
3068
.pdfтщательная разработка технологических процессов и соответствующей технологической документации (операционных карт, чертежей и эскизов). Это позволяет рабочему и наладчику самим, без каких-либо дополнительных указаний, самостоятельно выполнять порученную операцию по механообработке или сборке изделия.
Последовательность разработки технологического процесса изготовления машины
Для достижения требуемого качества машины наиболее коротким путем с наименьшими производственными затратами разработку технологического процесса ее изготовления необходимо выполнять в следующей последовательности:
1)ознакомление со служебным назначением машины;
2)изучение и критический анализ технических требований и норм точности, определяющих служебное назначение машины;
3)ознакомление с намечаемым объемом выпуска машин в единицу временииобщимколичествоммашин, изготавливаемыхпонеизменяемым чертежам;
4)изучение конструкторской документации – рабочих чертежей машины – и их критический анализ на технологичность;
5)разработка технологического процесса общей сборки машины и
еесборочных единиц;
6)изучение служебного назначения деталей, критический анализ технических требований и анализ конструкции деталей на технологичность;
7)выборнаиболееэкономичныхспособовполучениязаготовокдля изготавливаемых деталей;
8)разработка наиболее экономичных вариантов технологических процессов изготовления деталей;
9)разработка планировки размещения оборудования и рабочих мест в производственных участках;
10)разработкатехническихзаданийнапроектированиеиизготовление требуемого оборудования, приспособлений и инструмента;
11)апробирование технологического процесса и внесение в него необходимых исправлений при выявлении ошибок.
Изучение служебного назначения машины, анализ технических требований и норм точности на ее изготовление
Важным начальным этапом разработки технологического процес-
241
са изготовления машины является изучение ее служебного назначения. Полная, точная формулировка служебного назначения машины, содержащая численные значения ее основных функциональных параметров, позволяет принимать правильные решения, начиная с первых ответственных этапов технологического проектирования. Ошибки, допущенные при определении служебного назначения, нередко приводят к неправильной технологии изготовления машины, что неизбежно отражается на ее качестве.
Каждая создаваемая машина предназначена для выполнения определенного процесса, при выполнении которого достигается определенный результат, например получаемые изделия. В соответствии с этим изучение служебного назначения машины следует начинать с ознакомления с результатами ее действия, которые должны оцениваться численными значениями соответствующих функциональных параметров.
Так, например, изучениеслужебногоназначенияметаллорежущего станка следует начинать с ознакомления с геометрическими формами
иразмерами изготавливаемых на нем деталей и предъявляемых к ним требованийточности. Послечегонеобходимопроанализироватьтребования производительности обработки, потребляемой мощности, вида управления, надежности и др.
Различные машины выполняет свое служебное назначение при помощи исполнительных поверхностей, между которыми в процессе работы возникают размерные, кинематические, динамические, электрические и другие связи. У станков исполнительными поверхностями являются поверхности, определяющие положение обрабатываемой заготовки и режущего инструмента. При этом достигаемая на станке точность обработки определяется в основном действием размерных
икинематических связей. Поэтому при установлении соответствия служебного назначения машины с техническими требованиями на ее изготовление и нормами точности необходимо в первую очередь рассматривать размерные и кинематические связи, возникающие между исполнительными поверхностями. Требуемая точность относительного положения и движения исполнительных поверхностей, которые задаются как технические требования и нормы геометрической точности станка, определяется из условия обеспечения точности изготавливаемых деталей в соответствии со служебным назначением станка.
Вобщем случае переход от служебного назначения машины к тех-
242
ническим требованиям и нормам точности на ее изготовление для каждоготипамашинытребуетиндивидуальногорассмотрения. Примертакого перехода для токарного станка приведен в параграфе 2.1.
Формулировка служебного назначения машины должна включать также описание условий, при которых машина будет работать, выполняя свое служебное назначение. Эти условия обычно вытекают из характера процесса, выполняемого машиной. Для производящих машин, таких как металлорежущие станки, эти условия включают предельные отклонения параметров применяемых заготовок, режимы работы, потребляемую мощность, состояние окружающей среды и др.
Конструкторскую документацию и рабочие чертежи машины изучают для ознакомления с ее устройством, функциями отдельных узлов и механизмов. В начале следует рассматривать чертежи общей сборки машины, а затем сборочные чертежи ее основных узлов. При этом выявляют исполнительные поверхности машины, размерные и кинематическиесвязи, существующиемеждуними. Вкомплектконструкторской документации, какправило, входятразличныесхемы– кинематическая, гидравлическая, электрическая и др., поясняющие принцип работы машины. Междутемкаксхемыконструкторскихразмерныхсвязеймашины, определяющих выполнение соответствующих технических требований, технолог обычно выявляет и рассчитывает самостоятельно.
12.2. Основыразработкитехнологическогопроцессасборкимашины
Разработку технологического процесса сборки машины следует выполнять вопределеннойпоследовательностипоследующимэтапам:
1)ознакомление со служебным назначения машины;
2)критическийанализтехническихтребованийнаееизготовление;
3)ознакомление с объемом выпуска и величиной серии;
4)ознакомление с рабочими чертежами и проведение размерного анализа;
5)составление схемы сборки;
6)написаниетехнологиисборки, определениетрудоемкостисборки;
7)выбор вида и организационной формы технологического процесса сборки, определение необходимого числа рабочих-сборщиков;
8)составление технических заданий на проектирование сборочного оборудования и технологической оснастки.
Рассмотрим основные этапы разработки технологического процес-
243
сасборкимашинынапримересборкишестеренногонасоса, схемаконструкции которого приведена на рис. 11.2.
Формулировка служебного назначения – шестеренный насос моде-
лиД37М-1400050 предназначендляподачисмазкиктрущимсяповерхностям деталей трактора под давлением 0,6 МПа (6 атм.) при производительности 30 л/мин, которая должна создаваться при частоте вращения входного вала n-1 = 350 оборотов в минуту.
Приведенная формулировка точно отражает назначение насоса, подтверждая его численными значениями основных функциональных параметров, наличие которых однозначно определяет изделие и позволяетпроверитьегокачествонастенде. Этосущественноупрощаетпроцедуру сдачи изделия заказчику.
Критический анализ технических требований необходимо выпол-
нять на предмет их соответствия и достаточности служебному назначению изделия. Технические требования должны непосредственно вытекать из служебного изделия, их выполнение обеспечивает формирование требуемого качества изделия. Однако необоснованно жесткие требования приводят к удорожанию изделия, а неопределенные требования, в которых отсутствуют значения допускаемых предельных отклонений, могут привести к снижению качества и вызывают сложности при сдаче изделия заказчику. При выявлении указанных несоответствий проводятся согласования с разработчиками конструкции, в результате чего в конструкторскую документацию вносится необходимая коррекция.
На рассматриваемый шестеренный насос конструктором были установлены следующие технические требования [30]:
1.Обеспечить радиальный зазор между шестернями и корпусом в пределах 0,07 – 0,15 мм.
2.Обеспечитьторцевойзазормеждушестернямиикорпусомвпре-
делах 0,02 – 0,1 мм.
3.Зазор между крышкой и торцем оси ведомой шестерни должен быть в пределах 0,3 – 0,5 мм.
4.В собранном насосе при прокручивании от руки зубчатые колеса должны вращаться плавно.
5.Насос в сборе должен быть чистым и работать бесшумно.
6.Зазор между торцем колеса на входе и корпусом должен быть в пределах 0,5 мм.
7.Насос в сборе подвергается обкатке на стенде в течение 3-5 мин.
244
Выполнение технических требований 1 и 2 непосредственно влияет на производительность насоса, которая является одним из основных функциональных параметров, определяемых его служебным назначением. При наличии больших зазоров возникают потери (утечки), которые приводят к потере производительности, а при малых зазорах увеличиваются силы трения и крутящий момент на входе, что в пределе может привести к заклиниванию. Величины потерь Qy [л/мин] при различных значениях радиальных и торцевых зазоров определяются путем теоретических расчетов и экспериментально на стендах:
Qy = Qyp + Qyт + Qyз,
где Qyp – потери, обусловленные наличием радиального зазора; Qyт – потери вследствие наличия торцевого зазора;
Qyz – потери вследствие неплотности контакта зубьев.
Для рассматриваемого насоса их численные значения составляют
Qy = 0,441+0,072+1,8 = 2,31 л/мин.
Это позволяет конструктору рассчитать фактическую производительностьнасосаQф сучетомпотерь, обусловленныхналичиемзазоров Qy и потерь на всасывании Qвc = 4,83 л/мин:
Qф = Qт n + Qу + Qвс ,
где Qт – теоретическая производительность насоса за один оборот колеса; n – частота вращения входного вала.
В числовом выражении это составит
Qф = 41,95 – 2,31 – 4,83 = 34,81 л/мин.
Следовательно, выполнение технических требований 1 и 2, связанных с обеспечением точности зазоров, позволит гарантированно обеспечитьтребуемуюпроизводительностьнасоса: 34,81 л/мин 30 л/мин.
Технические требования, приведенные в пп. 4 и 5, необходимо уточнить, так как они заданы без указания допускаемых предельных значений. Требование по п. 4 следует формулировать так: в собранном насосе приводной вал должен вращаться плавно при приложении крутящего момента не более 1,5 Н м. Требование по п. 5 следует формулировать следующим образом: уровень звукового давления при работе насоса под нагрузкой не должен превышать 35 дБ.
Зазор между торцем зубчатого колеса и корпусом (см. п. 6) следует ограничить нижним предельным отклонением 0,2 мм. Это означает, что зазор должен быть выдержан в пределах 0,2 – 0,5 мм.
Объем выпуска насоса и величина серии соответственно составля-
ют N = 100000 шт/год и Е = 300000 шт. Ознакомление с этими данными позволяет рассчитать количество лет непрерывного выпуска изде-
245
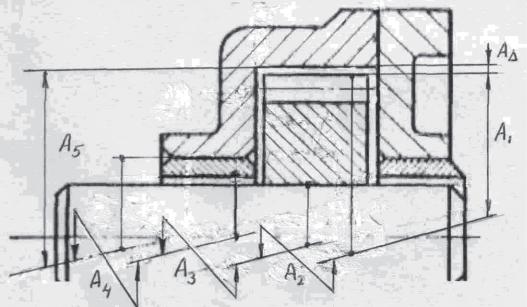
лий. Оно составляет три года k = 300000/100000 = 3 г. Опираясь на данные, приведенные в табл. 10.1, можно сделать вывод, что создаваемое производство является массовым и должно быть организовано по поточной форме. Для выполнения сборочных операций необходимо будет использовать наиболее производительное оборудование и технологическую оснастку, включая и специальную, затраты на приобретение которых будут компенсированы амортизационными отчислениями за три года его эксплуатации.
Ознакомление с рабочими чертежами и проведение размерного анализа проводят с целью выявления методов достижения точности, которые могут быть использованы при сборке машины и коррекции чертежей. Для этого техническое требование, связанное с необходимостью достижения заданной точности линейного или углового размера, формализуюткакзамыкающеезвеноконструкторскойразмернойцепи. Эту цепь выявляют, а затем рассчитывают в номиналах и в допусках с учетомвыбираемого методадостижения точности замыкающегозвена. Рассмотрим это на примере обеспечения требуемой точности радиального зазора А , размерная цепь для которого представлена на рис. 12.1:
А = А1 + А2 + А3 + А4 + А5.
Рис. 12.1. Размерная цепь, определяющая формирование радиального зазора в шестеренном насосе
Расчетразмернойцепивноминалахсучетомданных, приведенных в чертежах, показывает, что номинальные размеры звеньев (размеры деталей, образующих конструкторскую цепь) определены правильно:
А = 48 + 0 + 0 + 0 + 48 = 0.
246

Далее выполняем расчет в допусках. Для осуществления сборки насоса в условиях массового поточного производства выбираем метод полной взаимозаменяемости:
T = |
в – |
н = 0,15 – 0,17 = 0,08 мм; |
о = |
в + |
н |
0,15 + 0,17 |
|
|||||||||||||||||||
|
|
= |
|
|
|
|
|
= 0,11, |
||||||||||||||||||
2 |
|
2 |
|
|
|
|||||||||||||||||||||
а средний допуск на составляющие звенья составит |
|
|
|
|||||||||||||||||||||||
|
|
|
|
|
|
Tср = |
T |
0,08 |
|
|
|
|
|
|
|
|
|
|
|
|
||||||
|
|
|
|
|
|
|
|
= |
|
|
= 0,016 мм. |
|
|
|
|
|
|
|||||||||
|
|
|
|
|
|
m – 1 |
6 – 1 |
|
|
|
|
|
|
|||||||||||||
Между тем как согласно чертежам, на детали входящие в размер- |
||||||||||||||||||||||||||
ную цепь А , установлены следующие допуски: |
|
|
|
|
|
|
|
|
||||||||||||||||||
|
|
|
|
|
|
А1 |
|
|
|
А2 |
|
|
А3 |
|
|
А4 |
|
|
|
А5 |
|
|
|
|
||
|
|
|
|
в |
|
0,016 |
|
0,015 |
|
0,072 |
|
0,025 |
|
|
0,125 |
|
|
|
|
|||||||
|
|
|
|
н |
|
0 |
|
|
–0,015 |
|
0 |
|
|
–0,025 |
|
|
0,075 |
|
|
|
|
|||||
|
|
|
|
Тi′ |
|
0,016 |
|
0,03 |
|
|
0,072 |
|
0,05 |
|
|
0,05 |
|
|
|
|
||||||
При заданных в чертежах расширенных допусках согласно методу |
||||||||||||||||||||||||||
полной взаимозаменяемости на замыкающем звене получим: |
|
|
|
|||||||||||||||||||||||
|
i 5 |
|
|
|
|
|
|
|
|
|
|
|
|
|
|
|
|
|
|
|
|
|
|
|
|
|
Ɍ'c |
¦Ɍic |
0,016 |
0,03 0,072 0,05 0,05 |
|
0,218 ɦɦ ɜ ɦɟɫɬɨ T' |
|
|
0,08; |
||||||||||||||||||
ɜ |
i&ɜ1 |
&ɜ |
&ɜ |
&ɜ |
'ɧ |
0,015 0,072 0,025 0,125 0,016 |
0,253ɦɦ; |
|||||||||||||||||||
'' |
'2 '3 |
'4 |
'5 |
'1 |
||||||||||||||||||||||
'ɧ' |
'ɧ2 'ɧ3 'ɧ4 'ɧ5 'ɜ1 |
|
0,015 0 0,025 0,075 0 0,035ɦɦ. |
Этоозначает, чтоточностьразмеров, заданнаявчертежах, позволяетрешитьзадачуобеспечениярадиальногозазораА пометодучастичной взаимозаменяемости, при которой коэффициент риска составляет
t |
Ɍ' |
|
|
|
|
|
0,08 |
|
|
|
|
|
|
1,3 , |
|
i 5 |
1/ 9 0,016 |
2 |
0,03 |
2 |
0,072 |
2 |
0,05 |
2 |
0,05 |
2 |
|
||||
|
|
||||||||||||||
|
¦Ȝi2Ȧi2 |
|
|
|
|
|
|
||||||||
|
i 1 |
|
|
|
|
|
|
|
|
|
|
|
|
|
|
а процент изделий с недопустимым значением радиального зазора со- |
|||||||||||||||
ответственно составит: (при t =1,3) р % = 18,7 %. |
|
|
|
|
|
Для решения задачи по методу полной взаимозаменяемости требуется совместно с конструктором осуществить коррекцию допусков в сторону их ужесточения. Уменьшенные допуски и откорректированные значения предельных отклонений, позволяющие обеспечить требуемую точность радиального зазора А по методу полной взаимозаменяемости, приведены в таблице:
|
А1 |
А2 |
А3 |
А4 |
А5 |
в |
0 |
0,005 |
0,045 |
0,01 |
0,075 |
н |
–0,015 |
–0,005 |
0,02 |
–0,01 |
–0,065 |
Тi |
0,015 |
0,01 |
0,025 |
0,02 |
0,01 |
247

Таким образом, при откорректированных значениях допусков
получим: |
|
|
|
i 5 |
|
|
|
|
|
|
|
|
|
|
|
Ɍ' |
|
¦Ɍi |
0,015 |
0,01 0,025 0,02 0,01 0,08; |
|
||||
'ɜ |
& |
|
& |
|
i&1 |
|
& |
|
' |
|
0,005 0,045 0,01 0,075 0,015 |
0,15; |
'ɜ |
'ɜ |
'ɜ |
'ɜ |
'ɧ |
|
|||||||
' |
2 |
ɧ |
3 |
ɧ |
4 |
ɧ |
5 |
ɧ |
1 |
ɜ |
|
|
ɧ |
& |
& |
& |
& |
' |
0,005 0,02 0,01 0,065 0 |
0,07 . |
|||||
'' |
'2 |
'3 |
'4 |
'5 |
'1 |
|||||||
Проведение размерного анализа позволяет также в ряде случа- |
||||||||||||
|
|
|
|
|
|
|
|
|
|
|
ев выявить последовательность сбор- |
|
|
|
|
|
|
|
|
|
|
|
|
ки узлов машины. Так, например, при |
|
|
|
|
|
|
|
|
|
|
|
|
установке крышки 12 на корпус 1 (см. |
|
|
|
|
|
|
|
|
|
|
|
|
рис. 11.2) необходимо обеспечить со- |
|
|
|
|
|
|
|
|
|
|
|
|
вмещение осей отверстий двух вту- |
|
|
|
|
|
|
|
|
|
|
|
|
лочных подшипников 5. |
|
|
|
|
|
|
|
|
|
|
|
|
Согласно приведенным выше рас- |
|
|
|
|
|
|
|
|
|
|
|
|
четамсреднийзазорвподшипникесо- |
|
|
|
|
|
|
|
|
|
|
|
|
ставляет 0,03 мм, а наименьшая допу- |
|
|
|
|
|
|
|
|
|
|
|
|
стимая толщина масляного слоя при |
|
|
|
|
|
|
|
|
|
|
|
|
контакте вала должна составлять 0,01 |
|
|
|
|
|
|
|
|
|
|
|
|
мм. Следовательно, для компенсации |
|
|
|
|
|
|
|
|
|
|
|
|
отклонения от соосности и непарал- |
|
|
|
|
|
|
|
|
|
|
|
|
лельности двух осей остается 0,03 – |
|
|
|
|
|
|
|
|
|
|
|
|
0,01 = 0,02 мм. Схема линейной К и |
|
Рис. 12.2. Схема линейной К∆ |
|
угловой размерных цепей, опреде- |
||||||||||
и угловой μ∆ |
размерных цепей, |
|
ляющих совмещение осей двух вту- |
|||||||||
определяющих совмещение осей |
|
лочных подшипников приведена на |
||||||||||
двух втулочных подшипников |
|
|
рис. 12.2. |
|
||||||||
|
|
|
|
|
|
|
|
|
|
|
|
|
|
|
|
К = –К1 – К2 + К3 + К4 μ∆= –μ1 – μ2 + μ3 + μ4. |
|
Если оставшиеся 0,02 мм равными долями распределить на ком-
пенсацию смещения и поворота, то допуск на смещение осей составит ТК =0,01, а допуск на поворот Т = 0,01/45. В этом случае при решении задачи по методу полной взаимозаменяемости средние допуски на
составляющие звенья составят: |
0,01 |
|
|
||||||
– для линейной цепи К∆ Tср = |
|
= 0,002; |
|||||||
|
5 – 1 |
|
|||||||
– для угловой цепи μ |
|
T |
|
= |
0,01/45 |
|
= 0,002/45. |
||
∆ |
ср |
|
|||||||
|
|
|
|
5 – 1 |
|
Анализ полученных цифр показывает, что обеспечить такую высо-
248
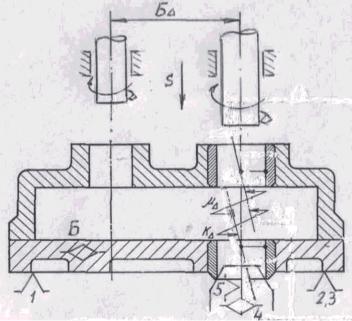
куюточностьнасоставляющихзвеньяхметодамивзаимозаменяемости практически не представляется возможным и экономически нецелесообразно. Нельзя решить эту задачу и методом регулировки. Если перемещение крышки в привалочной плоскости позволит совместить центры двух отверстий, то обеспечить требуемую точность углового положения осей отверстий не представляется возможным.
В соответствии с этим решение этой задачи возможно только при использовании метода пригонки. Сущность пригонки в данном случае заключается в выполнении совместной расточки отверстий в двух подшипниках, расположенных в крышке и корпусе. Однако для этого вначале необходимо выполнить определенные сборочные операции: запрессовать две втулки в корпус и крышку; установить крышку на корпус и закрепить ее крепежными деталями; просверлить и развернуть в крышке и корпусе два отверстия под две контрольные шпильки; установить две шпильки в отверстия, обеспечив неизменность положения крышки относительно корпуса; затем выполнить с одной установки тонкую расточку отверстий в корпусе и крышке. На крышку и корпус ставят клеймо одного номера, что означает возможность их использования только в таком сочетании.
Послерасточкикрышку снимают и выполняют общую сборку насоса согласно схеме, приведенной на рис. 11.3.
Расточку отверстий выполняют на специальном двухшпиндельном вертикально-расточном станке (рис. 12.3). Второй шпиндель осуществляет расточку в корпусе второго отверстия под ось 8, на ко-
торую устанавливают зубчатое колесо 7. Это позволяет получить также требуемуюточностьрасстояниямеждуосямидвухзацепляемыхколес.
249
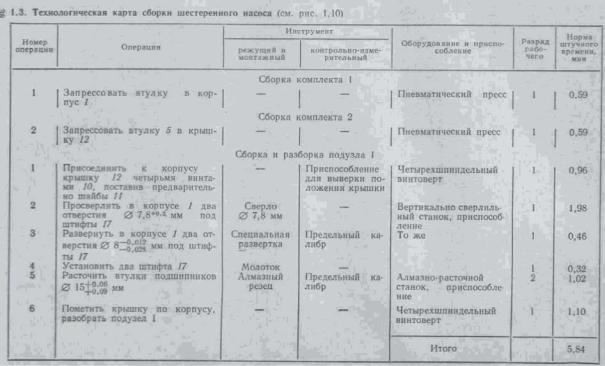
Базирование корпуса на станке осуществляют с использованием двойной опорной базы. Роль двойной опорной базы выполняет необработанноеотверстиевкрышке. Вотверстиевводятподпружиненныйконус, который обеспечивает центрирование – точное расположение отверстия относительно оси шпинделя. Это позволяет обеспечить равномерность припуска в растачиваемых отверстиях. После установки и закрепления корпуса подпружиненный конус автоматически отводится вниз, освобождая отверстие для прохода расточной оправки.
Составление схемы сборки насоса (см. рис. 11.3) выполняют в соответствии с методикой, изложенной в параграфе 11.1. В данном случае схема сборки составлена с учетом необходимости выполнения совместной расточки отверстий в корпусе и крышке и последующей разборки– снятиякрышкидляустановкивкорпусвала4, оси8 идвухзубчатых колес 6 и 7.
Технология сборки для массового производства требует подробной проработки. Ее записывают в технологическую карту (табл. 12.1), а затем нормируют и определяют общую трудоемкость сборки, которая для рассматриваемого насоса составляет То = 13,34 мин.
Таблица 12.1 Технологическая карта сборки шестеренного насоса
250