
Дерябин Нормирование точности узлов и деталеы в машиностроении 2015
.pdfМинистерство образования и науки Российской Федерации
НАЦИОНАЛЬНЫЙ ИССЛЕДОВАТЕЛЬСКИЙ ЯДЕРНЫЙ УНИВЕРСИТЕТ «МИФИ»
Трехгорный технологический институт
И.П. Дерябин, И.Н. Миронова
НОРМИРОВАНИЕ ТОЧНОСТИ УЗЛОВ И ДЕТАЛЕЙ
В МАШИНОСТРОЕНИИ
Учебно-методическое пособие к курсовому проектированию
Рекомендовано к изданию УМО "Ядерные физика и технологии"
Москва 2015
УДК 621.753(07) Д369
Дерябин И.П., Миронова И.Н. Нормирование точности узлов и дета-
лей в машиностроении: Учебно-методическое пособие к курсовому проектированию. – М: НИЯУ МИФИ, 2015. – 120 с.
Учебно-методическое пособие к курсовому проектированию составлено в соответствии с Государственным образовательным стандартом по дисциплинам «Метрология, стандартизация и сертификация», «Основы взаимозаменяемости».
В пособии дан теоретический материал для изучения задач нормирования точности с подробным указанием методик расчета и выбора посадок, расчета калибров, размерных цепей. Приведена методика назначения требований к точности геометрических параметров детали с учетом требований стандартов по основным нормам взаимозаменяемости.
Пособие предназначено для бакалавров по направлению 15.03.05 «Конструкторско-технологическое обеспечение машиностроительных производств», 12.03.01 «Приборостроение» и специалистов по направлению 15.05.01 «Проектирование технологических машин и комплексов».
Пособие подготовлено в рамках Программы создания и развития НИЯУ МИФИ.
Рецензент канд. техн. наук, доц. С.П. Максимов.
ISBN 978-5-7262-2170-0 |
© Национальный исследовательский |
|
ядерный университет «МИФИ», 2015 |
Редактор Е.Н. Кочубей
Подписано в печать 20.11.2015. Формат 60×84 1/16 Печ. л. 7.5. Уч.-изд. л. 7.5. Тираж 60 экз.
Изд. № 1/34. Заказ № 20.
Национальный исследовательский ядерный университет «МИФИ». 115409, Москва, Каширское шоссе, 31.
ООО «Баркас». 115230, Москва, Каширское ш., 4.
СОДЕРЖАНИЕ |
|
1. Общие положения и содержание курсовой работы |
............................... 4 |
2. Примеры расчетов деталей и их оформления |
|
в курсовом проекте .................................................................................. |
6 |
2.1. Назначение и выбор посадок ......................................................... |
6 |
2.2. Посадки с натягом ............................................................................ |
7 |
2.3. Посадки подшипников качения .................................................... |
12 |
2.4. Гладкие калибры ............................................................................ |
14 |
2.5. Резьбовые калибры ........................................................................ |
17 |
2.6. Размерные цепи .............................................................................. |
22 |
3. Требования к оформлению курсового проекта .................................... |
27 |
3.1. Оформление пояснительной записки ........................................... |
27 |
3.2. Особенности оформления чертежей ............................................ |
28 |
3.3. Оформление схем контроля .......................................................... |
35 |
Приложение 1 ............................................................................................. |
36 |
Приложение 2 ............................................................................................. |
38 |
Приложение 3 ............................................................................................. |
39 |
Приложение 4 ............................................................................................. |
40 |
Приложение 5 ............................................................................................. |
46 |
Приложение 6 ............................................................................................. |
47 |
Приложение 7 ............................................................................................. |
48 |
Приложение 8 ............................................................................................. |
49 |
Список рекомендуемой литературы ....................................................... |
120 |
3
1.ОБЩИЕ ПОЛОЖЕНИЯ
ИСОДЕРЖАНИЕ КУРСОВОЙ РАБОТЫ
Всовременных условиях развития машиностроительного про- изводства повышение качества работы конструкторов и технологов связано с компьютеризацией производства. Поэтому выпускники технического университета должны быть подготовлены к исполь- зованию персональных компьютеров в практической деятельности на производстве. Разработанная авторами автоматизированная си- стема расчётов по курсу «Метрология, стандартизация и сертифи- кация» прививает студентам навыки работы на компьютерах. Эту автоматизированную систему расчётов можно использовать как при выполнении курсовых и дипломных проектов, так и в условиях действующего машиностроительного производства.
При выполнении курсовой работы по дисциплине «Метрология, стандартизация и сертификация» студенты должны научиться пользоваться справочниками и стандартами, обосновывать назна- чение параметров точности, выбирать оптимальные посадки, рас- считывать предельные калибры для контроля деталей, проводить размерный анализ конструкций, подготавливать конструкторскую документацию.
Материалы пособия направлены на формирование у студентов следующих компетенций:
– способности участвовать в разработке проектов изделий ма- шиностроения с учетом технологических, конструкторских, экс- плуатационных, эстетических, экономических и управленческих параметров (ПК-8);
– способности разрабатывать (на основе действующих стандар- тов) техническую документацию (в электронном виде) для регла- ментного эксплуатационного обслуживания средств и систем ма- шиностроительных производств (ПК-13);
– способности разрабатывать проектную и рабочую техниче- скую документацию машиностроительных производств, оформлять законченные проектно-конструкторские работы разрабатываемых проектов и технической документации действующим стандартам, техническим условиям и другим нормативным документам (ПК- 15);
4
–способности участвовать в организации эффективного кон- троля качества материалов, технологических процессов, готовой машиностроительной продукции (ПК-24);
–способности выполнять работу по определению соответствия выпускаемой продукции требованиям регламентирующей доку- ментации (ПК-32);
–способности разрабатывать документацию (графики работ, инструкции, сметы, планы, заявки на материалы, средства и систе- мы технологического оснащения производства) отчетности по установленным формам, а также документацию, регламентирую- щую качество выпускаемой продукции (ПК-43);
–способности выбирать методы и средства измерения эксплуа- тационных характеристик изделий машиностроительных произ- водств, анализировать их характеристику (ПК-52).
Для выполнения курсового проекта каждому студенту выдаётся чертёж узла с указанием исходных данных и курсовое задание, ко- торое включает выполнение следующих пунктов:
1) назначение посадок для всех сопрягаемых размеров и обозна- чение их на выданном чертеже узла;
2) расчёт и выбор посадок для гладких цилиндрических соеди- нений: а) с натягом или зазором, б) переходной;
3) расчёт и выбор посадок подшипников качения;
4) расчёт исполнительных размеров гладких калибров;
5) расчёт исполнительных размеров резьбовых или шлицевых калибров;
6) расчёт сборочной размерной цепи.
Большая часть расчётов может быть выполнена на персональ- ном компьютере с использованием «Автоматизированной системы расчётов по курсу “Метрология, стандартизация и сертификация”».
Графическая часть курсовой работы включает:
1) построение схем полей допусков посадок с натягом, с зазором или переходной посадки;
2) построение схем полей допусков посадки подшипника каче- ния;
3) построение схем полей допусков гладких калибров;
4) построение схем полей допусков резьбового или шлицевого соединения и соответственно рабочих калибров для контроля резь- бовой или шлицевой детали;
5
5)рабочий чертёж калибра (гладкого, резьбового или шлицево-
го);
6)рабочий чертёж зубчатого колеса;
7)рабочий чертёж заданной детали;
8)схему контроля технических требований.
2.ПРИМЕРЫ РАСЧЕТОВ ДЕТАЛЕЙ
ИИХ ОФОРМЛЕНИЯ В КУРСОВОМ ПРОЕКТЕ
2.1. Назначение и выбор посадок
Единая система допусков и посадок (ЕСДП) гладких элементов деталей и их соединений для размеров до 3150 мм изложена в ГОСТ 25346-89 и ГОСТ 25347-82.
Значения основных (ближайших к нулевой линии) отклонений валов и отверстий для размеров до 500 мм приведены в прил. 1 и 2. Второе, неосновное, отклонение вычисляют по формулам:
ei =es – IT; |
EI = ES – IT; |
es = ei + IT; |
ES = EI + I |
где IT – допуск отверстия или вала, принимается согласно прил. 3. При выборе квалитетов необходимо пользоваться рекомендаци-
ями, приведёнными в справочной и учебной литературе [1–4]. Сочетание любых основных отклонений с любым квалитетом
даёт свыше 1000 полей допусков для валов и отверстий. Однако ГОСТ 25347-82 выделяет поля допусков предпочтительного при- менения; ими являются 16 полей допусков валов (g6, h6, js6, k6, n6, p6, r6, s6, js7, h7, e8, h8, d9, h9, d11 и k11) и 10 полей допусков от- верстий (H7, JS7, K7, P7, N7, F8, H8, E9, H9 и H11).
Посадки, как правило, должны назначаться в системе отверстия или системе вала. Применение системы отверстия предпочтитель- нее. Систему вала следует применять только в тех случаях, когда это оправдано конструктивными или экономическими условиями, например, если необходимо получить разные посадки нескольких деталей с отверстиями на одном гладком валу.
При номинальных размерах от 1 до 500 мм рекомендуется назначать предпочтительные посадки:
– в системе отверстия: Н7/е8, Н7/f7, H7/g6, H8/e8, H8/h7, H8/h8, H8/d9, H9/d9, H11/d11, H11/h11 (посадки с зазором); H7/p6, H7/r6,
6
H7/s6 (посадки с натягом); H7/js6, H7/k6, H7/n6 (переходные по- садки);
– в системе вала: F8/h6, H7/h6, H8/h7, E9/h8, H8/h8, H11/h11 (по-
садки с зазором); P7/h6 (с натягом); Js7/h6, K7/h6, N7/h6 (переход- ные посадки).
Кроме указанных, допускается применение других посадок, об- разованных полями допусков валов и отверстий по ГОСТ 25347-82. При этом необходимо, чтобы посадка относилась к системе отвер- стия или системе вала и чтобы при неодинаковых допусках отвер- стия и вала больший допуск был у отверстия, и допуски отверстия
и вала отличались не более, чем на два квалитета.
Назначение посадок на чертеже. В общем случае выбор поса-
док производится расчётным методом, методом прецедентов (ана- логов) или методом подобия [2].
В курсовом проектировании на выданном студенту чертеже узла для всех сопряжений необходимо проставить посадки:
–полученные расчётом;
–назначенные исходя из условий работы деталей в узле (мето- дом прецедентов или методом подобия).
Номинальные размеры сопряжений указаны в таблице на сбо- рочном чертеже узла в строке с указанным № вариантом.
Расчётные посадки (посадки с натягом, посадки подшипников качения и другие) назначаются после соответствующих расчётов согласно выданному заданию.
При назначении остальных посадок на сборочном чертеже узла задания, кроме работы с программой «Назначение посадок», следу- ет ознакомиться с примерами применения посадок с зазором [2,
т. 1, с. 297–318], с натягом [2, т. 1, с. 340–346] и переходных [2, т. 1,
с. 322–333]. Правила обозначения посадок на чертежах рассмотре- ны в учебнике [3, с. 210–212], а также в справочниках [1, 2].
2.2. Посадки с натягом
Посадки с натягом предназначены для неподвижных неразъём- ных соединений без дополнительного крепления деталей. Расчёт таких посадок выполняется с целью обеспечения неподвижности соединяемых деталей (прочности соединения) и прочности соеди- няемых деталей.
7
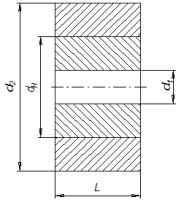
Порядок расчёта посадок с натягом подробно изложен в спра- вочнике [2, т. 1] и учебных пособиях [3–5]. При расчёте посадок с натягом определяются минимальный [Nmin] и максимальный [Nmax] расчётные допустимые натяги. Минимальный натяг рассчитывает- ся из условия обеспечения прочности соединения, а максимальный натяг – из условия обеспечения прочности сопрягаемых деталей.
Расчётная схема посадки с натягом приведена на рис. 2.1. На этой схеме указаны основные расчётные харак- теристики: dн – номинальный диаметр соединения, мм; d1 – размер отвер- стия полого вала (для сплошного вала d1 = 0), мм; d2 – наружный диаметр втулки, мм; L – длина сопряжения, мм.
Необходимые для расчётов значе- ния: коэффициента трения f, модуля упругости Е, коэффициента Пуассона µ, предела текучести σт, шероховато- сти поверхности Rа и коэффициента линейного расширения для различ-
ных материалов приведены в табл. 2.1–2.5.
|
|
|
|
|
|
|
Таблица 2.1 |
|
||
|
Значение коэффициента трения f |
|
|
|
|
|||||
|
|
|
|
|
|
|
|
|
|
|
|
Способ соединения деталей |
Сталь – |
Сталь – |
|
Сталь – |
|
Сталь – |
|
||
|
сталь |
чугун |
|
бронза |
|
латунь |
|
|||
|
|
|
|
|
|
|||||
|
Механическая запрессовка |
0,15 |
0,17 |
|
|
0,07 |
|
0,1 |
|
|
|
При нагревании или охла- |
0,20 |
0,15 |
|
|
0,20 |
|
0,17 |
|
|
|
ждении сопрягаемых деталей |
|
|
|
|
|||||
|
|
|
|
|
|
|
|
|
||
|
|
|
|
|
|
|
Таблица 2.2 |
|
||
|
Значение модуля упругости Е и коэффициента Пуассона |
|
||||||||
|
|
для различных материалов |
|
|
|
|
||||
|
|
|
|
|
|
|
|
|
|
|
|
Материал |
|
Е, Н/м2 |
|
|
|
|
|
|
|
|
Сталь |
|
2,1 1011 |
|
|
|
0,3 |
|
|
|
|
Чугун |
|
1 1011 |
|
|
|
0,25 |
|
|
|
|
Бронза |
|
0,9 1011 |
|
|
|
0,33 |
|
|
8
|
|
|
Таблица 2.3 |
Значение предела текучести σТ для различных материалов |
|||
|
|
|
|
Материал |
σт, Н/м2 |
Материал |
σт, Н/м2 |
Сталь 20 |
26 107 |
Бр.АЖН-11-6-6 |
39 107 |
Сталь 35 |
31 107 |
СЧ 12 |
12 107 |
Сталь 40 |
33 107 |
СЧ 18 |
18 107 |
Сталь 45 |
36 107 |
СЧ 28 |
27 107 |
Бр.АЖ 9-4 |
20 107 |
ЛМц ОС58-2-2-2 |
34 107 |
Бр.ОФ 10-1 |
20 107 |
|
|
Таблица 2.4
Шероховатость поверхности Ra (мкм) вала и отверстия для посадок с натягом (в числителе для вала, в знаменателе для отверстия)
Поверхности деталей в |
|
Ква- |
|
|
Номинальные размеры, мм |
||||||
посадках с натягом |
|
литет |
|
до 50 |
св. 50 до 120 |
св. 120 до 500 |
|||||
Собираемых под прессом |
|
6–7 |
|
0,4/0,8 |
0,8/1,6 |
|
1,6/1,6 |
||||
Собираемых способом |
|
– |
|
|
|
1,6/(1,6…3,2) |
|
||||
термических деформаций |
|
|
|
|
|
||||||
|
|
|
|
|
|
|
|
|
|
||
|
|
|
|
|
|
|
|
|
|
|
Таблица 2.5 |
Коэффициенты линейного расширения для металлов и сплавов |
|||||||||||
|
|
|
α10– 6, град– 1 |
|
|
|
|
|
|||
|
|
|
|
|
|
||||||
|
Температурный перепад при нагревании деталей, °С |
||||||||||
Металл |
20…100 |
|
20…200 |
|
20…300 |
|
20…400 |
20…500 |
|||
|
|
|
|
|
|
Значение α |
|
|
|
||
Сталь |
10,6 |
11,3…13 |
|
12,1…13,5 |
|
12,9…13,9 |
13,5…14,5 |
||||
углеродистая |
|
|
|||||||||
|
|
|
|
|
|
|
|
|
|
|
|
Сталь |
8,4…11 |
8,7…11,3 |
|
9,2…11,4 |
|
9,2…11,5 |
9,5…11,6 |
||||
хромистая |
|
|
|||||||||
|
|
|
|
|
|
|
|
|
|
|
|
Чугун |
8,7…11,1 |
8,5…11,6 |
|
10,1…12,2 |
|
11,5…12,7 |
12,9…13,2 |
||||
Бронза |
17,6 |
17,9 |
|
|
19,2 |
|
– |
– |
|||
алюминиевая |
|
|
|
||||||||
|
|
|
|
|
|
|
|
|
|
|
|
Бронза |
17,6 |
17,9 |
|
|
18,2 |
|
– |
– |
|||
оловянистая |
|
|
|
||||||||
|
|
|
|
|
|
|
|
|
|
|
9
Шероховатость сопрягаемых поверхностей можно определить по формуле зависимости шероховатости от допуска IT на размер. Для нормальной относительной геометрической точности (для до- пуска формы или расположения) используется примерно 60 % до- пуска размера:
Ra ≤ 0,5IT.
При выборе стандартной посадки с натягом исходными данны- ми являются номинальный диаметр сопряжения dн и расчётные значения допустимых натягов [Nmin р] и [Nmax р]. По полученным значениям расчётных натягов выбираются стандартные посадки с предпочтительными полями допусков таким образом, чтобы их предельные табличные натяги Nmin т и Nmax т не выходили за преде- лы расчётных натягов, а надёжность соединений была максималь- ной. Исходя из этого, для обеспечения работоспособности стан- дартной посадки необходимо выполнить условия неравенства [5]:
а) Nmax т ≤ [Nmax р], тогда [Nmax р] – Nmax т = |
сб; |
б) Nmin т ≥ [Nmin р], тогда Nmin т – [Nmin р] = |
э; |
в) сб > э, где сб – запас на сборку; |
э – запас на эксплуата- |
цию.
Условия а) и б) являются обязательными, условие в) в ряде слу- чаев может не соблюдаться.
Запас на эксплуатацию э учитывает возможность повторной запрессовки при ремонте, наличие динамических нагрузок при ра- боте и другие условия. Чем больше запас на эксплуатацию, тем выше надёжность и долговечность прессового соединения.
Запас на сборку сб учитывает перекосы при запрессовке и дру- гие неучтённые в формулах условия сборки. Чем больше сб, тем меньше усилие запрессовки, напряжения в материале деталей, при- водящие к их разрушению.
Стандартные посадки выбираются согласно приведённым усло- виям по таблицам ГОСТ 25347-82 из числа предпочтительных (см. также п. 2.1 данного учебного пособия), по литературе [2, т. 1, табл. 1.49] или по прил. 4.
При наборе стандартных посадок может возникнуть три случая. 1. Согласно условиям а) и б) подобрана только одна стандартная
посадка, тогда её следует проставить на чертеже сборочного узла.
10