
Учебное пособие 800568
.pdfтура электролита 65 , плотность тока 1 мА/см2 и время нанесения составляет 16 минут [1].
При получении пленок золь-гель методом, сначала готовят раствор ацетата меди (Cu(CH3COO)2 × H2O) в изопропиловом спирте (C3H8O) 0,1 моль и перемешивают 60 минут при 20 . Покапельно добавляется 1 мл диэтаноламина ((CH3CH2)2NH) для стабилизации раствора. Затем снова перемешивают ещѐ 20 минут. Подложками выступают, предварительно очищенные, предметные стекла. Плѐнка наносится центрифугированием при 1500 об/мин. Далее 10 минут идет процесс сушки при температуре 250 и снова наносится пленка. Процесс повторяется до тех пор, пока не будет получено 8 слоев пленки. Последним этапом метода является отжиг образцов группами. Он происходит в квазизамкнутом объѐме при 300, 400,
500, 600 [2].
В методе спрей-пиролиза подложкой выступает так же предметное стекло, которое нагревают до 340 с помощью ИК керамического нагревательного элемента. Для создания аэрозоля был использован аэрограф OPHIR AC004A, сопло которого имеет диаметр 0,3 мм. Однако, для аэрографа необходимо давление воздуха, с обеспечением которого, помог безмасляный поршневой компрессор
AS186.
Синтезируются пленки из водного раствора хлорида меди (CuCl2 × 2H2O), молярное содержание меди в котором составляет 0,1 M. В качестве растворителя выступает дистиллированная вода объемом 200 мл. Далее, используя магнитную мешалку IKA RH basic 2, перемешиваем растворы полчаса при комнатной температуре. Последним этапом является изотермический отжиг длительностью 3 часа при температуре 500 .
Толщина тонких пленок измерялась на интерференционном микроскопе МИИ-4.
Удельное сопротивление пленок измерялось четырехзондовым методом.
С помощью спектрофотометра СПЕКС ССП-715-М были исследованы спектры пропускания и поглощения пленок CuOx.
На основе измерения зависимости пропускания T от длины волны был рассчитан коэффициент поглощения α. Далее по имеющимся данным была построена зависимость (αhν)2 от hν. Спектры пропускания и поглощения пленок CuOx, изготовленных
160

методом электрохимического осаждения, в координатах T(λ) и (αhν)2 = f(hν) представлены на рисунке 1 [3].
Пленки CuOx, изготовленные методом электрохимического осаждения, имеют параметры, приведенные в табл. 1 [1].
Пленки CuOx, изготовленные золь-гель методом, имеют параметры, приведенные в табл. 2 [2].
Рис. 1. Спектры пропускания и поглощения пленок CuOx, изготовленных методом электрохимического осаждения
Таблица 1 Электрофизические параметры пленок CuOx, изготовленных
методом электрохимического осаждения
Ширина |
Удельное |
Прозрачность, |
Коэффициент |
Толщина, |
запрещенной |
сопротивление, |
% |
поглощения, |
мкм |
зоны, эВ |
Ом×см |
|
см-1 |
|
2,1 |
8,1×106 |
1,5 |
76412 |
0,67 |
|
|
|
|
|
Таблица 2 |
Электрофизические параметры пленок CuOx, изготовленных |
|||||
|
|
золь-гель методом |
|
|
|
Т, |
Без отжи- |
300 |
400 |
500 |
600 |
|
га |
|
|
|
|
1 |
2 |
3 |
4 |
5 |
6 |
ρ, Ом∙см |
355,5 |
352,1 |
19,3 |
35,8 |
271,3 |
Eg, эВ |
2,75 |
2,7 |
2,65 |
2,8 |
3,25 |
Т, % |
43,5 |
33 |
32,35 |
30 |
55 |
α, см-1 |
32738 |
44000 |
34477 |
39218 |
11791 |
161
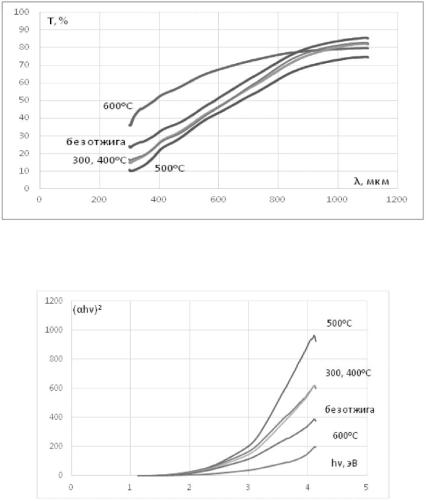
На рис. 2 приведены спектры пропускания тонких пленок CuOx, изготовленных золь-гель методом, а на рис. 3 - их спектры поглощения.
Рис. 2. Спектры пропускания тонких пленок CuOх, изготовленных золь-гель методом
Рис. 3. Спектры поглощения пленок CuOх, изготовленных золь-гель методом
162

Спектры пропускания пленок, изготовленных методом спрейпиролиза, приведены на рис. 4, а на рис. 5 изображены спектры поглощения.
Рис. 4. Спектры пропускания тонких пленок CuOх, изготовленных методом спрей-пиролиза
Рис. 5. Спектры поглощения пленок CuOх, изготовленных методом спрей-пиролиза
163
Установлено, что пленки, изготовленные методом электрохимического осаждения, имеют пропускание более 1,5 %, золь-гель методом - более 50 %, а методом спрей-пиролиза – более 25 %.
Пленки, изготовленные электрохимическим осаждением, имеют удельное сопротивление 8,1×106 Ом×см, золь-гель методом - 206 Ом×см, методом спрей-пиролиза - 3,29×106 Ом×см.
Стоит акцентировать внимание, что в зависимости от способа синтеза пленок, значения проводимости, концентрации и подвижности основных носителей варьируются в широком диапазоне.
Литература
1.Рембеза С.И. Исследование свойств пленок оксида меди
(I)на поверхности ITO, синтезированных методом электрохимического осаждения / С.И. Рембеза, Д.С. Пермяков // Микро- и нанотехнологии в электронике. – 2019. Материалы XI Международной научно-технической конференции. - С. 423 – 426.
2.Пермяков Д.С. Исследование влияния температуры отжига на свойства пленок CuO, полученных золь-гель методом / Д.С. Пермяков, А.О. Левченко, А.А Карионова. // Воронеж: изд-во ВГТУ. - 2019. 59 научно-техническая конференция профессорскопреподавательского состава, сотрудников, аспирантов и студентов ВГТУ: тез. докл. – 13 с.
3.Юлчиев Ш.Х. Использование пиролитических металлооксидных пленок для изготовления фотоэлектрических преобразователей энергии / Ш.Х. Юлчиев, С.И. Рембеза, В.Е. Полковников, Д.С. Пермяков, М.А Белых // Вестник ВГТУ. – 2019. Том 15. № 5. -
С. 72 - 77.
Воронежский государственный технический университет
164
УДК 621.382
Т.Г. Меньшикова, П.С. Панов
ОПТИМИЗАЦИЯ ПРОЦЕССА РАЗВАРКИ КОНТАКТОВ ПРИ ИЗГОТОВЛЕНИИ ИС
Целью данной работы является исследование стабильности параметров ультразвуковой сварки методом «клин – клин» алюминиевой проволоки, влияния плазменной обработки на разрывные показатели и качественные характеристики сварного соединения без участия обработки и с использованием плазмы.
В настоящее время в современных СБИС и полупроводниковых приборах, у которых размер контактных площадок достиг микронных размеров, процесс присоединения проволочных выводов, контактных площадок корпуса, с контактными площадками кристалла занимает одну из самых сложных и трудоемких операций.
Прогресс в развитии методов формирования межсоединений позволил существенно снизить трудоемкость операций и добиться заметных успехов на пути к их полной автоматизации. Однако трудоемкость операции формирования межсоединений остаѐтся определяющей в процессе производства изделий микроэлектроники и для разных типов приборов составляет от 30 до 60 % всей трудоемкости сборки. При этом на долю разрушения межсоединений приходится и значительный процент отказов изделий при эксплуатации. Нужно учитывать все нюансы при формировании петли, подбора параметров и контроли качества разварки.
Одной из причин брака является загрязнение поверхностей корпуса и кристалла органическими и неорганическими частицами. Возникновение этих загрязняющих веществ возможно при наличии человеческого фактора, так же и при технологическом процессе при производстве ИС. Для устранения загрязнений с покрытия был разработан метод очистки в низкотемпературной плазме в смеси газов 90 % Ar + 10 % H2. Подложка помещается в камеру с плазмой, бомбардируя заряженными частицами, удаляется с нее загрязнения, а
165

система откачки удаляет их из камеры. Вторым плюсом данного метода является активация поверхности. После обработки подложки в плазме наблюдается улучшение адгезионных свойств что характеризуется уменьшением равновесного угла смачивания θ. Повышение адгезионных свойств подложки так же подтверждается экспериментальным путем при проверке методом сдвига кристалла и отрыва проволочного соединения.
Для обработки образцов применяется низкотемпературная, газоразрядная плазма, в установке плазменной очистки AP1000 при режимах, указанных в таблице.
Технологические режимы плазменной обработки
Было протестировано 5 одинаковых образцов со смонтированным кристаллом в металлокерамический корпус с золотым покрытием 3 - 5 мкм. Образцы изделий разваривались сначала до плазменной обработки, а потом после нее. На рисунке указаны результаты испытания проволочного вывода на отрыв.
166

|
Средние значения параметров на отрыв |
|
||||||||
|
|
проволочного вывода |
|
|
|
|||||
|
16,50 |
|
|
|
|
|
|
|
|
|
. |
16,00 |
|
|
|
|
|
|
|
|
|
гр |
|
|
|
|
|
|
|
|
|
|
15,50 |
|
|
|
|
|
|
|
|
|
|
, |
15,00 |
|
|
|
|
|
|
|
|
|
отрыв |
|
|
|
|
|
|
|
|
|
|
14,50 |
|
|
|
|
|
|
|
|
|
|
14,00 |
|
|
|
|
|
|
|
|
|
|
13,50 |
|
|
|
|
|
|
|
|
|
|
13,00 |
|
|
|
|
|
|
|
|
|
|
на |
12,50 |
|
|
|
|
|
|
|
|
|
12,00 |
|
|
|
|
|
|
|
|
|
|
усилие |
11,50 |
|
|
|
|
|
|
|
|
|
11,00 |
|
|
|
|
|
|
|
|
|
|
10,50 |
|
|
|
|
|
|
|
|
|
|
10,00 |
|
|
|
|
|
|
|
|
|
|
9,50 |
|
|
|
|
|
|
|
|
|
|
|
|
|
|
|
|
|
|
|
|
|
|
9,00 |
|
|
|
|
|
|
|
|
|
|
1 |
2 |
3 |
4 |
5 |
6 |
7 |
8 |
9 |
10 |
|
|
|
|
|
Точка отрыва |
|
|
|
|
|
|
|
|
Кристалл до |
|
Кристалл после |
|
|
|
||
|
|
|
Траверса до |
|
Траверса после |
|
|
|
||
|
Результаты испытания проволочного вывода на отрыв |
|
По результатам исследования влияния плазменной обработки на прочность проволочных выводов можно сделать вывод, что действительно улучшилась прочность проволочных соединений на кристалле и на траверсе. В среднем на кристалле усилие на отрыв увеличилось на 14,3 % (1,97 гр.), тогда как на траверсе на 19,5 % (2,63 гр.), что говорит о том, что плазменная обработка лучше повлияла на пористость золотого покрытия траверс, тогда как ее влияние на алюминиевую контактную площадку кристалла было менее значительно. Так же стоит заметить, что при тестировании на отрыв, без плазменной обработки изделия, точка практически целиком отслаивалась с алюминиевой поверхности контактной площадки, а после проведения плазменной обработки проволочный вывод рвался в шейке сварного соединения.
Воронежский государственный технический университет
167

УДК 621.382
Р.С. Гусев, С.А. Акулинин
АНАЛИЗ ИЗМЕРИТЕЛЬНОЙ СИСТЕМЫ РЕКО-8301 ДЛЯ ИЗМЕРЕНИЯ ПАРАМЕТРОВ МОДУЛЕЙ CУПЕРКОНДЕНCАТОРОВ
В работе анализируется метод измерения электрической ѐмкости (С) и эквивалентного последовательного сопротивления (ESR) модулей cуперконденсаторов и метод оценки ресурсов на основе циклов заряда-разряда.
Источники вторичного электропитания (ИЭП) на сегодняшний день играют очень важную роль в обеспечении работы радиоэлектронной аппаратуры, вычислительной техники, систем управления промышленным оборудованием, в том числе на железных дорогах. К числу основных характеристик ИЭП можно отнести электрические показатели, эффективность функционирования, масса - габаритные параметры, надежность и стоимость. Они служат для бесперебойного электропитания радиоэлектронных узлов и блоков аппаратуры, систем промышленной автоматики [1,2].
Стандартным методом определения ресурса модулей СК является применение циклов заряда - разряда СК. Этот метод применен в измерительных системах серии РЕК0-8301 и заключается в том, что сначала полностью заряжаем СК до максимального допустимого напряжения, а затем разряжаем до минимального значения напряжения. Количество циклов задаѐтся пользователем. Важно отметить, что в процессе испытаний автоматизированная измерительная система серии РЕК0-8301 производит измерения емкости и эквивалентного последовательного сопротивления модулей суперконденсаторов [3]. Технические данные автоматизированных измери-
168

тельных систем серии РЕК0-8301 для определения ресурса соответствует требованиям, установленным в IEC 62193-2 (таблица).
Основные технические характеристики автоматизированных измерительных систем серии РЕК0-8301
169