом этапе осуществляют классификацию изготавливаемых деталей машин и выявляют типовую деталь в каждом из классов;
•на втором этапе разрабатывают типовые технологические процессы на изготовление типовых деталей соответствующих классов.
Таким образом, первый этап типизации – классификация, основной задачей которой является приведение всего многообразия деталей, их поверхностей и сочетаний к минимальному количеству типов, для которых можно разработать типовые технологические процессы обработки.
Основнымипризнакамидляклассификациидеталейявляются: общность их служебного назначения, близкая по геометрии конфигурация, близкие габаритные размеры деталей; одинаковый уровень параметров точности, включая требования к шероховатости поверхностей, а также близкие параметры материала, что определяет в целом общность процесса обработки. Помимо этого, учитывают также объём выпуска, раз-
127
мер партии обрабатываемых заготовок, условия производства и систему организации, применяемое оборудование, инструмент и др.
Построение технологической классификации деталей осуществляют путем разделения их на классы, к которым относят: валы, зубчатые колёса, корпуса, втулки, диски, рычаги, плиты, ходовые винты и червяки и др. Каждый класс деталей, в свою очередь, делят на подклассы, а затем на группы и подгруппы, в которых учитывают характерные конструктивные признаки деталей. Разбивка классов на подклассы, группы и подгруппы заканчивается типом (типовой деталью).
Вгруппе деталей, подобранных на основе изложенных выше положений, выбирают типовую деталь, которая охватывает конструктивные особенности и требования всех деталей группы. Если такую деталь среди группы подобрать трудно, тогда создается «комплексная» деталь, то есть искусственная деталь, охватывающая все особенности деталей группы. Типовую (комплексную) деталь удобно получить путем вычерчивания в одном масштабе всех деталей группы при наложении их контуров.
На типовую или «комплексную» деталь разрабатывают типовой технологический процесс и необходимую для обработки всех деталей группы технологическую оснастку. Таким образом, типовая деталь представляет совокупность деталей одного класса, имеющих в определенных производственных условиях одинаковый маршрут, составленный из типовых технологических операций. Типовая технологическая операция характеризуется единством содержания и определенной последовательностью технологических переходов, выполняемых при изготовлении группы изделий с общими конструктивными и технологическими признаками.
Выполнение классификации деталей обычно сочетают с унификациейистандартизациейихконструкцийилиотдельныхэлементов. Это позволяет увеличить количество деталей в партии и применить при их изготовлении более прогрессивную технологию, сократив номенклатуру используемого режущего инструмента и другой технологической оснастки.
Типовые технологические процессы разрабатывают на основе анализа и обобщения опыта передовых предприятий с учетом объема выпуска изделий.
Вних предусматривают использование высокопроизводительного
128
оборудования, типовых схем базирования и типовой технологической оснастки, средств механизации и автоматизации, использование прогрессивных методов получения и обработки заготовок.
На машиностроительном предприятии разработку типовых технологий рекомендуется выполнять в двух вариантах. Рабочий вариант разрабатывают с учетом условий завода и имеющегося оборудования. Перспективный вариант разрабатывают с учетом возможности использования всех достижений, включая современные методы обработки, применение новейшего оборудования и прогрессивных методов организации производства.
Типовые технологические процессы оформляют в виде технологических карт. На основе разработанного типового технологического процесса составляют рабочие технологические процессы для конкретных деталей данного класса. Это делают путем удаления из типового процесса отдельных операций, выполнения которых для изготовления данной детали не требуется. В результате работа инженера-технолога существенно упрощается, а качество технологического проектирования возрастает. При этом представляется возможным составлять качественные технологии на достаточно сложные детали технологам, не имеющим большого опыта работы на предприятии.
На рис. 10.2 в качестве примера приведен типовой технологический маршрут изготовления ступенчатых валов, включающий выполнение 19 операций, которые необходимы для изготовления типовой детали – вала-шестерни. Для изготовления других деталей данного класса требуется выполнение меньшего числа операций. Так, например, согласно конструкции гладкого полого вала, для его изготовления необходимо выполнить 10 операций, а для шлицевого вала-шестерни – 15 операций. Пример, приведенный на рис. 10.2, наглядно показывает, что типовая деталь объединяет совокупность деталей определенного класса, которые могут быть изготовлены по общему технологическому маршруту, составленномуизтиповыхопераций, выполняемыхнаоднотипном оборудовании с использованием однотипных приспособлений.
Если процесс разработан на унифицированные детали, то для них составляют одну технологическую карту с нормами времени. По мере приобретения нового оборудования, совершенствования методов обработки и технологий типовые технологические процессы периодически корректируют.
129
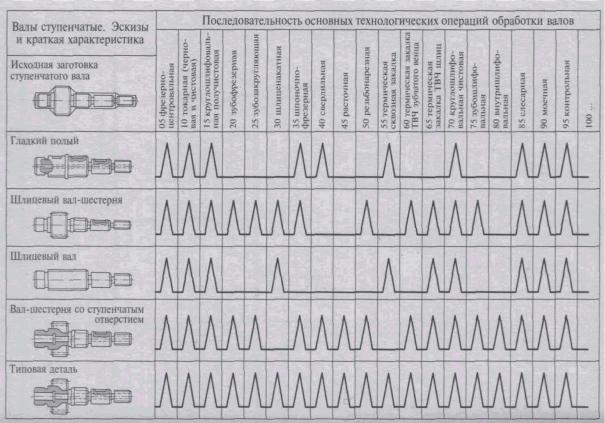
Типизация технологических процессов обеспечивает устранение многообразия возможных технологических решений при изготовлении
Рис. 10.2. Типовой технологический маршрут изготовления ступенчатых валов
деталей различного класса путем обоснованного сведения их к ограниченному числу наиболее эффективных вариантов, обеспечивающих короткий путь достижения требуемой точности деталей с наибольшей производительностью.
Классификация деталей по размерам конфигурации и общности процессовобработкипозволяетлюбуюдетальмашиныотноситьктому или иному классу, что позволяет получить технологический процесс ее изготовления, подобный процессу типовой детали данного класса.
Применение типовых технологических процессов не только способствует внедрению передового опыта в машиностроение, но также позволяет существенно уменьшить трудоемкость разработки рабочих технологий на новые изделия, обеспечив сокращение цикла подготовки производства, значительно упрощает работу инженерамтехнологам.
Типизация технологических процессов существенно сокращает технологическую подготовку производства и обеспечивает стабиль-
130