
Учебное пособие 800417
.pdf
При выбранной системе координат изгибающий момент от равномерно распределённой нагрузки (включая и нагрузку от собственного веса вала) интенсивностью q в сечении с координатой х1
на первом участке (0 ≤ x1 ≤ С ) равен
2
|
|
|
|
|
|
|
|
|
|
|
|
|
|
b |
|
|
|
|
|
|
2 |
|
|
|
|
|
|
|
|
|
|
|
|
|
|
|
||||||||||
|
qb |
|
|
|
|
|
|
q |
|
|
x1 |
|
|
|
|
|
|
|
|
|
|
b |
|
|
|
b |
2 |
2 |
|
|
||||||||||||||||
|
|
|
|
|
2 |
|
|
|
|
|
|
|
|
|
|
|
|
|||||||||||||||||||||||||||||
|
|
|
|
|
|
|
|
|
|
|
|
|
|
|
|
|
|
|
|
|
|
|
|
|
|
|
|
x1 |
. |
(4) |
||||||||||||||||
MX1 |
|
|
|
|
x1 |
|
|
|
|
|
|
|
|
|
|
|
|
|
|
|
|
|
|
|
|
|
|
|
|
|
|
|
|
|
|
|
||||||||||
|
2 |
|
|
|
|
|
2 |
|
|
|
|
|
|
|
|
q |
2 |
|
|
|
|
|||||||||||||||||||||||||
2 |
|
|
|
|
|
|
|
|
|
|
|
|
|
|
|
|
|
|
|
|
|
|
|
|
|
|
|
|
8 |
2 |
|
|
||||||||||||||
Дифференциальное уравнение изогнутой оси на этом участке |
||||||||||||||||||||||||||||||||||||||||||||||
цилиндра выразится |
|
|
|
|
|
|
|
|
|
|
|
|
|
|
|
|
|
|
|
|
|
|
|
|
|
|
|
|
|
|
|
|
|
|
|
|
|
|
|
|
|
|||||
|
|
|
|
d |
2 |
y1 |
|
|
|
|
|
|
|
|
|
|
|
|
|
b |
|
|
|
|
|
b |
2 |
|
|
2 |
|
|
|
|
|
|
|
|||||||||
E1I1 |
|
|
MX |
|
q |
|
|
|
|
|
|
x1 |
|
. |
|
|
|
|
(5) |
|||||||||||||||||||||||||||
|
|
|
|
|
|
|
|
|
|
|
|
|
|
|
|
|
|
|
||||||||||||||||||||||||||||
|
|
|
|
|
dx2 |
|
|
|
|
1 |
|
|
|
|
|
|
|
|
4 |
|
|
|
8 |
|
|
|
2 |
|
|
|
|
|
|
|
||||||||||||
|
|
|
|
|
|
|
1 |
|
|
|
|
|
|
|
|
|
|
|
|
|
|
|
|
|
|
|
|
|
|
|
|
|
|
|
|
|
|
|
|
|
|
|
|
|
|
|
Проинтегрировав это дифференциальное уравнение дважды, |
||||||||||||||||||||||||||||||||||||||||||||||
получим: |
|
|
|
|
|
|
|
|
|
|
|
|
|
|
|
|
|
|
|
|
|
|
|
|
|
|
|
|
|
|
|
|
|
|
|
|
|
|
|
|
|
|
|
|
||
|
|
d |
2 |
y1 |
|
|
|
|
|
|
2 |
|
|
|
|
b |
2 |
x1 |
|
|
|
|
|
|
|
3 |
|
|
|
|
, |
|
|
|
|
(6) |
||||||||||
|
|
|
|
|
|
|
b x1 |
|
|
|
|
|
|
|
|
|
|
x1 |
|
|
|
|
|
|
|
|
||||||||||||||||||||
E1I1 dx2 |
q |
4 |
|
|
|
|
8 |
|
|
|
|
6 |
|
D1 |
|
|
|
|
|
|||||||||||||||||||||||||||
|
|
|
|
|
1 |
|
|
|
|
|
|
|
|
|
|
|
|
|
|
|
|
|
|
|
|
|
|
|
|
|
|
|
|
|
|
|
|
|
|
|
|
|
|
|
||
|
|
|
|
|
|
|
|
|
|
|
2 |
|
|
|
|
|
2 |
|
2 |
|
|
|
|
4 |
|
|
|
|
|
|
|
|
|
|
|
|
|
|
||||||||
|
|
|
|
|
|
|
|
|
b x1 |
|
|
|
b |
x1 |
|
|
|
|
x1 |
|
|
|
|
|
|
|
|
|
|
. |
|
(7) |
||||||||||||||
|
|
|
|
|
|
|
|
|
|
|
|
|
|
|
|
|
|
|
|
|
|
|
|
|
|
|
|
|||||||||||||||||||
E1I1y1 q |
8 |
|
|
|
|
16 |
|
|
24 |
|
D1x1 D2 |
|
|
|||||||||||||||||||||||||||||||||
|
|
|
|
|
|
|
|
|
|
|
|
|
|
|
|
|
|
|
|
|
|
|
|
|
|
|
|
|
|
|
|
|
Согласно рис. 1 а, при х=0 угол поворота dy1 |
= 0 и прогиб |
|
|
dx1 |
|
у1=0. Тогда из уравнения (7) постоянные интегрирования D1 = 0 и D2 = 0. Окончательно уравнение изогнутой оси на первом участке выразится
|
y |
|
|
|
dx2 |
|
|
|
(6b b |
2 2x2 ). |
|
|
|
|
|
|
|
(8) |
|||||||||||||||||||||
|
|
|
|
|
1 |
|
|
|
|
|
|
|
|
|
|
||||||||||||||||||||||||
|
|
48E I |
|
|
|
|
|
|
|
|
|
||||||||||||||||||||||||||||
|
|
1 |
|
|
|
|
1 |
|
|
|
|
|
|
|
|
|
|
|
|
|
|
|
1 |
|
|
|
|
|
|
|
|
|
|
||||||
|
|
|
|
|
|
|
|
|
|
1 |
|
|
|
|
|
|
|
|
|
|
|
|
|
|
|
|
|
|
|
|
|
|
|
|
|
|
|
||
На втором участке |
c |
x |
|
|
|
b |
изгибающий момент в сечении |
||||||||||||||||||||||||||||||||
|
|
|
2 |
|
|
|
|
||||||||||||||||||||||||||||||||
с координатой х2 равен |
|
|
|
2 |
|
|
|
|
|
2 |
|
|
|
|
|
|
|
|
|
|
|
|
|
|
|||||||||||||||
|
|
|
|
|
|
|
|
|
|
|
|
|
|
|
|
|
|
|
|
|
|
|
|
|
|
|
|
|
|
||||||||||
|
|
|
|
|
|
|
|
|
|
|
|
|
|
|
|
|
|
|
b |
|
|
|
|
|
2 |
|
|
|
|
|
|
|
|
|
|
|
|||
|
|
|
|
|
qb |
|
|
|
|
|
|
|
|
|
|
q |
|
x2 |
|
|
|
|
|
b |
2 |
2 |
|
(9) |
|||||||||||
|
|
|
|
|
|
|
|
|
|
|
|
|
2 |
|
|
||||||||||||||||||||||||
|
|
|
|
|
|
|
|
|
|
|
|
|
|
|
|
|
|
|
b |
|
|
|
x2 |
. |
|||||||||||||||
MX1 |
|
|
|
|
|
|
|
x1 |
|
|
|
|
|
|
|
|
|
|
|
|
|
q |
|
|
|
|
|
|
|
|
|||||||||
|
|
2 |
2 |
|
|
|
|
2 |
|
|
|
|
|
4 |
|
|
|
|
|||||||||||||||||||||
|
|
|
|
|
|
|
|
|
|
|
|
|
|
|
|
|
|
|
|
|
|
|
|
|
8 |
2 |
|
|
|||||||||||
Дифференциальное уравнение изогнутой оси на этом участке |
|||||||||||||||||||||||||||||||||||||||
|
|
|
d |
2 |
y2 |
|
|
|
|
|
|
|
|
|
|
|
|
b |
|
|
b |
2 |
|
2 |
|
|
|
|
|
|
|
|
|
||||||
E |
I |
2 |
|
|
|
M |
X2 |
|
q |
|
|
|
|
x2 |
|
. |
|
|
|
|
|
|
(10) |
||||||||||||||||
|
|
|
|
|
|
|
|
|
|
|
|
|
|
|
|
|
|||||||||||||||||||||||
2 |
|
|
|
|
2 |
|
|
|
|
|
|
|
|
|
|
4 |
|
|
|
|
8 |
|
2 |
|
|
|
|
|
|
|
|
|
|||||||
|
|
|
dx2 |
|
|
|
|
|
|
|
|
|
|
|
|
|
|
|
|
|
|
|
|
|
|
|
|
|
|
Интегрируя это уравнение дважды и подставляя значения постоянных интегрирования, получим уравнение прогибов на втором участке:
31

|
|
|
y2 |
q |
[ x2 (48b 24b2 16x2 ) |
(11) |
||||||
|
|
334E1I1 |
||||||||||
|
|
|
|
|
|
|
|
|
|
|||
|
|
|
c(1 )(48b x 24b2x 8c2 x 6b2c 12b c 3c3 )] |
|||||||||
|
При x |
b |
максимальный прогиб равен: |
|
||||||||
|
|
|
||||||||||
|
|
2 |
|
|
|
|
|
|
|
|||
ymax2 |
f2 |
|
q |
[ b3(12 7b) c(1 )(24b2 12b3 |
4bc2 6b2c 12b c 3c3 )] |
|||||||
334E1I1 |
||||||||||||
|
|
|
где |
|
|
E1I1 – коэффициент приведения жесткости; |
||||||
|
|
|
|
|
|
|
|
|||||
|
|
|
|
|
|
|
|
E2I2 |
|
|
||
|
|
|
|
|
|
|
|
|
|
с – длина среднего участка жесткостью E1I1;
Для вала с опорой посередине (рис. 3) находим дифференциальные уравнения изогнутой оси и прогибы на участках.
Рис. 3. Расчетная схема прогиба вала, с опорой посередине.
На первом участке (0 ≤ x1 ≤ С ) изгибающий момент в сечении
2
с координатой х1 равен
|
|
|
|
|
|
|
|
|
|
|
|
|
b |
2 |
|
|
|
|
|
|
|
|
|
|
|
|
|
|
|
||
|
qb |
|
|
|
|
|
|
q |
|
|
x1 |
|
2 |
|
|
b |
|
b |
2 |
|
|
||||||||||
|
|
|
|
|
|
|
|
|
|||||||||||||||||||||||
|
|
|
|
|
|
2 |
|
|
|
x1 |
|
|
|
|
. |
(12) |
|||||||||||||||
MX1 |
|
|
|
|
|
x1 |
|
|
|
|
|
|
|
|
|
|
|
|
|
|
|
|
|||||||||
|
|
|
|
|
|
2 |
q |
2 |
|
|
|
|
|||||||||||||||||||
|
|
2 2 |
|
|
|
|
|
|
|
|
|
|
4 |
|
8 |
|
|
||||||||||||||
Дифференциальное уравнение изогнутой оси на первом |
|||||||||||||||||||||||||||||||
участке цилиндра имеет вид |
|
|
|
|
|
|
|
|
|
|
|
|
|
|
|
|
|||||||||||||||
|
|
|
|
|
|
|
|
|
|
|
d2 y1 |
|
x12 |
|
|
|
b |
|
|
b2 . |
|
||||||||||
|
|
|
|
|
|
|
|
|
|
|
|
|
|
|
|
|
|
|
|
|
|
|
|
|
|
|
|
|
|
|
|
|
|
|
|
|
|
E1I1 dx2 M X1 |
2 |
|
4 |
8 |
|
|
|||||||||||||||||||
|
|
|
|
|
|
q |
|
|
|
|
|||||||||||||||||||||
|
|
|
|
|
|
|
|
|
|
|
|
|
1 |
|
|
|
|
|
|
|
|
|
|
|
|
|
|
|
|
|
|
Дважды интегрируя, получим уравнение изогнутой оси на |
|||||||||||||||||||||||||||||||
первом участке |
|
|
|
|
|
|
|
|
|
|
|
|
|
|
|
|
|
|
|
|
|
|
|
|
|
|
|
|
|
|
|
y |
|
|
dx12 |
|
|
(2x2 |
6b 3b2). |
|
|
|
|
|
|
|
|
|
|
|
|
|
(13) |
||||||||||
48E I |
|
|
|
|
|
|
|
|
|
|
|
|
|
|
|
||||||||||||||||
1 |
|
|
1 |
|
|
1 |
|
|
|
|
|
|
|
|
|
|
|
|
|
|
|
|
|
|
|
||||||
|
|
|
|
|
1 |
|
|
|
|
|
|
|
|
|
|
|
|
|
|
|
|
|
|
|
|
|
|
|
|
32

На втором участке ( с ≤ x2 ≤ b ) изгибающий момент в сече-
|
|
|
|
|
|
|
|
|
|
|
|
|
|
2 |
|
|
|
|
|
|
|
2 |
|
|
|
|
|
|
|
|
|
|
|
||
нии с координатой х2 |
равен |
|
|
|
|
|
|
|
|
|
|
|
|
|
|
|
|
|
|
|
|
||||||||||||||
|
|
|
|
|
|
|
|
|
|
b |
2 |
|
|
|
|
|
|
|
|
|
|
|
|
|
|
|
|
|
|
|
|
|
|||
|
|
|
|
|
|
|
|
|
|
q |
|
|
x2 |
|
|
|
|
|
2 |
|
bx2 |
|
|
b |
2 |
|
|
(14) |
|||||||
|
|
|
|
|
|
|
|
|
|
|
|
|
|
|
|
|
|
||||||||||||||||||
|
|
|
|
|
|
|
|
|
|
2 |
|
|
|
|
|
x2 |
|
|
|
|
|
. |
|
||||||||||||
|
|
|
|
|
|
MX 2 |
|
|
|
|
|
|
q |
|
|
|
|
|
|
|
|
|
|
|
|
|
|
|
|||||||
|
|
|
|
|
|
|
|
|
2 |
|
|
|
|
|
2 |
|
8 |
|
|
|
|||||||||||||||
|
|
|
|
|
|
|
|
|
|
|
|
|
|
|
|
|
2 |
|
|
|
|
|
|
|
|
|
|||||||||
|
|
|
|
Дифференциальное уравнение изогнутой оси на этом участке |
|||||||||||||||||||||||||||||||
выразится |
|
|
|
|
|
|
|
|
|
|
|
|
|
|
|
|
|
|
|
|
|
|
|
|
|
|
|
|
|
|
|||||
|
|
|
|
|
|
|
|
|
|
|
|
|
|
|
|
|
d |
2 y2 |
|
|
|
x22 |
|
bx2 |
|
b2 |
|||||||||
|
|
|
|
|
|
|
|
|
|
|
|
|
E |
I |
2 |
|
|
|
|
q |
|
|
|
|
|
|
|
|
|
|
|
||||
|
|
|
|
|
|
|
|
|
|
|
|
|
|
2 |
|
|
|
|
|
|
|
|
|
||||||||||||
|
|
|
|
|
|
|
|
|
|
|
|
|
2 |
|
|
|
|
|
|
|
|
|
|
|
2 |
|
|
|
|
||||||
|
|
|
|
|
|
|
|
|
|
|
|
|
|
|
|
|
dx2 |
|
|
|
2 |
|
|
|
|
8 |
|||||||||
|
|
|
|
Проинтегрировав это уравнение, получим уравнение проги- |
|||||||||||||||||||||||||||||||
бов на втором участке |
|
|
|
|
|
|
|
|
|
|
|
|
|
|
|
|
|
|
|
|
|
|
|
||||||||||||
y |
2 |
|
q |
|
[16x4 |
32bx3 24b2 x2 |
24bcx |
|
|
|
|
|
|
(15) |
|||||||||||||||||||||
|
|
|
|
|
|
|
|
||||||||||||||||||||||||||||
|
|
|
|
|
2 |
|
|
|
2 |
|
|
|
|
2 |
|
|
|
|
|
2 |
|
|
|
|
|
|
|
||||||||
|
|
|
|
|
384E2I2 |
|
|
|
|
|
|
|
|
|
|
|
|
|
|
|
|
|
|
|
|
|
|
|
|
|
|
||||
8(1 )(c3 |
3b2c)x2 48 b cx2 |
8bc3 |
(1 )(3c4 |
6b2c2 ) 12 b c2 ] |
|||||||||||||||||||||||||||||||
|
|
|
|
При x2 |
b |
максимальный прогиб равен |
|
|
|||||||||||||||||||||||||||
|
|
|
|
|
|
||||||||||||||||||||||||||||||
|
|
|
|
|
q |
2 |
|
|
|
|
|
|
|
|
|
|
|
|
|
|
|
|
|
|
|
|
|
|
|
|
|
|
|
||
f |
|
|
|
|
[3b4 (1 )(12b3c 6b2c2 |
|
4bc3 |
3c4 ) 12b2c2 8bc3 12 bc(2b c)] |
|||||||||||||||||||||||||||
1 |
|
384E2 I2 |
|
||||||||||||||||||||||||||||||||
|
|
|
|
|
|
|
|
|
|
|
|
|
|
|
|
|
|
|
|
|
|
|
|
|
|
|
|
|
|
|
|
|
Значение прогиба вала может быть уменьшено путем изменения его конструкции или системы нагружения. Из опыта эксплуатации валковых машин установлено, что суммарный прогиб средних сечений валов относительно их торцов для валковых пар не должен превышать 0,10...0,15 мм, где меньшие значения прогиба относятся к валам с более жесткими покрытиями.
Таким образом, разрабатывая валковое оборудование, конструктор имеет возможность определить прогиб валов и сравнить их с допустимыми значениями, задавая тем самым уровень качества обработки материала на этапах проектирования.
Литература:
1. Demidov A.V., Udval L., Belov S.V., Fomin Yu.G. STUDYING THE RELATIONSHIP BETWEEN WOOL MOISTURE CONTENT AFTER EXPRESSION AND TECHNOLOGICAL FACTORS. Известия высших учебных заведений. Технология текстильной промышленности. 2004. № 6. С. 100-102.
Воронежский государственный технический университет
33
УДК 677 057
А.В. Демидов
РАЗРАБОТКА ОБОБЩЕННОЙ МОДЕЛИ ВАЛА ВАЛКОВЫХ МАШИН
Встатье проводится анализ различных конструкций валов и предложена обобщённая модель вала с целью дальнейшей разработки САПР валкового оборудования
Внастоящее время большое влияние уделяется развитию вал-
ковых машин с рабочей шириной свыше 1800 мм. При этом возникают дополнительные технические и технологические проблемы. Значительное влияние на конечные свойства технологического продукта оказывает наличие деформации (прогиба) валов. Исследовательские работы в данной области имели цель определить величину этой неравномерности и разработать условия ее снижения путем применения специальных конструкций валов и механизмов их нагружения.
Для разработки обобщенной модели валов проанализированы их отдельные конструктивные решения, представленные на рис. 1, с точки зрения показателей металлоемкости и прогиба.
Наиболее простое конструктивное решение имеет сплошной вал (рис. 1 а): он прост в изготовлении, его собственный вес обеспечивает хороший прижим при обработке материала, имеет малый прогиб за счет большой жесткости, однако повышенная материалоемкость заставляет искать другие решения конструктивного оформления без значительного увеличения сложности металлоконструкции. Вал с бомбировкой (рис. 1 б) можно назвать частным случаем сплошного вала. Такой вал позволяет получить хорошие результаты при постоянной, заранее определенной нагрузке. Вал с рубашкой в виде трубы и цапфами, закрепленными на торцевых сечениях трубы (рис. 1 в), имеет малый вес, но максимальные, по сравнению с другими конструкциями, прогибы. Заглубление опор внутрь рубашки (рис. 1 г) приводит к уменьшению прогибов, а применение двойных заглубленных опор (рис. 1 д) позволяет уменьшить размер контакта цапфы с рубашкой, что дает снижение собственного веса вала счет уменьшения веса цапф.
34
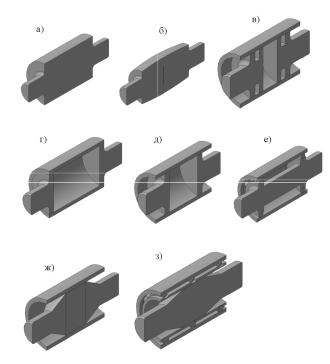
Рис. 1. Схемы конструкций валов
Вал с раздельным сердечником проще в изготовлении, чем вал со сплошным сердечником. Вал с рубашкой в виде трубы и сплошным сердечником (рис. 1 е) прост в изготовлении и имеет меньший прогиб по сравнению другими конструкциями. Данный эффект достигается с использованием опор качения, установленных по краям рубашки. Вал с рубашкой, закрепленной посередине, и сплошным сердечником (рис. 1 ж), имеет меньший прогиб за счет уменьшения воспринимаемой нагрузки в центральной части рубашки. Уменьшение прогиба достигается также с применением конструкции вала со сплошным сердечником и двумя рубашками (рис 1 з). Прогиб первой (внутренней) рубашки уменьшается за счет ее крепления на сплошном сердечнике посередине. В дальнейшем передаваемая нагрузка ко второй (внутренней) рубашке выравнивается в результате установки ее на опоры качения, закрепленных по краям и середине первой рубашки.
35
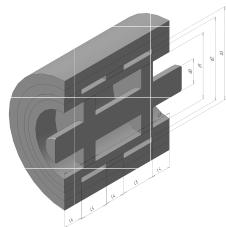
Рассмотренные конструкции валов могут быть представлены в виде обобщенной модели. Применяющиеся системы автоматизированного проектирования валкового оборудования включают в себя САПР конструкций валов. Для разработки обобщенной модели вала (рис. 2) валы классифицированы по следующим признакам: структуре вала, количеству опор, способу крепления рубашки, типу сердечника (оси) и привода.
Для обработки материалов с равномерной толщиной наиболее перспективным является использование малопрогибных конструкций валов (крепление рубашки на трех опорах, серединной или заглубленное) с более равномерным распределением давления в жале.
Рис. 2. Обобщенная модель вала
Все исследования валковых модулей можно разделить условно на три направления:
-расчет на прочность и жесткость валов;
-статический анализ (определение неравномерности давления
взоне контакта валов);
-динамический анализ (определение частот и форм собственных колебаний валов).
Обобщенная модель (рис. 2) позволяет проектировать валы различных конструкций с учетом характера действующей нагрузки, используя сочетания конструктивных параметров сердечников и рубашек, а также способов их крепления и соединения.
Воронежский государственный технический университет
36
УДК621
О.К. Битюцких СОЕДИНИТЕЛЬНЫЕУСТРОЙСТВАИ ИХ КЛАССИФИКАЦИЯ
Встатье приводится современная классификациямашиностроительных муфт
Втехнике соединительные устройства — это муфты. Они предназначены для тех валов, концы которых подходят один к другому вплотную или же удалены на небольшое расстояние. Соединение валов муфтами обеспечивает передачу вращающего момента от одного вала к другому. Валы, как правило, расположены так, что геометрическая ось одного вала составляет продолжение геометрической оси другого вала. С помощью муфт можно также передать вращение с валов на зубчатые колеса, шкивы, свободно насаженные на эти валы.
Применение муфт в машиностроении вызвано необходимо-
стью:
- получения длинных валов, изготовляемых из отдельных частей, компенсации небольших неточностей монтажа в относительном расположении соединяемых валов;
- придания валам некоторой относительной подвижности вовремя работы (малые смещения и перекос геометрических осей валов);
- включения и выключения отдельных узлов; - автоматического соединения и разъединения валов в зависи-
мости от пройденного пути, направления передачи вращения, угловой скорости, т.е. выполнения функций автоматического управления;
- уменьшение динамических нагрузок.
Современные машины состоят из ряда отдельных частей с
входными и выходными концами валов, которые соединяют с помощью муфт (рисунок).
Многообразие конструкций муфт усложняет их классификацию. Простейшая муфта сделана из куска ниппельной трубочки и соединяет вал электромоторчика с крыльчаткой автомобильного омывателя стекла. Муфты турбокомпрессоров реактивных двигателей состоят из сотен деталей и являются сложнейшими саморегулирующимися системами.
37
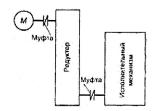
Принципиальная схема машины
Группы муфт различают по характеру соединения валов: - муфты механического действия:
а) жесткие (глухие) — практически не допускающие компенсации радиальных, осевых и угловых смещений валов;
б) компенсирующие — допускающие некоторую компенсацию радиальных, осевых и угловых смещений валов благодаря наличию упругих элементов (резиновых втулок, пружин и др.);
в) фрикционные - допускающие кратковременное проскальзывание при перегрузках;
- муфты электрического (электромагнитного) действия; муфты гидравлическогоили пневматического действия.
В электрических и гидравлических муфтах, используют принципы сцепления за счет электромагнитных и гидравлических сил. Эти муфты изучают в специальных курсах. Далее анализируются только механические муфты. Большинство применяемых муфт стандартизованы. Основной характеристикой при подборе муфт по каталогу или справочнику является передаваемый момент, учитывающий наиболее тяжелое условие ее нагружения.
Классы муфт различают по режиму соединения валов:
-нерасцепляемые (постоянные, соединительные) – соединяют валы постоянно, образуют длинные валы;
-управляемые (сцепные) - соединяют и разъединяют валы в процессе работы, например, широко известная автомобильная муфта сцепления;
-самодействующие (самоуправляемые, автоматические) - срабатывают автоматически при заданном режиме работы (обгонные, центробежные, предохранительные);
-предохранительные муфты, разъединяющие валы при нарушении нормальных эксплуатационных условий работы;
-прочие.
По степени снижения динамических нагрузок муфты бывают:
38
-жесткие, не сглаживающие при передаче вращающего момента вибрации, толчки и удары;
-упругие, сглаживающие вибрации, толчки и удары благодаря наличию упругих элементов — пружин, резиновых втулок и др.
Основная характеристика муфты - передаваемый вращающий момент.
Существенные показатели - габариты, масса, момент инерции. Муфта, рассчитанная на передачу определённого вращающего момента, выполняется в нескольких модификациях для разных диаметров валов. Муфты — автономные узлы, поэтому они легко стан-
дартизируются.
Муфты рассчитывают по их критериям работоспособности: прочности при циклических и ударных нагрузках; износостойкости; жёсткости.
На практике муфты подбираются из каталога по величине передаваемого вращающего момента Т=ТВала К, где ТВала - номинальный момент, определённый расчётом динамики механизма (наибольший из длительно действующих), К - коэффициент режима работы.
В приводах от электродвигателя принимают:
-при спокойной работе и небольших разгоняемых массах (приводы конвейеров, испытательных установок и др.) К = 1,15... 1,4;
-при переменной нагрузке и средних разгоняемых массах (металлорежущие станки, поршневые компрессоры и др.) К= 1,5...2;
-при ударной нагрузке и больших разгоняемых массах (прокатные станы, молоты и др.) К= 2,5...3.
Диаметры посадочных отверстий муфты согласуют с диаметрами концов соединяемых валов, которые могут быть различными при одном и том же вращающем моменте вследствие применения разных материалов и различной нагруженности изгибающими моментами. Основные типы муфт регламентированы стандартом для некоторого диапазона диаметров валов и рассчитаны на передачу определенного момента.
Наиболее слабые звенья выбранной муфты проверяют расчетом на прочность по расчетному моменту Тр.
Работа муфт сопровождается потерями. По опытным данным при расчетах КПД муфт обычнопринимают η=0,985...0,995.
Многообразие узловых конструкций машин способствует ши-
рокому распространению муфт в машиностроении.
Воронежский государственный технический университет
39
УДК 621.791
В.В. Постоев, Ю.С. Ткаченко
ВОССТАНОВЛЕНИЕ ДЕТАЛЕЙ МЕТАЛЛООБРАБАТЫВАЮЩИХ СТАНКОВ ГАЛЬВАНИЧЕСКИМИ ПОКРЫТИЯМИ
В статье показана роль гальванических покрытий при восстановлении деталей, представлены результаты некоторых исследований и направления дальнейших исследований
Большинство деталей металлообрабатывающих станков работают в сложных условиях. Условия работы оказывают значительное влияние на конструктивные и технологические параметры деталей. При восстановлении деталей станков в производстве широко используются способы восстановления гальваническими покрытиями. Нанесение гальванических покрытий это один из преимущественно распространённых способов зашиты металлов от коррозии.
Оно позволяет :
Наносить равномерные покрытия с различной твердостью (600 …12000 МПа) и износостойкостью при отсутствии термического воздействия на детали, вызывающего в них нежелательные изменения структуры и механических свойств.
Получить с большой точностью заданную толщину покрытий, снизить до минимума припуск на последующую механическую обработку или исключить ее из технологического процесса.
Автоматизировать процесс, что гарантирует получение высококачественных покрытий требуемой толщины и с заданными механическими свойствами.
Наиболее широко в практике ремонтного производства для восстановления изношенных деталей применяют осталивание (железнение). Данный способ восстановления позволяет: наращивать на детали большой слой стали(до 5 мм); использовать дешевый электролит, который получается путем травления железной стружки в соляной кислоте; достигать высокой производительности процесса (обеспечивается отложение стали толщиной 0,13-0,26 мм/ч, т.е. примерно в 8 раз чем при хромировании).
Помимо восстановления изношенных деталей осталиванием применяют для исправления брака механической обработки и для
40