
Дерябин Нормирование точности узлов и деталеы в машиностроении 2015
.pdf
2.Согласно условиям а) и б) подобрано несколько стандартных посадок. В этом случае необходимо выбрать одну наиболее грубого квалитета, а если таких несколько, то из них выбрать ту, у которой выполняется условие в).
3.Не удаётся подобрать оптимальную посадку из стандартных полей допусков. Тогда надо применить:
1) селективную сборку;
2) дополнительные крепления;
3) изменить конструктивные параметры соединения, техноло- гию сборки или физико-механические свойства материала.
Если студентом изменяются некоторые исходные данные, то их
корректировку следует согласовать с преподавателем.
Пример графического оформления. Схема расположения по-
лей допусков посадки с натягом оформляется на листе формата А4. На рис. 2.2 приведён пример графического оформления посадки с натягом в соответствии с результатами расчёта по программе «По- садки с натягом» автоматизированной системы.
Рис. 2.2. Графическое оформление посадки с натягом
11
Точность формы (отклонение от цилиндричности) указывается равным 0,25Td (TD), а шероховатость поверхностей – согласно ис- ходным данным.
2.3. Посадки подшипников качения
Посадки подшипников качения на вал и в корпус назначаются в зависимости от типа подшипников, его размеров, условий эксплуа- тации и характера действующих нагрузок на кольца.
Тип подшипника и его присоединительные размеры заданы в таблице на чертеже узла задания, а класс точности подшипника и его серия принимаются произвольно и указываются в пояснитель- ной записке. Для большинства механизмов общего назначения применяют подшипники 0 класса точности. Параметры подшипни- ков приведены в [6].
Методика расчёта и выбора посадок для колец подшипников ка- чения с радиальной нагрузкой изложена в [2–5].
При выборе посадок следует учитывать основные виды нагру- жения колец подшипников. Нагружение внутреннего или наружно- го кольца подшипника постоянной по направлению радиальной нагрузкой для вращающегося кольца вызывает циркуляционное нагружение, а для не вращающегося – местное. Существует общая рекомендация: посадку вращающихся колец подшипников (цирку- ляционное нагружение) необходимо выполнять с гарантированным натягом, а посадку не вращающихся колец (местное нагружение) – с гарантированным зазором.
Посадки местного нагруженного кольца на вал следует выби-
рать по [2, т. 2, табл. 4.89; 4, табл. 25].
При циркуляционном нагружении колец подшипника выбор по- садки производится по наименьшему расчётному натягу Nmin, обес- печивающему необходимую прочность соединения вращающегося кольца с поверхностью сопрягаемой с ним детали [2, 4]. Наиболь- шая радиальная нагрузка, действующая на подшипник, указана на чертеже узла задания. По найденной величине Nmin для внутреннего кольца подшипника [4, табл. 26], для наружного кольца [4, табл. 27] выбирают ближайшее поле допуска и затем проверяют выбранную посадку по допустимому максимальному натягу [4, табл. 26, 27].
12

Пример графического оформления. Посадка подшипника ка-
чения с валом и корпусом оформляется на листе формата А4. На рис. 3.1 дан пример графического оформления посадок внутренне- го и наружного колец подшипника с валом и корпусом в соответ- ствии с результатами расчёта по программе «Посадки подшипни- ков» автоматизированной системы.
Рис. 2.3. Графическое оформление посадки подшипника качения
На сборочном чертеже подшипникового узла допускается указы- вать только размер, поле допуска и предельные отклонения на диа- метр вала или отверстия, без указания поля допуска подшипника.
Для построения схем расположения полей допусков внутренне- го и наружного колец подшипника, их отклонения находят по
13
ГОСТ 520-71 [2, т. 2, табл. 4.82–4.86; 4, табл. 26, 27]. Верхнее от-
клонение присоединительных диаметров колец подшипников все- гда равно нулю.
Для построения схемы расположения полей допусков вала и от- верстия корпуса, их отклонения находят по ГОСТ 25346-89 или по прил. 1–3.
На схеме расположения полей допусков отверстия корпуса, ва- ла, наружного и внутреннего колец подшипника также определяют предельные значения зазоров и натягов при сборке подшипника с корпусом и валом.
Шероховатость посадочных поверхностей вала и корпуса для соединения с подшипником назначается по [2, т. 2, табл. 4.95], а точность формы в пределах около 0,3Td (TD).
2.4. Гладкие калибры
Виды гладких нерегулируемых предельных рабочих калибров для контроля отверстий и валов с номинальным диаметром от 1 до 500 мм и контрольных калибров для калибров-скоб установлены ГОСТ 24851-81 и приведены в табл. 2.6.
Таблица 2.6
|
|
Виды гладких калибров |
|
|
|
Обозначение вида |
Наименование вида калибра |
|
калибра |
|
|
|
|
|
|
|
Калибры для вала |
ПР |
|
Калибр-скоба гладкий проходной |
НЕ |
|
Калибр-скоба гладкий непроходной |
|
Контрольные калибры для калибров-скоб |
|
К-ПР |
|
Калибр-пробка гладкий контрольный проходной |
|
для нового гладкого проходного калибра-скобы |
|
|
|
|
К-НЕ |
|
Калибр-пробка гладкий контрольный проходной |
|
для нового гладкого непроходного калибра-скобы |
|
|
|
|
К-И |
|
Калибр-пробка гладкий контрольный для кон- |
|
троля износа гладкого проходного калибра-скобы |
|
|
|
|
|
|
Калибры для отверстий |
ПР |
|
Калибр-пробка гладкий проходной |
НЕ |
|
Калибр-пробка гладкий непроходной |
14
Расчёт гладких калибров сводится к определению исполнитель- ных размеров измерительных поверхностей, ограничению откло- нений их формы и назначению оптимальной шероховатости. В ка- честве исполнительного размера калибра-пробки берётся наиболь- ший предельный его размер с отрицательным отклонением, равным допуску на изготовление калибра, а в качестве исполнительного размера скобы берётся наименьший предельный её размер с поло- жительным отклонением, равным допуску на изготовление калибра.
Формулы для определения исполнительных размеров гладких калибров и допуски приведены в ГОСТ 24853-81 (для размеров до 500 мм). Здесь же даны схемы расположения полей допусков ка- либров и контркалибров относительно поля допуска контролируе- мой детали. Методика расчёта гладких калибров для контроля от- верстий и валов приведена в [2].
При расчёте исполнительных размеров калибров необходимо пользоваться следующими правилами округления:
–размеры рабочих калибров для контролируемых деталей квали- тетов 6–14 и всех контрольных калибров следует округлять до вели- чин, кратных 0,5 мкм, при этом допуск на калибры сохраняется;
–размеры, оканчивающиеся на 0,25 и 0,75, следует округлять до величин, кратных 0,5 в сторону сокращения производственного допуска контролируемой детали.
Числовые значения допусков формы калибров, как и допусков размеров, приняты по квалитетам ГОСТ 25346-82 (см. прил. 3). Под допуском формы гладкого калибра понимается разность между наибольшим и наименьшим действительными размерами калибра.
Параметр шероховатости поверхности калибра Rа – 10 % от до- пуска на изготовление калибра, но не более 0,2 мкм при допусках
контролируемых деталей 6–12 квалитетов.
Пример графического оформления. На листе формата А4
строится схема расположения полей допусков вала, ПР и НЕ ка- либров-скоб и контркалибров, а также схемы расположения полей допусков отверстия, ПР и НЕ калибров-пробок. Оформляется рабо- чий чертёж калибра-скобы или калибра-пробки (вставки или насадки к пробке) по всем требованиям ГОСТов и ЕСКД.
На рис. 2.4 дан пример графического оформления указанных полей допусков в соответствии с расчётами по программе «Гладкие калибры» автоматизированной системы.
15

Рис. 2.4. Пример графического оформления схемы расположения полей допусков гладких калибров
Конструкция и основные размеры калибров-скоб определяются по ГОСТ 14807-73–18369-73 и прил. 5.
Конструкция и основные размеры калибров-пробок определя-
ются по ГОСТ 14807-69–14827-69 и прил. 6, 7.
Технические требования на гладкие калибры-скобы и калибры- пробки назначаются по ГОСТ 2015-84.
Правила маркировки гладких калибров оговорены ГОСТ 201584. На нерабочей поверхности калибра наносится номинальный размер проверяемой детали, обозначение её поля допуска, число- вые величины предельных отклонений проверяемой детали, обо-
16

значение назначения калибра (например, ПР, НЕ, К-Н и т.п.). У пробок с ручками маркировка должна быть нанесена и на ручке. Для нашего примера (см. рис. 2.4) на калибре-скобе наносится
24u7 (++0,0520,041 ) (если скоба односторонняя, двухпредельная, назначе- ние калибра опускается), на калибре-пробке ПР – 24Н7(+0,021)ПР. Правила указаний на чертежах о маркировании приведены в ГОСТ 2.314-68 ЕСКД. Выносная линия с точкой от места нанесения мар- кировки оканчивается за контуром детали знаком маркировки – окружностью диаметром 10…15 мм. Внутри знака указывается но- мер пункта в технических требованиях, в котором приведены ука- зания о маркировании. Пример формулировки пункта в техниче-
ских требованиях чертежа:
маркировать: 24 Н7 (+0,021)ПР.
2.5. Резьбовые калибры
Основные виды калибров для контроля внутренней и наружной метрической резьбы указаны в табл. 2.7.
Таблица 2.7
Виды калибров для контроля резьбы
Обозначение |
|
Наименование вида калибра |
вида калибра |
|
|
|
|
|
|
Калибры для контроля внутренней резьбы |
|
|
|
1. Резьбовые калибры |
ПР |
|
Калибр-пробка резьбовой проходной |
НЕ |
|
Калибр-пробка резьбовой непроходной |
|
|
2. Гладкие калибры |
ПР |
|
Калибр-пробка гладкий проходной |
НЕ |
|
Калибр-пробка гладкий непроходной |
|
|
Калибры для наружной резьбы |
|
3. Резьбовые кольца и контркалибры к ним |
|
ПР |
|
Калибр-кольцо резьбовой проходной |
КПР-ПР |
|
Калибр-пробка резьбовой контрольный проходной |
|
|
(для нового ПР) |
КПР-НЕ |
|
Калибр-пробка резьбовой контрольный непроходной |
|
|
(для нового НЕ) |
17
Обозначение |
Наименование вида калибра |
|
вида калибра |
||
|
||
К-И |
Калибр-пробка резьбовой контрольный для контроля |
|
|
износа ПР |
|
НЕ |
Калибр-кольцо резьбовой непроходной |
|
КНЕ-ПР |
Калибр-пробка резьбовой контрольный проходной |
|
|
(для нового НЕ) |
|
КНЕ-НЕ |
Калибр-пробка резьбовой контрольный непроходной |
|
|
(для нового НЕ) |
|
|
4. Гладкие калибры |
|
ПР |
Калибр-скоба гладкий проходной |
|
НЕ |
Калибр-скоба гладкий непроходной |
|
К-ПР |
Калибр-пробка гладкий контрольный для проходного |
|
|
гладкого калибра-скобы |
|
К-НЕ |
Калибр-пробка гладкий контрольный для непроходно- |
|
|
го гладкого калибра-скобы |
|
К-И |
Калибр-пробка гладкий контрольный для контроля |
|
|
износа проходного калибра-скобы |
При расчёте калибров для метрической резьбы необходимо определить их исполнительные размеры. Исполнительными разме- рами для калибров-пробок являются наибольший предельный раз- мер для всех диаметров, а для калибров-колец – наименьший пре- дельный размер диаметров кольца.
Формулы для определения исполнительных размеров резьбовых калибров-пробок и колец, а также гладких калибров для контроля внутренней и наружной метрической резьбы приведены в ГОСТ
24997-87 и в [4].
Основные размеры и допуски контролируемой метрической резьбы с номинальным диаметром от 0,25 до 600 мм указаны в сле- дующих стандартах:
–профиль резьбы – ГОСТ 9150-81;
–диаметры и шаги – ГОСТ 8724-81;
–основные размеры резьбы – ГОСТ 24706-81;
–допуски и посадки резьбы с зазором – ГОСТ 16093-81.
На рис. 2.5 показан номинальный профиль резьбового соедине- ния и его основные параметры: d – наружный или номинальный диаметр; d1(D1) – внутренний диаметр, d1 = D1 = d – 2 · 5/8H =
18

= d – 1,0825331755 P; d2 (D2) – средний диаметр, d2 = D2 = d – 2 ×
× 3/8H = d – 0,649519053 P. Общая схема расположения полей до- пусков резьбового соединения приведена на рис. 2.5.
Рис. 2.5. Основные размеры метрической резьбы
Основные отклонения h и Н равны нулю; остальные отклонения определяют по формулам:
для болтов
esd = –(80 + 11P); esf = –(30 + 11P);
ese = –(50 + 11P); esg = –(150 + 11P);
EIF = +(30 + 11P); EIG = +(15 + 11P),
где es – верхнее отклонение болтов, мкм, Р – шаг резьбы, мм, EI – нижнее отклонение гаек, мкм.
Допуски диаметров резьбы, мкм, для степени точности 6 опре- деляются по формулам:
Td (6) = 180 3 P2 − 3,15 / |
P ; Td2 = 90P 0,4d 0,1; |
TD1(6) = 230P 0,7 |
(при Р ≥ 1 мм); |
TD1 = 433P – 190 P 1,22 (при Р ≤ 0,8 мм);
TD2 (6) = 1,32Тd2 (6).
19
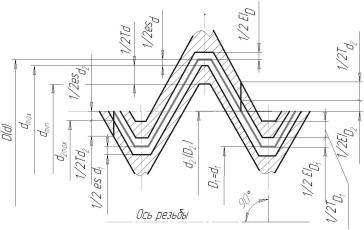
Допуски остальных степеней точности определяются умноже- нием допуска степени точности 6 на коэффициенты, представлен- ные в табл. 2.8.
Таблица 2.8
Степень точности |
3 |
4 |
5 |
6 |
7 |
8 |
9 |
10 |
Коэффициент |
0,5 |
0,63 |
0,8 |
1 |
1,25 |
1,6 |
2 |
2,5 |
Допуски на внутренний диаметр d1 наружной резьбы и наруж-
ный диаметр D внутренней резьбы не устанавливаются.
Пример графического оформления. На листе формата А3 (или большем) строится схема расположения полей допусков резьбового соединения и калибров для контроля внутренней и наружной мет- рической резьбы. На рис. 2.6 дан пример графического оформления полей допусков резьбового соединения и калибров для контроля внутренней метрической резьбы в соответствии с результатами расчёта исполнительных размеров по программе «Резьбовые ка- либры» автоматизированной системы.
Рис. 2.6. Схема расположения полей допусков резьбового соединения
При оформлении чертежа предварительно рассчитывается и строится номинальный профиль резьбового соединения в соответ- ствии с данными чертежа узла и согласно выбранному масштабу. Для расчёта и построения используется ГОСТ 9150-81 или рис. 2.7.
20