
Учебное пособие 800579
.pdfШтамповке свойственны и некоторые недостатки:
1.Ограниченность штампованных изделий по массе. В настоящее время преимущественно штамповкой изготавливают изделия массой до 100 кг, однако штамповочное производство непрерывно развивается в направлении увеличения массы поковок. Иногда изготовляют поковки массой до 2 тонн;
2.Высокая стоимость штампа, который в отличие от универсального инструмента свободной ковки является узкоспециализированным, т. е. годным для изготовления только одной определенной поковки.
Поэтому штамповка выгодна лишь в серийном и массовом производствах.
В качестве исходного материала применяется сортовой прокат, прессованные прутки, литая заготовка. В крупносерийном производстве часто применяется прокат периодического профиля, что сокращает подготовительные операции.
Штамповка может быть облойная (с заусенцем) и безоблойная (без заусенца).
Облойная штамповка отличается тем, что поковка по месту разъема штампа имеет заусенец (облой). Заусенец получается потому, что в штампе имеется специальная канавка вокруг ручья для помещения избытка металла (облоя). При этом полость штампа хорошо заполняется металлом, так как объем заготовки берется больше объема ручья штампа. Такие штампы называются открытыми (рисунок 10.10). Облойный способ, несмотря на потери металла, получил большое распространение, так как в этом случае надежно обеспечивается заполнение полостей штампа, а объем заготовки может быть лишь приблизительно равен необходимому. По окончании штамповки облой удаляется на обрезных штампах (рис. 10.10).
Безоблойная штамповка производится в закрытом штампе. Заготовка помещается в полость одной части штампа,
адругая часть входит в первую как в направляющую. В
180
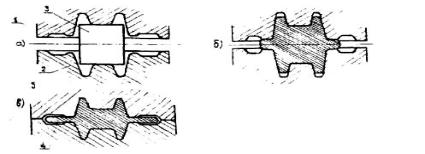
зависимости от сложности получаемого изделия и вида применяемой готовки штамповка может быть одноручьевой или многоручьевой.
При многоручьевой штамповке заготовка штампуется последовательно в нескольких ручьях. Каждый ручей имеет определенное назначение, и их разделяют на следующие виды:
штамповочные: чистовой (окончательной) и предварительный (черновой).
В зависимости от сложности получаемого изделия и вида применяемой готовки штамповка может быть одноручьевой или многоручьевой.
При многоручьевой штамповке заготовка штампуется последовательно в нескольких ручьях. Каждый ручей имеет определенное назначение, и их разделяют на следующие виды:
1. Штамповочные: чистовой (окончательной) и предварительный (черновой).
Рис. 10.10. Схема облойной штамповки в открытом штампе: 1,2 – части штампа; 3 – заготовка; 4 – заусенец (облой); 5 – канавка для облоя
2.Заготовительные: |
протяжной, |
подкатной, |
формовочный, гибочный. |
|
|
3. Отрезной (нож).
Окончательный ручей имеется во всяком штампе; остальные ручьи применяются в тех или иных комбинациях в зависимости от конфигурации поковки.
181
Окончательный ручей служит для получения готовой поковки и представляет собой точное отображение последней, но с размерами, большими на величину усадки металла. Вокруг открытого чистового ручья имеется канавка для заусенца.
Предварительный ручей служит для снижения износа окончательного ручья и придания заготовке формы, близкой к заданной. Отличается от чистового несколько большими штамповочными уклонами и отсутствием канавки для облоя.
Заготовительные ручьи используют для первоначальной обработки с целью постепенного приближения формы заготовки к форме готового изделия.
Формовочный ручей служит для придания заготовке формы, соответствующей форме поковки в плоскости разъема.
Пережимной ручей используют в тех случаях, когда нужно создать местное уширение за счет незначительного перераспределения металла вдоль оси.
Подкатной ручей служит для значительного увеличения одних поперечных сечений за счет уменьшения других, то есть для перераспределения объема металла вдоль оси заготовки.
Протяжной ручей используется для увеличения длины отдельных участков заготовки за счет изменения их поперечных размеров, когда длина заготовок меньше длины поковки.
Гибочный ручей служит для изгиба заготовки и придания ей формы, соответствующей форме поковки в плоскости разъема. В следующий ручей заготовку передают с поворотом на 90° вокруг ее оси.
Отрезной ручей применяют, когда нужно отделить поковку от прутка, при удалении клещевины, при разрубке поковок на части.
Штампы для горячей штамповки работают в очень тяжелых условиях. Поэтому штамповая сталь должна обладать высокими механическими свойствами прочностью, ударной вязкостью, твердостью и сохранять эти свойства при повышенных температурах. Кроме того, нужны
182
износостойкость и хорошая обрабатываемость резанием. Штампы изготавливают из специальных сталей 5ХНМ, 5ХГМ, ХНТ, Х12Ф, Х12М и др.
Штамповка так же, как и ковка, может производиться на молотах и прессах.
Достоинства молотов: большая универсальность, меньшая стоимость оборудования, хорошо отделяется окалина от удара.
Достоинства прессов: повышенная точность из-за отсутствия ударной нагрузки; большая производительность за счет того, что штамповка осуществляется за один ход ползуна, а не за несколько ударов на молоте; большая безопасность работы и отсутствие сотрясений почвы; ниже требуемая квалификация рабочего.
Листовая штамповка – способ изготовления тонкостенных изделий из листового материала, ленты или полосы с помощью штампов. Листовой штамповкой обрабатывают все технические металлы и их сплавы, картон, пластмассы, кожу и другие материалы. Очень много разнообразных по конфигурации деталей можно получить, совмещая в технологическом процессе листовую штамповку и сварку. Так получают детали гильзы, корпуса ракет, бензобаки, баллоны и т. д.
Характерным для листовой штамповки является то, что толщина стенок деталей обычно мало отличается от толщины исходной заготовки.
В зависимости от толщины заготовки штамповку делят условно на тонколистовую (до 4 мм) и толстолистовую (свыше 4 мм).
Широкое распространение листовой штамповки объясняется тем, что этот процесс дает возможность:
1.Обеспечить очень высокую производительность (до 1 000 – 50 000 деталей в смену с одного штампа).
2.Механизировать и автоматизировать штамповочные работы, что облегчает труд рабочего.
3.Обеспечить достаточно высокую точность деталей, а, следовательно, их взаимозаменяемость.
183

4.Получить детали с хорошим качеством поверхности.
Все разнообразные по форме и размерам детали получают, применяя поочередно отдельные элементарные операции. Операции листовой штамповки можно разделить на две группы: разделительные, в которых одну часть заготовки отделяют от другой (отрезка, вырубка, пробивка), и формоизменяющие, в которых происходит перемещение одной части заготовки относительно другой без разрушения (гибка, вытяжка, формовка, обжим, отбортовка, закатка, правка и некоторые другие). Рассмотрим основные из этих операций.
Отрезка–отделение части заготовки по незамкнутому контуру. Осуществляется на ножницах с параллельными ножами, гильотинных и дисковых.
Вырубка–отделение части заготовки по замкнутому контуру, причем отделяемая часть является изделием (рис. 10.11а).
Рис. 10.11. Операции листовой штамповки: а) вырубка и пробивка; б) гибка; в) отбортовка; г) вытяжка; д) обжим; е) раздача
Пробивка– отделение части заготовки по замкнутому контуру, причем отделяемая часть является отходом. Эти две операции, отличающиеся только по назначению, осуществляются при помощи штампа, состоящего из пуансона 1 и матрицы 2.
184
Гибка – придание плоской заготовке изогнутой формы по заданному контуру (рис. 10.11б).
Отбортовка – образование борта (горловины) по внутреннему или наружному контуру листовой заготовки (рис. 10.11в).
Вытяжка – образование полой детали из плоской заготовки (рис. 10.11г). Во избежание образования складок осуществляют вытяжку с прижимом. Если за одну вытяжную операцию изделие получить невозможно, применяют несколько последовательных вытяжек. Между операциями производят отжиг, травления для снятия окалины, промывку и сушку.
Сущность операций обжима и раздачи ясна из рис. 10.11 д, е. Формовка – операция, дающая местное изменение формы. Формовку применяют при изготовлении ребер жесткости средней части полого изделия и т. д. Формовку осуществляют
спомощью резиновых вкладышей, жидкости, взрывов и т. д.
Вкачестве машин–орудий при листовой штамповке применяют различные прессы: кривошипные, фрикционные, гидравлические.
Все прессы можно разделить на прессы простого и двойного действия. У прессов простого действия имеется только один ползун, на котором укрепляется пуансон. Такие прессы используются для вырубки, прошивки, гибки и простой вытяжки.
Прессы двойного действия имеют два ползуна. Наружный ползун обеспечивает прижим листовой заготовки, внутренний главный ползун выполняет основную операцию штамповки (вытяжку, гибку или формовку).
Основным инструментом при листовой штамповке является штамп, который состоит из рабочих элементов (пуансона и матрицы) и ряда вспомогательных устройств (рис. 10.12).
185
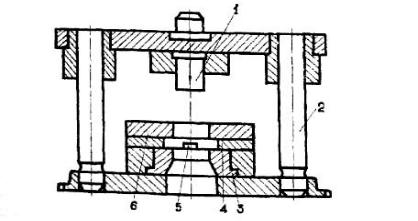
Рис. 10.12. Штамп для вырубки: 1 – пуансон; 2 – направляющие колонки; 3 – матрица, 4 – планки; 5 – упор; 6 – съемник
Пуансон крепится к ползуну пресса, матрица – на столе. Чтобы обеспечить совпадение осей матрицы и пуансона, перемещение верхней плиты выполняют по направляющим втулкам. Во многих штампах имеются съемники, выталкиватели и другие устройства. Для направления подаваемого в матрицу металла используются направляющие планки.
Ротационное обжатие. Ротационным обжатием
(редуцированием) называют способ формообразования давлением сплошных и полых деталей – тел вращения переменного сечения вдоль оси. Редуцирование методом ротационного обжатия осуществляется как в горячем, так и в холодном состоянии, что обеспечивает экономию металла на 5
– 25 %, повышает производительность в 20– 31 роз и повышает исходные прочностные показатели до 50 %.
Ротационное обжатие осуществляется на специальных ротационно-обжимных машинах. Схема головки одношпиндеольной ротационнообжимной машины с одной парой матриц показана на рисунке 10.13а, б, а общий вид на рис. 10.13в.
186
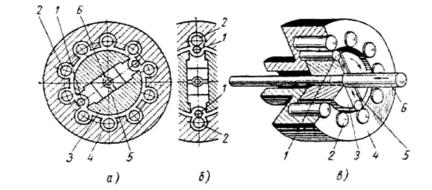
Рис. 10.13. Схема ротационно-обжимной машины
Головка, закрепленная неподвижно в корпусе станины, имеет в передней части отверстие, в которое запрессовано закаленное кольцо. Между кольцом и шпинделем 3 помещена обойма 4 с четным числом роликов 2. Боковые поверхности роликов частично выступают со стороны внутренней поверхности обоймы. Шпиндель 3, вращающийся с определенной скоростью, имеет диаметральный паз, по которому бойки с матрицами 5 совершают возвратнопоступательные движения в радиальном направлении.
Движение матриц от центра происходит за счет центробежной силы, а к центру (рабочее движение) – от давления роликов 2, установленных в обойме 4 на ролики 1. При движении к центру матрицы рабочими поверхностями деформируют металл заготовки 6. Теоретическое число обжатий в минуту N определяют по формуле
=· ,
где – число оборотов матриц в минуту; – число роликов в обойме. Заготовка подается в матрицы, коническая часть которых обжимает передний конец ее в течение нескольких последовательных ударов. После каждого совместного удара (обжатия) в момент, когда матрицы находятся в разжатом положении, следует осевое движение подачи заготовки. Величина подачи зависит от диаметра заготовки, степени деформации и свойств материала заготовки (рис. 10.13).
187
При изготовлении небольшого числа деталей, деформируемых с малыми обжатиями, подача заготовок осуществляется вручную, длинные же заготовки даются автоматически, для чего в ротационно-обжимной машине предусматривается специальное приспособление. Отсутствие огранки при редуцировании цилиндрического сечения обеспечивается большим числом наносимых ударов в минуту.
Точность размеров при редуцировании соответствует 6-8 квалитетам, а шероховатость поверхности – RZ= 2,5– 0,8 мкм.
Порошковая металлургия. Порошковая металлургия–
отрасль технологии, занимающаяся изготовлением материалов и деталей из металлических порошков.
Порошковая металлургия позволяет получать материалы и детали, обладающие высокой жаропрочностью, износостойкостью, стабильными магнитными свойствами; полупроводниковые материалы, материалы, не смешивающиеся в оплавленном виде и не образующие твердых растворов, пористые материалы, материалы высокой чистоты, заданного химического состава и др.
Методами порошковой металлургии зачастую могут быть получены детали, которые получают и литьем, но при этом потери значительно меньше:
3–7%, тогда как при литье они достигают 50–80%. Механические свойства полученных изделий незначительно уступают свойствам литых и кованых изделий. Изделия, полученные порошковой металлургией, по точности размеров и шероховатости поверхности не требуют дополнительной обработки.
Сущность способа заключается в спекании при высокой температуре специально подготовленного брикета. Брикет получают прессованием металлических порошков под давлением. По форме и размерам брикет представляет собой будущую деталь.
Металлические порошки получают двумя основными методами: механическим (размол в шаровых или вихревых мельницах) и физико-химическим (восстановление из окислов, электролиз и др.).
188
Технологический процесс металлокерамики складывается из следующих операций: 1) приготовление шихты требуемого состава; 2) дозирование; 3) формование детали; 4) спекание; 5) калибровка.
Сначала порошки очищают химическим, гидромеханическим или магнитным способами, затем проводят измельчение для выравнивания зернистости в шаровых мельницах. Возникающий при этом наклеп снимают отжигом в защитой атмосфере. Далее шихту просеивают и смешивают в вибрационных или барабанных смесителях.
Полученную шихту дозируют по массе или по объему. Формование (получение брикета заданной формы и раз-
меров) осуществляют путем прессования в стальных прессформах, реже прокаткой (для получения листа, полосы или ленты). Прессование осуществляют на механических и гидравлических прессах, жидкостью через пластичную оболочку, взрывом и т. д. В зависимости от размеров детали применяют одностороннее или двухстороннее прессование.
Спекание отформованных брикетов (деталей) производят в водородных или вакуумных печах при температуре сп = (0,7–0,8) пл °С, где пл – температура плавления основного компонента шихты.
В результате спекания происходит настолько прочное сцепление частиц порошка (вследствие диффузии), что отдельные частицы порошка как бы перестают существовать самостоятельно. В результате спекания, происходит: а) упрочнение и изменение физико-химических свойств, вследствие изменения величины и качества контактных участков; б) изменение размеров детали (усадка или рост); в) изменение микроструктуры (рост зерен и др.).
Время спекания составляет 0,5–6 часов. Горячее прессование, заключающееся в одновременном прессовании и спекании, сокращает время в 20–30 раз, производится при более низкой температуре и давлении, чем спекание. Однако недостатком горячего прессования является малая стойкость прессформ.
189