
Учебное пособие 800417
.pdfможностью одновременного управления по 2-м координатам апроксимируют траекторию обработки последовательностью отрезков определенной длины, которая определяется возможностью интерполятора СЧПУ. При отсутствии поддержки круговой или винтовой интерполяции аппроксимацией криволинейной траектории занимается постпроцессор. На производительность обработки оказывает влияние размер буфера СЧПУ. Для передачи УП, размер которых превышает размер свободной памяти СЧПУ, используется режим Dynamic Numeric Control (DNC). В этом режиме программа обработки не записывается в память системы ЧПУ, а выполняется прямо с компьютера. Система ЧПУ имеет специальный программный буфер, в который приходит часть программы. Как только этот буфер заполняется, система посылает сигнал на компьютер, чтобы тот прекратил передавать данные. В это время СЧПУ станка выполняет кадры УП, находящиеся в буфере. Когда буфер освобождается, система ЧПУ посылает новый сигнал на ПК, который разрешает дальнейшую передачу данных. Этот процесс продолжается до полного выполнения УП. Для работы в режиме DNC необходимо, чтобы СЧПУ станка было соответствующим образом подготовлено производителем, а на персональном компьютере находилось программное обеспечение с поддержкой этого режима. При малой длине отрезков резко увеличивается размер управляющей программы и при переполнении буфера происходит остановка наполнения буфера до тех пор, пока не будут отработаны кадры управляющей программы (УП) из буфера. Отсутствие встроенной функции Look Ahead негативно сказывается на производительности обработки. Назначение блока Look Ahead опережающего просмотра состоит в определении условного времени отработки кадра в циклах интерполятора для последующей коррекции контурной скорости и анализе в каждом кадре базовых параметров движения (вектора контурной скорости в начале и конце кадра, скорости по дополнительным координатным осям, пути в основной системе координат, радиуса кривизны траектории движения). В результате своей работы блок Look Ahead определяет скорость в конце кадра и новое значение контурной скорости подачи. СЧПУ с функцией Look Ahead анализирует траекторию и позволяет плавно изменять подачу в процессе резания. Даже при наличии данной функции при малом размере буфера наблюдается снижение производительности из-за ограниченного количества кадров УП, анализируемых СЧПУ.
61
Использование дополнительной поворотной оси приводит к значительному расширению технологических возможностей станка. Также появляется возможность изменить схему формообразования. Дополнительная поворотная ось C позволяет обрабатывать криволинейные профили посредством согласования перемещения рабочих органов по осям X, Y и поворотной оси C. Реализация данного согласования ложится не только на постпроцессор, но и на микроконтроллер, управляющий поворотной осью. Постпроцессор представляет собой либо отдельный, либо интегрированный в систему
Computer-Aided Manufacturing (CAM) программный модуль, основ-
ной задачей которого является преобразование разработанной траектории перемещения инструмента относительно заготовки в УП для конкретного станка с ЧПУ, основываясь на особенностях его кинематики. Исходной информацией для получения программы обработки на станке с ЧПУ является геометрия детали определенная на проектно-конструкторском этапе. Затем при создании управляющей программы для станка с ЧПУ технолог-программист пользуется CAM-системой. Система генерирует файл, содержащий информацию о положении, траектории инструмента, режимы резания и другие технологические параметры. Далее вступает в работу постпроцессор, который обрабатывает эти данные и формирует управляющую программу для определенного станка. В данном случае к 3-м управляемым координатам, 2 из которых могут управляться одновременно, добавляется координата, отвечающая за поворот стола. За перемещение РО станка по дуге отвечает круговая интерполяция вызываемая подготовительными функциями G02 или G03. При использовании дополнительной поворотной оси круговая интерполяция заменяется на линейную в плоскости обработки и поворот заготовки на определенный угол. При расфрезеровывании отверстий, радиус которых не превышает диаметр инструмента и их ось совпадает с осью вращения стола, инструмент совершает движение по винтовой линии.
Управление поворотным столом осуществляется при помощи микроконтроллера ATmega328. К нему подключается драйвер шагового двигателя (ШД), назначением которого является преобразование команд контроллера шагового двигателя в импульсы, подаваемые на обмотки ШД и их усиление. ШД - это синхронный бесщёточный электродвигатель с несколькими обмотками, в котором ток, подаваемый в одну из обмоток статора, вызывает фиксацию ротора.
62
Последовательная активация обмоток двигателя вызывает дискретные угловые перемещения ротора.
Передача данных на микроконтроллер осуществляется через виртуальный COM порт. Такой режим управления позволяет подключать дополнительные программируемые периферийные устройства. Использование дополнительной поворотной оси позволяет сократить основное время и снизить погрешности формы при обработке деталей сложной формы, особенно на трех осевых фрезерных станках с возможностью одновременного управления только по двум координатам.
Воронежский государственный технический университет
УДК 621.9.06
Д.М. Черных
ИНФОРМАЦИОННО-ИЗМЕРИТЕЛЬНАЯ СИСТЕМА ДЛЯ КОНТРОЛЯ ПРОЦЕССА ФРЕЗЕРОВАНИЯ
В данной статье представлена схема информационно-измерительной системы для оценки совокупности вибрационных процессов, возникающих в процессе резания
Для исследования процесса резания разработана информаци- онно-измерительная система, структурная схема которой представлена на рис. 1.
Система датчиков (Д1… Д4) и (Т1… Т3) воспринимает измеряемые величины и создает на выходе электрические сигналы u1…u7, зависящие от значений измеряемых величин x1(t)...x7(t) и совокупности помех. Принцип действия датчиков, их конструкцию и предельную чувствительность определяет взаимодействие чувствительного элемента датчика с объектом. Выходные аналоговые сигналы датчиков разного типа могут иметь значительно отличающиеся уровни напряжений и характеризоваться разными частотными диапазонами.
Для измерения сил резания используется система тензометрических датчиков, позволяющих измерить степень деформации, вызываемой воздействием сил резания. Работу тензометрического датчика определяет тензорезистор, сопротивление которого изменяется в зависимости от его деформации. Тензометрические датчики, используе-
63
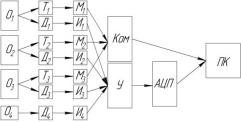
мые в экспериментальной установке, состоят из тензорезисторов МТ-EA-06-3.18AD-120 подключенных по мостовой схеме.
Рис. 1 Структурная схема информационно-измерительной системы О – объект исследования, О1 – шпиндельный узел, О2 – полугайка, О3 - полугайка, О4 – стол, Т1, Т2, Т3 – тензометрический датчики на базе МТ-EA-06-3.18AD-120, Д1, Д2, Д3 – пьезоэлектрические акселерометры 356А34, , Д4 – пьезоэлектрический акселерометр 356А61, И1, И2, И3, И4 – электронные интеграторы A5970AD, М1, М2, М3 – измерительные модули ZET 7111, У – усилитель АP5200- 8-19”, АЦП – аналого – цифровой преобразователь LTR24,Ком –
коммутатор ZET 7174, ПК – персональный компьютер
Тензодатчики, установленные на полугайках шариковинтовых передач, служат для измерения соответственно составляющих сил резания по осям X, Y, а установленный на передней опоре шпинделя – по оси Z. В начальном состоянии, мост состоящий из тензорезисторов уравновешен. При изменении сопротивления тензорезистора, мост разбалансируется, появляется разность потенциалов (напряжение), пропорционально изменяющийся степени деформации тензорезистора. Для устранения ошибок измерения сил резания, вызванных температурными деформациями передней опоры шпиндельного узла, для тензометрического датчика необходимо использовать мостовую схему установки тезорезисторов с температурной компенсацией.
Выход тензометрических мостовых схем представлен в единицах деформации (με) или в выходном напряжении (мВ/В или μВ/В) относительно напряжения питания моста. Эти величины соотносятся согласно следующей формуле:
e0 (E/4) KS 0 ,
где KS – K-фактор;
64
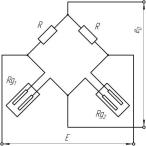
0 – деформация;
E – питание моста;
e0 – выходное напряжение.
Если питание моста E 1В и К-фактор KS 2 , то:
2e0 0 .
Рис. 2. Мостовая схема соединения тензорезисторов МТ-EA-06-3.18AD-120 с температурной компенсацией.
R – постоянное сопротивление, Rg1 – активный тензорезистор, Rg2 – компенсирующий
Таким образом выход по деформации будет в 2 раза больше, чем выходное напряжение моста.
Сигнал с тензодатчика поступает в измерительный модуль ZET 7111 Tensometer-CAN. Измерительный модуль преобразует входной сигнал (напряжение) в значение измеряемой величины и передает результаты в цифровом виде. Совокупность модулей ZET 7111 образуют измерительную сеть на базе интеллектуальных датчиков, которая объединяется при помощи ZET 7174, подключенного к ПК при помощи USB интерфейса.
Для оценки совокупности вибрационных процессов, возникающих в процессе резания, электромеханические датчики устанавливаются на наружное кольцо передней опоры шпинделя, на полугайки шарико-винтовых передач приводов подач и на стол. Использование пьезоэлектрических акселерометров, преобразующих механические колебания в электрические сигналы, позволило проводить высокоточные измерения и анализ механических колебаний при помощи измерительных приборов. Линию действия датчика определяют по отношению к осям опоры (например, в осевом или ради-
65
альном направлении). Измеряемой величиной является радиальная или осевая составляющая вибрации наружного кольца подшипника. В качестве измеряемого по умолчанию параметра используется
среднее квадратическое значение виброскорости, v (мкм/с). Сравнение метрологических и эксплуатационных свойств датчиков виброскорости и акселерометров показывает, что у акселерометров они выше почти по всем показателям. Поэтому для измерения виброскорости наиболее часто используют акселерометры с последующим интегрированием сигнала.
Измерение вибраций на полугайке происходит по осям X, Y и Z при помощи акселерометра 356А34. Благодаря наличию трех независимых чувствительных элементов, обеспечивается одновременное измерение вибраций и ударных взаимодействий в трех ортогональных направлениях. Измерение виброскорости на столе выполняется при помощи акселерометра 356А61.
Трехкомпонентные устройства используются для определения объемного фазового портрета виброскоростей на объекте в точке крепления. Данные устройства сочетают высокие значения собственной частоты, ударной стойкости и осевой чувствительности со встроенным предусилителем и низким собственным шумом. Большинство предусилителей обеспечивает не только преобразование импеданса, а также усиление и формирование отдаваемого акселерометром электрического сигнала.
Пьезоэлектрические датчики вибрации на собственной резонансной частоте имеют существенный подъем амплитудночастотной характеристики. Превышение резонансного уровня над уровнем рабочего участка может превышать 50 дБ. При наличии входных воздействий на датчик составляющих с частотами, близкими к резонансным, или при ударных воздействиях формируются сигналы высокой амплитуды за счет подъема амплитудночастотной характеристики на резонансе, который вызывает перегрузку входного усилителя, при которой этот усилитель попадает в состояние насыщения, что нарушает правильную работу обратной связи этого усилителя.
Все электромеханические датчики для повышения достоверности функционирования и расширения динамического диапазона измеряемых параметров подключены к усилителю АP5200-8- 19”. Промежуточным звеном между акселерометром и усилителем являются электронные интеграторы. Их использование позволяет
66
получать из сигналов акселерометров, которые отдают сигнал пропорциональный ускорению, сигналы виброскорости и виброперемещения. Усилитель имеет калиброванный и регулируемый коэффициент усиления и усиливает сигнал до нужного для измерительной, анализирующей или регистрирующей аппаратуры уровня.
В свою очередь усилитель подключается к соответствующему ана- лого-цифровому преобразователю, который выполняет сравнение входной величины с некоторой базовой величиной (как правило, с опорным напряжением).
На вход АЦП подается нормированное аналоговое напряжение un(t), предварительно усиленное до требуемого уровня и с ограниченным в высокочастотном диапазоне спектром для уменьшения погрешности дискретизации.
В данном случае используются сигма-дельта АЦП LTR24. Выбор сигма-дельта АЦП обусловлен высокой точностью в связи с крайне низким уровнем собственного шума. Данный АЦП представляет собой систему с обратной связью, основанную на том, что входное напряжение сравнивается со значением напряжения, накопленным интегратором. В зависимости от результата сравнения на вход интегратора подаются импульсы положительной или отрицательной полярности. В результате на выходе компаратора получаем совокупность единичных сигналов.
Автоматизация процесса регистрации, обработки и сохранения измерительной информации приводит к увеличению точности и достоверности экспериментальных данных. Использование программного средства ZETLAB BASE позволяет осуществить многоцелевой анализ процессов, в частности:
1.Анализ сигналов. (Узкополосная спектральная обработка сигналов, поступающих с модулей АЦП. Просмотр различных характеристик: спектров, спектрограмм и 3D-спектрограмм.)
2.Измерение электрических параметров сигнала. (Измерение параметров сигналов, поступающих на входные каналы модулей АЦП.)
2.1. Частотомер. (Программа предназначена для измерения частоты сигнала, поступающего на входные каналы модулей АЦП и анализаторов спектра. На индикаторе отображается измеряемое значение частоты и время периода сигнала, соответствующее измеряемой частоте. Имеется возможность изменения времени
67
усреднения отображаемого значения (0,1; 1 или 10 с) и выбора необходимого канала модуля АЦП и анализатора спектра.
2.2. Виртуальный фазометр. (Программа фазометра предназначена для измерения разности фаз двух сигналов, поступающих на входные каналы анализаторов спектра. В верхней строке индикатора отображается текущее значение разности фаз в градусах, в нижней - разность фаз в радианах. Имеется возможность изменения усреднения отображаемого значения (0,1 или 1 с) и выбора необходимых каналов анализаторов спектра).
3. Визуализация сигналов.( Отображение временных реализаций сигналов в плоскостях и объеме, построение параметрических зависимостей двух или трех величин, отображение и редактирование записанных данных в графическом и табличном виде.)
3.1.Многоканальный осциллограф. (Программа отображения формы сигналов по нескольким каналам)
3.2.XYZ-осциллограф. (Программа отображения параметрической зависимости 2-х или 3-х сигналов.)
3.3.XY-плоттер результатов измерений сигналов. Привлекательность программного комплекса ZETLAB за-
ключается в возможности обмена данными и моделями с распространенными программами Excel, математическим пакетом MathCAD и программной средой Lab View. Это предоставляет возможность обработки и представления данных с использованием математических средств MathCAD. Работа совместно с Lab View позволяет строить совместные алгоритмы обработки данных и проектировать управляющие устройства.
Совместно с персональной ЭВМ, оснащенной специализированным программным обеспечением, система сбора данных образует информационно-измерительную систему (ИИС). ИИС — это многоканальный измерительный прибор с широкими возможностями обработки и анализа данных. На основе ИИС могут быть построены различные автоматизированные системы управления (АСУ), среди которых: информационно-логические комплексы, ин- формационно-вычислительные комплексы, информационнодиагностические комплексы и информационно-контролирующие системы.
Воронежский государственный технический университет
68
УДК 621.9.06
Д.М. Черных, М.В. Крупенин
ИСПОЛЬЗОВАНИЕ НЕЙРОННЫХ СЕТЕЙ В ГРУППОВОМ ПРОИЗВОДСТВЕ
В данной статье предложен новый подход к групповой обработке, основанный на использовании нейронных сетей на базе самоорганизующихся карт Кохоненна
Одной из основных тенденций развития машиностроения является усложнение конструкции объектов производства с повышением требований к времени переналадки оборудования для выпуска новой продукции. Успешное выполнение поставленной задачи невозможно без использования прогрессивных технологий обработки и обновления производственных фондов на базе станков с числовым программным управлением. Одним из прогрессивных методов оптимизации цикла технологической подготовки производства является использование метода групповой обработки, что позволяет значительно снизить трудоемкость обработки.
Групповое производство - это прогрессивная в техникоэкономическом отношении система организации дискретных производственных процессов, технологической составляющей которой является групповая унифицированная форма организации технологических процессов. В основе групповой обработки должна лежать классификация объектов производства с унификацией технологических решений, что позволяет автоматизировать ТПП.
Одной из основных задач, связанных с автоматизацией ТПП является интеграция группового производства в используемую PDM систему предприятия. Это позволит создать единое информационное пространство, объединяющее процессы управления инженерными данными, информацией об изделии, технической информацией. В данном случае необходимо разработать информационные модели для технологической подготовки группового производства.
Для начала необходимо и возможно решить задачу кластеризации, т.е. статистической процедуры, выполняющей сбор данных, содержащих информацию о выборке объектов, и затем упорядочивающая объекты в сравнительно однородные группы. В качестве методики группирования деталей для их обработки по групповой технологии на станках с ЧПУ, основанной на нейросетях, целесооб-
69
разно использовать самоорганизующиеся карты Кохонена. Они представляют собой нейронную сеть с обучением без учителя, выполняющую задачу визуализации и кластеризации.
Самоорганизующиеся карты Кохонена используются для решения таких задач, как моделирование, прогнозирование, выявление наборов независимых признаков, сжатие информации, а также для поиска закономерностей в больших массивах данных. Наиболее часто описываемый алгоритм применяется для кластеризации данных.
Самоорганизующаяся карта состоит из компонентов, называемых узлами или нейронами. Каждый из узлов описывается двумя векторами. Изначально известна размерность входных данных, по ней некоторым образом строится первоначальный вариант карты. В процессе обучения векторы веса узлов приближаются к входным данным.
Результатом работы нейронной сети будет являться совокупность кластеров, в которые будут объединены объекты производства.
Для каждого кластера необходимо определить паттерн обработки, основанный на пуле объектов обработки, состоящих из определенной совокупности поверхностей, характерных для данного кластера. Каждому объекту обработки будет соотнесена определенная стратегия обработки с указанием наиболее подходящего инструмента и режимных параметров, исходя из информации полученной из PDM системы. Основываясь на этих данных будут определены оптимальные схемы базирования и оборудование.
Воронежский государственный технический университет
70