
Учебное пособие 800579
.pdf
производительнее зубофрезерование червячными фрезами. Зубодолбление – эффективный метод изготовления блоков из двух и трех зубчатых колес.
3) Схема зубострогания
При зубострогании вращающееся нарезаемое коническое колесо как бы находится в зацеплении с воображаемым плоским колесом, у которого роль двух зубьев выполняют два резца, имеющие вращательное и встречные возвратнопоступательные движения строгания (рис. 7.6).
В процессе одной обкатки резцы строгают один зуб с обеих сторон, после обработки каждого зуба цикл повторяется.
Этот способ зубообработки чаще используют для изготовления высокоточных конических зубчатых колес.
Рис. 7.6. Схема зубострогания
Для осуществления нарезания зубьев методом обкатки требуются специальные зубообрабатывающие станки:
110
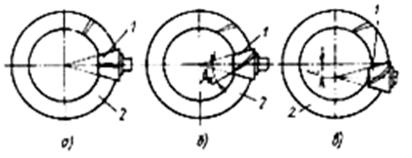
зубофрезерные, зубодолбежные, зубострогальные, зубопротяжные и др.
Обработка конических зубчатых колес.
Типы конических зубчатых колес. В зависимости от формы зуба различают прямозубые конические колеса, нулевые, с криволинейными зубьями и гипоидные.
Рис. 7.7. Типы конических колес: а) прямозубые; б) с криволинейными зубьями; в) гипоидные. 1 – шестерня; 2 – колесо
Упрямозубых колес зубья при своем продолжении пересекают ось колеса (рис. 7.7,а). Эти колеса просты для изготовления и сборки. Их применяют для передачи небольших крутящих моментов с окружными скоростями до 5- 10 м/с.
Унулевых колес зубья криволинейные с углом наклона в середине венца, равным нулю. Эти колеса изготовляют на тех же станках и тем же инструментом, что и конические колеса с криволинейными зубьями. Нулевые колеса устанавливают в тех же узлах, что и прямозубые. Они могут работать плавно и бесшумно при более высоких окружных скоростях, чем прямозубые колеса.
У колес с криволинейными зубьями угол наклона линии зуба в середине венца не равен нулю (рис. 7.7,б). Вследствие кривизны зубьев при зацеплении обеспечивается
111
непрерывный контакт одновременно на нескольких зубьях. Они способны передавать крутящие моменты примерно на 30% выше, чем нулевые и прямозубые конические колеса тех же размеров. Конические колеса с криволинейными зубьями применяют в оборудовании всех типов, при окружных скоростях до 40 м/с. У гипоидных колес ось ведущей шестерни 1 смещена относительно оси ведомого колеса 2 выше или ниже на величину Е (рис. 7.7,в). Гипоидные колеса прочнее и бесшумнее в эксплуатации, чем конические колеса с криволинейными зубьями. Их применяют в узлах и механизмах с окружными скоростями 5-40 м/с и менее.
Методы получения заготовок. Объемная холодная штамповка является наиболее эффективным методом малоотходного изготовления деталей. При высокой производительности она обеспечивает минимальный припуск (0,1-0,3 мм) на сторону, получение гладкой поверхности без окалины, значительно сокращает или полностью устраняет последующую механическую обработку. Например, коническую шестерню-вал с диаметром зубчатого венца 40 мм изготовляют за пять переходов с производительностью 30 шт/мин. Потеря металла в стружку составляет 2—7%.
Горячая штамповка конических колес с припуском 0,6— 0,8 мм на сторону под чистовое зубонарезание разработана ЗИЛом совместно с НИИТ автопромом. Применяется для конических колес дифференциала автомобиля с модулем 5 мм и выше. Предварительно нагретую с помощью ТВЧ до температуры ковки мерную заготовку 1 сателлита дифференциала ( = 11; = 6,35 мм; = 30 мм) штампуют за два перехода: осадка заготовки 2 для очистки от окалины и приближения ее диаметра к диаметру поковки и штамповка заготовки 3 с формообразованием зуба. Штамповку выполняют на кривошипном горячештамповочном прессе с номинальным усилием 16 МН и производительностью 300 шт/ч. Масса заготовки снижена на 0,37 кг. При этом за год экономится 472 т легированной стали, сокращена операция
112
чернового зубонарезания, высвобождены рабочие, станки, производственная площадь и т. д.
Метод порошковой металлургии позволяет получить значительную экономию металла. Прямозубые конические колеса дифференциала автомобиля изготовляют на автоматической линии в три последовательных перехода: точное взвешивание порошка и изостатическое формование в эластичной или деформируемой оболочке, спекание при температуре 1315°С и окончательная горячая штамповка на горизонтальном эксцентриковом прессе за один ход Производительность пресса 360—450 шт/ч. Прямозубые конические колеса, обработанные этим методом, не требуют дополнительной механической обработки; их точность соответствует точности колес, нарезанных методом кругового протягивания. Отход металла в стружку составляет около 5%.
Заготовки, полученные методом пластической деформации в холодном или горячем состоянии, обычно имеют неоднородную твердость и неблагоприятную для резания структуру металла. Для устранения указанных недостатков заготовки перед механической обработкой подвергают нормализации, улучшению, отжигу, отпуску. Наилучших результатов при обработке заготовок из легированных сталей достигают при изотермическом отжиге. После изотермического отжига заготовки имеют крупнозернистую ферритно-перлитную структуру с твердостью НВ 156—207 и пределом прочности при растяжении σв = 520 ÷ 686 МПа. Если заготовки имеют пониженную твердость, то при обработке зубьев металл налипает на режущие кромки инструмента, параметр шероховатости поверхности повышается. Слишком твердый материал вызывает повышенное изнашивание инструмента.
Точность обработки заготовок. Качество окончательно изготовленных конических и гипоидных зубчатых передач в значительной степени определяется точностью обработки заготовок. Наиболее ответственными поверхностями являются шейки, отверстия и опорные торцы, которые являются базами
113
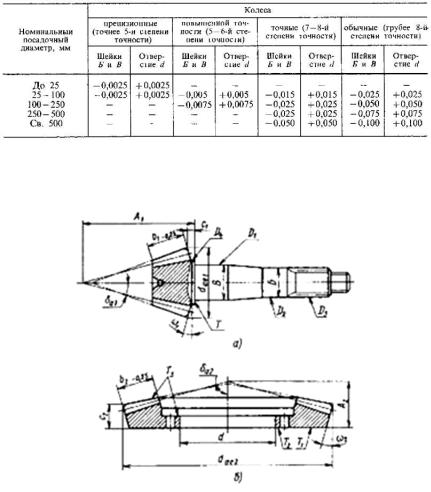
при зубообработке, контроле и сборке. В табл. 7.1 приведены допуски на отверстия и шейки типовых конических зубчатых колес в закаленном и незакаленном виде в зависимости от их степени точности (ГОСТ 1758-81).
Таблица 7.1 Рекомендуемые допуски на заготовки конических зубчатых
колес, мм
Максимальное биение поверхностей Т, D1 и D2 шестерни относительно оси детали в незакаленном и закаленном виде составляет 0,005 — 0,01 мм (рис. 7.8,а).
Рис. 7.8. Допуски на основные размеры и поверхности: а) шестерни; б) колеса
114
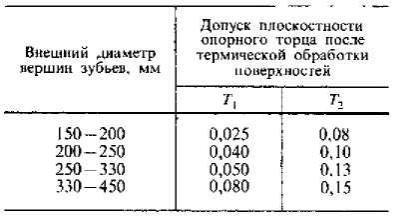
Биение незакаленной цилиндрической поверхности D4, служащей для контроля точности установки зубчатого колеса при сборке в редукторе, относительно поверхностей D1 иD2 должно быть в пределах 0,005—0,01 мм. Биение поверхности D3 ограничивается допуском в том случае, если она используется для зажима во время зубонарезания и контроля. После термической обработки и зачистки центров необходимо править деталь таким образом, чтобы максимальное биение поверхности D1 после правки не превышало 0,025 мм, а поверхности D2 — 0,04 мм. Для конических колес (рис. 7.8,б) устанавливают допуски плоскостности опорного торца (табл. 7.2). Допуск плоскостности опорного торца до термической обработки для поверхностей Т1 и Т2 составляет 0,025 мм; допуск круглости отверстия d до термической обработки — 0,025 мм, а после термической обработки — 0,08 мм.
Таблица 7.2 Рекомендуемые допуски (мм) плоскостности торца
У зубчатых колес, которые закаливают в штампах, биение конуса вершин зубьев и поверхности прижимного фланца Т3 до термической обработки не должно превышать 0,075 мм. Указанные поверхности в процессе закалки соприкасаются с поверхностями штампа, поэтому при
115
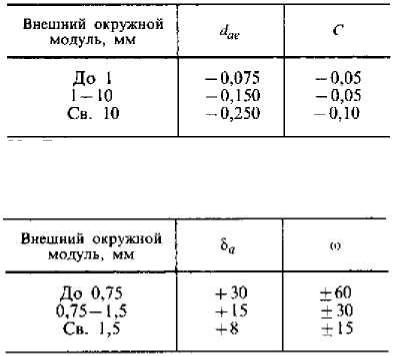
давлении незначительные погрешности могут вызвать деформацию заготовки колеса.
Кроме допусков на базы заготовок конических зубчатых колес устанавливают допуски на внешний диаметр вершин зубьев (табл. 7.3), расстояние С от базы до внешней окружности вершин зубьев, угол δа конуса вершин зубьев (табл. 7.4), угол заднего конуса ω, базовые расстояния A1 и А2, ширину зубчатого венца b и др.
Таблица 7.3 Рекомендуемые допуски на внешний диаметр и расстояние от
базы до внешней окружности вершин зубьев, мм
Таблица 7.4 Рекомендуемые допуски на угол конуса вершин и угол заднего
конуса, угловые минуты
Когда конус вершин зубьев или задний конус используют в качестве баз при механической и термической обработках, допуски на угол конуса вершин и угол заднего конуса необходимо ужесточить.
116
Нарезание конических колес с прямыми зубьями. Наи-
большее распространение в промышленности получили три метода нарезания зубьев: зубострогание, зубофрезерование и зубопротягивание.
Зубофрезерование дисковыми модульными фрезами осуществляют методом врезания с единым делением. Этим методом изготовляют зубчатые колеса невысокой точности (9—10-й степени); его в основном применяют для чернового нарезания зубьев в условиях серийного производства. Обра-
ботку проводят на зубофрезерном станке ЕЗ-40 = 320 мм; = 8 мм) с двухпозиционным поворотным столом.
Стандартные модульные фрезы не обеспечивают равномерного припуска под чистовую обработку, поэтому, когда необходим минимальный припуск, применяют специальные фрезы, спроектированные только для данного колеса. Время нарезания одной впадины зубьев 5—20 с. Скорость резания при обработке быстрорежущими фрезами чугунных колес 20—25 м/мин, стальных 25 — 30 м/мин. Черновое нарезание зубьев модульными фрезами можно проводить в делительной головке на фрезерном станке. Номер фрезы определяют по справоч-
нику в зависимости от приведенного числа зубьев |
= |
|
. |
|
|||
Зубострогание является наиболее простым и |
|
|
|
|
менее про- |
изводительным методом по сравнению с другими методами нарезания прямозубых конических колес. Благодаря универсальности и несложной конструкции режущего инструмента он получил широкое распространение в единичном и серийном производстве. Обработку зубьев проводят на зубострогальных станках методом обкатки с единичным делением. В основу процесса нарезания зубьев на этих станках положено станочное зацепление обрабатываемого колеса 3 (рис. 7.9) с воображаемым производящим колесом 4, роль зубьев которого выполняют зубострогальные резцы 1 и 2.
117
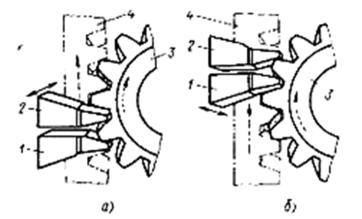
Рис. 7.9. Схемы расположения зубострогальных резцов: а) в начале резания; б) в конце резания
При обработке зубострогальные резцы, установленные в резцедержателях ползунов станка, получают возвратнопоступательное движение, необходимое для резания Совместно с обрабатываемым колесом резцам сообщают также движение обкатки, В результате последовательных огибающих резов прямолинейные режущие кромки резцов формируют октоидный профиль зубьев обрабатываемою колеса.
Конические колеса с модулем до 4 мм нарезают из целой заготовки за одну операцию методом обкатки, а с модулем свыше 4 мм за две операции — черновую и чистовую. Черновое нарезание зубьев можно выполнять методами обкатки, врезания или комбинированным, включающим врезание и обкатку.
Черновое нарезание методом врезания является наиболее простым и экономичным. При этом методе движение обкатки отсутствует, подачу в направлении режущего инструмента совершает стол с заготовкой. Черновое нарезание осуществляют обычно на 0,1—0,3 мм глубже теоретической высоты зуба, что позволяет устранить возможность касания вершинами чистовых резцов дна впадины зуба и тем самым
118
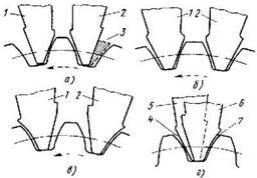
улучшить их резание. Припуск на чистовую обработку зубьев определяют в зависимости от внешнего окружного модуля.
При способе одинарного деления методом врезания стандартные резцы 1 и 2 обрабатывают противолежащие стороны одного зуба (рис. 7.10,а). Нагрузка на резцы во время резания различная. Нижний резец 2 производит обработку в сплошном металле, он нагружен значительно больше верхнего резца 1, который удаляет оставшийся во впадине металл 3. Способ одинарного деления применяют для колес с большой шириной зубчатого венца в единичном и мелкосерийном производстве.
Рис. 7.10. Схемы чернового зубострогания
При способе двойного деления верхний 1 и нижний 2 резцы одновременно обрабатывают две соседние впадины зубьев методом врезания (рис. 7.10,б). Деление производят через два зуба, Резцы имеют трапециевидный профиль, их проектируют отдельно для каждого колеса. Этот высокопроизводительный способ зубострогания применяют в серийном производстве для черновой обработки конических колес с числом зубьев более 24 и шириной зубчатого венца ≤ 0,25 , где — внешнее конусное расстояние.
Черновое нарезание зубьев с модулем до 6 мм и малым числом зубьев, профиль которых имеет значительную кривизну, целесообразно выполнять фасонными резцами (рис. 7.10,в). Форма режущей кромки резцов приближена к про-
119