
Учебное пособие 800670
.pdf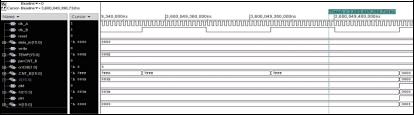
Рис. 11. Иллюстрация начала работы счетчика часов H
Рис. 12. Иллюстрация переключения регистров S, M и H
Литература
1.Евстифеев, А.В. Микроконтроллеры AVR семейств Tiny и Mega фирмы ATMEL [Текст]: руководство пользователя / А.В. Евстифеев. - 5-е изд., стер. – М.: Издательский дом «Додэка-XXI», 2008. – 560 с.
2.Поляков, А.К. Языки VHDL и Verilog в проектировании цифровой аппаратуры [Текст] / А. К. Поляков. – М.: СОЛОН-Пресс, 2003. – 320 с.
3.Стиль программирования на языке Verilog [Текст]: Verilog style and coding guidelines, SUN Microsystems / Г. Дайкема, П.
Монше, Д. Нельсен и др.; пер с англ. О.А. Ефремова.: 2002. – 30 с.
Воронежский государственный технический университет
41
УДК 621.9
Н.В. Ципина,А.А. Алехин
ПРИМЕНЕНИЕ 3D ПРИНТЕРА ПРИ ИЗГОТОВЛЕНИИ ИЗДЕЛИЙ РЭС
Рассмотрено применение 3D принтера при изготовлении изделий радиоэлектронных средств
3D принтер – это устройство, которое послойно создает физический объект по виртуальной трехмерной модели. При помощи такого устройства можно изготавливать практически любые объекты. Необходимые модели разрабатываются при помощи специального программного обеспечения для трехмерного моделирования.
Технология изготовления физических трехмерных объектов с использованием цифровых данных была впервые разработана Чарльзом Хуллом в 1984 г. В 1986 г. он получил патент на свое изобретение и назвал данную технологию Стереолитография. После получения патента, Чарльз Хулл основал компанию 3D Systems и разработал первый промышленный станок для 3D печати. Так как термин «3D принтер» в то время еще не использовался, станок назывался просто «аппарат для стереолитографии». Технология 3D печати была достаточно нова в то время, и компания 3D Systems изготовила и поставила первую модель станка нескольким избранным заказчикам. В 1988 г., основываясь на откликах клиентов о станке, компания разработала усовершенствованную модель 3D принтера SLA-250 и было начато его серийное производство.
К концу 1988 г. технологии 3D копирования получили широкую популярность, появились новые технологии: моделирование методом наплавления (Fused Deposition Modeling (FDM)) и метод селективного лазерного спекания (Selective Laser Sintering (SLS)). Технология моделирования методом наплавления была изобретена Скотом Крамп в 1988 г. В следующем году им была основана компания Stratasys и налажено промышленное производство станков. В 1992 г. компания продала свой первый станок "3D Modeler". В том же году компания DTM выпустила на рынок станок, работающий по технологии селективного лазерного спекания (SLS). В 1993 г. в Массачусетском технологическом институте (MIT) была изобретена и запатентована еще одна
42
технология 3D печати. Она получила название «Технологии трехмерной печати» и была подобна технологии струйной печати, используемой в 2D принтерах. В 1995г. компания ZCorporation получила от Массачусетского технологического института патент на использование технологии и начала производство 3D принтеров, на базе 3DP технологий. [7]
В 1996 г. были произведены станки "Genisys" от компании
Stratasys, "Actua 2100" – от 3D Systems, и "Z402" – Z Corporation. В
течение этого времени впервые появился термин «трехмерная печать» для обозначения станков быстрого моделирования. В конце 1990-х - начале 2000 гг., в продаже появились несколько моделей станков по относительно низким ценам. В 2005 г. компания Z Corporation выпустила на рынок революционно-новую модель Spectrum Z510 – станок 3D печати с высоким разрешением цветов. Еще один прорыв в области трехмерной печати произошел в 2006 г. с созданием общедоступного проекта Reprap, нацеленного на производство 3D принтера, способного воспроизводить детали собственной конструкции. Первая модель Reprap, произведенная в 2008 г., может произвести приблизительно 50% своих собственных частей. Вторая модель проекта Reprap находится в настоящее время в стадии разработки [7].
Существуют такие 3D принтеры, которые способны печатать одновременно двумя и более разными материалами или выполнять многоцветную печать. В связи с этим помимо технологии печати принтеры подразделяются и следующие типы:
1.Монохромный. Особенность данного вида – возможность использования только одного цвета для печати.
2.С возможностью использования 3D-прототипов. То есть, принтеры, которые могут работать после загрузки 3D-модели. Такой тип позволяет проработать самые мельчайшие детали будущего объекта.
3.Принтер, со встроенной камерой обдува. Данная особенность позволяет исключить последний этап создания объекта
–финальную обработку. То есть на выходе получается готовая 3Dмодель, не требующая какой-либо обработки и очистки.
Первый порошковый 3D принтер был разработан в нидерландском университете в городе Твенте. Устройство работает по технологии спекания порошка с использованием связующего вещества. То есть печатающая головка наносит связующее вещество
43
на определенные места (в соответствии с компьютерной моделью), после чего вал наносит тонкий слой порошка. Далее головка снова наносит связующее вещество, после чего вал наносит тонкий слой порошка и так далее.
Принтер достаточно просто собрать. Он изготовлен из стандартных комплектующих, которые весьма просто найти.
Такой принтер способен работать и с другим типом порошков
– металлическая пудра. Для этого порошковый принтер должен работать по технологии запекания.
Гипсовый 3D принтер относится к виду порошковых устройств, но он способен работать только со связующими веществами и исключительно со строительными порошками, такими как гипс, цемент, шпаклевка и так далее.
Гипсовый 3D принтер работает по такому же принципу, как и порошковый аппарат. С его помощью можно создавать самые разнообразные изделия из строительных порошков. Такие устройства часто используются в дизайнерских студиях для создания украшений интерьера.
Фотополимерный 3D принтер. Данная технология работает по принципу постепенного создания объекта их жидких фотополимеров. В процессе создания ультрафиолетовый лазер засвечивает определенные места (в соответствии с компьютерной моделью), которые под воздействием ультрафиолета затвердевают. Конечно, процесс засветки достаточно длителен, а каждый слой измеряется в микронах. Засветка фотополимера может также осуществляться и при помощи ультрафиолетовой лампы через специальный фотошаблон, который меняется с каждым новым слоем.
Стереолитографический 3D принтер отличается высокой точностью. Даже персональные модели не сильно уступают в точности профессиональным аппаратам. Конечно, для достижения такой точности пришлось принести в жертву скорость, однако в некоторых случаях точность изготовленных моделей имеет наибольшее значение.
Лазерный 3D принтер работает по разным технологиям – плавление, спекание или ламинирование.
Технология плавления заключается в том, что используемый порошок предварительно разогревается до температуры близкой к плавлению. После этого луч лазера плавит порошок, формируя слой.
44
Далее слой должен застыть, после чего насыпается следующая порция порошка, и лазер наносит следующий «рисунок».
Такие принтеры способны работать практически с любыми термопластичными материалами. При этом скорость печати может достигать нескольких десятков мм/час. Конечно, есть и отрицательная сторона медали. Поверхности изготовленных деталей при помощи такого принтера является слишком шероховатой, а также требуется весьма длительное время для подготовки к работе.
Преимущество, заключается в том, что такие устройства способны работать с металлическими порошками. Это позволяет создавать настоящие металлические изделия, которые не уступают по прочности деталям, изготовленным традиционным способом. Конечно, в случае с металлическими порошками после печати изделие нуждается в последующей обработке – в насыщении бронзой и запекании в специальной печи.
Технология спекание заключается в том, что лазер выжигает в порошке из легкосплавного пластика контуры изготавливаемой детали. После завершения процесса излишки порошка просто стряхиваются с поверхности готового изделия.
Ламинирование – это процесс, при котором изделие изготавливается из большого количества слоев расходного материала. Эти слои накладываются друг на друга и склеиваются. В процессе наложения слоев лазер вырезает в каждом из них нужный контур в соответствии с компьютерной моделью.
Сублимационный 3D принтер представляет собой устройство, которое используется для переноса изображений на рельефные объекты. Это осуществляется путем нагревания специальных красителей в определенных местах, которые под воздействием температуры начинают испаряться и оставлять рисунок на поверхности каких-либо изделий.
Восковой 3D принтер. Воск – это уникальный материал, который имеет низкую температуру плавления, Благодаря чему с ним очень просто работать. Именно по этой причине многие дизайнеры выбирают именно этот материал.
Конечно, изделия в человеческий рост 3D принтер не сделает, однако точность моделей, сделанных при помощи трехмерной печати, просто поражает.
Цветной 3D принтер позволяет создавать модели разных цветов. Такая возможность достигается благодаря тому, что в
45
принтере используется печатающая головка с несколькими экструдерами – устройствами, которые плавят и наносят расходный материал, к примеру, пластик.
Такие устройства уже сегодня пользуются огромным спросом. Как правило, в качестве расходного материала такой 3D принтер использует пластик. [1]
В зависимости от типа принтера необходимо использовать соответствующие материалы. К примеру, порошковый аппарат может работать только с порошками и связующими веществами. Поэтому прежде чем покупать тот или иной 3D принтер необходимо определиться с тем, в каких целях он будет использоваться. Конечно, стоит понимать, что разные материалы для 3D принтеров имеют различную стоимость. Также они могут иметь разное качество. Более распространенные и крупные бренды предоставляют качественные материалы, из которых получаются наиболее прочные изделия. Поэтому не стоит экономить на материалах.
Помимо всего прочего технология трехмерной печати постоянно развивается, появляются новые принтеры, которые имеют уникальный принцип работы. Также ведутся активные разработки расходных материалов, и с каждым годом их список становится все длиннее.
Также 3D-принтеры можно классифицировать по целевой аудитории: производственные; персональные; потребительские; профессиональные.
Потребительские 3D-принтеры, в первую очередь, ориентированы на художников, дизайнеров, архитекторов, которые предпочтительно работают дома.
Модели подобного класса без проблем создают несложные модели небольших размеров. Основным рабочим материалом служит ABSили PLA-пластик.
Особенность 3D-принтеров данного класса – медленная
работа и относительно низкое качество печати. |
|
|
||
3D-принтеры |
для |
персонального |
||
использования рекомендуются |
для |
дизайн-студий, |
рекламных |
|
агентств, а также малого бизнеса. |
|
|
|
|
Цена таких аппаратов |
на |
порядок выше, |
но |
вложения |
оправдываются более высокой производительностью, а также точностью печати.
Профессиональные |
3D-принтеры необходимы |
лишь |
|
46 |
|
компаниям, деятельность которых подразумевает систематическое их использование.
Принтеры данного класса могут похвастаться высочайшей точностью и скоростью работы, но требуют определенных навыков управления.
Производственные 3D-принтеры используются лишь для мелкосерийного или серийного производства (то есть тогда, когда необходима печать большого количества объектов). Использование аппарата имеет несколько нюансов:
-наличие обученного персонала;
-большое помещение;
-необходима подводка к высоковольтной линии и
газовой трубе.
Для печати могут использоваться самые разные материалы – порошки, пластики, металл.
Производство деталей, изготовленных с помощью аддитивных технологий, в ближайшее будущее найдет широкое применение для производства радиоэлектронных изделий. Так, к примеру, если напечатать слой за слоем изделия из кобальтхромового порошка, то оно будет легче и долговечней. [2]
Что же касается современности, то сегодня трехмерная печать активно используется не только в промышленности и строительстве, но и занимает свою устойчивую позицию в радиоэлектронной промышленности.
Литература
1.http://www.techno-guide.ru
2.http://3dprinn.ru
3.http://pechatnick.com/
4.Слюсар, В.И. Фаббер-технологии. Новое средство трехмерного моделирования [Текст] / В.И. Слюсар // Электроника: наука, технология, бизнес. - 2003. - № 5. C. 54 - 60. (2003).
5.3D INDUSTRY. Все о 3d печати [Электронный ресурс]: Режим доступа: http://www.3dindustry.ru/article/676/
6.3D-принтеры и технология трехмерной печати [Электронный ресурс]: Режим доступа: http://vektorus.ru/auxpage_3d- printery-i-tehnologija - trehmernoj-pechati
7.http://help31.ru
Воронежский государственный технический университет
47
УДК 621.396.
В.С. Скоробогатов, Ю.М. Данилов
СНИЖЕНИЕ ПРОИЗВОДСТВЕННОГО ШУМА ПРИ ПРОЕКТИРОВАНИИ ОБОРУДОВАНИЯ В ЛИНИЯХ
ЭЛЕКТРОННОЙ ПРОМЫШЛЕННОСТИ
Приводятся рекомендации и формула по выбору условий для снижения влияния производственного шума в линиях электронной промышленности
Под шумом понимается комплекс звуков, неблагоприятно воздействующих на организм человека, мешающих его работе и отдыху. С физической точки зрения звук представляет собой волнообразно распределяющееся колебательное движение частиц упругой среды.
Источником шума являются колеблющиеся твердые, жидкие или газообразные тела. Колеблющееся тело возбуждает в упругой среде, например в воздухе, механические колебания, при которых частицы среды в непосредственной близости от колеблющегося тела смещаются, приходя в состояние ритмического движения. Чем больше амплитуда колебания звучащего тела, тем больше амплитуда звукового давления и соответствующая сила звука.
Звуковым давлением дБ, Н/м2, называется переменное давление, избыточное над равновесным, возникающее при прохождении звуковой волны в жидкой или газообразной среде. Звуковые колебательные движения происходят по синусоидальному закону, время, в течение которого колеблющееся тело совершает одно полное колебание, называется периодом колебания и измеряется в секундах.
Число полных колебаний, совершенных в течение одной секунды, называется частотой колебания. Единица измерения частоты – герц f, Гц, равна одному колебанию в секунду. Частотой колебаний определяется высота тона. Чем больше частота колебаний, тем выше тон слышимого звука.
Интенсивность звука является характеристикой звукового поля в определенной точке пространства и измеряется в децибелах
(дБ).
Колебания с частотой от 16 до 20 000 Гц человек воспринимает как звук. Наименьшая сила звука, которая может
48
восприниматься органами слуха, носит название порога слышимости данного звука. При увеличении силы звука выше определенного предела ощущается болезненное давление в ушах, которое оценивается как порог болевого ощущения. Нормальные органы слуха наиболее чувствительны к звукам с частотой от 500 до 4000 Гц (имеющим наименьшие пороги слышимости). Некоторые технологические процессы и операции в электронной промышленности (штамповка в металлозаготовительных цехах, резка слитков на пластины, шлифование, полирование, и т. п.) сопровождаются интенсивным производственным шумом.
Промышленный шум от работающего оборудования можно подразделить, на низкочастотный (f = 300 - 400 Гц), среднечастотный (f = 400 - 1000 Гц) и высокочастотный, если наибольшие уровни в спектре расположены выше частоты f = 1000 Гц.
Для определения уровней звукового давления, для различных технологических операций работы современного оборудования электронной промышленности, рассчитаны формулы.
Для шлифования и полирования
дБ = 91,3 + 0,016 · f - 0,0000053 · f 2. |
(1) |
Для механических цехов
дБ = 80 + 0,0118 · f - 0,0000044 · f 2. |
(2) |
Для штамповочно-прессовых цехов
дБ = 88,67 - 0,00133 · f . |
(3) |
Формулы (1) – (3) представляют средние результаты наложения десятков измерений спектров на рабочих местах одной и той же профессии.
Предельно допустимый уровень шума на рабочих местах в цехах 80 дБ. На основании измерений, полученных в производственных условиях можно сделать вывод, что промышленный шум при отдельных процессах и операциях превышает допустимый уровень и является опасным для здоровья рабочих при длительном контакте с ним.
Производственный шум не только вызывает поражение внутреннего уха, но и оказывает общее воздействие на организм, особенно на сердечно-сосудистую и нервную системы. Это
49
проявляется в виде головокружений, шума в ушах, головных болей, изменении артериального кровяного давления, изменения ритма сердечных сокращений и т. п. Производственный шум, мешая сосредоточиться, может снижать работоспособность и способствовать увеличению несчастных случаев — травм.
Воздействие шума на организм зависит от его частотного состава (спектра). Допустимые уровни звукового давления на постоянных рабочих местах устанавливаются в соответствии с гигиеническими нормами.
Допустимые уровни звукового давления на рабочих местах зависит от среднегеометрической частоты октавных полос f, Гц.
Для постоянных рабочих |
мест в |
производственных |
|
помещениях и на территории предприятия |
|
|
|
дБ = 99,5 - 0,00852 · f + 0,000000666 · f 2. |
(4) |
||
Для помещений и участков точной сварки, машинописных |
|||
бюро |
|
|
|
дБ = 83,63 -0,0106 · f - |
0,000000856 · f 2. |
(5) |
Радикальным мероприятием по борьбе с производственным шумом является устранение источника его возникновения. Это осуществляется рационализацией технологических процессов и оборудования, а также внедрением технологических усовершенствований и приспособлений, способствующих снижению
. уровней шума. Устранение причин шума должно начинаться с момента конструирования оборудования.
Для уменьшения шума ударные процессы заменяют безударными, например кузнечные и штамповочные молоты — прессами, ударную правку — вальцеванием, пневматическую клепку и чеканку — сваркой и гидравлической клепкой.
Подшипники качения заменяют подшипниками скольжения (при этом меняется также частотный состав шума), переходят на безредукторные передачи, плоскоременные передачи заменяют на
клиноременные, |
возвратно-поступательные |
движения |
— |
||
вращательными. Уменьшают интенсивность вибрации |
больших |
||||
поверхностей |
(корпуса агрегата, |
кожухи, крышки) заполнением |
|||
специально предусмотренных |
воздушных |
полостей |
демп- |
фирующими материалами, ослабляющими вибрацию силами трения
или |
звукопоглощающими материалами. Между вибрирующим |
|
50 |