
Учебное пособие 800417
.pdf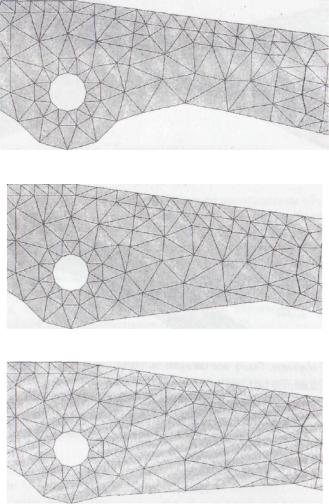
а
б
в
Рис. 5. Фрагменты изменения конечнозлементной сетки модели рычага в зоне перехода:
а ~ базовая конструкция; б - вариант 1; в -вариант 2
51
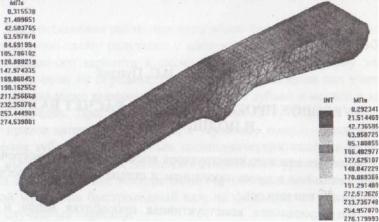
Рис. 6. Эпюра распределения интенсивности напряжений в рычаге, изготовленном из различных материалов:
слева - ВТ22; справа - сталь
Проведенные исследования показали, что конструкция рычага удовлетворяет условиям прочности, но имеет резервы для снижения концентрации напряжений. Численный эксперимент выявил характер распределения напряжений в рычаге. Незначительным изменением конструкции было достигнуто значительное снижение градиентов напряжений рычага привода багажного люка.
Используемая методика позволяет проектировать детали механизмов, обладающих наиболее рациональным распределением материала в конструкции и соответственно обладающих наименьшим весом.
Литература
1. Зенкевич О.С. Метод конечных элементов в технике. - М.:
Мир,1975.- 541 с.
2. Галлагер Р. Метод конечных элементов. Основы. - М.:
Мир,1984.-428с.
Воронежский государственный технический университет
52
УДК 621.81(075)
В.А. Нилов, А.В. Демидов, О.К. Битюцких
СОВРЕМЕННЫЕКОНСТРУКЦИИ ПОДШИПНИКОВ СКОЛЬЖЕНИЯ
Подшипник — это изделие, являющееся частью опоры, которое поддерживает вал, ось или иную конструкцию, фиксирует положение в пространстве, обеспечивает вращение, качание или линейное перемещение (для линейных подшипников) с наименьшим сопротивлением, воспринимает и передаёт нагрузку на другие части конструкции.
Подшипник скольжения — опора или направляющая механизма или машины, в которой трение происходит при скольжении сопряжённых поверхностей.
По направлению восприятия нагрузки различают подшипники радиальные, предназначенные для восприятия усилий, перпендикулярных к оси вала (рис. 1), и осевые (упорные) - для восприятия нагрузок, действующих вдоль оси вала. В зависимости от режима смазки подшипники скольжения делятся на гидродинамические и гидростатические, газодинамические и газостатические (роль смазки выполняет воздух или нейтральный газ), а также подшипники с твёрдой смазкой. Существует множество конструктивных типов
подшипников скольжения: самоустанавливающиеся, сегментные, самосмазывающиеся и др. [1].
Подшипники скольжения применяются:
-при ударных и вибрационных нагрузках;
-при особовысоких частотах вращения;
-для точных опор с постоянной жесткостью; -для опор с малыми радиальными размерами; -для разъемных опор;
-для особо крупных и миниатюрных опор; при работе в экс-
тремальных условиях (высокие температуры, абразивныеи агрессивные среды);
-для неответственных и редко работающих механизмов.
53
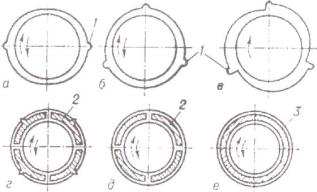
Рис. 1. - Схемы радиальных подшипников скольжения: а) - эллиптический; б) - с жёсткими секторами; в) - из смешанных секторов; г) - из секторов, образованных качающимися
вкладышами; д) - из свободных вкладышей; е) - с «плавающим» вкладышем; 1) - место подвода смазки; 2) - сектор;
3) - кольцеобразный «плавающий»вкладыш
Достоинства подшипников скольжения:
- надежно работают в высокоскоростных приводах; -способны воспринимать большие ударные и вибрационные
нагрузки; - бесшумность работы;
-сравнительно малые радиальные размеры; -разъемные подшипники допускают установку на шейки
коленчатых валов; -простота конструкции;
-для тихоходных машин могут иметь весьма простую конструкцию [2].
Недостатки подшипников скольжения:
-в процессе работы требуют постоянного надзора из-за высоких требований к смазыванию и опасности перегрева; перерыв в подаче смазочного материала ведет к выходу из строя подшипника;
-имеют сравнительно большие осевые размеры; -значительные потери на трение в период пуска и при
несовершенной смазке; - большой расход смазочного материала.
54
В области турбомашиностроения в последнее время все большее применение в качестве опор высокоскоростных роторов находят конические опоры скольжения, позволяющие одновременно воспринимать как радиальную, так и осевую нагрузку [3...5]. Наибольшее распространение получили конические гладкие гидродинамические подшипники (ГДП), обеспечивающие необходимую несущую способность. Однако достаточно часто такие опоры скольжения не обеспечивают необходимой устойчивости движения ротора. Решение данной проблемы было найдено в виде использования конструкции конического многоклинового гидродинамического подшипника (МГДП) [6]. Совмещение в одной конструкции двух различных типов опор скольжения позволяет получить новый тип гибридного подшипника, совмещающего в своей конструкции гладкую и многоклиновую части. Преимущество данного типа подшипника заключается в следующем: гладкая часть опоры обеспечивает большую грузоподъемность, тогда как многоклиновая - большую устойчивость. Использование таких типов опор необходимо в случаях, если требуется обеспечить большую грузоподъемность при сохранении устойчивого положения роторов высокоскоростных турбомашин. Это особенно актуально для различных высокоскоростных турбоагрегатов.
Рассматриваемый подшипник представляет гибридную опору, состоящую из конических гладкой и многоклиновой частей (рисунок 2). Длина гибридной опоры определяется из суммы длин гладкой и многоклиновой частей.
Смазка является одним из основных условий надёжной работы подшипника и обеспечивает: низкое трение, разделение подвижных частей, теплоотвод, защиту от вредного воздействия окружающей среды и может быть: жидкой (минеральные и синтетические масла, вода для не металлических подшипников), пластичной (на основе литиевого мыла и кальция сульфоната и др.), твёрдой (графит, дисульфид молибдена и др.) и газообразной (различные инертные газы, азот и др.). Наилучшие эксплуатационные свойства демонстрируют пористые самосмазывающиеся подшипники, изготовленные методом порошковой металлургии. При работе пористый самосмазывающийся подшипник, пропитанный маслом, нагревается и выделяет смазку из пор на рабочую скользящую поверхность, а в состоянии покоя остывает и впитывает смазку обратнов поры.
55
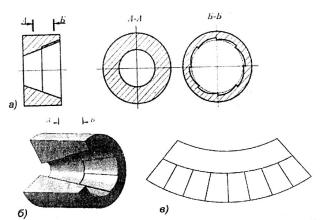
Рис. 2. Конический гибридный гидродинамический подшипник: а) расчетная схема; б) 3D – модель; в) развертка опорной поверхности
В настоящее время исследования в области расчета и проектирования конических опор жидкостного трения основаны на ряде допущений: поток смазочного материала полагается ламинарным и изотермическим, свойства смазочного материала (плотность, вязкость и др.) считаются постоянными и т.п. Вместе с тем, в ряде случаев, при проектировании опорных узлов высокоскоростных турбомашин возникает необходимость учета упомянутых явлений. Кроме того, в процессе течения смазки в гидравлических каналах опор возможно вскипание /кавитация смазочного материала и его переход в двухфазное парожидкостное состояние.
Несущая способность конических гибридных ГДП, смазываемых водой, возрастает с увеличением угловой скорости и относительного радиального эксцентриситета и уменьшением радиального зазора, угла конусности и температуры смазочного материала.
Литература
1.http://bse.sci-lib.com
2.http:www.polyinfo.ru
3.Токарь И .Я. Проектирование и расчет опор трения. М: Машиностроение, 1971. - 168 с.
4.Корнеев А.Ю., Савин Л.А., Соломин О.В. Математическая
56
модель неизотермического турбулентного течения смазочного материала в конических опорах жидкостного трения // Вестник машиностроения, 2005. - № 7. - С. 37 - 42.
5.Корнеев А.Ю., Савин Л.А., Соломин О.В. Расчет статических характеристик конических опор жидкостного трения // Вестник машиностроения, 2006. - № 12. - С. 37-41.
6.Корнеев А.Ю., Савин Л.А., Соломин О.В. Конические подшипники жидкостного трения: монография. М: Машиностроение - 2008. -172 с.
Воронежский государственный технический университет
УДК 621.9.06.529
А.В. Бесько, С.Н. Яценко, И.В. Кононенко
ОБЕСПЕЧЕНИЕ КАЧЕСТВА ШЛИФОВАННЫХ ПОВЕРХНОСТЕЙ ЗА СЧЕТ ПРИМЕНЕНИЯ СМАЗОЧНО-ОХЛАЖДАЮЩИХ ТЕХНОЛОГИЧЕСКИХ
СРЕД
Применение смазывающе-охлаждающих технологических сред является одним из наиболее эффективных методов тепловой защиты обрабатываемых поверхностей и способствует достижению заданного качества обработки
Качество поверхности, обработанной шлифованием, предопределяется тепловыми явлениями, возникающими в зоне обработки. Механизм формирования поверхностного слоя можно представить следующим образом: поверхностный слой обрабатываемой детали, составляющий припуск на обработку, подлежит удалению, которое осуществляется абразивными зернами, находящимися в контакте с обрабатываемой поверхностью. Этот процесс сопровождается трением зерен по контактирующей поверхности обрабатываемого материала. Именно поэтому процесс абразивной обработки сопровождается высокими температурами, соизмеримыми с температурой плавления обрабатываемого материала, а в зоне обработки возникает жидкая фаза, и протекают процессы, известные как течение Куэтта. Учитывая, что шлифование является финишным методом обработки и предопределяет наследственность детали, следует обратить особое внимание на уменьшение тепловыделений в зоне обработки.
57
Одним из наиболее эффективных методов тепловой защиты обрабатываемой поверхности в зоне обработки является применение смазывающе-охлаждающих технологических сред (СОТС). Путем их рационального использования можно значительно уменьшить силы трения в контакте "шлифовальный круг - обрабатываемая деталь", а также соответствующие тепловыделения, интенсифицировать отвод тепла, улучшить удаление стружки и отходов шлифования из зоны резания и с рабочих органов станка. В результате можно отсрочить затупление, засаливание и износ шлифовального круга, повысить его работоспособность, обеспечить значительное повышение производительности обработки и улучшение качества деталей.
Применение смазывающе-охлаждающих технологических сред является эффективным способом защиты поверхности заготовки в зоне обработки от тепловых деформаций, влияющих на качество деталей и стойкость режущего инструмента. Высокая эффективность использования смазочно-охлаждающих технологических сред в зоне шлифования в системе «инструмент-деталь» обуславливает повышенное внимание многочисленных исследователей к этой проблеме. В значительной степени вопросы охлаждения в зоне контакта обрабатываемой поверхности и инструмента можно решать при использовании СОТС. Однако эта система реализуется в настоящее время в неполной мере из-за отсутствия научных основ определения состава охлаждающей жидкости с учетом кинематических и динамических условий эксплуатации при реализации конкретных технологических процессов.
Действие СОТС на систему «инструмент-деталь» в процессе обработки можно разделить на охлаждающее, смазывающее, моющее и режущее действие.
Охлаждающий эффект СОТС весьма существенен и снижает температуру резания на 150 -170 С по сравнению со шлифованием без охлаждения. Однако и смазывающее воздействие смазочноохлаждающей жидкости (СОЖ) также весьма существенно.
Жидкостьв зонуобработки подводитсянесколькими способами: 1) посредством патрубка, расположенного так, чтобы струя СОЖ непрерывно подавалась в зону шлифования и омывала поверхность деталей. Специальные заслонки патрубка предотвращают разбрызгивание смазочно-охлаждающей жидкости. Ширина заслонок и патрубка подбирается так, чтобы струя жидкости покрывала
58
всю ширину шлифовального круга. Для станков средних размеров рекомендуется подавать 15-30 и более литров СОЖ в минуту;
2)путем распыления - охлаждение туманом. Применяется метод подачи охлаждающей жидкости в виде мелких капелек. Капли, попадая на нагретую деталь и инструмент, быстро нагреваются и испаряются, отбирая у детали и инструмента очень большое количество тепла. Жидкость распыляется специальным инжекторным устройством. При таком способе охлаждения обеспечивается лучшее качество обработки поверхности, чем при подводе жидкости по патрубку. Но шум форсунки вызывает утомление рабочего, и атмосфера цеха насыщается парами, содержащими масло.
3)через поры шлифовального круга. Под действием центробежных сил жидкость проходит сквозь поры круга на периферию и разбрызгивается по радиусу круга.
Способ подвода охлаждающей жидкости через поры круга эффективен при обработке твердых сплавов, вязких цветных сплавов (алюминия, свинцовистых и цинковых сплавов) и пластмасс.
4)СОЖ подается под давлением на рабочую поверхность шлифовального круга вне зоны резания через одно или несколько сопел. Струи СОЖ, обладающие большой кинетической энергией, легко пробивают воздушный поток, окружающий шлифовальный круг, и с определенной силой воздействуют на рабочую поверхность круга, очищая его поры и абразивные зерна от частиц металла
иотходов шлифования. Рабочая поверхность круга смачивается СОЖ, и на абразивных зернах образуются смазочные пленки эффективной толщины.
Доказывая роль СОТС при подаче классическим методом, то есть поливом струей, в снижении теплонапряженности процесса шлифования, дифференцировано рассмотрено влияние характеристик СОТС, величины подачи жидкости в зону обработки, параметров процесса шлифования, режимов резания. В тоже время известно, что более эффективен метод, когда СОТС подается через поры шлифовального круга. Исследования и опыт промышленного использования доказали существенные преимущества этого метода по сравнению с подачей СОТС свободно падающей струей. Стойкость круга увеличивается в 2-2,5 раза, уменьшается износ шлифовального круга, снижается шероховатость шлифуемой поверхности и толщина дефектного слоя, создается возможность интенсификации режимов резания и повышения режимов обработки. Некоторая
59
усложненность конструкций устройств, обеспечивающих подачу СОТС через поры шлифовального круга, является одной из причин, из-за которых этот метод при таких явных преимуществах не нашел широкого применения в промышленности.
Математическая модель течения смазывающе-охлаждающей технологической среды дает возможность успешно решать проблему интенсификации теплопереноса в канале с проницаемой стенкой при моделировании процесса шлифования. Компьютерный эксперимент по оценке эффективности подачи СОТС в зону контакта «инструмент-деталь» дает возможность сделать соответствующие выводы, которые представляют интерес для широкого внедрения способа подачи СОТС через поры круга при шлифовании.
Знание теплофизических и гидравлических особенностей в процессе шлифования позволит оптимизировать процесс применения СОТС во всем широком аспекте характеристик СОТС и режимов резания.
УДК 621.9.04
Д.М. Черных
ИНТЕГРАЦИЯ ДОПОЛНИТЕЛЬНЫХ УПРАВЛЯЕМЫХ ОСЕЙ В СЧПУ ДЛЯ ПОВЫШЕНИЯ ПРОИЗВОДИТЕЛЬНОСТИ И ТОЧНОСТИ ПРИ ОБРАБОТКЕ СЛОЖНЫХ ПОВЕРХНОСТЕЙ
Вданной статье рассмотрена возможность изменения схемы формообразования сложных криволинейных поверхностей посредством использования дополнительной поворотной оси
Всовременных условиях перед машиностроительными пред-
приятиями ставят задачи повышения качества продукции и снижения издержек производства. При обработке деталей со сложными криволинейными поверхностями с повышенными требованиями к точностным характеристикам, в частности в авиакосмической отрасли, возникает ряд проблем, связанных с невозможностью обработки криволинейного профиля без получения погрешностей формы. Это происходит вследствие большого количества факторов, в том числе из-за ограничений, накладываемых системами числового программного управления (СЧПУ) и несовершенством кинематики металлообрабатывающих станков. СЧПУ фрезерных станков с воз-
60